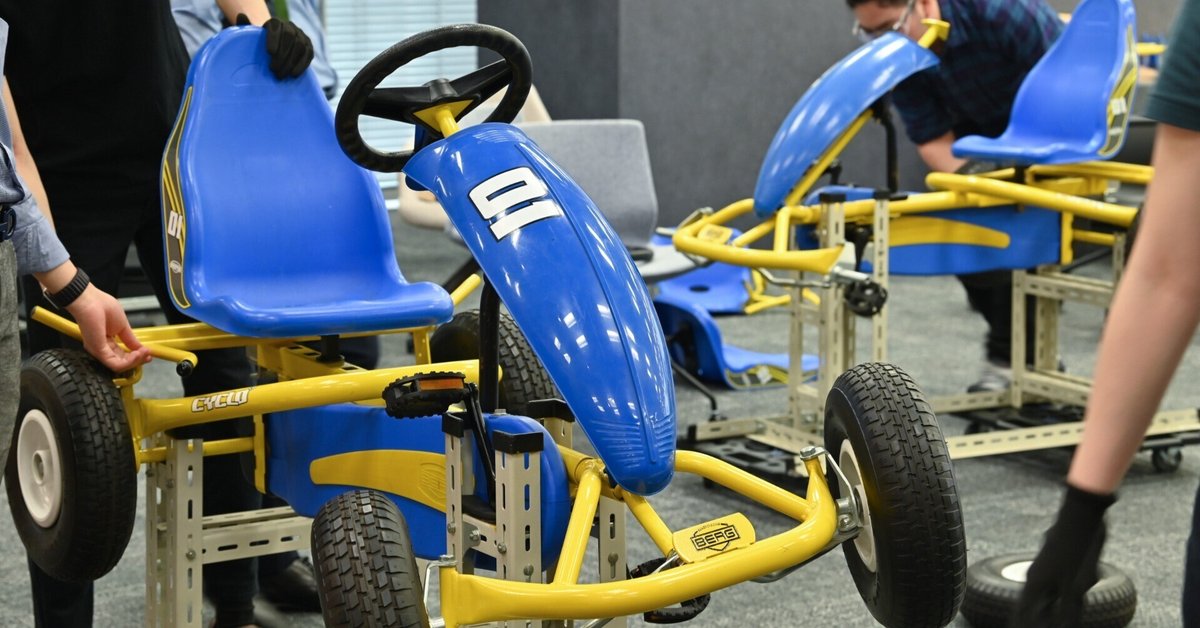
【人材育成】ペダルカートからカイゼンを学ぶ!カートファクトリーを実施しました🚙
2024年5月、新入社員を対象としたカートファクトリーが開催されました。
カートファクトリーとは、ペダルカートを作りながらものづくりについて体験を通して学習するプログラム。
チームでカートを分解・組み立てし、タイムや安全性などさまざまな側面から改善策を考え、またカートを作り、さらなる改善策を練り・・・ということを繰り返しながら、ものづくりを学びます。
今回はJMACで行われた新人研修をレポートします!📝
カートファクトリーの詳細はこちら↓
まずはカートの構造を確認する
カートファクトリーは、言われたままにやってみるのではなく、「自分たちで考えて実行する」ことが要求されます。
