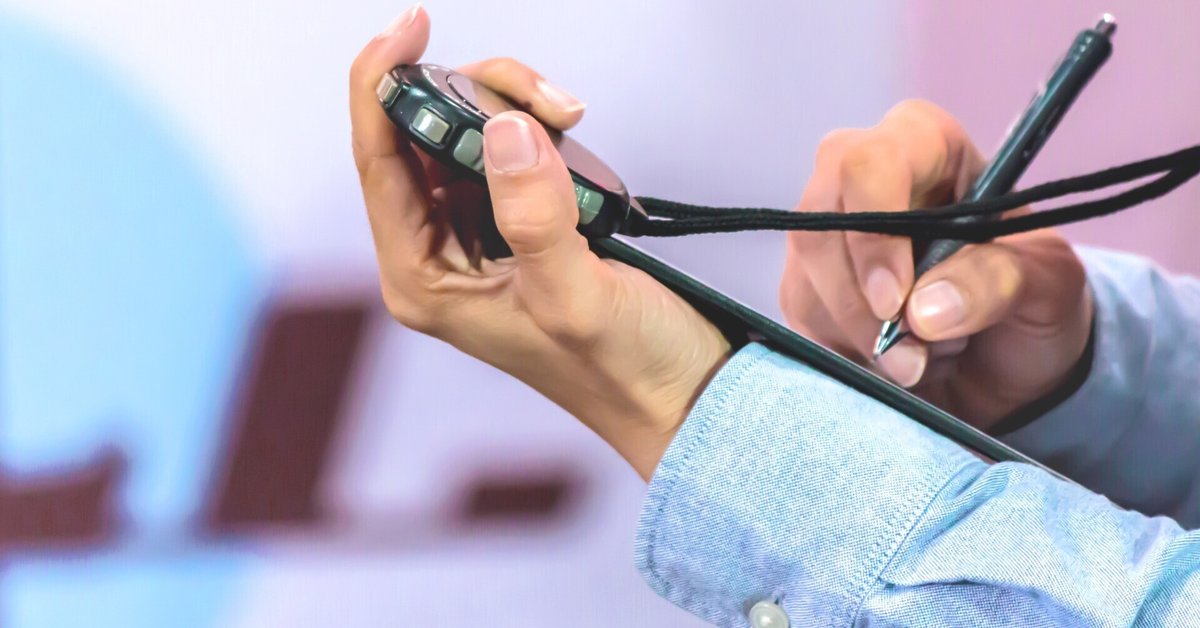
グッドデザイン賞を受賞したら、現場作業の秒数を計測して分析することが仕事になった話
「あのAGV、導入効果がいまいち上がっていないから、一度現場に行ってほしい」
「グッドデザイン賞」受賞のよろこび。
その余韻に浸っていた私に、営業がそう声をかけてきました。
グッドデザイン賞の審査をされる先生方に、
「このAGVはお客様の現場で結果が出ています」
と言ってしまっていたこともあって、
これは私が何とかしなければ!と思い、現場に行ったことが、デザイナーとして新たな道を歩むことになるとは、この時までは思ってもみませんでした…
はじめまして。シャープのED(エキスパートデザイナー)村岡寛です。
無人搬送車(AGV;Automated Guided Vehicle)のデザインを担当してまして、シャープにはキャリア採用で入社し、前職からプロダクトデザイナーをしております。
それは、シャープに入って2年目でした。
私がデザインしたAGVが2019年グッドデザイン賞を受賞したこと時のこと。
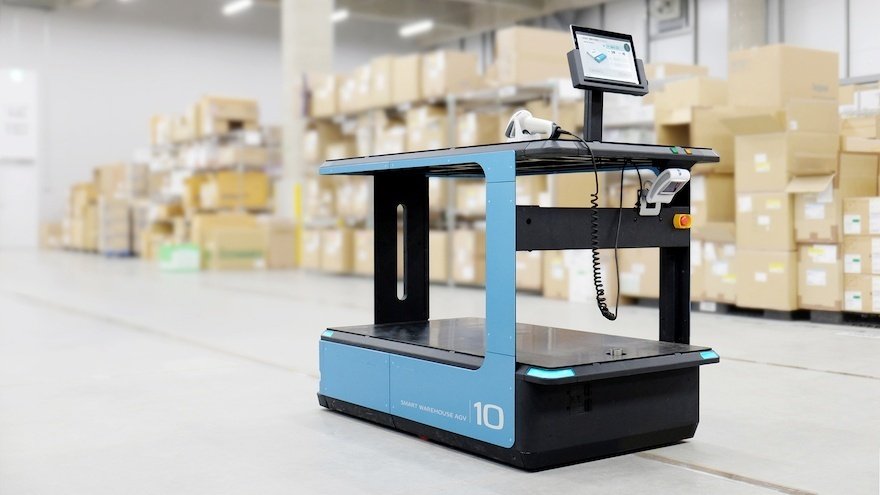
プロダクトデザイナーの私がどうやって、現場で効果が出ていなかった問題を何とかしてきたのか、という話をしていきたいと思います(なんとか出来たという感じではなく、本当に何とかしてきたといった感じです)。
デザインの話と関係ないやん!と思われるかもしれませんが、デザイナーが秘めている新たな可能性が見えてくるのではと思ってますので、ぜひ最後までお付き合いいただければと思います。
■ デザイン賞の受賞で足りなかったことは、二度とやりたくない作業が教えてくれた
いきなり実例でお話していきたいところですが、いったん、ここでは架空の物流倉庫(新設)を仮定して、作業の流れをまず紹介させてください。
1. 作業プロセスすごろく
新設の倉庫では、同じ業務をしている既存の倉庫を見せていただき、新設倉庫ではどのような作業工程をイメージしておられるのかなどをヒアリングしていきます。複数の倉庫を見学させていただくケースもあります。
すでにAGVを導入されているお客様ではある程度、具体的なイメージを持たれているケースもありますが、この時点ではあくまでもフラットに、現在の作業工程を視察します。
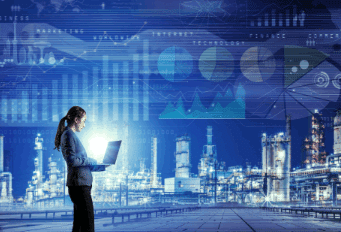
可能であれば、現場の作業者さんとのコミュニケーションも積極的に取るようにしています。
実際の作業を日々やっている人がどんな気持ちで、何に注意しているか。嫌なこと、しんどいことは何か?
