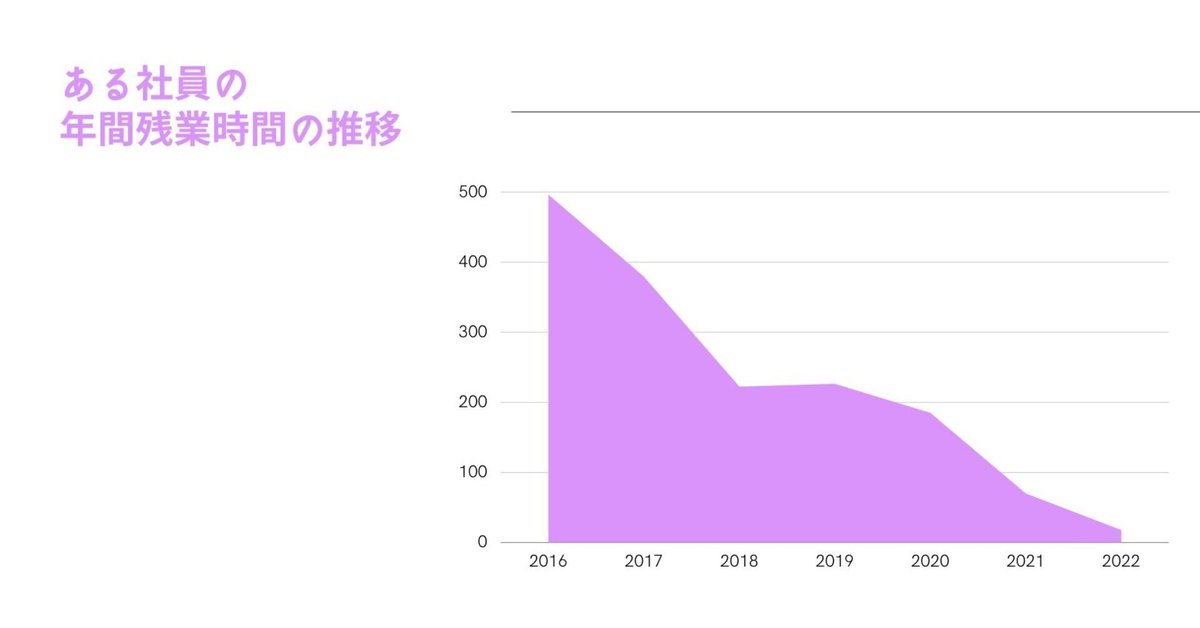
とある工場のカイゼン(2018-2022)
1.三田理化工業㈱ 消耗品事業部
三田理化工業の消耗品事業部は、洗浄滅菌済みの注射薬液瓶を製造・販売しています。
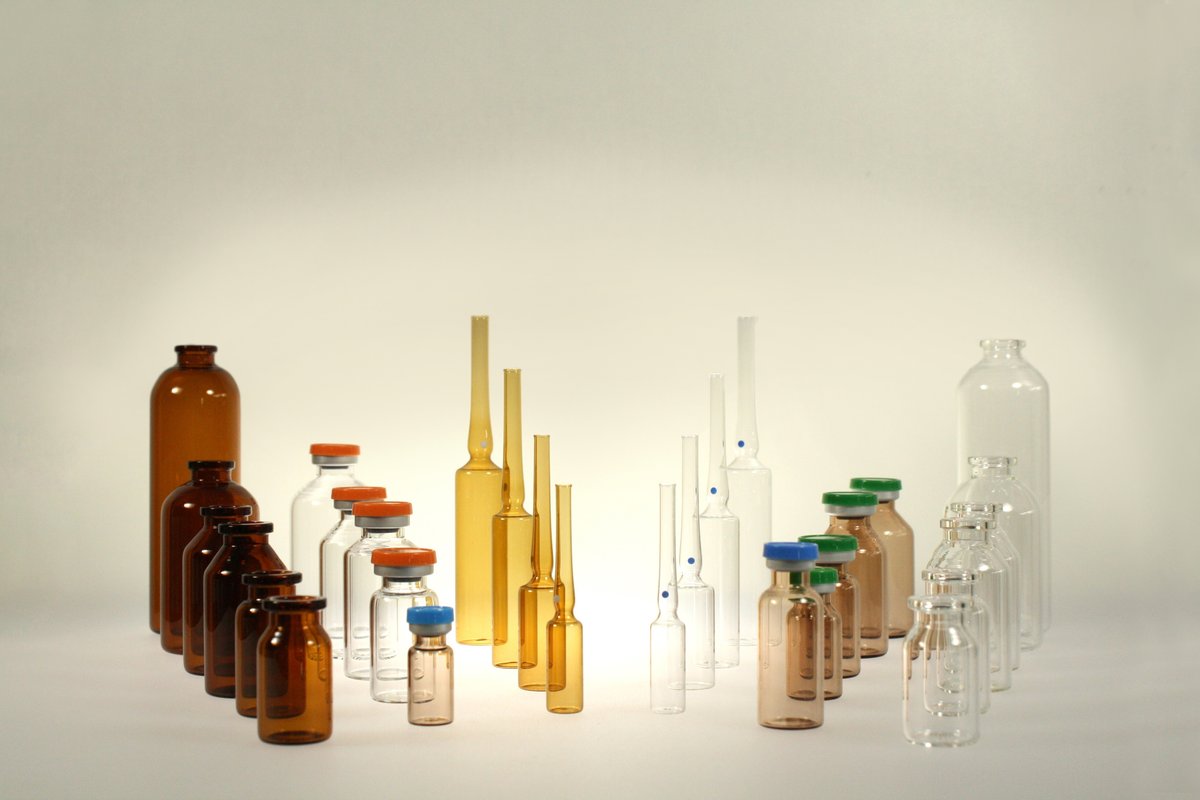
兵庫県西脇市にあるクリーンルームのある工場「開発センター」で滅菌済み製品を製造しています。
主なお客様は病院薬剤士、栄養士、そして製薬企業の方々です。
10本単位という少量と、数十種類の瓶から選べる多品種が特徴で、主力製品のステリバイアルの発売から40年以上ご愛顧頂いてます。また、一般医療機器 クリアシールステリバイアルも製造しています。
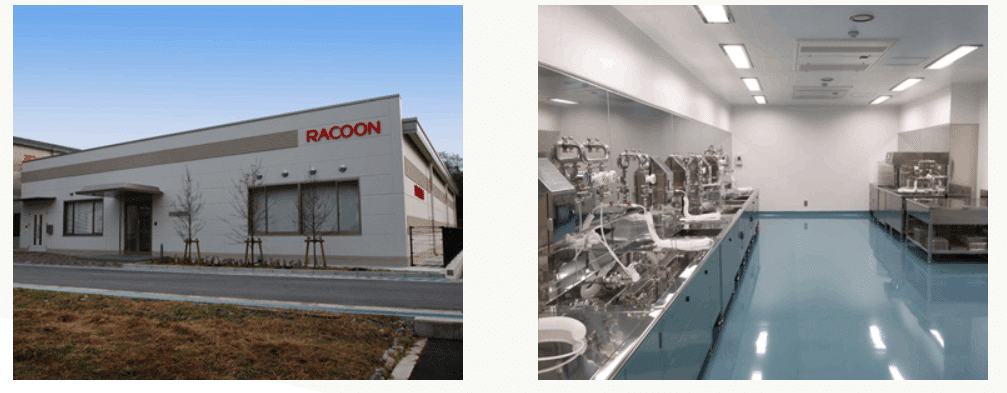
2.積み重なる問題2017
私が入社した2017年4月、消耗品事業部は追い込まれていました。
消耗品事業部の事業部長(兼センター長)と、品質管理部門の責任者が2017年3月に退職。長年トップダウンで引っ張ってきたリーダーがいなくなり、事業部は舵を失いました。
急遽、現場のまとめ役だった方にセンター長に就任頂きましたが夏にはダウン、そのまま退職されました。
次のセンター長のバトンは2017年6月に入社したばかりの方に。元々そのポストに向けた採用でしたが、本来は1年ほど準備期間を設ける予定でした。
また、2016年末に大阪本社の営業事務2名が揃って退職。後任の方が入社するまで一時的に社長が受注入力作業を行うスクランブル体制でした。
私は当時、別事業部の営業として働いていましたが、ある時センター長から「正直、厳しい…」とお話を聞き、社長と相談して開発センターに異動しました。2018年1月のことでした。
開発センターの生産プロセスに入ってみると、問題が見えてきました。
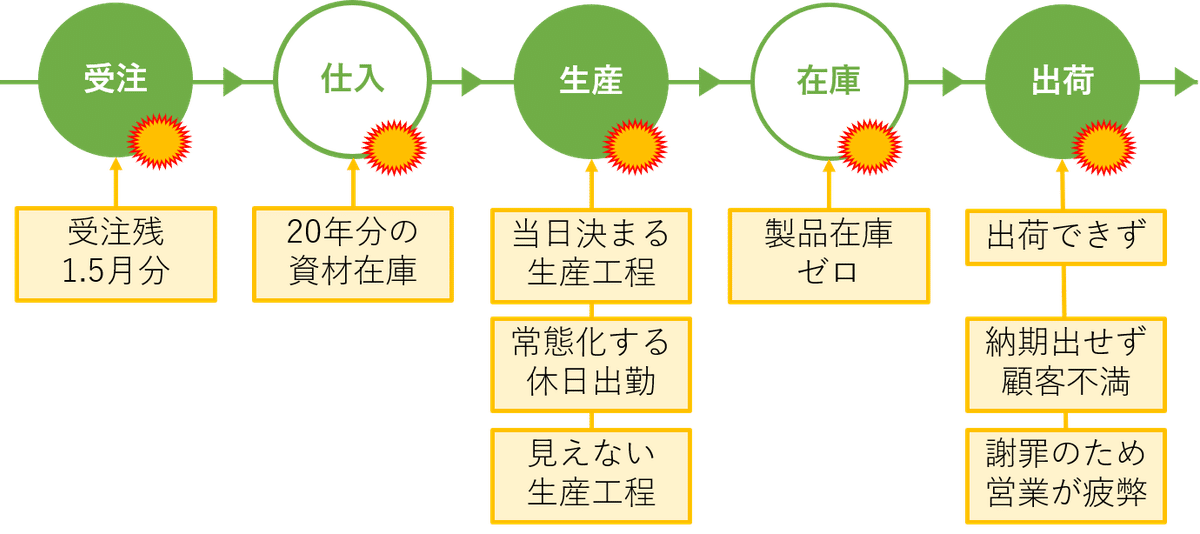
①積み重なる受注残
受注に対して生産が追いつかず、大量の受注残がありました。受注残金額は売上の1.5ヶ月分。主力製品の平均納期は24日。実際には受注後3ヶ月かかる製品もあり、当社の消耗品事業部としては異常事態でした。
②当日決まる生産工程
受注残をいつごろ出荷出来るか、営業が聞いても開発センターは回答出来ませんでした。作業現場であるクリーンルームと事務所の情報が分断され、どの工程にどのロットがあるかを把握する方法がありませんでした。
