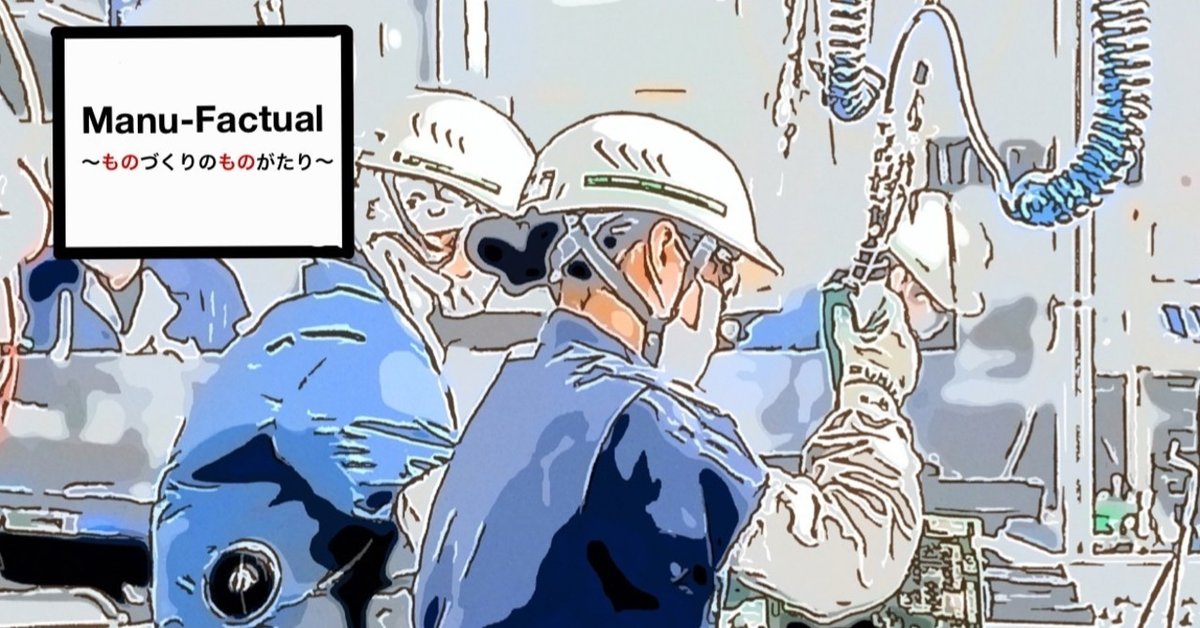
【自工程完結編3:不可能を可能にもする自工程完結】
本マガジンの過去の投稿は上記に入れています。
ご存じのようにこれまでトヨタは、トヨタ生産方式を展開し、世界で確固たる地位を築き、その生産方式自体米国でも研究され体系化されリーン生産方式としても名をはせています。そんなトヨタがさらに仕事の質を改善するため、10年以上にわたって取り組んでいる「自工程完結」について対話形式で解説していきます。自工程完結とは、「良い仕事しかできない(やり直しがない)、良いものしか作れない(作り直しがない)という条件は何かということを徹底的に科学的に実現しようとする」考え方です。
さて、今回は過去のマガジンで心理的安全性を学んだ、製造課長の正輝が再登場します。
ある時、課内の工程主任であるの流星(若手)が現場への仕事指示の仕方、仕事の進め方で苦労しているところを目にします。そこから下記の本をベースに自工程完結の指導を実施し、実際の導入に取り組んでいきます。
・・・・・
◆複数工程にまたがる課題
👱;おはようございます。
👨;おはよう。今日も、現場で活用する自工程完結について解説するぞ。実際にトヨタでの「水漏れ」という不具合の改善例を取り上げる。ぜひ参考にしてみてくれ。2000年頃の活動だそうだ。
👱;2000年?そんな頃から取り組みを始めたのですね。。
👨;まず、この水漏れ対策の背景だ。著者の佐々木さんが、組み立て部という製造担当部門の部長に移動したときに仕事を改善しようと思ったそうだ。本気になって何か新しい取り組みをしようとね。最も難しい課題が良いと考え、課長を集めて聞いてみると、出てきたのが「水漏れ品質保証」だったというんだ。それでこの問題を自工程完結の概念を使って取り組むことにしたそうだ。
👱;なるほど。でも、すみません。水漏れっていったい何ですか?