そこに入り込めると、ユーザビリティ面からも導入効果を出すことができます。
「分からない」「暑い、寒い」「面倒くさい」「怖い」などデータ分析には現れない心理面のエラーを、データと紐づけて拾っていくと発想のきっかけになります。
もちろん作業のお邪魔はできませんので、何も聞けないことも多いです。
その時はじっと観察させていただきます。
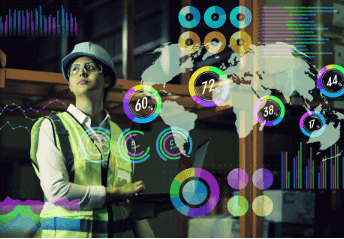
同じ会社の倉庫でも、現場の作業者の皆さんが独自に工夫されているので、工程が整理されていないことが多く、現状の作業の全容を正しく理解することは容易いことではありません。
そこで、お客様の了承を得た場合には、現場を案内していただきながら動画を長回しで収録していきます。現場見学では見逃していたことも、動画で見直すと「この人はこんな作業をしていたんだ」と発見することも多くあります。
そうした現状分析をまとめて、図のような「作業プロセスすごろく」を作成していきます。
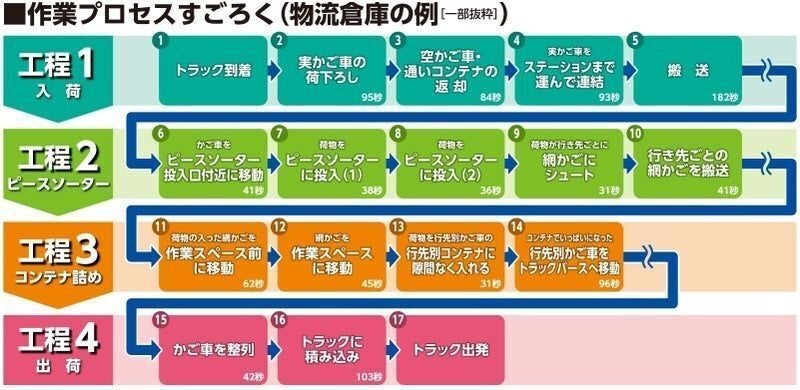
この図は単純化していますが、実際の作業工程は一直線ではなく、途中で枝分かれしているなど、もっと複雑な「すごろく」になります。
この図をもとに、お客様と作業プロセスの認識を合わせていきます。
お客様ご自身も
「こんな工程もあったのか」
と、作業工程を見直すきっかけになることも多いです。
2. 単工数分析(オプションです)
これは別途費用をいただくオプション作業になるのですが、さらに深い作業の分析を求められるお客様には
「作業プロセスすごろく」の各作業にかかる時間を測定した「単工数分析」を作らせていただきます。
これは全体の作業工数の把握と、自動化されたときの効果を予測するためのベースとなるデータになります。
作業している動画を見て、
ストップウォッチで秒数を計測して、
平均値を出す
を繰り返すという、ひたすら、ひたすらに工数のかかる地味な作業で、正直言うと、毎回、二度とやりたくないと思ってしまいます。
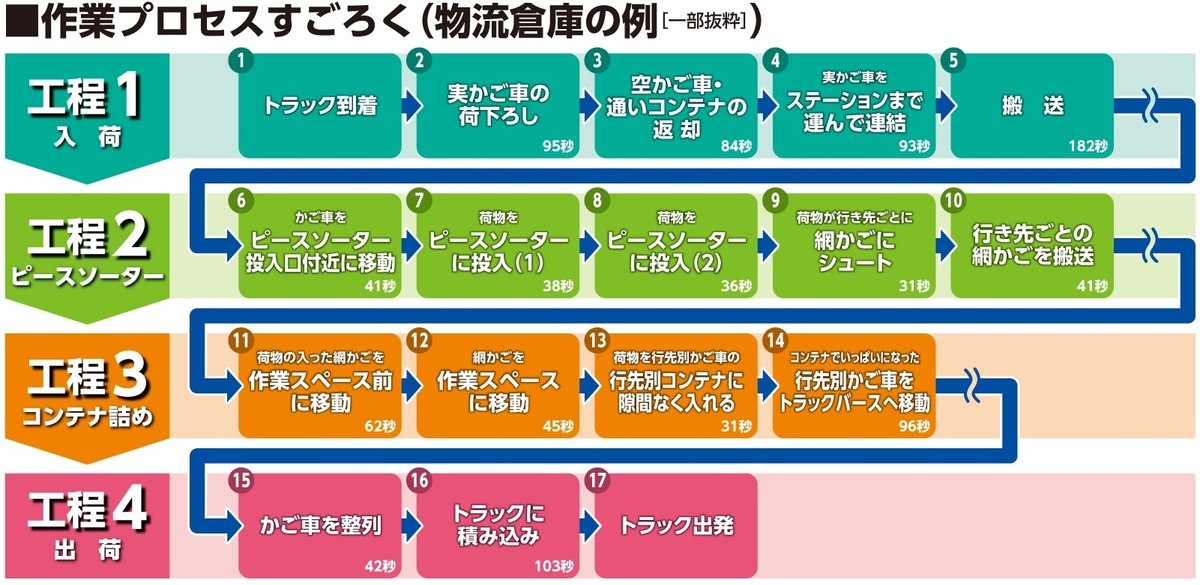
単工数分析はモノづくりの工程設計ではよく行われる作業だそうです。シャープの事業部には生産技術の猛者がたくさんいて、現場を一通り見るだけで作業プロセスが把握でき、複雑なものを単純化してキラーソリューションを創出するという特殊能力を備えた人もいます。
そんな能力がないデザイナーの私は、ひたすら単工数分析をして問題が大きい工程を見つけ、理詰めで正しい答えに、にじり寄るしかありません。
生産技術の猛者たちにダメ出しを受けながら学んできたので、私でもお客様に感心していただけるような単工数分析を作成できるようになりました。
さらに、現場に埋もれすぎないある意味素人であるからこそ、根本的な問題に気付けるのではないかとも思っていますので、デザイナーとしての感性も大切にしながら、この作業を行っています。
3. ソリューション提案と効果出し
