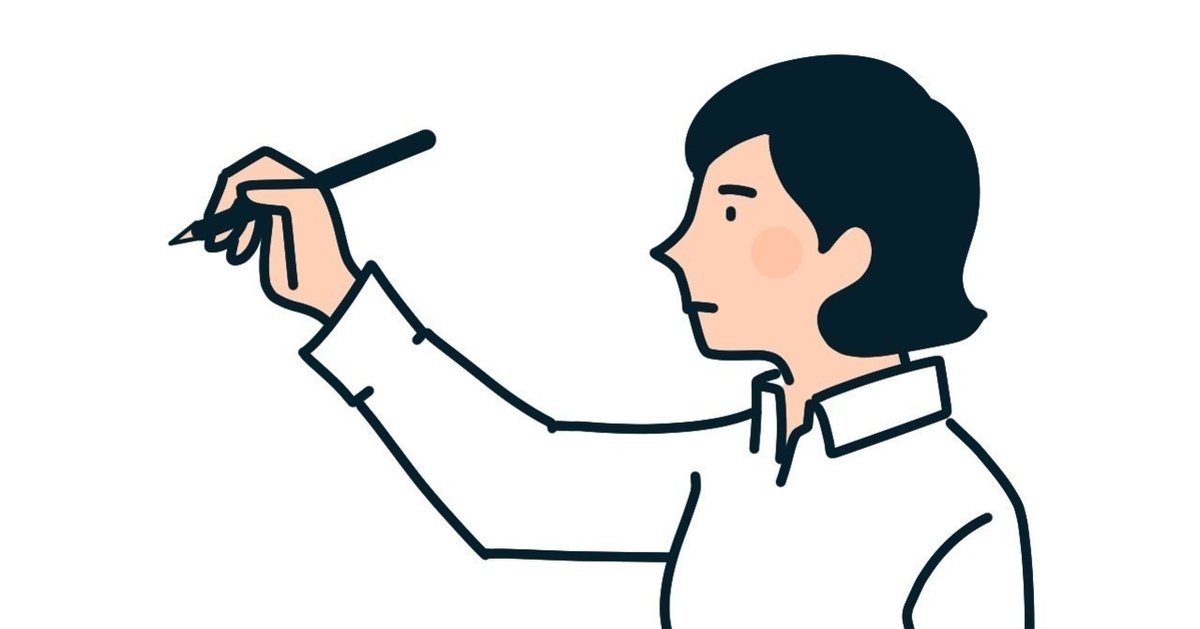
業務改善の落とし穴(前編)
雨の月曜日です。雨って嫌ですよね?
僕は雨と蚊が嫌いです。特に夏の雨は蚊も呼んでくるのでやっかいですね。週のスタートが雨だと何とも気が乗りづらいですが、集中して仕事に取り組みたいと思います。
今日は「業務改善の落とし穴」というテーマで書きたいと思います。
緊急事態宣言後に一気にテレワークになった企業も多いのではないでしょうか。
対面を基本としていた業務フローから準備期間もなくテレワークへの移行が進んだため、様々ところでコンフリクトや業務の玉突き事故が増えているのではないかと予測しています。
今、多くの企業でこれまでの業務オペレーションから新しい業務オペレーションに再設計しなければならない課題を抱えた現場が多そうです。
そこで業務改善のポイントというか、僕なりに大切だな~と思う視点を書いていこうと思います。主なターゲット読者は部門長や管理職の方ですね。
早速ですが、皆さんは業務改善って言葉好きですか?
僕は何となく苦手ですね。特に「さぁ業務改善しよう!」みたいなのが苦手です。業務改善ってもっと日常的にやるべきことだと思っています。
意識的に取り組むのではなくて業務の地続きな感じで取り組み結果として改善されているというのが本質かなと思っています。
業務改善には大きく会社でできる事と、個人でもできる事の2つがあると思っています。
① 会社で出来ること:プロセス改善(全体を視る!)
② 個人で出来ること:仕事の受け方改善(目的を知る!)
大きなテーマをみんなで取り組む業務改善と、一人ひとりの心がけで十分に改善できるテーマの2つになります。前編では①の会社できること(プロセス改善)編を書こうかと思います。当たり前で超基本的なことですがお付き合いください。
① 会社で出来ること:プロセス改善(全体を視る!)
