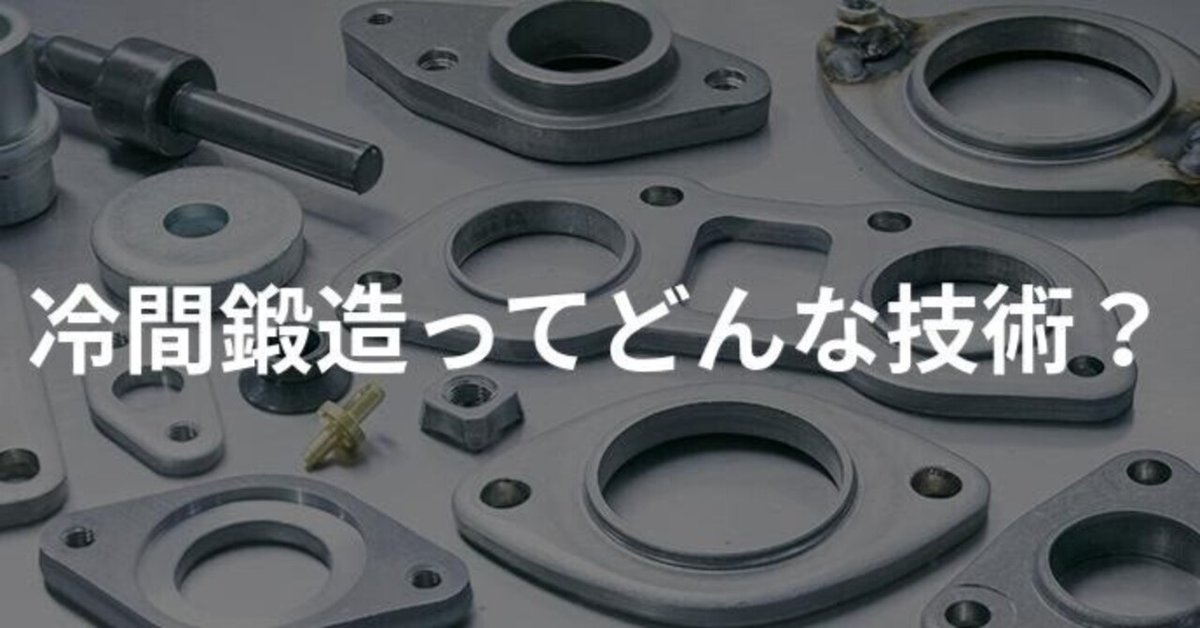
冷間鍛造ってどんな技術?
冷間=冷やすわけじゃないよ!
こんにちは、(株)オーテックの小川広佑です!
私は、大学は文系学部に進学、新卒では広告業界で働いていたため、入社するまで機械工学の知識は皆無でした。(たまに、自転車のメンテナンスで部品をばらしたりするくらい、、、)
入社当初、「冷間鍛造」と聞いて頭の中が「?」な状態でしたが、冷間という名前がついていますが、加工する金属を冷やしたり、金属が冷たいわけではないです。
一般的な金属の加工方法として、「熱間鍛造」と「冷間鍛造」、「切削」などの工法があり、冷間鍛造は常温で金属を加工する工法です。
他の加工方法と比較してみると…
熱間鍛造との比較
熱間鍛造は、その名の通り金属を高温に熱して柔らかくし、成形する方法です。例えば、刀鍛冶が刀を打つシーンを思い浮かべてみてください。熱した金属をハンマーで叩いて形を作る、まさにあれが熱間鍛造です。
一方、冷間鍛造は金属を熱くしないので、素材の細かい結晶構造が崩れにくく、より高い強度を持つ部品が作れるというメリットがあります。しかも、熱を使わないため、冷却の時間や手間が省けて効率的です。
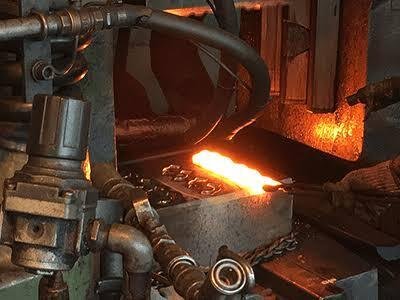
切削加工との比較
切削加工は、金属の素材を削り取って目的の形状にしていく方法。これは加工の精度が高く、細かいデザインが得意です。しかし、削り取る分だけ材料が無駄になるというデメリットも。
冷間鍛造の場合、材料を「削る」ではなく「押し固める」ので、素材のロスが少なく、環境にもやさしい。しかも、部品の強度も高いまま維持できます。特に、自動車や飛行機の部品など、強度が要求される製品にはうってつけです。
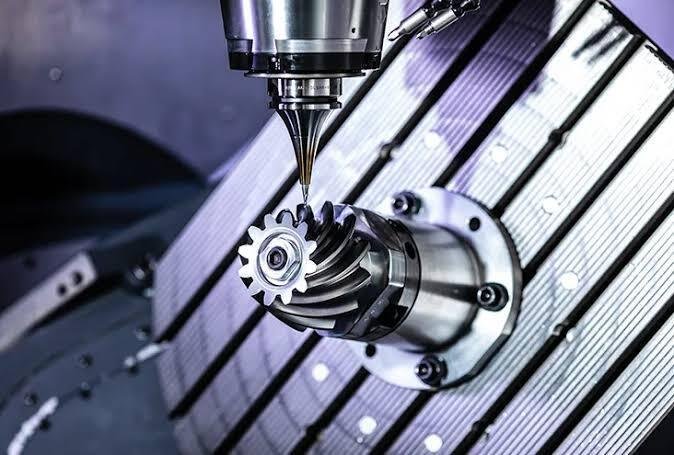
冷間鍛造って何がスゴイの?
