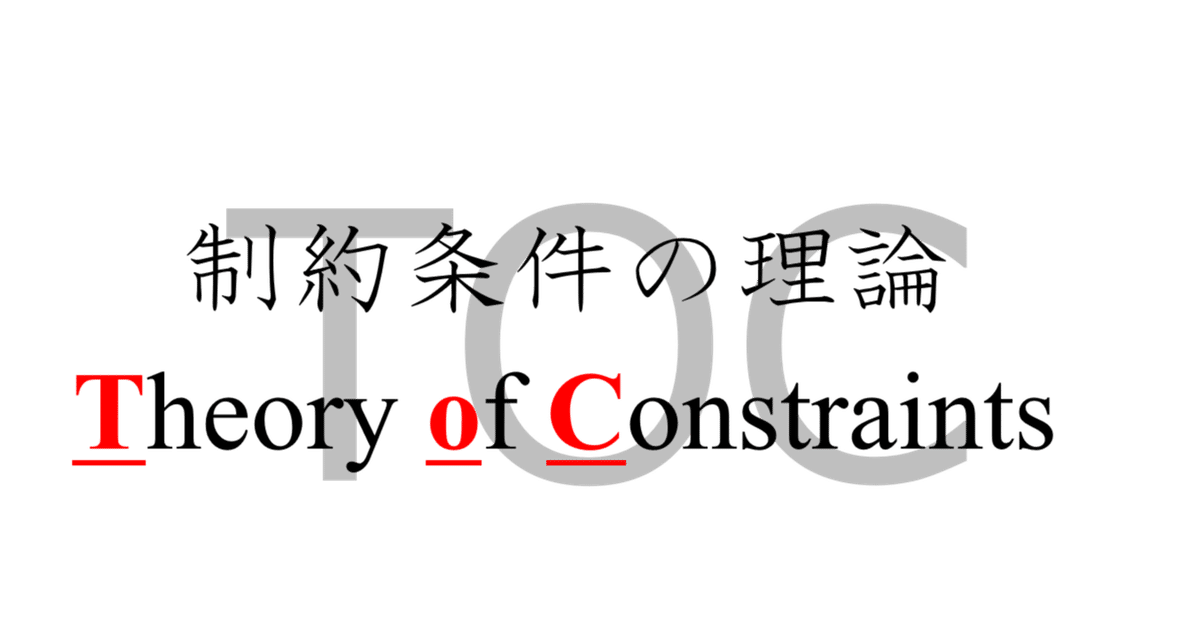
生産理論について:TOC(後編)
前編に引き続き、制約条件の理論(TOC:Theory of Constraints)について書きます。トヨタ生産方式(TPS:Toyota Production System)とも関連させていますので、ぜひご覧ください。
4. ボトルネックの発見→活用→強化→管理のサイクル
「ザ・ゴール」によると、在庫と業務費用を削減しながら、市場の求めるスループットを向上するためには、ボトルネックの発見→活用→管理→強化のサイクルを回すことが重要と書かれています。
ですが、私は「ザ・ゴール」で説明されている「活用」と「管理」が同じに見えてしまったのと、以下のブログを拝見して、製造業的には以下の方が理にかなっていると感じ、非常に分かりやすかったため、ボトルネックの①発見→②活用→③強化→④管理の流れで説明します。
①ボトルネックの発見
まずは、現状を把握することで、ボトルネックを発見することがスタートです。工場においてボトルネックを見つけるためのヒントは、工程前の仕掛品の多さ、つまり、モノの滞留が起きている場所です。また、別の視点では、外注部品のリードタイムの長さが挙げられます。
例えば、トヨタグループ全企業にTPSが浸透しているといった強力な生産思想の共有がない限り、外注先のリードタイムコントロールは困難と想定されます。リードタイムが長ければ、その部品が必要な作業までに部品が揃わず、次の作業がスタートできない場合が考えられます。
②ボトルネックの活用
ボトルネックが見つかったら、ボトルネックを活用します。遠足、マッチ棒のゲームからも明らかなように、ボトルネックが生産できなかった分だけ、工場全体のスループットが下がります。つまり、ボトルネックがスループットを律速していると言えます。ボトルネック活用のためには、以下が挙げられます。
ボトルネックを止めない(ボトルネックだけ2直、3直制にして常に稼働させる)
ボトルネックを通過する部品の優先順位付けをする(ABC分析により、A分類:特急、B分類:準特急、C分類:普通、のように管理の緩急をつける。特急品は優先的に対応する)
ボトルネックとなる外注部品を管理する(外注先のリードタイムから逆算し、その部品が必要な作業の開始までに部品集結が可能なよう、外注タイミングをコントロールする。TPSでの「手待ちのムダ」の排除に該当)
ボトルネックで必要以上にモノをつくらない(TPSでの「つくり過ぎのムダ」の排除に該当。カンバンによる仕掛品の工程間滞留量の規制、小ロット流し、シングル段取りの適用)
ボトルネックに不良を流さない(ボトルネックが不良を生産したら、手直しにより、コスト増が二重でのしかかる。TPSでの「不良をつくるムダ」の排除に該当。自工程完結を徹底的に行います)
③ボトルネックの強化