コンサルタントからの一方的なレクチャーはなく、適宜アドバイスを受けながらも、基本的にはチームメンバーが自分自身で考えて進めます🤔
実際に手を動かして自らが作業者となるため、座学とはまた違うリアルな「ものづくり」を体感しながら学ぶことができます。
・リアル環境での学び
・失敗体験からの学び
・チームでの学び
とはいえ、目の前に並んでいるのは見たことも触ったこともないペダルカート。まずは手順書を見ながら構造を確かめます。
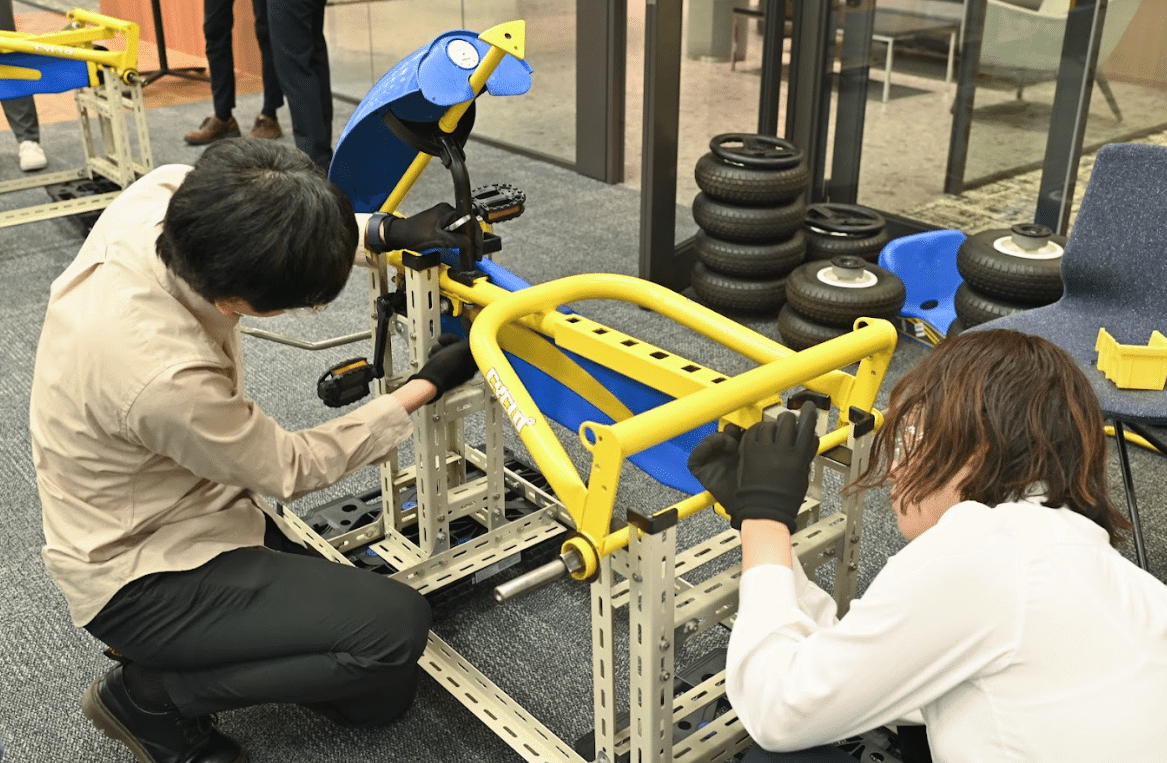
実際にやるまでは「ねじを外して、つけるだけでしょ?」なんて思っていましたが、使い慣れていない工具ばかりで一苦労。
ソケット、レンチ、スパナ・・・🔧🔩
