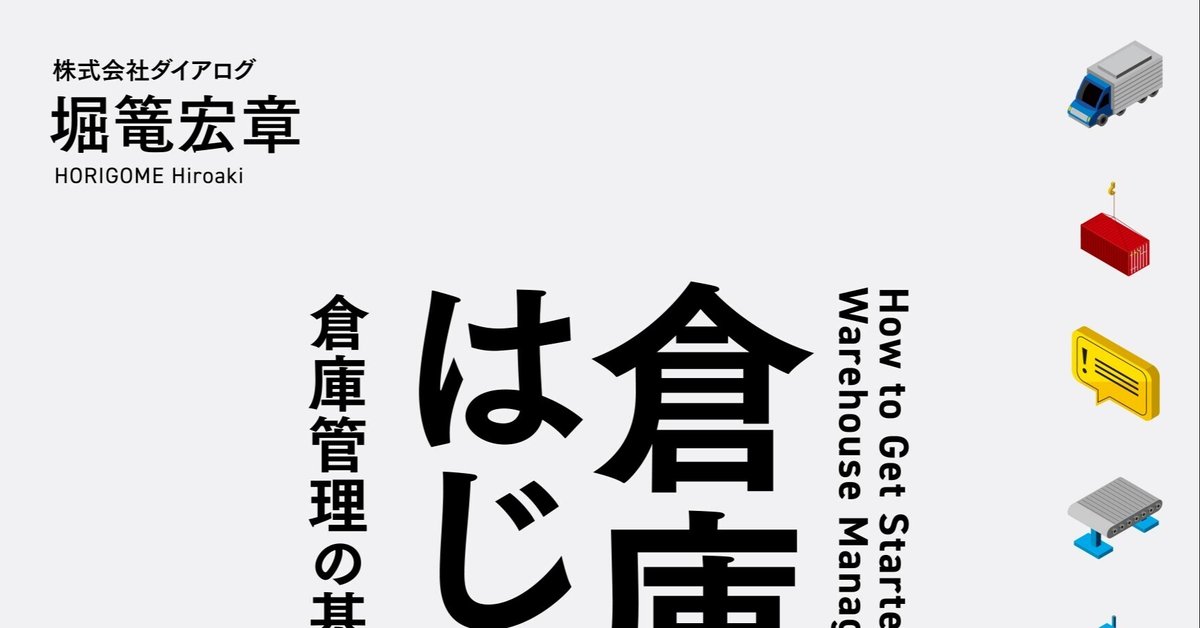
倉庫DXのはじめかた
フォレスト出版編集部の寺崎です。
3月決算の弊社では、毎年3月末に「断裁リスト」というものが営業部からあがってきます。
断裁とは「売れずに倉庫に残った書籍を切断・破棄すること」です。編集者にとって自分が企画した商品が「断裁」されるのは、とても悲しくつらいことです。
しかし、倉庫のスペースには限りがあるため、いつまでも保管しておくわけにはいきません。そこで、多少の在庫を残しながら、余分な冊数を泣く泣く年度末に断裁するというわけです。
ところで、こうした「倉庫「在庫」の世界にもDXの波がやってきているようです。これまで「在庫管理」はビジネス書のテーマとしては古く、昔から地味ながらロングテールな書籍が多いジャンルです。
ところが、最近は営業部からも「在庫管理の本は最近売れない」という話をちらほら聞きます。
なぜか。
おそらく倉庫管理、在庫管理の合理化が進んでいて、昔ながらの在庫管理手法が通用しなくなっているからではないでしょうか。
そんな時代に沿ったボーンデジタル書籍がKindle FDBシリーズから発売となりました。
『倉庫DXのはじめかた』です。
今日は本書から特別に「第2章【商品管理】在庫のすべてをデジタル化する」から一部抜粋してご紹介します。
【商品管理】在庫のすべてをデジタル化する。
■在庫管理の本質は生産性の向上
一般的に在庫管理というと「自分たちが商品をどれだけ持っているか」を把握するもの。把握した情報は、いわゆる企業の貸借対照表(BS:バランスシート)に記載される一つの資産、負債としての情報と考えられています。そう考えると、在庫量を多すぎず少なすぎず、適切な量に管理することが在庫管理の本質だと思われがちです。しかしこれはあくまで経営観点での話。現場で求められる考えではありません。現場において最も大切なのは「作業を最適化するための在庫管理」なのです。つまり「生産性を最大限に向上させるための在庫管理」これこそが物流現場における在庫管理の本質だといえます。
では、生産性を向上させる在庫管理とはどのようなものでしょう? ご家庭の食器棚をイメージしてみてください。使用頻度の高いコップと来客用に使うコーヒーカップがあったとして、食器棚のどんな場所にしまうでしょうか?おそらく前者は手前に置き、後者は手の届きにくい奥の方へしまうでしょう。
このようにものの用途や内容などに合わせて配置場所を考えることが、作業する上で一番大事になります。商品に足が生えて勝手に動いてくれるわけではありませんから、ものを動かすためには、必ず人の手による作業が必要です。人手がかかる以上、人の動きを最適化し、生産性を高めることは必然です。工場の場合は「一時置き場」を設けるケースがあります。荷物が整理されて正しい場所に置ける状態になるまで、仮置きするための置き場所を設けるのです。
特にトヨタ系の企業などでは、入荷した荷物の置き場を詳細にルール化しています。在庫の配置がいかに作業効率を左右するかを知っているからこそ定めたルールであり、まさに在庫管理の本質を追求している例でしょう。
■最適化への第一歩は「適当に放り込まない」
ご家庭でありがちな光景だと思いますが、小さな子供が「あれがない」「これがない」と訴えてくることはないでしょうか? しまう場所が決まっていても適当な場所に放り込んでしまうために、どこにあるか分からなくなってしまう。子供の話であればほほえましく聞いていられますが、これと同じ現象が倉庫でも起きているのです。
生産性を欠いたNG行動としてありがちなのが、ルールを決めずに空いている場所に置いてしまうこと。入荷されたら、その都度倉庫の空いている棚にポンと置く。残念なことに、こうした無計画な在庫配置をしている倉庫はかなりの数で存在します。
ただし倉庫で働くのは子供ではなく大人。ある程度は作業者の頭の中に置いた場所の記憶があります。だから安心、ということではなく、実はこれが非常にリスクの高い運用なのです。
もし荷物の場所を知っている作業者が休暇や退職で不在になったら現場はどうなるでしょう? 荷物の場所を調べるすべもなく混乱に陥るに違いありません。いわゆる属人化された状態になると、現場全体の作業がコントロールできなくなってしまいます。
