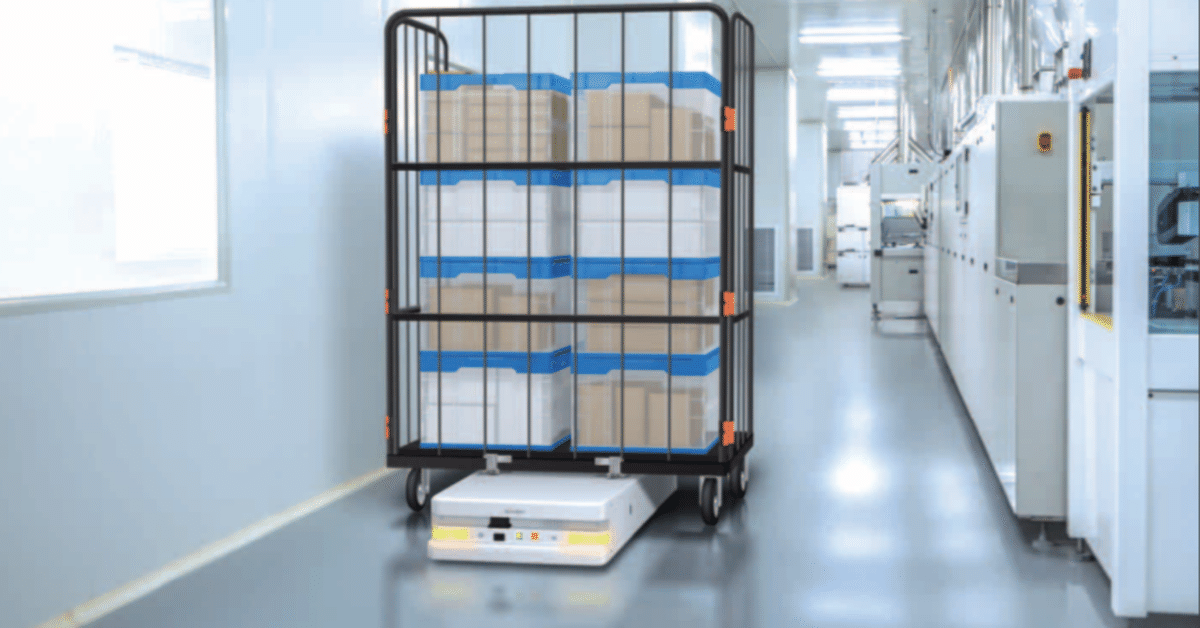
なぜAMRが動かなくなったのか
AGVが動かなくなったんですが…。
それは、僕が数カ月前に導入を終えたお客様からのお電話でした。
導入していただいたのはガイドレス(無軌道)モデルのAGV。
一般にはAMR(Autonomous Mobile Robot)と言われる無人搬送車です。
まず、現場のご担当者様に動かなくなった状況をお聞きしました。
「昨日まではちゃんと動いていたんだけれど、
今日になってルートの途中で急に動かなくなったんです」
「動かなくなった場所の近くに、今日、何かものを置きませんでしたか?」
と、ご確認していただくと、新しい人が入ったのでAGVが走るルートの近辺に作業台を設置していたことが分かりました。
そこで、「その作業台をルートから少し離してみてください」とお願いすると、AGVはまたちゃんと動き出すようになりました。
申し遅れました、シャープ AGVプロジェクトマネージャー 清水 一寿です。
もし、この記事が少しでもお役に立ちましたら、ハートマークのスキボタンを押していただけると励みになります。
僕はプロジェクトマネージャーとして、AGV導入プロジェクトを提案から見積もり、受注後の社内開発、導入立上、アフターフォローの技術側のとりまとめ業務を担当しています。
シャープがガイドレス(無軌道)モデルのAGVを開発して以降は、その案件を中心に担当し、これまでたくさんのお客様に導入してきました。
導入立上の際には、お客様のご要望通りにAGVが動くかのテストを入念に行いますし、現場の皆様に取り扱いで注意していただきたいこと、メンテナンスやトラブルなどへの対処をご説明していきます。
しかし、定着するまでは冒頭のような「動かなくなった」というようなご連絡が来ることがあります。
それは、AGVの中でも新しい無人搬送車であるガイドレス(無軌道)モデル、つまりAMRの特性がまだ広く知られていないからかもしれません。
ここでは今後のAGVの主流になるであろうAMRの導入のポイントや可能性について、僕の経験からお話をさせてください。
■AMRはなぜ動かなくなってしまうのか?
