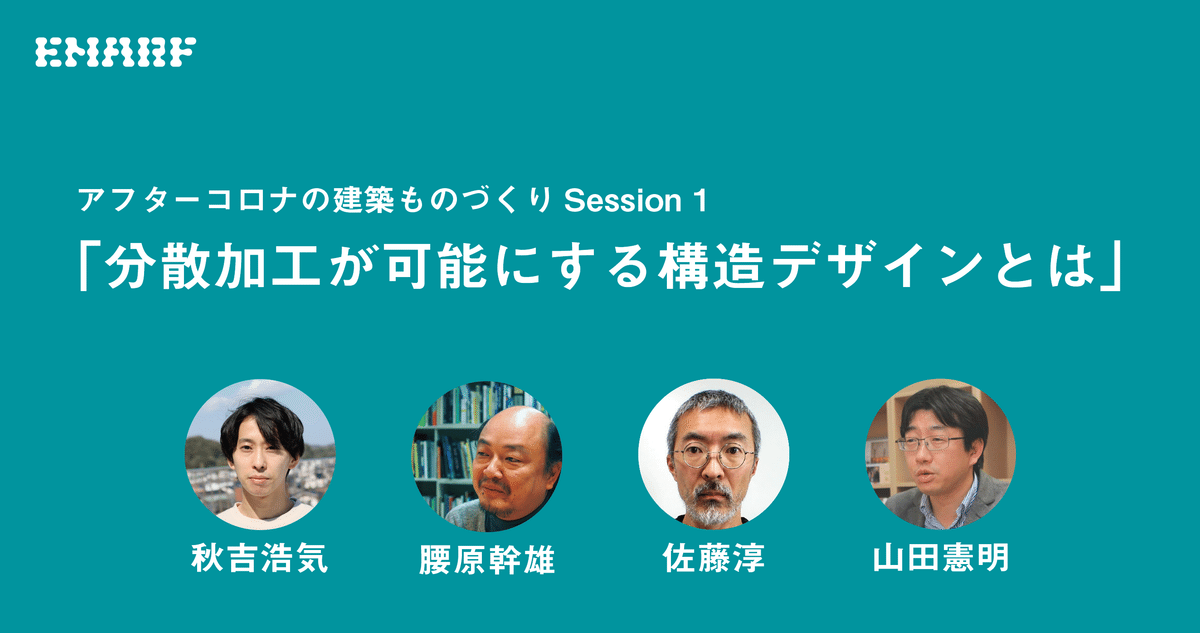
EMARF3.0ローンチ記念イベント「アフターコロナの建築ものづくり」開催レポート Vol. 2
建築テック系スタートアップVUILD(ヴィルド)株式会社では、5月27日に「EMARF 3.0」のローンチを記念し「アフターコロナの建築ものづくり」をテーマにオンラインイベントを開催しました。第一線で活躍する構造家3名と建築家3社をゲストにお招きし、500名を超える方々にも視聴していただきました。
開催レポートVol. 1では、VUILD代表・秋吉浩気より 「オンラインで建築する - EMARF3.0とは」と題し、CADと工房をクラウドでつなぐ、日本初のクラウドプレカットサービス「EMARF 3.0」をご紹介しました。
開催レポートVol. 2となる本記事では、第一線で活躍する構造家3名をお招きし、アフターコロナの時代にあって建築ものづくりはいかに可能か、分散型ものづくりの可能性を模索します。
Session 1 「分散加工が可能にする構造デザインとは」
登壇者:
腰原幹雄(東京大学生産技術研究所教授、NPO法人team Timberize理事長)
佐藤淳(東京大学新領域創成科学研究科准教授、佐藤淳構造設計事務所)
山田憲明(山田憲明構造設計事務所)
秋吉 Session 1を始めますが、簡単に登壇者をご紹介します。腰原幹雄先生は、先々週EMARFを使った制作のご相談をいただき、今日の昼に完成したものがあって、その話をしていただきます。佐藤淳さんは、先ほど紹介したShopBotを使ってものづくりされていますし、われわれVUILDも「SDレビュー2019」で発表したような大型の建築でご一緒しています。山田憲明さんは、日本建築学会の『建築討論』というウェブメディアでお声がけいただき、「デジタル時代のクラフツマンシップとは」 という論考を執筆させていただきました。それ以前は、同じく建築学会の『建築雑誌』の編集委員だった時に「昭和電工(大分県立)武道スポーツセンター」のお話を伺いました(2018年10月号)。私が聞く限りでは、分散加工をしてつくられていて興味をもっています。
最初に皆さんにプレゼンテーションをしていただき、その後、構造家の観点からデジタルファブリケーションや分散加工の可能性について議論していけたらと思っています。
腰原幹雄 「家具と建築の間」
腰原 今日は「家具と建築の間」を考えてみたいと思います。普段は東京大学で教えていますが、 NPO法人「team Timberize」という活動もしていて、2001年から都市型の木造建築を実現するために色々なことを考えてきました。2000年に建築基準法が変わりましたが、具体的な技術整備がされないとなかなか実現しません。
2005年には、5階建ての「金沢エムビル」ができましたが、「なぜ木造なのか」とか「鉄骨造と変わらないじゃないですか」と言われてしまいました。新しい技術を使って建築をつくるには、まずは真似から始めなければいけないという意味では、なかなか評価をしてもらうのは難しいと思いました。その後はなかなかできなくて、2013年に東京で5階建ての「下馬の集合住宅」をつくる機会がありました。この時には、内部空間として鉄骨造やRC造とは違う木造の特殊性を出しています。2015年には、生産性を考えて、ミサワホームさんの住宅で使うパネルシステムを利用して4階建ての「赤羽の集合住宅」ができました。最近はだいぶ様変わりしてきて、2016年には6階建てで、下3層がRC造・上3層が木造、免震システムまで含まれた建築「高知県自治会館」ができましたし、2017年には、下3層が鉄骨造・上4層が木造の「国分寺フレーバーライフ社ビル」ができました。都市型の木造は、普通の木造とは違うところを目指さないといけないのと、もっと汎用性があって普及しないことにはなかなかコストメリットが出てこない。そういうわけで、2019年からは街中によくあるような4階建てのペンシルビルが簡単にできるような生産システムや部材規格を考え、プロトタイプとか仕組みづくりに取り組んでいます。魅力ある建築をつくると共に、生産システムを整備して、汎用性があって、経済性も重視した建築をつくらないといけないと思っています。
