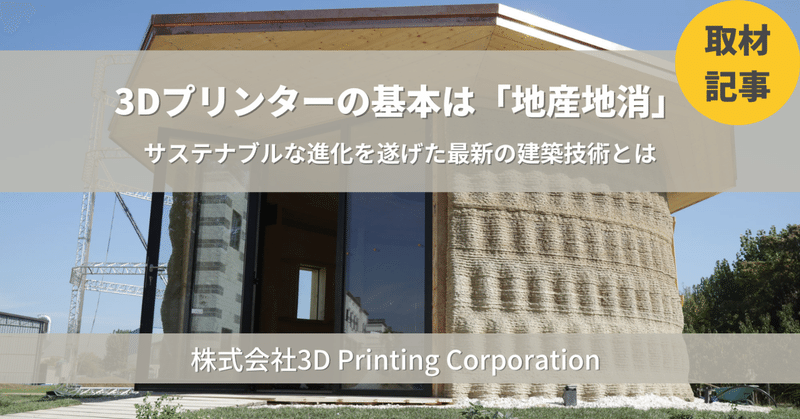
【取材記事】3Dプリンターの基本は「地産地消」サステナブルな進化を遂げた最新の建築技術とは
現在、製造現場で浸透している3Dプリンティング技術。10年ほど前の日本でのブーム以来、目覚ましい進化を遂げ着実に社会実装が進んでいます。株式会社3D Printing Corporationは3Dプリンターを用いた製品開発、材料開発、受託製造などを行っており、今回新たに「住宅建築可能な3Dプリンター」の導入に至りました。サステナブルな最先端3Dプリンターの技術や特徴、省エネのメリットや将来の展望などを中野さんに伺いました。
【お話を伺った方】
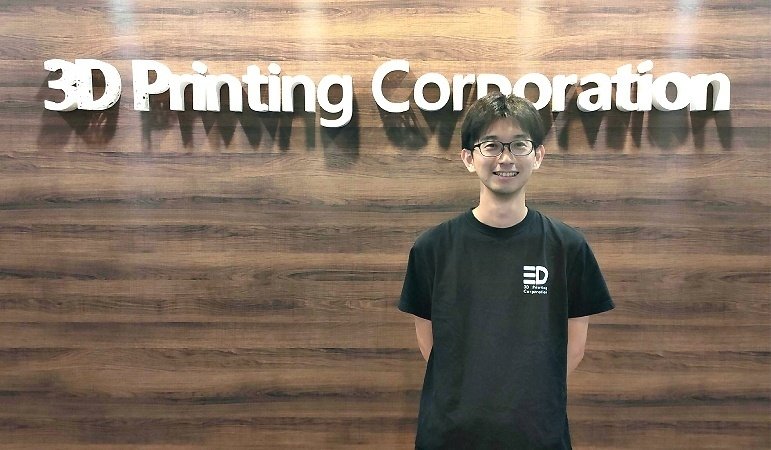
株式会社3D Printing Corporation 営業担当
■未知の造形を創り出す「3Dプリンター」の優れた特長
mySDG編集部:御社のご紹介からお願いいたします。
中野さん:弊社は、株式会社3D Printing Corporationといいます。3Dプリンターを事業の軸に日本で活動している設立8年目のスタートアップ企業になります。
弊社の社長はアメリカ人、副社長は韓国人というインターナショナルな環境なので、海外の最新トレンドやマシンの情報をより早く取り入れることができ、最先端の技術を提供しています。
山梨から4年程前に横浜に移転し、現在はリーディングベンチャープラザ横浜新技術創造館に拠点を構えています。工場に3Dプリンターを10種類以上設置しており、製造・納品、3Dプリンティングの開発案件などを受けて事業展開をしています。
mySDG編集部:開発の案件例をご紹介いただけますか?
中野さん:例えば「3Dプリンターを活用し、今までにないほど柔軟性に優れたクッションを作りたい」という案件の場合に「ラティスメッシュ」という網目状の構造で造形できるのですが、これが他の製法だと非常に困難なんです。このような今までにない造形物を作れることが3Dプリンターのメリットです。まだ世界中で実現されていない造形の開発をし、設計・製造まで手がける開発案件が多いですね。

mySDG編集部:「ラティスメッシュ」とは、Webサイトに掲載してあるヘルメットの内側に使用されている網目状のものですか?
中野さん:はい。ヘルメットに使うと通気性が良いので作業現場では快適さが増し、アスリートのヘルメットに採用すればパフォーマンスの向上が期待できます。
今までの素材だと、クッション性が高ければ風を通しにくいというデメリットがありましたが、3Dプリンティングはクッション性と快適さを両立できる、とても優れた技術なんです。
mySDG編集部:なるほど。私は特長を存じ上げませんでした。この優れた特長はどれくらい周知されているものなのですか?
