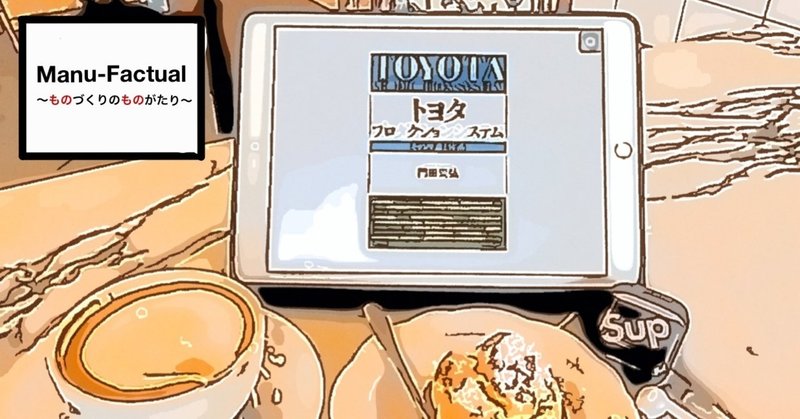
【(追加)トヨタ生産方式/TOC編14;注文が増えたり減ったり。。どうしたらいい?(part1)総量の平準化】
*トヨタ生産方式の一連の解説は、上記マガジンに入れています。
大卒で大手素材メーカーの工場に配属された若手の紫耀(しょう)と同じ工場に転勤してきた別部署の中堅社員の管理者の健(タケル)との会話です。先輩に指導を受けながら、トヨタ生産方式について学び、自部署の課題を解決に挑戦するようです。前回の投稿までで、ジャストインタイムとニンベンのついた自働化、かんばんの運用について学び、それらを使って改善するべき7つのムダについて学びました。
ということで、マガジンを終了していました。が、、終了から約1か月、平準化についての説明不足にモヤモヤしておりましたので、追加で解説させていただきます。2回に分けて解説させていただきます。JITをす実現するにあたって非常に重要な前提になってきますので、新しいマガジンが始まるこのタイミングでどうしても入れたく、挟ませていただきました。
(ですので、次々回からビジョナリーカンパニーになります。)
なお、この投稿は下記の本の4章に沿って解釈をいれながら記載しております。
・・・
◆注文量が増えたり減ったり
🧒;おはよう。突然朝から呼び出してすまん。
👨🦱;おはようございます。全然かまわないですが、どうしました?この間管理会計終わったばっかりですが。
🧒;いや、実は、トヨタ生産方式のところで大事なことを伝え忘れていたんだよ。
👨🦱;だいぶ飛びましたね。ちなみになんですか?
🧒;うん。飛んだ。伝えたいことは平準化だ。
👨🦱;平準化って、JITを実現するための前提条件だってならったやつですよね。
🧒;そうだ。前回JITのところで少しだけ触れただけだったけどすごく重要なところだからちょっと細かく解説するよ。
👨🦱;はい。よろしくお願いします。生産の平準化ですね。確かに困っているんです。生産数量がばらつくと人員変動が大きくて、量が少ないと人を抱えているとコストになるし、数量が多いときは、人が少なくてスループットが上がらないし。ザゴールで、スループットを増やせばいいというのはありますが、それは注文がある際に適応しやすい話ですよね。本当に1直分数量が少ないときはさすがに人員のやりくりを考えないといけないですよね。もちろん、その活用がマネジメントの肝というのはわかっているのですが。
◆平準化の概念
🧒;でしょ。その部分のヒントになるのが「平準化」の考え方なんだ。トヨタ生産方式の究極目的は、コスト低減によって、利益を増大させることだったね。つまり無駄を省くということ。
👨🦱;はい。その中でも不要な在庫を減らしていくことが肝です。これを実現しようとしているのがJITですね。
🧒;その通り、販売面でみる場合、売れる製品を売れる量だけ供給することにすれば実現できる。トヨタの場合、変動する需要に生産を対応させる手段として「生産の平準化」を実施しているんだ。この概念は、製品の流れる量のばらつきをできるだけ小さくすることなんだ。そして、2つの種類があって、「総量の平準化」と「品種別の平準化」がある。今日は量の平準化について話をするよ。
◆総量の平準化
🧒;総量の平準化とは、簡単に言ってしまうと、毎日同じ数量だけ作ることをいう。
👨🦱;なにを当たり前なことを、、それができれば苦労しないですよね。
🧒;でも、今月の数量全体をまじめに1日当たり同じ生産数量にしようって考えたことある?
