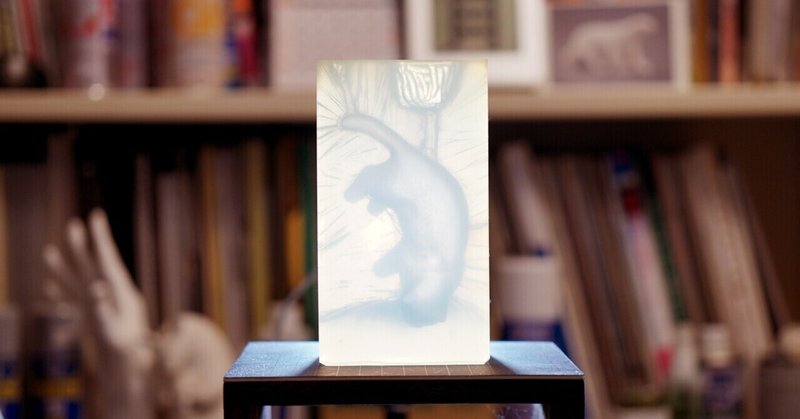
細かすぎて誰も聞いてくれない。レジンフィギュアの作り方。無理やりお話しします。(2:シリコーン型篇)
私はネコ専門の造形作家で、レジンで小さなフィギュアを作っています。その制作プロセスをご紹介する記事の2話目です。完成した原型を元に、シリコーン型を作るところまでをお話しいたします。
【写真上:私のネコフィギュア作品です】
空気の流れを考えて、型の中での姿勢を決めます。
最終的にはシリコーン型にレジンを流し込んで完成させるのですが、そのためには型の中で空気がきれいに逃げて原型全体にレジンがいきわたる必要があります。
そのためには空気が滞りなく逃げて排出されるような、型の中での原型の角度・姿勢が非常に重要です。
なお余談ですが、シリコーンは英語ですが、カタカナの場合、シリコンとシリコーンは違う言葉です。シリコンはケイ素で「Silicon」。シリコンバレーとかはこちらですよね。一方シリコーンは「Silicone」でゴムのような素材。今回私がお話しするのはゴムのようなSilicone=シリコーンの方です。余談まで。
【上図:右のような原型の角度を目指します】
姿勢を決めたら、そのまま固定します。
型の中での姿勢を決めたら、原型をその姿勢で正確に固定する必要があります。これも意外と難しい事で、試行錯誤の末、温度90度くらいのお湯で軟化し冷えると固まる樹脂「型取くん」を使って不安定な原型の角度を固定しています。
【写真上:微妙な角度で原型を固定している。白っぽい部分が型取くん】
次に固定した原型に垂直にドリルで穴を開けるのですが、樹脂粘土の原型は、それほど硬くはないので、万力などの固定具で圧力がかかる固定はできません。
そこで強く固定するのではなく弱い力で穴を開ける、という逆の発想でたどり着いたのが、固定されたハンドドリルでそっと穴を開けるという方法です。
【写真上:垂直に穴を開けるため手動のボール盤を使います】
【写真上:慎重に手でドリルを回して、垂直に穴を開けている】
ドリルで開けた穴に金属ステム(軸)を差し込み、そのステムの刺さった原型をひっくり返して重りに固定します。重りはなるべく小さくても重いものが良いので銅の塊を使っています。実は比重ではわずかに鉄よりも重いそうです。
【上図:理想の角度を計算して、軸と重りで自立させる概念図】
【写真上:実際に軸と重りで自立させたところ】
容器を作り、シリコーンを注ぎます。
ここまでくれば、後はこの角度を維持したままシリコーンで覆います。そのために囲いを作って容器状にします。今はモチーフのサイズに合わせて、その都度プラ板で作っています。
【図:角度を維持したままシリコーンを注ぐ概念図】
【写真上:モチーフサイズに合わせた囲いをプラバンで作ります】
【写真上:分量を計算してシリコーンを注ぐ】
シリコーンにはいろいろな種類がありますが、私は少し高価ですが透明タイプを使用します。それは後ほどご説明しますが、シリコーンを分割する時に原型を傷つけないように刃物を使って目視でカットするので、シリコーンの中で原型の位置が目で見える必要があるためです。
シリコーンの注入から硬化にかけては、シリコーン内に気泡が残らないようにする必要があります。シリコーンの硬化には時間がかかるので、ほっておいても自然に多くの気泡はゆっくり液外へ排出されますが、しかし確実に全く気泡の残らないシリコーンにするには「真空脱泡機」を使うのが最適です。
重要機材「真空脱泡機」登場
真空脱泡機とは、密閉容器内の空気をポンプで排出して庫内を真空(低圧)にし、シリコーン内の気泡を強制的に排出させるというものです。