同じ無人搬送車でも、従来からの有軌道モデルでは、お客様から「動かなくなった」という連絡を受けることはほとんどありません。
AMRが動かなくなってしまう原因をご説明する前に、AGVとAMRの違いをおさらいしてさせてください。
AGVとAMRの違い
AGV(有軌道モデル)は、床に貼っている磁気テープをトレースしながら走行していきます。
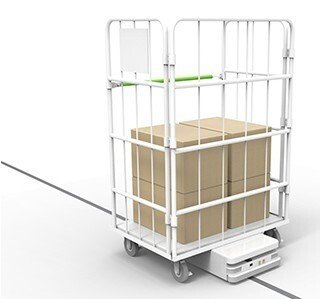
もう少し専門的なお話をすると、磁気テープの下には非接触で情報を読み取れるICタグ(RFIDタグ※)がポイントとなる位置に設置されていて、AGV本体はそれを読み込んで磁気テープ上のどこを走っているかを特定しています。
※RFID:Radio Frequency Identificationの略。情報が書き込まれたタグと電波などでワイヤレス通信し、情報の読み取り等を行うこと。
磁気テープのガイドに沿って走るので
・軌道がずれにくく、走行精度が高い
・停止精度が高いので、他の機器との荷物の受け渡しなど連携がしやすい
というメリットがあります。
それに対して、
ガイドレスモデル(AMR)は、あらかじめマップ編集ソフトで設定されたルートを各種のセンサを使って装置自体が自己位置を推定し周囲の状況を確認しながら、自律的に走行します。
当社のAMRは、カメラやレーザーなどのセンサと、エンコーダ(機械的な移動量、方向や角度をセンサで検出する装置)やジャイロセンサなどを搭載し、独自のアルゴリズムで高精度な自己位置認識と障害物検知を実現しています。
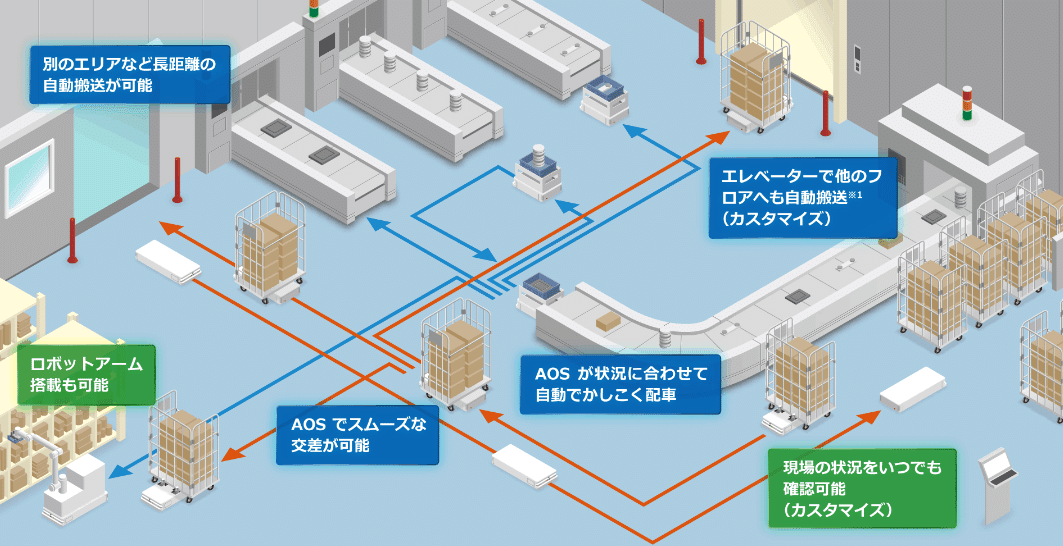
・磁気テープなどガイドを施工する必要がないので、頻繁に配置変更を行う工場や倉庫でも、手軽にルート変更が可能
というのが、一番のメリットです。
また、有軌道のAGVもAMRも人や物などの障害物を検知して自動停止しますが、AMRはルートの通路幅に余裕がある場合は、障害物を回避して走行が可能というメリットもあります。
冒頭でお話しした「動かなくなった」トラブルの原因は、
あらかじめ設定されている地図にはない作業台をAMRが障害物として検知し、回避できないと判断して止まってしまった
ことでした。
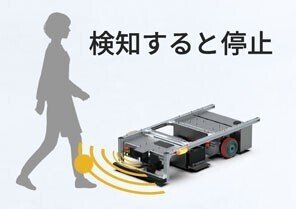
AMRは走行ルートに多少のずれが出ることを考慮して、有軌道のAGVよりも少し余裕のある通路幅が必要になります。
また、AGVの場合は磁気テープが貼られているので走行ルートが見た目で分かりますから、ルート上に障害となるような物を置かないなどの対策が徹底しやすいですが、AMRではルートが見えないので、ついついルート上に物を置いてしまうことが起きやすいのだと思います。
最初の問い合わせは圧倒的にAMR
「AGVを導入したい」というお問合わせで、お客様からまず聞かれるのはAMRについてです。
何と言っても
「磁気テープを貼らなくても導入できる」
というのは大きな魅力で、もう10年以上AGV を使っておられるお客様でも、「磁気テープがいらないならAMRに切り替えたい」とおっしゃる方も多くおられます。
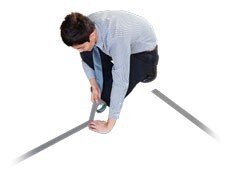
磁気テープを施工するには、走行ルートの決定から「墨だし」という仮施工をして走行テストを行い、問題がないと確認した後、本施工へと進みます。走行する距離やコースの複雑さにもよりますが、最低でも1週間程度、長ければ2週間ほどかかる場合もあります。
