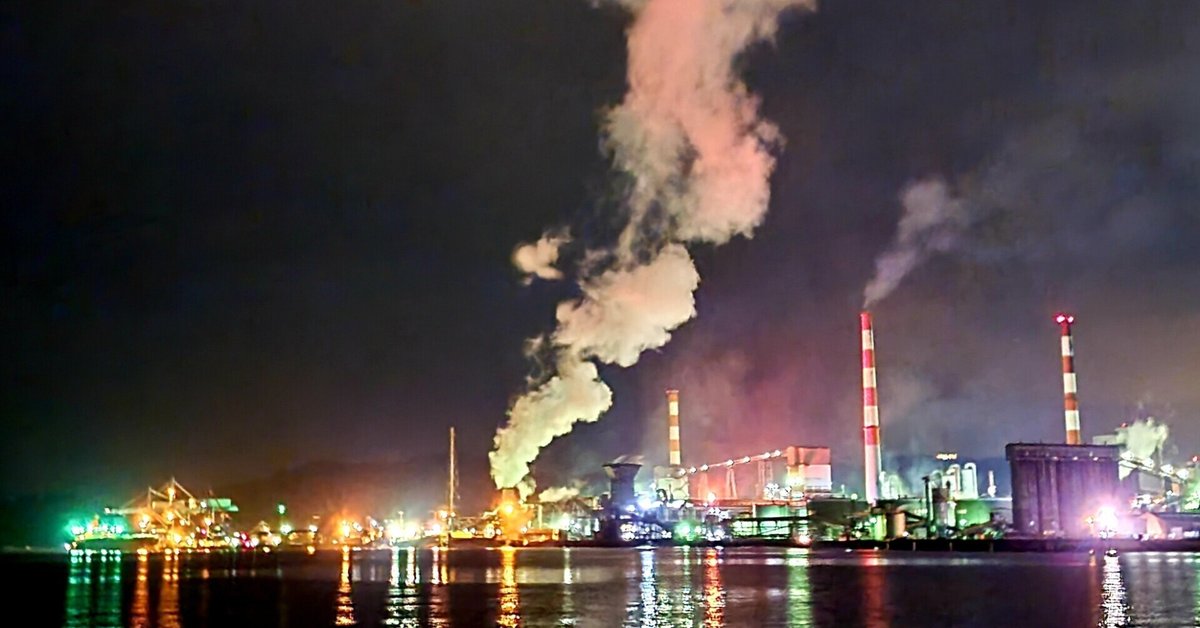
企業から見た"脱グローバル"と"内製化"の必要性
平成は日本の企業にとってアウトソーシング(外注化)とオフショアリング(海外化)の時代であったが、とうとうその限界が見えてきたように感じる。
「内製より外注した方が安い」という幻想
製造業の世界では「内製より外注した方がコストが安い」という言葉をよく耳にする。読者の方にもそういった方は多いだろう。しかし本当にそのほうが安いのか。改めて考えるべきであると私は思う。
多くの企業は加工費(主に現業の人件費)だけを持ち出して外注化の方がコストが低いと推進してきたが、実際はどうか。発注や受け入れの業務に加えて進捗管理や伝票の発行など、直接費用低減のためにむしろ間接費用(主にホワイトカラー業務)が増加していることを見逃している。
「外注に出した方が安い」というのは、その多くの場合は単に物を作る作業者の賃金を比べたものにすぎない。しかしそれは現業部門にかかるコストだけが見える化されていることにより「安い」というように見えてしまうだけなのではないだろうか。
製造部門偏重の"生産性の見える化"
私自身工場での研修を受けた際にも感じたことだが、現在の工場における生産にかかる作業というものの多くは見える化され、単位時間当たりの生産量を定量的に測れるようになっている。しかし間接要員(コストセンター)の業務というのは単純な作業ではないのでそのように定量化されていない。この非対称性が直接費用へ偏った見方となり、安易な外注化につながってきたのではないだろうか。
このような偏った見方のまま外注を増やしたり、海外生産をしたりすれば自らの組織内にノウハウが積み重ならないばかりか、間接部門の必要人員ばかりがどんどん増えてしまう。
海外で生産すれば安く作れる?
