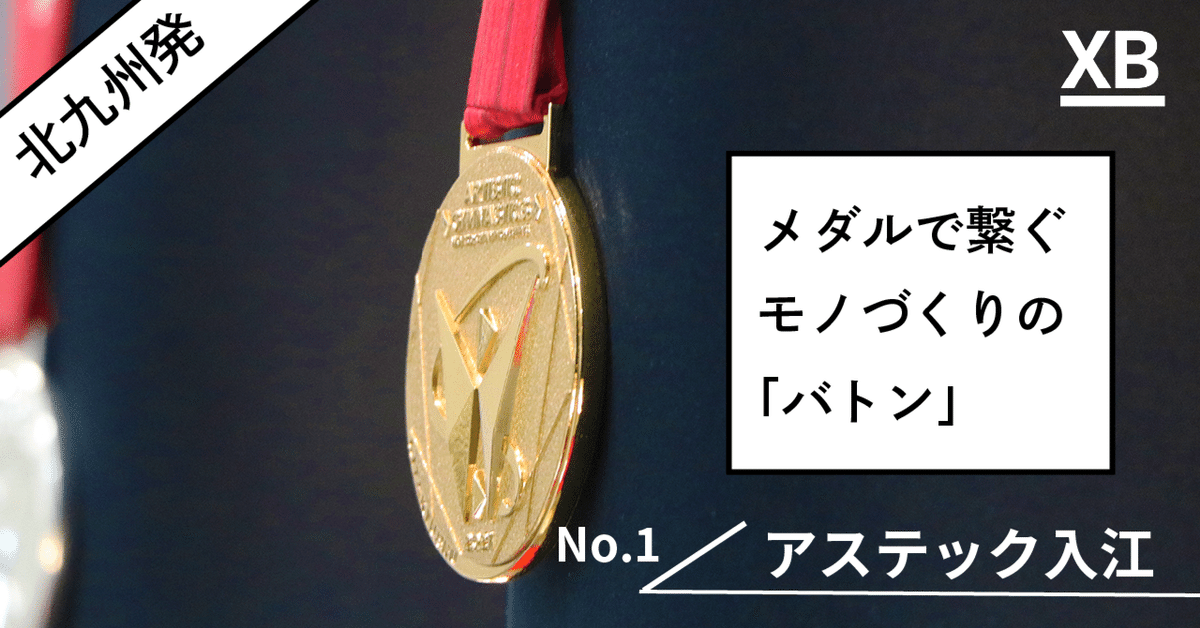
【新連載】「現代の錬金術」によるメダルを生み出すトップランナーが担う使命
~メダルで繋ぐモノづくりの「バトン」~
【第1走者】アステック入江
7月26日に開幕したパリオリンピック。
日本から遠く離れたパリの地で、世界中から集結したアスリートたちが自らの力を最大限に発揮すべく4年に1度の夢舞台で熱戦を繰り広げている。
頂点を目指す熾烈な争いは人々に感動を与え、時に残酷な結果を選手に突きつける。
そんな筋書きのないドラマの頂点に立った者を称える存在が「メダル」だ。
異なる色彩を放つ金・銀・銅のメダルは実際の重さ以上の価値を持ち、厳しいプレッシャーを耐え抜いたアスリートに華を添える。
オリンピックに限らず、あらゆる競技において欠かせないメダル。
実は、「ものづくりの街・北九州」で都市鉱山を素材として活用する「リサイクルメダル」を制作する取り組みが続いてきたことをご存じだろうか。
パソコンや携帯電話、家電製品などの基板から素材を回収した後、切削、研磨、めっき加工といった各企業がそれぞれの技術を駆使してメダルを作り上げる過程は、リレー競技でバトンを渡すかのように映る。
そこで、今回から4回にわたってリサイクルメダルに関わる北九州の各プレーヤーに焦点を当て舞台裏を紐解く。
