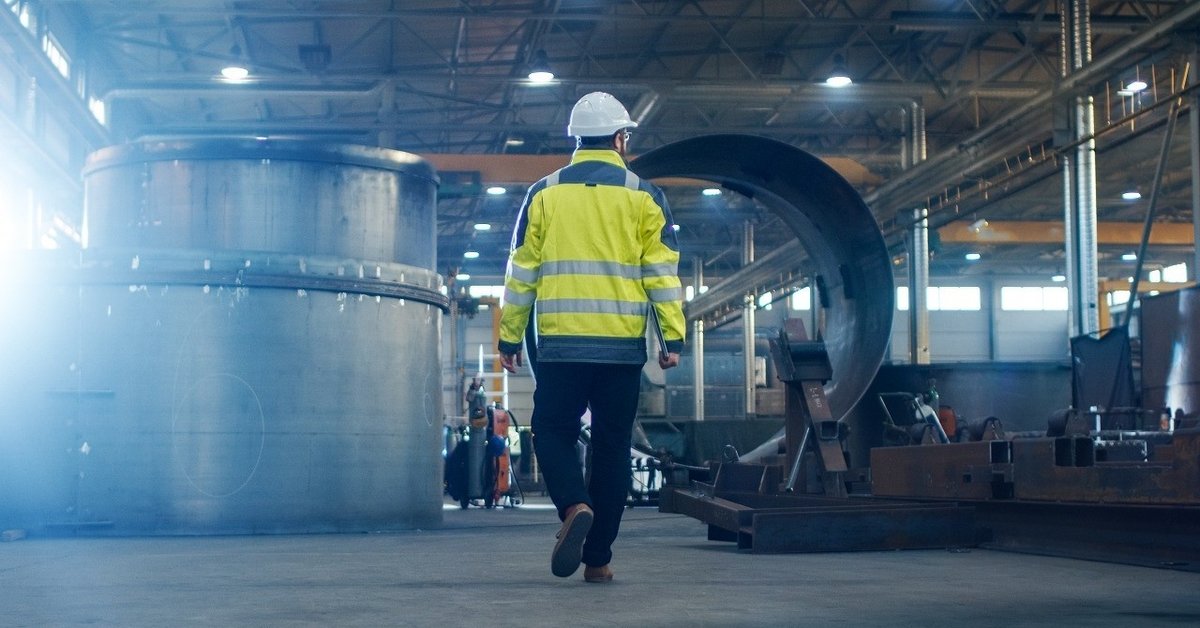
川崎重工とBCGで感じた重工業の課題
4月に株式会社東京ファクトリーという会社を設立し、現在は重工業の生産現場向けのSaaSプロダクトの開発を行っています。
重工業は参入障壁が非常に高いこともあり、ベンチャー企業がなかなか入りづらい領域かと思うのですが、なぜ私がこの領域で起業をしたのか、川崎重工業とBCGでの勤務経験を通して感じた日本の重工業界の課題を基にまとめてみました。
1. 川崎重工で感じた重工業の抱える問題
2013年に新卒で川崎重工業に入社した私は兵庫県の加古川にある工場で産業用のボイラーを製造する生産技術エンジニアとして社会人生活をスタートしました。
生産技術というと会社によってその役割は若干異なるのですが、配属された部門では大きく以下の3つの役割がありました。
①設計が発行した図面に基づき与えられた予算・納期内でQCD(Quality:品質、Cost:コスト、Deliverly:納期)を満足するべく生産計画の立案~現場への説明・指示~現場フォローアップを行う
②製品の受注前段階で見積を行う
③自社の製造能力を向上させるための設備投資の計画・実行を行う
重工業が特殊なのは②の”製品の受注前段階での見積”が発生することです。通常、製品の価格は需要と共有のバランスによって決定されるのが一般的ですが、重工業の場合は受注生産のみになるので、見積を複数社行った後に、安い価格を提示した会社が受注するというプロセスで製品の価格が決定されます。
国内の工場で10件程度の①のプロジェクトや②③の業務に携わった後は、海外生産管理課という部署に異動になり、東アジア(中国/台湾/韓国)の外注会社に常駐して製作指導を行っていました。
転職をする前の1年ほどは中国の合弁会社で福島県須賀川市向けのごみ焼却ボイラーを製造するプロジェクトにスーパーバイザーとして派遣され、現場の製作指導を行いました。
中国で感じた疑問
中国の合弁会社はこれまで多くの中国国内向けのボイラーを製造していたのですが、日本向けのボイラーを製造するのは、彼らにとって初めてのことで、"日本品質"を現地の人たちに理解してもらい品質要求を満たし無事製品を納品することをミッションとして合弁会社に常駐していました。
メーカーでは当時まだ若手とみなされる私にとって、中国の合弁会社が日本向けの製品を製造できるかの試金石となるこのプロジェクトはとても大きなチャレンジでしたが、川崎重工と合弁会社の双方から多大な協力をいただき、時に衝突もありましたが順調にプロジェクトを進めていました。
自分の計画や指示を元に部材が徐々に製品の形になっていくことは、元々プラモデル作りや工作などが好きだった私にとってとても楽しく、やりがいを感じて仕事をしていました。
しかし、同時に「自身が一生懸命取り組んでいるこの業務は中長期的に見て会社のためになっているのだろうか?」という疑問も抱きました。
当時、私の派遣元である日本の工場では受注が減っており、人の配置転換を進めるなど非常に苦しい状態でした。というのも、日本の国内工場は人件費が高いので、国内工場で生産をする前提で見積を行うとコスト競争力が無くなり製品を失注してしまうため、外注での製作前提でプロジェクト管理部門は見積を行わざる負えないという背景がありました。
日本の国内で製造するのは、納期の短い製品や、実験的に製造する製品、日本の管理レベルでないと製造できない高品質が要求される製品だけでした。
私はプロジェクトを通して合弁会社に日本の品質レベルや管理手法を中国の会社に指導し、彼らでも製作可能にすることで、自らが国内工場で獲得してきた知見を海外に流出させているのではないかと感じていました。
同時に海外の現場でもう一つ実感したのは、日本の生産現場のレベルの高さでした。管理手法が優れていることもさることながら、作業員の製品に対する理解やリテラシーの違いなどの根幹の部分はまだまだ差が開いていると感じました。これは、海外では転職が当たり前でなかなか技能者が育たないことや文化の違いも原因かと思いますが、積み上げてきたものづくりの経験の違いがやはり大きいと思います。