また、全製品の在庫が無い状況で、朝礼では「今日は〇〇を生産してください」という指示があるのみ。計画的に生産が行われている様子はありませんでした。
③大量の資材在庫
この状況の中、資材在庫だけが倉庫に積み上がり、作業効率が悪い。この在庫が適切な数かどうかも分かりませんでした。
④常態化する休日出勤
生産が追いつかない状況から、5~7名の生産グループのメンバーの休日出勤が常態化しており、ある人は年間500時間近くの残業していました。現在では到底考えられません。
⑤消耗品の営業部門の疲弊
生産現場だけでなく、営業グループも疲弊していました。営業は受注しても、出荷できませんのFAXを入れる、納期の質問の電話に「すみません回答できません」という答えを繰り返すしかなく、またその対応に追われ新たな案件や改善活動に取り掛かる時間はありませんでした。
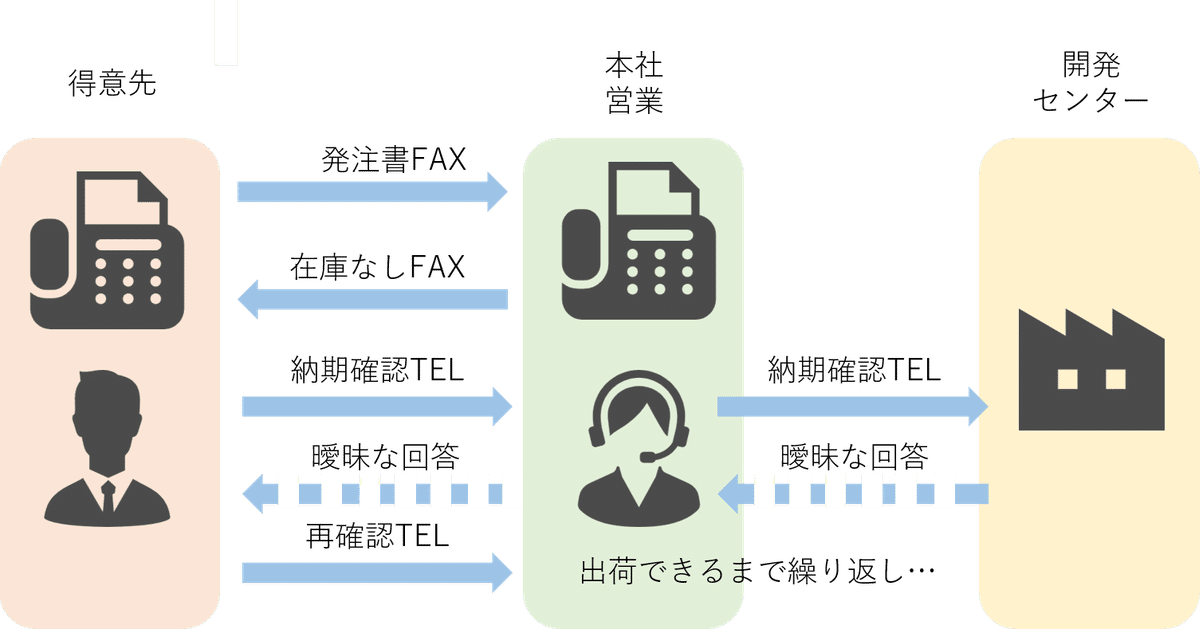
ここから、新しいセンター長と、開発センターのメンバーと共に少しづつカイゼンを積み上げていくことになります。
3.会議をしよう
開発センターは会議がほとんどありませんでした。退職した事業部長がすべての意思決定を行い、決定事項を朝礼で伝えていたので会議が必要ありませんでした(逆にすごいと思う)。
本来、業務改善の有効な施策の一つにムダな会議を減らす事がありますが、開発センターでは会議を増やすことにしました。
各グループのリーダーが集まって工程を決める工程会議と、営業に納期を回答する営業ミーティングの2つの会議をセンター長が新たに作りました。
ただ、その会議も当初はうまくいきません。
工程会議ではどの製品を生産するかを決めますが、そのために必要な「今、工程内にあるロットはどこにあるか」を把握するだけで1時間かかっていました。
営業ミーティングでは、受注残に対する納期回答をするのですが、この情報も精度が低く、「来月……中旬くらい…」といった曖昧な回答しか返せませんでした。
センター長は会議に毎回5種類の紙を持っていました。

私はこの状況を見て、この紙を1枚ずつ減らすこと、センター長に情報がすぐ伝達されることを目標に設定します。情報の一元化、見える化です。
合わせて会議体を増やしました。リーダーがグループの情報を把握した上で工程会議に望めるように、毎朝グループで打合せする時間を設けました。