現状分析が終われば、提案内容をアイデアレベルで工程ごとに見える化していきます。
例えば、
入荷搬送ではこのAGVが使える、
ピースソーターの工程ではこのようなAGVソリューションがある、
出荷搬送ではこのAGVが良い、
というようにアイデアを膨らませます。
現状分析を検討する中で見えてきた無駄な工程を省きましょう、という提案を行うこともありまして、シャープは取り扱い商材が幅広く、様々なソリューションに対応させていただいています。
「実はここまでやりたい」
「もっとこういうことがやりたい」
というお客様の潜在的なご要望を引き出すために、技術者もデザイナーもお客様に寄り添うことを第一に考えて、まずはアイデアレベルで仮説提案を行い、お客様の要望をお伺いしながらブラッシュアップし、より具体的な提案へと発展させていきます。
デザイナーが提案に参加しているメリットが最も発揮できるのは、この仮説提案の段階だと考えています。
人がピッキングするブースにAGVがやってきて、そこで商品をチェックしながら配送先ごとに積み込んでいく、というソリューションを提案したとします。
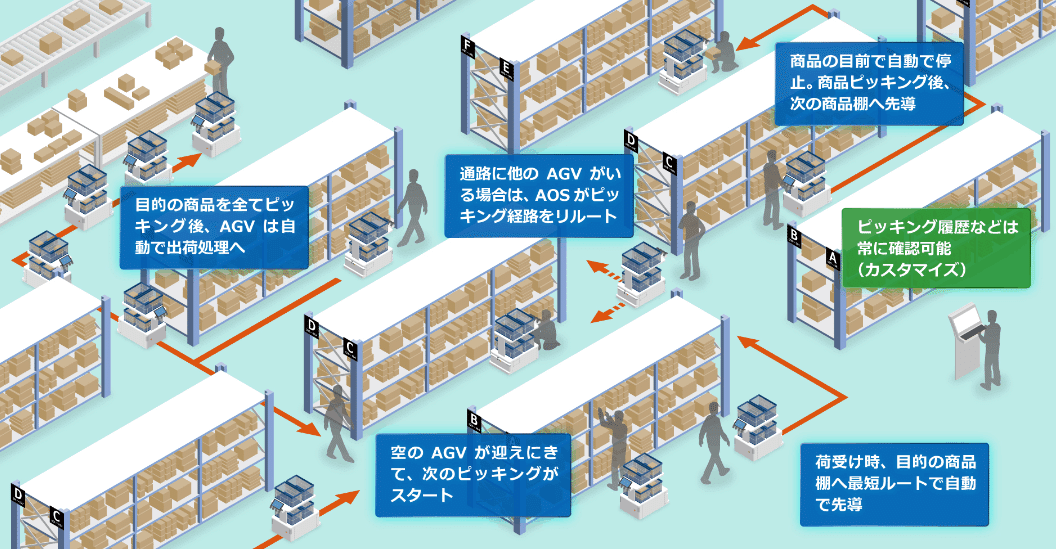
人が作業するブースはどんな形なのか、
チェックするタブレットはどんな画面が見やすいか、
AGVはどんな動きをするのか、
フロア全体のイメージはどんなものになるのか、
言葉だけの説明では、お客様になかなか伝わりません。
デザイナーは3D-CADで設計の真似事ができるため、設計者がアサインされていないごく初期段階でもリアルな絵が描けます。そのため、お客様も導入後のイメージがわきやすく、要望を精度よく汲み取ることができます。
ラフスケッチ段階からビジュアルで提案でき、お客様の要望がより具体的になれば、完成予想パースやVR(バーチャルリアリティー)などへと発展させていくことができます。
仮説提案~最終提案への作業と並行して、AGVの導入効果を具体的な数字で提案する作業もまとめていきます。
AGVの作業を人が行う場合の作業工数とAGVにより自動化が可能な工数。それを比較して、各作業工程でどれだけの効果が期待できるかなどを具体的な数字で出していきます。
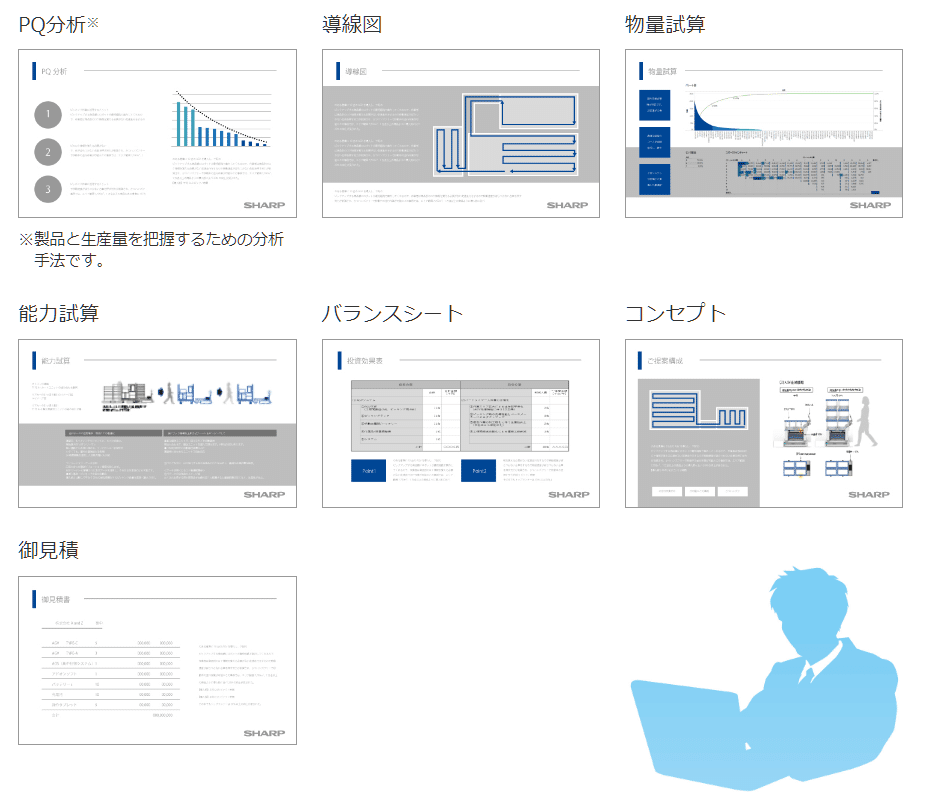
デザイナーは現場に埋没しない自由な発想とは言っても、コストを度外視した提案では、それこそ「絵に描いた餅」となってしまいます。
最も肝心な導入コストの算出、つまりお見積もりは、営業やSEが中心となり調整していくことになります。
シビアな結果とコスト意識の高い営業や
SEと連携しながら、
デザイナーが参加しているからこそのお客様に喜んでいただける提案
を追求しています。
■デザイナーがAGVの効率を上げてみた
シャープに転職した当初は、AGVの色・形・ユーザビリティのデザインが中心でした。
冒頭でお話したグッドデザイン賞を受賞した製品の導入効果が伸びてなかったことをきっかけに、導入したAGVの効果を上げる立案を行うようになり、技術と一体になってデザイン・エンジニアリングを進めるワークスタイルに変わっていきました。
