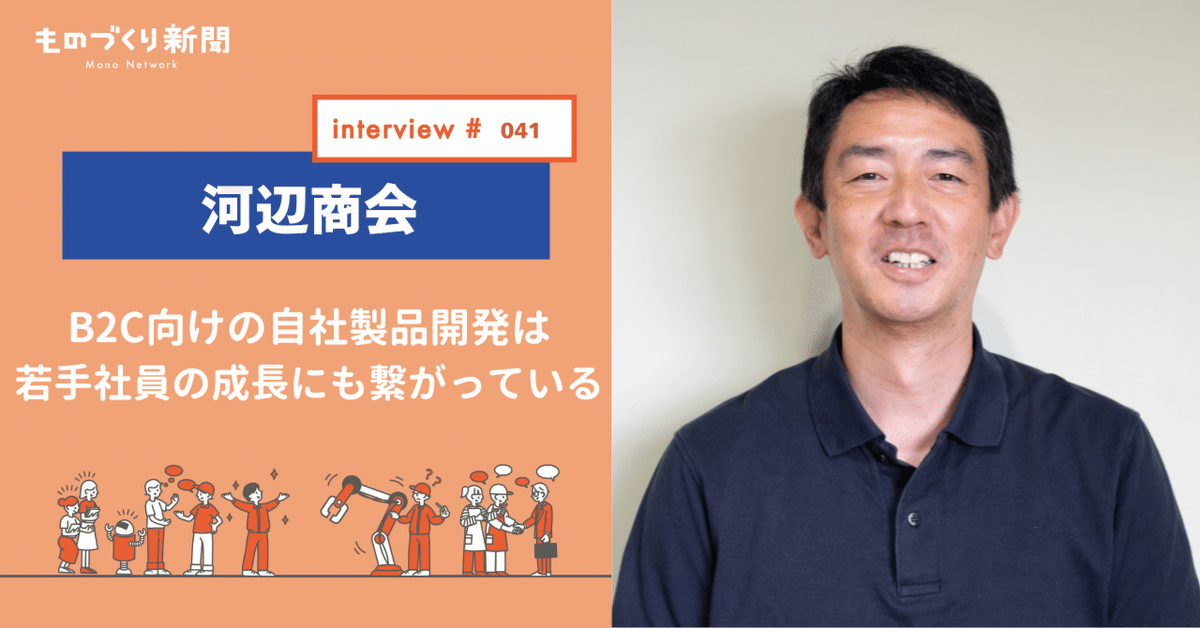
シンプルだけど真似できない工夫がぎっしり詰まった自社製品 株式会社河辺商会 福田康一さん
JR阪和線が走る鳳(おおとり)駅を降り、徒歩で10分ほどの場所にある株式会社河辺商会(かわべしょうかい)さんを訪ねました。
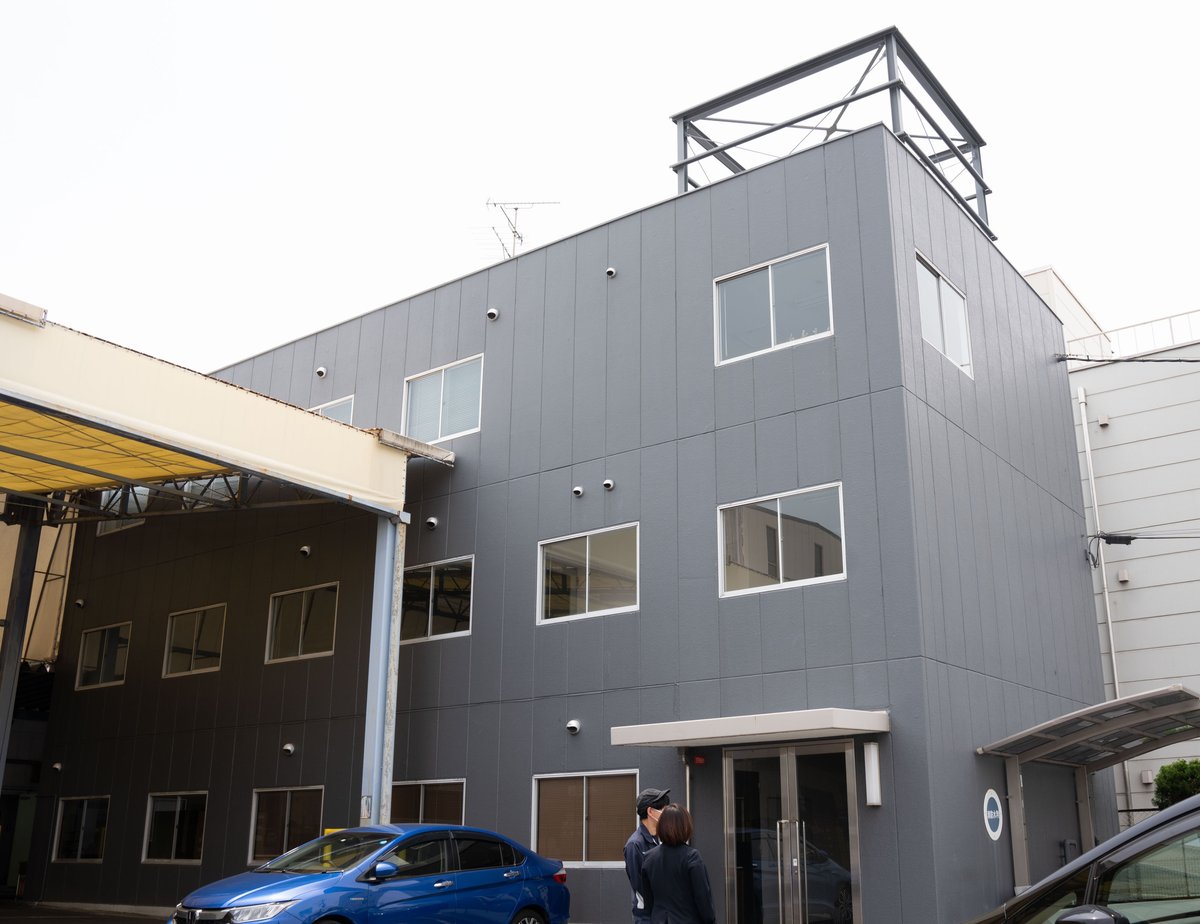
河辺商会はプラスチック金型設計・製造、成形をはじめ、成形加工品に付随する塗装やめっき加工などの二次加工を行っています。
河辺商会は繊維を加工する機械や部品を取り扱う商社からスタートしました。その後、金属製だった部品がプラスチック製へと変わり、河辺商会もプラスチック部品を提案するようになりました。そしてそのプラスチック部品を自社で成形するようになり、今ではプラスチック成形が主力事業となりました。
中でも製品の外観となる部分の成形を請け負ってきた経験が豊富で、カメラやテレビの外側など外観を綺麗に見せるための技術が誇りだといいます。
外観を綺麗に見せるためのポイントのひとつ
金型の製造技術
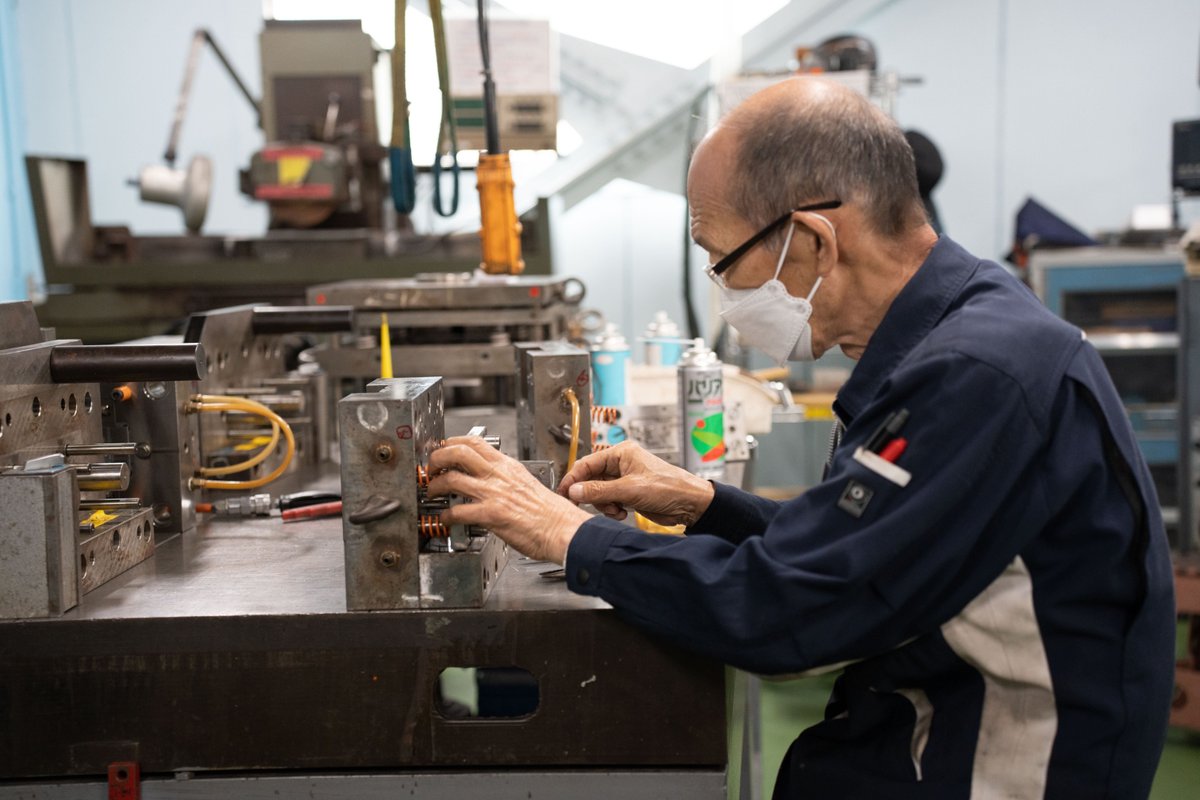
