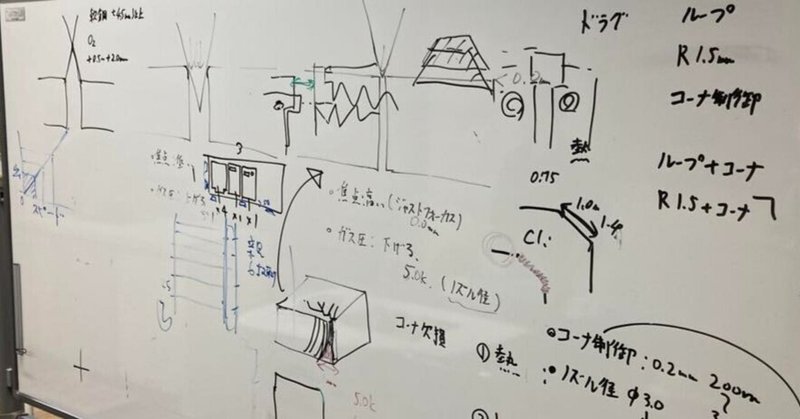
複雑だけど面白い、レーザー加工機の加工条件出しのはなし。
こんにちは、製造部の松田です。
当社で切断加工に用いているレーザー加工機は、
レーザーの熱で素材を溶かすことで物を切断します。
すなわち素材の融点以上の温度になるまで
レーザーの熱を与えてあげないと切れないわけです。
しかも、詳しくは後に書きますが、
素材に熱を加えすぎてもダメなことも多く、
要するに”ちょうどいい”程度に熱を加えないと
工業的に良いものづくりにならないわけです。
この”ちょうどいい”程度になってくれる
設定値のことを「加工条件」と呼びます。
今回は、この加工条件を切り口に、
レーザー加工機について覗いてみましょう。
熱が足りなくてもダメ、与え過ぎてもダメ
冒頭にも書いたように、
レーザーは熱で溶かすことで
ものを切断加工します。
そのため熱が足りないと切り切れずに、
素材が中途半端に溶けたり焦げたりする
とてももったいない結末をむかえます。
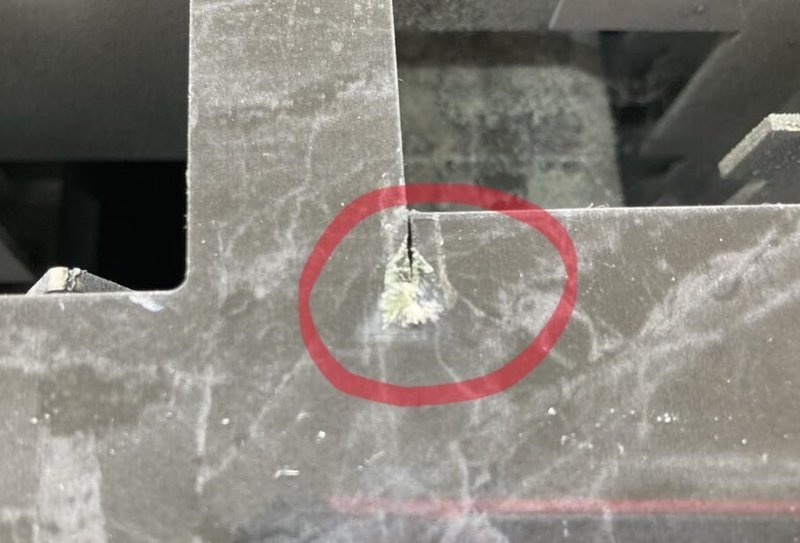
溶融物が表面に吹き上がってしまっている。
しかし、実は熱を与えすぎるのも考え物なんです。
熱を十分に与えると、切断することは確かにできます。
しかし、例えば金属板をイメージすると、
金属は温められると伸びます=長さが変わる、
高温だと酸化しやすくなります=物性が変わる
そのため製品にするには適さなくなってしまいます。
しかも!金属のように熱膨張でも
破断しない素材はまだ良いです。
熱膨張するとすぐにヒビが入ってしまう
セラミックやガラスはすぐダメになります。
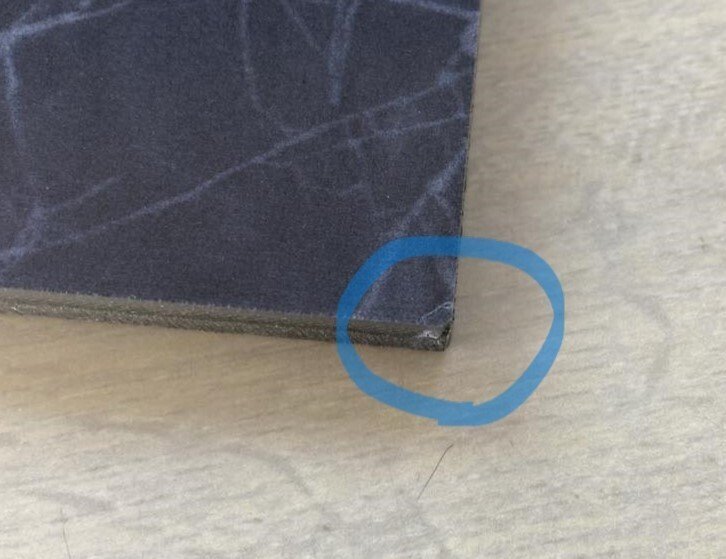
熱膨張などにより素材に欠けなど不具合が出ることを
「熱影響」と呼んだりすることが多いです。
要するに、熱は足りなくてもダメだし
与えすぎてもダメということになります。
熱を与える"ちょうどいい"領域を探る
それが「加工条件出し」!