初回は、電子部品の基板からメダルの素材を回収する工程を担当するアステック入江。
「現代の錬金術」ともいえる技術を確立した背景には、環境問題に対する世の中の関心が高まる前からの取り組みが起点となっている。
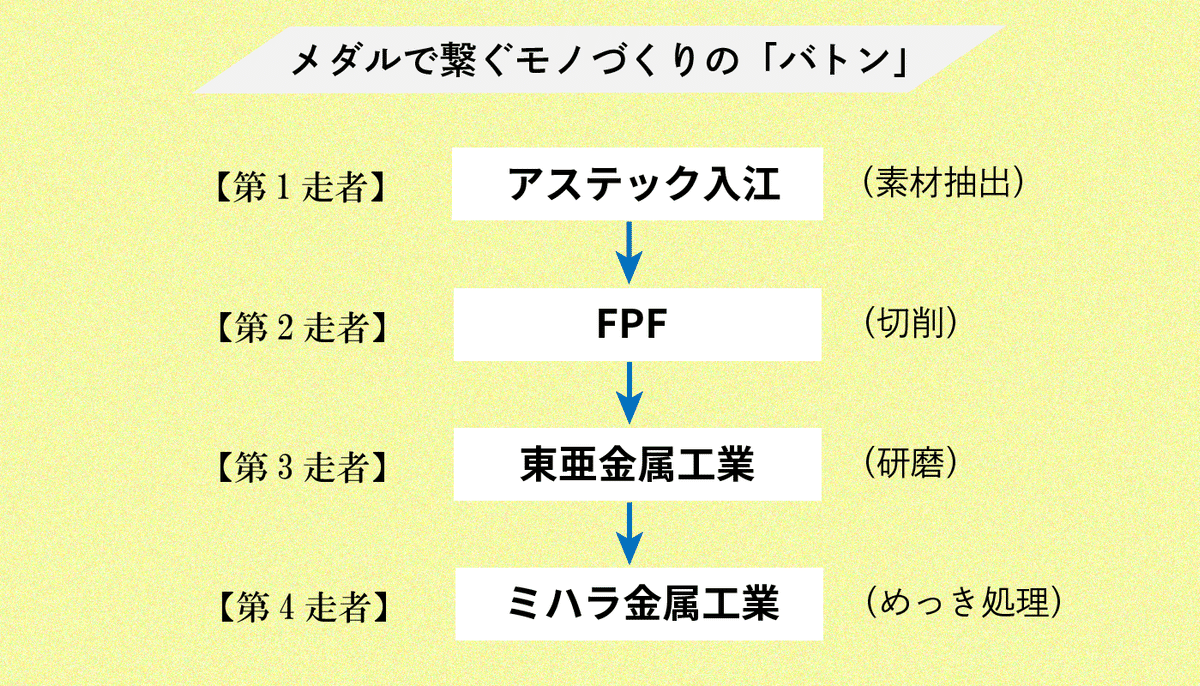
《Part.①》「明日」と「技術」を見据えて進んだ事業展開
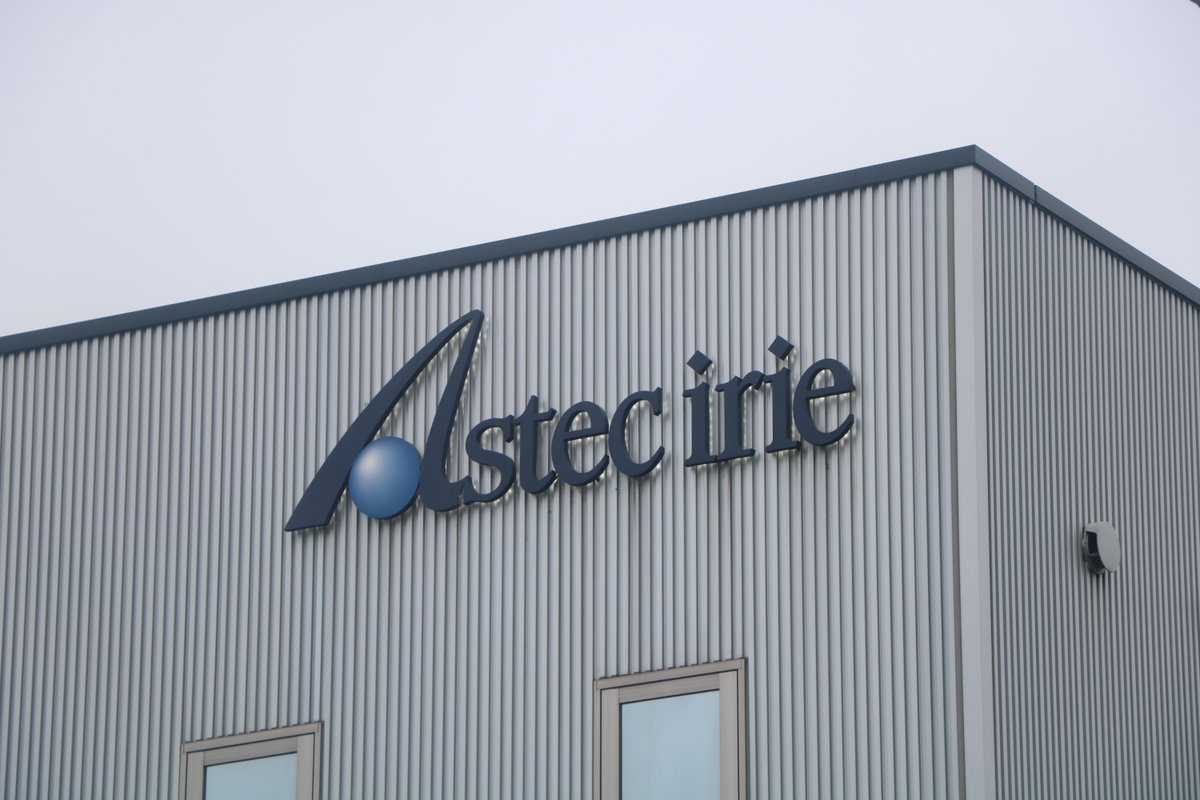
1910年に官営八幡製鉄の請負事業者として創業したアステック入江。
「鉄の街」である北九州とともに発展を続け、溶銑予備処理(溶融状態における鉄の不純物除去)や転炉スラグ処理(銑鉄から炭素やリンなどの不純物除去)など製鋼工程における中核を長らく担っている。
1980年代後半には製鉄業界の不況に伴う「鉄冷え」から脱却を図るため、ファインセラミックス加工の研究・事業化にも乗り出した。
1990年代に入ると、転炉の際に生じる粗粒ダストを原料として鉄粉の製造・販売を開始。
さらにプリント基板やICのリードフレームを加工する際に生じるエッチング廃液のリサイクルで事業化するなど、環境問題に対する世の中の関心の高まりやニーズに応えてきた。
1992年に変更した現在の社名は「明日」「テクノロジー(技術)」の意味が込められ、時代の一歩先を見据えて事業を派生しながら歴史を重ねている。