プラスチックを熱して溶かし射出成形して冷却するという射出成形の過程の中で、射出するタイミングでプラスチック原料の中に含まれているガスも一緒に金型に入ってしまうことがあります。ガスが入ってしまうと、外観上にモヤッとしたような跡が残ったり、金型自体の損傷に繋がってしまいます。そこで大事なのが、そのガスを金型からどう抜くかというガス抜きの技術です。河辺商会は金型の入れ子や突き出しの形状や位置を工夫したり、ピンにガス抜きの効果が期待できる加工を施すなどの工夫をして、外観を綺麗に見せるための工夫をしているそうです。今回は大阪府堺市の本社で代表取締役社長の福田 康一(ふくだ こういち)さんにお話を伺いました。
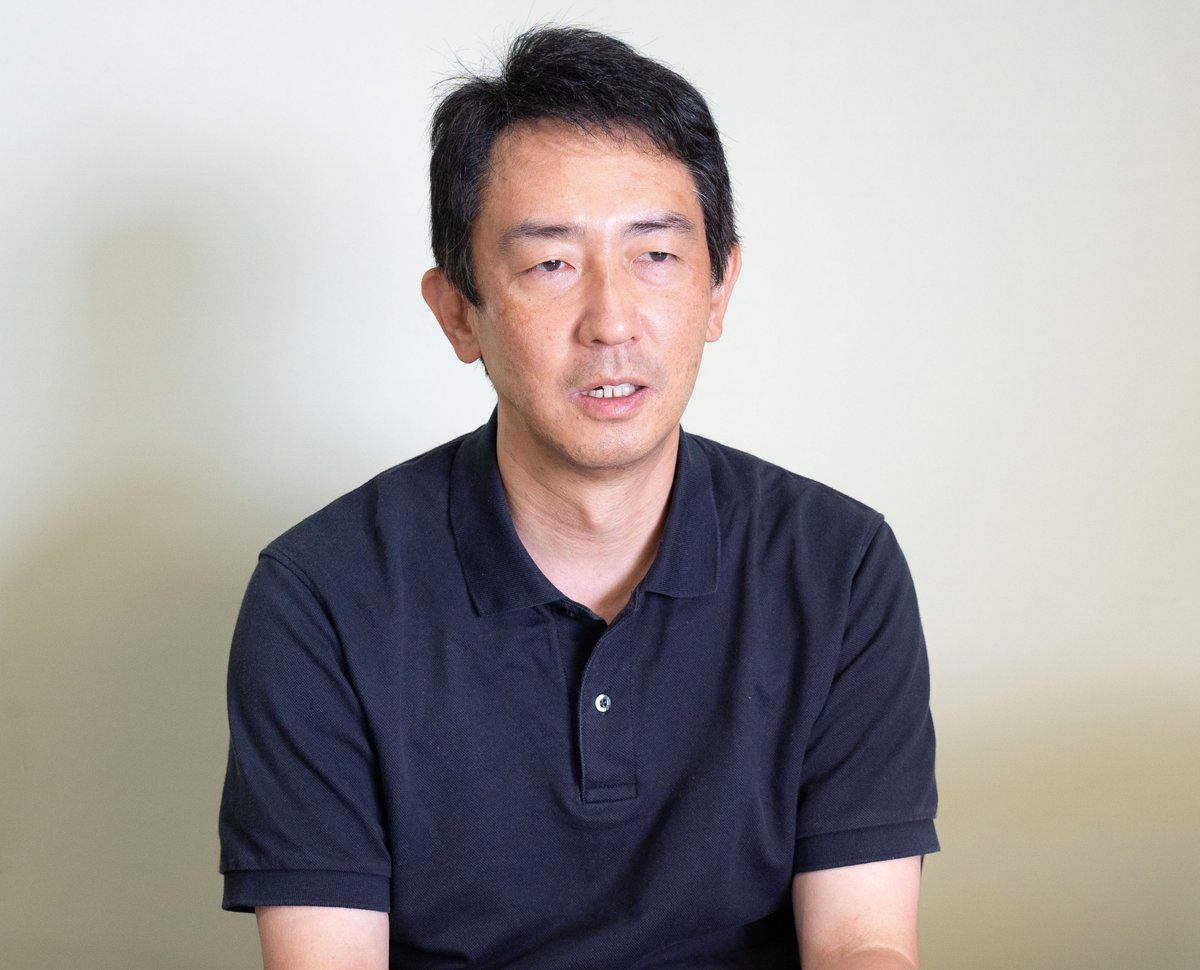
ーーお生まれは大阪府ですか?
大阪府阿倍野区で生まれ育ちました。
ーー学生時代に熱中したことはありますか?
小学生の頃は野球をしていて、中学校は野球部がなかったのでラグビー部に所属し、高校ではサッカーをしていました。子供頃からスポーツが好きです。
ーー大人になってからもスポーツはされているのですか?