きっかけとなったAGVの導入効果を上げるための取り組みについて、お話しさせてください。
まず、AGVの導入概要は
【導入先】
医療系専門商社の物流倉庫(新設)
【導入目的】
倉庫が拡張され、入出庫の搬送作業の負担が増加。
自動搬送でその負担を軽減するとともに、ピッキングなど業務の効率化を実現する。
【導入機種】
台車を連携し最大500㎏の牽引が可能な有軌道タイプのAGVを17台、集中制御システム(AOS)
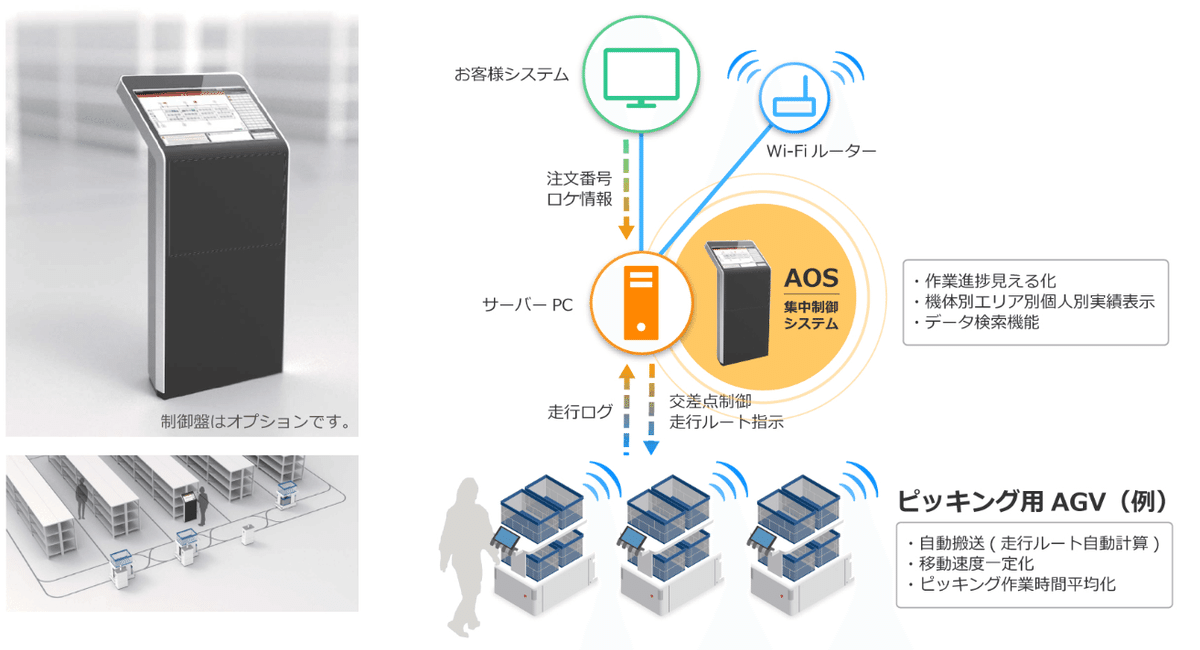
付け加えますと、導入したAGVは
・台車を牽引して入出庫作業での無人搬送に活用するもの
・ピッキング作業のアシストに活用するもの
に分かれます。
無人搬送では、お客様が期待されていた通りAGVが作業員さんの負担軽減に大きな効果を上げていました。
それに対して、ピッキング作業のアシストで活用しているAGVは、目標としていたピックアップ数をなかなか達成できていませんでした。
私のミッションは、
目標を達成できない原因を探り、
ピックアップ成績を向上させる
ための提案をすることでした。
その現場で導入されているピッキングアシストシステムは
・倉庫管理システム と AGVの集中制御システム(AOS)が連携
・ピッキング対象品の棚の前まで作業員を先導
・ピックする商品はタブレット画面に表示
・ピックした商品はその場で検品してミスを防いでいく
というもの。
このシステムでは、台車を押す労力が削減され、かつハンズフリーで移動中の並行作業が可能です。
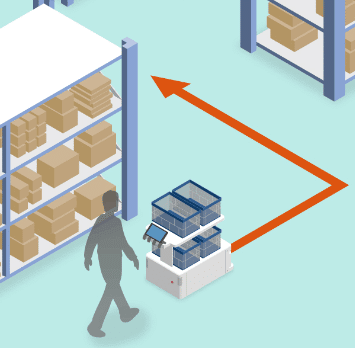
作業員さんの負担を軽減できることはもちろんですが最大のメリットは
今日、来られたばかりの作業員さんでも、
商品棚をすべて把握しているというベテランの作業員さんと同じように
ミスなく効率的なピッキングができること。
つまり、AGVが作業員さんの能力差をカバーしてくれることです。
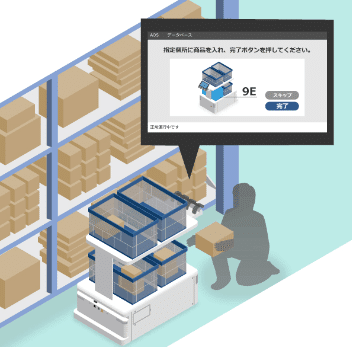
僕はまず現状の作業を把握するために、AGVのログデータの解析から始めました。
AGVやAOSはさまざまなログデータを蓄積しています。
この現場では倉庫管理システムとも連携していますので、
A地点で20秒停止して5個の商品をピック
B地点で30秒停止して8個の商品をピック
C地点………
というようなことも簡単に解析できます。
そのデータをもとに、作業員さんの行動を現場観察させてもらうことで、ログデータだけでは分からない生産性の低下の要因が見えてきました。
AGVがスタートして作業が終わる時間のうち、準備や払い出しなど
ピッキング以外の作業時間(不働時間)が20~25%を占めている
ことが分かりました。
AGVは棚の近くに止まり、どの棚から商品をピッキングするかタブレットに表示しますが、まだ作業になれていない方は、棚にたどり着くまで時間が掛かっていました。