他方で、小さな木造建築として、バス停、KIOSK、現場小屋などをつくっています。そこでは通常の木造では使わないような75mm角の材や、36mm厚、28mm厚の合板を使います。秋吉さんにお願いをしたのは、農家の無人販売所のプロジェクトです。2019年からアイデアを温めて設計をしてきたものの、具体的なつくり方はほったらかしにしたままでしたが、ふと思いついたのがEMARFでした。研究室の学生にRhinocerosを使ってもらってモデルをつくり、接合部や穴の開け方など、機械との整合性について細かい打合せをしました。2回だけの打合せで、つい昨日、ShopBotで加工をしてもらい、先ほど完成しました。
これらは、建築としては箱型のパネル構造、壁式構造の延長です。この無人販売所や、75mm角の現場小屋というのは、100mm厚のパネル工法や105mm角の線材による軸組工法の木造住宅の縮小コピーです。他方、先ほど紹介したような大きな建築は拡大コピーです。210mm角の柱や、210m厚のCLTで7-8mのスパンをとばすということで、単に部材の大きさが違うだけです。
ただ、加工のためのパネルの大きさの制限があるので、大きな建築をつくろうとした場合、小さい部品を沢山組み合わせてつくらざるを得ません。材料費やShopBotによる加工費は安いのですが、組み立てる手間(人件費)が増えれば大変なことになります。日本では、費用を削るには、材料費がかかっても大きな部材を集めるのがセオリーですが、EMARFは、DIYによってつくる楽しみや、他の価値を付加できるのかがひとつの課題だと思います。
また、今回思ったのは、やはり構造システムの単なる縮小コピーではなく、そこに工夫が必要だということです。これは、CLTの解体材を組み合わせてつくった「CLT cafe」です。海に面した建築で、この階段状の部分は、内部から見れば壁であり、光を入れる開口部でもあり、外側から見れば観客席として機能します。
これまでは線材で柱梁、面材で床壁を構成するという前提がありましたが、EMARFとShopBotで建築をつくろうとすると、そうした既に名前があるような特定の部位ではなく、新たに命名しなくてはならないような部位を生み出し、それによって空間をつくっていくようなことを考えなくてはいけないと思います。「家具と建築の間」ということで、柱梁を兼ねた部材や、壁のような床、屋根のような壁といったものです。あるいは、単材ではなく小さい部品を組み合わせるトラス構造やシェル構造、組積造のような構造形式が良いと思います。小さい部品を、別々の工場に分散して沢山つくってもらい、それらを集めてつくるような、これまでにない新たな構造形式を目指す必要も感じました。
佐藤淳 「デジタルファブリケーションと新しい構造」
佐藤 私は、秋吉さんと一緒につくったツリーハウスと、今考えているデジタルファブリケーションについて、お話をしたいと思います。
