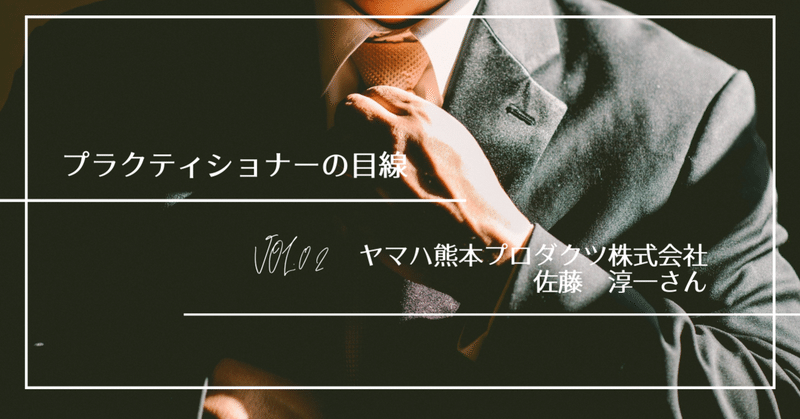
(後編)真の一貫工場へ。
前回、ヤマハ熊本プロダクツ株式会社(以下、YKP)・佐藤淳一さんへのインタビュー(前編)では、バブル崩壊後の構造改革から始まったご自身のキャリアと、TOCとの出会いに至るまでのお話を伺いました。今回(後編)は、YKPが「マネのできないモノづくり」を目指し、「真の一貫工場」へ進化することを目標に掲げて以来、製造企画課長として挑戦してこられた過程についてお話を伺っていきます。
1)2012年に企画部署が新設された経緯を教えてください。
-「自立」
佐藤:2012年に製造企画課長となり、私を含めて4名の新設部署がスタートしました。YKPが「マネのできないモノづくりでキラリと輝き、真の一貫工場へ進化する」という会社目標を掲げたのもこの頃です。ボート製造からエンジン製造への事業転換をして以来、マリンエンジン事業の期待に応えようと愚直にやってきた結果、YKPは順調に黒字業績を続けていました。一方で、YKPとして「自立」しなければならないという思いが社内全体に醸成されていたことも、企画部門新設の背景にあったと思います。
製造企画課は、YKPトップの思いを戦略、戦術に展開していくことをミッションとし、そこには「品質改革プロジェクト」や「原価低減プロジェクト」、そして私がリーダーとなった「SCM改革プロジェクト」が立ち上がりました。「モノのつなぎ、コトのつなぎ、ヒトのつなぎで製販一貫化確立」というプロジェクトスローガンを打ち上げ、私自身はこれを実現するための「プロセスデザイナー」となることを宣言したんです。社員一人一人にとっての「自立」の在り方が問われ、自立のためには「一人一芸」だということで、個々のコアコンピタンスや強みをどう確立していくかを真剣に考える機会に恵まれたのは、私にとって幸運でした。
2)TOCを試行するまでに12回のプレゼンを経たと伺いましたが。
-最初のつまずき
佐藤:「清流化=TOC(制約理論)」だということで、製造から事業までを含めたフローの清流化に向けて意気込んだ私ですが、実は問題提起の段階からつまずいてしまいました。ボート事業部事業企画に出向した時の気付きから、私自身は「製造と事業(販売)」を視野に入れた「一貫工場」を目指す必要があると信じて疑わなかったのですが、それはYKPの責任範囲を超えるものだとする認識が大半でした。当時支援していただいたTOCエキスパートと一緒に、所謂「フィージビリティ・スタディ*」を行い、3回目のプレゼンあたりまでは、「どれだけ販売機会が損なわれているか」という点を訴えようとしましたが、残念ながら、YKP社内で問題そのものへの同意を得ることができませんでした。
振り返ってみると、「なんとかTOCをやってみたい」という気持ちが先走ってしまい、私のいた組織が本当に必要としているニーズや課題の所在を捉え切れていなかった、つまり解くべき問題が何なのかというスタート地点からボタンの掛け違いがあったように思います。問題解決のプロジェクトを新たに立ち上げるためには、まず最初に、「対象とする組織を明確に定義すること」の重要性を学んだわけですが、ボタンを掛け違えたまま物事を進めようとしてしまうケースは、意外に多いのかもしれません。最初から事業(販売)までを含めたサプライチェーン全体の改革を提案した私は、相手の立場を尊重できておらず、要するにやりたいことを相手に押し付けようとしていたことに気付きました。
*フィージビリティ・スタディ(Feasibility Study):実現可能性を事前に調査、検討すること。
-何が問題か?誰の問題か?
