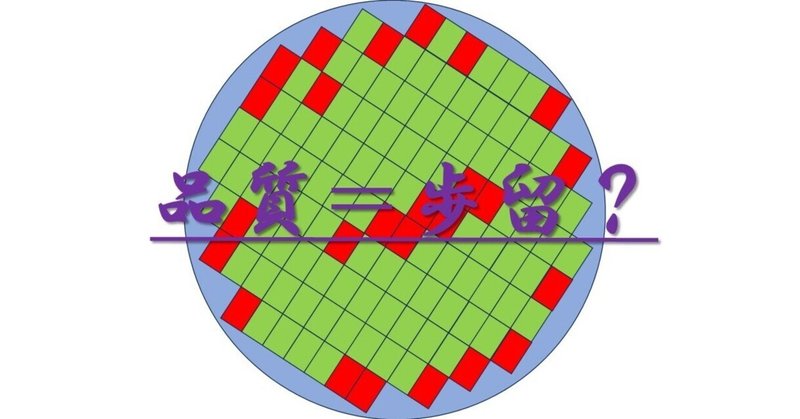
半導体製造現場の品質管理
はじめに
ここでは、高度にIoT化された半導体デバイス製造における品質管理の状況を説明させていただき、そのエッセンスをご理解していただいたうえで、他の製造業に係る方々の現場でも、品質管理に活かせることは無いか期待しています。品質管理でも、まずは見えるかですが、生産装置からのオンラインデータ取得が必要でありますが、そのデータの利用方法を述べさせて頂いております。
前提
半導体デバイスの製造はウェハを準備し、そのウェハを多数の工程で順次処理することで進行します。一般に、半導体の製造工程は、「前工程」と「後工程」の二つに分けられますが、ここでは、「前工程」の製造現場における品質管理に関して議論したいと思います。
その前にですが、半導体デバイスを製造するためには、その半導体デバイスが組み込まれて動作する電子機器から指定される要求性能が存在し、その要求性能を実現するための回路設計から品質の作りこみが実行されます。回路設計の結果である回路図は、その回路をシリコンウェハ上で作り上げるための露光パターニングマスクセット(数十枚の写真原版のセット)の作成が必要となります。このマスクセットを使い、「前工程」では、ウェハ上に回路が形成されていく工程が実行されます。半導体デバイスの品質は、これらの回路設計やマスクセットの出来栄えにも依存しており、「前工程」の作り込み品質へも大きな影響を与えます。更に、「前工程」で製造された半導体デバイスチップは、「後工程」のパッケージングが完了して、市場で利用される実際の半導体デバイスとして製品が完了しますので、「後工程」での作り込み品質も大きな影響があります。また、最終的な品質は、電子機器に組み込まれ、長年動作した時点で、その善し悪しが証明されることから、設計、製造、市場の利用状態までの製品の全ライフサイクルを通しての品質管理作業が必要です。
しかしながら、ライフサイクルは、数年から数十年に渡っての期間となってしまうので、半導体デバイスの「前工程」での品質管理は、ウェハ上のチップ収率である歩留まりを指標に活動が展開されます。当然、同一製品が、市場で品質異常を発生してしまった場合には、「前工程」の作り込み品質に立ち戻り、改善活動が実行されます。
「前工程」
製造ラインでは、小さい規模でも数万、大工場では数十万のウェハを仕掛として持っていますし、その製造過程では、一千を超えるような工程を処理されますので、それぞれのウェハ毎の各工程の出来栄えを管理することは、人間業では行えません。そのため、半導体製造工場では、早くから製造装置はオンライン化され、加工状況を電子データで管理出来るように構成されてきました。また、千工程を終了した時点で、不良品と判明しては、大きな損失を生むだけですので、工程のうち数十パーセントは出来栄え監視のための検査、計測のための工程が挿入されており、この計測結果も電子データとして監視対象として利用しています。
製造装置、検査・計測装置がオンライン化され高度にIoT化された「前工程」ラインでは、一般的に次のようなIoTシステムが整備されています。