「冷間鍛造」は、熱を加えずに成形するため、金属の素材そのものの強度をしっかり保ちながら、非常に精密な形状を作り出すことができます。そのため、以下のようなメリットがあります。
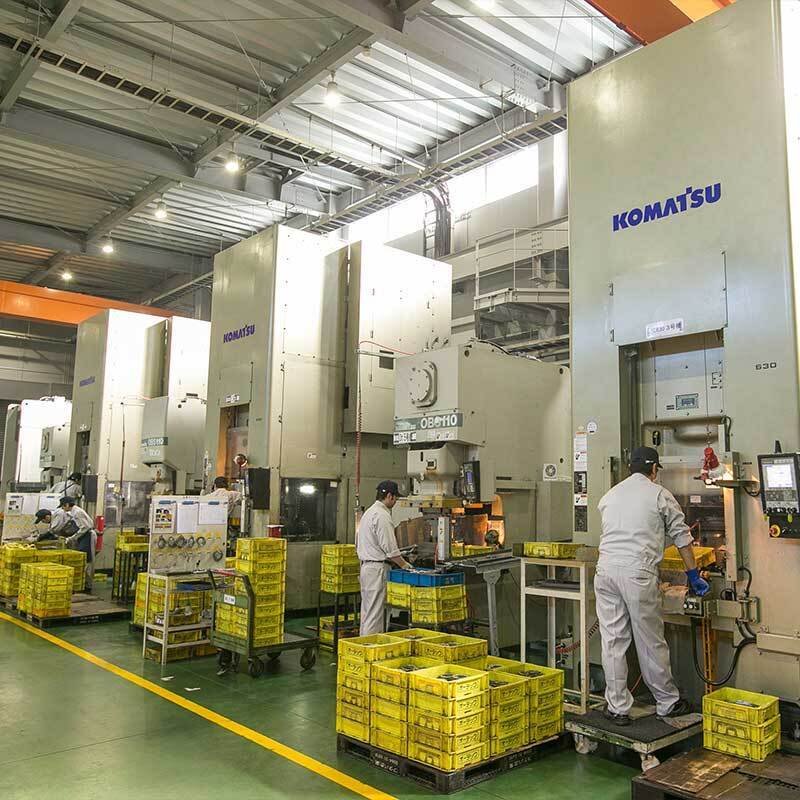
冷間鍛造のメリット
高精度な成形
冷間鍛造は、細かい形状でもしっかりと成形できるため、製品の寸法精度が非常に高いのが特徴です。強度が高い
熱間鍛造や切削と比べて、冷間鍛造で作られた部品は素材の強度を保ったまま加工できるため、強度の高い部品が求められる場面で活躍します。材料の無駄が少ない
切削加工のように削りカスが出ることがないため、材料の無駄が少なく、コストパフォーマンスも良いです。生産性が高い
熱間鍛造のように材料を加熱して冷ますプロセスが不要なので、スピーディーに生産できる点も魅力です。
詳しく知りたい方は、こちらもご参照ください。
冷間鍛造は、今の時代にこそ求められる技術!
「冷間鍛造」は、金属加工の中でも高精度・高強度・高効率を誇る加工法です。また、昨今ではCO₂の排出量規制やSDGsの観点から「冷間鍛造」の技術は再評価されてきております!