施工後の補修やメンテナンスはそれほど手間のかかるものではありませんが、最初の施工は時間もコストもかかる作業になりますから、有軌道ではルートを手軽に変更するという訳にはいきません。
フォークリフトが行き交う現場なので、
これまでは磁気テープが貼れず、AGVが導入できなかったが、
AMRなら導入できるのではないか
というお問い合わせも多くいただきます。
フォークリフトなどの作業車が通ると磁気テープをいためてしまうので、有軌道ではその場所を避けるなどルートを変える必要がありましたが、AMRは安全が確保できていれば、そうしたルートの制約はありません。
そうしたメリットがあるAMRですが、一方で、有軌道に比べて走行精度や停止精度が低いというデメリットがあります。
そこで、通常のところはガイドレスで走行し、他の機器に荷物を受け渡したり、集荷場に運んできたカゴ車や台車を整列して並べるなど、正確な位置決めが必要なポイントでは磁気テープで誘導するという方法が取られます。
つまり、有軌道とガイドレスの両方の機能を備え、ガイドレスのルートと有軌道のルートを自動で切り替えるハイブリッドの無人搬送車です。
シャープのガイドレスモデルは、すべてハイブリッド
となっています。
ですから、他の設備との連携など、従来のAGVと同様に多彩な使い方ができ、生産現場や物流倉庫など、様々な場所で導入いただいています。
「シャープのAMRはどんな現場でも導入できる」と言いたいところですが、やはり苦手な現場もあります。
それは環境の変化が多いところです。
午前中と午後で荷物の置き場所が変わる、繁忙期には臨時の機械を設置するなど、現場環境が頻繁に変わるところは、AMRの走行が安定しないケースがあります。
見た目で分かる変化は対処しやすいですが、人ではあまり変わっていないように見えていても、AMRからは大きく変っているような変化もあります。
AMRの目から見た「環境が変わる」とは?
先にお話したように、AMRは本体に設定されている地図に基づいてセンサで自己位置を推定しながら走行していきます。
地図には壁や柱、設備など動くことがないものを基本に設定し、AMRはその壁や柱、設備などとの距離感を読み取りながら自律走行していきます。
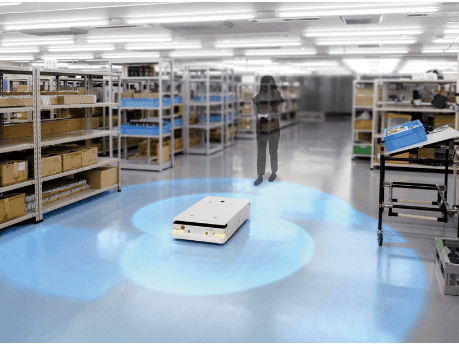
ルート上に人が立っていたり、荷物が置かれていると、それは地図にはない障害物として判断します。自分の本体と台車の大きさを計算しながらルート上で回避できると判断すれば、障害物を回避して走行していきます。
しかし、例えば、地図上の基準としている柱の横に荷物などが置かれていると、AMRが地図と違うと認識してしまい、不安定な動きになることがあります。
逆に、いつも荷物があるものとして地図に描いてしまうと、荷物がなくなってしまった時に地図とは違うと認識してしまい、これも不安定な動きになることがあります。
この状態を人で例えると、こんな感じになります。
机が並んだ部屋を、入口から3番目の机を左に曲がって、そこから2番目の机のところで右に曲がると出口に着くというような地図を事前に渡され、覚えたとします。
目隠ししていても机の配置が変わっていなければ、出口にたどり着くのはそれほど難しいことではないでしょう。ところが、机の配置が変わっていると、出口にたどり着くのは非常に難しくなります。