野球は昔から所属しているチームがあり、今でも週に1、2回程楽しんでいます。サッカーは子供が所属していたサッカーチームの父兄が集まって結成したサッカーチームに所属しています。子供たちはもう卒業したのですが、父兄は今でもチームを続けてサッカーを楽しんでいます。
薬剤師として働いた後、ものづくりの世界へ
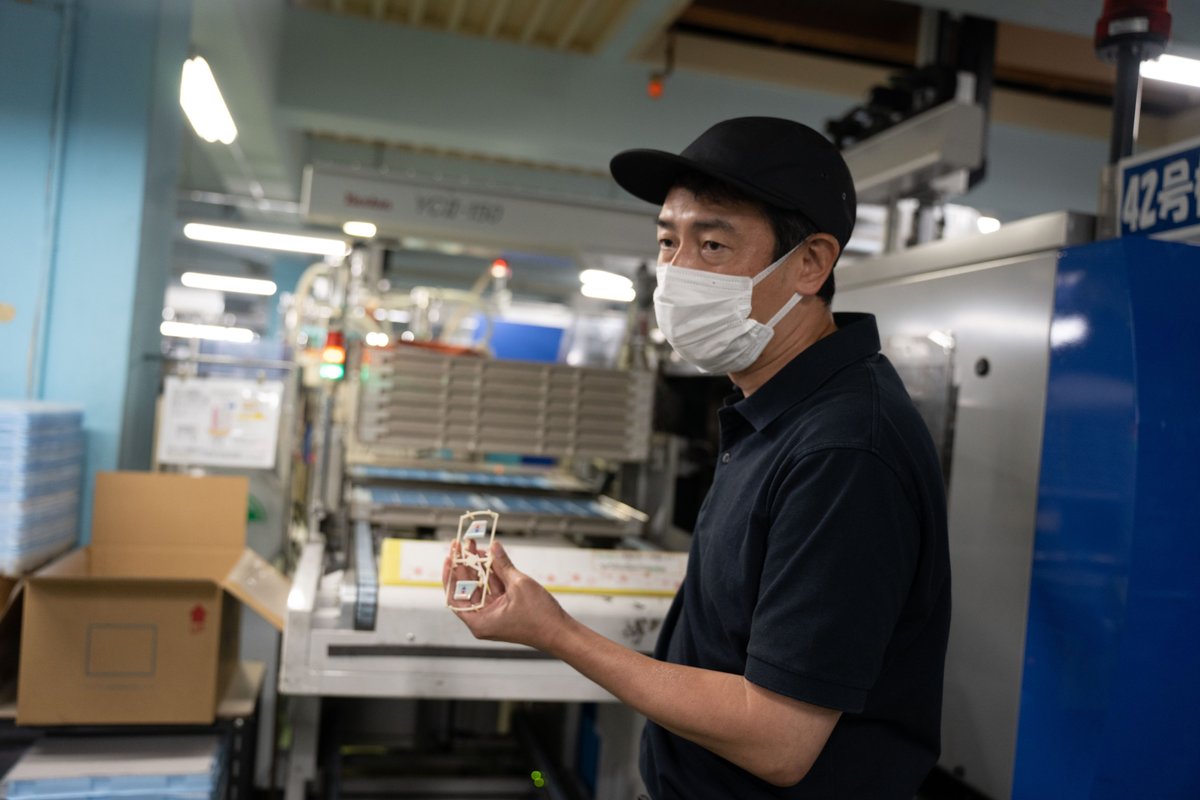
ーー河辺商会は福田さんご一家の家業ではないのですか?
河辺と付いているように創業者は河辺さんです。河辺さんが後継者を決める際に、社内からではなく当時プラスチック材料商社で営業の仕事をしていた私の父親に声がかかったそうです。その当時私は20歳くらいで薬学部の学生だったので、父親が河辺商会で社長になることは聞いていましたが、自分が将来その跡を継ぐということは全く考えていませんでした。
ーー薬学部に通われていたのですね。
母を含め、母の実家が薬剤師をしている家系だったことも影響して、私も薬剤師になろうと考えていました。薬学部を卒業後は薬剤師として働いていました。
ーー薬剤師として働きながらどのようなきっかけで河辺商会に入社したのでしょうか?
前から父の中では次の後継者について考えていたとは思うのですが、タイに海外工場を作るという計画が立ち上がった時に、改めて後継者について考え出したのだと思います。当時私は薬剤師として働いていましたが、2人の弟はまだ学生だったこともあり、私が薬剤師を辞めて河辺商会に入社することを決めました。
ーー薬剤師からの転身に関して、当時はどんなお気持ちでしたか?
薬剤師として働いている頃から、いつかは自分が社長として調剤薬局を開業したいと考えていました。父親から将来を見据えて河辺商会に入社しないかと話があった時に、調剤薬局の社長ではないけど社長になる夢を叶えるのは河辺商会でもできるなと思い決断しました。とはいえ、ゼロからのスタートでしたので苦労もありました。
どんな思いでものづくりをしているのか 現場の思いを身を持って経験
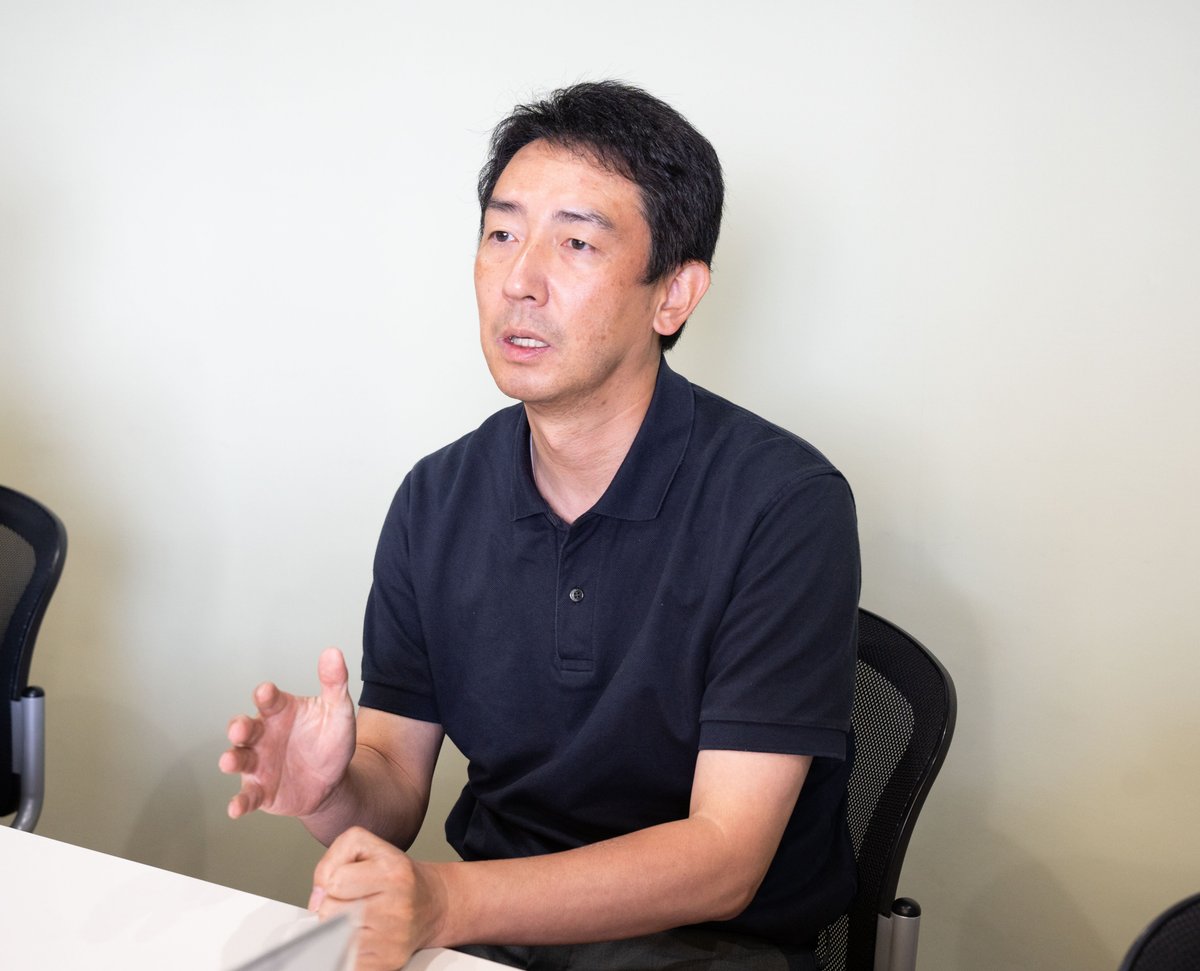
ーーどのようにして製造業の仕事や業界について勉強されましたか?
