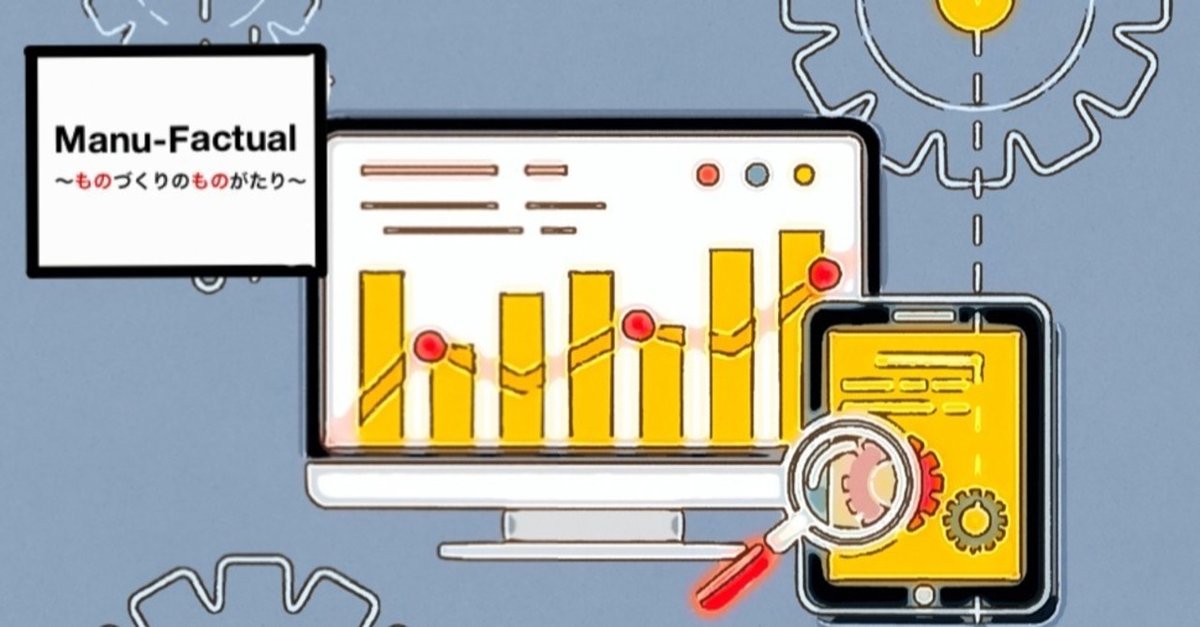
【見える化編6:中核「問題の見える化」(後半)】
本マガジンのテーマは「見える化」です。私も12年ほど、工場管理行っていますが、何度も何度も聞くキーワードが見える化です。ただ、これは工場の管理だけでなくすべての仕事、ビジネスにとって重要な考え方であり、活動であると思います。経験がある方が多いと思いますが、問題や状況が正しく見えるということができれば解決策や必要なアクションは自然と出てくるものです。そんな見える化について、体系的にかつ実例も入れて解説している名著「見える化-強い企業をつくる「見える」仕組み 遠藤功氏著」について解説していきます。2005年が初版で、15年前の本ですが、間違いなく今でも通用する内容です。
今回も、製造部の上司の正輝と部下の流星が登場します。流星は前回自工程完結を学んで実践していく中で、見える化がすべての改善活動につながってくることに気づき始めます。そして、再度正輝と会話している中で、見える化とはなんなのか、どう使っていくべきなのかということについて、本を使って学んでいきます。前回、見える化の体系について指導を受け、今回から具体的な事例の解説に入っていきます。今回は問題の見える化の中の「真因の見える化」と「効果の見える化」について学びます。
・・・・・・・・・
👱;おはようございます。
👨;おはよう。前回、「問題の見える化」の中でも「異常の見える化」「ギャップの見える化」「シグナルの見える化」について解説した。今日は「問題の見える化」の残りの「真因の見える化」と「効果の見える化」について解説する。ちなみに体系は下記だ。常に頭に入れておいてくれ。
👱;わかりました。
◆「真因の見える化」
👨;さて、「真因の見える化」の解説をしていこう。異常や問題を引き起こしている真の理由が「見える」ようになれば、当然対策は実施しやすいし、効果も得やすい。だが、実際や異常や問題が見えたからといって、すぐにその真因がわかるなんてことはほとんどないと思う。
👱;はい。問題の事象を分析・考察をしないと真因が見えてこないケースがほとんどですね。そして真因といっても実際にやってみるまでは仮説の域はでません。
👨;そうだよな。だからこそ、トヨタでは5回なぜを繰り返すなど行っている。そして、真因をつかむためには、真因を探るために必要な情報やデータが「見える化」されていなければならないんだ。
👱;そうですよね。そこにいくまでにそもそも見える化が必要ですよね。
👨;そう。そしてその際重要なのは、一般には守秘性が高いと思われるような情報やデータまで現場に「オープン」にすることなんだ。「ここまで開示するの?」というデータを「見える化」を行ってこそ、現場の知恵や創意工夫は生まれてくるんだ。一つの例を紹介しよう。
◆トヨタにおける「原価の見える化」
👨;トヨタの「見える化」は決して、モノづくりの現場に限ったことではないんだ。トヨタでは、なかなか「見える化」させにくい原価をガラス張りにし、大幅なコストダウンを実現してきたのは知っているかい?