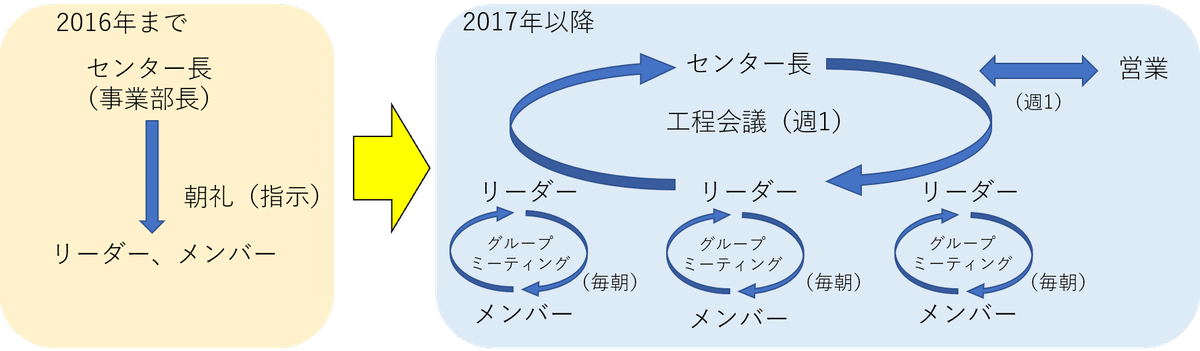
4.ロット番号台帳をエクセルに、kintoneに
開発センターでは、製造ロットごとに作業指示書を発行し、ロット番号のシールを貼っていました。その台帳は手書きで管理していました。
そこで、覚えたてのvlookup関数を駆使して、エクセルでロット番号台帳を作成しました。
三田理化工業に入社当時、私はエクセルの関数をSUMしか知りませんでした。ただ、kintoneを覚え始めたことでエクセルにもvlookup関数というものがあり、別シートから必要な情報を抜き出せることを知りました。(普通逆だと思いますが、私はkintoneを通してエクセルでデータを扱うことを覚えました)。
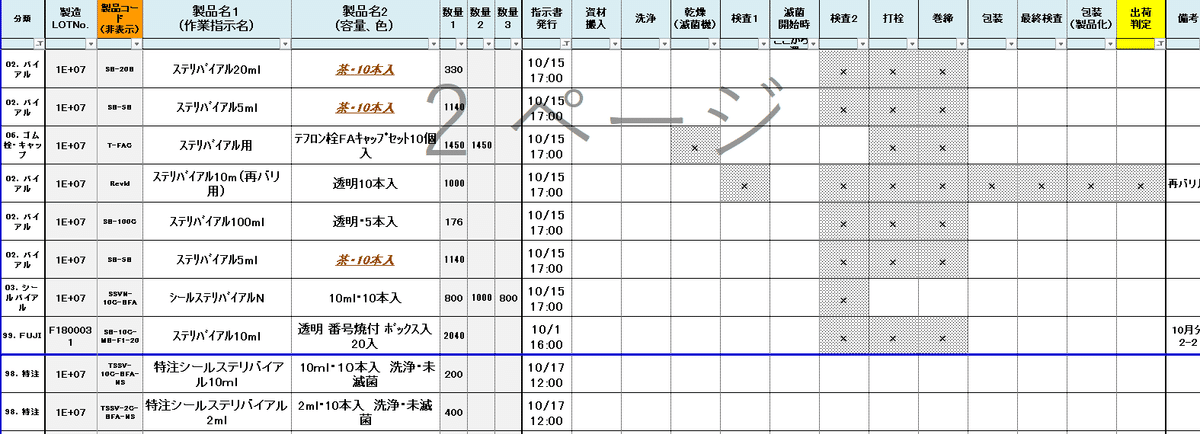
・製品マスターシートがあり、製品コードを入力すると、その製品に不要な工程は✗がつく。(vlookup関数)
・日付を入力すると色が付き、出荷判定が完了するとソートで消す。
といった機能を持ち、初めて関数を使ったにしては上出来ではないか!と思い、愛着がありました。
ただ、このエクセルも運用してみると問題がありました。
①進捗を現場が手書きし、エクセルに打ち込む
エクセルを複数で一度に開けないので、A3の紙で印刷、工場のホワイトボードに貼り出して、作業者に手書きで進捗を記入してもらいました。その手書き情報をエクセルに打ち込み、また出力する、この作業に1週間で3時間くらいかかっていました。
②データが蓄積する度に重くなる
最初の頃は良かったのですが、全行でvlookup関数がついているシート、すぐに重たくなりました。営業からは「すぐに開けず、顧客に回答出来ない」と言われ、一手間かけてデータを軽くして提供していました。
③更新が1週間おき
手書きのデータを手打ちするのも手間がかかるので、更新が1週間おきになりました。リアルタイムの情報共有は実現していません。
結局、2年でこの台帳はkintoneに変えます。ただ、紙→エクセルの段階があったのでkintoneへの移行はスムーズに進みました。
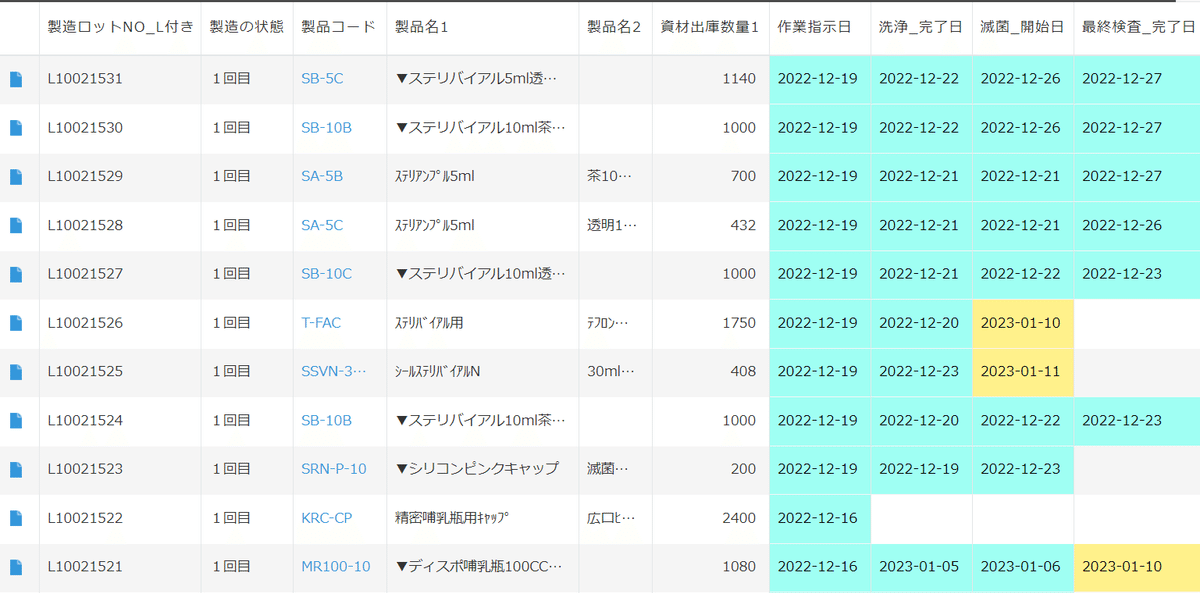
kintoneでロット管理、進捗管理をすることでメリットが生まれます。
①現場が直接入力できる。