① MES(Manufacturing Execution System)
② QCシステム
③ APC(Auto Process Control)システム
④ 自動着工システム
⑤ 自動搬送システム
⑥ ディスパッチャ―
⑦ EES(Equipment Engineering System)
⑧ FDC(Fault Detection & Classification) システム
⑨ 生産統計システム
⑩ 稼働管理システム
⑪ VM(virtual Methodology)システム
この中で、品質管理に利用されるシステムは、②QCシステム、⑦EES及び⑧FDCシステムです。品質管理に主に利用されるのは、その名の通り②QCシステムです。このQCシステムでは、歴史的には、検査及び計測工程のデータを扱っていましたが、近年、必要に迫られ、装置データをも監視対象として来ました。一方、ESSでは、装置の制御データを利用し、装置の挙動を高度に解析するために導入され、また、FDCシステムでは、更に一歩進んだ形で、製造装置の稼働状況や故障に至る過程を分析するシステムを指しています。
QCシステム
半導体デバイスの「前工程」である一千工程の中には、先にも述べたように数十パーセントに上る出来栄えチェック工程が含まれており、即ち、加工工程では、寸法測定、成膜工程では、膜厚測定に加え、その中には、異物検査工程が含まれており、抜き取り検査ではあるものの、ポイントとなる工程での出来栄えをチェックしています。検査装置もオンライン化され、検査結果を製品情報と関係付けてこのシステムに報告しています。これらのデータを工程、製品毎に収集、統計出来るシステムが、QCシステムです。即ち、各検査工程のデータを収集し、工程毎、製品毎に統計管理が出来るシステムです。
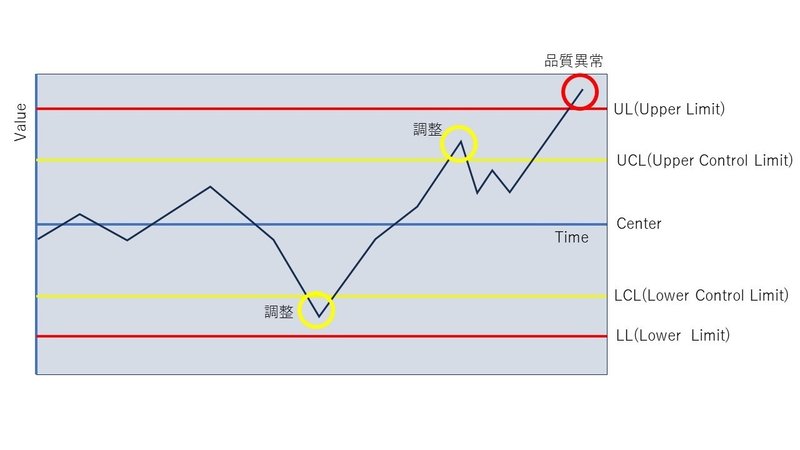
このQCシステムでは、規格管理が適用され、規格を逸脱した製品もしくは加工装置は、流動、作業が停止されて、品質確保のための復旧検討が開始されることになります。また、一般的には、規格の内側に、傾向監視のための管理規格が設定され、これを超えた場合、管理規格内に戻すための処置が検討されます。規格管理に留まらず、管理図管理、傾向管理が実現されており、品質異常を感知する警戒の体制が整えられています。生産装置は、日々その状態が変化して行くことが一般的で、出来栄えが規格を逸脱しない様に、定期的なメンテナンスや、作業条件の調整を、QCシステムの情報を頼りに実施します。
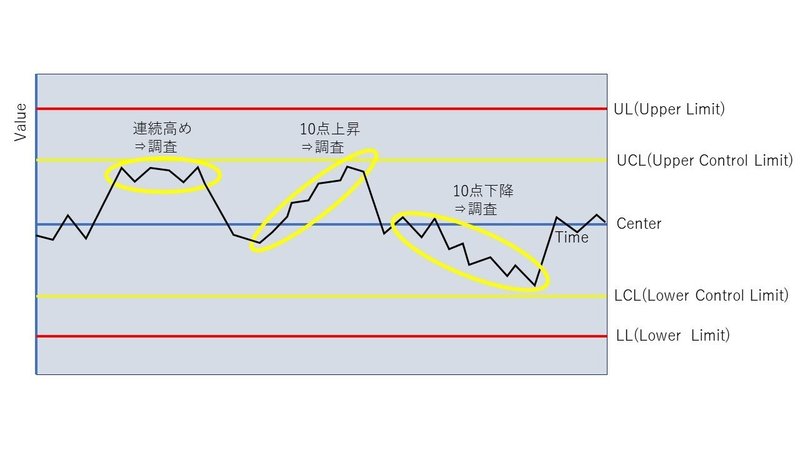
近年では、このQCシステムに検査装置の出来栄えデータに加え、生産装置から排出されるオンラインの各種重要パラメータを同じシステムで管理出来るようにしてきました。即ち、製品処理中の出来栄えに直接係る温度であったり原料供給量であったりする制御パラメータを直接観測することにより、工程毎に監視しようというものです。但し、このシステムでは、データ通信量が限られるため、扱えるデータは、製品処理中の各種パラメータの平均値、最小値、最大値に限られるのが一般的であり、監視も限定的にならざるを得ない限界はあります。しかしながら、過去の品質異常時の履歴を捉え、各種装置パラメータの変動状況のデータが存在すれば、異常に至る前の値に規格値の設定が可能となり、品質管理の大きな指標となります。
