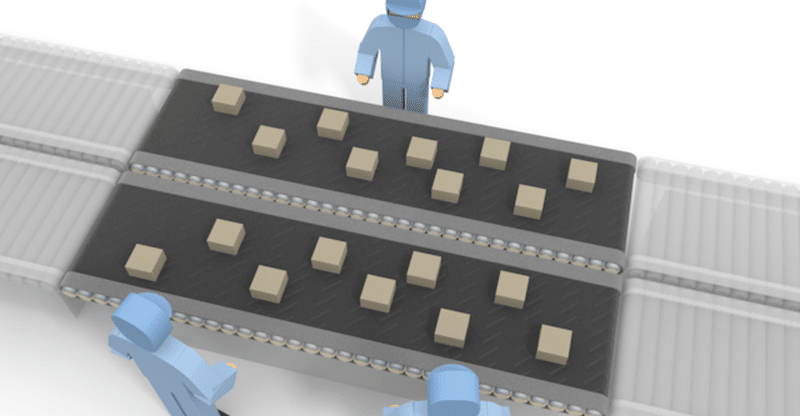
ライン生産でロボットを導入する際に気を付ける事 食品製造の場合
食品工場の場合、多くはライン生産を導入しております。食品の場合、材料を投入した後で、その材料が加工され、各工程を通過していくわけですが(いわゆるバッチ生産)、前工程(材料加工等)の能力に依存するケースが多く、後工程の大半はその能力に合わせて、いかに止めずに生産を行うかが、ポイントとなってきます。その為、包装工程には特に人手を要します。
昨今の労働力不足を受けて、今包装工程の自動化を導入するケースが増えておりますので、一点アドバイスをしたいと思います。
一般的に自動化には「専用自動機」か「ロボット」を用いられますが、多品種少量、レイアウト変更等を考慮すると「ロボット」を用いて検討するケースが増えております(技術難易度にもよりますが)。その為、自動化を検証する際には、「上手くワークを取り出せるか(PICKING)」「上手く定位置(箱やトレイ等)に置けるか(PLACE)」を主に議論が進められます。そして、実験等を重ね出来ると判断された後はタクトタイム等の時間を算出し現状の生産能力をカバーできるか検討します。ここまでが順調にいくと、あとはその情報を基に構想設計へと移ります。
構想設計フェーズでは設計者が「〇〇台のロボットを使えば、現状の生産能力を満たす」という意識をもって作業を進める事があります。そしてよく出てくる構想図面というと、「ライン生産上に〇〇台のロボットが加わっただけ」の図面です。勿論、これでうまくいくケースもあります。が、ここで提案を受けた貴方は注視しておくべき点があります。
「それは、後工程で異常が発生したケースを考えているか」という視点になります。
ご存知のように、包装工程の後には金属探知機やシール貼付け、箱詰め工程等があります。例えば、後工程の金属探知機が反応しコンベアが停まった場合、例えば後工程に搬送しているコンベアにワークが詰まり押せ押せ状態になった場合・・・等はどうなるでしょうか?
きっとコンベアにワークが溜まり、ロボットは正常作業しなくなると思います。そして、その時に流れてくるワークはピッキングできない状態となります。量にもよると思いますが、コンベアから落下したり、機械に挟まれたりで、ワークをロスする恐れがありますね。
つまり自動化を構想する際にはこのようなイレギュラーを想定して設計を進める必要があります。例えば今回のケースですと、中間(ロボットの前工程)にバッファ機構を設け、後工程の異常時には仮置きバッファで一時置きしてあげるとか、コンベア自身を周回式にして溜まらないようにしてあげるような機構が必要です。この辺りは予算やスペースを考慮してどちらが好ましいかを判断すると良いと思います。
言われてみると当たり前の事なのですが、よくありがちな事例なのでご紹介しました。いずれにしても部分的な最適化を求めるのではなく、全体最適化を考慮する必要があると思います。この点はオペレーション面でも同じことが言えますね。
それではまた。
もし私の記事が貴方にとって有用なものでしたら、サポート頂けると大変うれしいです。よろしくお願いします。