👨;自動車は屋外で走るものだから、雨風に打たれる。当時は水漏れが起きることがごく稀にあったそうだ。そのために行われているのがシャワーテストというもので、出来上がった車に水を激しく書ける。そして水漏れがないか見ていくんだ。
👱;その名の通りの現象でしたね。しかし、水漏れが流失したらまずいですから、必死でチェックするということですね。車買って、雨の日に運転していて、水が漏れてきたなんていったら大騒ぎしますもんね。
👱;なるほど。でも、それが見つかると製造部門としてはショックですね。きっとそれが見つかれば厳しい指摘が入るでしょうから。
👨;ああ。でも本当に細かなところまで見るそうだ。そうすると、鉄板と鉄板の間が微妙にあっていなかったり、溶接際に小さな穴が開いてそこから水が入ったり、ゴムの継ぎ目から水があふれだしたりといった原因がごく稀に見つるのだという。そして、水漏れがやっかいなのは、それぞれのプロセスごとにチェックするのではなく最後の検査1度でチェックするのでどこに問題があったか把握するのに大きな労力がかかるんだ。組み立てだけではない、塗装、その他工程含めてチェックしなければならない。
👱;そうなると、原因把握にも時間がかかるでしょうし、うちの工程の責任でないのでは?と思ってしまう可能性もありますね。
👨;ああ、そうなんだ。この課題をみんなで考えようと、佐々木さんから提案し品質管理部含め、車体、塗装、組み立てなど各部門から担当者を出してもらって、週に2回ほどミーティングを開始したそうだ。ここで、まさにポイントは、それぞれの部門がしっかりと水漏れ対策をするということ、つまり「自分の工程」で「仕事を完結させる」ということだったんだ。この時、検査をしなくてもいいレベルで水漏れを防ぐ。そんなことが目標だったそうだ。
👱;検査なし?今まであったかつ、複合工程にまたがる不具合を検査なしにできるなんてななかなすごい目標ですね。
👨;ああ、でもそれが本当にできてしまったんだ。
👱;どうやって・・・。
◆水漏れにかかわる2000以上の作業を洗い出す
👨;水漏れの難しさは、それぞれのプロセスが“水漏れに対して悪いことをやっている”という自覚がないことだったんだ。確かに、原因をチェックして、担当部門にフィードバックするが、実際に不具合が起きた作業をしていたのは、何日も前だ。その時にどんなことをして、何が起きたなんてみんな忘れてしまっているんだ。
👱;そりゃ、そうです。。それも発生するのは滅多にないですしね・・。仮に1000回に1度水漏れにつながる小さなミスをしたとしても覚えていないですね。
👨;ああ、例えば溶接なんかは1日400台の作業をする、そして1台に30か所ほど溶接をする。とても覚えてられない。
👱;はい。そして、皆悪気があるわけではなく一生懸命やっているなかで起こってしまうことですしね。。しかるべき手順も踏んでいるはず。
👨;そう。だからこそ、気をつけろという言葉だけで終わってしまっていたそうだ。だから、低い確率であるが一定数発生してしまう。根本対策になかなかつながっていかない状況だった。
👱;でも、何をもってすればちゃんとやったことになるのか・・。わからないですよね。難しいですね。
👨;ああ、でもよく聞いてみると、設備がやりにくい、設計構造上これは難しい、道具がないなどの声が上がったそうだ。そして、そうした声のもとに作業を改善していったのである。一つの「工程」で「完結」するために何が必要なのか一つ一つ洗い出していったそうだ。
👱;ここでも、一つ一つ作業を洗い出すということが重要だったというわけですか。
👨;ああ、細かくはないけどもすべてで2000以上の作業を洗い出したらしいぞ。
👱:それはすごい・・。執念ですね。
👨:執念というか、効果があることを確信していたんだろう。最初は佐々木さんが一部長として取り組んでいたプロジェクトに過ぎなかったんだけど、工場長がそれに目を付けて工場全体に活動が、全体に広がっていったという。そして、取り組みを進めていくうちに興味深いことも起きていったようだ。
👱:興味深いこと??