中野さん:3Dプリンティングに先進的に取り組まれてる企業様はよくご存じですね。製造業で3Dプリンターが1台も入ってない会社は今ほとんどありません。試作品を作るために初めて取り入れてから10年くらい使い続けているパターンが多いですね。しかし、社内開発に使われることが主に多いので、一般の人にはあまり認知されてないんです。
■「WASPシリーズ」革新的!建築可能な3Dプリンター
mySDG編集部:今回新しく導入された建築が可能な3Dプリンターについて特徴を教えてください。
中野さん:はい。イタリアのWASP(ワスプ)社の3Dプリンターになります。
まずWASP社の理念からご紹介させていただくと「人間の根源的な欲求に対して、先進的な技術で回答を出す」というビジョンを掲げています。先進的な技術の部分は3Dプリンティングですね。
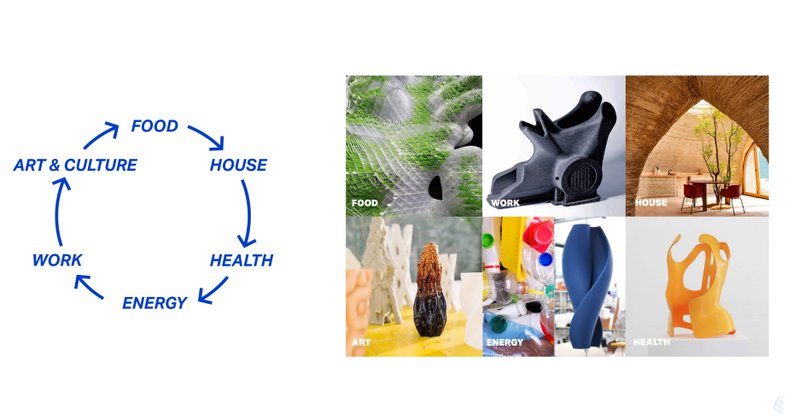
中野さん:WASP社は人間の欲求を「食料、住居、健康、エネルギー、仕事、芸術」の6つに定義をしていて、この欲求を3Dプリンティングで回答=実現していきたいということです。
例えば住居が必要であれば、コンクリート系の3Dプリンターを使って建築をする。仕事で利用したいのならペレット式を使い造形物を造る。人の欲しいと思う欲求に答えるため、さまざまなものを造ることを可能にし、人間の更なる発展に寄与したいと考える3Dプリンターの老舗の会社です。
今回プレスリリースに記事を掲載し、お問い合わせを多数いただきました。3Dプリンティングで家を建てたいお客さんは多いようですね。
mySDG編集部:ドーム状の個性的な形でしたよね。
中野さん:そうですね。他の事例もあります。2021年のドバイ万博でクリスチャン・ディオールが披露したポップアップストアですね。クレーンのシステムを2台使って、同時に作った建築になってます。筒状に建てて屋根に蓋をのせる建築方法です。
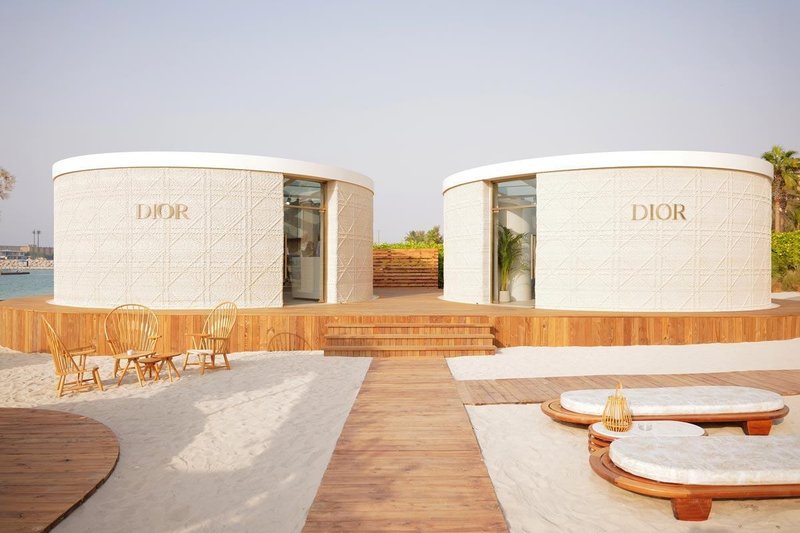
