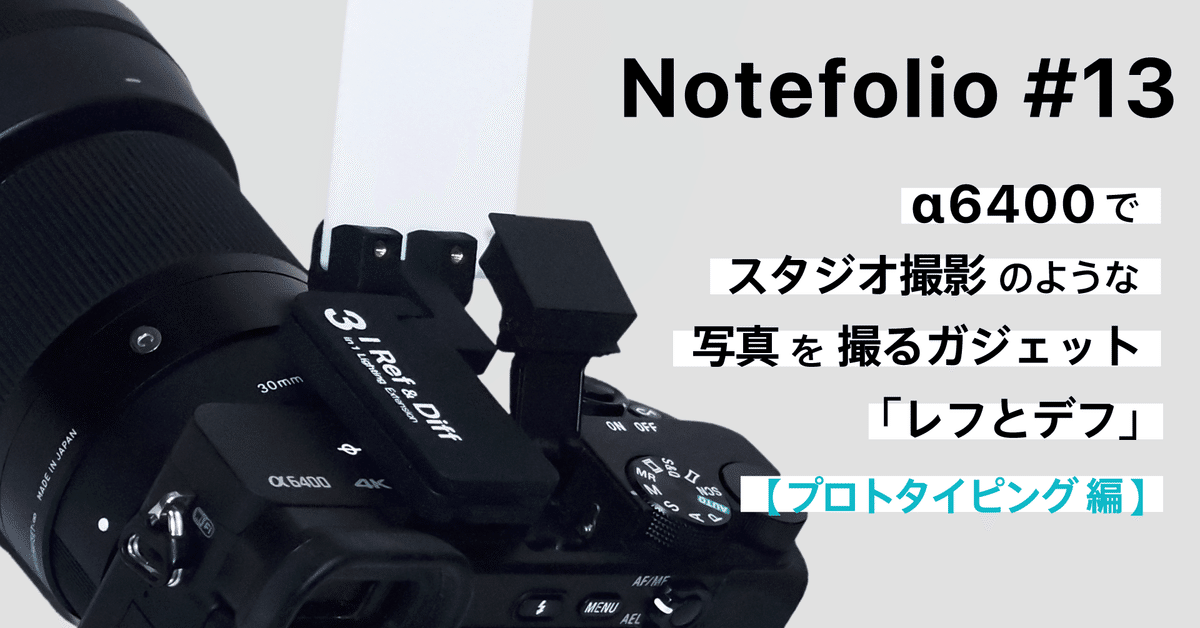
Notefolio #13 | α6400でスタジオ撮影のような写真を撮るガジェット「レフとデフ」【プロトタイピング編】
こんにちは、七海 乃音です。
「レフとデフ」3記事目、今回は「プロトタイピング編」またの名を、めげないしょげない七転び八起き編です。
完成した量産モデル
CAMPFIREの活動報告でお伝えしておりますが、ついに実際にご支援していただいた方にお届けする量産モデルが完成いたしました。
しかし、最初に「α6400に装着するミニディフューザーを作ろう」と考えたときにすぐにこの形にたどり着いたわけではありません。
考えて、手を動かして何かモノを作るとき、最初に思いついた形とは全然違うカタチに行き着く事は珍しくありません。
要件と、構造の変遷
まずは、このミニディフューザー「レフとデフ」の機能要件・設計要件を決めました。
--------------------------------------------------------------------------
■機能要件
内蔵フラッシュから発光される光の一部を上方に反射、残りを拡散させる。
■設計要件
機能要件を満たす拡散板をα6400内蔵フラッシュの前に保持できる構造体。
--------------------------------------------------------------------------
ざっくりといえばざっくりですが、このように置きました。
CADとスケッチアプリを使って設計し、3Dプリンターで各パーツを出力し、アクリルのカットを業者に発注し、ネジやナットも取り寄せて、そして組み立てて試作を重ねていきました。
最初の試作からちゃんと機能した試作に行き着くまで、大きく分けて3つの構造の物を作りました。
細かな修正、改善を含めるとおそらく十数バージョン作ったと思います。
バージョン1(まずは、最初の発想を形にしてみる。)
実は、最初のバージョンはホットシューに取り付けるものではなく、内蔵フラッシュの頭に直接取り付ける構造でした。
当初こういう構造にした理由は、その方が構造としてはシンプルで、ユーザーとしても使いやすく、設計・実装としても難易度が低いと考えたのです。
取り付け方法は、バネを内蔵してしっかり内蔵フラッシュの頭をロックする機構にしています。
折りたたみ可能にして、コンパクトに持ち歩けるというのは最初から考えていました。
しかし、この最初の試作には問題が2点起きました。
--------------------------------------------------------------------------
■問題点①
ミニディフューザーが重すぎて、内蔵フラッシュの頭がもたげる。
■問題点②
内蔵フラッシュが破損するリスクがある。
(実質的に内蔵フラッシュの頭が大きくなった事で、力を受けやすくなった。しかし、その力に耐えられる設計にはなっていない(当たり前)ため、破損する危険性が高くなってしまう。)
--------------------------------------------------------------------------
ミニディフューザーを極限まで軽くすれば、問題点①は解決する可能性はありますが、取り回しよく便利に使えるものにするためには問題点②は別の方法で解決した方がよいと考えました。
そんな状態で使っても精神衛生上よろしくないですしね。。
バージョン1.5(バージョン1の問題点①を解決)
ちなみに問題点①の解決は試みていて、こんな折りたたみ式の脚を作ったバージョンもあります。
この脚は、カメラボディの角を支点にミニディフューザーを支えているのですが、よりミニディフューザーとカメラボディとの動きの自由度をなくしたことで、余計に問題点②の大きさが増したので却下となりました。。
むしろバージョン1の方が、内蔵フラッシュの関節の自由度分だけ、力が逃げるので良かったのです。。うぅ。。
バージョン2(失敗を踏まえ、発想を転換)
そこで、覚悟を決めてホットシューへの取り付けを行い、そこから内蔵フラッシュ前方へレフ板を伸ばす方法を模索し始めました。
α6000シリーズをよく見ると分かるのですが、ホットシューと内蔵フラッシュは横並びになっており、ちょっと面倒なのです。たとえばCanon Kissのようなホットシューと内蔵フラッシュが直線上になっているカメラならばもっと設計しやすいのですが。。
そして試作したのがこちらです。