最初から河辺商会に入社するのではなく、まずは取引先の関連会社に入社し様々なことを教えていただきました。入社してすぐに「金型って何ですか?」と聞いたくらいゼロからのスタートでした。中途採用として入社して、叱っていただきながら教育していただけたことは私にとって良い経験でした。
ーー具体的にはどのようなお仕事をされていましたか?
めっき加工の会社でしたので、最初の1年間は現場でめっき加工をしたり、二次加工として塗装やレーザー加工をしていました。次の1年間は、完成した金型を試作成形して、条件出しや問題点の洗い出しなどをする「成形立ち上げ」をしていました。当時は忙しく1日あたり1人4、5型の金型を担当していて、試作でサンプルを数個成形し、型を変えてまた試作成形するというのをひたすら繰り返していました。
ーー成形立ち上げの仕事はいかがでしたか?
今だと速度や条件を細かく何段階も設定することもあるのですが、当時私たちが試作成形で理想としていたのは「一速一圧」という考え方です。速度も圧力も一つの条件で整形ができれば、気温や環境のちょっとしたブレがあっても対応できます。
とにかく、現場を知らずに物事を会議の中だけで話したところで現場の人には伝わらないということを理解しなさいという父の考えもあり、現場の方々がどんな思いでものづくりしているのかを身をもって体験する必要性を感じていました。
入社後すぐにタイ工場の立ち上げへ
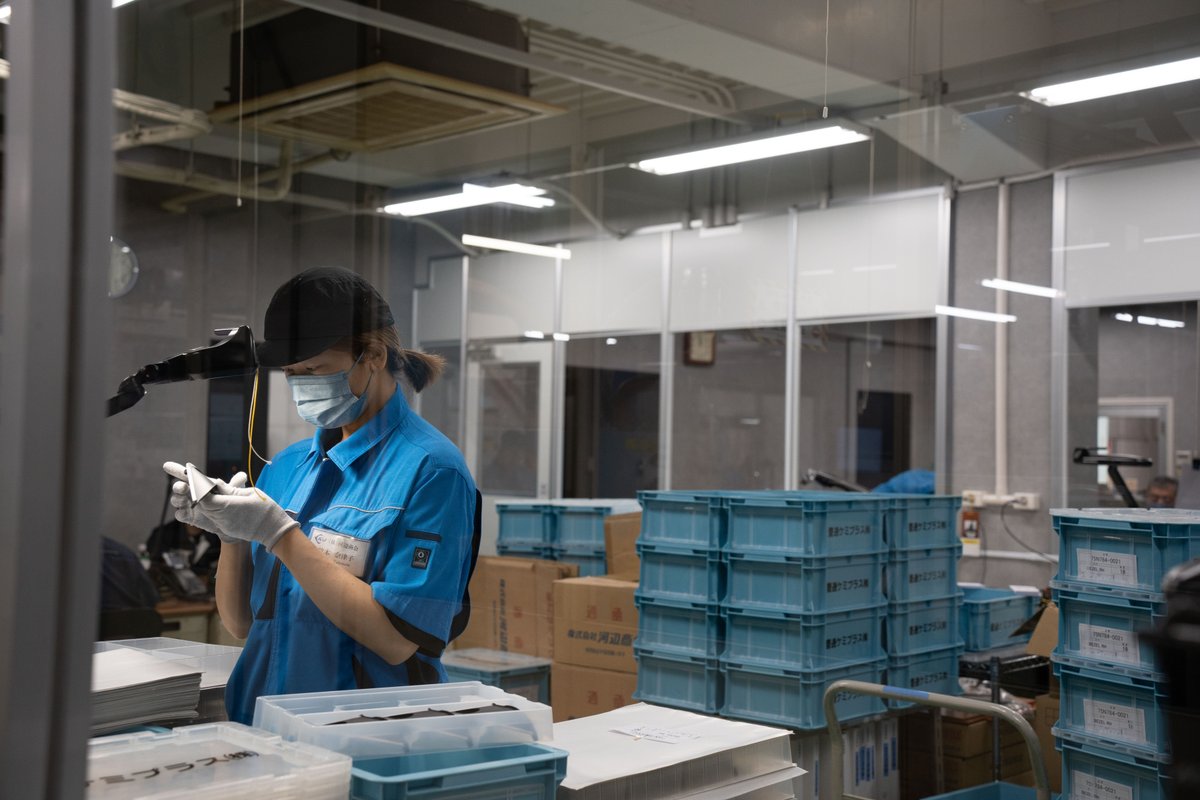
ーータイ工場はどのようなきっかけで立ち上げたのですか?
以前からお取引のあったお客様がタイに進出されていたことがきっかけです。車のコンビネーションスイッチ(ライトやウインカーなどが1つにまとまっているスイッチ)のプラスチック部品製造の仕事をするためにタイに進出しました。
ーータイでは具体的にはどのような業務を担当されていたのですか?
はじめは日本からタイに移管されてきた金型を受け入れて、タイでの生産に対してお客様に承認を取る仕事がメインでした。ですが、金型がタイに移ってすぐに量産というわけにはいきませんでした。工場監査なども必要で立ち上げた最初の年は金型はあるのに成形できず監査だけで終わった状態でした。
ーー承認や監査で1年間もかかるのですね。
その間、お金はどんどん減っていくので近くにある工業団地の中にある同業他社さんにお願いして仕事を貰っていました。日系企業が集まっていた工業団地だったので頼みやすく、社員の教育も踏まえて仕事をしていました。
ーー日本で受注した案件をタイで生産することが多いのでしょうか?
日本で受注した案件をタイで量産するケースと、タイ工場が現地の日系企業とお取引し量産するケースがあります。タイ工場は、日本ではお付き合いがない日系企業ともお取引しています。日本だけ、タイだけ、ではなく私たちがお客様に技術開発のご提案をし、日本での生産を安定的に行い、その先で海外にも広げてもらうことを目指しています。
ーータイ工場には何年間勤務されていたのですか?