慣れていない人にとっては聞いたこともない工具がたくさん。
さらにサイズも細かくあるのでどれを使ったらよいのか分かりません。
何度も分解と組み立てを繰り返し、ようやくカートの構造がつかめたところで、1回目のRUNに挑戦です!
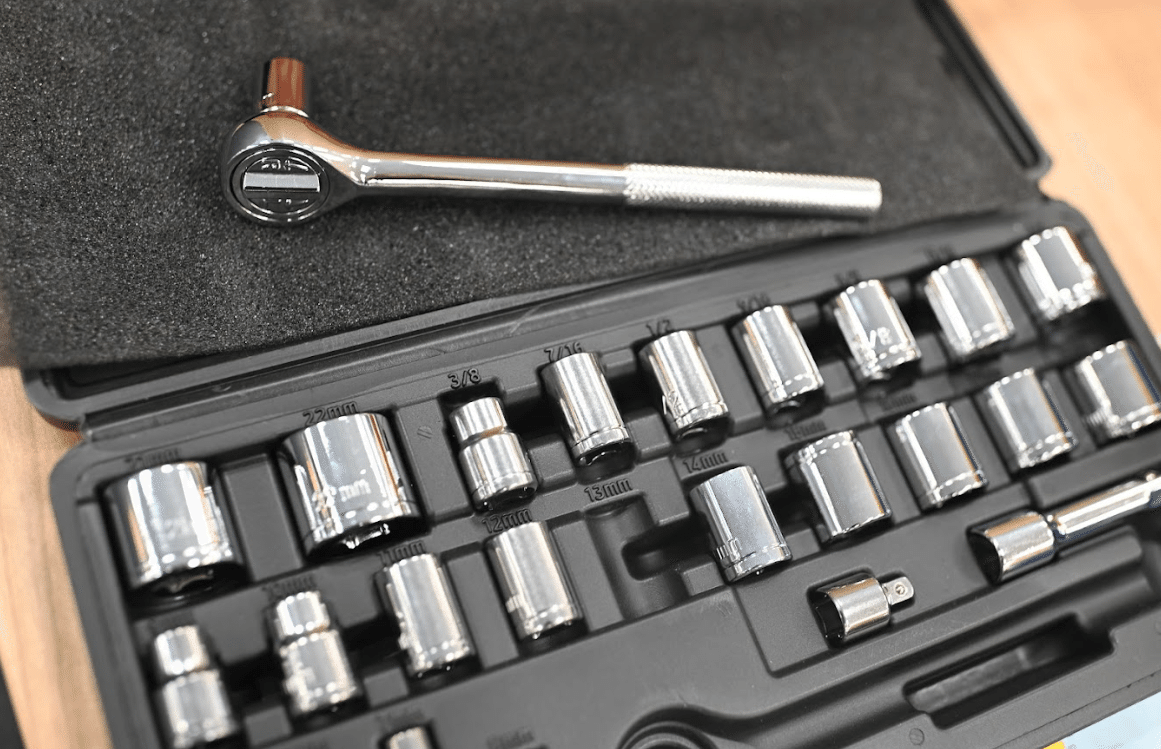
RUN1周目
カートファクトリーでは解体、分解の一連の作業を繰り返すことを「RUN」と呼び、現場と同じようにそれぞれの役割を決めて行います。
リーダー:指示だし
品質:品質として適正かチェック
解体:カートを解体する
組み立て:カートを組み立てる
物流:それぞれの工程に必要な部品を届ける
他の人は作業を録画し、問題点を発見します。