ホットシューに取り付ける本体からレフ板までに2軸作り、折りたたみからの展開と、レフ板の角度調整を行えるようにしました。さらにこの軸の構造から縦撮影にも対応できそうだったので、各パーツの可動域や干渉を考慮して設計しました。
また、ホットシューへの取り付けるための接続部も本体の中に折りたたんで仕舞えるようにしました。
軸まわりは結構悩みました。
軸にはその位置できちんと保持できなければなりませんし、外れることがあってはだめです。
保持できるにはどういう設計と製造をすればよいかや、固定方法も軸の片側で固定する場合と両方で挟み込んで固定する場合とでは異なります。それぞれ設計、製造、組み立ての難易度、かかるコストのバランスの中で決めていきました。
バージョン3(量産も視野に入れて、再設計)
このあたりから量産と販売を視野に入れはじめました。
最初は自分用に作るだけだったのですが、ずっと自分のプロダクトを持ちたかったことと、設計〜量産・出荷までの一連の工程をやってみたかったので、ちょうどよい機会でした。
あまりにニッチな製品なので、万が一にもバズって大量受注なんて事もないですし。。
バージョン2は、ヒンジの設計の甘さと強度不足でさらなる改良が求められるモデルだったのですが、バージョン3では製造方法変更による設計変更も必要でした。
というのも、これまでの試作では自宅のFDM(熱溶解積層方式)の3Dプリンターでパーツの出力していたのですが、これで最終製品を作るには難易度が高く、まだノウハウが足りないと感じていたため、機械部品に向いているSLS(粉末焼結積層造形)かMJF(マルチジェットフュージョン)で出力するナイロン(ポリアミド)で作る事にしました。
各3Dプリンターの方式・特徴・材料については、こちらが参考になります。
実は、3Dプリンターと一口に言っても、その方式はいろいろとあるため、設計への影響も出てきます。
物を作るというのは、常に「設計」と「製造」はセットですゆえ。
ちなみに、SLSやMJFの3Dプリンターはおいそれと個人で所有できないほど価格も大きさも桁が違うので、DMM.makeなどの3Dプリントサービスへ発注する事になります。
FDM → SLS/MJF への設計変更は、今回の場合はむしろ設計の自由度が上がるため、FDMでは難しかった箇所に角丸を付けられたり、パーツ点数を減らしたりする事ができました。
DMM.makeの各マテリアルのデザインガイドラインはこちらにありますので、3Dプリントにご興味ある方、発注される方は見てみてください。
そして、出来上がったのがこちらです。
左がFDMで試作した自宅製造版で、右がMJFで製造した量産版です。
まずはじめに感じるのが、MJF積層痕ぜんぜんない!!きれい!!!
って事です。
おそらくまだまだ3Dプリンターを扱う事、3Dプリント品を扱う事は一般的ではないため、初めて目にする人は「なんか変な線が入ってる。。」と感じてしまいがちだと思うのですが、僕たちが普段目にしてる大量生産品と比較すると仕方ない部分です。今のところは。
逆に3Dプリントは、ワンオフの異なるモデルを都度出力する事ができるので一長一短です。それぞれ得意な事が違うのです。
あと、表面はマット感があってかっこいいですね。
ロゴは自分でデザインして、UVプリンターで印字しました。
UVプリンターも個人ではおいそれと所有できるものではないため、Fab施設へ借りにいきました。
最後に。
書き始めたら思いの外長くなってしまいました。。
これを最後まで読む人はいったいいるのでしょうか。。暇なの?
(ありがたい仏の心を持った読者に喧嘩売る発言
これでも材料の物性の事とか、FDMとMJFの設計の事とかテクニカルな事はわりとはしょりましたが、いつも勉強中なので自信持って発信できる事がないな?
今回、十数バージョンの試作を経てやっと製品版ができました。それは製造業では普通の事だと思いますが、こんな単純な製品でも一人でやりきるのは、それでもめげないしょげない七転び八起きの精神が必要です。って書くとなんだかマッチョイズムぽくてヤなのですが、それでもものづくりが好きだからでしょうか。もしくはドMなのかな。そうかな。
世の中もっともっとすごい製品を作り上げてる人は無数にいて、底辺ひとりメイカーの僕はよく打ちのめされています。いや、打ちのめされてしかいないな。。でも、それでも作る事を続けていくつもりなので、手を動かして物を作る人の知識、モチベーション、応援になれる事が少しでもあれば嬉しいです。
この記事が参加している募集
この記事が気に入ったらサポートをしてみませんか?