kintone化したことで、これまで作業者に紙に書いてもらっていた進捗入力が、クリーンルームからタブレット端末で入力できるようになりました。
②ロット情報(生産情報)と品質情報を紐づけ可能になる。
ロット情報がkintoneに蓄積するため、そのロットでの不適合やイレギュラーが発生した場合の情報を紐づける事ができるようになりました。
③他部署がリアルタイムに閲覧できる。
これまで1週間おきに更新される重たいエクセルを開かないと生産状況が確認出来ませんでしたが、kintoneに変えていつでも最新情報を閲覧出来るようになりました。
5.既存のシステムをちゃんと使う
課題の一つの倉庫に積み上がる資材在庫。資材によっては20年分あるものもあり、過剰在庫であることがわかりました。この解決策は、2016年に導入済みの基幹システムにありました。
基幹システムでは仕入と在庫を管理しているので、これらの情報を結合すれば発注店管理出来るはずだ!と考え、システム屋さんに「発注点管理したいので機能追加してください!」とお願いしたら「…ありますよ」と言われました。これで、無限に買ってしまう資材の問題は解決しました。こんなふうに一つ一つ手探りで進んでいます。
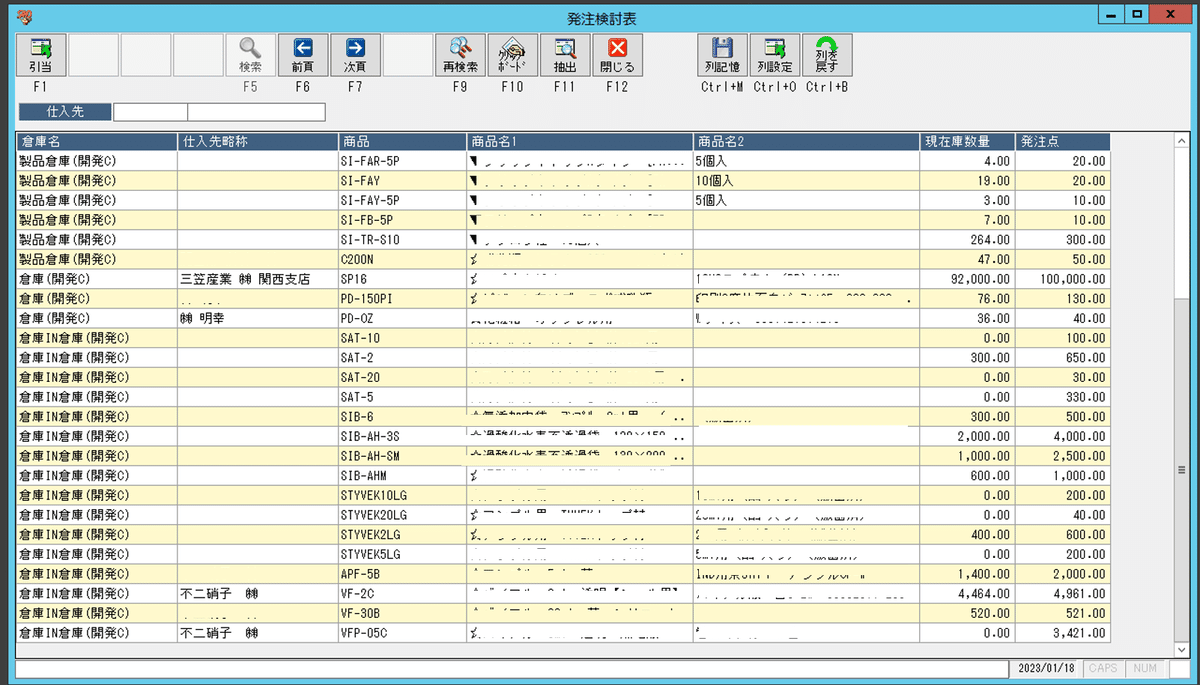
6.情報共有はslackとスプレッドシートに
開発センターの出荷グループと、本社にいる営業グループは、日々受注と出荷についてリアルタイムのやり取りをしています。
例えばこんなやり取りが1日に何回もあります。
お客様からAという商品、20箱の注文が来ました。そこで営業は、A商品の製品在庫を確認するため、製品在庫というエクセルを開いて在庫数を確認しようとしますが開けません。営業はお客様の電話を保留にして、開発センターに電話して「製品在庫のエクセル閉じてください」と電話します。
エクセルが開いたことを確認し、製品在庫を確認してから「すみません、在庫がございません」という回答をします。
そこでまず、1日に10回以上やり取りする電話をslackに変更しました。営業は作業中の出荷グループの手をあまり止めたくない。出荷グループは作業中に電話で依頼を受けても作業後に忘れてしまう、といった課題を持っていたこともありすぐにフィットしました。
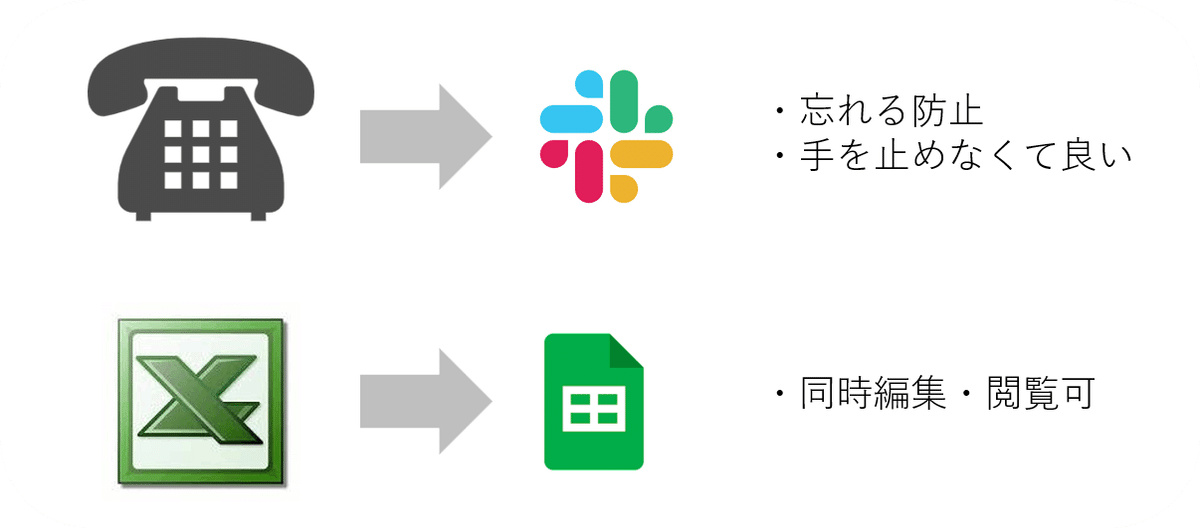