仕事は基本的に工程に分かれプロセスでつながっているので、前の工程から自部門が受けて、また次工程へ仕事を受け渡すという感じで仕事が流れているかと思います。
この場合いかに自部門の業務改善をしたところで前後の工程が改善されなければ本質的な問題は改善しないなんてことはよくあることです。本質的な業務が改善されないのに、これを業務改善と呼ぶにはあまりにも無理があるというものです。
業務改善に取り組むことが悪いとは全く思いませんし、いいこだと思っていますが「その努力に見合うリターンを得れるのかな~」と思うことが多いです。
なので、仕事の入り口から出口までの全体像と工程間のプロセスをしっかりと把握した上でそのプロセスのボトルネックを改善していくのがすごく大事です。
例えば製造プロセスの中にボトルネックがあるとします。 A部門 から B部門へ、B部門から C部門へという形で仕事を受け渡していく時に明らかに途中のB部門の歩留まりが多く製造プロセスのボトルネックだとします。
ただ、このボトルネックを改善するためにB部門が取り組んだところで効果が限定的ということはよくある話しです。
一見するとB部門の歩留まりが悪いのだけど、その原因を作っているのはA部門の半製品の精度かもしれませんし、そもそもの製品設計に問題があるかもしれません。
要は改善の前に全体プロセスを俯瞰する視点を持った方がいいと思っています。これは何も社長や部門長や管理職だけでなく、社会人になったら持っておきたい視点だと思っています。
この視点を持つことで自分の仕事の意味や役割を自覚することができ、自らの成長カーブを引き上げることができると思っています。
話しは大きくなってしまいますが日本の自動車産業はトヨタ自動車をはじめ高度な生産性を保っています。
これも系列を含めた全体の製造プロセスを生態系と捉え、その生態系を維持・改善していく大きな視点で絶え間ない業務改善を繰り返した結果です。
自動車産業(製造業全部ですが)はリーン生産方式を採用していると言われます。
●リーン生産方式
無駄のないスリムな生産方式で,従来の大量生産方式に代わるもの。具体的には,トヨタなど日本の自動車メーカーで一般化しており,労働力,在庫,製品開発期間,工場スペースなど企業活動の中のあらゆるものをできるだけ少なく使い,欠陥を減らし,1車種当たりの生産量を少なくし,多様化する顧客ニーズに対応するシステムのこと
トヨタがアメリカに進出した時代は大量生産大量消費時代でした。自動車といえばアメリカのフォードやGMが世界を牛耳っていた時代です。
規模の経済では戦えないトヨタがとった戦略がこのリーン生産方針です。
日本語に意訳すると「トヨタ生産方式」になるかと思います。ジャストインタイムとか、かんばん方式を聞いたことがある方は多いのではないでしょうか。
当時のトヨタはムダな在庫・設備を生まない、持たないために角度の高い需要予測を長期→中期→短期で試行錯誤していました。
自動車業界の特徴としてエンジン、シャシー、アルミフレーム、ミッション、ガラス、タイヤ、ハンドル、シートなどの各パーツを系列と呼ばれるメーカーと協力して製造しています。
トヨタは需要に合わせて必要な各パーツを仕入れ、工場のラインに流して顧客のオーダーにあった車に組み立てしていくのです。
例えばこの時にミッションの工程だけ設備投資して生産量を増やしても意味がありません。ミッションのインプット(生産量)が上がっても次工程にスループット(納品)できなければミッションの工場に在庫が溜ってしまうことになります。
要は次工程の生産力も同時上げなければ折角の設備投資も宝の持ち腐れになるのです。
何とも当たり前のことなのですが、系列とはいえ別会社である企業間の需要をできるだけ平準化することで全体の平均稼働率を上げる絶妙なオペレーションが裏側には存在しているのです。
この思想は製造プロセスだけの話しではなくて、バックオフィス業務にも当てはまります。事務部門の効率を阻害するのは、前工程である営業部門というのはどこにでもある話しです。
そして営業部門の効率を上げていくにはその前工程であるお客様を巻き込んだ業務改善が求められています。
自動車業界のような大きな枠組みでなくても、会社やチームでできる業務改善に取り組んだほうが効果は遥かに大きいです。
自部門だけでなく前後の部門を巻き込んだ業務改善の視点をもち取り組むことが結果として大きな成果を生むので是非トライして欲しいと思います。
特にテレワークは一過性ではなく、継続的なことが予測されます。
パッチワークの業務改善(自部門だけ)ではなく、少なくても前後を巻き込んだ改善に取り組むことで多くのスタッフが前向きに働ける環境を整えることができると思います。
うちの会社も頑張ります。
こんにちは。最後までお読み頂きましてありがとうございます。このnoteは僕のつたない経営や、インナーブランディングを行う中でのつまづきや失敗からの学びです。少しでも何か皆様のお役に立てたら嬉しいです。サポートはより良い会社づくりのための社員に配るお菓子代に使わせていただきます!