これは、ツリーハウスクリエイターの小林崇さんと、建築家の西田司さんたちと協働したプロジェクトです。厚さ6cmの板材を組んだ、カマキリの卵のような非対称の曲面が特徴です。この、下見板が4枚重なっている状態を木組みでつくることが課題でした。今はまだ最初に手描きのスケッチや、スタイロフォームを削って形状を探っていますが、いずれ、画面上で3Dモデリングしながら考えられるようになる時代も遠くないだろうという気がしています。刻み方を考えて、実際に全パネルを3Dプリントしてみて、データが正しいことを確認しました。全部で388枚の板が必要でしたが、西田さんがこういうものを刻むならShopBotだと言うので、秋吉さんに協力を依頼しました。1台のShopBotでは間に合わないということで、研究室にも導入して刻んでいきました。3軸だったので、まずコの字型の荒削りをして、それを大工さんに渡して台形の蟻型に削ってもらっています。ただ、うちの研究室のメンバーは木工に慣れていなかったので、誤差が出て、大工さんには「愛ある」愚痴を言われましたが。そうしてふたり当番で3カ月間刻み続けてできました。全体が非対称なので、パネル自体や角度、ジョイントの傾きも様々でしたが、それらをすべてパラメトリックに生成しています。
このプロジェクトを通じて感じたのは、デジタル系のものづくりのひとつの方向性として、最後は大工に仕上げてもらう可能性です。もちろんすべてCNCでできるようにする方向性もありえます。一方で、CNCが発達してできることが増えると大工の仕事がなくなるのではなく、大工はより精緻な刻みができる人たちだということがわかったので、普段は発揮できていないそういう技を引き出すような機械と大工の関係があってもいいと思います。
デジタルファブリケーションを駆使したパラメトリックデザインを建築で実現するには、まだまだ手間がかかりますが、少し頑張れば実現できる状況が整って、数年前に比べれば、途方もないものではなくなったと感じています。デジタルファブリケーションを駆使して自由な形状がつくれるようになってくるなかで、今、私が研究をしているのは、「木漏れ日」のような空間です。
細かい部材や半透明の部材を使った構造デザインを追求すると共に、木漏れ日をスペクトルで分析しています。例えば「サニーヒルズ」(設計:隈研吾建築都市設計事務所)では、6cm角の木材を複雑に組み合わせて3階建ての重量を支えています。同時に、内部空間はまさに木漏れ日のような空間になっていますが、スペクトルで分析するとススキ野原や綿雲のナチュラルさをもっていることがわかります。スペクトルの詳しい話は今日は省略します。
形態解析に関して私が試しているのは、複数の荷重条件に対する総合評価で最適化する手法です。多面体や自由曲面、積層型、柱が林立するものなど多彩に適用できます。最近着目しているのが、局所的な形状操作です。例えば、ディンプル(くぼみ)を水玉のようにつけたり、葉脈のように溝をつけたりすることで面の構造が強くなります。ではどんな形状が強いのかと解析すると、花柄が強いことがわかりました。製作はなかなか一筋縄ではいかないのですが、デジタルファブリケーションによって可能になるのではないかと期待しています。
鉄骨ではラチス構造も提案しています。パリの「エッフェル塔」はラチス構造の斜材をさらにラチスにして透明感を生み出していますが、そこからさらにもう一段階ラチスをラチスにした構造ができないかと考えています。
こういう形状最適化は、透明感ある自由形状の構造を実現するのに役立ちます。木組の発展形のプロジェクトが、隈研吾さんと協働しているバンクーバーのパーゴラです。非常に複雑な接合部があり、うまくCNCを操らなくてはいけません。これができるとかなりの自由度をもって全体が設計できます。交差の角度とひねりの角度が自由な相欠きです。
実現したものとしては、高知県の「梼原町立図書館/梼原町複合福祉施設」(設計:隈研吾建築都市設計事務所)で、4本交叉の木組みがまとわりついたものがあります。このような形態の実現が、公共工事の限られた予算と時間のなかでも可能になってきています。耐火の都合で柱梁のフレームは鉄骨造ですが、方杖が木造で、地震時にのみ効くものということで、現しの木組みができました。ピッチをランダムにすることで、森の中のような雰囲気を実現しています。