入社して間も無くタイに渡り、2014年まで8年ほどタイの工場で働いていました。
自社のことを知ってもらうための社内向けブランディング
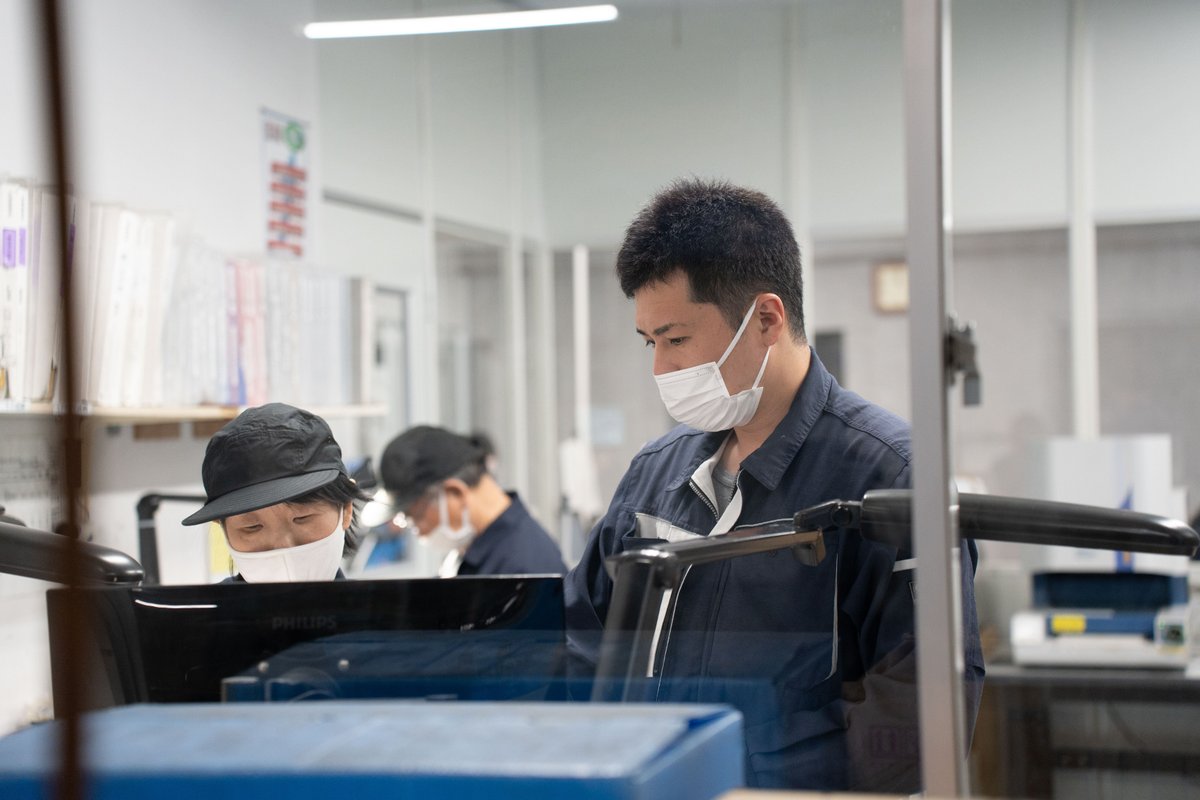
福田さんは2014年に日本に戻り、2018年に代表取締役社長に就任しました。
ーー日本に戻られてから、採用や人材育成はどのようにしていますか?
採用活動はもちろんのこと、入社後に辞めてしまっては意味がないので長く働くことができる環境づくりにも力を入れました。最初は入社後すぐに辞めてしまうというケースが続いていたのです。
ーー長く働くことができる環境づくりとは、具体的にどのようなことを行いましたか?
まずは社内の雰囲気を明るくしようと考え、はじめは自分達で壁を塗ったり部屋が明るくなるように工夫しました。あとは社内向けのブランディングです。自分たちの強みや、河辺商会ってどんな会社なのかという部分を社内のメンバーがあまりわかっていませんでした。外向きにアピールする前にまずは社内だと感じていたので、私がどんなことを会社でやっていきたいかを社員に伝える「方針発表会」を行いました。
ーー方針発表会はどのようなことを行うのですか?
会社や私がどういうことを考えていて、どこに力を入れていくのかということを知ってもらおうという機会です。方針発表会だけではなく、3ヶ月に1回社内報も発行して社内に向けて発信しています。
ーー社内報を発行されているのですね。どのようなことを掲載しているのでしょうか?
社内報では、取り組んでいる仕事や改善に対する結果報告や、社員の頑張りを知らせることが多いです。他部署で頑張ってくれている人のことはなかなか見えないこともあるので、ちょっとした取り組みでも頑張ってくれている人を紹介しています。会社や仕事について社員インタビューをしたこともあります。社内のメンバーに、自社のことをわかってもらうための取り組みですね。
ーー技術やノウハウを先輩から後輩に教える際はどのようにしていますか?
資料にまとめて残して伝えやすいようにしています。でも、技術というのは仕事をしながら若手に教えるしかないのかなとも感じています。ただ、そこに関しては、特に外観が重要で製造技術や量産のノウハウが必要なカメラなどの量産の仕事がどんどん減ってきてしまっています。よって、ベテランから若手に教育できる機会も減り、技術の伝承がしづらいという問題があります。
ーー試作などではなかなか教えきれない部分もありますか?
設計や試作での工夫や量産途中でのトラブル対応は、実際の量産中にやりながら教えるのが一番ですね。量産の案件がない中で、ただ勉強してもらうというのはなかなか難しいなと思います。
自分たちと“肌が合う”デザイナーと共に製品開発
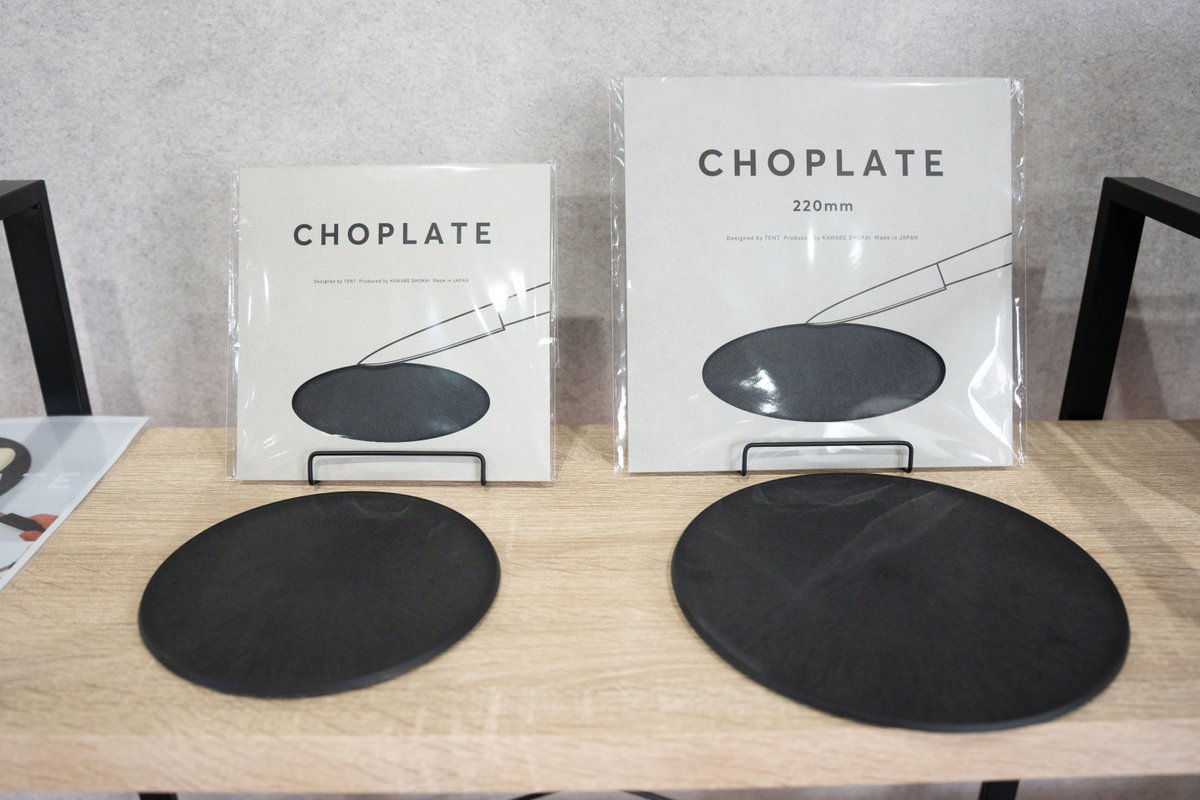
河辺商会が手掛ける自社製品は、「まな板になるお皿”CHOPLATE ”」です。まな板として食材を切ることはもちろん、まな板をそのまま皿にして食卓に出すこともできる製品です。
ーー自社製品開発に取り組んだきっかけを教えてください。
会社の将来を考えた時に、自分たちだけではなくお客様の事業も縮小傾向にあり、事業や業界がどんどん縮小・衰退していくのではないかという不安がありました。このまま衰退を受け入れてしまったら、長い間ベテランから引き継いできた技術止めることになり、それはしたくないと思いました。そこで、技術を活かして新しいことができないかと考えて挑戦することにしました。
ーーそこで“自社製品開発”に踏み切ったのは何か理由があるのですか?