AMRを安定して運用するためには、「環境の変化をどう抑えていくか」
が大きなポイントになります。
■トラブルに対処する方法
AMRの導入は事前に環境の変化などを考慮に入れながら、地図やルートの設定を行っていきます。それでも、動かなくなったり走行が不安定になったりするトラブルが起こることがあります。
その対応も見ておきましょう。
導入当初のトラブルは、冒頭でご紹介したような何か物を置いたり、移動したことで起こるものが多く、その場合は、置いた物をどけてもらったり、もとに戻してもらうことで復旧すれば問題ありません。
障害物をもとに戻してもAMRが動かない、原因が分からないという時は、
ログデータを解析して、トラブル原因を特定します
当社のAMRは走行していた直前の何分間の
・レーザーセンサのスキャンデータ
・タイヤの回転数の計測データ
・加速度センサのデータ
などのデータを本体に保存するようになっています。
こうしたログデータは、導入時にお渡ししているメンテナンスツールで簡単に取り出せるようになっていますので、そのデータをお送りいただき、当社のコンピュータで動きを再生し、解析することでトラブルの原因を特定していきます。
また、本体とは別に集中制御システム「AOS(AGV Operating System)」には直前の動きだけでなく、さらに長い時間の走行データが保存されています。
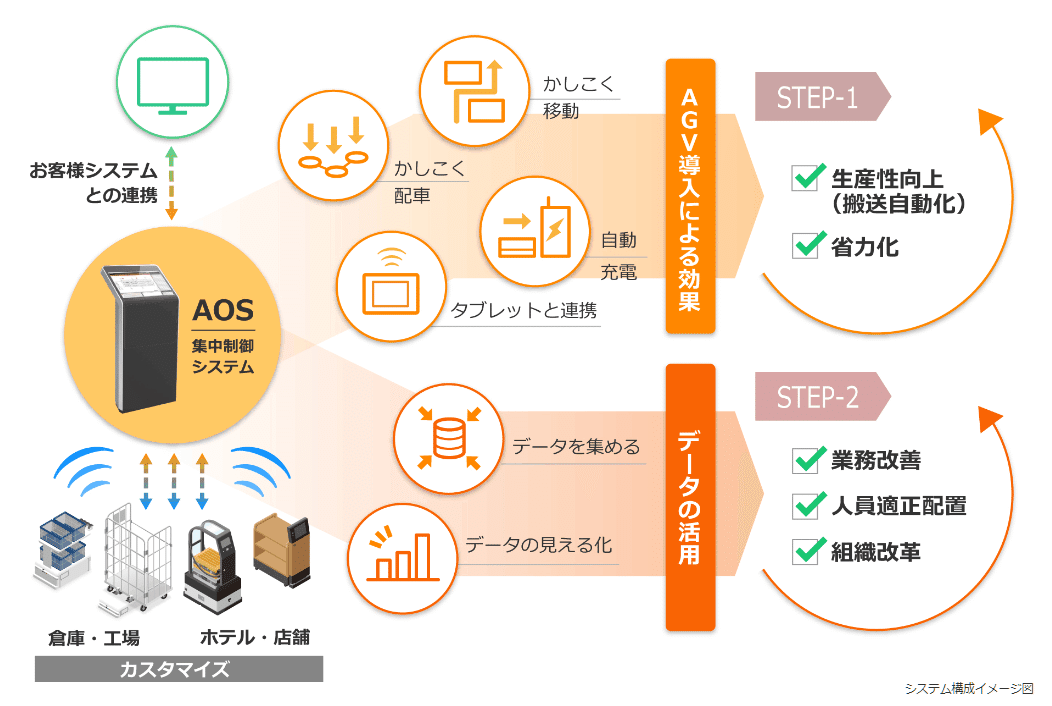
ほとんどのケースでは本体のログデータで原因は特定できますが、万が一トラブルが頻発するというようなケースでは、制御システムのデータも参考にしながらどこでトラブルが起こったか、より深く分析していきます。
シャープではトラブルに適切に対応することで経験とノウハウを積み重ね、様々な環境の現場にAMRの導入を広げてきました。
僕が担当した導入例から、2つほど紹介させてください。
1つは、温泉熱を利用してパプリカを周年栽培する大規模農業施設への導入事例です。
収穫したパプリカを積む台車は約200㎏にもなり、それを栽培室から集出荷室まで運ぶというもので、最も遠いところでは約180mも離れています。
重い台車を牽いて何往復もする作業は大きな負担になっているので、それをAGVで自動化できないか
というのが、導入前の課題でした。
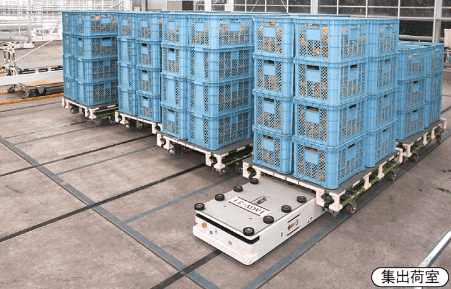
栽培室では収穫などの作業をするために金属製の車輪を付けた高所作業車が通り、磁気テープを貼ることができません。
そのため、ガイドレスモデルで搬送するしかありませんが、広大な施設でAMRが自己位置を推定するための目印となる柱などの構造物があまりなく、頼りになるのは苗を植えるために規則的に並んでいるバー状の設備でした。
ところが、そのバーは床から少し浮いた位置に設置されているため、AMRのレーザーセンサがスキャナできるかできないかのギリギリの位置にあります。そのため、最初のテスト走行では動きがとても不安定でした。
そこで、
地図の作成に工夫をする
ことにしました。
AMRが見えるものを人間の目で再現することは難しいので、通常は、リモコンを使ってAMRを走らせてみてベースとなる地図をつくり、どこを走るかのルートを設定していきます。
この農園の栽培室では、その方法では走行が安定しなかったので、