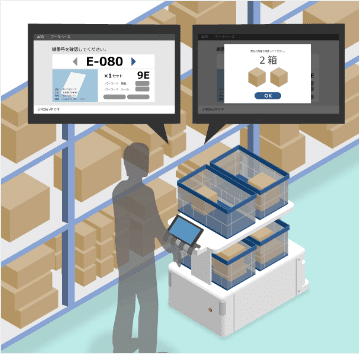
また、このアシストシステムでは、1度の搬送で4つの配送先をピッキングしていくマルチピッキングに対応しています。4つの配送先をより分かりやすく表示する工夫も必要だということも分かりました。
現場観察で得た課題をもとに、下記のような生産性向上メニューを提案しました。
1. 準備や払い出しなど作業を入荷担当者が兼任し、ピッキングの不働時間を削減する
2. 配送先ごとに注文書を色分けして、4つの配送先の同時ピッキングを分かりやすくする
3. 左右表示、棚の表示など、タブレットのユーザーインターフェースをより分かりやすいものにする
この提案をもとに、実証実験を行ってもらい、その結果を分析してさらに改善していくことで、ピックアップ成績は目に見えて向上していきました。
もちろんそれは、私の提案の効果だけでなく、作業者さんの習熟の効果や現場の方々の独自の改善によるところも大きいと思います。
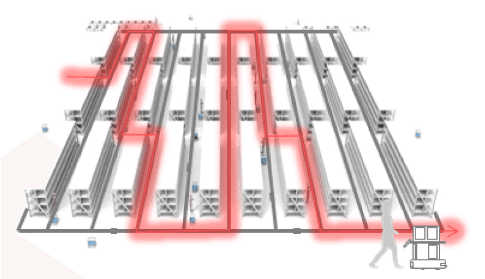
現場を観察して課題を解決していく、というソリューションの貴重な経験となりました。
■ソリューションデザインとは
私がいま展開している活動は
ソリューションデザイン
というものです。
一般には聞きなれない言葉ですし、人によって捉え方が違うかもしれないので、私が行っている「ソリューションデザイン」について少し説明させてください。
ソリューションデザインとは、
受注前の提案段階で、
現場観察や工程分析をもとに、ソリューションの仮説をたて、
「完成予想図」や「VR(バーチャルリアリティー)」で見える化してお客様と検討・修正を繰り返し、
お客様の理想のソリューションへ近づけていく
ことです。
デザイナーがこの段階に入るようになる前は、現場の平面図と「この工程をAGVにすると、これだけ生産性が上がります」
というような言葉でソリューション検討が行われていました。
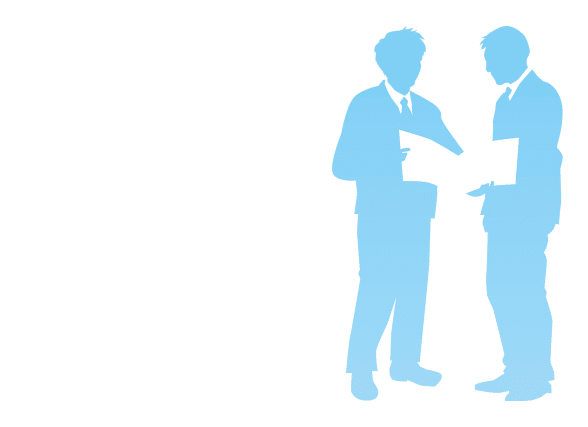
シャープ以外では、AGVでのソリューション提案にデザイナーが参加しているような会社は聞いたことがないので、おそらく現在もこのような提案が多い状況だと思っています。
従来、デザイナーがソリューション提案に参加するのは、開発のもっと後工程でした。
例えば、
操作するハンドルはこんな形にした方が作業しやすい、
安全性を高めるにはこんな素材を使う方が良い、
操作ボタンの位置はここの方が効率的に作業できる
など、インダストリアルデザインとか、UI(ユーザーインターフェース)デザインと呼ばれる具体的な部分のデザインですね。
しかし、根本的なソリューションを実現するとなれば、従来のデザインの手法だけでは限界があります。課題を解決するためには、こんな機能も必要になるとか、この性能を高めた方が良いとか、
従来のデザインの枠を超えた発想やアイデアが必要です。
それがソリューションデザインだと、私は考えています。