EES(Equipment Engineering System)
EESは、半導体製造装置から排出されるデータを利用するための統合したシステムで、主に装置メーカー毎に提供されているローカルなシステムです。主な目的は装置の有効稼働率(OEE:Overall Equipment Efficiency)を向上させることですが、収集されたデータは、平均値、最小値や最大値の様に、装着されたセンサーの代表値だけでなく、時系列データも扱える点で、超微細の半導体デバイス製造では、必須のシステムとなって来ています。
まず、データ収集と監視が主な機能で、装置から排出される生データを収集し、運用状況や異常を監視します。データはリアルタイムで収集され、そのサンプリング頻度も、100msec~1sec程度で収集可能であり、代表値からは非常に大きなデータが得られます。一方、装置メーカーには、装置の設計思想や、組み込まれている部品の特性も分かっており、詳細データにより監視すべきデータは理解しているはずで、加えて全世界に展開されている市場からのフィードバックもあることから、装置の安定稼働、品質維持に対する高度なアプローチが期待されます。
EESでは、専用のサーバーを設け、生産装置から排出されるオンラインデータをきめ細かく、多量に取得でき様にしています。このデータの解析には、これまで用いてきた統計的手法だけではなく、ビッグデータ解析の手法が導入され、多変量解析が広く利用されています。多変量解析の各種手法を駆使することにより、重要な問題を検出する事例も多く報告されています。
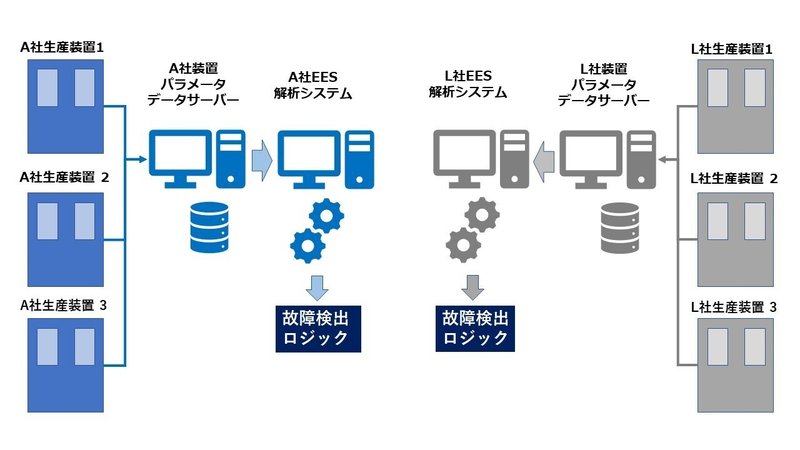
半導体デバイス製造で品質異常が発生した場合、このEESシステムで、解析することにより、膨大な装置データを利用して、事象の真因の追求が可能です。事象の原因が分かれば、対応策も立案できますし、同じ事象を回避するための監視すべきセンサーデータも分かることから、EESでの監視アルゴリズムの設定も可能となります。
事象のトリガーは、三つのパターンが想定されます。それは、①製品歩留まり低下、②検査・計測データの管理外れ及び③同一生産装置機種の同一センサーデータの比較から大きく外れているものの抽出であると思います。①の製品歩留まり低下では、歩留まりの予算や目標値が決まっていれば、一義的に問題装置が特定されます。②の検査・計測データの管理外れでは、当然、規格及び管理規格が設定されているハズで、外れ発生時には、対象設備と項目は、自動的に設定されます。一方、③の同一生産装置機種の同一センサーデータの比較は、未知の問題へのアプローチであり、解析工数の配分にも影響されますし、解析実行者のセンスにも寄る所が大きく、生産ラインの将来の業績を大きく左右する可能性を有していると思います。即ち、ここに投ずる工数と人材により、異常検知レベルが決定されますし、異常検知の感度設定により、生産量も左右されるという問題が存在します。但し、感度良く、異常発生の可能性のある生産装置を事前に見いだせれば、経営指標の向上に貢献できるでしょう。