何度かやっていると作業自体には慣れてくるものの、サイクルをくりかえすことで疲労から集中力が低下し、ペースが落ちる人もいました。逆に流れに乗ってスピードアップする人も🚙
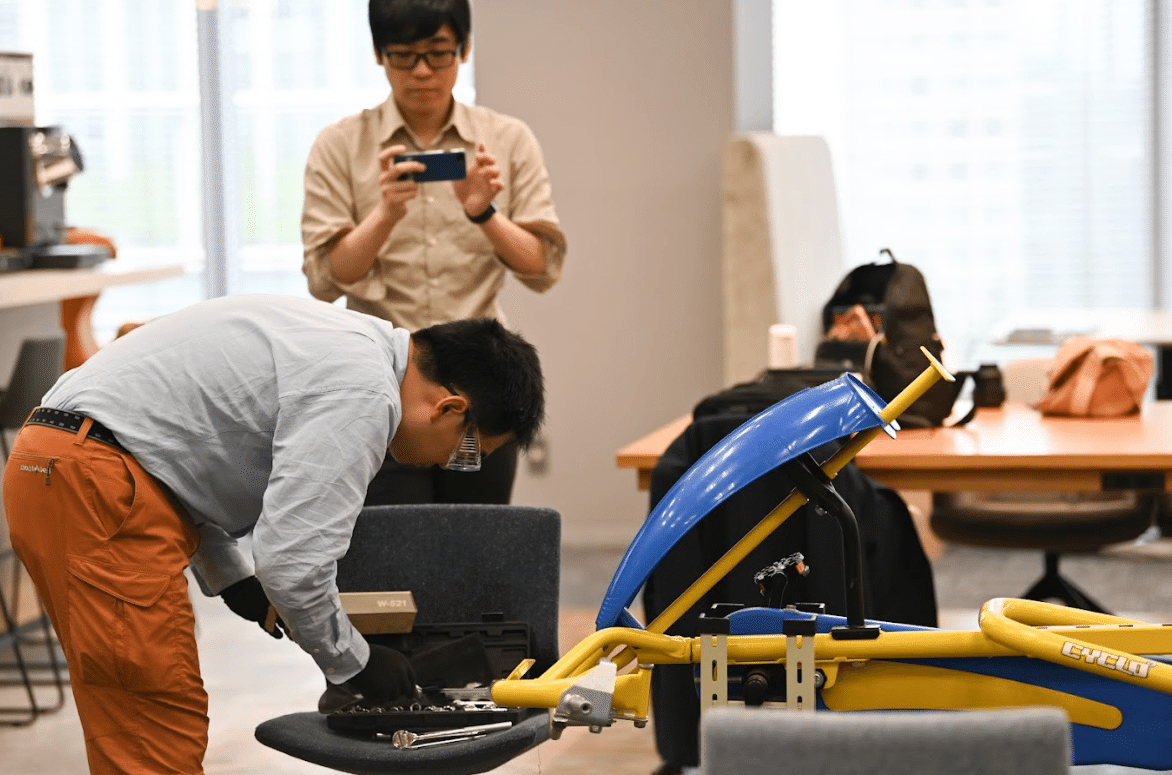
改善①
上手くいかない作業のコツの検証を行います💭
「作業の順番はどうすればよいのだろう。」
「移動時間が多くなっている。効率をあげるにはどうすればよいか」
自分の工程だけではなく、別の工程も巻き込んで相談します。
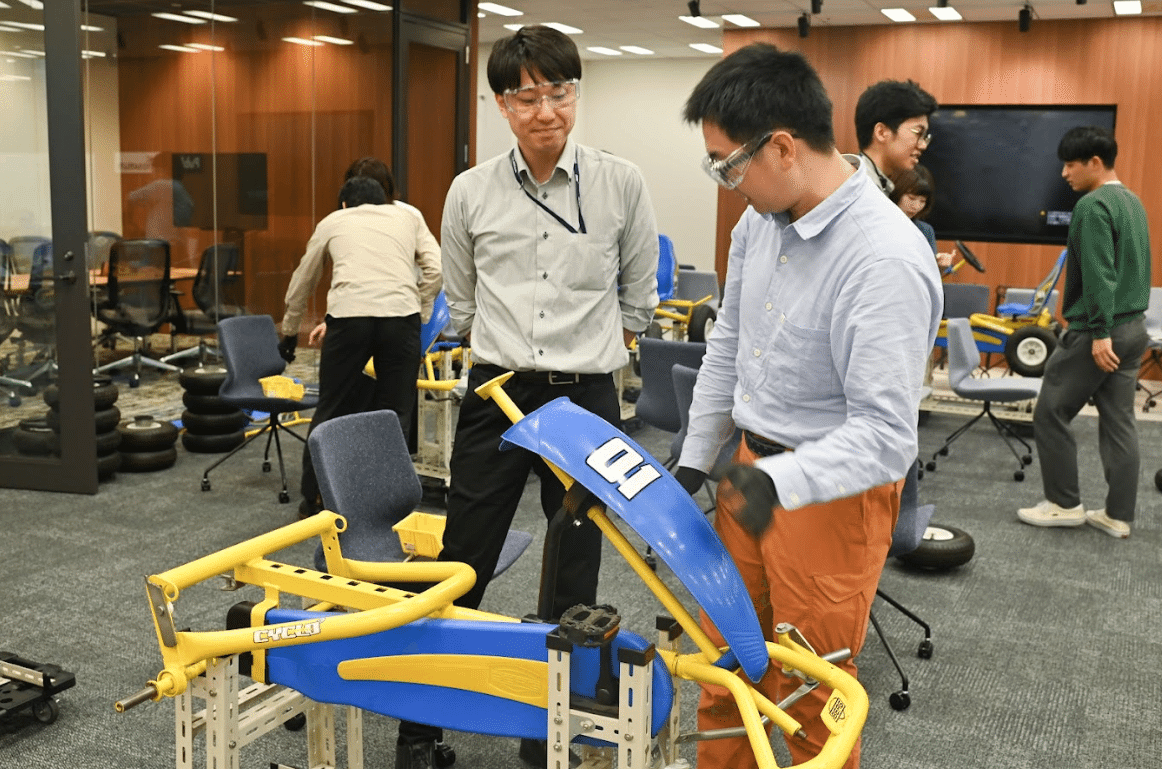
「ここはこうやって持つとスムーズにいきます!」
「こうやると引っ掛かることなく早く部品が抜き取れます!」