ソリューションデザインは一朝一夕にできるものではなく、豊富な経験が必要だと思っておりまして、私のベースとなっているのは、前職での経験です。
医療機器メーカーでの経験
私は前職の医療機器メーカーで、医療機器・分析機器のデザインを担当していました。具体的な製品で言うと、CTスキャナ、放射線治療装置などX線を使った大型の画像診断装置などを中心に担当していました。
病院で使われる機器で、検査でお世話になったという方も多いでしょうし、放射線科を舞台にしたTVドラマもありましたので、何となくその形は想像していただけると思います。
その仕事で、回診用のX線撮影装置の開発を担当することになりました。動けない患者さんのところに装置を手で押して移動して撮影するレントゲン装置です。
実際に使われるのは放射線技師さんなど専門職の方々に限られるので、使っていてどんな課題があるのかは、私たちデザイナーにはなかなか分かりません。
ですから、まず医療現場に行って放射線技師さんの行動を観察させてもらい、お話を伺って問題点を探していきます。
現場観察させていただくと、いろいろな課題が見えてきました。
例えば、
身長の低い人は操作するために装置の上に乗らざるを得ない、
全身に火傷をおって包帯でぐるぐる巻きの患者さんはX線撮影のために大変な苦痛を強いられる、
点滴をされている患者さんは点滴の支柱が邪魔になって撮影しにくい
など。
そうした病院取材で問題点を発見し、アイデアをスケッチしてモックアップを作り、そのモックアップを持ってまた病院に行って意見を聞いて、問題点を発見する。
そのスパイラルを繰り返すような開発の仕方でした。
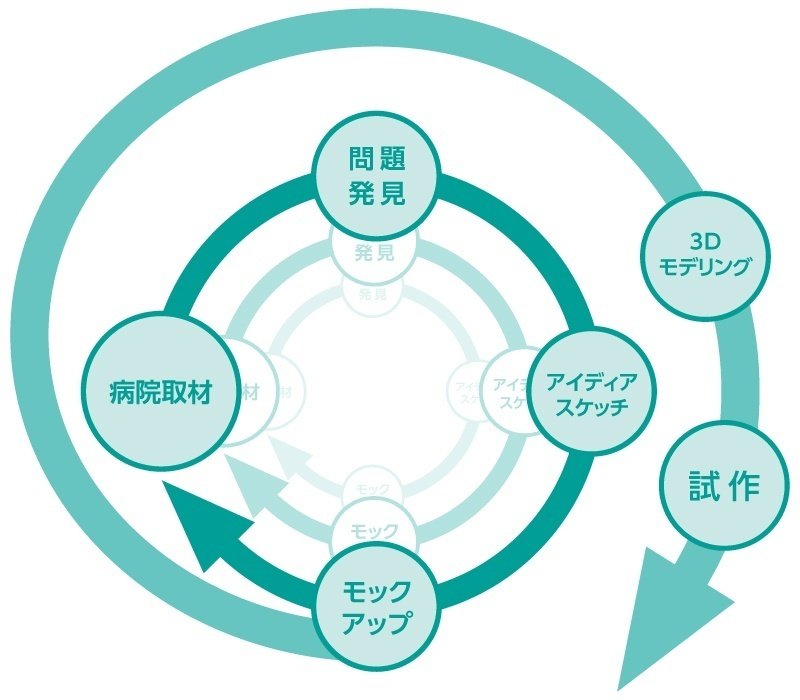
現場に入り込んで潜在的な課題を発見して「どう解決するか」を実現する。それは「商品導入価値」を「お客様と共創」していくことです。
最終的に撮影するためのアームと支柱が伸縮する新しいタイプの回診用X線撮影装置の開発にこぎつけることができ、ソリューションとして販売することができました。
ちょっとプレゼンテーションのような話になって恐縮なのですが、デザイナーがソリューションに参加する意味について、もう少しだけ説明させてください。
今までは、仕事の分担が進んでいたことで、デザイナーは現場には詳しくありませんでした。
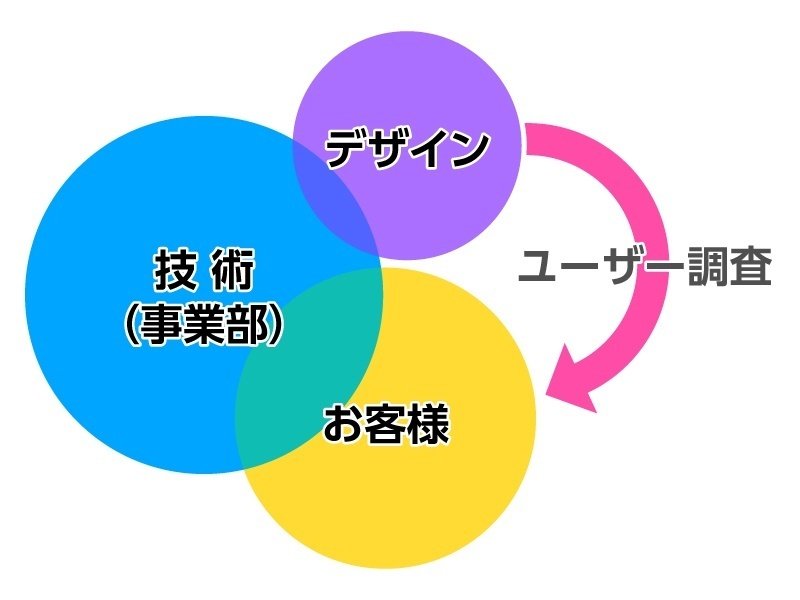
一方、技術や営業は現場に埋没することで先入観のない発想は難しかったと考えています。
それに対して、デザイナーが現場に深く入り込みお客様の課題を理解していく「ソリューションデザイン」では、
シビアな結果とコスト意識を持った技術や営業と、
俯瞰的な視点で先入観のないデザインが
対等に議論することで、本質的なソリューションが可能になります。
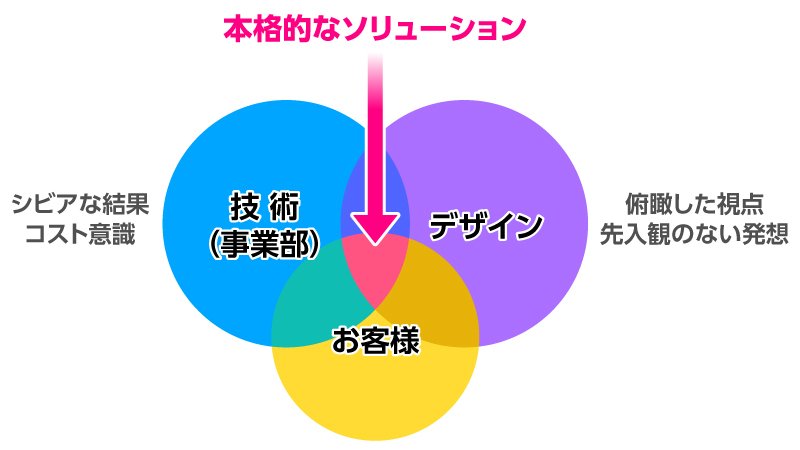
いろいろお話をしてきましたが、、、
本音を言いますと、
やっぱり良いデザインの仕事がしたい!