FDC(Fault Detection & Classification)システム
FDCとは、製造装置からのセンサーデータをモニタし、異常を検出して分類することを指しています。その利用方法としては、データをリアルタイムで監視して、装置故障を検出し、迅速な対応することを目的にしています。故障による突然の装置停止を回避するもので、これにより装置の平均稼働率を向上させ、生産性を高めようとするものです。異常検知のための対象センサーデータの選出や、検出のためのアルゴリズムは、前述のEESでの解析結果を受けて、その結果をリアルモニター化する場合も多いと思います。また、故障やトラブル発生を事前に検知して、突発的な装置停止を回避出来れば、そこで発生する品質問題を防ぎ、製品の品質を安定化することも可能です。
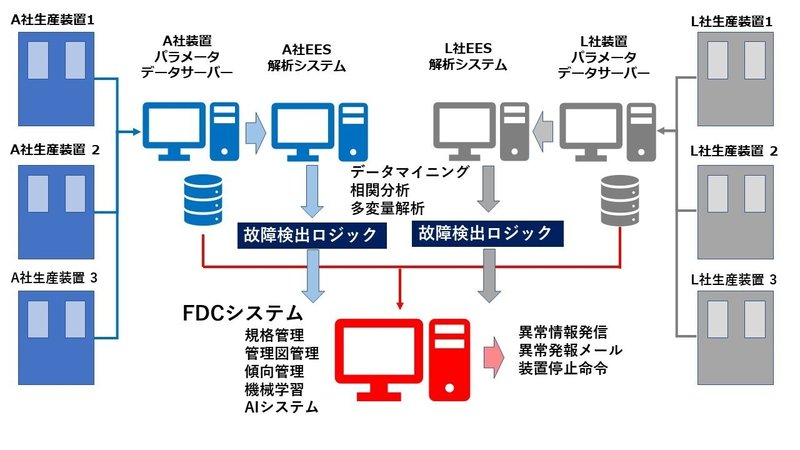
これまでのQCシステムでは、製品処理時のセンサーデータから得られる平均値、最小値、最大値等の代表値を用いているために、このシステムを装置異常の見地に利用しても、タイムラグが発生しており、異常発生装置の停止もしくはアクションは、その製品処理後や事象が検知された後の人が認知する数時間後、数日後の活動となってしまう問題がありました。これを解決するために、FDCでは、リアルモニターを実現するものであり、指定されたセンサーデータや設定されたアルゴリズムにより、装置停止や改善アクションのためのトリガーを上げるものです。また、対象センサーデータも、それまでが製品処置に影響を与える温度、圧力や原料供給量であったものが、ハード的なトラブル要因も対象としてきた点で革新的であります。ハード的なトラブル要因を検知するためには、例えば、真空ポンプの駆動電流や温度を対象として、ポンプ故障を事前に予知するとか、搬送系のロボットの振動データを対象として、駆動部の摩耗劣化による故障を事前に検知する等のアプローチが可能となります。これらを検知して事前に対応処置することを予知保全、予兆保全と言い導入が促進されてきています、予知保全が的確に実行されれば、突然故障時に発生する異常製品発生も抑制されますし、突然の設備停止による生産量のダウンの影響も、計画的に回避できることになります。
一方、半導体デバイスの微細化に伴い、短時間の制御状態の変動が問題となって来ています。また、生産装置での処理もマルチステップ化されて、センサー情報もレシピ内で複雑に変動することにより、大きなトラブルを生みことが多くなってきています。この様な状況下では、センサーデータの波形を利用することにより、高度な装置状態の判定が求められています。波形の変動は、人間の目には差異として良く認識できますが、ソフトウェアで判断することは簡単ではありません。
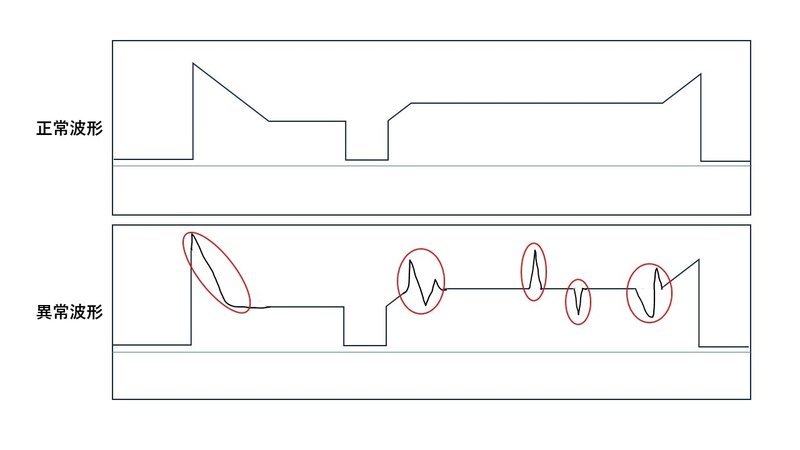
