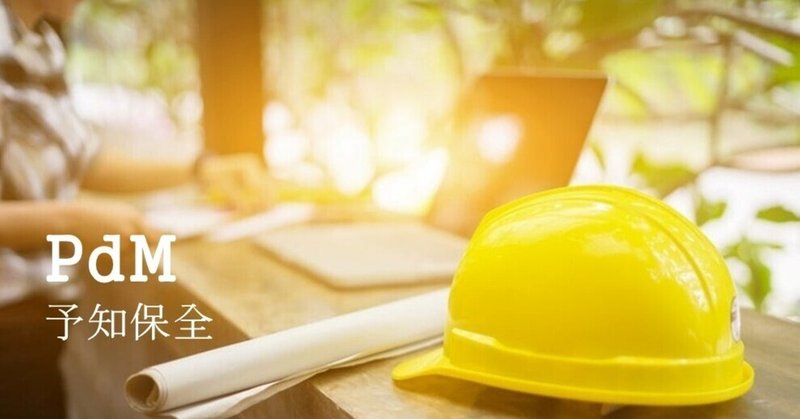
予知保全 (PdM): 産業分野向けIoT・ビッグデータ処理の中心ユースケース
本記事は、予知保全(PdM)に関する記事です。ローカル5G、エッジコンピューティングの普及の後押しを受けて、より広範囲に適用されるであろうソリューションであり、インダストリアルIoTにおける中核となるアプリケーションです。
保全(メンテナンス)にまつわる課題と進化
工場やプラント等、各種施設では、生産設備の経年劣化や多様化、複雑化に対応するコストの増大、熟練技術者の高齢化や減少、若い世代へのノウハウの伝承、環境問題やSDGsへの対応など課題が山積しています。そのため、設備の安定稼働を最大化するためのメンテナンス業務を、これら課題に対応しながらどう高度に保っていくかは、産業分野における重大なテーマになっています。
以前は、工場や施設における機器のメンテナンスといった場合、定期的な点検や、故障が起きたときの反応的な対処である事後保全(Breakdown Maintenance)というアプローチが大半を占めていました。時代と共に、そのような受身的なメンテナンスから、機器の平均的な寿命にもとづいて予防的、計画的にメンテナンスする予防保全(PvM)へと変わり、そして、1990年代以降から機器の故障を予測して対応していく予知保全(PdM)のアプローチが始まり、広く活用されています。
予防保全(Preventive Maintenance: PvM)との違い
予知保全(PdM)は、予防保全(PvM)と混同されることがありますが、予防保全は前述したように、機器の平均的寿命等に基づいて行われる点検・メンテナンスです。
予防保全では、機器のメンテナンスが必要かどうかに関わらず、定期的に実施されるものです。メンテナンススケジュールは、使用状況か時間のどちらかの条件に基づいて設定されます。例えば、暖房機は毎年冬になる前に点検したり、自動車は5,000km~10,000kmごとにエンジンオイルを交換したり、4年に一度タイヤを交換したりします。
予知保全(Predictive Maintenance: PdM)とは
予知保全(PdM)は、予防保全とは異なり、工場内の機械や設備の不具合や故障を予め知り、機械や設備を監視し最適な状態に保つことを言います。
PdMは、通常の運転中に機器の状態とパフォーマンスをモニタリングし、将来のパフォーマンスに影響を与えると予想される問題が検出された場合にメンテナンスを行うことになります。そのため、メンテナンスを最小限におさえてコストを削減しつつ、故障の可能性も低減し、機器の寿命を伸ばします。
(予防保全との対比で行くと、PdMは、予防保全で発生する定期的な部品の交換や修理でまだ使える部品でも交換してしまうといったムダの発生を抑えることができます。)
PdMの適用範囲は、日用品から最大級の産業用エンジンに至るまで幅広く及びます。PdMは、コーヒーマシンやプリンタなどの小さな日常的な機器を監視するためにも有効ですが、高額な機械や装置に利用することのメリットを認識し、工場・施設全体で、ファシリティマネジメント(FM)の中核としてPdMを導入することで利益を得ることができます。これは、工場のスマート化・DXともつながり、インダストリアルIoTの実現に大きく関わります。
効果的なPdMを実現するためには、大量のデータを処理する必要があり、その上で洗練されたアルゴリズムを実行し、正しく故障を予測していく必要があります。そこで、テラバイトにも及ぶデータを保存して必要な機械学習アルゴリズムを実行できるIoTベースのソリューションが導入され、進捗状況を把握し、産業機器が故障するケースの予兆を適切に識別できるようになりました。今日、AI/IoTベースの予知保全システムは、産業になくてはならないものとなっています。クラウド、データレイク、ストリーミングデータ処理、機械学習アルゴリズム、昨今はエッジコンピューティング、とビッグデータ活用の技術群がフル活用されるアプリケーションと言えます。
PdMの利点
PdMの利点は、メンテナンスコストの削減に加えて、計画されたダウンタイムの最小化、装置の寿命の最大化、従業員の生産性の最適化、加えてそれらによってもたらされる収益の増加を含みます。PdMのもう一つの利点は、PdMを実施することにより、機器・設備管理者が結果をもとにしたアナリティクスを行うことで、さらなる収益性の改善につながる最適化の実行ができるようになります。継続的な最適化の実行は、ロバストな工場・施設のオペレーションを作り上げます。
もちろんPdMは計画外のダウンタイムも防止します。Wall Street Journal によると、計画外のダウンタイムの42%は、設備の故障によって引き起こされています。PdMによる、故障を発生させないでコントロールしていくオペレーションにより、計画外のダウンタイムによるビジネス的損失や最悪の場合に発生する事故等による従業員のケガも防ぐことができます。
(PdMによるROI改善の効果に関しては、本記事の最後の部分で述べています。)