佐藤:最初のつまずきを反省しつつ、私の責任範囲である製造領域で、つまりYKPで部品製造に関わる関係者が、日頃から何に思い悩んでいるのか、まずはこれに正面から向き合うことにしました。
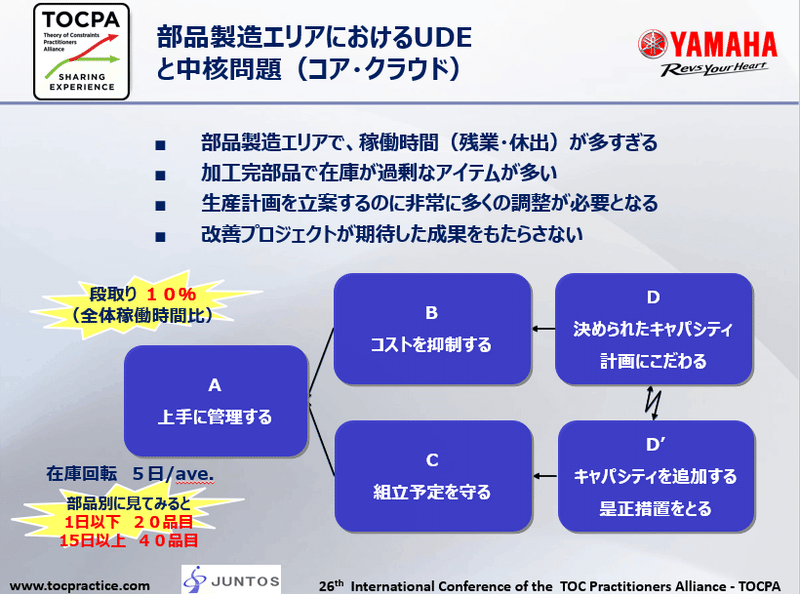
部品製造現場の声に耳を傾けて聞こえてきたのは、「生産目標を達成するために予め計画された残業時間(休日出勤含む)をいつも超過してしまうこと」、「過剰在庫の問題」、「生産計画立案にかかる多大な調整時間」、「期待した成果が得られない改善プロジェクトの数々」といったものでした。上の図に示したのは、現場が日常的に抱えている悩み事が発生する構造を表わしたもので、コア・クラウド*と呼ばれるものです。TOC思考プロセスに関する詳しい説明は割愛させてもらいますが、部品製造は「コストの抑制(原価低減)」と、「組立予定日までの製造期日厳守」という二つを常時要求されていました。ある時は「在庫を抱える」、またある時は「(まとめてつくるために)段取り回数を減らす」といった判断に揺れ動きながら、それでもうまくいかないので、結果的に残業は20時間/月の予定を超過して、いつも30~40時間/月かかっていました。
毎月開催される生産会議では、「予定通り行かないなあ」、「なぜだ?保全は何をやっている!?」、「計画の精度が悪い!」といった言葉が飛び交っていましたが、現場では「予定通り行かないのは仕方のないことだ」と受け止められ、むしろ生産目標達成のために必要なことだと前向きに捉えている人もいたくらいです。
ある時、「どうしても予定外の突発残業、休出が発生してしまいますが、これが無くせたら嬉しいですか。」と職長に投げかけた私の質問に、「そりゃ予定通りやれたら、従業員にも迷惑がかからないし、調整も楽になるからいいが。」という言葉が返ってきました。「本当はそうしたいが、なかなか実現できないこと。(半ば諦めてしまっていること)」それはつまり、なんとかできれば相手が喜んでくれることであり、これが「解くべき問題」であると確信した瞬間でした。ここに辿り着いた後、現場から汲み取った現実の問題に上層部が同意、納得してくれたのは言うまでもありません。
*コア・クラウド:TOC思考プロセスの中で紹介されるツールの一つで、様々なUDEs(Un-Desirable Effects: 好ましくない事象)が発生する根本原因を表現するもの。
-解決策をうまく説明できない。
