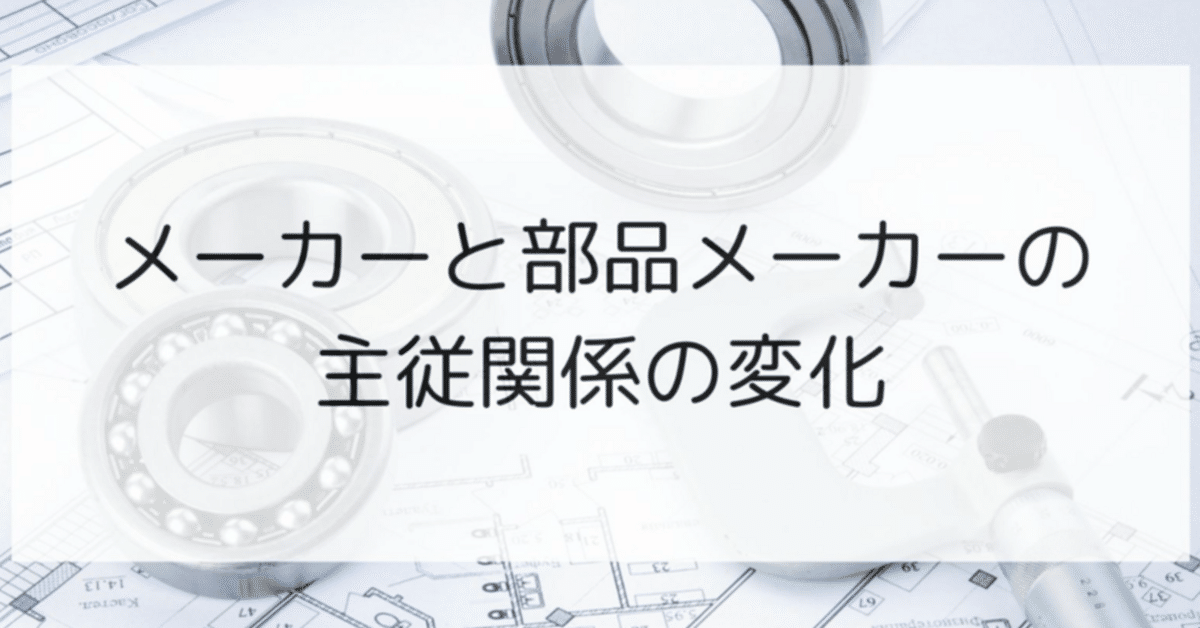
メーカーと部品メーカーの主従関係の変化②
「メーカーと部品メーカーの主従関係の変化①」から続く
(2) 「ものづくり3.0」、そして「ものづくり4.0」へ
(クローズド型/オープン型)
「ものづくり3.0」の世界でのキーワードは、「オープン型」です。
「ものづくり2.0」の世界までは、「モジュラー型」で各部品をつなぐインターフェイスが共通化されても、社内やグループ内などに閉じられたものでした。
これに対して、主導権を握った部品メーカー側が仕様をオープン化することによって、市場での規格の統一化を図り、グループの枠を超えて複数の完成品メーカーと取引を行うようになります。
部品メーカーが1社の要求水準に合わせて仕様を決める形ではないので、そこで提示される共通仕様に完成品メーカーが合わせる形となります。
このため、両者の関係性は水平分業体制になるとともに、部品の大量生産が可能となるため、コストは大幅に削減できるようになります。
インターフェイスもオープン化されているため、多くの企業が参入していくことが可能となり、コスト削減競争の結果、大量生産された製品は一気にコモディティ化していきます。
21世紀に入るとこうした流れがさらに進み、グローバル仕様を決める決定権が、各モジュールや製品全体をつなぐソフトウェアを設計する事業者に移行していきました。
製品の設計者と生産者の完全な分業が行われるようになり、ソフト面の商品企画・設計力とビジネス構想力を併せ持つ限られた者のみが、プラットフォーマーとなりました。これが「ものづくり4.0」の世界となります。
わかりやすい例は、スマートフォンの設計を行うアップルと受託生産を行う鴻海精密工業(フォックスコン)などの関係です。
1990年代は製造業において、こうした革命が起きた画期的な時代であり、そのキーワードはデジタル化です。例えば、1970年代までの電化製品は、アナログ技術で作動する基幹部品が多面的に組み合わさり、相互依存しながら機能をしていたため、自動車の場合と同様にインテグラル型の製品でした。
ところが、1980年代以降、「マイコン」(マイクロ・コントローラ・ユニット)と呼ばれる電気機器を制御する回路とそれを動かすソフトウェアである「ファームウェア」が大きく進化したことで、デジタル化が一気に加速します。
1980年代以降普及するエレクトロニクス製品、例えばCD、DVD、デジカメなどの音響・映像機器、パソコンや携帯電話などの情報通信機器、薄型テレビやデジタル家電などで、完成品メーカー側も積極的にオープン化戦略をとりました。
1980年代からの円高と相まって、日本のエレクトロニクスメーカーは、安価な労働力を求めてアジア諸国へと生産拠点の移転を行い、現地メーカーの生産力が大きく向上しました。
こうした企業の中から、OEM生産を皮切りに国際競争力や技術力を高めてEMS(製造受託会社)と呼ばれる段階に進む企業が、次々と現れるようになりました。