そのバーをレーザーセンサが反応するかどうか分からなくても、あるものとして地図に入れておくことにしました
AMRはレーザーセンサだけでなく、タイヤの回転数や加速度センサのデータを組み合わせて自己位置を推定していきます。レーザーセンサで地図上のバーの何本かは読み取れなくても、読み取ったバーで自己位置を補正するようにしたのです。
そうした工夫で、AMRは非常に安定して走行できるようになりました。
こうした調整や現場に即したカスタマイズで、非常に使いやすい無人搬送を実現できたと、お客様に大変喜んでいただきました。
また、僕自身も当社にとっても、農業施設という生産現場や物流現場とはまた違った環境への導入は、とても良い経験になりました。
もう一つの事例は、環境が安定しない現場へのAMRの導入です。
これは物流倉庫でも、生産工場でもありました。
提案時のご説明から、AMRは環境の変化があると走行が不安定になるので、
「できるだけ環境を整えてください」
とお願いしていましたが、それでも業務上でどうしても置かざるを得ない物が出てきます。
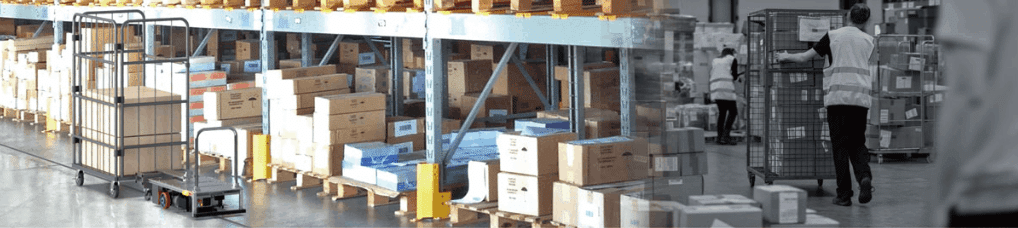
導入の立上テスト期間中も走行が不安定になることが多く、テストがいつ終わるか分からないという状況になりました。
お客様に環境を整えていただくようお願いするだけでなく、当社の方でもソフト開発の担当者に協力してもらって、対応を検討しました。
先ほどお話したように、AMRはレーザーセンサ、タイヤの回転数や加速度センサなどのデータを統合させて自己位置を推定し、走行しています。
導入先の物流倉庫も生産工場も床面は綺麗に整備されていて、AMRのタイヤはグリップがしっかりきき、空転が起こりにくい現場でした。
そこで、ソフト開発の方で
自己位置の推定方法
をタイヤの回転数を重視するように「味付け」をしてもらいました。
つまり、タイヤの回転数の精度が高いことをプログラムに反映させて走るようにすることで、ルート周辺の環境が変化する影響を相対的に下げるようにしたのです。
そうした対策で多少の環境変化でもAMRの走行は安定するようになり、無事導入できました。
こうした対応ができたのは、
シャープは開発と営業の距離が近い
からだと思います。
お客様からこんな要望をいただいたけれど、それを実現するにはどうしたら良いか、こんなカスタマイズはできないかなど、開発陣に気軽に相談できる体制があります。
それもハードウェア、ソフトウェアの両方で対応できますので、お客様との接点になっている営業やプロジェクトマネージャーは非常に心強いものがあります。
■AMRの進化の方向性
磁気テープで誘導するAGVは、もう何十年という歴史があります。
カゴ車を牽引するための機構や、障害物を検知するシステム、複数台を制御するシステムなど、周辺機能は近年でも進化を続けていますが、基本的な走行機能では技術的に確立されています。
だから、安定的に運用ができるという点で、現状でも最も信頼度があります。
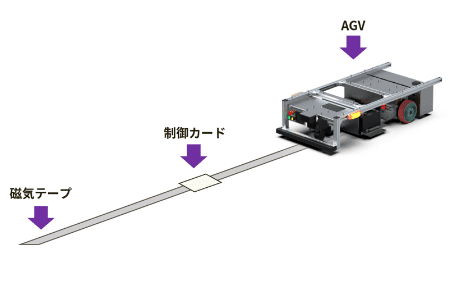
それに対してAMRはまだまだ新しい技術で、無人搬送車として進化の余地が残されています。ここでは僕が個人的に考えるAMRの進化の方向性をお話したいと思います。
AMRはあらかじめ設定された地図をもとに決められたルートを走り、荷物を運んでいます。設備などのレイアウト変更があった場合には、専用のソフトを使って地図を更新してルートを設定します。