《Part.②》人々の生活の中に眠る「鉱山」をどう生かすか
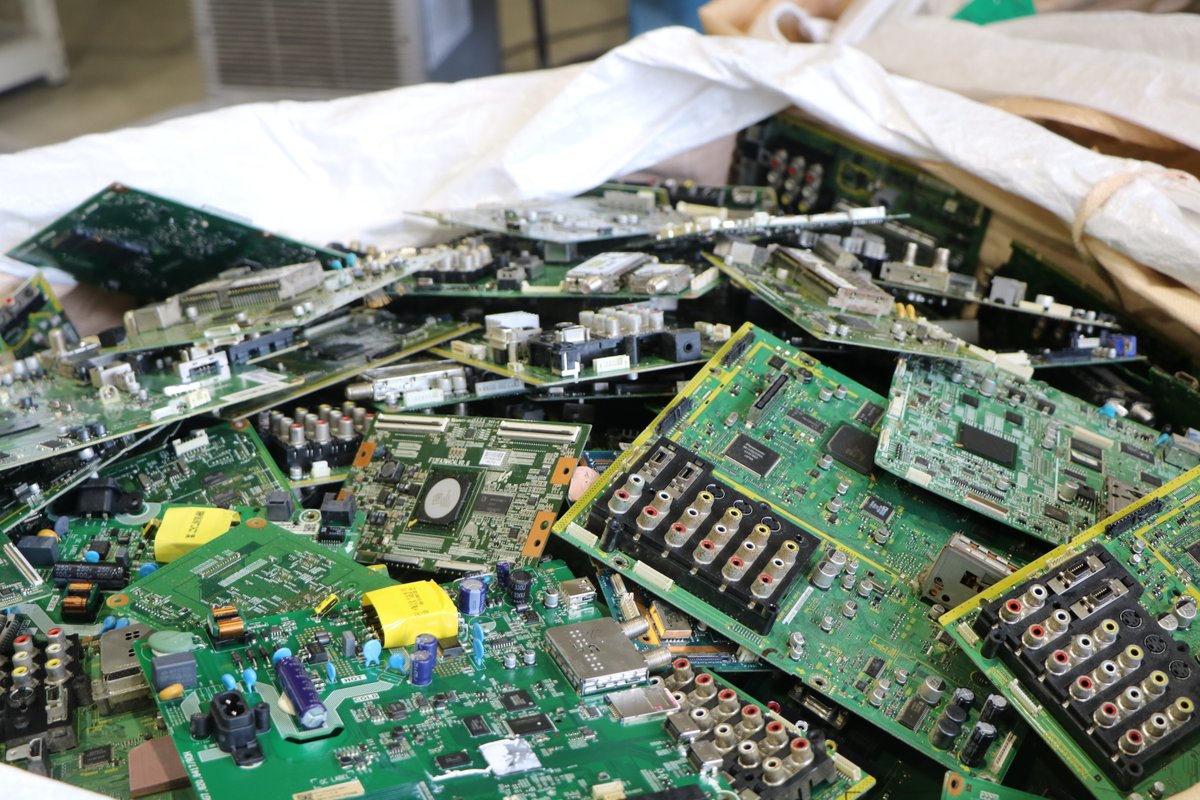
そんなアステック入江とリサイクルメダル制作との関わりは、2014年に立ち上げた都市鉱山リサイクル事業に行き着く。
一般的に使用済みの家電製品やパソコンなどを処理する際、効率的に進めるため破砕によって処理する。
ただ、内部に含まれるプリント基板には金をはじめさまざまな鉱物資源が含まれ、「都市鉱山」として再活用することに世の中の関心が高まっていた。
そんなタイミングでアステック入江は、塩化鉄液にプリント基板を浸けて他の金属を溶かして金だけを溶かさず回収する技術を世界で初めて確立した。
実は、この技術が確立する裏に、事業化に至らなかったある取り組みが前段階としてある。
都市鉱山リサイクル事業の立ち上げ前、樹脂めっきが施された使用済みの自動車部品や蛇口を回収して樹脂と金属に分離する技術の確立を進めていた。
結果的に分離技術は確立したが、当時は樹脂めっき製品のリサイクルに対する需要が乏しく事業化を断念した。
ただ、この時に確立した技術が金を抽出する際に生かされた。
むしろ、アステック入江がリサイクル技術確立に向けて苦労したのはプリント基板を処理する「前」と「後」の過程にある。
「前」の過程となるのが、使用済みのプリント基板の調達だ。