こうした属人化はリスクであるにも関わらず、常態化しているのが現実。常態化してしまうのは人の心理が影響しています。「自分にしかわからない」という優越感は作業者のプライドになる。自分にしかわからないことが増えれば増えるほど「自分は倉庫を把握している」と満足し、結果的に改善の必要性を感じなくなってしまうのです。
こうしたプライドは幻想であり、意味のないものです。属人化を打破するためには、間違ったプライドを突き崩す根本的な改善が必要になります。
■データ化が可能にする7つの「ない」の追求
それでは倉庫の作業生産性を高めるためにどうしたらよいか。私は7つの「ない」による業務効率の最大化を提唱しています。7つの「ない」とは「持たない」「貯めない」「待たない」「歩かない」「考えない」「探さない」「書かない」を指します。
ここに倉庫で頻繁に起こる作業者の行動をまとめてみました。
・どこに置いたかわからないと「探す」
・誰が置いたかわからないから「考える」
・とりあえず置いて「貯める」
・荷物を取りに行くために遠い距離を「歩く」
・荷物の到着を「待つ」
・情報を手書きでメモする
・置き場所を探して荷物を「持ち」続ける
これらは生産性につながらない、とてももったいない行動です。
特に「歩く」という行為は、効率化を妨げる危険なものです。というのも、たくさん歩いて疲弊すると、あたかも頑張った気分になってしまうのが人間の本能だからです。商品を探しながら歩く。不必要に遠い場所まで商品を取りに行く。ただ歩いているだけでは実際には何の価値もありません。最近は健康ブームということもあり、作業中に万歩計をつけて「私は今日何万歩歩いた」と誇らしげにカウントしている作業者もいますが・・・。効率化という観点では全く意味のない数字です。個人の健康管理やカロリー消費量を計算するためであれば問題ありませんが、これを「仕事の成果」として捉えるのは問題です。先述の「自分は倉庫を把握している」気になってしまう心理と同様、歩いた歩数を頑張りと考えるのは、在庫管理の本質からは外れているといえます。
このように倉庫の生産性を高めるためには、先ほど挙げたもったいない行動をすべて排除し、7つの「ない」を追求しなければなりません。ここで必要になるのがデータ化なのです。
■紙の管理はいい加減でも通用してしまう
7つの「ない」の1つ、「書かない」についても解説しておきましょう。突然ですが、小学生が取り組む夏休みの宿題の定番に「毎日の天気を記録する」というものがあります。実際にはきちんと毎日記録している小学生は少数であり、ほとんどは過去の新聞を引っ張り出して調べて書くか、調べもせずに適当に書いてしまうものです。実はこれと同じことが在庫管理の現場でも起こっています。
たとえば入荷状況を紙に記録する作業を後回しにする。本来は最終的な配置場所を記録すべきところを「一次置き場」と書いたまま放置されるケースなどがよく見られます。紙によって管理する行動がおざなりにされ形骸化してしまうと、何の意味もない作業になっていくのです。
紙による管理は、作業者の記憶に頼る属人化された状態よりは良い状態だといえるでしょうが、問題はあります。前述のとおり記録するタイミングなどが担当者の判断に委ねられるため、標準化しにくいのです。フォーマットが機能しないばかりか、記録しなくても作業が進められてしまうからです。
では「書かない」ためにはどうするべきか。すでにお気づきと思いますが、紙による管理の問題はデータ化が解決します。バーコードやタグを利用し、情報が発生した時に発生した場所で即座に入力していく方法です。データ化には主にバーコードやRFIDといったツールが使われています。記録されるのは、定められたフォーマットに従ったデータ。つまり書き換えや入力内容に制約をつけることで作業をコントロールできる状態が生まれるのです。
在庫管理における「ものの流れ」の中で、データ化はできるだけ早いプロセスで導入することが理想です。倉庫に入荷した時点ですぐに商品がデータ化できると良いでしょう。ちなみにAmazonの場合、発送購入した商品の配達状況をトラッキングすると「営業所を出ました」「最寄りの中継所です」「いま配送中です」という情報がリアルタイムに更新されます。これは発送に関わる企業を横断して、上流から下流に至る全情報のデータ化に成功している例です。ここまで実現したら最高ですが、せめて中継する営業所内の状況だけでもデータ化できると良いでしょう。営業所内の業務効率が上がり「デキる会社」として評価されるはずです。