次にボトルネック自体の能力を向上、すわなち、ボトルネックを強化します。あらゆる手を使って、ボトルネック工程の能力向上を目指します。ここで威力を発揮するのがIE(Industrial Engineering)です。日本IE協会では、以下のように定義されています。
IEは、価値とムダを顕在化させ、資源を最小化することでその価値を最大限に引き出そうとする見方・考え方であり、それを実現する技術です。
仕事のやり方や時間の使い方を工夫して豊かで実りある社会を築くことを狙いとしており、製造業だけでなくサービス産業や農業、公共団体や家庭生活の中でも活用されています。
個人的には、「必要最小限のリソースで、最大限の能力を引き出すこと」と理解しています。
「ザ・ゴール」の例を挙げると、ボトルネックの加工工程の処理能力向上のために、すでに導入済みの最新の工作機械に加えて、倉庫に眠っている古い工作機械を使えるようにした事例があります。
これは、TPSでの「加工そのもののムダ」を排除した改善と考えられます。最新の工作機械を追加導入するまでもなく、所望の品質を満たせる工作機械であれば、古くてもちゃんと動けば大丈夫ということです。
また、熱処理工程では、熱処理中に他の部品の前準備を完了させることで、外段取りの内段取り化を行っています。これは、TPSでの「段取りの改善」に当たります。
さらに、今までは異なる熱処理条件で行っていた部品を、切削加工の条件を見直すことで、同一の熱処理条件でバッチ処理できるようにし、炉への投入回数削減を実現しています。
以上のように、知恵を振り絞り、さまざな工夫を適用することで、ボトルネックの能力を高めていきます。
④ボトルネックの管理
ボトルネックを強化し続けると、そのボトルネックに次いで能力の低い工程がボトルネックになります。つまり、新たなボトルネック工程が誕生し、ボトルネックが工場のあちこちに移動し始めます。
理想論では、ボトルネックが常に同じになっていると、管理がしやすいです。しかし、一般的には、市場の求めるスループット以下の工程は複数存在することが多いと思われます。
まずは、最大のボトルネックに手を当て、次に現れたボトルネックを発見し、活用し、強化し、のサイクルを繰り返すことで、工場全体のスループット向上につながります。
5. ドラム・バッファ・ロープ
ボトルネックの発見、活用、強化、管理のサイクルを経て、スループット向上を目指しますが、同時に在庫、業務費用削減も達成しなれけば利益創出は叶いません。
ここでは、ボトルネックをペースメーカーにした「つくり過ぎのムダ」「在庫のムダ」「手待ちのムダ」排除について説明します。
ボトルネックをペースメーカーとして、すべての工程の資材(素材、仕掛品、完成品)投入の合図を出す「ドラム」、納期を時間で保護する「バッファ」、早すぎる資材投入を防ぐ「ロープ」、合わせて「ドラム・バッファ・ロープ」と呼びます。
①ドラム