👨:一つの事例何だけども、鉄板を溶接するプロセスでは火花が散るよな?あれは飛ばさないほうがいい。あれは溶けた鉄が飛散しているのだからね。その溶けた鉄がピンホールを作り水漏れになる可能性がある。
👱;はい。
👨;どうすれば、火花が飛び散らないか、溶接部分に直角に溶接ロボットを充てる問題。さらに溶接チップのの先端部分の問題。ちょうどいい太さがあるそうなんだ。最終的に直角にあてるということと、溶接するたびに先端のサイズを調整する設備を導入して火花を飛ばさいことを実現したそうだ。
👱:なるほど。一つ一つ潰していくと解決しますよね。確かに。
👨;それと、実はその火花は設備は汚すし、車に着くと塗装不良につながるもので元々邪魔者だったそうだ。つまり、水漏れ対策で火花を見直したことで他の面でもメリットがでてきたということなんだ。後工程の塗装工程にもメリットが出ている。
👱:なるほど。すべてはつながっていると。なので、水漏れに関して自工程完結は仕事全体の質を上げたということなのですね。
👨;その通りだ。この活動は一つ一つの作業をきちんと洗い出すという取り組みから始まる。非常に大変だ。だから、最初なかなか受け入れられなかったそうだ。だが、1年続けて2年目に入ってくと声が上がったことが改善されたり、水漏れもゼロになっていないがご利益があることがわかってき現場の空気が大きく変わっていったそうだ。そして、2年目が終わることには多くの部門に広がっていき、水漏れが一気に減っていったそうだ。
👱;すごい。小さなところから徐々に広がり全体に広がっていったのですね。でも2年ですか、なかなかかかりましたね。
👨:ああ、結果は努力と比例するものではないからね。でも積み重ねていくうちにどこかで一気に成果になったりすることが往々にあるよな。自分の方向を信じて、そこまで踏ん張れるかが現場では勝負だ。
👱;はい。
👨;そして、改善されたものは標準化し、現場で定着する活動を新たに進めていったそうだ。そうすることで、自分たちの工程で仕事を完結できる、つまり自工程完結ができるようになっていったというんだ。そして、自分たちの仕事にどんどん自信を付けていくことができたんだ。
👱;なるほど。そして成功体験を得るとその活動がどんどんと広がっていくわけですね。
👨;ああ、そして、活動後、水漏れに関しての活動を全社大会で発表したそうだ。そうしたら、社内で競争が始まり、自分たちもやろうと自工程完結への取り組みが各工場に展開されていったそうだ。
👱;まあ、そこですぐに競争意識が芽生えて発展していくのがトヨタって感じですね。すごい・・・。でも工場には展開したと。
👨;そして、2007年に当時の自動車業界の変化からの危機感も後押しして、スタッフ部門への自工程完結の取り組みが始まっていったんだ。つまりトヨタ全社への波及だ。次回、その部分を解説していこう。
・・・・・・・・・
今回は不可能を可能として水漏れ対策を例に自工程完結を解説しました。やはり地道ですね。作業を洗い出し、徹底的に改善を積み上げていく。なかなかできません。でも、これを積み上げることで連鎖的にメリットが発生してきますね。努力は比例はしないが、積み上げることで一気に成果を上げることがあるというのは、本当に腑におちます。さて、次回はスタッフ部門へこの自工程完結という考え方が展開されていきます。
下記の固定記事に、このnoteのコンセプト、これまでのマガジンについて説明しています。ご興味あればスキ・フォローいただければ嬉しいです。
番外編マガジンもあります。是非覗いてみてください💁♂️
#製造
#理論と実践
#ものづくり
#成長
#5S
#トヨタ生産方式
#ジャストインタイム
#自働化
#リーンプロダクション
#ザゴール
#制約理論
#ドラッガー
#ビジョナリーカンパニー
#アドラー
#コーチング
#情報リテラシー
#要件定義
#会計
#損益計算書
#決算書
#損益分岐点
#原価低減
#平準化
#両利きの経営
#両利きの組織
#心理的安全性
#グーグル
#システム
#発注側
#会社改造
#事業再生
#自工程完結
この記事が気に入ったらサポートをしてみませんか?