次に、工程会議、営業ミーティングの会議資料をエクセル(2003)からスプレッドシートに変えました。
基幹システムから1日1回、製品在庫と受注のCSVデータをスプレッドシートの貼付け用シートに貼り付けると、各製品ごとの現在在庫数、受注残数が計算される仕組みになっています。
現在は、これを営業と開発センターがリアルタイムに確認しながら、出荷日や、次の生産予定を立てています。
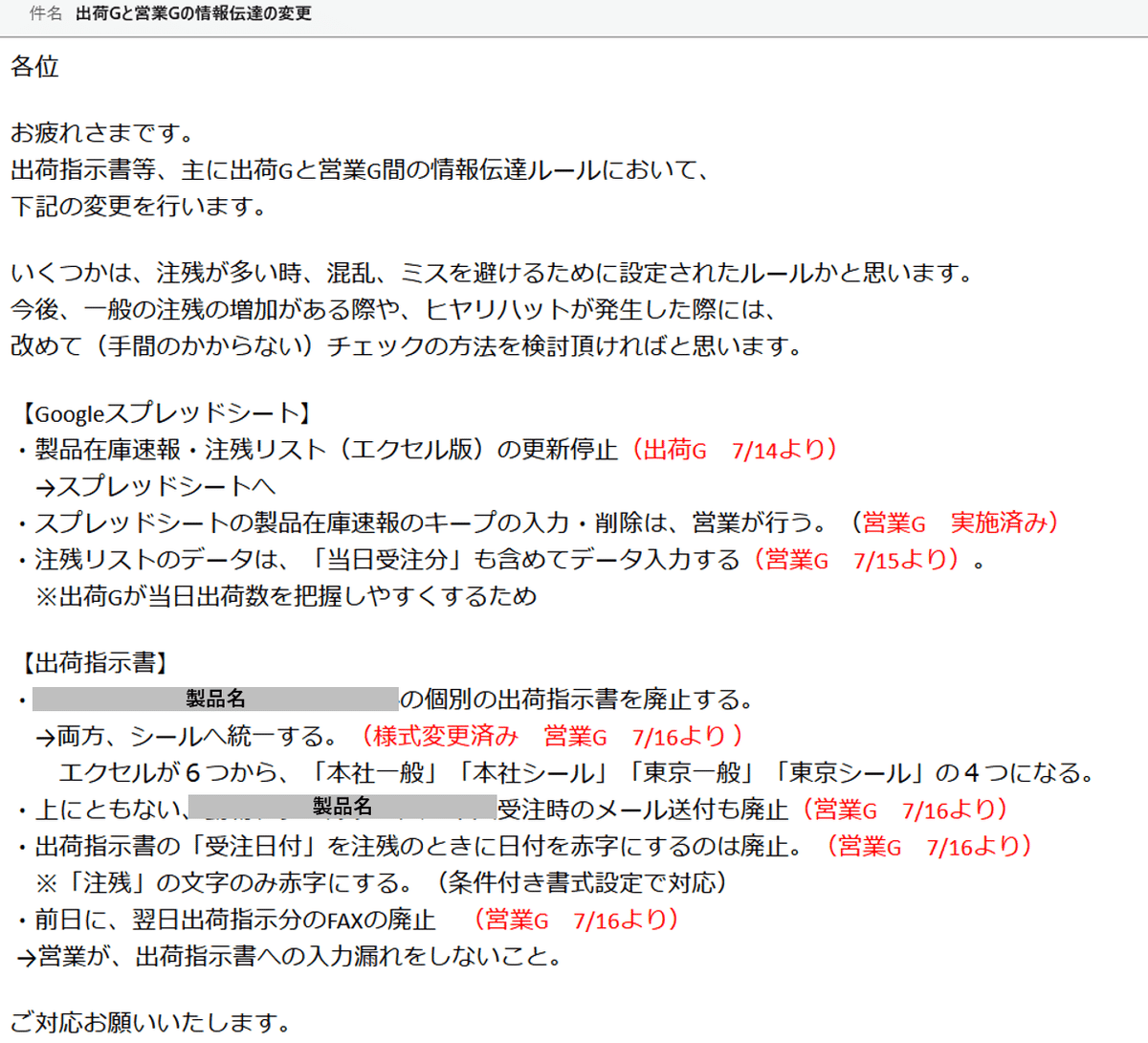
これらの改善の結果、センター長は工程会議に1種類の紙だけで次の予定を立て、受注残の製品の出荷日を週単位で回答出来るようになりました。
生産計画を立てた結果、効率よく生産が進み、2018年の夏には受注残は1.5ヶ月分から0.5ヶ月分まで減りました。残業も半分に減らすことが出来ました。
7.設備管理を残そう
良い方向に進むと思われた2018年、工場の稼働が停止します。弊社の重要な工程、滅菌を行う設備が故障してしまい、修理に3ヶ月を有しました。その間、医療機器は生産出来ず受注残が積み上がります。なくなったと思われた受注残との戦いが再び始まりました。
どれだけ生産性を上げても設備が止まれば終わる…それを痛感した私は設備の点検、部品保管を強化する方針をセンター長と確認します。
開発センターの建設は2012年、設備の更新が迫っており、時期が重ならないよう更新計画も必要でした。
そこで、これまで紙で管理されていた設備情報をkintone化します。kintoneの設備管理台帳アプリ、そして設備の点検・校正の情報を入力するアプリを組み合わせることで、次回の点検日に通知が飛び、漏れなく定期的な点検が行われるシステムを作りました。
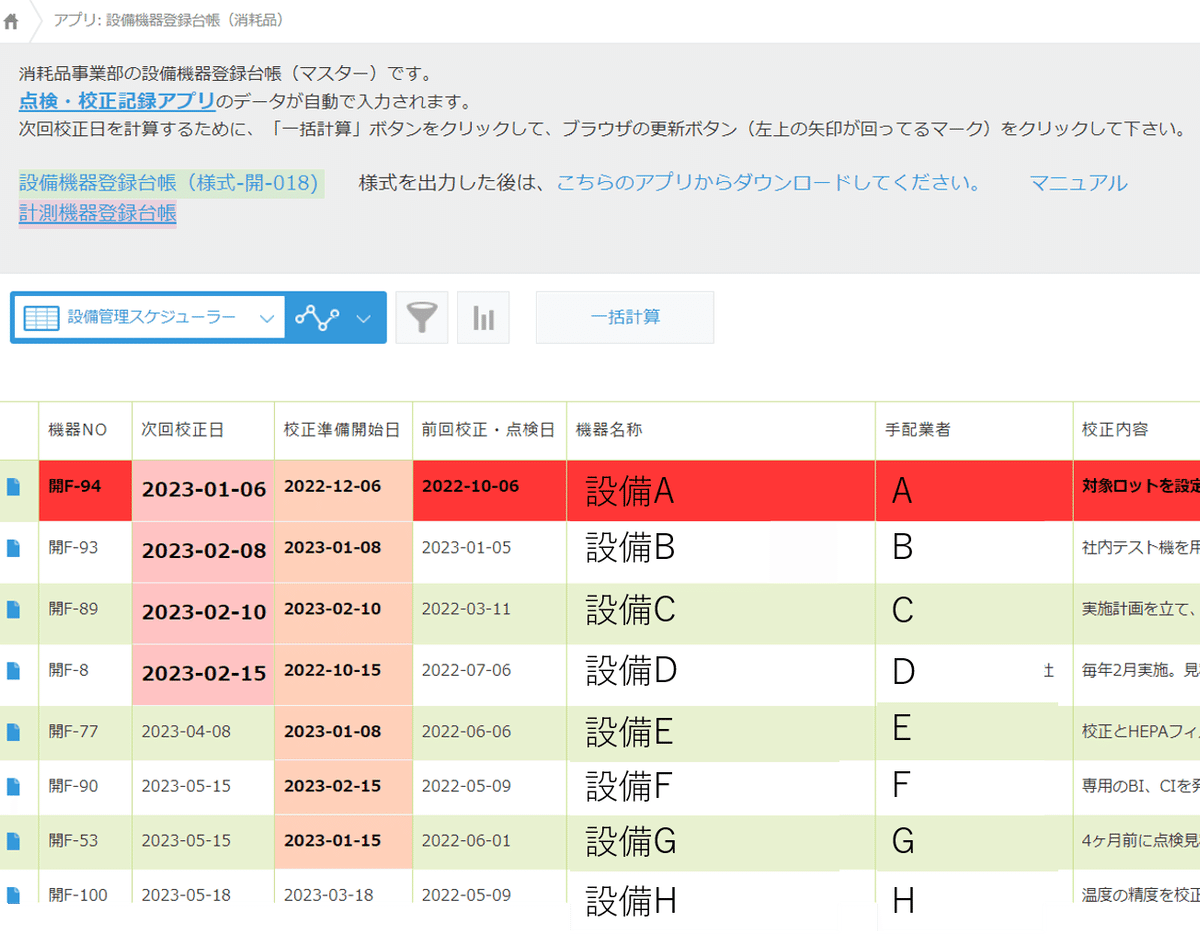
その後は大きな設備停止の影響はなく、故障した滅菌機を増設してバックアップを設けたり、海外製でメンテナンスコストの高い設備を国内製に変更する、といった計画的な設備投資が出来るようになりました。
8.検査基準を明確に
弊社消耗品の特徴は、全数外観検査をしていることです。これだけの問題を抱えていた理由の一つはこの外観検査に時間がかかるからでした。患者さんの血液に入る注射薬を入れる容器、受注残がどれだけあっても検査を簡素化することは絶対に出来ませんでした。
ただ、検査工程を観察すると検査スピードが人によってばらつきがありました。ヒアリングすると検査速度が遅いのではなく「これは合格か不合格か」と悩む時間が長いことがわかりました。