今、デジタルアプリケーションの現実的な可能性を感じていると共に、複雑な幾何学を操るための研究も同時にしているところです。
山田憲明「分散加工を実現するための構造とディテール」
山田 秋吉さんから「昭和電工(大分県立)武道スポーツセンター」について紹介してほしいという話がありました。この建築は割とスタンダードな設計・施工でしたが、分散加工をしているということで話題提供ができればと思います。
約70m✕100mの無柱空間をもつメイン競技場と約30m✕100mの無柱空間をもつ武道場の二棟があり、メイン競技場の屋根に木造を使っています。幾何学的には3つの円筒面を組み合わせています。妻面では、妻壁から屋根が約9m張り出すため、カーテンウォールの支持構造も含めて鉄骨造としています。
プロポーザルでは鉄骨を主体にした提案で選ばれたのですが、せっかくなら大分県の木材を活かそうという話になって、基本設計の段階でメイン競技場を木造化していきました。大分県には大断面集成材の工場がないので、杉の製材を使うことにしました。丸太の末口は直径30cmくらいのものが多いので、120mm×240mm、長さが4m以下の平角材で大空間をつくっていくということになりました。
梁間方向は最大70m、桁行方向は100mあり、 妻面にはガラスのカーテンウォールがあって、力を流せる支持構造をつくりにくいので、シンプルに梁間方向に架け渡すことにしました。細くて短い材で架け渡すために、力学的に効率の良い形を採用しなければいけません。まず鉛直荷重を支えるために両側の客席にアーチを架け、その形に水平荷重がかかると逆対称形モーメントになり、それに沿って部材を配置すると応力が小さくなるので、上下をひっくり返してトラスにしています。鉛直力を支えるアーチ梁と水平力を支えるトラスを組み合わせたトラスアーチという構造です。
短い材料を大量に使うので、どう加工を単純化するかが切実な課題でした。そこを間違えるといくら安い材を使ったとしても、膨大な工事費になってしまいます。課題を整理すると、①アーチ形状を通直材でどのように構成するか、②箇所数が膨大になるので接合部をどう合理化するかです。通常アーチは、二次曲線やカテナリー曲線を使うとモーメントが小さくなって合理的なのですが、そうすると曲率がすべての場所で変わってきてしまうので、ここでは円弧にすることで曲率を統一しています。アーチのスパンが場所によって異なりますが、ライズ-スパン比を一定にすることで、円弧の中心角が一定になります。さらにすべてのアーチにおいて中心角を等分割すれば、すべてのスパン、箇所で角度が統一されます。
これだけでは、まだ合理化が足りないので、さらに力学的なことも考えて、部材構成と接合部ディテールを検討しました。①下弦材間の圧縮軸力伝達、②アーチ下弦材の座屈の抑制、③ブレース端部のディテールという3つが課題でした。①については、木材同士を小口面で密着させてその支圧で伝えることにしました。その分精度の高い加工と建て方が必要になりますが、ボルトの本数を大幅に減らせます。②については、3つの木材をH型に組むことで2方向座屈させにくくしています。③については、丸鋼ブレースを1本の高力ボルトで取り付け、そのボルトからフラットバーを介して木に伝えるというディテールで、プレートを分けることによって、角度がどう変わっても同じディテールでできるようにしています。
また、施工段階での合理化としては、意匠設計の石本建築事務所さんがRhinocerosでモデルをつくり、構造設計のうちの事務所では、Midas iGenを使ってモデルをつくって相互に共有していました。それを施工者のフジタさんが、BIMソフトのTekla Structuresで統合しています。その統合したモデルから、鉄骨ファブや、西日本の6つの木造ファブに送って分散加工しています。同じディテールなので、検査はすべて回らなくて済みました。また、フレームの上に合板を張るのですが、RhinocerosでBIMモデルを読み込んでシミュレーションをして、合板形状データを出力して切断加工しています。