それが私たちデザイナーのモチベーションになっています。
私がシャープに転職したのも、前の会社でジョブローテーションによってデザインの現場から離れたことがきっかけでした。
CS(Customer Satisfaction)やRPA(Robotic Process Automation)、働き方改革など、新しい経験ができたことは良かったのですが、管理職になってデザインの一線から外れてしまうのが嫌で、より広い領域の商品をデザインしたいという思いに駆られた、というの転職したのが理由です。。
データサイエンティストについて
シャープ以外で、AGVでのソリューション提案にデザイナーが参加しているような会社は聞いたことがないと思っていますが、データサイエンティストの方が参加しているケースはあるかも知れません。
ただ最初のコンペの段階で、データサイエンティストが参加しているか、現場の分析までしてソリューション提案しているか、というとまだまだ聞いたことがありません。
「弊社では、導入後にこういう人材でこういうことをこういう分析もさせていただきます」といった感じで、受注が決まってからデータサイエンティストの方が参加されることはあると思います。
お客さまの中の
「何かモヤモヤとした、何かやりたいことがあるんだけど、何かこう、具体的にはやりたいことは決まってないんだよ」
みたいな状態。
デザイナーは、そのモヤモヤ、、、
ちょっと何かふにゃふにゃした状態と同じようなテンションで付き合える。
そして絵にできる、
お客様も導入後のイメージがわきやすい提案資料に落とし込んでいける、
そのことこそが、デザイナーの強みだと考えています。
■待望のデザインのお仕事
私たちのソリューションデザインがお客様に評価され、受注をいただければ、待望のデザインの仕事が始まります。
AGV本体や周辺設備などのインダストリアルデザイン、
UXデザイン(User Experience ユーザー体験=ユーザーがその製品、サービスを使う使用感のデザイン)、
タブレットやモニター、サインなどのUI(ユーザーインターフェース)デザイン、
グラフィックデザインなどの詳細デザインです。
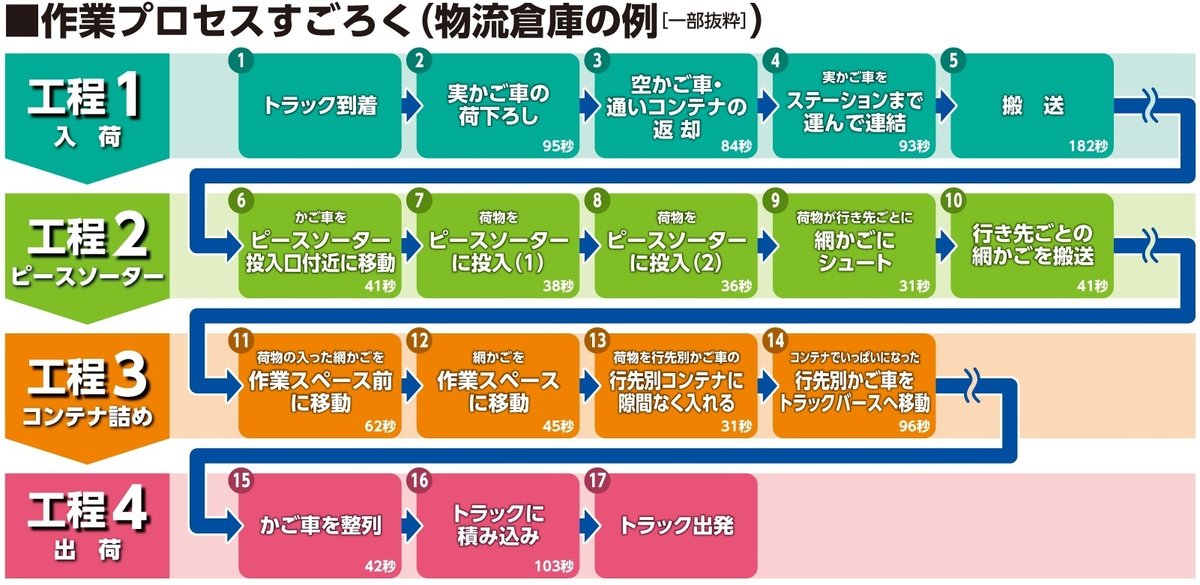
現場観察から始まって現状分析、ときには単工数分析の果てしなく地道な作業を乗り越え、お客様とやり取りをしながらの提案づくりと長い助走を走ってきたのは、このデザインをするためのものでした。
サークルマスター
これまでに様々なデザインをしてきました。
「村岡のデザインは、丸いものが多いよね」ということから、技術やSEの部署からは”サークルマスター”という称号(?)もいただいています。
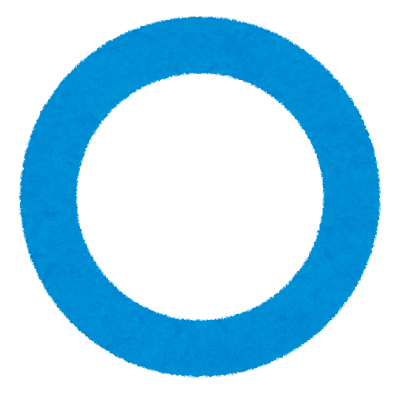
自分ではあまり意識していなかったのですが、言われてみると確かに丸いものやアールの付いたデザインが多いように思います。
そう言えば、前の会社でも「四角いデザインを丸くする男」と呼ばれていたような気がします。
たしかに、丸いカタチのAGVをデザインしたこともありました。
しかし、これは自分の好みだから丸くしたという訳ではありません。
AGVをできるだけ人が作業するブースに近付けたい。しかし、近付いたAGVが素早くその場を離れるには、その場で回転して反転しなければならない。
四角いAGVが回転するには対角線の長さの余裕が必要になるので、丸いカタチが一番近付けることになります。だから、丸いAGVにしました。
前職の医療機器でも「患者さんをなごませたい」という意図で、デザインに丸いデザインを取り入れていたのです。
ネジは隠すな!と怒られ
デザイナーとしては、ネジはできるだけ隠しておきたい。
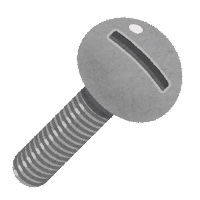
営業とこんな会話をしたこともありました。
営業
「今はまだ見積り段階で、設計段階じゃないんで、まだですけど、『あいつ(私のこと)に、ネジ見えへんところにつけるのだけはやめさせろ』と言われてます」
デザイナー(私)
「いやいや、ネジは見えないところにつけてこそのネジですから」
営業
「いやいやいや、それちゃいます。絶対駄目ですって。メンテナンス性すっごい悪くなります。現場の人はやっぱりすぐにパっとアプローチできないと。アプローチするところにネジがないと、それはダメ、工業的には絶対ダメです」
デザイナー(私)
「ネジを隠したうえで、見えるところにフタを外した取れるようにして、そこに三角を書いておきます。シールか何か、三角の形のネジみたいな」
営業
