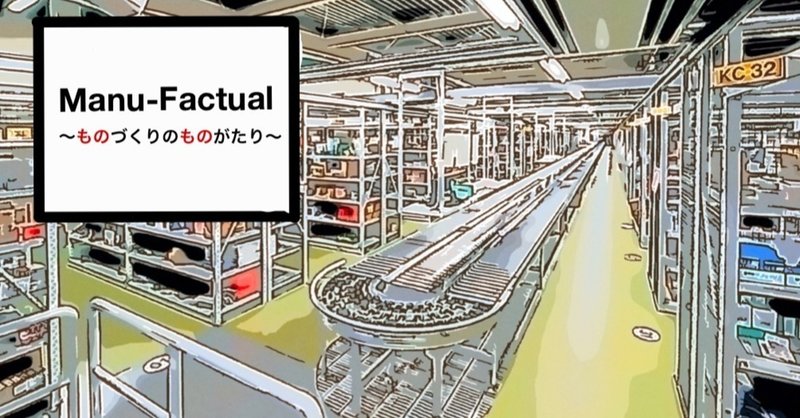
【(追加)トヨタ生産方式/TOC編15;注文が増えたり減ったり。。どうしたらいい?(part2)品種別数量の平準化】
*トヨタ生産方式の一連の解説は、上記マガジンに入れています。
大卒で大手素材メーカーの工場に配属された若手の紫耀(しょう)と同じ工場に転勤してきた別部署の中堅社員の管理者の健(タケル)との会話です。先輩に指導を受けながら、トヨタ生産方式について学び、自部署の課題を解決に挑戦するようです。前回の投稿までで、ジャストインタイムとニンベンのついた自働化、かんばんの運用について学び、それらを使って改善するべき7つのムダについて学びました。
ということで、マガジンを終了していました。が、、終了から約1か月、平準化についての説明不足にモヤモヤしておりましたので、追加で解説させていただきます。2回に分けて解説させていただきます。JITをす実現するにあたって非常に重要な前提になってきますので、新しいマガジンが始まるこのタイミングでどうしても入れたく、挟ませていただきました。
なお、この投稿は下記の本の4章に沿って解釈をいれながら記載しております。
・・・
◆品種別数量の平準化
👨🦱;おはようございます。
🧒;おはよう。今日は、総量の平準化の発展概念の「品種別数量の平準化」について話をするよ。
👨🦱;また、わかりにくそうですね。具体的にはどんなものが「品種別数量の平準化」なのですか?
🧒;OK。例えばさ、カローラには,ボディの型(セダン,ハードトップ,ワゴンなど),エンジン排気量,グレード,変速方法などの組合せによって何千種類という様式があるとのことだ。もし、この最終組立ラインが,自工程の能率だけを考えて,今日はセダンのみ,明日はハードトップのみ,明後日はバンのみ,といった形で流していけば,どうなるかな。
👨🦱;たぶん、セダンの部品を作っている前工程は,今日は仕事はありますけど,明日も明後日も仕事がないです。その他車種の前工程は、それぞれ明日,明後日になるまで仕事がないですよね・・。だから、どの部品のラインも毎日毎日仕事があるように生産計画を立てて,在庫をたくさん抱えるしかないですよね。
🧒;そう。それってトヨタ生産方式の目指している方向と逆になっちゃう。多くの無駄が前工程に発生しているよね。そこで登場するのが、「品種別数量の平準化」なんだ。
👨🦱;おお、それはいったいどんなものなのでしょうか?
🧒;たとえばさ、1か月20日稼働で1万6000台のカローラを作るとする。その内訳をセダン(A品)9,600台,ハードトップ(B品)4,800台,ワゴン(C品)2,400台とすると,1日2直の生産体制では1直当たりにセダン240台,ハードトップは120台,ワゴンは60台作ることが必要になる(下記図参照)。
👨🦱:はい。そうなります。
🧒;つまりさ、1直あたりに品種ごとの必要数量を割り振ることを「品種別数量の平準化」というんだよ。
👨🦱:品種ごとに、必要数量に割り振る。なるほど、必要な分を割り振って、それに必要な1個当たりの加工スピードを算出、それが目標となるタクトタイムになるのですね。
🧒:そう。そして、究極を言うと、品種ごとに製品が平均的に売れていく速度で生産することを目指すってことになるんだ。製造のタクトタイムと売れるスピードが一致していれば在庫はゼロになる。完全な引っ張り式の状態だね。これは1個流しの概念になるね。
👨🦱:そうですね。一つの注文を受けたら一つ作る。それを拡大していく。理想ですね。
🧒;あくまでも目指す姿だ。このように,製品の種類ごとにその月に売れる速度に合わせて作ることを,「製品販売構成比率の平準化」(product sales rate smoothing)というんだ。
👨🦱:そうか。これができると、前工程の生産も追随すればいいから在庫はなくなりますよね?