成功率が低いと感じる作業は運に身を任せるのでなく、対処法を模索。次に作業するチームメンバーのために作業のコツや改善点を、カートをつかって実演しながら全員の前で発表します🙋
今回の結果を経て、各工程の必要人数や分担などを見直しました。時間の記録や録画を見ながら各工程ごとの分析を行い、タイムを縮めるために思いつく限りのことを話し合います。
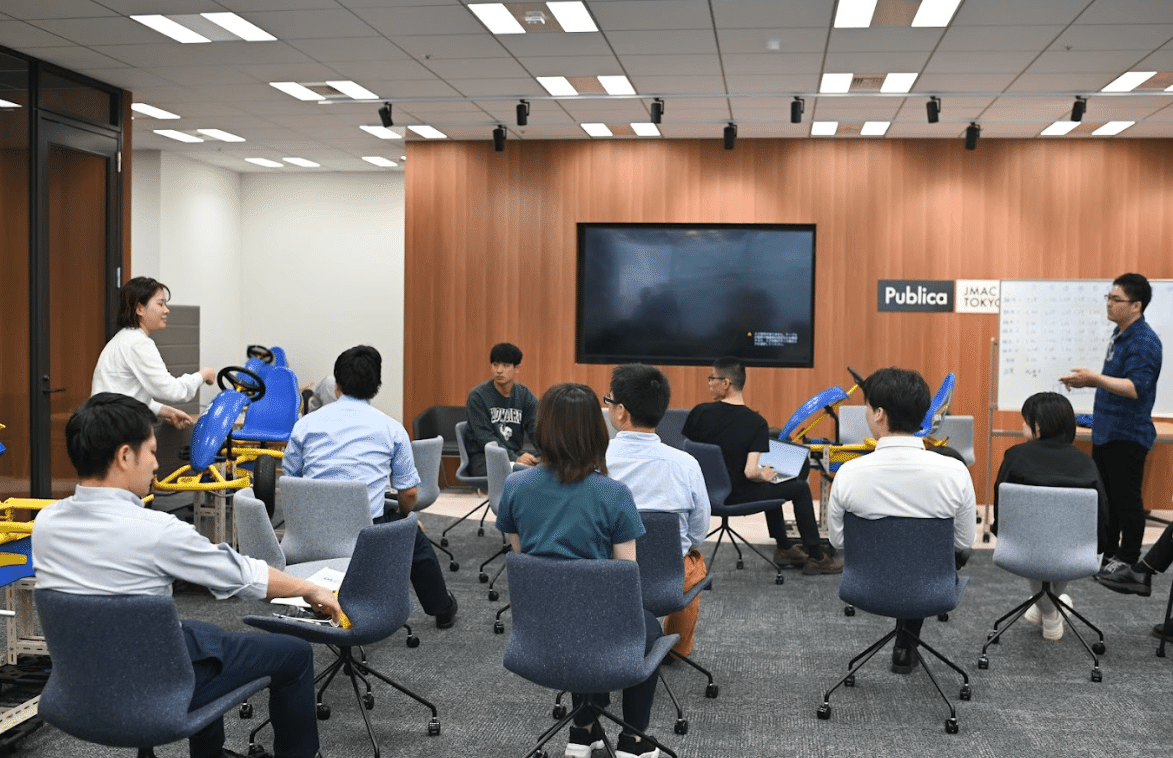
RUN2周目
反省点、改善点をもとに再びRUNを行います。
各工程1周目とは別の人が担当するため、引き継ぎも重要になります。
先輩コンサルタントからは、
「作業のやり方だけではなく、さまざまな側面から考えてほしい」
「各工程・作業のバランスに着目してほしい」
とアドバイスがありました。
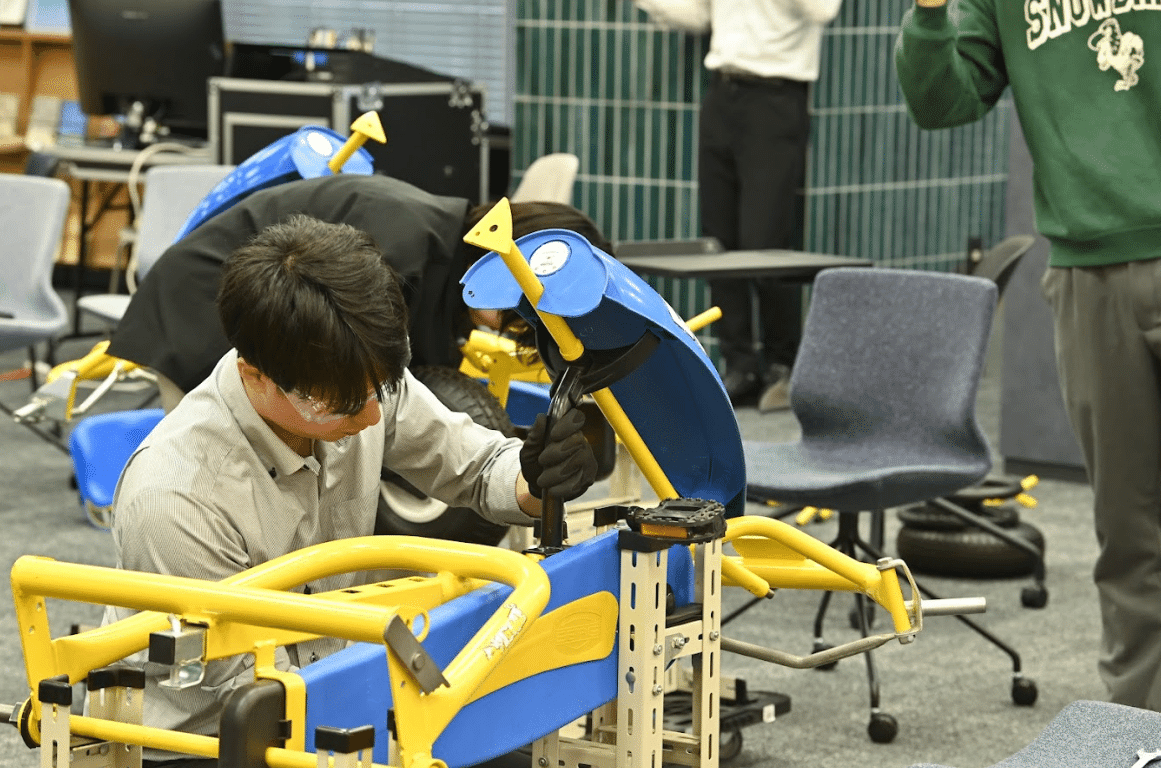