これまでは困った時はベテランが判断し、最終は限度見本を確認する、というやり方で来ていましたが、明確な基準を設けたほうが良い、と判断しました。
そこで社長から製品誕生のエピソードや過去のクレームを調べ、お客様の求める品質にあった外観検査基準を設け、検査員に統一しました。
この結果、バラつきがあった検査速度が均一化しました。
9.使わないマニュアルを資産に
ISO9001を取得している三田理化工業、製造工程はマニュアルがありますが、ここ数年のカイゼンを進める中でマニュアルの更新がおざなりになっていました。
また、これまでは管理部門が現場の意見を聞きながらマニュアルを作っていましたが、それも手間がかかりましたし、結局作業者が後輩に指導するときにそのマニュアルを使っていませんでした。
そこで、現場の作業者自ら手順書を作成・改訂出来るよう、全部マニュアル化プロジェクトを立ち上げました。業務すべて手順化しよう!と呼び掛け各部署から複数名参加頂き、毎月進捗を確認しながら手順書の改訂を進めてもらいました。
また、これを実現出来るよう、kintoneで品質文書を管理出来るようにし、承認フローを簡素化しました。
その結果、前年は50件だった改訂件数がこの年は100件と倍増しました。
マニュアル整備はすぐに成果が現れませんが、この取組みを通じて、これまでPCを触ったこと無い(お孫さんのいる)作業者の方が「一つマニュアル作れた!」と動画のリンクもつけたマニュアルを作ってくれるといった日常業務にはない刺激がありました。
これまで現場が見ていなかったマニュアルを、自分たちの手で資産に変えていく様子は、見てるこちらも楽しかったです。この取組は、各部門の部門目標として次年度も続いています。
10.押印文書もkintoneで
開発センターでは、滅菌した証明書等、品質文書を顧客に提出する場合があります。その場合は文書に会社印を押印するのですが、会社印は大阪の本社にしかありません。そこで、文書(またはデータ)を本社に送って、押印してもらってから、開発センターに戻す作業が発生します。
このような紙の移動をなくすため、承認作業をkintone化しました。具体的にはステータスが「承認済み」になったレコードだけ、押印済みの品質文書が印刷する仕組みを作りました。この仕組みはアトツギのkintoneユーザーから教えてもらいました。