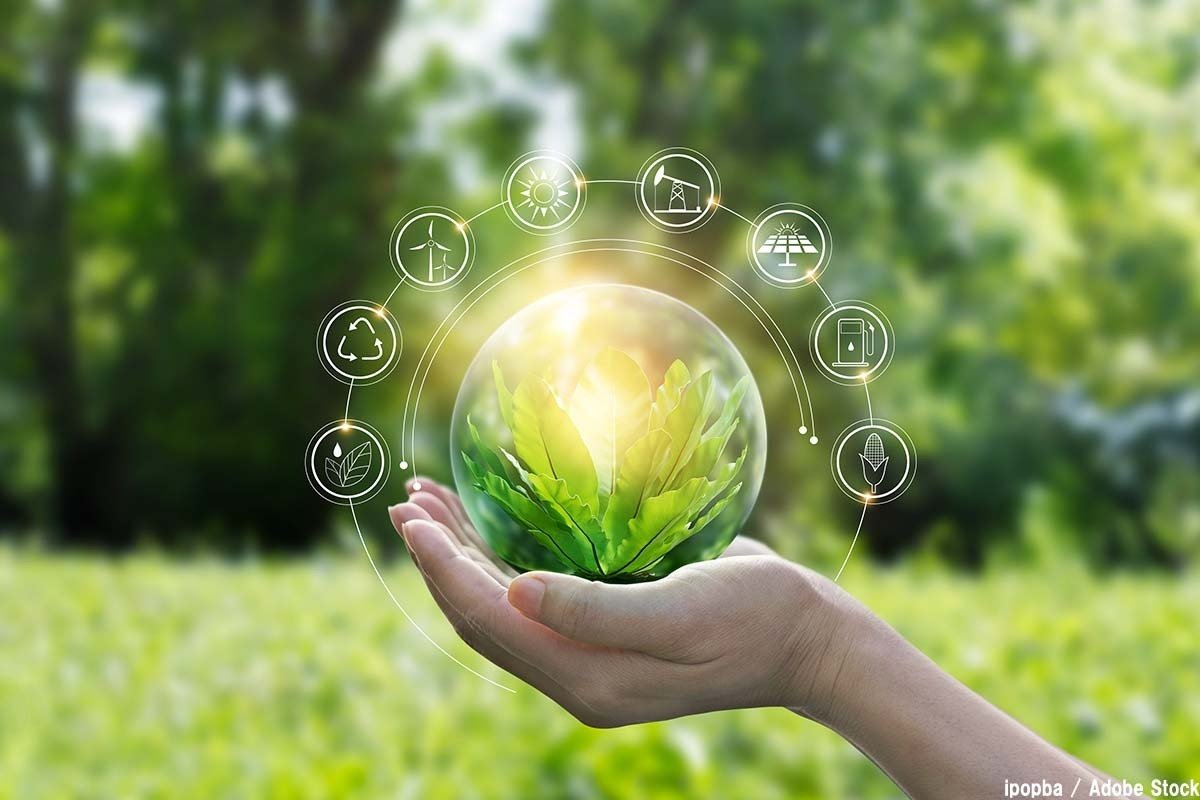
エネルギー消費の削減
冷間鍛造は、金属を常温で加工するため、熱間鍛造のように金属を高温に加熱するための大量のエネルギーが必要ありません。加熱プロセスを省くことで、エネルギーの消費を大幅に抑えることができます。これによりCO₂排出量を抑えることができます。材料の無駄を減らす
冷間鍛造は、材料を削るのではなく、圧力をかけて変形させるため、切削加工に比べて材料のロスが非常に少ないのが特徴です。無駄な廃材や削りカスがほとんど出ないため、素材を効率的に活用でき、資源の節約に繋がります。リサイクル可能なプロセス
冷間鍛造で使われる金属材料は、再利用が可能なものが多く、廃棄物の最小化に貢献しています。さらに、リサイクルされた材料でも強度や精度を保ちながら加工ができるため、循環型経済を推進する重要なプロセスとなります。長寿命な製品の製造
冷間鍛造は、加工中に金属の結晶構造を乱すことが少ないため、最終製品は高い強度と耐久性を持ちます。長持ちする製品を作ることは、頻繁な交換やメンテナンスを減らすことに繋がり、長期的に見て資源とエネルギーの節約にもなります。環境負荷の低減
冷間鍛造は、環境に優しいだけでなく、作業環境にも負担が少ない工法です。熱を使わないため、作業場の冷却コストや排気ガスの処理も必要なく、環境への影響が少ないクリーンな加工方法です。
まとめ
「冷間鍛造」の特徴や魅力を知っていただけましたでしょうか?
当社では、この「冷間鍛造」の工法を利用して自動車部品以外の新たな製品の開発にも取り組もうとしております。もし、「こんな製品があったらいいのに」と思われることがあれば、当社までお問合せください!お待ちしております!
記事の内容が面白かったら、フォローやSNSでのシェアを宜しくお願いします!
当社に興味がある方は、こちらもご参照ください!
応援したいと感じて頂けたらサポートお願いします! 頂いたサポート費は、AIやDXの調査費用として使わせていただきます! より良いコンテンツの制作を頑張ります!