基板にはさまざまな鉱物資源が使われているが、1つずつに含まれている量はごくわずか。
大量の基板を回収する必要が生じるが、安定的な数量の調達先を確保できるようになるまでには数年がかりを要した。
「後」の過程にあるのが、回収した基板の処理方法の確立だ。
破砕による処理が一般的なのは、作業として効率的な点が挙げられる。
アステック入江は基板のはんだを溶かして電子部品を分離する技術も確立したが、当初は全ての部品を手作業で選別していた。
細かな部品を人の手で選別する作業は負荷がかかり、コストも要する。
その後、半導体やコネクタ、コイルなど約8種類の選別するようになり、実証を重ねて画像識別による自動選別システムの導入までこぎつけた。
分別することで破砕した基板と比べて割高に売却でき、事業としての採算性を高めている。
《Part.➂》メダルづくりで直面した「純度」
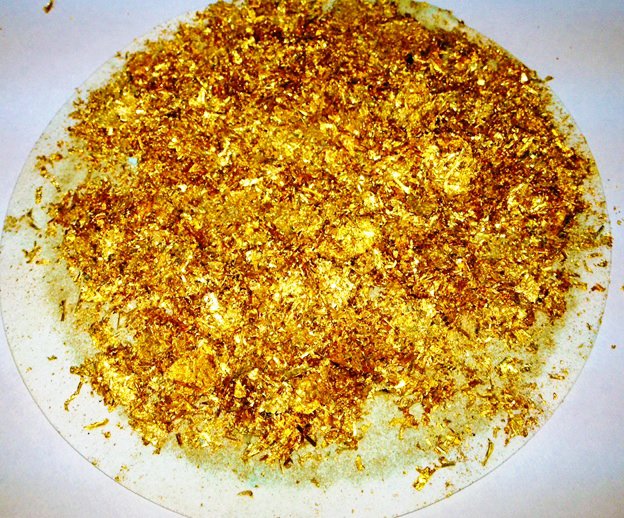
その後、毎年2月に地元・北九州で開催される北九州マラソンの2018年大会では北九州市が中心となり、市内のモノづくり企業が集結して「リサイクルメダル」の制作が始まることになる。
アステック入江は2018年の大会では金の抽出を担当し、2019年以降は各工程を担当する企業をまとめる役割も担うようになった。