大量に小さい部材を組み立てるので、いかに早くできるか、下弦材がしっかり密着するかなどを検証するために、接合部のモックアップを何回もつくって改善していきました。その後、全体のスパンの1/5くらいの実物大のモックアップで練習をしています。
分散加工では、大きなトラブルもなくつくることできました。先ほど、腰原先生も言われていましたが、同じ細かいパーツを沢山つくるのに向いていると思います。大分ではまさにそういう考え方で実現しました。
ディスカッション 「設計と製作の間」
秋吉 ありがとうございました。ディスカッションを始めたいと思います。EMARFは、ShopBotでの加工なので合板のサイズという制限がありますが、VUILDの工場には6mくらいの大型5軸加工機を入れました。設計事務所としては、佐藤淳さんと一緒に初めての大きな建築をつくっています。ゆくゆくは、フンデガーなどの大型加工機にも対応していきたいと思っています。山田さんが紹介してくださった分散加工は、そうした将来がイメージしやすく感銘を受けました。腰原さんのお話は家具と建築の間についてでしたが、EMARFが大きな建築にも参入していく可能性や障壁についてアイデアをいただければと思っています。
山田 今後、大型建築にも加工で対応していくということですが、構造解析のプロセスも重要になってくると思います。今のEMARFのシステムだと、構造解析とはリンクしていないので、構造家は再確認が必要になってきそうです。そのあたりも合理化できればもっとおもしろくなるだろうと思いました。
秋吉 構造の解析と、接合部の形状を具体的にモデリングしていく工程は別だという気がしています。接合部の形状をモデリングし終えたら、EMARFに入れることで自動的にそれをパーツに解体するというアルゴリズムを組んでいます。現時点では家具スケールなので各々の判断に委ねていますが、建築はきちんと構造家の方と接合部をつくってから加工に入るはずです。
佐藤 木材を加工して組むことを考える時、立体の解析データをつくります。実際に構造計算をする際には、例えば単純化して線材モデルにしたりします。ただ、木組で組んだ接合部の性能を知りたい時、どういう解析モデルで考えればいいかという研究をしている人はいるのではないでしょうか。腰原さんご存知ないでしょうか。
腰原 FEM(有限要素法)で解けないことはないと思いますが、実際に使う木材の繊維方向や節をどうチェックするかが問題だと思います。そういう意味では、一番許容しやすかったのが、105mm角とか120mm角で、多少の欠点があっても絶対的な性能は問題ないですし、それより大きな材であればよりいいはずです。佐藤さんのように、細い材かつ断面欠損が大きくなってくると、木材よりもっと均質な材料の方が、解析もしやすくなって良さそうです。仕組みとしては、樹脂のような均一なものであれば、接合部も単にソリッドとして解くことができます。木材でやるかやらないかによってだいぶ違う気がします。
佐藤 山田さんの大分県の競技場では、円弧に単純化して、柄材の角度を一定したという話でしたが、今の時点で、公共工事においてどれくらい単純化が必要かということをよく表していると思いました。本当は力学的にはもう少しこうしたかったというところはあるのでしょうか。
山田 円弧にすると若干曲げが出るのですが、その上にトラスがつくので十分に効率性を失わない範囲かなということで採用しました。一番クリティカルなのがアーチの下弦材で、接点間の長さを揃えたかったので、円弧にして等分割したのは結果的には良かったと思っています。