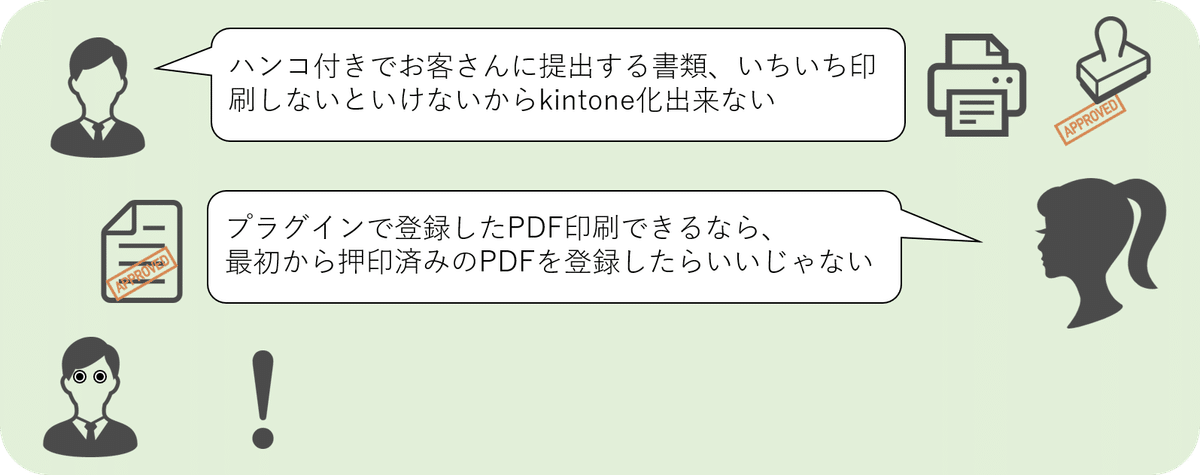
ハンコは押すもの、という固定観念に縛られた自分の頭の硬さを痛感しました。
11.会議資料はフォーマット化
毎月、売上の進捗を確認する営業会議が行われます。消耗品事業部の営業は、毎回ピボットテーブルで独自分析した売上資料をまとめ、提出していました。この担当者は資料作成に丸1日費やしていましたが、情報が多すぎて、会議でその情報の意味が伝わっていませんでした。(これは管理職が会議や資料の意図を伝えずに資料作成のみ指示してたから)
そこで、基幹システムから出したCSVデータを貼り付ければSUMIF関数で集計できるフォーマットを作成しました。この結果、資料作成は20分程度で完了しました。また、製品ごとに売上推移を見ることで、打ち手を考え、実行しその結果を確認することが出来るようになりました。
アウトプットを明確にすることは結果的に作業効率化につながります。
12.カイゼン成果
これまでのアクションの結果です。
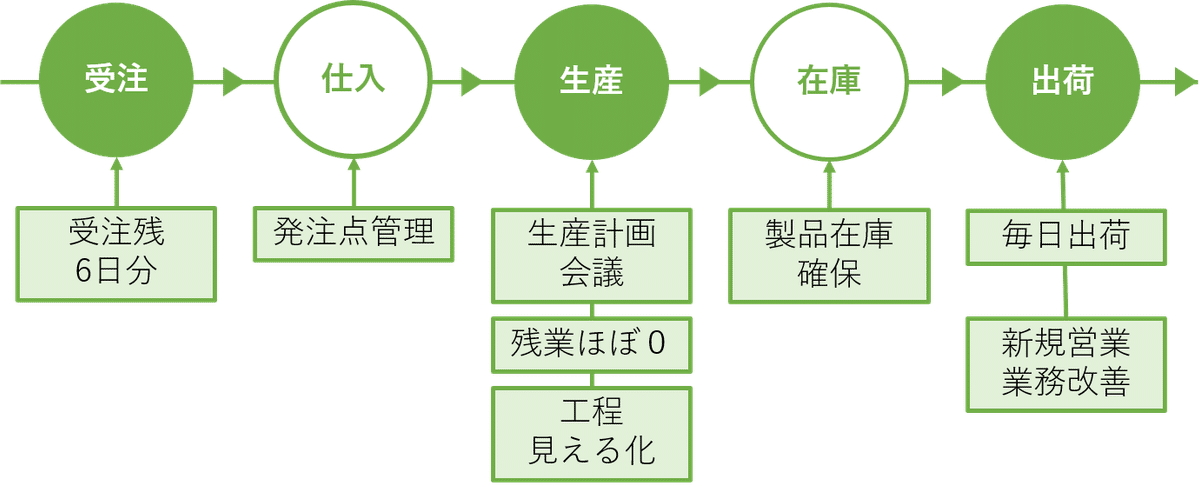
①残業はほぼゼロ(年間18時間)
2017年は社員5-7名がほぼ毎週、土曜日に終日残業していました。平日も1時間残業しており、一人当たり年間500時間、センター全体で年間3000時間以上あった残業時間は2022年時点で休日出勤も平日残業も全てなくなりました(休日の設備更新などは有り)。
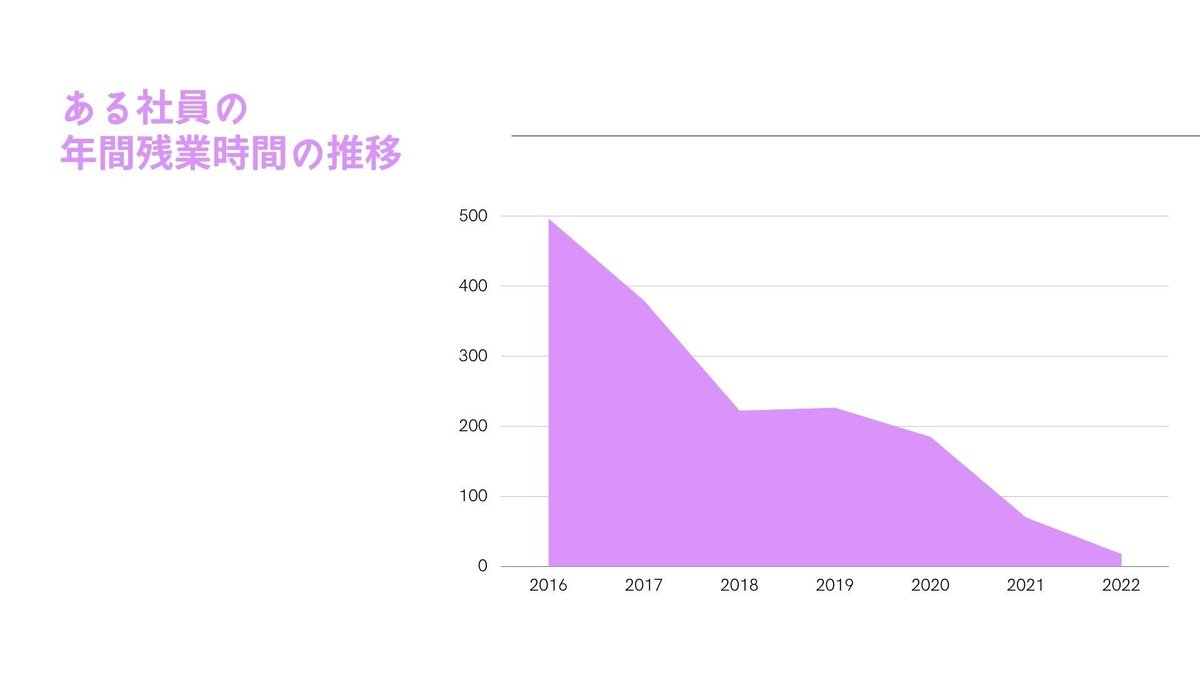
②過去2年間の離職率0%
開発センターに限れば2021年-2022年の2年間は離職率は0%、その前年もご家族の介護で退職された1名だけでした。
私が入社した時は多くのベテランが退職し、新しい方々ばかりだったのが、ほぼ皆さん勤務年数5年以上になりました。3名、パートから正社員に代わって頂きました。また、この間に2名、計3回の産休・育休がありました。実は、創業70年で産休制度の活用は初めてのことでした。
③出荷日数が平均1日に
残業をなくしても生産スピードは保ち、最大平均で24日かかっていた納期が、1日に短縮されました。
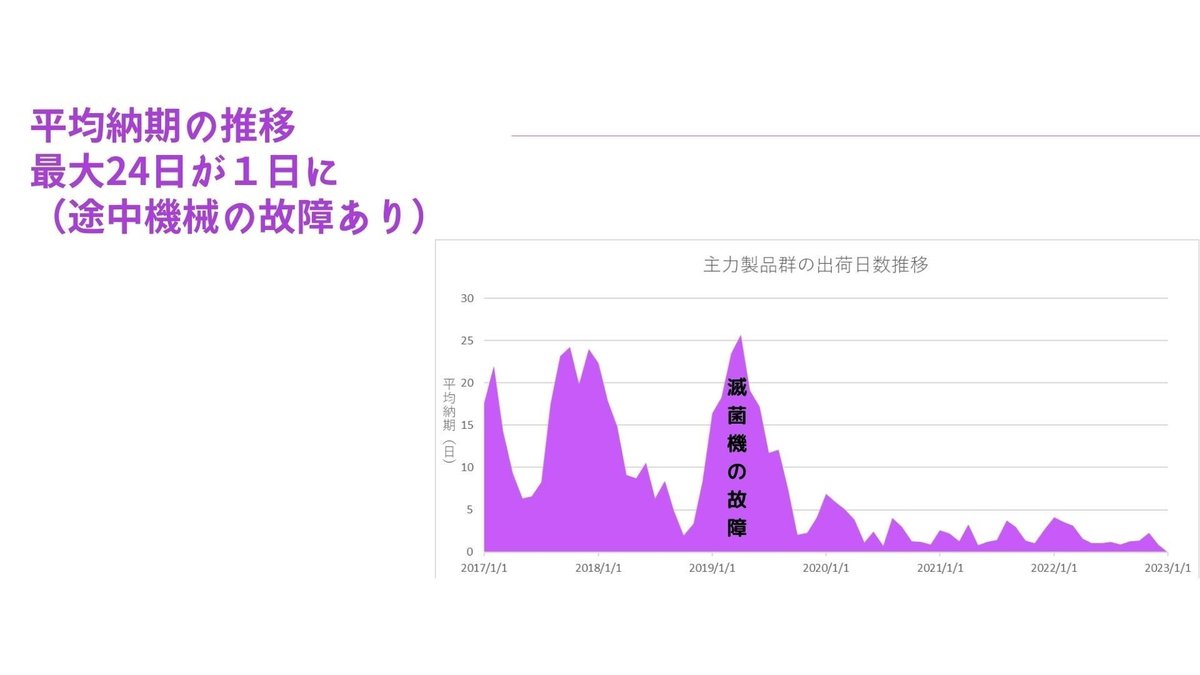
病院で待つ患者さんのためにすぐにバイアルを使いたい、とおっしゃって頂く薬剤師の方々にできるだけ早く届ける事ができるようになりました。