佐藤:上層部に対する4回目のプレゼンあたりからは、別の問題にぶつかりました。解くべき問題について関係者間の共通認識が持てたのは良かったのですが、それを解くための方法をうまく説明できなかったんです。「設備投資でもない、IT投資でもない。魔法の杖か。TOCっていったい何なのか、よく分からなくなってきた。」という反応にうまく対処できませんでした。
2013年、我々が導入しようとしたのは、MTA(Make To Availability)というTOCソリューションの一つだったのですが、日本国内で公表された事例はなく、その具体的な導入方法については手探りの状態だったんです。この手法は、当時在庫生産環境向けのソリューションとして紹介されたそうですが、YKPはMTO(Make To Order:受注生産)の仕組みで動いていましたから、MTOからMTAへのトランスフォームという点に議論が噴出しました。「昔のだんご生産に戻るのか」という上層部からの指摘があったのですが、それは在庫生産そのものに対する強い反対意見だったわけです。受注生産から在庫生産に移行すると聞けば、誰しも在庫が膨らむと思いますよね。実はそうではないというロジックを説明し、納得してもらうまでに大変苦慮したのを記憶しています。
上層部の承認が得られず、途中で諦めそうになった私の心を奮い立たせたのは、「もしこれが成功したら日本初!いやアジア初だ!」ということでした。私も部下も、初めて実現できるかもしれないことに挑戦するチャンスにロマンを感じていたんですね。だからこそ、12回も粘りに粘ることができたんだと思います。
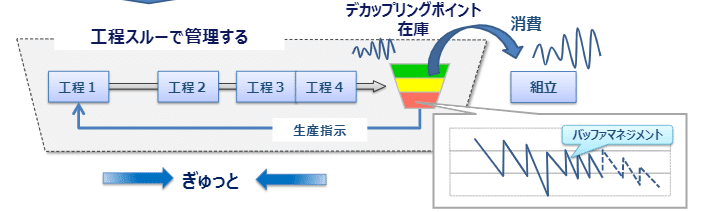
-経営陣へのBuy-In
佐藤:概ねの方向性について関係者の同意が得られた後も、経営陣からソリューション導入の最終承認をもらうまでには、まだいくつかの準備が必要でした。当時、私は社外勉強会でTOCのマネジメント・ツール(TOC思考プロセス)を学んでいたのですが、「移行ツリー*(TrT: Transition Tree)」と呼ばれるフレームワークを使って準備を進めました。(以下参照)
*移行ツリー:目標達成のための行動計画を作成するTOC思考プロセスのフレームワーク
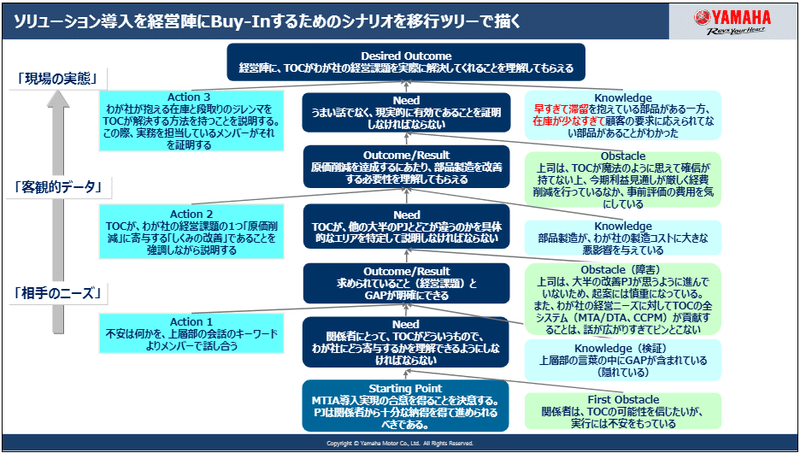