日本の重工業の強みはこの蓄積してきた経験をベースにした”ものづくり力”であり、今後も国際的な競争力を有するためには日本国内で引き続き生産を行うことが不可欠です。そのためには、以下の3つが必要だと考えています。
①生産革新によりコスト競争力を獲得する。
②継続的な改善活動により品質を維持・向上させる。
③新製品の開発により実証実験の場として国内工場を活用する。
短期的に利益を追い求める場合は当然海外への生産拠点の移転は不可欠だと思います。しかし、長期的に見ると新製品の開発などを行い続け、日本の生産体制を維持することがより大切です。現在は日本全体を見ても生産拠点の移転が進む一方で生産体制の維持の方が難易度が高いので後回しになってしまっているのではないかと思います。
意思決定の重要性を実感し転職
私は中国での経験を通して、経営の意思決定の影響の大きさと中長期的な視点で意思決定をすることの重要性を実感しました。
そして、そのような意思決定ができる人になるためにはどうすれば良いかと考えてみると、川崎重工業に居続けた場合、意思決定ができるポジションにつけるのは数十年かかるうえ、不確実性が高いと感じました。また、そのようなポジションについた場合も、当時の環境で経験を積むことで適切な意思決定ができるようになれるのか自信がありませんでした。
そのため、お世話になった川崎重工業を退職し、企業の意思決定のサポートを生業としている戦略コンサル会社に転職することしました。
(もちろん他にも様々な理由はありましたが、ここでは割愛いたします)
2. BCGでの経験と外から見た重工業
BCGでは、主に製造業・エネルギー企業を対象にしたターンアラウンド、デジタルトランスフォーメーション、シナリオプランニングなどのプロジェクトを経験しました。(残念ながら重工業の案件には従事する機会はありませんでした)
アジャイル開発の経験
BCGで携わったプロジェクトの中でも特に現在の業務に役立っているのは、クライアントの営業組織へのデジタルツール導入をサポートするプロジェクトです。クライアントの営業マンは家庭に訪問しヒアリングやそれに基づいて社内の関係部門と日程調整などのやり取りをしなければならないのですが、それを電話などで行っており非効率であったため、タブレットでその作業を行えるようにして業務効率を改善する、ということを主目的とした案件でした。
私はこの案件でクライアントの営業現場からヒアリングを行い、ビジネス要件を明確にしたうえで、クライアントの開発部門にそれを伝えて開発されたものを確認するという、アジャイルな手法で、いわゆるPMO(Project Management Office)を行っていました。
それまで開発に携わったことのなかったのですが、この案件を通してビジネス上の困りごとをデジタルの力で解決していくという開発の面白さとアジャイル開発の手法を知ることができました。
他の産業に携わる中で感じた重工業の課題
BCGで様々な業界を見ていく中で、改めて実感したのは重工業の現場こそデジタルの導入余地が大きいのではないかということです。現場で働いていた時はそれが当たり前だと感じていたのですが、他の産業で様々なデジタル化の取り組みが行われている中で、重工業の製造現場ではA1で印刷した紙の図面を用いることが常識であったり、ハンコを捺印した紙の資料を現場の掲示板に張り付けて工程管理を行っていたりなど、数十年前からオペレーションが変わっていない領域が多く残されていたことへの違和感を覚えました。
ではなぜ重工業の現場はレガシーなのか?と考えたときに、仮説としてセル生産方式であるがゆえに最新のテクノロジーが入り込む余地が少ないからではないかと思います。(ライン生産方式の場合は人が固定されて製品が動くのに対して、セル生産方式ではものが固定されて人が動き回ります。重工業の場合は製品が巨大なので、ラインに製品を乗せることが出来ず、製品を動かすだけでもコストがかかるのでセル生産方式が一般的です。)