佐藤 デジタルデータから迅速に加工できるようになれば、バリエーションが増えても大丈夫なので、新しい構造デザインにつながっていきそうです。
腰原 結局、デジタルデータは異なる形であっても単に数字でしかないわけです。設計者のルールやジオメトリを施工者が確認するために、施工図があって、部品図をつくり直すという慣習がありますが、デジタルデータのやり取りであれば、結んでいる点や接合部の情報をフィードバックさえすればいい。今までは頭で理解するためとか、人にわかりやすく伝えるためにジオメトリを整理していましたが、デジタルではその必要がなくなり、部材の番号さえ管理できれば良くなるはずです。古い人間の僕らは、数字だけでは間違っても気がつかない怖さがありますが、そのあたりを変えられるかがポイントだと思います。
山田 佐藤さんが考えた接合部は複雑ですが、それぞれの角度や形は誰かが図を描いているのでしょうか、それとも自動的に生成するルールがあるのでしょうか。
佐藤 昔、うちのインターンが、角度を与えれば刻み方が自動生成されるというアルゴリズムをつくってくれました。ツリーハウスでも変わっていく角度をパラメトリックに生成しています。
ただ、ShopBotで加工してから、大工さんに単に溝の底の幅を広げてほしいという話をしたのですが、そうはいかない、それでも隅出しはするから寸法おさえは必要なのだと(笑)。自動生成したパーツから寸法値を提示するのは逆に手間がかかるので、それすら自動化できるようにプログラムを組んでおけば良かったなと思いました。接合部の形状は基本的にはこちらで生成しますが、割と半自動的に素早くできます。
山田 ありがとうございます。腰原先生もおっしゃられていたように、部材の番号さえ管理できればなんでもつくれるというのはまさしくその通りだと思いました。その時に、佐藤さんのアルゴリズムのように、複雑なデータの生成をある程度楽にできるともっとやりやすくなると思います。
ディスカッション 「人間の経験と知恵をどう使うか」
腰原 設計者がデータをつくるとなると、施工者や加工者の知恵をどこでフィードバックするのでしょうか。もちろん設計者が「これが一番合理的だから、この通りやればいい」という世界もありますが、やはり材料や道具や加工機、また、それを扱う人によっても得手不得手があるわけです。設計者からの情報だけで製品になるのではない方がおもしろい気がします。途中でイレギュラーな要素を落とし込めないというのは、デジタルやBIMなど、一気通貫ものの弱点ではないでしょうか。
秋吉 腰原さんからはスケールの軸が提示されましたが、一方で時間の軸もあると思います。デジタルファブリケーションだと試作が簡単にできます。われわれが設計した「まれびとの家」をつくる時には、自分たちが考えた納まりのモデルを村の製作所に置いておくことで、いろんな大工さんが意見をしてくれておもしろかったです。デジタルファブリケーションは、設計者と施工者がコミュニケーションするための媒体にもなると思います。
山田 熟練技能とデジタルとの融合点は色々あると思います。「まれびとの家」は1,000箇所の仕口があるそうですが、その雛形をつくる時に熟練大工に入ってもらって、遊びや隙間を検証して、そのうえで同じ形状を沢山つくられていますね。また、建て方の順序を現場に入ってから変えたというのもユニークだと思いました。
腰原 今までは二次元の図面しかなかったので、想像力によって立体的に考えられる人とそうではない人がいましたが、EMARFのシステムは建築の専門ではない人でも立体で見ることができるという魅力があります。ただ僕らは、実際に手で模型をぐるぐる回して納まりを考えたり、構造的には少しひねってみて感覚的にわかるということも必要です。やはり3次元データだけを見せられてもつまらないとすると、試作でそういうことができれば、大工さんとも技術を活かすためのコミュニケーションができそうです。共通言語のツールになっていくのはもうひとつのメリットですね。