PdMを支える検知技術
PdMにおいて、 故障を効果的に予測するためには、現在の状態を的確に把握するモニタリングの技術やソリューションが欠かせません。まず以下ではそれら検知技術について述べます。
画像解析
通常のカメラによる画像解析です。近年、ディープラーニングによる画像認識の精度が極めて高くなったため、安価なカメラとの組み合わせでPdMを実現することも増えました。また、ボアスコープ(工業用内視鏡)を用いた検査や、ドローンやUGVに取り付けたカメラによるモニタリング等も行われるようになり、発展の著しい検知手段です。汎用性の高い技術のため、機械の個々のコンポーネントからプラントシステム、屋根、更には建物全体、橋などに至るまで、あらゆるものを調査するために使用され、PdMを支えます。
赤外線サーモグラフィー
非破壊検査の一つである赤外線(IR)サーモグラフィーは、PdMでも広く使用されています。 赤外線カメラを使用することで、機器の高温(ホットスポット)を検出することができます。
故障した電気回路を含む摩耗した機器は、一般的に熱を発し、熱画像上にホットスポットとして表示されます。赤外線検査は、ホットスポットを迅速に識別することで問題を特定し、コストのかかる修理やダウンタイムを回避することができます。 赤外線技術も、カメラによる画像解析と使用条件は同様のため、同じく汎用性が高い技術となります。
音響モニタリング
音響技術は、機器内のガス、液体、または真空の漏れを検出するのに使用されます。また、回転機械の摩耗なども聞き取り、劣化を予測するのに役立ちます。他にもベアリングの摩耗や潤滑不足、電気期の不良、バルブの漏れ等も周波数の検知によってモニタリングできます。
振動解析
主に高速回転機器に使用される振動解析は、機器に内蔵されたリアルタイムセンサーを使用して機械の振動を監視することができます。ピーク状態で稼働している機械は、特定の振動パターンを示します。 ベアリングやシャフトなどのコンポーネントが摩耗したり故障したりすると、機械は異なる振動パターンを発生し始めます。振動解析によって機器をモニタリングすることで、既知の故障モードと測定値を比較し、問題が発生しうる予兆をつかむことができます。
振動解析で検出できる問題には、ミスアライメント、シャフトの曲がり、アンバランス部品、機械部品の緩み、モーターの問題などがありますが、振動分析での故障の予測は他の検知技術と比べると難しいため、経験豊富な技術者のノウハウと組み合わせて予測モデルを構築(HITL)したり、またオペレーションを設計することが重要になってきます。
オイル分析
オイル分析も、効果的な検知技術です。オイルの状態をチェックし、粘度、水や摩耗金属の有無、粒子数、酸の数や塩基の数を明らかにすることで、異物や汚染物質が混在しているかをモニタリングします。
その他の検知技術
これらの技術の他にも、モーターの運転状態を詳細に把握するモーターの状態解析や、遠心冷凍機やボイラシステム内の管壁の厚さの変化を特定する渦電流解析等の技術を使用することもあります。
PdMプログラムを実現するためのシステム
適切な検知技術と、機械学習による予測モデルに加えて、センサーのデータを統合管理していくデータ管理システムや、また、そもそものCMMS(設備保全管理システム)とのインテグレーションを行っていくことで、PdMプログラムが実現されます。成功を確実にするためには、トータルで機能する仕組みを作り上げていくことが必要です。
PdMプログラムを確立するステップ
従前の予防的・計画的なメンテナンスのやり方から、PdMへと移行することは、時間がかかり、時には複雑さを増すケースがあります。ですが、それによってもたらされる大きなメリットも同時にあるため、これは追求する価値のある旅となります。
PdMを工場や施設内のプログラムとして確立していくには、いくつかのステップが必要です。以下にその項目について記します。
・主要なステークホルダーとのPdMのコンセプトの共有、ゴールの設定
・対象となる機器の棚卸、履歴の分析
・過去の故障記録のレビュー(ダウンタイム、機器の欠陥、機会損失、規制上の罰金等、故障における影響について)
・職場の安全性に関する記録のレビュー
・既存のメンテナンスの現状アセスメント
・棚卸・レビューした情報やアセスメントに基づくPdMのケースの構築
・プログラムのPoC(パイロット)実施のための機器の選定、オペレーションの策定
・主要なステークホルダーとのケースの共有と、PoCの投資判断
・PoCの実行(データの収集と予測モデルの構築、実際のオペレーションとの整合性確認)とその評価
・PdMプログラムの対象範囲・規模の決定と投資判断
・システム化計画の立案とCMMSとの統合
・設備・施設のアップグレード
・オペレーションのためのトレーニング
PdM導入における留意点
PdM導入にあたっては、その対象範囲を見定めます。PdMで管理する対象には、規模の小さなものから順に「部品」「機器」「プロセスライン」「工場・施設全体」とレベルが分かれます。PoCを通しながらも、PdMプログラムの対象範囲をステークホルダーと共有・合意しておくことが大切です。
