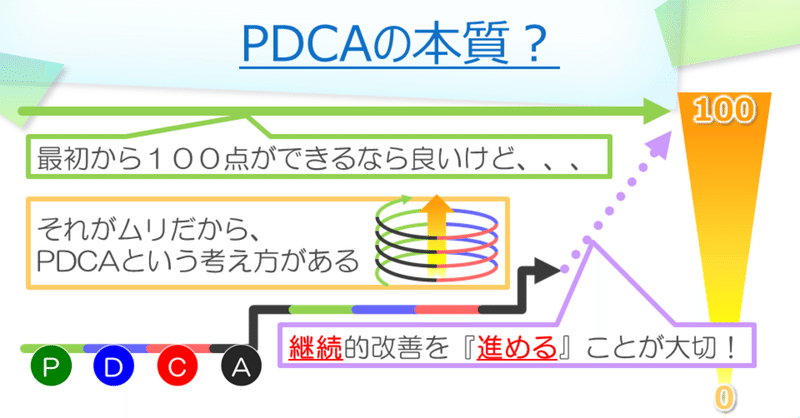
HACCPを上手く使うために⑫ ~手順4 フローダイアグラム 何のために作るんですか?
こんにちは! あたたけ です。
引き続きHACCPの話です。
今回は『手順4 フローダイアグラム』についてです。
実際の食品工場での取り組みや研修などを見ると、
この辺りから『本格的なHACCP』の雰囲気が出てくると感じます。
確かにフローダイアグラムはハザード分析のために大事な資料です。
あたたけの場合、工場確認にお伺いする際には、
自分自身で製造工程の全体像をつかむため、最も重視しています。
ですが、あくまで『HACCPプラン作成の準備段階』ということが忘れられ、
過剰な作り込み(≒時間のかけすぎ)をしていると感じることもあります。
『重視する』と『時間をかけて作り込む』はだいぶ違うんですよね。
なぜ、過剰な作り込みをしているのか?
理由は『最初から100点を目指す、日本的?気質』と
『フローダイアグラムの目的を充分に理解していない』だと思います。
順に考えていきましょう。
①最初から100点満点はとれるのか? とる必要はあるのか?
これはフローダイアグラムに限りませんけどね。
以前、『HACCPはPDCA』というようなことも書きましたが、
PDCAというものは、継続的改善を確実に進めるためのものです。
つまり、『改善が行われるのは当然のこと』という考え、
言い換えれば『最初から完ぺきな仕組みは作れない(作るのは難しい)』
という考えが根本にあると思います。
まぁ、
『現状には完ぺきに対応しているが、世の中の進歩や要求の変化に
対応していくための継続的改善を進める』というのが
理想ではありますが、あくまで『ただの理想』です。
失敗や間違いを認めることを恐れすぎじゃないかなぁと思います。
というような話をすると、
『じゃあ、食品事故を起こして良いの?』と言われるのですが、
『じゃあ、今の管理手段は完ぺきなの?』と言い返したいところですが、
これは売り言葉に買い言葉というヤツですね。
実際のところは、『満点じゃないけど決して不合格点ではない』というのが
多くの食品工場でのあたたけの印象です。
HACCPの目的は、『HACCPに取り組む』ではなく
『HACCPを使って、より良い管理手段にする』です。
大事なのは、フローダイアグラムやハザード分析の書類ではありません。
それらを通して、適切な管理手段を考えることであり、
実際の作業をより良いものにしていくことです。
であれば、変にカッコつけずに、
とりあえず出来る範囲・わかる範囲で作れば良いと思います。
NATO(Not Action,Talk Only)と言われないようにね。
※この辺りは、教える側の姿勢にも問題があるかもしれません。
『ダメ出しするのがエライ』という勘違いが未だに残ってる。。。。。
本当にエライ指導者とは、『知識だけでなく意欲も伸ばす指導者』
だと思います。上から目線でダメ出しだけでは意欲は伸びないです。
②フローダイアグラムの目的は?
HACCPの取り組みで見ると、
『ハザード分析をしやすくするため、(今の)製造工程を見える化する』
ですね。
ただ、最初に『あたたけは工場確認時に重視する』と書いたように、
工程の見える化ということ自体が、工場の全体像を把握するため、
とても便利に使うことができます。
これはHACCPチーム(に限らず工場で働いている人)にも同じです。
なので、『フローダイアグラムには管理手段なども書き込む』ことが
推奨されているテキストを見かけます。
このこと自体は正しいと思いますが、
先ほどの『①最初から100点を目指す』と結びつくと
『フローダイアグラムの時点で、
完ぺきにハザードを管理できる管理手段になっているか考える』という
次に行うハザード分析を全否定する発想になっていることがあります。
HACCPではあくまで『準備段階』の文書を
『最終的な情報共有に活用する』という矛盾が。。。。
これを解決するには、
まずは、準備段階の資料と割り切って『今の』製造工程を見える化する、
その後、ハザード分析などを進め随時改善する、というのが現実的です。
ん???
これって、さっきの①で書いたのと同じですね!
とりあえず出来る範囲・わかる範囲で作れば良いんです!
ということで、今日の一言です。
『フローダイアグラムは便利&見栄えする書類。
ただし、真の目的はハザード分析の支援。
時間をかけるのであれば、フローダイアグラムではなくハザード分析。』
次回はフローダイアグラムの続きです。
目的を踏まえて、どんな作り方が良いのか考えていきましょう。
それでは、今回はこの辺りで!
この記事が気に入ったらサポートをしてみませんか?