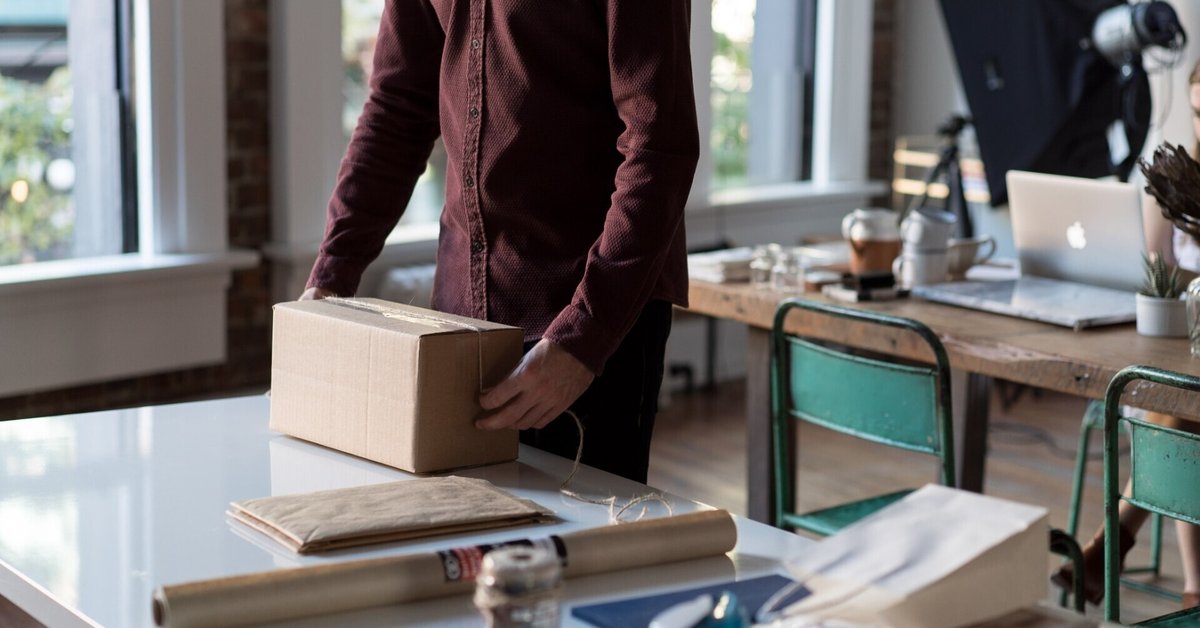
今更聞けないピッキング方式?仕分けにおける【種まき】と【摘み取り】を解説
普段何気なく受け取っている宅急便。amazonなどで頼んだものが綺麗に箱に梱包されていて届けられることも多いかと思います。
物流関係者にとってはピッキングは馴染みあるかと思いますが、なかなか方式自体を質問することは当たり前すぎて聞きづらい、なんて声もよく聞きます。
ここではピッキング方式の主な2種類「摘み取り方式」「種まき方式」をご紹介していきます。
ピッキングとは梱包する作業
まず方式の詳細に入る前に、ピッキングの定義から整理しておきます。ピッキングとは
ピッキング:工場や倉庫などにおいて、指示書や伝票に沿って製品や部品、材料をピックする作業
です。我々が普段頼んでいるAmazonなどの商品もこれらのピッキングを経てお届けされています。
さらにはピッキング方式として2種類、「摘み取り方式」「種まき方式」があります。
商品を取りに行く「摘み取り」方式
摘み取り方式は商品を「摘み取って」各発送先毎に梱包をしていく方法です。
こちらは花に擬えて、各商品(花)が置かれている場所まで歩いて行ってピッキングをする方式になります。
"シングルピッキング"、 "オーダーピッキング"などと呼ばれ、1行ずつ処理を行うことからそう呼ばれています。
すなわち、少量多品種に関しては有利な手法になります。商品が梱包できしだい発送ができるので、カスタマー毎に出荷制約時間などがある際には優先的に進められます。
デメリットとしては商品場所までの移動を伴うので、移動距離、移動時間がかかります。こちらは以前の記事でAmazon物流センターの従業員が1日当たり24キロメートル歩行していると発表したところにもあるように、商品数が増えると作業によってはかなりの移動距離・時間が発生します。
商品を撒きに行く「種まき」方式
種まきは商品を「撒く」方式になります。摘み取りと異なり、発送先へ送る梱包箱が置かれている場所まで商品を持っていく方法です。
"トータルピッキング"などと呼ばれ、まとめて作業を行ってからエリア別に仕分ける時などに使用されます。
種まきのメリットはまとめて商品をとってから撒くので、多頻度の商品については作業効率が上がります。わざわざ商品を取りに行くこともないので、撒き先が少なければ少ないほど効率は上がります。
一方でデメリットとしては撒き終わらないと全体作業が終わらないので特定の発送先のみ早く終わらせるなどの対応が難しくなります。
また、発送先が増えれば増えるほど撒き先が増えるので占有する面積が多くなります。事業拡大においてはかなり厄介な難題ですね。
方式の主な違いは商品固定か発送先固定
この二つの仕分け方法の違いをまとめると下記の図のような形になります。
少量多品種化している現代においては商品単位は摘み取り方法が増えており、さらにそこに対してAMRやAGVといったような自動化技術が現場作業を支えている、ということになります。
よくある事例としては、種まき、摘み取りはカートピッキングなどが挙げられます。
かなり時代を感じますが、この物流倉庫などはカートピッキングで行われていますね。
どちらがいいか、というのが次に気になるところですが、まず前提の考え方として、
アイテム数>出荷先(発送先)の数・・・摘み取り方式
アイテム数<出荷先(発送先)の数・・・種まき方式
と考えられることが多いです。これは例えば、対象のアイテム数が1000個で発送先が10カ所の場合、摘み取り方式が向いています。10個の梱包箱が必要なところにさえ行けばいいので、「行かなくていいところ」が多々発生します。
もしこれが種まき方式を選んだとすると、1000品の中でオーダーがある商品の往復が必要となり、非効率になるケースが想定されます。
一方、アイテム数が10個では発送先が1000箇所の場合、種まき方式で10回の往復で配ってしまった方が効率的と考えられます。
あとは、発送先の制約時間などを含めてどちらが方式として最適かを検討していく形になります。ここについては受注状況と倉庫レイアウトを突き合わせながらケースバイケースで検討していくのが一番でしょう。
方式も含めて動線は最短で
今日は2つの方式を紹介しました。
この方式においてもそうですが、どの作業も「最短で行う」という作業が求められています。特に動線では一筆書きのような経路を作り込むことで最短経路は実現可能になります。
目の前の作業から、「最短とは?」を求めていく習慣があるといいかもしれませんね。
この記事が気に入ったらサポートをしてみませんか?