地図をなくすという訳にはいきませんが、多少の変化であれば、
AMRが地図を自動で更新していく
という新たな機能を付けることが考えられます。
この機能があれば、多少の環境の変化があってもAMRは安定して走行できるようになります。ただし、地図をどのような基準で更新していくかが、ノウハウになると思います。
シャープは物流倉庫や生産現場から、飲食店、農場などいろいろな環境の現場にAMRを導入していますから、そのノウハウを活かしてどんな現場でも対応できる優れた地図更新機能を開発することができると思います。
設備の横にピタッと止まる
現状のAMRは停止精度が低いため、設備などと荷物の受け渡しをする場合には、停止させたい位置の周辺に磁気テープを貼って、AMRを正確な位置で停止するよう誘導する方法をとっています。
その磁気テープをなくして、AMRが自律走行して設備の横にピタッと止まるような機能が求められています。
これを実現するには設備の位置を正確に認識するようなセンサや、AMRの姿勢を制御する技術など、より高度な技術が必要になります。
シャープの開発陣はそれだけの技術は有していますし、また、AGVの設備連携で豊富なノウハウを持っていますので、十分実現可能だと考えています。
次に安全面では、
より広く周囲の形状を認識できる立体カメラの搭載
が考えられます。
現在の検知方法では、本体上部の障害物を検知することが難しく、台車などの高さがあるものを運搬中に上部から飛び出している障害物を引っかけてしまうという課題があります。
立体カメラを搭載することで、例えば、ルート上で人が手を出しているような場合にもそれを回避したり、停止したりすることができるようになり、より安全性が高まります。
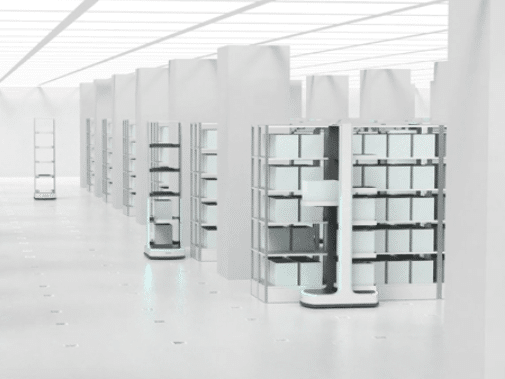
年々、AGVのニーズが高まり、使い方も多様化しています。特に、近年の物流センターでは業務に合わせて複数の種類のAGVを導入するケースも増えています。
1社のAGVメーカーで多様化するすべてのニーズに応えることは難しくなってくるでしょう。一カ所の現場に複数のメーカーのAGVが走るというケースは、これからどんどん増えてくると思います。
その際に問題になってくるのが、制御システムです。
メーカーごとにシステムが違ってくるというのは、お客様にとって不便になってくるので、将来的にはメーカーの枠を超えた統合ソフトが必要になってくるでしょう。
これはAGV業界全体に関わってくることですので、いつ実現できるか分かりませんが、少なくとも制御システムの重要性がこれまで以上に高まってくることは間違いないと思います。
■良いAMRを見極めるポイント
慢性的な人手不足やネット通販の急速な拡大などで、無人搬送車の需要は拡大しています。
なかでも磁気テープを貼らなくていいガイドレスモデルへの関心は非常に高くなっており、展示会ではこれまでAGV とはあまり関係ないと思われたメーカーさんが次々と新規参入されているのをよく見かけます。
まさに、AMRブームという状況です。
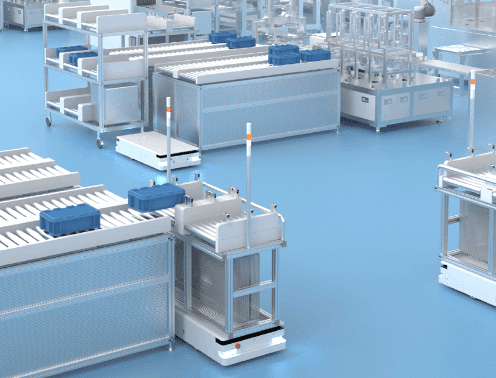
様々な製品が登場するなかで、どう選んだら良いのかと悩まれるお客様も多いでしょう。
多様な現場にAMRを導入してきた経験を基に、お客様にあったAMRを見極めるポイントを紹介していきましょう。
基本的な走行性能は?