7回目のプレゼンを行った頃には、「やってみようか」という言葉を上層部から頂いていましたが、製造部のコンセンサスを得ることには細心の注意を払いました。企画部署にいる我々が、新しい試みを提案するのは当然のことなのですが、製造部署からすれば、既にTPM(保全、品質、小集団現場改善)、いわゆる“現場力”というところから様々な成果を出していましたし、むしろ、新たな試みによって品質や納期に悪影響を及ぼすリスクに懸念を示されました。ですから、ソリューションの押しつけにならないよう、彼ら自身が抱えている「在庫と段取りのジレンマ」を解消するための手段であることを理解してもらうことに時間をかけました。企画部署が描いたうまい話ではないことを経営陣に理解してもらうためにも、まずは製造の現場で実務を担当するメンバーが納得し、それを彼ら自身が証明できるようにするための支援に全力を尽くしました。
3)TOC導入から結果が現れるまでにどれくらいの時間がかかりましたか。-やると決めたら早いのが「やらまいか精神」のYKP。
佐藤:やると決まってからの展開は早かったですね。2013年3月からのPOC(Proof of Concept)に要したのは約5カ月間。その後、システム開発などの準備期間を経て、2014年1月からロールアウト(全部品展開)しました。製造リードタイムは18日から10日へ、そして後工程(組立)への遅延件数は2013年との比較で263件から98件にまで改善されました。改善効果については、2016年5月に開催された第26回TOCPAカンファレンス(福岡)の発表資料に詳しく記載していますので、ご興味のある方はそちらの資料をご覧ください。
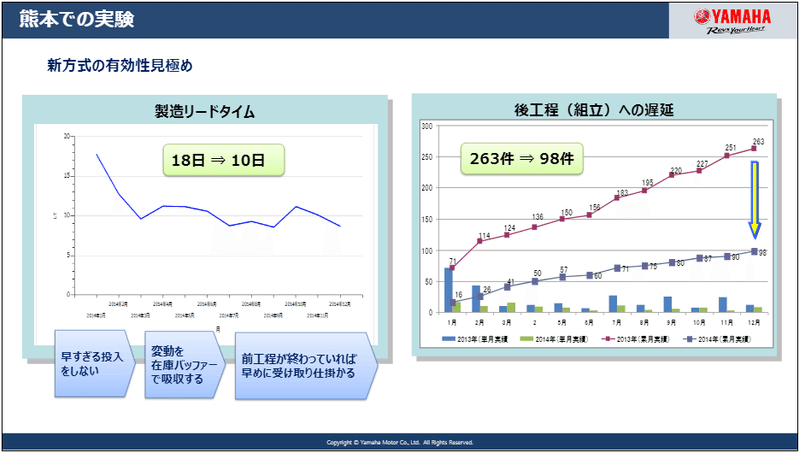
-最後に:共感してもらえる言葉を見つける
佐藤:ソリューションの導入過程で、私が大事だと感じたソフト面のポイントを、最後に一つだけ紹介させてください。それは、みんなが共感してくれる、みんなに響く「言葉」を見つけ出すことなんです。専門用語やロジックを使って正論をかざしても、なかなか響かないし、むしろ反発されてしまいますよね。最近、私がよく使う言葉の一つは、「お作法」です。ソリューションを導入、運用していく過程では、当然ながら様々な障害が発生しますし、時には基本ルールから逸脱して、妥協した運用方法に流れてしまうことがあります。そんな時、「お作法に照らし合わせると、これってどうでしたっけ?」と言うと、軌道修正のための前向きな議論に繋がって、協力して障害を乗り越えていけるんです。TOCのプラクティショナーにとって、相手の気持ちに寄り添って、お互い気持ちよく仕事をしていくための「言葉」を適切にチョイスしていくことは、私の経験上、とても大事なことだと感じています。
あとがき