中でも感じるのは、海外生産に踏み切る際の間接コスト増だ。輸出入の手続きの業務を行う部門が必要になるのはもちろん、度量衡など規格の違いはもちろん法務や言語、文化の違いなどとても多くの壁が待ち受けていて手間がかかる。みなさんは「3ガロン」と聞いてサイズ感がイメージできるだろうか。これは世界一の国家、アメリカで標準的に使用されている体積の単位である。よくアメリカの大統領は「非関税障壁が~」と日本を批判するが、アメリカこそヤード・ポンド法などという●みたいな計量単位を採用しやがって、というのはものづくりをする人は一度は思ったことがあるのではないかと思う。
そして当然ながら、標準的な規格の違う国で生産する場合は部品の規格から全て作り直しである。海外展開するときに製造法を合わせるのがいかに大変か想像できるだろうと思う。
日本は世界で最も工場への規制がゆるい国
他にも工場を建てる際における諸規制について。実は日本というのは世界的にみると少し異質な存在である。工場を作る際の規制が実質的にかなりユルいのだ。
最近は国家戦略特区のような規制緩和地区を作る話が多くあるが、日本の場合その源流のような存在として各地方にある工業団地があげられる。あれは主に都道府県が優先的に水道を整備(個人が利用する水道は市町村が整備)し、騒音や電磁波、振動といった各種規制が緩和される実質的な経済特区となっている。
これが諸外国ではそうはいかない。日本と比較すると厳しいことが多いのだ。特に電磁波。日本だと、大電流を制御するなどで干渉する電磁波が設備内から出てても工場内であれば意外となんとかなるが、外国ではそうはいかず、日本用に設計した生産ラインを日本と同じように稼働させていくことは難しい。するとそういった場所では従来の日本での設備や仕組みの見直しや再設計が必要になったりして経費がかさむ。
他にも日本より停電が頻繁に起きる国なんていくらでもあるし、港湾、道路インフラの未発達により調達コストが日本より多くかかることは往々にしてあることだ。
このように、日本ほど製造業ファーストで法規制が為されてきた国はどこにもないということを私自身、つくづく実感している。
貿易は、コストである
さらにリードタイム(発注から納品までの時間)の問題もある。
「トヨタが嫌う7つのムダ」という言葉を聞いたことのある人もいるのではないだろうか。トヨタ自動車が工場内の改善の着目点として挙げる7つのムダ要素だ。その中の一つとして「運搬のムダ」が挙げられる。
貿易というのは国際間のモノの移動であり、そうなれば当然リードタイムは伸びてしまう。モノの移動距離というのは、本質的に短ければ短いほど短納期、低コストを実現できる。これは自明であり、必要以上の海外調達は大きなコスト増の犠牲を伴うことになる。故に多国間取引というのは最低限に抑える方が良いだろうと私は考えている。
不確実性の時代に国際水平分業は"巨大なリスク"
今はコロナ禍であり、さらに政情も安定的とはとても言えない。人の移動が難しいことに加え、そもそもどこかの国が法改正を行って部品や材料の供給体制が狂ってしまってはもとこもない。このような自体はつい1年前には誰にも予想できなかったことであり、そして同時に今後のことは今まで以上に予想がつかない。中野剛志 経済産業省参事官によれば、このような「不確実性の時代」において企業に求められることはエンジニアリングチェーンの再編であるという。
企業は利益最大化の原理をもとに行動指針が定められるが、先が見えない不確実性の時代では、利益最大化の計算など不可能だ。
本国は企画と設計だけをして、外国の子会社に部材や組み立てを発注して、という国際水平分業による生産方式は平和な時代においては合理性があるやり方ではあるが、今のように生産して納品するまでに社会情勢が変わってしまうような状況では、設計と生産が密に連携し機動的に方向転換を可能とする「アジャイル型生産」こそが合理的であるという。アジャイル型、ウォーターフォール型という言葉はソフトウェアの世界でよく聞く言葉であるが、それを大規模な製造業においても適用せよというのである。
日本企業は"元々は"伝統的にアジャイル型生産
我が国の誇るトヨタ自動車という会社はどこにあるだろうか。豊田市という名古屋から離れた地方都市に存在する。そこに本社管理部門・設計部門・生産部門が一体となって存在している。もちろん他にも工場はあるが、そこに企画から生産までに関わる人が一体として存在することが大きい。
ものづくりをする際、生産する人の視点、設計する人の視点というのは往々にして違うものであり、その違いを工程間ですり合わせを重ねていくことで改善していく。これが日本企業の伝統的なものづくりのやり方であり強みである。これをスムーズに行うためにはそれぞれが近い場所にいて、綿密なコミュニケーションを取っていることが必須だ。
しかしこの30年で日本では国内需要が見込めないことから海外展開と水平分業化が進み、このような日本の強みが薄れてしまった。
さらには国内でも分業が進み、東京に本社置いて工場は地方、と分かれ、本社勤務の人が「僻地勤務絶対ムリ~」などと抜かしている始末である。このような企業ではこれからの時代に置いていかれてしまうだろう。
技術と人材の内製化出来ぬ企業に待ち受ける空洞化
技術者の流出が問題になってからはや10年以上が経過している。アウトソーシングとオフショアリングにより技術の空洞化が進んだことはもちろん、はたらく人の気持ちも日本企業から離れてしまっている。
エンジニアからの搾取が招いた日本の製造業の凋落
確かに、優秀な人材を外部から引き抜くのは一つの方法として大切だが、それはあくまで一時しのぎの助っ人にすぎない。今こそ数年後のことを見据え内部強化を図る時期であり、来るべきコロナ以後の世界における企業競争に打ち勝つ力を蓄える時期である。短期的利益ではなく、将来どうなるかわからない不確実性、それに耐える力をつけることこそが求められている。
この記事が気に入ったらサポートをしてみませんか?