ここで登場したのが機械学習です。既に、株価の予測や気象データの予報の時系列データから未来を予測する方法として、リカレントニューラルネットワーク (RNN) や ロングショートタームメモリ (LSTM)が利用され、一部、実績を挙げていると聞いていますし、既存の波形から特徴量を抽出するためには、畳み込みニューラルネットワーク (CNN) や 1D-CNN が有効であり、半導体装置から排出される時系列データの異常判定にも導入が始まっています。FDCシステム内に学習システムと監視アルゴリズムの管理、配信機能を整備することにより、AIの利用も進められるでしょう。
FMEA
半導体デバイスが、車の制御系に採用されていく中で、要求される品質も、車載品質レベルが要求される中で、半導体製造へのFMEA(故障モード影響度解析)による重要工程把握が、必須となっています。FMEAは、製造プロセスに潜在する故障モードを事前に洗い出し、影響を分析評価したうえで対策を講じる解析手法です。量産前に、抽出された問題を最小限にしておけば、製品の信頼性向上につながるというアプローチです。製造ラインでは、工程FMEAを実施します。これは、 製造ラインで半導体デバイス製造工程での生じ得る問題に着目し、加工工程毎に故障モードを洗い出し、対策を講じます。その加工工程で発生するトラブルのモードを洗い出し、発生頻度と半導体デバイスの品質に与える影響度合いを指定して、この掛け算で影響度を算出し、影響度の高い工程を重要管理工程として認識することにより、品質監視のレベルを上げることにします。
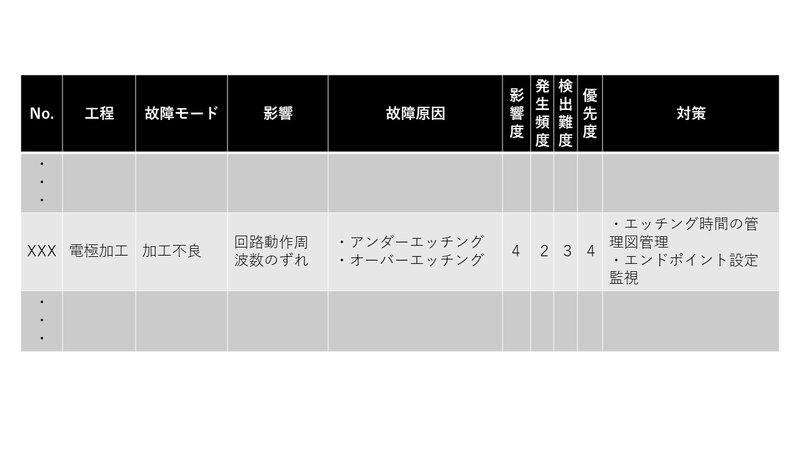
これにより、量産時の品質管理を初動から高いレベルで維持しようとするものであります。製造上のトラブルは、実際にトラブルを経験した関係者には強く記憶されますが、これを他者に共有することは難しいという問題があります。FMEA上でトラブルと重大性が記述されていれば、関係者への共有は的確に行えることになります。
一方、蓄積されたノウハウを活用して信頼性の高い製品を提供できるようになりますが、品質に異常を与ええるトラブルは、過去に発生したものでしか認識されておらず、未知のトラブルは、意識しようがないという問題があります。
管理項目、その内容の相互ベンチマーキング
この様に既知の品質トラブルについては、対象工程に適用されている生産装置のセンサーデータの監視が設定され、的確な品質監視が適用されているであろう。しかしながら、未知の品質異常は、それを予測することは不可能であるとともに、その時点では、監視されていない、もしくは、監視の網が緩いことから、実際に発生して見ないと、監視すべきセンサーや、その監視方法、監視レベルは分からない。そうなると、実際、異常が発生するのを待つしかない。そこで、展開したのが、管理項目のベンチマークです。これは、種類の異なった生産装置であっても、構成するユニット、部品や部材を比較して、他機種装置で実施されている監視状況、項目を採用検討していくというものです。例えば、エッチング装置と薄膜成膜装置であっても、真空ポンプや搬送ロボットは装備されているので、それぞれの部位で実施されている品質監視項目を比較して、無いものは適用展開を検討していくという作業です。担当するエンジニアは、目の前で品質異常が発生した場合には、当然、管理項目の追加と監視作業は、大きな義務を背負って、これを推進するわけであすが、まだ、発生していないトラブルに対して、新たに管理項目を追加して、監視作業を追加することには、大きな抵抗感が伴います。これを打破して、展開することは、品質管理責任者や経営者の手腕や思によるところが大きいことは間違い無いでしょう。