以前から挑戦してみたいなとは思っていました。おそらく私が知らないだけで、創業から67年間の中で自社製品を作ろうという話は何度か出たと思うのです。でも、結果的にできなかったのは色々な問題があったからなのだと思うのですが、若手メンバーにそういう話をすると、実はちょっとやってみたいですというメンバーが2名ほどいたのです。じゃあ一度挑戦してみようかと思い、3人で自社製品開発を始めました。
ーー若手メンバーの立候補があったのですね。
でも、私を含めて製品開発の経験がなく何を作るかというところから全く決められませんでした。ターゲットを決めて、その人たちが困っていることはどんなことなのか洗い出して、じゃあこれを作ろうと決めても、形にする技術がなく立ち止まるというのが3ヶ月くらい続きました。
ーーその状況を打破したきっかけは何かあったのですか?
このままじゃまとまらないと思い大阪府堺市の産業振興センターの方や、ものづくり支援課の方に相談しました。そこで「大阪製ブランド」という大阪の町工場で作っている自社製品を認定している取り組みがあることを教えてもらいました。認定している製品を見ると、町工場とデザイナーがタッグを組んでオリジナルの製品を開発している方々が沢山いたのです。
ーー製品のデザインを外部委託して一緒にものづくりするという方法ですね。
そうです。その時に、デザイナーさんとコラボすることで何かできるかもしれないというイメージが膨らみました。じゃあどんなデザイナーさんとコラボしたらいいのかというところを考えるようになりました。
ーー自分たちのやり方や考え方に合うデザイナーさんを探し始めたのですか?
はい。堺市から紹介してもらったり、デザイナーコミュニティに参加したりするうちに、ウェブデザイナーやパッケージデザイナーなど様々なデザイナーさんがいることを知りました。その中で、製品をデザインすることはプロダクトデザインだとわかり、プロダクトデザインをしている方々にコンタクトを取るようになりました。中でも既に町工場さんと共に製品開発をしているデザイナーさんの方が相性が良いのではないかと思いました。
様々な方にコンタクトを取りましたが最終的には、その時既に『大阪製ブランド』に認定されていた藤田金属株式会社様に相談をさせていただき、ご紹介いただいたデザイナーのTENTさんと一緒に『CHOPLATE』を開発しました。
ーー相性を重視したのですね。
自分で調べてみると町工場とは関わりのないデザイナーさんの方が多くて、そういうデザイナーさんコミュニティに参加しても、ちょっと違うなと思うことも何度もありました。そういう失敗をしながら、私たち町工場と近い目線で一緒にやっていただける方にたどり着きました。
シンプルながら技術と知恵がぎっしり詰まった自社製品
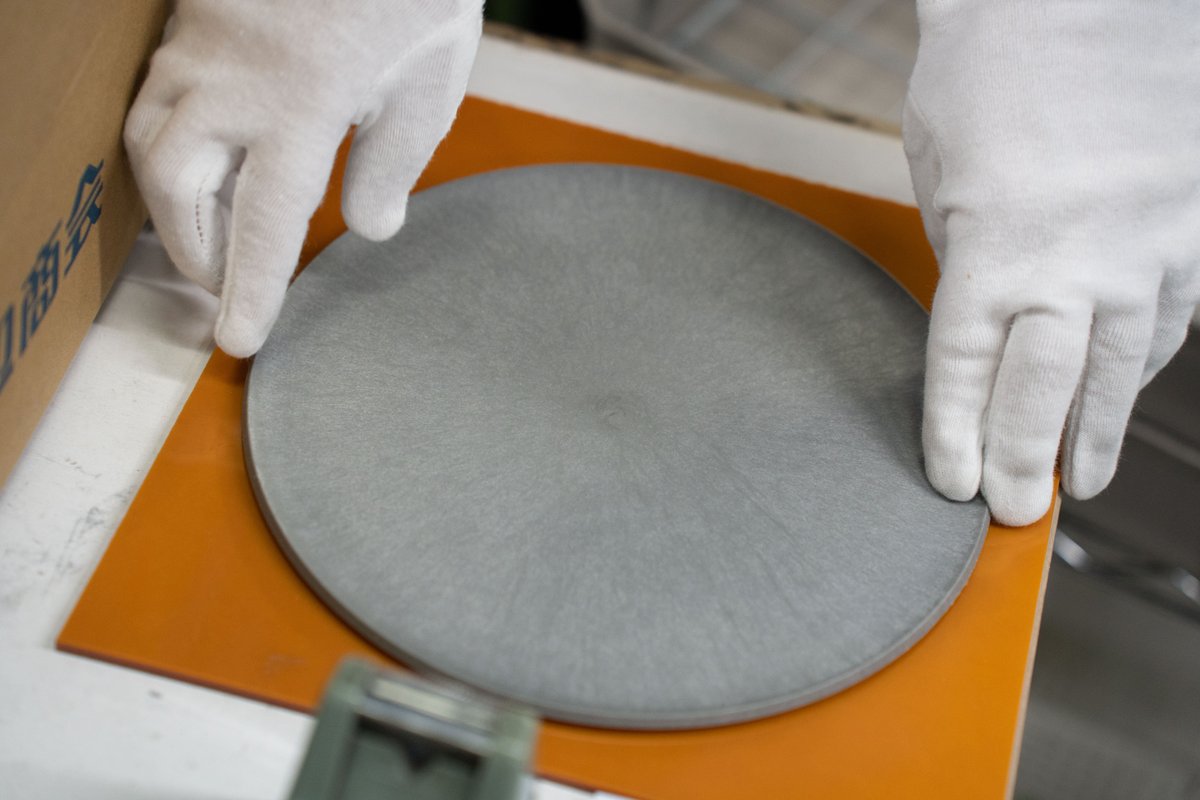
ーー自社製品としてまな板を作ろうとなったのはなぜですか?
