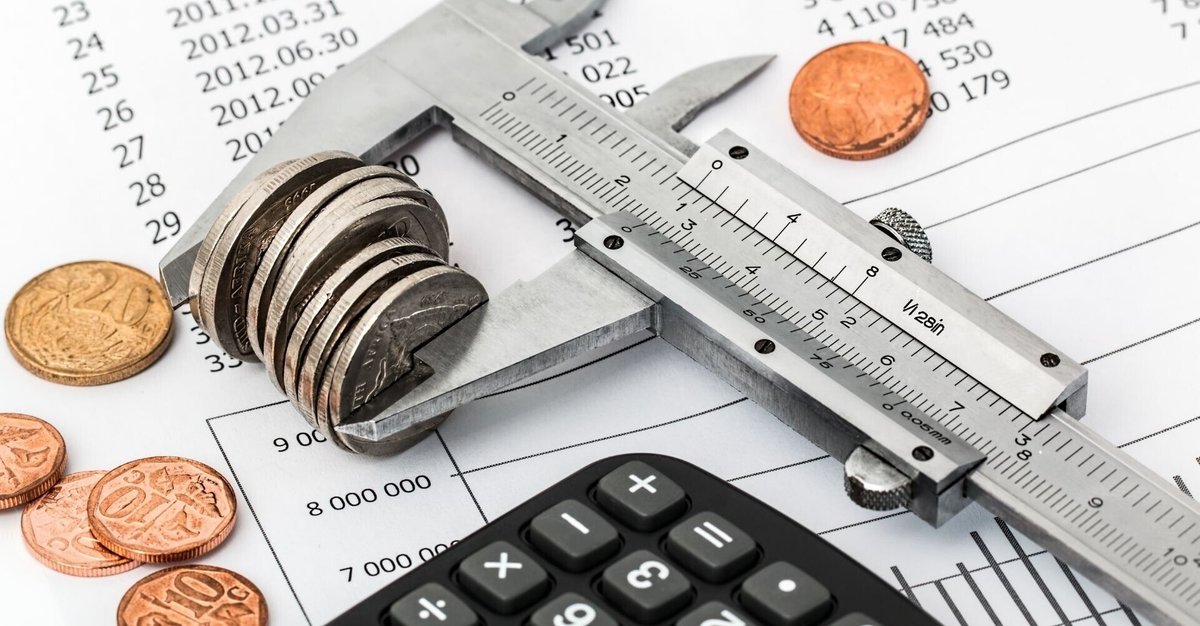
生産管理システムを勉強してみた#11(最終章)
新しいキャリアに挑戦予定
すぐに戦力になれるように生産管理システムについて勉強を開始
1日1章ペースを維持し約2週間でついに最後の章です!
ここまで来るとだいぶ生産管理システムの概要と詳細が分かってきました。
結局生産管理システムの導入が難しく、なかなか進まない理由は第1章にも記載がありましたが以下の7つほどに分解できるかと思います。
<生産管理システムが難しい理由>
①生産管理システムは工場(会社)全体に関連する幅の広いシステム
②ゆえに、スコープが決まらない
③最もコアとなる生産計画サブシステムは顧客の業種・業態で多岐にわたる
④ゆえに、生産計画サブシステムの標準化(パッケージ化)が難しくカスタマイズ化され、導入期間・コストともに膨大となる
⑤各顧客の業態・業種と合わせてスコープ対象(例:生産計画+在庫管理など)の現場オペレーションを把握する必要がある(ベンダー側も)
⑥システム導入に向けた調整作業が多く、目的がぼやけやすい
⑦導入してみたものの要件定義が甘く、運用できない
難しい理由が明確になったら成功させる要因も絞れます。
<生産理システムの導入を成功させる重要項目>
①生産管理システムの全体像を関係者全員が理解し、スコープを決める
②現在の課題を明確にし、どのサブシステムに関係が深いかを決定する
③課題を解決することでどんな成果を得たいかを決める
④成果を関連する部門でKPIに落とし込む
⑤KPI達成に向けて運用する人(現場)に目的を共有する
⑥生産管理システム導入によって見える化した指標を共有しカイゼン活動のタネにする(現場レベルで自分事化)
この本をまとめての最終的な所感です。第1章の冒頭にも追加しておきます。
参考図書
「第10章 生産管理から考える在庫と在庫管理」の振り返り
第10章は在庫に関する概要と、その削減目的の明確化の説明でした。ただ闇雲に削減してBSをスリムにするのではなく、目的を明確しそのための活動を明らかにすることが詳細に説明されていました。
第5章から続けている以下の全体振り返りもテンプレートとして載せておきます
―――――――――――――――――――――――――――――――
第1章 生産管理システムが漠然としている背景
第2章 製造業の業態と流れる情報(滞りがちな情報)の整理
第3章 生産管理システムを重要要素で分解し、ユーザーの業態要素との組み合わせ方
※第4章以降は、3-1の生産管理は7つの主要機能で考えるをイメージするとよいです。
第4章 生産計画をコアとした時の、販売管理サブシステム(特に受注)と購買管理サブシステムとの関係(EDI機能含む)
第5章 コアとなる生産計画の作成ステップと攪乱の考慮
第6章 基準生産計画に含まれる製品の生産計画と必要部材を確認して製造指示への落とし込みを実施するMRP
第7章 生産管理システムの土台を支えるBOMの中身について理解
第8章 購買管理システムを理解するための購買業務について
第9章 工程管理システムへのデータインプットと改善方法について
第10章 在庫とは何か、その管理目的の定め方
――――――――――――――――――――――――――――――
第11章 工場財務と原価管理システムの留意点
第11章のまとめ
生産管理システムは生産計画をコアとして、工程管理、在庫管理、原価管理と一連の流れで考える必要があると分かりました。
緻密な原価管理をするためには正確な工程管理、在庫管理が不可欠であり、それは現場サイドのマインドによって精度が変わります。
DXという言葉で一括りにされていますが
・経営者の課題認識とそれを解決したい意思
・それを各部門長が自分事に落とし込み自部署のKPIを熟考する
・KPI達成のための具体的な活動を現場レベルに落とし込みKPIを共有し工場全体で自分事化する