つい先日、部品組立を担当する部署から全部署に対して応援要請があった際、佐藤さんは自ら志願して現場応援に入ったそうです。「エスノグラフィー」と呼ばれることがありますが、佐藤さんがこれまでやってこられたフィールドワークを重視するスタンスが現れていると感じました。基幹職となった今も、真の問題を掘り当てるための努力を惜しまないその行動力には頭が下がります。佐藤さん曰く、「顕在化している情報から改革は起こせない。現場で飛び交っている“コトバ”や、管理者、作業者の行動、表情を観察することから潜在ニーズを見つけることが大事だと思うんです。」という言葉が印象的でした。
2016年開催のTOCPAカンファレンス(福岡開催)で事例発表された際、佐藤さんは本社の生産管理部長を招待されたそうです。その時に、「オールヤマハで展開すれば効果は熊本の50倍だ!」と言われたことに大変勇気付けられたそうです。そして翌年の2017年から、佐藤さんはヤマハ発動機モーターサイクル事業に出向され、YKPでのTOC導入実績をもとに、「プロセスデザイナー」としての活躍の場を拡げていかれました。本社で取り組んでこられたことについても、近い将来に是非インタビューさせていただきたいと思います。佐藤さん、今回はインタビュー記事の作成にご協力いただき、誠にありがとうございました。
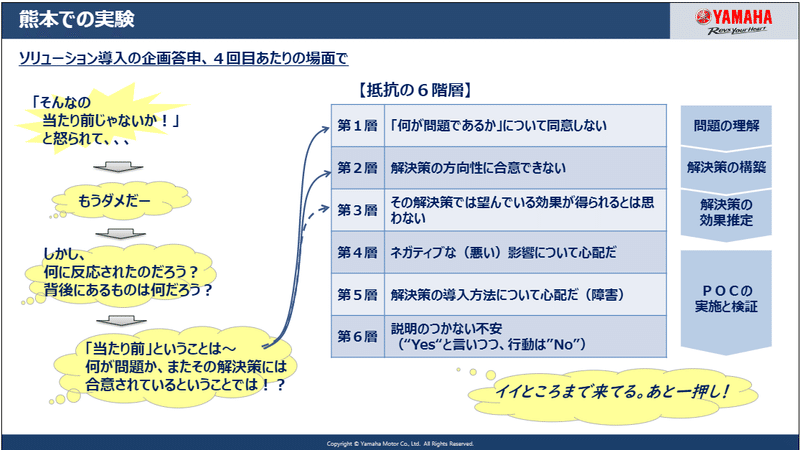
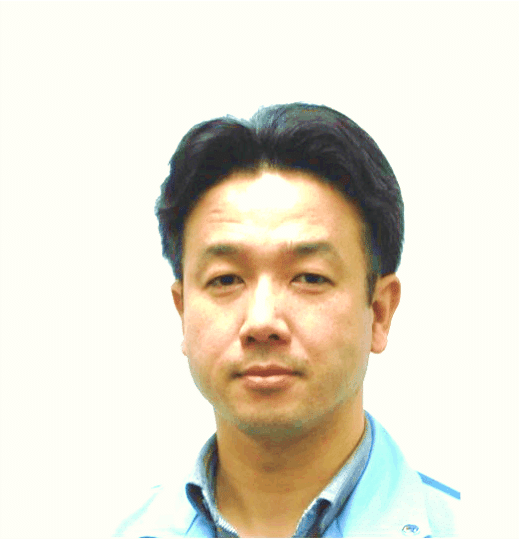
ヤマハ熊本プロダクツ株式会社
佐藤淳一氏の略歴
1991年-22歳 ヤマハ熊本プロダクツ株式会社に新卒入社。生産管理配属。
1996年-26歳 ボート事業部事業企画に出向
1998年-28歳 熊本に帰任し、ERP導入に関わる
1999年-30歳 マリンエンジン製造への事業転換
2008年-39歳 基幹職登用(生産管理課長)
2012年-43歳 企画部門新設(製造企画課長)
2017年-48歳 ヤマハ発動機モーターサイクル事業出向
2021年-53歳 熊本に帰任し、現在は後進の育成にあたる
(事例発表)
第26回TOCPA国際カンファレンス(福岡)
「TOC補充ソリューションを用いた生産方式改革」-2016年5月19日
第51回TOCPAカンファレンス(オンライン)
「私のTOC Journey」~問題と解決策、感情とロジック、モノと人、人と人をつなぐウィングマン~」-2021年11月18日
本記事に関するご質問、その他TOCPA Japanへのお問合せはこちらから。
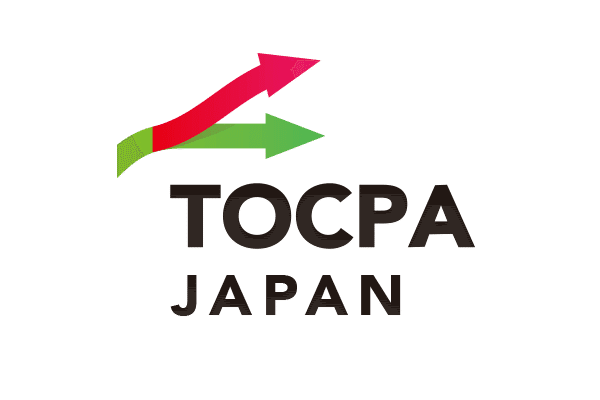
この記事が気に入ったらサポートをしてみませんか?