改善②
3回目のRUNの前に再び作戦会議。
「現在のレイアウトは適切なのか?」
「作業によって秒数にバラツキがあるから、平準化するためには作業の割り当てを見直したほうがよいかもしれない」
悩んでいるだけでは進まないので、まずは一度試してみる思い切りの良さも必要です。
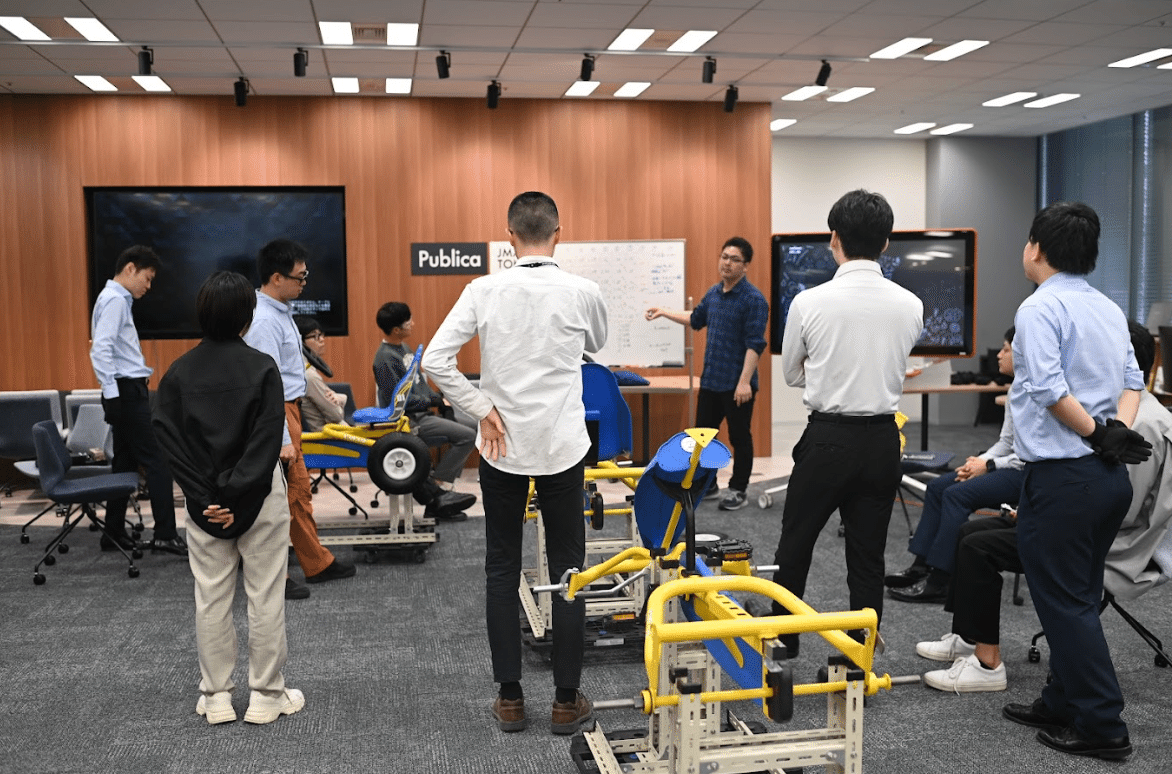
なにか気づきがあったときに、小さなことでも黙っているのではなく発言し、一緒に考えていくことがチームワークには求められます。
また、作業している本人だけでなく、見ている第三者の立場から動きが悪かったところを遠慮なく指摘し合う空気づくりも重要です🙂
なんでも発言できる環境で、現状に満足せずどんどん改善サイクルをまわしていくことは、コンサルタントだけではなくすべての現場や仕事で必要なことだと思います。