ライン生産の場合は繰り返し生産により作業が単純化されるため、IoTやAI、それによるビッグデータの活用などの最新のテクノロジーが入り込む余地が大きかったのに対して、セル生産の場合は人がほとんどの作業を担うためより労働集約であり、IoTやAIなどの最新のテクノロジーの恩恵を受けずらかったのではないかと思います。(もちろんセル生産方式でも、ロボットを用いた溶接や3D計測による品質・工程の改善など各種取り組みは行われていますが、デジタルツインや需要予測、故障予知、製販連携まで取り組んでいるライン生産に比べるとデジタル化は進んでないと言えます)
このように重工業の現場は非常にレガシーであることにBCGで様々な産業を見ていく中で気が付いたのですが、重工業に対してはAIやIoTの導入を進めるよりも、業務やプロセスのデジタル化が有効だと言えると思います。
3. 起業のきっかけ
BCGでは日系メーカーから外資系戦略コンサルへの転職だったのでギャップが大きく大変なことも多かったですが、非常に優秀な人たちと共に仕事ができて学びが大きく転職して正解だと感じていました。また、様々な業界から人が転職してくるので人材の多様性にも富んでおり、様々な考え方の人がいて視野を広げることができました。
その中でも影響を受けたのは、入社三カ月で退職して起業をした中途入社同期でした。終身雇用が大前提の大企業に新卒で入社した私にとって周囲にそのような人はいなかったのでかなり新鮮でした。また、たまに元同期のオフィスの引越しなどで手伝いをすることなどがあり、同期が退職してからも話をすることが度々あったのですが、意思決定をほぼすべて自分一人で行っており、とても活き活きと仕事をして楽しそう見えました。
そんな中、エンジニアリング会社出身のBCGerと共に仕事をしていた時に、自身が重工業に対して感じていた課題を解決するツールの素案を思いつき、先述した案件で実際に開発に携わった経験から自分でやってみることもできるのではないかと考えるようになりました(当初思いついたのは、不良票をベースにしたBIツールのようなもので現在のツールとは異なります)。
ちょうどその頃、同期が興した会社の企業価値は2桁億円になっており、自分のアイデアや手腕で逞しく事業を行うことに対する憧れもより一層強くなりました。
そして、そのアイデアをベースに様々な人と議論をしていき事業計画を深めていく中で、自身の持っているアイデアを実現化することで、一番思い入れのある重工業にとって良いインパクトを与えることができると確信することができたので、2020年頭にBCGを退職し起業をしました。
4.東京ファクトリーの目的
今後ますます海外へ生産拠点の移転が進んでいく中で、日本の重工業メーカーが世界No.1であり続けるためには、海外生産拠点で得られた情報を蓄積してそれを日本にフィードバックし、製造ノウハウを保持することで、”製造”という単純労働集約な事業から”生産ノウハウの提供”というより高付加価値な事業にシフトしていくことが必要だと思います。
東京ファクトリーではサプライチェーンの見える化と製造情報の蓄積を実現するプロダクトを開発しており。このプロダクトを通して日本の重工業界が世界No.1であり続けるために貢献していければと考えております。
5.最後に
ここまで読んでいただいた皆様ありがとうございます。すごく長文なってしまい失礼いたしました。
東京ファクトリーでは一緒に開発を行っていただける仲間を募集しております!これまで製造業に携わってきて同様の課題を感じたことのある方、レガシー産業にデジタルの力で挑みたいと考えている方、創業初期のベンチャー起業に興味のある方は是非以下の弊社求人ページよりご連絡ください!
https://herp.careers/v1/tokyofactory
次回以降はもっと端的な文章にして情報発信していければと考えていますので、引き続きよろしくお願いいたします。
この記事が気に入ったらサポートをしてみませんか?