河辺商会が得意とする外観が重視される製品、中でも黒色の製品を作ってきたことを活かした製品にしようとスタートしました。最初はVRゴーグルなど家電に近いものをイメージしていたのですが、外注加工が必要になり費用がすごくかかることがわかり、まずは社内にある既存の設備で完成させられるものにしようとなりました。そして、いくつかあったアイデアの中からまな板になりました。
ーー丸い形は最初から決まっていたのですか?
最初のアイデアは一般的な四角いまな板でした。ある時会話の中で弊社の若手メンバーが「見た目が黒でかっこいいので、刺身をカットしたあとお皿に盛り付け直さずそのまま食卓に並べてもいけますね!」と言ったのがきっかけで、ただのまな板ではなくお皿にもなるまな板という路線になり、丸い形になりました。
ーー『CHOPLATE』のこだわり、工夫した点を教えてください。
こだわったのは樹脂の材料選定です。普段使用している樹脂とは違う樹脂を使っているのですが、様々なメーカーから樹脂を取り寄せては試しての繰り返しでやっと辿り着きました。材料選定に関しては、最初に手を挙げてくれたうちの1人が中心となってくれました。
ーー樹脂のこだわりをもう少し詳しく教えてください。
『CHOPLATE』の素材には強度を高めるためにガラス繊維を混ぜています。強度のためにガラス繊維を入れること自体は他の製品でもよくあることです。ただ、ガラス繊維が表面上に出るので外観上NGとなることがあります。ですので、隠すために上から塗装することがほとんどです。『CHOPLATE』も最初はもっと表面の粗さが目立っていたのですが、成形時の温度調節を工夫してここまで抑えることができました。
ーーこの表面はそう設計されたデザインのように感じました。
そうなんです。粗さをこのレベルまで抑えられると食品を置いた時に映えるとデザイナーさんから言われたので、塗装はせずそのままの状態を採用することになりました。更にこの皿の表面には「シボ加工*」が入っているのです。実はガラス繊維入りの樹脂を使うとシボがほとんど見えなくなってしまうにも関わらずやっています。
*物理的にシワ模様(シボ)を付ける表面処理の一つ。金型の表面にシボ加工を施すことで成形品にその模様が転写する。
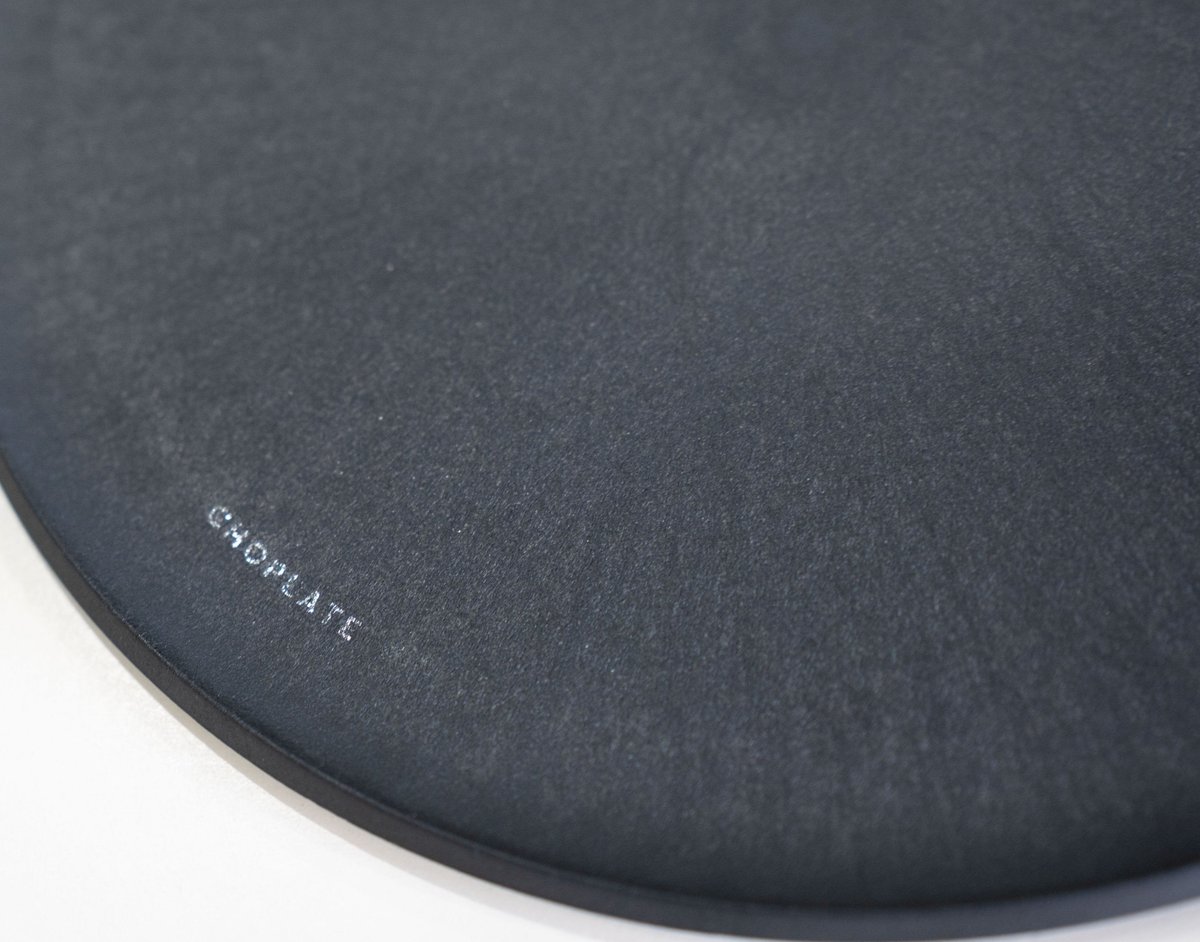
ーーそれはどうしてですか?