EMSは受託製造に特化した企業ですが、世界中のメーカーから製造を請け負う中で培った技術やノウハウを活用して、製品設計や生産技術・ラインエンジニアリングの開発を行う企業も出てきています。
EMSの重要性が高まった背景には、エレクトロニクス製品のコモディティ化と新製品の寿命が短縮化されたことが挙げられます。製品のコモディティ化が進むと、製品ごとの本質的な機能にはほとんど差が見られなくなり、付随的な機能追加やデザイン性などマーケティングによる差別化に、競争の中心が移ります。
このように製品サイクルが短縮化されると、完成品メーカーが新製品の開発を行いながら、自社の製造工場のラインを製品サイクルに合わせて更新していくことが困難となってきます。このため、特定の製造ラインに特化して多数の企業と取引できるEMSの強みが活かされることになります。
1990年代後半以降は、ソフトウェアの重要性が高まったこともあり、設計と製造の分離が一層進みました。もっとも進んだのは、製品開発サイクルが短く、生産設備投資に莫大なコストがかかる半導体業界です。半導体のイノベーションの速度を表す表現として、インテルの創業者のゴードン・ムーアが述べた「半導体の集積率は18カ月で2倍になる」という通称「ムーアの法則」がよく知られています。
半導体の集積率が2倍になるということは、同一性能の半導体の製造コストも半分に下がることを意味しています。このような製品開発サイクルの業態では、各社が自身の強みを生かして開発か製造のどちらかに特化することが最善の選択となります。製品の企画・設計・マーケティング・販売などの機能に特化した企業を「ファブレス」、生産機能に特化した企業を「ファウンドリ」と呼びます。
半導体業界における「ファブレス」の代表は、
クアルコム、
ブロードコム、
エヌビディア、
AMDなど、いずれも米国企業である一方で、
「ファウンドリ」の代表は、
TSMC(台湾)、
サムスン電子(韓国)、
UMC(台湾)、
グローバルファウンドリーズ(米国)などが挙げられます。
一見すると、シリコンバレーの米国企業が設計を行い、アジアの新興国企業に生産を委託する水平分業のように見えますが、構図はそれほど単純ではありません。
特にTSMCの近年の技術開発のスピードは目覚ましく、2010年代後半には最先端の7nm(ナノメートル)のチップはTSMCしか生産できないという状況を作り上げ、半導体業界全体の主導権を握るまでの存在に成長しました。
TSMCに対抗するために、自社で開発から製造までを行う垂直統合型の半導体メーカーの代表であるインテル(米国)やサムスン電子(韓国)も、ファウンドリ事業にも力を入れるようになりました。
特にインテルは「IDM2.0」戦略を打ち出して、インテルの持つプロセス技術とパッケージング技術を活かすファウンドリ事業を推進することで再び業界の主導権を握ろうとしています。(図-2)
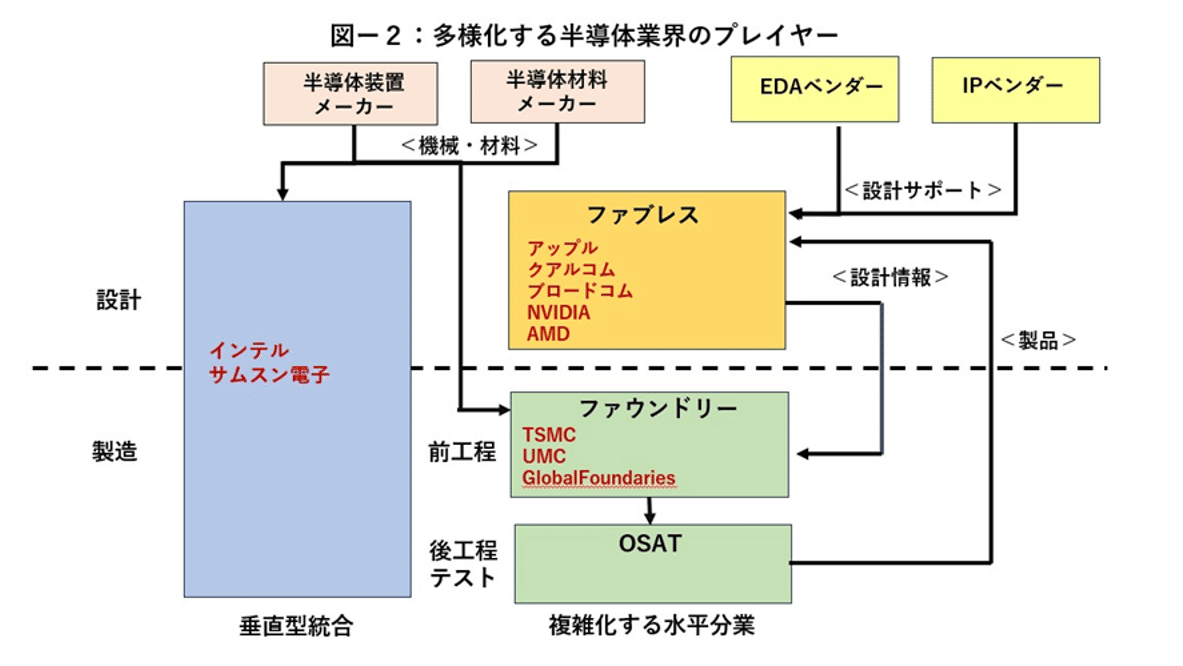
(3) 日本のエレクトロニクス産業の敗北から学ぶ教訓
ここまで、高度経済成長期の自動車産業から最先端の半導体産業までを例に、「ものづくり」における分業体制がどのように変わってきたのか、振り返ってきました。