市内のモノづくり企業同士が連携を図るにあたり、課題とされたのが素材の「純度」。
抽出した素材に不純物の割合が多いと脆くなり、加工の際に支障が生じるとされてきた。
特にめっき処理に使う素材に不純物が多いと、メダルの母材との密着具合は弱くなる。
2018年の制作では、参加する企業同士が何度も打ち合わせを重ねて何とか完成にこぎつけた。
その後、2021年の東京オリンピック・パラリンピックの際には選手たちに贈呈するメダルに使われるリサイクル金属の素材を供給した。
ユニークな取り組みはさまざまなメディアでも取り上げられ、2021年に地元・北九州で開かれた世界体操を始め、今ではさまざまなスポーツイベントでリサイクル素材を活用したメダルが用いられている。
《Part.➃》メダルの先に見据える未来
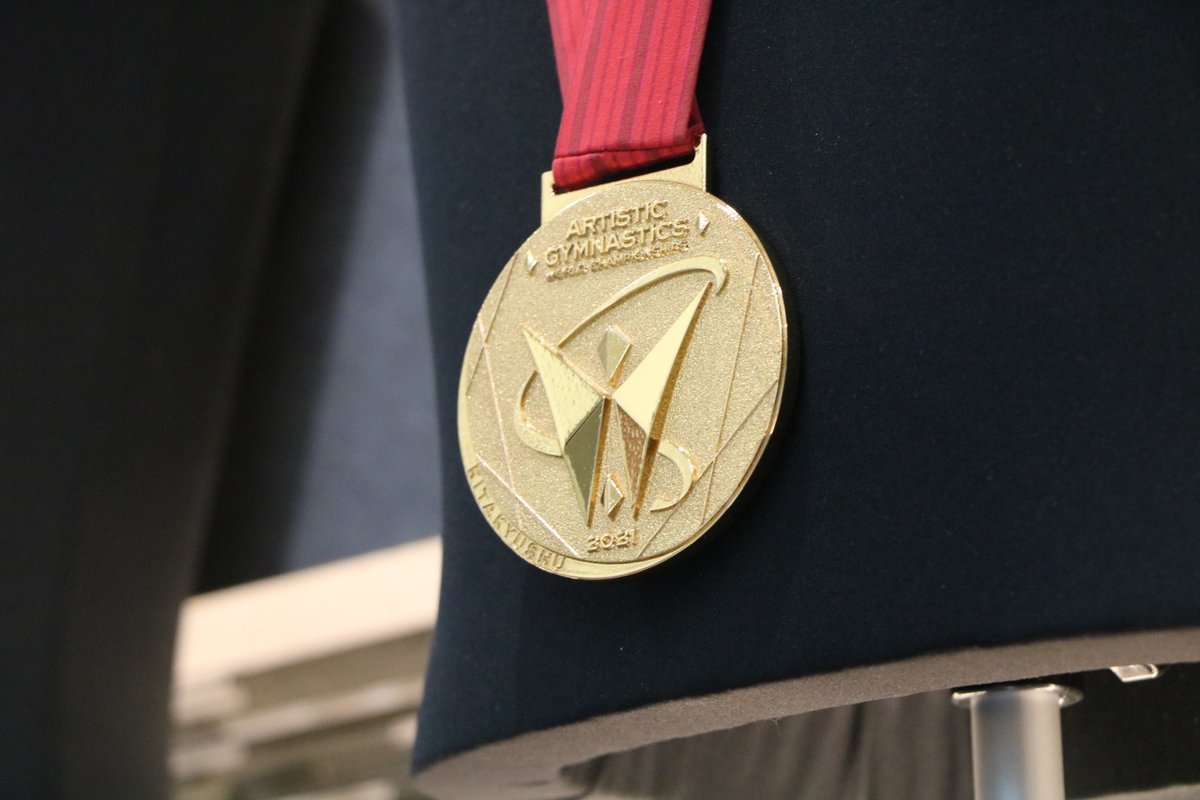
定期的にメダルを作る機会を得て、制作を重ねるごとに各業者との連携やメダルの精度も上がってきた。
ただ、アステック入江にとってリサイクル素材によるメダル制作は1つの切り口でしかない。
世の中に溢れる家電製品の部品や素材を循環的に使うには、自社の事業展開だけでは到底追い付かない。
数年前からは都市鉱山リサイクル向けに確立したシステムの外販にも乗り出し、他社を含めた体制づくりを図ろうとしている。