👨🦱;そういわれると、、生産計画に言われるままに納期厳守目指して作っていて、日々の生産数量に関しては言われたまま作っています。
🧒;でしょ。ちょっとこのまま聞いてくれ。例えば、トヨタで言えば量産車種であるカローラの全体生産計画は、まずその月の予測数量に基づき月単位の生産計画が立てられる。これをその月の稼働日っ数で割ることによって、1日当たりの生産台数を求めて毎日日当たり平均台数だけコンスタントに生産する計画をする。これが「総量の平準化」なんだ。
👨🦱;でも、もし月の半分までは出荷数量が少なくて、後半が多かったらしたらどうするのですか?最初にたくさん作ることになって在庫をためて、そのあと出荷されていく。結局在庫を作ってしまって無駄ですよね?
🧒;そう。だから、「総量の平準化」を実施する際には、生産計画はできるだけ短い期間について立てることが望ましい。2週間であったり、毎週で決めているところもあると聞くよ。
👨🦱;そうなんですが、いやいや、でも短くしすぎたら毎日同じ数量というという総量の平準化ができないじゃないですか。
🧒;まあ、そりゃ限界があるよね。やはり1週間という単位が限界なのではないかな。実際は、1か月単位で決めていくのが一般的と言われている。それでも月次の数量を見てなるべくばらつかないようにしていくのが重要なんだよ。あくまでも、目指すべき概念ということだ。
👨🦱;目指すべき概念ですね。わかりました。もし、販売・計画側で量の平準化を目指したとして、製造として、具体的に何をしていくべきなのでしょうか?
◆全工程での同ピッチ生産、タクトタイムでの生産
🧒;そう。本題はそこだ。製造として何をしなければならないかだ。製造は平準化を達成するためにすべての工程を同じピッチにする必要がある。最終工程が総量の平準化、つまり安定した生産数量を達成して出荷するということだけでなく、すべての工程がタクトタイムに従った生産をしなければならない。
👨🦱;タクトタイム。。。ざっくりは理解していますが、1個当たりの生産にかかる時間ですよね。タクトタイムに従った生産・・。
🧒;そうだ。じっくり行こう。例えば、最終ラインにおけるトータルな日当たり平均生産量で1日の稼働時間数( 480分または960分)を割って全仕様の平均タクトタイム(平均の1個当たりの生産時間)を求める。そして,そのタクトタイム(あるいはサイクルタイム)に従って、工程の人員数の割当をるということを言っているんだ。ただ、もちろん最終工程には部品が必要だ。だから、このタクトタイムに、すべての前工程がピッチを合わせて生産しなければ最終工程の量の平準化は達成されない。だって、部品が同じタイミング来ないんだからね。すべての工程で同じ時間で製品・部品が作られていくイメージだ。
👨🦱:なるほど、タクトタイム理解しました。そして、全ての工程でピッチを合わせなけなければならないこともわかりました。ただ、タクトタイムに従って工程の人員数を割り当てるとはどういうことでしょうか?
🧒:うん。下の表を見てくれ。
👨🦱;おお、これは日当たりの生産計画、総人員、その日の必要人員、そしてライン停止時間、結果としてのタクトタイム(1個当たり流す時間)が書いてあるものですね。
🧒:そう、これはある月の例を示している。ゆっくり、表を見ながら聞いてくれ。生産計画表は1日から15日まではだいたい1日当たり250台であるが, 16日から31日までは200台に減っているよね。このためこのラインに割り当てられた人数は1日から15日までは総人員54名であるが, 16日から31日までは総人員44名である。ところが,3月2日には総人員54名のところ2名の欠員があり,当日の実際人員は52名となっている。
👨🦱;はい。わかります。
🧒;うん。そして、この2名の休みが原因となって,ラインストップが生じ3月2日には1日のトータルで80分のラインストップが生じている。この例では、ラインストップ時間は欠勤する人が増えれば長くなる傾向がある。
👨🦱;わかりました!この場合、1個あたりにかけられる時間によって、そのラインの必要人数が決まってくるということですね。タクトタイムが長ければ、人をかけて早く作業をする必要がないということですね。ちなみにこの表からすると、このモデル工場では半月毎に人員の配置転換がラインの中で行われるように見えますね。
🧒;そう。くどくなるけど、仮に人員が減ることでラインストップが増えるという工程であれば、稼働時間を必要生産数量で割る。そうすると、1個当たりの時間がわかる。その1個あたりの平均生産時間を満たすための人数を揃えるということになるね。
👨🦱:そして、この考えを活用して、需要の変動に人員の変動をどう対応していくかということが重要になってきますね。
◆需要変化に対する人員対応
🧒;需要増加にいかに対応するか。仮に、月に2回生産計画が更新されたとすると、月次の前月後半には,各生産ラインは種類別に1日当たりの生産量を知らされるとする。この場合、日当たりの平均生産量を決める月次計画を受け取った生産工程では,作業、人員をこの計画にに適合させなくてはならない。
👨🦱;作業と人員を適合させるですか。
🧒;トヨタでは、ある機械設備が消化すべき仕事量は通常,その機械設備の能力の90%程度に設定されている。つまり機会としては余裕を持っているんだ。例えば、10台の機会を用意して常に9人で動かしていくイメージだね。とはいえ、その10台の種類が違っていたら、多能工として働く各作業者は9人で10台もの機械を操作しなくてはならないということになる。
👨🦱;そうか、多能工化ができると、10台を9人で動かせるのか。
🧒;そうだ。そして、トヨタや自動車会社の場合、需要が増大すれば臨時工を雇い入れることになる。
👨🦱;おお、そうすると、その場合,各作業者は10台の機械をそれぞれ1人で受け持つことになって機械設備能力の100%活用が可能となるのですね。需要の増加に対応できる。
🧒;そう。でもその時に必要なのは,新規に雇い入れた未熟練労働者でも, 3日以内に機械の取扱いに習熟できるようにしておくことだね。それと個人的に思うのは技能がいる部分は固定しておいて、すぐに作業できる部分を変動できるようにしておくというのがいいと思う。
👨🦱;でも、急にというか短期的にだけ増えたらどうするのでしょうか?