佐藤 このツリーハウスのパネルをつくっていた時に、大工さんから、ShopBotで刻むときに木目の向きや節、ちょっとした割れ目など、板の状態を見て考えてやったのか、という愛情こもった愚痴を言われました(笑)。経験や勘という曖昧なものではなく、そういう知識をアルゴリズムとして認識してプログラミングできるようになると、デジタル機械に盛り込んでいけそうな気もします。
秋吉 まさにそのあたりは腰原さんにもよく言われていたことでした。次の「EMARF 4.0」でやろうとしているのは、今開発中の木目をスキャンするアタッチメントを実装しようとしています。要は、機械に目玉を付けるようなものです。含水率や繊維傾斜角なども拾ったうえで加工ができるようにしたいと思っています。
腰原 今、ラミナの集成材の選別はデジタルカメラとレーザーを使って、節がなるべく取られない長さを切ろうとか、ハイテクになっています。ただそれは、木質等級区分のなかで、明らかにダメなものをはじいているだけです。今、秋吉さんが話していたように、木目や繊維傾斜角が見えてくれば、割裂や目切れが避けられると思います。大工さんの経験値をデジタル的にも評価できるようになるというのは、大事なことだし可能だと思います。
木材がモデル化できれば、縮み方まで含めた推定もできるはずなので、大工さんの勘との勝負ですね。そうした理論的なところがうまく解決できるようになると、もっと楽しくなりそうです。
秋吉 今後は実験が重要になってくるのでしょうかという質問が来ています。
佐藤 先ほど紹介した隈研吾さんと設計した「サニーヒルズ」は、実は木組みプロジェクトの第3弾です。第1弾の時には、直交グリッドの立体をやったのですが、当時は私の研究室がなかったので、腰原さんに相談をして実験をしました。その実験と、線材でつくった試験体の解析モデルの対応性を確認して、建物全体のモデルをつくりました。こうしたことを1回やっておけば、他のプロジェクトで少々刻みが複雑化しても、残っている断面と解析モデルの関係が把握できているので、予想ができます。実験をやった方がわかりやすいという時はありますが、毎回実験が必要というわけではないと思います。
腰原 VUILDも、モックアップをつくるなら、実験装置も導入してしまえばいいのに。佐藤さんの実験の時は、研究目的のネタであれば設備が使えたので、試験体を提供してもらうことが条件でした。民間の設計者はアイデアをもってきて、研究者はみんなの役に立つようにする、といったウィンウィンの関係にあれば良いと思います。すごい実験をしましょうというよりも、それぞれの構造設計者によって大事なところが違っていて、「ここだけわからない」というのがあるので、小さい実験で目的が明確であれば気楽だと思います。
ディスカッション 「新しい道具と働き方やものづくりの変化」
秋吉 加工へのアクセスがしやすくなり、構造設計者の考える理想の接合部みたいなものが実現できるようになった時に、やってみたい構造デザインはありますか。
あと、今日の全体テーマの「アフターコロナ」について、個人的にはこれからは小さな建築や、工数が多くて時間がかかるけどそれでもいいというものづくりが増えてくるような気がしています。最後に皆さんから、加工によって構造デザインがどう変わるか、またアフターコロナの展望について伺えればと思います。
佐藤 今、CNCは主にドリル形式なのでそれに合わせた刻みを考えるとか、道具から工夫していますが、ノミのような動きをする研究もされていて、それができれば、刻める形も変わってきます。プログラムだけではなく、道具の発展性もまだまだ考えられます。つくりたい形のために道具を開発したり、もしくは逆に変な道具ができた時にそれをどう使うかを考えるという発想でも良いと思います。