これらをつなぐ重要なシステムが生産管理システムということが分かりました。
いまなぜ生産管理システムなのか?という自分への問いの答えは「日本が生産大国として隆盛していた時代は終わり、新しいPhaseに入る際にデータドリブンな現場に変革するため」だと答えがでました。
<11-1 要点>財務会計と管理会計
・生産管理における「財務」とは管理会計
①管理会計:自社の経営意思決定のために独自の工夫も凝らすことができる会計
②財務会計:外部公表が目的で、証券取引法や法律などに基づいて処理される
・管理会計は画一的では意味がなく、各企業の意思決定の仕組みを理解し、その企業にあった管理会計システムを構築する必要がある
引用:生産管理システム構築のすべて ISBN 978-4-534-04674-1 P216~219参照
<11-1 所感>
冒頭からとても大事な切り口が出てきました。生産現場の課題を見つけてもそれをどのように経営指標にフィードバックするか。も含めて検討しないといけないです。
本当に生産管理システムは奥が深い・・・
<11-3 要点>IFRSが生産管理システムに及ぼす影響
(※11-2は参考情報程度と判断しスキップしました。
・IFRS適用時のシステム面の注意点
①売上基準が検収時点に限定され、出荷基準だった場合、製品在庫担当者が売上基準を計上できなくなる
②在庫評価が取得時と時価でいずれか低い方を期末資産とする低価法が適用される
③IFRSにならって後入先出方は利用できなくなる
想定シーン:原価高騰で材料費が高くなっている局面
・先入先出法:仕入価格が安かった材料から出荷され、仕入価格の高い材料が在庫として残る(在庫評価 高)
・後入先出法:仕入価格の高い材料から出荷され、仕入価格の安かったころの材料が在庫として残る(在庫評価 低)
引用:生産管理システム構築のすべて ISBN 978-4-534-04674-1 P223~225参照
<11-3 所感>
第11章は工場財務パートだから、「さらっと読んで終わるか。」と思っていましたが、超重要。
導入を検討する顧客側、導入を提案するベンダー側も、経営者がYESというかどうかが関門です。
経営者は工場が正しく運営できる方法、工場の課題よりも、結局導入するとどうなるのか。を知りたいと思いますので、工場財務目線の指標を示すことができないと全く説得力がありません。
<11-4 要点>取り扱いによっては経営を誤らせる部門別損益
・部門別損益を作成する目的は「高収益部門、不採算部門を把握して高収益部門に経営資源を投入し、不採算部門を撤退・縮小するなど経営判断の指標を作成するため」
・共有費用(家賃、ユーティリティ、設備など)の配賦が高収益部門や不採算部門を不明瞭にする可能性がある
・活動基準原価計算(ABC:Activity Based Costing)は売上高、人員数、面積でコスト配賦をせず、活動に紐づけて配賦する手法
+長所:正確なコスト算出が可能、固定費のムダを把握できる
+欠点:活動把握の事務工数が大きい、会計原則では認められない
引用:生産管理システム構築のすべて ISBN 978-4-534-04674-1 P226~228参照
<11-4 所感>
生産管理システムというよりかは、部門長レベルの人が認識すべき内容です。最近は経理・財務の知識がないと部長職になれない会社や社員研修に経理・財務を取り入れたりする会社が増えています。
ビジネスパーソンとして、幅の利くスキルなので知って損はなしです。
<11-5 要点>損益分岐点分析による利益改善
・損益分岐点(BEP:Break Even Point)を改善する4つの方法
①売上高を増やす
②固定費を減らす
固定費は「人件費」「償却費」「経費」から構成される
③変動比率を低くする
製品歩留り(良品割合)の向上、部品共通化による仕入れ単価削減など