荷物を運ぶために必要な基本的な走行性能、つまり積載許容荷重や走行速度、最小旋回半径、想定稼働時間、障害物検知といった安全性能などをまずチェックしていきます。
お客様が求められる運ぶ荷物の重さや稼働時間がその仕様にマッチし、また通路幅などが現場環境に適応していれば、導入の候補になってきます。
製品として市場に出す以上、試作して走行テストを繰り返しているはずですから、どの製品も仕様に基づいた性能を発揮すると思います。
つまり、走ることは当たり前です。
これまでお話してきたように、AMRはあらかじめ設定した地図のルートを各種のセンサを使って自己位置を推定しながら走行するというのが基本ですから
・環境の変化に弱い
という弱点があります。
また、有軌道のAGVに比べて
・走行精度や停止精度が低い
というデメリットもあります。
ですから、最初はAMRの導入を考えられていたお客様でも、運用の安定性を考えて有軌道のAGVを選ばれるケースは珍しくありません。
そうしたAMRの弱点やデメリットを克服するための工夫やノウハウをどれだけ持っているか、つまり導入を成功させるためには、多様な現場環境に対応するノウハウが大きなポイントになります。
それを見極めるには、本体だけでなくソフトウェアの機能や性能もしっかり見ておく必要があります。例えば
・地図を作成するソフトの柔軟性
・ルートはどのように変更できるか
・トラブルがあった際のソフトウェアの対応方法
などになります。
また、AMRは有軌道のAGVに比べてダイナミックな経路変更や障害物回避ができることが特長で、そのメリットを生かすために一つの現場に導入される台数は増えています。
当然、それを制御するシステムの性能も重要です。
制御システムは
・同時に何台のAGV・AMRを制御できるか
・衝突回避や迂回、合流制御など経路指示を効率良くできるか
・お客様のシステムと連携できるか
・各AGVの走行データを蓄積し、見やすく表示できるか
などが、ポイントになります。
僕の経験上、AMRでのトラブルはソフト的に対応することがほとんどです。
柔軟なソフト開発やソフトウェアのカスタマイズの対応ができるかどうかが導入がうまくいくかどうかの鍵になってくると思っています。
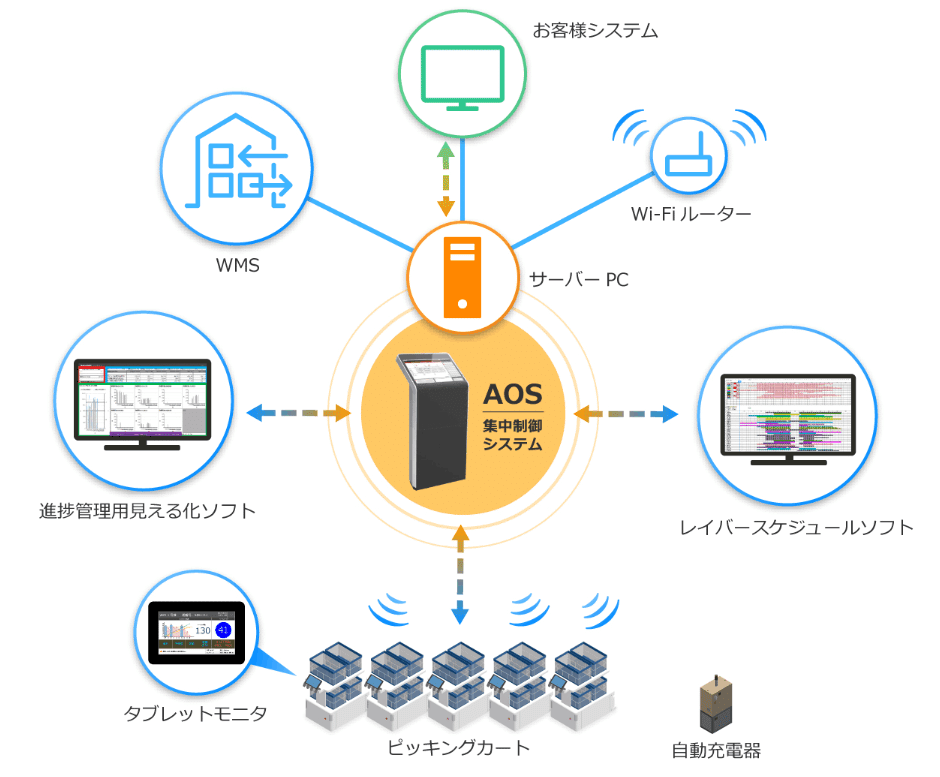
少し個人的なお話をさせていただきます。
僕はAGVの事業に携わる前に、自律移動式の業務用清掃ロボットの開発および商品化のプロジェクトに、実務リーダ役として携わっていました。
技術分野としては、データ解析などソフト系が中心で、清掃ロボットの開発ではシステム系の勉強ができ、今の業務にもとても役立っています。
現在、AGVのソフト開発を担当しているメンバーにも、その時の清掃ロボットの開発担当者がいて、中心となって活躍しています。