必要十分な熱を与えながら切るために、
どんな条件でレーザー加工機を走らせるか、
設定値をいじることを「加工条件出し」といいます。
機械の操作盤(電光スクリーン)に映し出された
いろいろな数字に値を入力していって、
「こういう条件で切ります」と機械に指示します。

加工条件における変数は主に6つ!
検討できる組み合わせは膨大に…
レーザー加工機のメーカーによって
若干の違いはあるとは思いますが、
加工条件出しのために使用できる変数として、
焦点の深さ
切断速度F
切断出力W
アシストガスのガス圧
ノズルの径および高さ
Dutyおよび周波数Hz
の6種類をいじって最適な条件を模索します。
それぞれについて説明しましょう。
【焦点の深さ】
小学校のころ、理科でレンズの集光について勉強しませんでしたか。
太陽の光で紙を燃やす実験などした経験があるかと思います。
レーザー加工機も同じくミラーで集光して熱を発生させます。
素材の厚みのどの程度を狙って光を集めるのかによって
加工時の熱の加わる早さと領域がかなり変わってきます。
素材の表面ちょうどに焦点をもってくる場合は
俗に「ジャストフォーカス」なんて読んだりします。
【切断速度F】
文字通り、切断する=レーザーを動かす速度のことです。
単位はF(mm/分)で表します。
F値が高いほど素早く切断することになるため、
生産性に加え熱影響を抑えることができます。
一方で、十分な熱を与えるまえに通り過ぎてしまうと
切りきれないという状況になってしまいます。
【切断出力W】
切断する力のことで、値が高いほど熱量が大きいです。
FとWはセットで加工条件出しをすることが多く、
Fを高めたい→Wを高めるといった方向性や、
Wを低くしたい→Fを下げるといった方向性で
条件を調整することが多くあります。
【アシストガスのガス圧】
レーザー加工機は単にレーザーを出すのではなく、
レーザーによる切断をより効率よく行うため、
レーザー光の周辺にアシストガスと呼ばれる
気体を噴射させて切断加工をしています。
アシストガスには主に空気、酸素、窒素の3種があり
切断する素材によって最適なものを使い分けます。
このアシストガスをどのくらい強く噴射するか、
それをガス圧の値で操作します。
ガス圧が高い方が切断による熱をすばやく冷却でき、
また溶融物であるドロスを吹き飛ばす効果が期待でき、
裏面などバリ取りが容易になるという利点があります。
【ノズルの径および高さ】
レーザー光はノズルの先端の穴から出ており、
レーザー光の周りの穴からアシストガスが噴射されます。
ガスの噴射効率を高めたりあえて低めたりする場合は
このノズルの径と高さの値を操作します。
ノズルの径とは先端の穴の大きさのことです。
穴の大きさが大きい方が、ガス圧が高い場合でも
安定してアシストガスを噴射しやすくなります。
ノズルの高さについては、例えば高さ=0に設定すると、
アシストガスは切断された箇所から排出されることになり、
冷却等の効果は高いですが機械が暴れるリスクが高いです。
逆にノズルが高すぎるとアシストガスが横から漏れやすく、
期待した冷却等の効果が薄れてしまいます。
【Dutyおよび周波数Hz】
マイナーなのでここでは省略します。
加工条件出しについてまた特集する機会があれば
そこで詳しくお話ししたいと思います。
一般的には、焦点→F&W→ガス圧→ノズル径
の順に検討することが多いとされます
加工条件出しではやみくもに6変数をいじるのではなく、
この変数から確定してゆくのがよいという
変数の優先順位があります。
一般的には、
焦点の深さが一番影響度が大きいとされ、
次にFとWを、一方を固定してもう一方を修正する方法で検討し、
ガス圧を低いものから徐々に上げて最適を探し、
最適なガス圧の効果を実現しやすいノズル径を当てる
の順番で検討したら上手くいくことが多いとされます。
もしかしたら他社さんのノウハウでは
ガス圧よりもノズルの高さの方が大事!
というやり方をされている所もあるかもしれませんが、
加工条件出しにおいて最重要は焦点という点は
どんな素材を加工する会社でも共通化と思います。
おわりに
ここまで記事をお読みいただきありがとうございました。
どんな加工機にもあてはまる当たり前の話ではありますが、
レーザー加工機も単に買ったからといって、
切りたいものを何でも綺麗に切れるわけではなく、
まず切りたいものの素材に適した
加工条件出しをする必要があります。
上記の6変数をいろいろいじって~…というのを読むと
なんだか面倒で大変そうという印象を受けるかもしれませんが、
鉄やステンレス、アクリルなどレーザーで切る主要な素材は、
実は加工機に条件がデフォルト登録されていることもあります!
しかし逆にいえば一般的でない素材を切る場合は
十中八九、加工条件出しをする必要があり、
デフォルトにあるレベルの条件しか経験がない場合は
条件出しのノウハウがなく参入ができないわけです。
当社では、例えばガラス層にセラミックといった
複数の素材が重なっている「複層材」と呼ばれる
ジャンルの材料をレーザー切断することも多いですが、
これらは全て当社で加工条件出しを1からしています。
ノウハウの有無がある種の参入障壁になってくれているわけです。
◆建築資材の製造外注・OEMは北陸マテリアル株式会社に!◆
▼▼▼その他の記事も是非!▼▼▼
この記事が気に入ったらサポートをしてみませんか?