④固定費の変動費化
一部工程の外注化、社用車のシェアリングカーへの変更など
引用:生産管理システム構築のすべて ISBN 978-4-534-04674-1 P229~231参照
<11-5 所感>
11-4と同じく生産管理システム云々でなく必須知識
<11-6 要点>全部原価と個別原価
・個別原価計算は、種類の異なる製品を個別に生産する形態に適用する
・総合原価計算は、個別原価計算のように生産ロット別でなく一定期間あたりの製品原価を求める手法で連続的に生産される場合に適用する
→当月総合原価=「当月製造原価+月末仕掛品」で表すことができ、月末仕掛品をどう評価するかが問題
・直接原価計算は費用を変動費と固定費に分け、
+変動費→個々の製品に割り当てる
+固定費→期間原価として処理
・全部原価は変動費も固定費も製品原価に含めて計算する
・環境会計は企業の環境保全への取組状況を定量的に管理するもの
引用:生産管理システム構築のすべて ISBN 978-4-534-04674-1 P232~236参照
<11-6 所感>
このセクションは正直わかりづらいです。こんな考え方があるのか。程度に留めておきます。
<11-7 要点>標準原価計算の考え方
・標準原価計算の目的は原価管理を行うための「原価の標準」を持つこと
・実際の生産活動の結果から算出された実際原価との差異を分析し改善していくための指標として以下の2つを用いる
①目標原価:一定利益を確保するための原価
②あるべき原価:経営資源を効率的に活用した場合に達成する原価
・操業度(繁忙度合)で製造コストは大きく変動する
+繁忙期:経営資源がフル稼働し、コストが下がる
+閑散期:経営資源が遊んでしまいコストが上がる
・加工費レートとは、各工程で製品1個当たりを加工するために要する固定費(加工費)であり、その設定方法として以下の二つがある
①人工数:組立など人作業が中心の場合
②機械工数:自動化が進んだ機械中心の工場などの場合
引用:生産管理システム構築のすべて ISBN 978-4-534-04674-1 P237~241参照
<11-7 所感>
このセクションは原価管理サブシステムを導入するうえで最初に定義が必要です。原価を把握して高収益部門・不採算部門を明らかにする。ただ原価の計算方法が部門別でバラバラだと話にならないですからね。(あまりないと思っていますが)
<11-8 要点>実績原価の管理
・原価管理の出発点は「設計段階からの原価企画」であり、設計段階でおおよその原価が決まる
・コンカレント(Concurrent:並列の)エンジニアリングとは「商品設計」「実験評価」「生産準備」「製造・出荷」に至るまでの各プロセス設計を同時並行に進めること
・グローバルに対応する原価管理では、正社員の人件費の考え方にも留意が必要
+US:レイオフ制度があり、工場で働く社員を変動費と扱う
+日本:工場で働く社員を固定費と考える企業が多い
・原価管理に作業日報を活用することで、経営指標のリアルタイム把握とアップデートが可能となる。作業日報に含めるべき項目は
①作業者、②工程、③品名、④良品数、不良品数、不良発生原因、⑤加工時間、⑥ダウンタイムとその発生理由
・原価カイゼンに終わりなく、その手法としてVA(Value Analysis)/VE(Value Engineering)がある。機能を落とさずにコストを下げる設計段階からの原価カイゼン
引用:生産管理システム構築のすべて ISBN 978-4-534-04674-1 P242~244参照
<11-8 所感>
最後の所感ということで冒頭のまとめに持っていきます。
北村友博氏がご自身の経験も含めて体系的にまとめてくれたこの本は生産改革を起こしたい人におすすめです。ありがとうございました。
2021年10月2日
この記事が気に入ったらサポートをしてみませんか?