「いやいやいやいや、絶対不採用になる。これはリアルに現場でメンテナンスをしてきた立場から言うと、ほんまにネジは出してくださいって」
デザイナー(私)
「そうなんですか。いや、マジで困ったなぁ」
営業
「ほんまに苦労するんですって」
デザイナー(私)
「医療機器はネジを出さんとってくれって、現場から言われるんです。なんでかって言うと、お客さんが自分で回せては困ると。」
営業
「逆です。FA(Factory Automation)は、物流もそうですけど、お客さんが触るんで。というかお客さんに触ってもらわないと毎回全部シャープで対応できるのかっていう話です。絶対にアプローチしやすいように。やっていくべきですよ。これから、絶対マジで、マジで気をつけてください」
デザイナー(私)
「これから調査します」
営業
「そら、ネジ見えないほうが見た目キレイに決まってるんですけどね。」
デザイナー(私)
「ネジ問題は前の会社でもずっと気にしてたんですよ。一つの装置に何個ついとんねんみたいな、ネジが多すぎて。外すのにものすごい時間がかかってるんじゃないかと。」
「『ネジを無くせ』、そういう話もあったんですよね。じゃあ、簡単に外せるカバーを作ったらいい。外したいときには外せる。」
「そういう発想でいくともしかしたら、ネジじゃないのかもしれないとか、ていうのは思ってます。一発で開けることができるけど、普段は開け方わからないような。もう、なんかもうネジ問題が高じて、ちょっとネジ自体をいま考えています」
…
AGVにおける良いデザインとは、何でしょうか。
製品開発におけるデザインの役割は、前職の医療機器でいえば、
人の命が助かること、
より元気になることに、
フォルムやユーザビリティ、環境やブランドのデザイン結果が寄与できていることです。
AGVのような無人搬送車の場合も基本的に同じだと考えています。
僕たちの提案したソリューションの導入によって、
安心して仕事ができる、仕事が楽しく、好きになる。
実際に働いてみると
3Kといわれるような従来のイメージとは違う、
オフィスで働いているように快適で、
世の中の先端を創っているような職場環境に変えていけたら、
良いデザインだと言えるのではないでしょうか。
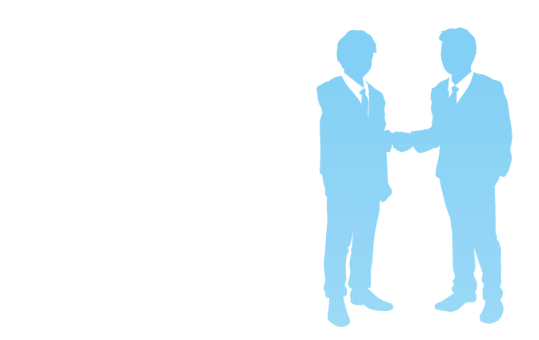
これらは人と一緒に働くロボットの話ですが、シャープのソリューションは、お客様によっては完全無人化をご提案するかもしれません。
そうなった場合は、いかに自然に結果を取り出せて、自律した生命体のように環境に負荷をかけず持続可能な事業活動を続けていけるかが、良いデザインの条件になってくると思います。
AGVや周辺機器のデザインを見ていくと、特に海外メーカーにデザイナーとしてリスペクトすべきものはたくさんあります。
ですが、シャープのように現場見学段階から施工・運用立ち上げまで、デザイナーが技術やSE同様にアサインされている開発スタイルの会社はほとんどありません。
AGVや周辺機器のデザインはもちろん、
「導入効果を出すこと」
「作業者の居住性や健康」
にデザイナーがこだわっている
のがシャープの特長です。
前職では専門的な装置であったので「性能を出すのは技術の仕事」と考えていましたが、AGVの開発は、世の中にまだないソリューションを生み出す仕事ですから、デザインも技術と同様、「導入効果=性能」を出すことに責任があると考えています。
シャープのAGVを導入して
「作業がしやすくなった」
「作業効率が上がった」
「生産性が向上した」
というデザインをこれからも追求していきますので、今の作業のこんな課題が解決できないかという困りごとがありましたら、気軽にご相談ください。
導入の効果出しまで寄り添うのが、シャープのデザイナーです。
また、もしこの記事が少しでもお役に立ちましたら、
ハートマークのスキボタンを押していただけると励みになります。
よろしくお願いいたします。
【2023年2月14日追記】
物流倉庫を多階層構造にすることで、収納力が1.5倍以上に拡大
自動搬送ロボットにより、ピッキング作業の省力化とスピードアップを実現します。
主な特長
1.物流倉庫の商品保管スペースを多階層構造にすることで、収納力を1.5倍以上に拡大
2.GTP(Goods to Person)方式により、自動搬送ロボットが商品棚をピッキング作業者のもとまで搬送。生産性の向上や人為的ミス抑制に貢献
3.規模に応じた3タイプ(100m2/250m2/500m2向け)の基本パッケージをご用意。個々のニーズに応じた柔軟なカスタマイズも可能
【関連記事】
【関連note】