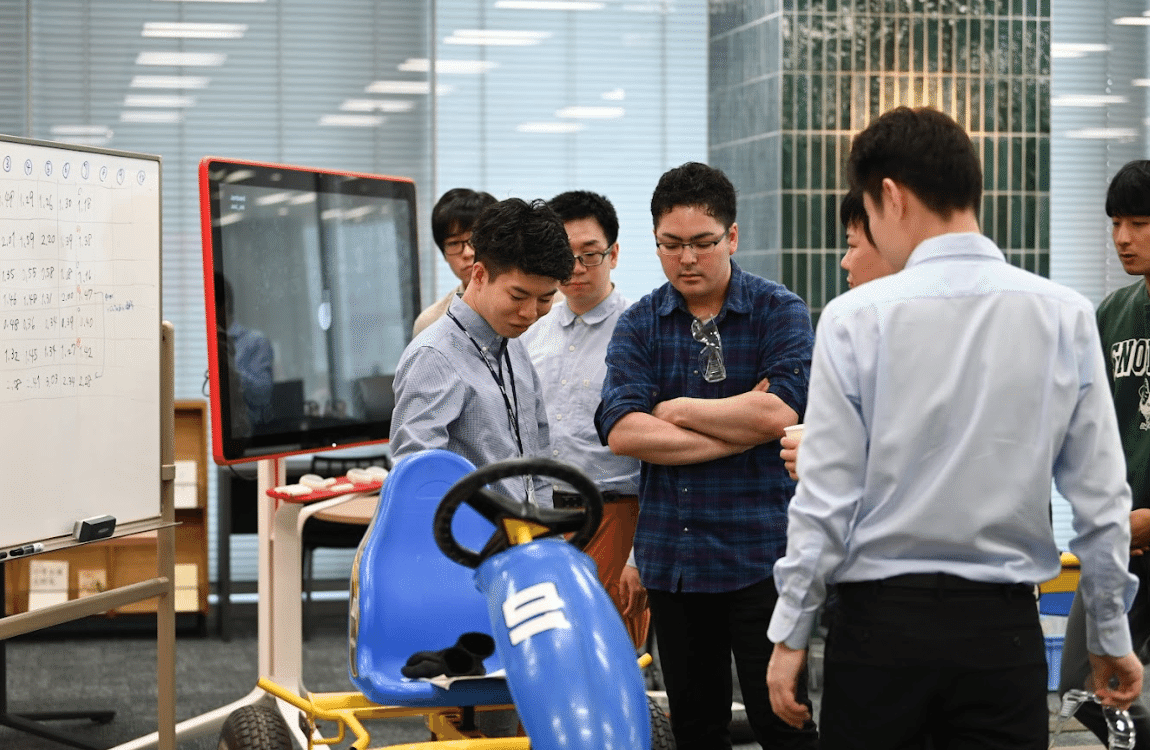
RUN3周目
いよいよ最後のRUN!
カートファクトリーに絶対の正解はありませんが、チームが導き出した最適解で挑みます。
焦ると地面に部品を落としてしまったり、思わず躓きやすい位置にモノを置いてしまったり、計画通りにいかない部分をどう対処するかも、リアル・シミュレーションの面白いところ!
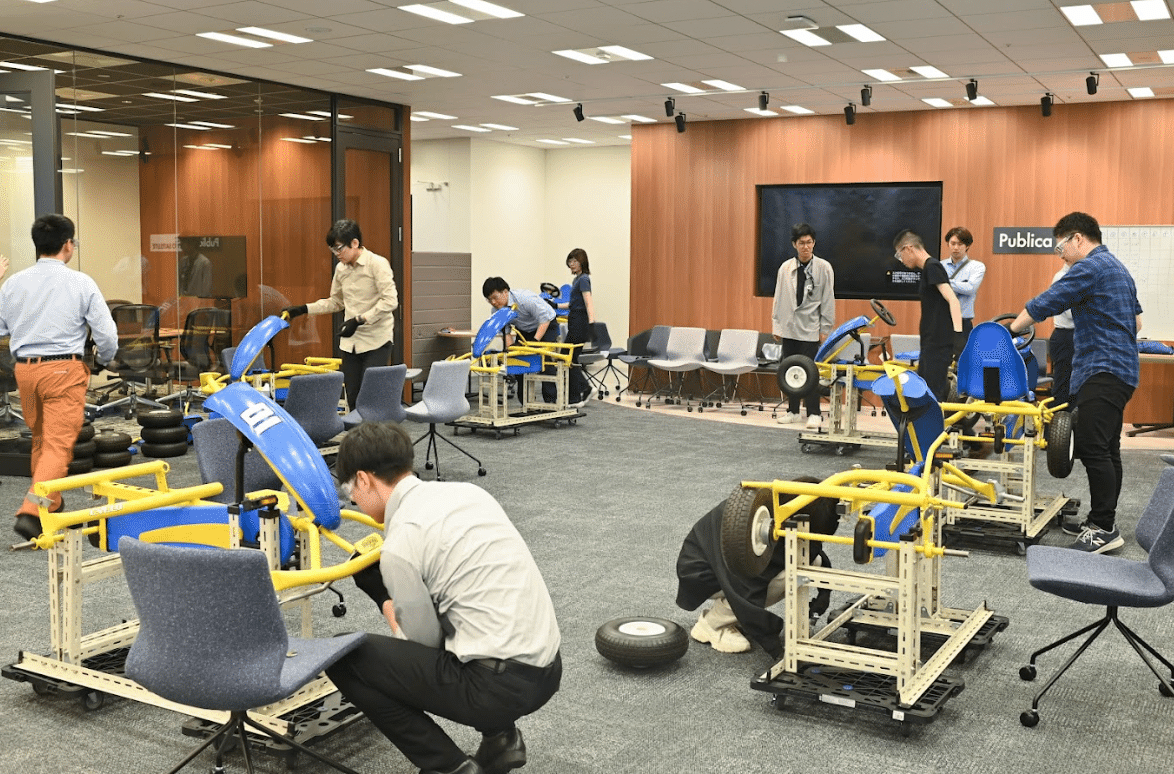
ふりかえり
受講生からは以下のような声が上がりました。
実際に作業をやっていると周りを見ることを忘れてしまい、
工程のつなぎ目をみれずに、個々の作業になってしまっていた。