🧒;そう。総量の平準化で目指した、同ピッチの生産ができるね。このように部品の引取り量あるいは使用量を平準化させることを,「部品使用の平準化」(partsusagesmoothing)というんだ。
👨🦱;そうなのですね。つまり、最終工程のゴールでの、「製品販売構成比率の平準化」を目指し、そのために連動する前工程で「部品使用の平準化」を行うという流れですね。
🧒;ここで、先ほどの図をもう一度みてみよう。ここで,タクトタイム(1個当たりの平均生産時間)は1直つまり480分当たりの生産量によって1直の時間480分を割ったものである。この計算結果によるとA品は2分に1台生産されればよく,B品は4分に1台生産されればよい。平均すると1.14分で1台生産されればよいのである。これが品種別数量の平準化を満たすための、それぞれの品種の生産スピードになるんだ。さっき君がいった通り、これが生産目標の目安になるよ。
◆3つの平準化の調整
👨🦱:おお、ということは、生産計画の度にすべての品種のタクトタイムを設定、そのタクトタイムに沿って生産していけば在庫はおのずと減っていく。それが、理想の1個流しに近づくということですね。
🧒;そう。でも、現実はそこで、生産の順序を決めなきゃいけないよね。
👨🦱:そりゃそうです。
🧒;さっき話したように、前提として平準化生産の最も基礎的な意味は,その月によってそれぞれの製品が売れる平均速度(上の表を使えば、,A品は2分に1台,B品は4分に1台,C品は8分に1台売れるなど)にあわせてそのスピードで1個ずつ作っていくということである。つまりタクトタイムにあわせてものを作る「製品販売構成比率の平準化」だといったよね。(部品使用の平準化も付随)
👨🦱;はい。それはわかりました。
🧒;そして,平準化生産にはもう1つ重要なポイントがある。品種によって難しさが異なることから発生するポイントなんだ。トヨタでは,同一ラインで流す各種の車の組付け工数を層別して,工数に関して大中小の3グループに分けている(これをトヨタでは,赤白黄と呼んで層別する)。
👨🦱;難しさ、、組付け工数?
🧒;工数って、人×時間を指すね。つまり組み立てのために何人でどの程度の時間がかかるかということを、3段階に分けているんだ。
👨🦱;なるほど。
🧒;そして、この工数大の車,工数中の車,および工数小の車をうまくバラつかせて平準化して流そうとするんだよ。これを「組付け工数の平準化」(work load smoothing)という。
👨🦱;時間と人がかかるもの、そうではないものを、組み合わせて計画を作るのですね。
🧒;そうそう。例えばある複数工程がつながっている場合を考えた場合。下記がある前工程での組付け工数の図と考える。A品が70秒,B品は50秒,C品は60秒である場合には,この図のようにA-B-C-A-B-Cといった順に流すならば,全工程工程トータルの平均タクトタイムが60秒の場合、この工程の後工程はラインはストップしないのである。常に平均60秒での供給に間に合うことになる。
ところが,(程度によるが)、次の図にみられるように工数大の製品Aがダンゴになって流されると,トータルのタクトタイム60秒が平均のこのラインでは、タクトタイム内に処理しきれなくなって後工程がラインストップを起こしてしまうのである。ラインストップを起こさないためにはピーク作業の70秒の製品Aをより短いタクトタイムで処理できるように,人員増とならざるを得ないであろう。
👨🦱:自分の工程でまとめづくりして効率を上げようとしても後工程を止めてしまうのですね。なので、タクトタイムをベースに全体平均のタクトタイムに送れないための生産順の組み合わせを行うのですね。
🧒:これを「組付け工数の平準化」というんだ。
👨🦱;なるほど、でもいっぱい平準化が出てきているのですが、
①「製品販売構成比率の平準化」,
②「部品使用の平準化」および
③「組付け工数の平準化」
の間には,どういう関係があるのでしょうか?整理したいです・・。
🧒:そうだね。①と②の間には正の相関があることは,これはシミュレーション実験によって十分照明されているようだ。①②と③の間には,コンフリクトが生ずることも多く,両者の調整が必要となる場合があるよね。だって、市場がほしいと言っている製品があって、それが売れるスピードと組付け工数は異なるからね。どちらかを平準化したらどちらかに負荷がかかるよね。実際はこのバランスが重要になってくるよね。
👨🦱;そうですね。実際品種がたくさんあった場合、タクトタイムをそれぞれで計算しなければならないし、売れるスピードと製造スピードは一致しないので、それを割り当てるって生産計画が大変ですよね。そこはトレードオフがでますね。
🧒;そう。なので、ここのすり合わせに関しては専門のシステムが通常必要になるよ。ただ、そのシステム導入前には標準化の概念が頭に入っていないといけない。要件定義だね。
👨🦱;なるほどです。わかりました。