【図上:真空脱泡の概念図】
【写真上:実際の真空脱泡機】
この真空脱泡機を使えば、ほぼ確実に全く気泡のないシリコーンにすることができます。しかし真空脱泡機が本当に活躍するのはシリコーンの脱泡よりも、最終プロセスのレジンの硬化の時です。そこは後ほどレジンの注型を紹介する時により詳しくお話ししたいと思います。
【写真上:シリコーンが固まって、囲いを取り外したところ】
いよいよ画期的なシリコーン分割法
原型の埋まったシリコーンが固まったら、シリコーンを分割して原型を取り出します。
今回お話しする方法は、先に原型全体をシリコーンで埋めて、後から分割するという方法ですが、この「後からシリコーンを分割して原型を取り出す」という方法自体が、実は非常に画期的な方法です。
これは私が考え出したわけではなく、先人の中でやられている方がいて、その断片的な情報から「おそらく、こうやっているのではないか」と推測と実験を重ねてたどり着きました。
この「シリコーン分割の段取り」については、この事だけで長い話になるため今回は省略させていただきます。別途この事だけで記事に書きたいです。
ともあれごく簡単に言うと、最もポピュラーな方法を何年か続けていくうちに「もっと他に良い方法があるはず」と思うようになり、さまざまな情報収集と試行錯誤の結果、現在の分割方法になりました。
さてここでは先に進めさせていただきます。
次は固まったシリコーンを分割しながら中の原型を取り出す段階です。
この「分割線」を「パーティングライン」と言うのですが、このパーティングラインを適切に決めないと、型から原型をうまく取り出せない事になってしまうため、非常にアタマの中で計算をしながらの作業になります。
【写真上:中の原型を傷つけないないように慎重に分割していきます】
ここも詳しく書きたいのですが長くなるのでごく完結にご説明すると、透明シリコーンから透かして原型の位置を見ながらイメージしているパーティングラインでカットしていきます。
実際は「2周で切る」感じです。一周めは原型を傷つけないように本体ギリギリで厚みのあるシリコーンを切り、2周めにより慎重に原型との接線を細い刃物で切っていきます。こんな感じで分割をしていきます。
【写真上:適切なパーティングラインで分割すると原型を容易に取り出せます】
シリコーン型に湯口やエアベントを作る。
シリコーンを分割して原型を取り出したら、あとは湯口(レジンを注ぎ込む入口)や、空気をスムーズに逃がせるようエアベント(通気口)などをシリコーンに彫刻刀で彫り込んで型を仮に完成させます。
仮にと言ったのは、実際はレジンを注型して空気の抜け方を見て、その都度空気のルートを太くするとかエアベントを増やすなどの調整をしてより精度の良いものに改良をしていくためです。
【写真上:湯口、エアベントの説明図】
シリコーン型の完成です。
シリコーン型のタイプには今回のように上からレジンを注ぐ「トップゲート方式」と、下部からレジンが上がってくるような「アンダーゲート方式」と2つの方法がありますが、原型1点だけの型なので構造がシンプルなトップゲート方式(+エアベント)にしています。
→この続きは「レジン注型から仕上げ篇」です。鋭意記事制作中です。
●下記URLは私の作品工房「benieda」のギャラリーサイトです。
https://benieda.com/
●日常的な制作のようすは下記 instagramで共有しています。
https://www.instagram.com/benieda/?hl=ja
この記事が気に入ったらサポートをしてみませんか?