まずは紙の管理から脱却し、バーコードやタグを活用したデータ管理へ移行する。これこそが在庫管理DXの出発点になります。
データ化の手段としては、JANコードが一般的です。購買力のある企業では独自の管理コードをつくる場合もあります。メーカーや卸会社に対してコードを商品に記載するよう依頼し、万が一記載がない商品は受け入れない、と厳格に定めているケースもあるようです。メーカーや卸会社へ協力を頼めない場合は、自社でシールやタグをつけるといった対応で十分です。
■在庫に触れたら即登録
紙の管理における問題点でも取り上げたように最も大切なのは、触ったらすぐに登録するように義務づけることです。まず商品が物流センターに届いたら、即座にデータと紐付ける。入荷時のデータ登録さえ徹底できれば、後の工程もスムーズに動きはじめます。
同時に、後のあらゆる作業工程で同じルールを義務付けましょう。ピッキング(倉庫から必要な商品を集める)作業の場合は「棚から商品を取り出すごとに登録する」といったイメージです。
あらゆる工程で「商品に触れたらすぐに登録する」ように義務づけると、各ポイントの情報が可視化されます。「商品を入荷した」「棚に入れた」「ピッキングをした」「検品をした」「梱包した」「出荷した」というように、倉庫全体の「ものの流れ」が手に取るようにわかるのです。倉庫全体の状況が把握できると、作業のコントロールも可能になります。
「商品を触ったらすぐに登録する」ルールが浸透すると、倉庫の状態が次の図のように表せるようになります。縦軸は作業している人数で、横軸が時間です。棒グラフは各作業(ピッキング、仕分け、梱包・出荷)を色分けして表示し、折れ線グラフでそれぞれ直接作業と間接作業に従事する人数を表しています。在庫管理における直接作業とは実際にものを動かす作業、間接作業とはそれ以外の全てを指します。
Beforeの図では「午前中にはピッキングの作業が多く、午後になると梱包の作業が多くなる」ことがわかります。また午後4時くらいになると相対的に間接作業に従事する人が増えていますが、これは作業分担が明確ではない人の数です。
こうして倉庫中の作業の様子が可視化されると、整理すべき問題が見えてきます。次の図のケースであれば、午前と午後に増えるピッキングと梱包作業の波を平準化し、さらに夕方に増える間接作業を整理しなければならないということです。これらの問題点を改善したところ(Afterの図参照)、作業波動を平準化でき、更に終業を前倒しできました。
このような倉庫の状況は、「商品を触ったらすぐに登録するルール」とデータ化によって可視化されます。この例では作業を5種類に分類していますが、より細かく分類できるのがベストです。
ーーーーーーーーーーーーーーーーーーーーー
【著者プロフィール】
堀篭 宏章(ほりごめ・ひろあき)
物流xITコンサルタント
株式会社ダイアログ執行役員 LogiX事業部事業部長
長野県出身。慶應義塾大学メディアデザイン研究家卒(メディアデザイン学修士)・最大手宅配会社、トランコム、ミスミ等物流に加え、コンサルティングファーム、SIでの経験も有し、業務とシステムを俯瞰的に見た上で、現実的かつ未来を見据えた全体最適な仕組み(システム)を構築することが得意とする。
特に、ITを深く理解している上で物流のメカニズムも理解しているため、物流の分野において最短距離で効果を最大化したソリューション設計及び実行が強み。現在は上記経験を踏まえ、株式会社ダイアログにおいて、物流xITの最適化を実現する様々なサービス提供を行っているLogiX事業部をリードしている。次世代クラウド型在庫・倉庫管理システム「W3 SIRIUS」「W3 mimosa」を軸に、物流センター内業務/システム改革を多数実施。
在庫管理に携わるすべての方におすすめできる『倉庫DXのはじめかた』は、通常ボーンデジタルだと本文が3万字程度のコンテンツが主流ですが、本書は8万字ほどの手厚いコンテンツとなっています。
ぜひ、スマホやタブレットを片手に読んでみてください。
この記事が気に入ったらサポートをしてみませんか?