例えば、ご飯がくっ付かないように丸っぽい突起があるしゃもじがありますよね。『CHOPLATE』にもシボ加工を施すことでそれと同じような表面になり、汚れがつきにくくなります。ただ、それをあまり言っていないので、洗った後に布巾で拭くと引っ掛かるという話をされることもあります。
ーー細かな工夫もあるのですね。
製品の見た目以上に細かい工夫があると思います。冷却もただコンベアの上に置いて冷却しているのではなく、別途冷却の仕組みがあったり、金型の管理も一工夫必要です。簡単に真似できるものではないと思っています。
自社製品プロジェクトメンバーの前川大智(まえかわ だいち)さんにもご参加いただきました。
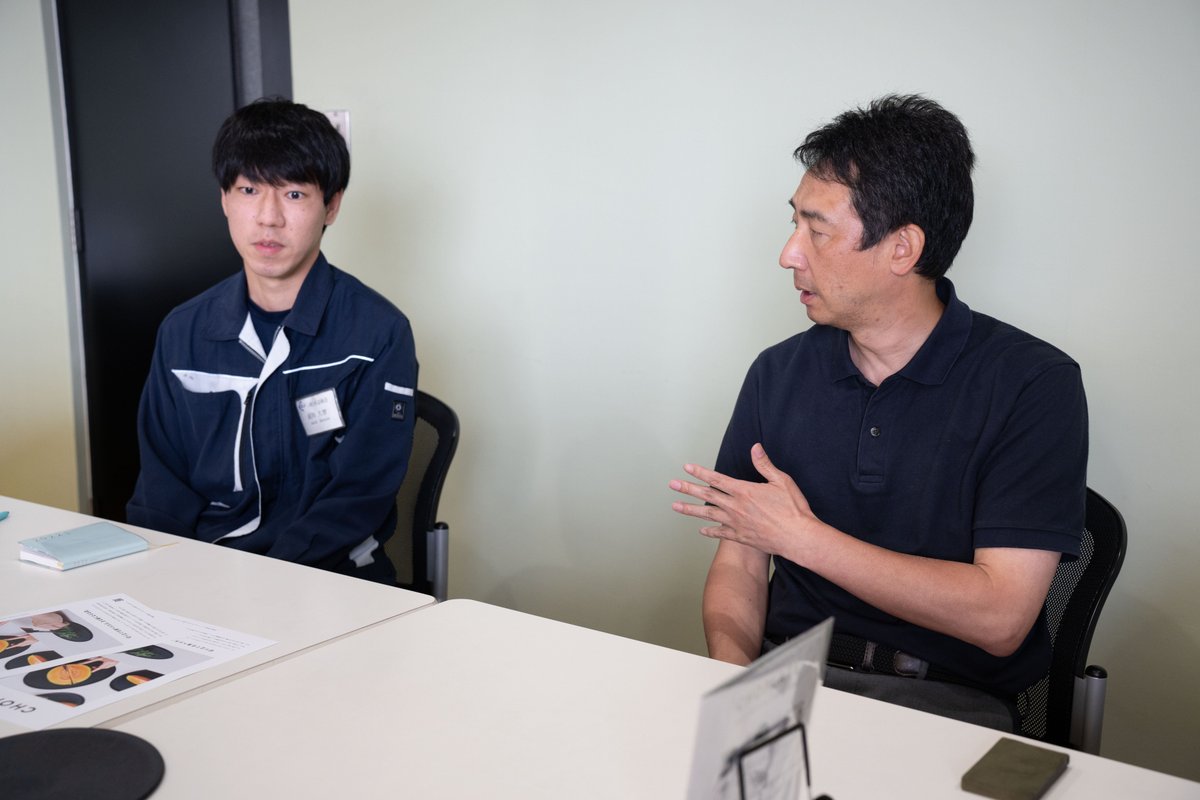
ーー前川さんは自社製品に関してどのような業務を担当されていらっしゃいますか?
前川さん:私の同期、先輩を含めた5、6名でホームページのレイアウトの検討や、SNSの更新などを行っています。製造業の仕事とはちょっと違う仕事ですが、興味のあることだったのですごくいい経験をさせていただいています。
福田さん:会社として長年B2C向けに販売経験があれば先輩から教わることもあると思いますが、全員がはじめてですので色々と大変だと思います。でも、徐々に若手を中心に積極的に勉強して挑戦してくれるようになりました。
ーー積極的に勉強して挑戦できる雰囲気は良いですね。
福田さん:この仕事に関わらず、新しい仕事というのは自分で考えてやらなければいけないことが多々あります。大変なこともありますが、高いモチベーションを持って仕事に臨んでくれていると感じます。
ーー福田さんが目指す会社とはどんな会社でしょうか?
みんなが100%の力を発揮できる会社です。お客様に迷惑を掛けないため、もっといいものをつくるためには時に厳しいことを言われたり、メンバー同士ぶつかることもあります。それでもお客様に喜んでもらうために、みんなが100%の力を出せる会社にしたいです。今まで取り組んできたのは、そのための環境づくりですね。
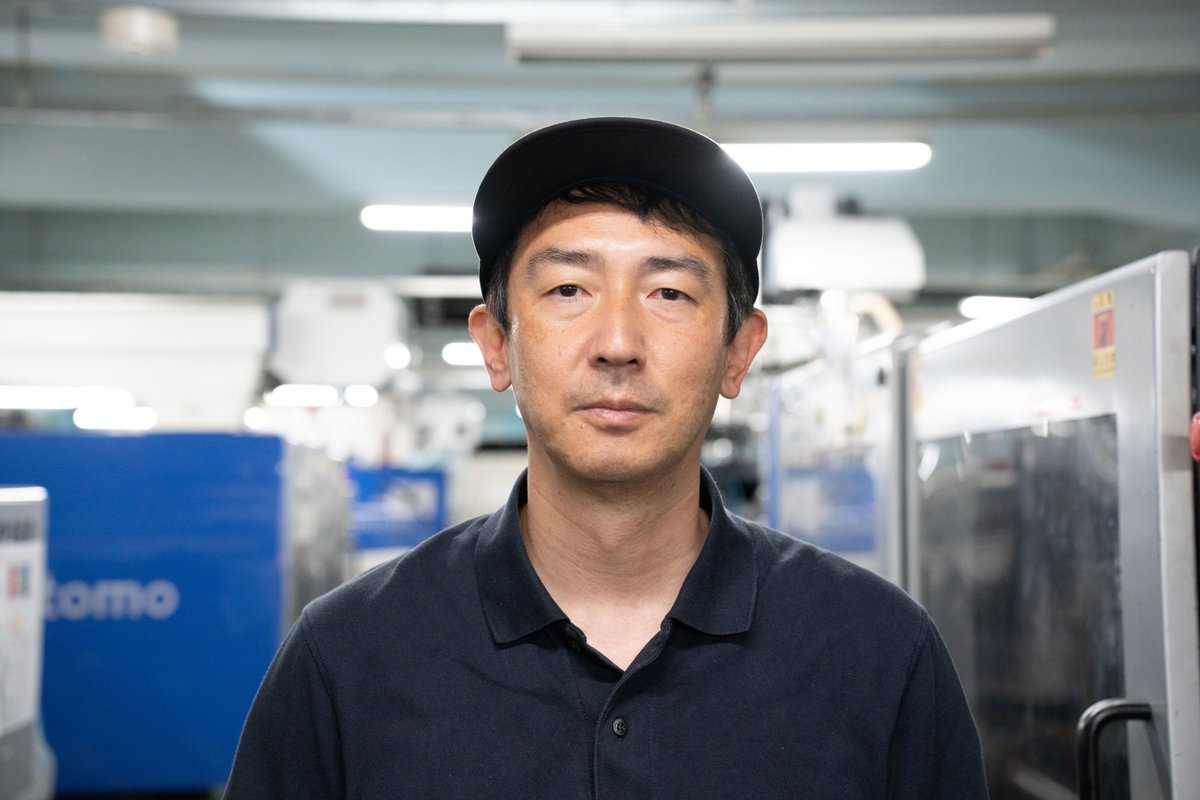
株式会社河辺商会
所在地 大阪府堺市西区平岡町85-1
代表取締役 福田康一
会社HP 河辺商会
編集後記
一見、シンプルなお皿に見えますが、様々な技術や狙いが盛り込まれていると感じました。町工場がつくる製品の魅力は細部に宿る技術にあると思います。
また、自社製品の開発や販売が若手社員の成長の機会にもなっているのが良いと感じました。福田さんのおっしゃっていたように、仕事へのモチベーションに繋がったり、本業とはまた少し違った目線からものづくりについて学ぶことができるのではないでしょうか。