ところで、上記でも、PoCを行うと書いていますが、PdMにおけるPoCは通常のAIやIoTソリューションにおけるPoCとは異なります。PdMは故障を予知することをもってその機能がきちんとワークしていることを確認するため、PoCにおいてはモニタリングの実施と予測モデルの構築のみもしくは、意図的に不具合を起こす仮のテストが必要となります。
PdMの実際の導入にあたっては、オペレーションのアップグレードが発生するため、管理者および従業員のトレーニングを行います。データリテラシーをも高めるリスキルを行うことが必要となるケースもありますが、工場・施設全体、もしくは組織のデータケイパビリティを高めることにつながります。
PdMは広く見るとデータドリブンでの工場・施設の保全と言えます。適切なデータ収集とその活用はPdMでも肝となる部分ですので、データドリブン経営に関する記事も参考になるかと思います。
また、PdMのコンセプトやユースケースを様々な階層のステークホルダーと共有・議論するためには、AIを経営における意思決定プロセスの中に組みこむためのワークショップ・ツールである「AIキャンバス」が参考になるでしょう。
PdMの応用
PdMは多く製造業の工場やエネルギー産業の施設において活用されています。例えば、石油・ガス会社は毎日、世界中の油田でセンサーを通じて膨大な量のデータを収集し、PdMに活かしています。
エッジコンピューティングの記事で、横河電機のキャビュテーション検知について触れましたが、これは高度なPdMの実装例です。
鉄道業界においてもPdMは応用されます。鉄道車両は初期投資が高いため、できるだけ長く運行を続けることが重要視されています。鉄道会社は、様々な技術やソフトウェアを駆使してPdMを実現し、運行コストを削減して車両の寿命を延ばすことで、車両の価値を最大限に引き出すことができます。
また、ビジネスの高収益化に貢献する応用もあります。顧客先での機械や設備の管理を行うフィールドサービスでは、従前、事後保全・予防保全によるアフターサービスとして行っており、サービスのための人員の確保からROIが低くならざるえないところもありました。しかし、PdMを導入したフィールドサービスでは、ROIの改善が見込まれ、収益の向上も可能になります。
PdMのROI
PdMの導入には、設備、システム(AI/IoT)、人員、トレーニングへの相当の投資が必要です。これらの初期投資は組織にとっては困難に思えるかもしれませんが、回収のためのROIも期待することができます。
デロイトのレポートによると、いくつかの工場・施設では、保守・修理・運用(MRO)にかかる部品の費用を5~10%削減し、全体的なメンテナンスコストも5~10%削減しています。また、米国エネルギー省のデータによると、機能的なPdMプログラムを実施することで、メンテナンスのROIは10倍に増加し、コストが25~30%削減され、故障が70~75%減少し、ダウンタイムが35~45%減少する可能性があることが示されています。国際航空運送協会(IATA) の資料では、PdMを始めとした取り組みにより航空機の稼働率が最大35% 向上し、保守・修理・運用(MRO)コストが15~20%削減されると試算しています。
PdMを成功させ、山積する課題を解決する
見てきたように多くのメリットもある予知保全(PdM)ですが、実現に向けたステップも多く、従来のアプローチより複雑なものになります。PdMプログラムを成功させるためには、いくつかのKSFが存在します。最も重要なのは、データドリブン経営と同じく、組織のトップ・経営陣がPdMの必要性を理解し、コミットメントを表明して現場をサポートすることです。そして、組織全体もその意義を理解し、新しいプロセスを習熟し、新たな知識をリスキルで獲得することが肝要です。
冒頭で述べた山積する様々な課題は時間とともにその深刻さを増し、待ったなしの状況になってきています。課題解決に向けた現状の打破を目指し、データ活用、デジタル化(DX)につらなるものとして、PdMの導入とその成功は極めて重要な取り組みになるでしょう。
References
Coleman, Chris, Satish Damodaran and Ed Deuel. “Predictive Maintenance and the Smart Factory.” Deloitte. 2017. https://www2.deloitte.com/content/dam/Deloitte/us/Documents/process-and-operations/us-cons-predictive-maintenance.pdf
Wall Street Journal. Accessed November 2, 2018. https://partners.wsj.com/emerson/unlocking-performance/how-manufacturers-can-achieve-top-quartile-performance/
この記事が気に入ったらサポートをしてみませんか?