◆平準化生産の要約
🧒:生産の平準化は一般的にいうと,生産におけるモノの流れる量のバラツキをできるだけ小さくすることなんだけど、厳密にはジャストインタイムの目的を実現するために,以下の3つの具体的な下位目標に応じて3つの平準化生産の概念がある。(本には4つ記載されているが本質的には下記3つなのでそれのみ記載)
(1)最終製品が最終組立ラインから生産されて販売市場に出ていくにあたり,各種の製品が市場で売
れる速度(1単位売れるための製品種類別の時間)に応じて生産すること。いいかえると、1日当たり(あるいは単位時間当たり)における各種製品の平均販売数量だけを毎日(あるいは毎時)コンスタントに生産すること。このことによって,最終製品の販売市場における余分な製品在庫を極力なくすことができる。これは,「製品生産の平準化」とか「製品販売構成比率の平準化生産」という。
(2) 最終製品を構成する各種の部品や原材料の使用量のバラツキをなくして、部品や原材料の在庫を極力小さくすること。これは「部品使用の平準化」である。ジャストインタイム生産では,かんばんによる「引っ張り方式」を用いるために,この目標が4つの平準化目標のうち最も重要である。
(3) 最終製品を組み立てる最終組立ラインにおいて,各種の製品の組立時間に大小があるために,長い組立時間を要する製品が連続してラインに投入されるとライン停止が生じてしまう。これを防ぐ目的で、組付工数の違う各種製品を均等なバラツキをもってラインに投入しなければならない。これは「製品工数の平準化」である。
(3)
👨🦱;なるほど・・。
🧒;上のような3つの平準化目標のいずれも達成するための意思決定事項は,最終組立ラインにおける各種の最終製品の投入順序をどのように決めるかということであるよね。これは,「混合組立ラインにおける製品投入順序計画(スケジューリング)」と呼ばれる問題になるんだ。
これは、だいぶ細かい話だから時間があるとき別で話そう。
👨🦱;なるほどです。ありがとうございます。
🧒;これで平準化の追加説明は終わりだ。総量の平準化と品種別数量の平準化についてわかってもらえたかな?
👨🦱:正直、わかったようでわかっていないところがあるで、実践しながらまた本を読んで勉強をしたいと思います。でも、下記のように思いました。
総量の平準化のポイント:
設備はキャパを持っておいて、人員は最小化しておく、そして生産量が増えた際には人員を増員させる。そのために、数日から1週間程度で教育できる仕組みを作っておく。また、各工程の中で技能がいるポジションとそうでないポジションを明確に分けて置き、増員されたメンバーは技能が不要なポジションに回すようにする。それにより、数量の絶対値に対応してく。
品種別数量の平準化ポイント:
まず、「製品販売構成比率の平準化」、「備品使用の平準化」を可能な限り行う。(*注意:受注量が少ない時でも、ここで設備キャパは変更しない。設備キャパまで落とすとスループットが減って逆に悪方向に行きます。総量の平準化の概念で、人と残業での増加幅は、もしくはコストアップを考慮しながら、余裕幅をつくること。この重要性を同じマガジンのTOC(ザゴール)編で、記載してます。)そして品種をすべての工程で分解し(製品別)そのうえで、全ての品種に対してタクトタイムを設定する(組付け工数の平準化)。そして、受注している品種構成とタクトタイムを確認し、システムを使って増員せず、工程が止まらない、常に平均タクトタイム以内で製造ができる計画を立てる。(システムに関しては今回言及せず、販売スピードと品種別生産スピードが完全一致は不可能でトレードオフは生じる。こればかりは、実践で調整するしかない。)
🧒;今回はそこまでわかっていればOKだよ。また時期が来たときに具体的な事例を紹介するね。いつになるか・・・だけど楽しみにしててくれ。
・・・・・・
今回は、品種別数量の平準化について話をしました。うまく解説できたか不安ですが、よくわからなかったら、上で添付した門田さんの本を読んでもらうか、ポイントの部分だけ覚えておいて、平準化が必要な時がきたら再度ポイント読んでいただければ幸いです。これで、トヨタ生産方式/TOCへの追記投稿は終了します。また、追加内容があったら随時投稿します。
明日からビジョナリーカンパニーの解説に入っていきます。フォロー、スキどうぞよろしくお願いいたします!コメントも待っています。
また、下記にこれまで作成した別マガジンを記載します。ぜひ覗いてみてください。
#製造
#理論と実践
#ものづくり
#成長
#5S
#トヨタ生産方式
#ジャストインタイム
#自働化
#リーンプロダクション
#ザゴール
#制約理論
#ドラッガー
#ビジョナリーカンパニー
#アドラー
#コーチング
#情報リテラシー
#要件定義
#会計
#損益計算書
#決算書
#損益分岐点
#原価低減
#平準化
この記事が気に入ったらサポートをしてみませんか?