さらに、JICA(国際協力機構)のニーズ確認調査事業でナイジェリアでの廃基板リサイクルの事業可能性について検証を進めている。
2020年に完成した新工場にある都市鉱山リサイクル用のスペースの一角には、フレコンバックに敷き詰められた基板を目にすることができる。
集められた基板について、工場長の古西政和氏は「10年~20年前の世の中の動きが見えてくる」と口にする。
アステック入江にある廃基板は、長らく家庭で使われてきた家電製品やパソコンなどが基になっている。
製品が生み出され、販売、使用に至る流れは消費者でもイメージしやすい。
ただ、「その後」がどのようになっているかを知る機会はほとんどない。
サステナビリティやサーキュラーエコノミーといった言葉がもてはやされるようになった昨今、アステック入江のように「再び生かす」過程を担う企業の役割がこれからより重要となってくる。
「勝者の称号」としての価値を持つメダル。
自らのものとして手にするまでの血の滲む鍛錬と苦悩の積み重ねは、その価値をより際立たせる。
一方でメダルの作り手たちに焦点を当てると、作り上げる過程でさまざまな苦心の跡が刻まれてきた。
そんな背景を読み解くと、メダルの存在はアスリートと作り手が互いに挑戦し続けた跡が交わる結節点なのかもしれない。
▼次回(8月1日(木)公開予定)の内容はこちら!
この記事が気に入ったらサポートをしてみませんか?