各工程の負担を減らすことばかりで、物流について考えられていなかった。
効率に気を撮られると安全面がおろそかになった。
標準時間をもっと使用して正確な予測が出来ればよかった。
どこまでなにを分析するか最初に定め、欲しいデータを揃えるべきだった。
一筋縄ではいかないカートファクトリー。改善を繰り返しても、どんどん次の改善が飛び出します。
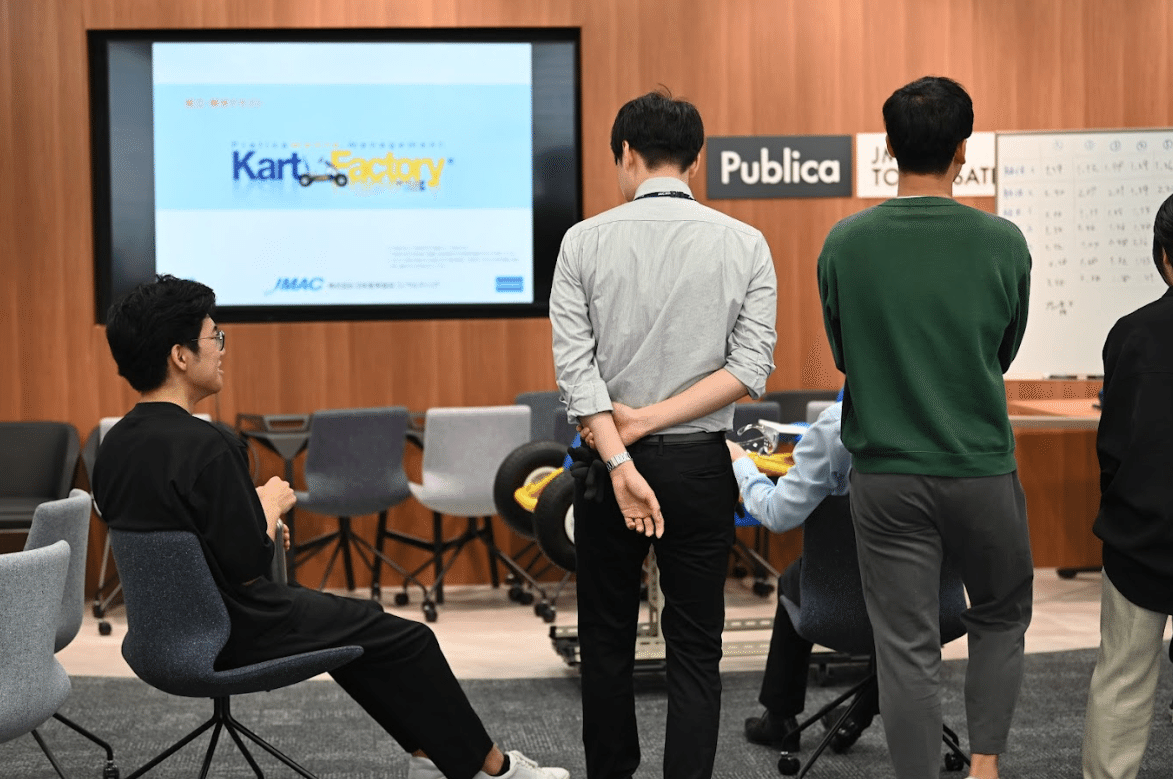
最後に先輩コンサルタントからレビューをもらい、カートファクトリーは終了。この後はアカデミー生の登竜門(?)、Pコースが待っています。
ここで得た知識をぜひ、次の研修でも役立ててほしいです。
Pコースのレポートはまた後日!お楽しみに!
お読みいただきありがとうございました。