こうした変革の過程で、かつては強かった日本のエレクトロニクス産業がその地位を失ってきたことは、私達の記憶にも新しいものでしょう。
パナソニック傘下にあった三洋の洗濯機・冷蔵庫事業が2012年にハイアール(中国)に売却され、かつては薄型液晶パネルで世界を席巻したシャープが2016年に鴻海(台湾)に買収され、東芝の白物家電部門が同年にマイディア(中国)に、映像事業は2018年にハイセンス(中国)に売却されるなど、例を挙げれば枚挙にいとまがありません。
日本のエレクトロニクス産業の衰退は、円高や日本国内市場の継続的なデフレなどの外部要因によるところもありますが、1990年代からすでに始まっていた、ものづくりにおける分業体制の変化に、日本企業がうまく対応できなかったことが、大きな原因となっています。
例えば、DVDプレイヤーや DRAMメモリーなど、日本の企業が主導的に開発を行い、特許の多くを有している製品群でも、市場に普及するビジネスの段階で競争力を失ったのは、「オープン型・モジュラー型」製品の特性を利用したビジネスモデルの設計に失敗したことが要因と言われています。
先に例を挙げた半導体業界でも、製品の開発・設計から最終完成品ができあがるまでの過程で、様々なアウトソースが行われています。
半導体製造装置メーカー、材料メーカー、設計段階での作業をハード・ソフトの両面で支援するEDAベンダー、設計図を提供するIPベンダー、製造の前工程を担うファウンドリ、製造の後工程とテストを行うOSATと多様なプレイヤーが、それぞれの強みを生かしながら、主導権争いを演じています。
こうした半導体のサプライチェーンの中でも、半導体製造装置や材料など日本の企業が強みを持っている部分も残っています。特にこれ以上の半導体微細化プロセスが困難になってきていると言われる中で、インテルがすでに本格的な採用を表明しているように、製造の後工程でのチップレット化の最新技術として「3Dパッケージング」が注目を集めるなど、競争ルールは今後も大きく変化する可能性が高いと考えられます。
IoTやAIの活用が広がり、すべての産業がこの影響を受けると言われている中で、日本のものづくりに携わる企業も、変化する競争ルールの中で自らの優位性をどのように築いていくか、改めて戦略を見直していく必要があると言えるでしょう。(山縣敬子・山縣信一)
<<Smart Manufacturing Summit by Global Industrie>>
開催期間:2024年3月13日(水)〜15日(金)
開催場所:Aichi Sky Expo(愛知県国際展示場)
主催:GL events Venues
URL:https://sms-gi.com/
出展に関する詳細&ご案内はこちらからご覧ください。
<<これまでの記事>>
諸外国の「ものづくり」の状況とトレンド①
諸外国の「ものづくり」の状況とトレンド②
諸外国の「ものづくり」の状況とトレンド③
日本の製造業の歴史を紐解いてみる
日本の製造業の成長を促した構造的要因とは?
日本の製造業の競争力を低下させた構造的要因
メーカーと部品メーカーの主従関係の変化①