👱;原価の見える化ですか?原価って、、それがもし外部に漏れてしまったら大変なことですよね。。そんなものを「見える化」してきたのですか?
👨;そう。言う通り、原価は社外に漏れてしまうリスクを恐れて、社内に対しても秘密扱いとなっているケースが多い。だが、さすがのトヨタでも、いつまでも原価は秘密だけどとにかくコストを下げろでは通用しなくなり、「原価の見える化」にも踏み切ったのだという。つまり、原価をオープンにすることによって、改善の出発点である「標準」を設定したんだ。
👱;コスト標準ですか。確かに標準が定まるとトヨタは強い気がします。
👨;その標準を「よりよい標準」に改善するため、部門横断的に知恵を出し合い、原価低減を進めていったんだ。
👱;なにか例ってあるんでしょうか?
👨;2000年初旬という昔の話ではあるが、代表例が、新型カローラの開発だという。カローラは一般大衆者として有名だが、性能・品質のよさに比べ、値頃感のある車として人気を博し、長期にわたって国内販売台数第一位を獲得している。だが、さらなる原価低減が必要であった。
👱;そこに出てきたのが、「原価の見える化」だったというわけですか。
👨;そう。総原価を見直すためには、部品一つひとつの単価にまでこだわり、ムダを排除していくことが不可欠である。部品単価の明細まで「見える化」し、どこにコスト上の問題があるのか、を徹底的に議論し、真因を探り当てるということをしたんだ。
👱;部品一つ一つの単価にこだわるって、同社部品って、数万点のレベルですよね。その中で、原価が上がる真因を見出すと。
👨;そう。そこまで「原価の見える化」を行って「ムダの真因が見える」ようにする。そして、「改善の知恵が見える」 という改善のサイクルを作っていったんだ。
👱;いかに、正しい方向性を決めて、行動を喚起するかですもんね。
👨;「原価の見える化」を推進した経理担当の荒木副社長 (当時 ) はこう語っているんだ。
「経理の一番大事な仕事は、『見える化』を進めることだ」
とね。
👱;経理の仕事ですか、なるほど今現場をイメージしていますが現場だけでなく営業や間接部門でも見える化しているということですね。
◆「効果の見える化」
👨;次は、「効果の見える化」だ。これまで述べてきているように、異常や問題が露見したら、対策を講じなければならない。異常や問題が「見える化」されれば、通常それを認識した人は何とかしようとアクションをとる。これが「見える化」の目的だ。
👱;でも、アクションをとったとしてもいきなり問題が解決されるなんてことは珍しいですし、効果的なアクションであるか、つまり正しい努力であるかがわからないといけないですよね。
👨;そう。その効果が「見える化」されなければ、問題解決が完了したとは言えないんだ。そして、「効果の見える化」を実践することは、どのような異常や問題にはどのような対策が効果的なのかを学習することにつながるんだ。つまり、組織力に直結していく。見える化の本質である現場力を高めるためには、「効果の見える化」は不可欠なんだ。そんな「効果の見える化」に取り組んでいる事例を一つ紹介する。
◆キヤノンの生産革新における「効果の見える化」
👨;トヨタだけでなく、キヤノンでも生産革新によるカイゼン活動が日常活動の中に埋め込まれているんだ。複写機をはじめとする映像事務機を生産する茨城県の阿見工場では、「一秒の視点」をスローガンに、作業効率の徹底追求が続けられているという。2005年の本だから今は不明だが、本質は変わっていないだろう。
👱;一秒の視点。。すごい視点ですね。そこまで細やかな改善が行われているということですね。
👨;カイゼンを継続させるための「月一改善」や「週一改善」「品質朝市」といった改善を実践する「場」が仕組みとして埋め込まれ、工場の幹部と現場が一体となってカイゼンに取り組んでいるんだ。
👱;その工場には改善文化が埋め込まれているのですね。