④トップダウンからボトムアップへ
2017年、前任者の圧倒的なトップダウンから開発センターのメンバーは考えることさえ禁止されてる空気がありました(実際、改善提案したら干された社員がいたらしい)。
そこから、カイゼン提案制度を作り、マニュアル作成業務を現場に渡し、毎週の会議、毎朝のグループミーティング、半年ごとのクレームの共有会など、現場と情報共有しながら進むように変えてきました。ボトムアップ、というよりはメンバーを信頼し、業務の領域が広がっていったイメージです。まだまだ情報共有は足りていませんが、組織全体で考えることでカイゼンの速度、精度は圧倒的に速くなったと思います。
⑤業績は劇的な改善をしていない…が
これらの改善成果から社員の方々は残業代がなくなりましたが、その代わりに期末賞与を支給できるようになりました。
ですが、劇的に業績が良くなったわけではありません。
この間、外部環境の変化により主力製品の利用が一部なくなる、資材、エネルギー価格が急騰するなど、逆風が吹き荒れていました。
それに対抗して新規案件を取ろうと思った矢先に新型コロナウイルスが流行し、展示会出展や引き合いがなくなりました。
ただ、これまでの変革がなければこれらの環境変化についていくことは出来なかったですし、そもそも社員が残ってくれていたかもわかりません。
ここからが攻めに転じる時です。
新型コロナウイルスによる停滞から、新薬の研究開発や治験が始まり、弊社にも新たな引き合いが増えています。これらに対応出来る余裕を持てたことがこれまでの取組の成果だと思っています。
⑥「この会社が好きです」
開発センターのメンバーからこの言葉を聞いて、この会社がますます好きになりました。多くの変化がある中でも一緒に前に進んでくれたこの開発センターのメンバーにさらに会社を好きになって頂けるよう、またこの会社に関わるすべての人達が幸せになれるよう、これからもあの手この手でカイゼンを積み上げていきたいと思います。
以上、この5年間のとある工場のカイゼン成果でした。
わぁわぁ言うとります。お時間です。さようなら。
大阪市在住の89年生まれ 父親経営の中小メーカーに在職。 グロービス経営大学大学院卒業 事業承継や、組織の変革、文系から見た社内システムの構築について掲載予定 好きなもの:サッカー(ガンバ大阪ファン)、漫画(オールジャンル)