ボトルネックのペースに合わせれば、設備の稼働率を必要以上に上げて、モノをつくり過ぎることはなくなります。擬人化すると、ボトルネック工程がたたくドラムのリズムにしたがって、各工程にモノが投入され、作業が進みます。これによって、素材、仕掛在庫、完成品在庫のすべてが必要最小限に保たれます。
②バッファ
在庫を必要最小限に保つと、予期せぬアクシデントによって納期が守れない可能性がでてきます。そのため、製品リードタイムから逆算して、ボトルネック工程とその前工程の間に時間的余裕を設けます。
③ロープ
先頭工程がボトルネックよりもスピードを上げ始めても、ボトルネックが制約をかけます。まるで、先頭工程が犬、ボトルネック工程が飼い主の関係のように、犬が突っ走っても、飼い主がロープを引っ張って進み過ぎを制限します。(この例えは、飼い主が犬の引っ張る力に負けないことが前提です。力の強い大型犬は大変ですね・・・)
このドラム・バッファ・ロープはTPSの「カンバン」と同じと言えます。TPSでは、カンバンを各工程でやり取りしていますが、TOCでは、ボトルネック工程がカンバンを発行し、各工程とやり取りをするイメージだと思います。
ここで、前編 3. ボトルネックの発見で突っ込んだ内容に対して、答えが出そろったと思いますので、以下に回答します。
「いやいや、そもそもボトルネックを先頭に持ってくる工程設計は可能なのか?」→ 物理的に持ってくることは不可能でも、ボトルネックをペースメーカーと考えれば、「先頭に立つ=指揮官となる」ことは可能です。
「彼がボトルネックを脱し、さらにスピードアップしたら、今度は他の誰かがボトルネックになるのではないか?」→ 新たなボトルネックを発見し、活用、強化、管理のサイクルを繰り返します。
「次の能力の低い人が、スピードアップした彼にキャッチアップすることで業務費用を使い、在庫(隊列が伸びる)が発生するのではないか?」→ 上記、ドラム・バッファ・ロープの考え方を適用します。
6. まとめ
これまでの説明を図にまとめました。TPSの7つのムダ排除と関連付けて表現しました。
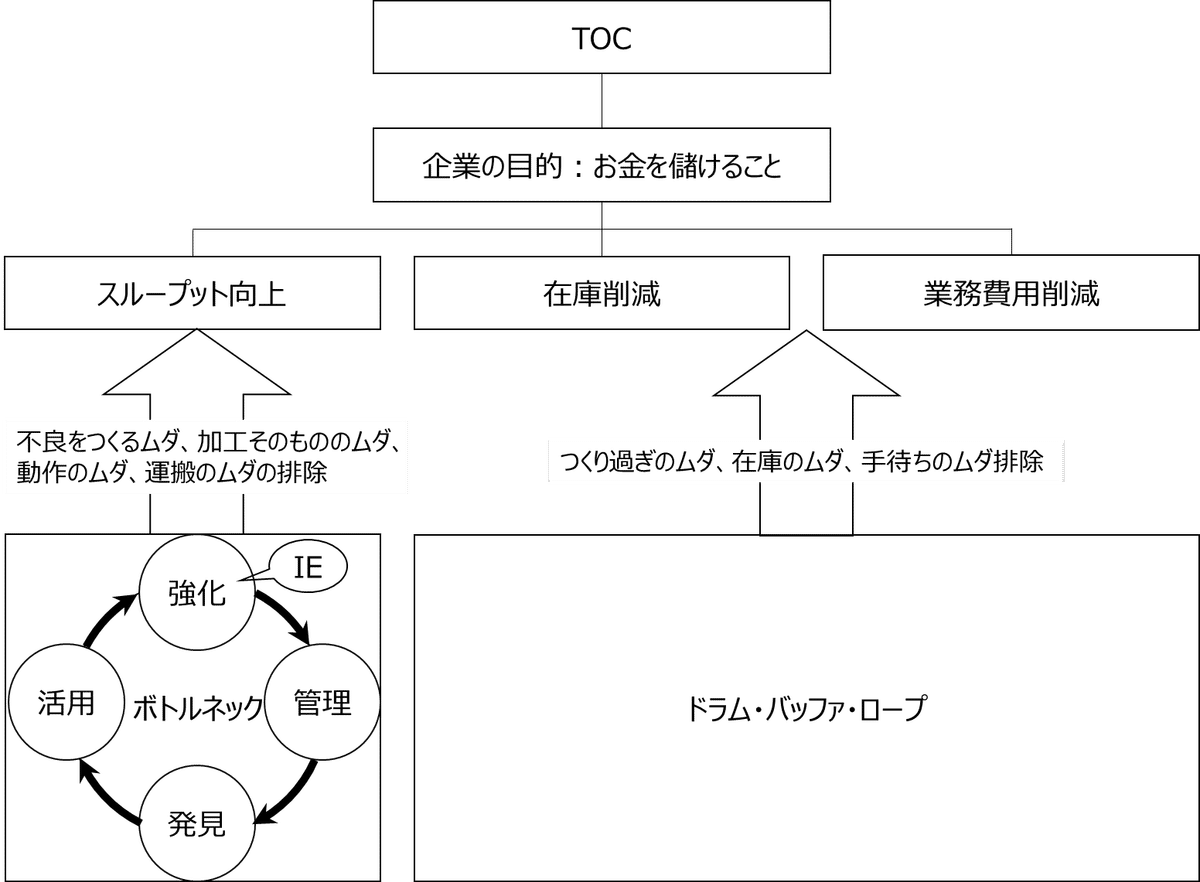
7. 所感
このブログ執筆前からずっと思っていたのですが、TOCとTPSは考え方がかなり似ていると思います。個人的には、TOCはTPSのさらに上位概念にある気がします。
TPSは製造現場から生まれたため、自然と製造現場のオペレーションに近い内容となり、TOCは物理学者の視点、つまり、アカデミックな世界から誕生したと考えれば納得感があります。
TPSは製造現場から製造現場以外(事務処理や日常生活への展開)へ、TOCはアカデミックな世界から製造業といった実務の世界へ発展していった、つまり、スタートは違ってもゴール、目指すべきところは同じと言えそうです。TPSと同じく、TOCの専門家や実際に生産に活かされている方がおられましたら、是非フィードバックをいただけたら幸いです。
8. 参考文献
以下、本ブログ執筆にあたり、参考にした書籍になります。
この記事が気に入ったらサポートをしてみませんか?