腰原 これまでは自分の頭で想像しやすくするために整理する作業が大半でしたが、新しい道具とデジタル化によって、わからないままつくることができるようになります。色々な人たちが関わる時には、それぞれの人間が理解できるルールを決めていましたが、状況が変わってくれば、その仕組み自体も変わると思います。
手間さえかけられれば、ひとつひとつ部材の形が違っても問題はありません。アフターコロナについて言えば、暇があれば、つくることが労働ではなくて趣味になって、人件費がかからないどころか、お金を払ってでもやりたいという人が出てくるかもしれません。土壁を塗るワークショップはそうなっています。生産の仕組みとして、大きいものを合理的に経済性優先でつくることはこれまでと変わらないかもしれませんが、それとは違う種類の建築が生まれてくるには、遊び心をもっていろんなことにチャレンジしたり、新しい道具を使って楽しくやろうよという雰囲気にできるかどうかですね。
山田 加工とは部材同士の接合をつくるものだと思いますが、建物や構造の形があって、それから接合部を考える傾向が僕にはあります。部材が混みそうだからこの構造は捨てようなどと考えてしまうのですが、逆に、接合部から構造やありえる建物を考えるような発想はおもしろいと思います。接合部ばかり考えているマニアックな人がいて、そういうところから新しい構造デザインにつながってくといいなと思いました。
佐藤 アフターコロナのイメージとしては、遠隔操作が進むのではないかと思っています。今、私の研究室でも事務所でも、メンバーはできるだけ外出せずに、私だけが伝令のように動くというスタイルを取っています。大学で3Dプリントするのでも、みんながつくったデータを受け取って私がプリント作業員になっています。遠隔操作の現場や製作をどのようにやるか工夫が進むと思います。
秋吉 EMARFは、遠方からでもデータを入稿すれば機械が動いて部品が届くというサービスです。実はShopBotは基盤を変えると遠隔操作できるのですが、そのあたりは「EMARF 4.0」で実装が間に合うかどうかという感じです。
佐藤 操作中の様子が高解像度で見られるようになると、やりやすくなるだろうなと思います。ウェブカメラの解像度は、今まだ配筋検査がちょっとできないくらいなのです。これが改善されると遠隔操作でやってみようという機運が高まると思います。
山田 EMARFでは、加工前に厳密な寸法が出せますが、加工後はどうでしょうか。それが検査の合理化にもつながっていくと思います。
腰原 3Dスキャンをすれば元の図面との誤差は出せますが、小さい部品だとなかなか高精度のスキャナーがないですね。
秋吉 デジタルファブリケーション系の論文では、竣工したものを3Dスキャンして評価するというようなものはあります。EMARFでは、そのあたりは正直あまり考えていなかったので今後の課題ですね。
まだまだお話していたいのですが、時間いっぱいになってしまいました。佐藤淳さんとは曲面パネルの建築をつくっていますし、実験が必要になるかもしれません。腰原さんも山田さんにも引き続きアドバイスをいただければと思います。ありがとうございました。
[2020年5月27日YouTube Liveにて開催]
text by millegraph[株式会社ミルグラフ]
▼開催レポートVol. 3はこちら
----------------------------------------------
facebook: https://www.facebook.com/VUILD.co.jp
instagram: @vuild_official & @vuild_architects
twitter: @VUILDinc