自律移動するロボットの制御やシステム開発に、豊富な知識とスキルを備えたメンバーが多くいることが、シャープのAMR開発の大きな強みです。
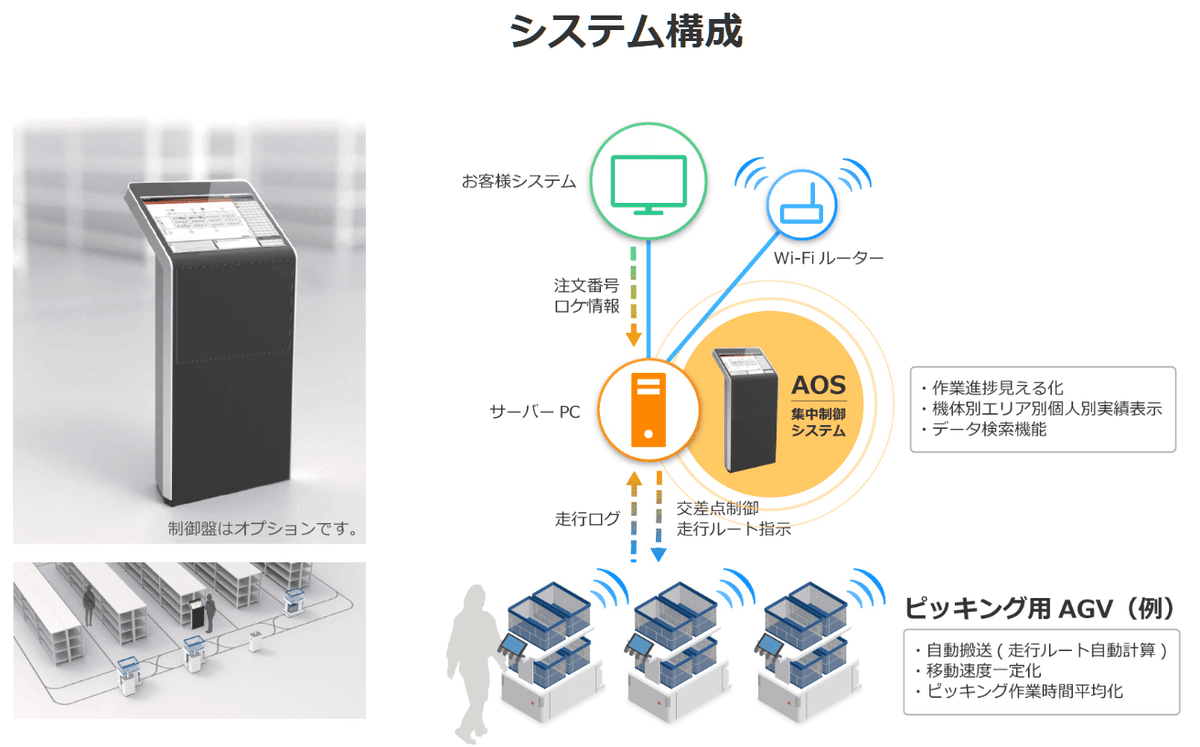
さらに独自の集中制御システム 「AOS」をはじめ、ソフトウェアの充実はお客様から高く評価されています。
AGVの制御ソフトウェアが充実していることは、自動搬送の効率を高めるだけでなく、業務の効率化にもメリットが生まれます。
当社の集中制御システム「AOS」では、蓄積されたAGVの走行データを整理して各種見える化表示や、解析ツールを構築することがカスタマイズでできます。
AGVの稼働状況からモノの流れが一目で分かることで、業務上のネックとなっている工程が即座に把握でき、人の配置の最適化など迅速な業務改善に貢献します。
最後に、より効果が上がるAGVの導入方法について考えてみましょう。
■より効果が上がるAGVの導入方法
例えば物流倉庫などでAGVを初めて導入するという場合
1. 倉庫の一部の業務にAGVに入れて、様子を見ながら拡張していく
2. 倉庫の搬送業務のすべてにAGVを導入し、それに合わせて工程も全面的に見直す
の二つの方法があります。
新設の場合には2の方法になるケースがほとんどだと思います。
既存施設の場合には、1か2で迷われるでしょう。
僕の経験からすると、2の導入に合わせてすべての工程を見直す方が、うまくいっているケースが多いです。
1の方法も、中長期的な計画を立てて着実に効果をあげているお客様もおられます。
しかし、人の配置などが大きく変ることがないことから、現場の方にとってのインパクトはどうしても弱くなります。AGV導入の効果が見えづらいことから、結果的に次のステップに進ことが難しくなるケースもあります。
2の方法は、ある意味で退路が断たれますので、現場との調整などより入念な準備が求められます。
勇気のいる決断となりますが、僕の経験上、人の搬送からAGVの搬送に全面的に入れ替えて、従来に比べて効率が悪くなったというケースはありません。
日本では生産現場を中心に、改善を重ねて業務を効率化していくことを得意にしています。
しかし、AGVの導入はモノの流れのすべてにかかわる搬送の改善ですから、導入を機に工程を一気に見直してしまう方が、効果がでやすいと思います。
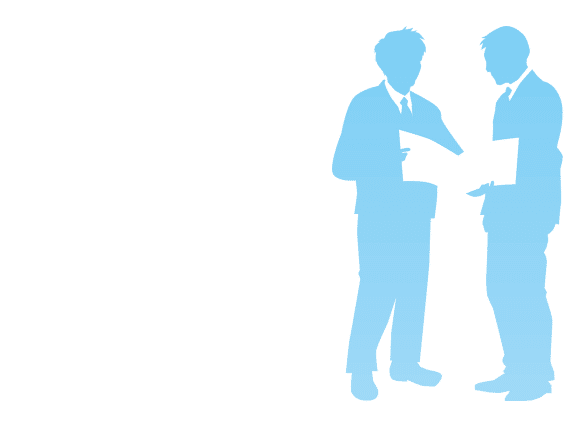
どちらの方法でも、
シャープは豊富な経験とノウハウでお客様を全面的にサポートし、
AGV導入を成功に結び付けていきます
ので、どうぞ安心してご相談ください。
また、もしこの記事が少しでもお役に立ちましたら、
ハートマークのスキボタンを押していただけると励みになります。
よろしくお願いいたします。
【導入事例の一覧】
【関連note】