👨;ああ、だが、こうした仕組みに加えて、キヤノンが重視しているのが「人づくり」でるというんだ。カイゼンは現場の主体性・自律性がなければ定着しないよな。ほかの人から言われてやっているというカイゼンは長続きしない。
👱;はい。すごくわかります。現場の作業者自身が当事者意識を持ってカイゼンに取り組むまないと、文化にはなっていかないです。すべての改善は、イベントになってしまします。
👨;そこで、阿見工場では、現場の自律性を喚起するために、カイゼンの「効果の見える化」に熱心に取り組んでいるんだ。
👱;自立性を喚起するために「効果の見える化」を行っているのですか。興味深いです。
👨;キャノンのといえば「セル生産方式」だよな。この工場でも、高級複写機を「セル生産方式」で生産している。「セル」とは「細胞」の意味で、ひとりから数人のグループが部品の取り付け、組み立て、加工、検査までの全工程を自己完結的に行う生産方式である。多能工化の極みといってもいいんだが、これには現場の従業員一人ひとりの自発性・創意工夫が肝になってくる。
👱;はい。わかります。
👨;このセル生産に取り組んでいる作業者は毎回、目標生産台数に到達した時刻を実績として記録する。それを前回の記録と比較して、どれだけ作業の効率が上がったかを認識し、その理由を解析する。
👱;理由を解析するのですか。それも個人やチームでですね。通常は数字を並べるだけになりますね。
👨;ああ。でも、その理由をきちんと解析できていくと「部品の配置方法を変えてみたら、昨日より一分早く目標台数をクリアーできた」などの成果が数値としてはっきり「見える」ようになるんだ。
👱;それに、自分の改善が具体的な効果として「見える化」されると改善へのモチベーションは上がってきますよね。
👨;効果を「記録」することはカイゼンの基本だ。カイゼンに取り組むと、知恵を出すことばかりに目が行き、どうしても記録がおろそかになってしまう。
👱;そうなんですよね・・。結構活動自体に集中しちゃって、あれ?そもそもこれってどういう数字だったんだっけ?効果ってどう測定するんだっけ?となってしまうのですよね。。
👨;効果があってもなくても、記録を残すことが現場改善の基本中の基本だ。キヤノンの生産現場では、作業者自らが、自分の作業改善のために「記録」を残し、そして、効果が上がったものについては、組織の知恵として組織内に「見える化」することが徹底されているんだ。
👱;効果があってもなくても、記録を残すことが基本中の基本。なるほどです。記録を取っていれば、この問題に対して、このアクションは効果がなかったということがわかることも一つの成果ですもんね。
👨;その通り。今回は、ここで終了だ。この「効果の見える化」まででの「問題の見える化」の解説は終了だ。次回は状況の見える化を解説する。
・・・・・・・・・・
今回は、問題の見える化の「真因の見える化」と「効果の見える化」について解説しました。体系化してわけていますが、もちろん本質は変わりません。無駄を見えるようにして、知恵を見えるようにするサイクルを作る、そして問題・異常にに気づく人を育てていくことが大事なのですよね。さて、次回は状況の見える化に入っていきます。
*下記の固定記事に、このnoteのコンセプト、これまでのマガジンについて解説しています。
#製造
#理論と実践
#ものづくり
#成長
#5S
#トヨタ生産方式
#ジャストインタイム
#自働化
#リーンプロダクション
#ザゴール
#制約理論
#ドラッガー
#ビジョナリーカンパニー
#アドラー
#コーチング
#情報リテラシー
#要件定義
#会計
#損益計算書
#決算書
#損益分岐点
#原価低減
#平準化
#両利きの経営
#両利きの組織
#心理的安全性
#グーグル
#推薦図書
#システム
#発注側
#会社改造
#事業再生
#見える化
この記事が参加している募集
この記事が気に入ったらサポートをしてみませんか?