🧒:そういう職場は、中抜き2交代にすべきじゃないかな。
中抜き2交代とは、
通常;朝出7;00-16:00 夜出;19:00-4;00
残業Max時: 朝出7;00-19:00 夜出19:00-7:00
という体制だ。残業で吸収ということになるね。そこにほかの部署から応援を頼む等の対応をしていけばいいと思う。いずれにしろ、短期で教育して配置するということは絶対に必要だね。
👨🦱:量が多くなったときはいいと思いますが、数量が少ないときはどうするのでしょうか?
🧒;その対応はやはり難しい。余裕を持った人員を持つことはNGだから、 まず、1人の作業者が取り扱う機械の台数は増やすことが必須になるね。
👨🦱;それに、1日当たりの数量が少ないのだから、1個当たりにかかる時間、タクトタイムは長くなりますよね。なのでゆっくりでいいから少ない人数で製造すべきということですね。
🧒:そうそう。ここまでは上で話してきたしわかるよね。でも、それ以上減って、いよいよ作るものがない場合どうするか。ここで、トヨタは面白い発想をするんだ。トヨタは,不必要な在庫を生産するよりも,余剰作業者は休ませるほうがよいと信じている。というのよ。取り得る措置としては,次のようなものが代表例として挙げられているよ。
・作業者を別の需要が増大した生産ラインへ配置転
・時間外勤務の削減
・有給休暇の取得
(特に季節的な景気下降期の1月とか8月に集中してとらせる)
・QCサークルの会合
・段取替え作業の練習
・機械の維持,補修
・改善用具の製造
・工場内の水もれの補修
・これまでサプライヤーから購入してきた部品を自社で製造
👨🦱;なるほど。
🧒;ここで、一番重要な目標は,結局工程を改善し,最小限の作業者数で需要に対応できるようにすることなんだよね。そして、ここ超ポイントなんだけど最小限の作業者数という考え方は重要だが,最小限の機械数で需要に対応しなければならないとはトヨタは考えないんだ。むしろトヨタでは,通常,多すぎるほどの機械設備能力を抱えているというんだ。(トヨタプロダクションシステム、門田安弘著 より)
👨🦱;なるほど、設備は十分に確保しておいて、人員を最小にしておく。そして量が増えたらほかの部署から応援を呼ぶ。その事前準備として多能工化しておけばよいのですね。臨時工の仕組みがある会社の方が少ないですからね。最少人数にして、多能工化して各部署のメンバーが移動できるようにしておく、設備は十分に持っておくということですね。
おお、これは自分の工程の管理の参考になります。自分の工程でどこまで適応できるか試してみたいですね。
🧒;その通りだ。ここまでが「量の平準化」とそれを実現するための製造がすべきことの説明だね。次回は「量の平準化」の発展概念である、「品種別数量の平準化」について解説するよ。この話を聞いてから自分の工程に適応していくでもよいと思うよ。
👨🦱;ありがとうございます。では、次回よろしくお願いします。
・・・・・・・・
今回は、マガジンの切れ目ということで、トヨタ生産方式の中で、説明できていなかった平準化について解説させていただきました。「量の平準化」はあくまでも概念で完璧は難しいです。ピッチを同期化し、数量のばらつきのバッファをどう持ち、人員はどうあるべきかについて解説させていただきました。次回は、「品種別数量の平準化」について解説します。ちょっとマニアックな内容かもしれませんが、フォロー、スキしていただけると嬉しいです。
また、下記にこれまで作成した別マガジンを記載します。ぜひ覗いてみてください。
#製造
#理論と実践
#ものづくり
#成長
#5S
#トヨタ生産方式
#ジャストインタイム
#自働化
#リーンプロダクション
#ザゴール
#制約理論
#ドラッガー
#ビジョナリーカンパニー
#アドラー
#コーチング
#情報リテラシー
#要件定義
#会計
#損益計算書
#決算書
#損益分岐点
#原価低減
#平準化
この記事が気に入ったらサポートをしてみませんか?