まとめ
半導体製造における品質管理活動は、数十万の仕掛ウェハを生産する中で、日々数百万工程・枚の生産装置での作業実績から得られるセンサー情報や検査・計測データから、異常データ、異常発生傾向を、如何に感度良く監視できるかという問題です。監視のレベルを上げれば良いのですが、日々数百万のウェハ作業量に対して、対象のセンサーデータ10個を対象としても、そのデータ量は、数千万件/日となってしまいます。その内、1割の異常監視として注目したとしても数百万件が抽出される分けで、とても人間が対応出来るものではありません。そこで、進め方としては、FMEAで重要工程、重要センサーデータを抽出して、注目データを絞り込みます。これらは、QCシステムでの監視設定はもちろんですが、EESやFDCを用いて、日々監視の網を張っておくことが重要となります。
一方、品質の最終的で絶対的な指標は、歩留まりですので、製品ウェハの生産が完了した後に得られる歩留まりと、それまでに得られているセンサーデータ、検査・計測データと比較検討することにより、歩留まり低下を引き起こしている工程を洗い出し、歩留まり低下要因の対策を打っていくことが重要です。
また、このアプローチでは、扱いデータが非常に膨大であることと、FMEAの所で述べたように、未知の問題に対するアクションは取り様が無いことから、良い歩留まりや、歩留まり程度の悪いウェハのセンサーデータを教師データとして、機械学習等を行うことを推奨します。持てるデータを有効に活かせるかが、今後の半導体製造の成否を決定するように思われます。
追記
半導体生産では、歩留まりとの勝負であることはご理解いただいていると思いますが、現実問題として、100%歩留まりは、殆ど現れません。通常は、下記の様に、良品と不良品がウェハ上に散在的に発生しています。
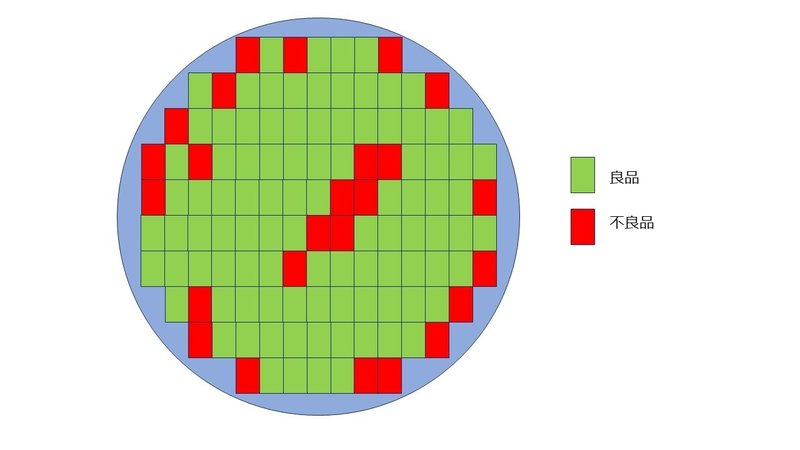
車載品である製品チップが、市場不良を生じると、お客様である車メーカーからお叱りを受けます。不良原因特定のために、上述の様に、不良品を生み出した対象ウェハを特定し、生産におけるセンサーデータ、検査・計測データと突き合わせて、工程での問題を探っていきますが、中々、真因には辿り着けない場合が多いです。その様なアプローチの中で、お客様から歩留まり状況を見せろというやり取りがあり、上図の様な図面をお見せしたところ、以下の様なコメントを受けたことが在ります。
『我々車メーカーは、傷のある車は出荷しない。半導体デバイスメーカーは、傷のあるウェハから製品を出荷するのか?』
こんなことを言われても・・・・ 100%歩留まりがほぼ有り得ない半導体デバイス製造に対して、そんな理不尽場要求をされても、対応の仕方がありませんでした。実情をご理解頂くしか御座いませんでした。
第1話
第2話
第3話
第4話
この記事が気に入ったらサポートをしてみませんか?