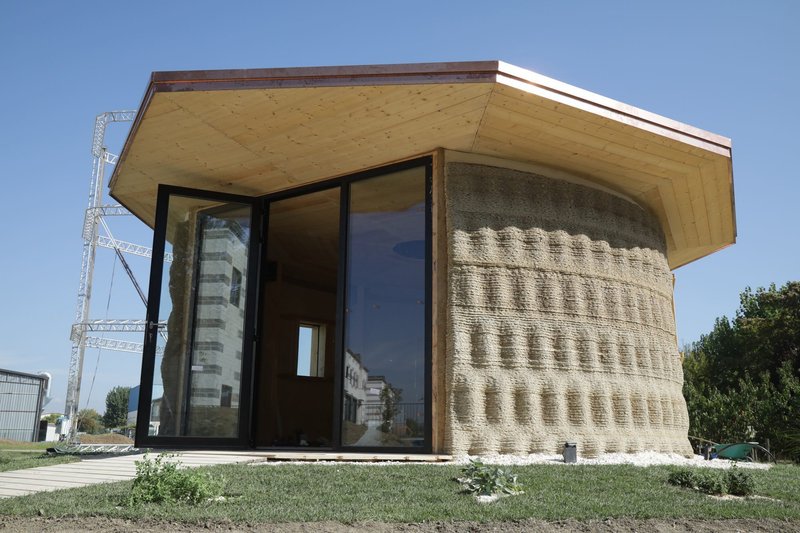
中野さん:グレーの家はWASP社内にある建物ですね。大体2LDKぐらいとか。
mySDG編集部:興味深い建築物ですね。壁の感触が気になりますね。日本に住んでいると建物の強度が気になりますがどのくらい丈夫なのでしょうか?
中野さん:3Dプリンティングのみで建築基準法をクリアするにはもう少し時間がかかるようです。住居は一番センシティブな部分ですから、イタリアでも地震などで倒壊のリスクを考慮した上で建築基準法が作られていて、日本と同等に厳しいと聞いています。
グレーの家は壁の内側に木の柱を立てて、木造建築扱いになっています。柱で屋根を支え、地震にも耐えられる構造にしているんですね。
WASP社の2023年度の「四角い家」を建てる最新プロジェクトでは、イタリアの建築基準法をクリアするように設計し、工法の開発も進めています。
■実は地球に優しい、3Dプリンターの基本は「地産地消」
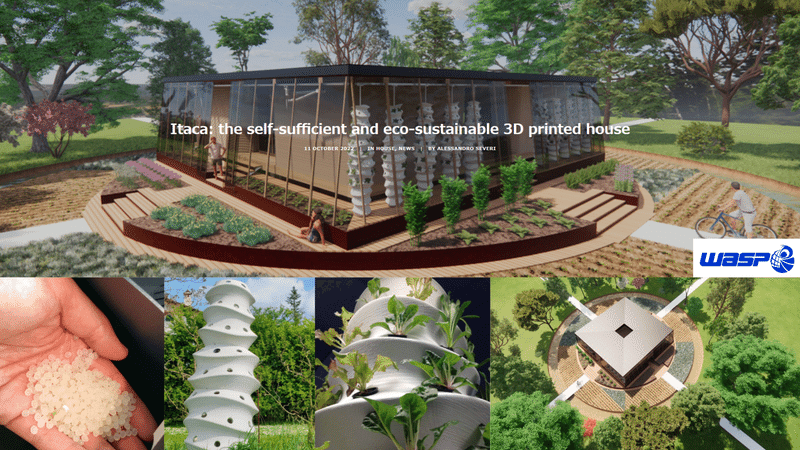
mySDG編集部:3Dプリンターで建てた住居は、従来の住居と比べて建築現場の労働者の人数や、使用する材料に大きな違いがあるとか。
中野さん:そうですね。2023年度の「四角い家」を建てる最新プロジェクトはその2つの省エネメリットを取り込んだ上、自給自足をテーマにしているんです。家の周りに家庭菜園を造り、かつ白いタワー状のプラントの中で野菜の栽培ができるようになっています。プラントは高さがある造形物なので実際に植物を植えて成長テストをし、クリアしたものを採用してます。
菜園とプラントを組み合わせて大人4人分の食材を自給自足できるように設計されており、食料問題をコンセプトにしたボローニャ州と進めている一大プロジェクトなんです。
mySDG編集部:さまざまな問題に取り組んだプロジェクトなんですね。省エネのメリットも詳しく教えて下さい。
中野さん:3Dプリンター建築には「基本的な省エネのメリット」が2つあります。
1つ目は使用する材料です。通常は木材を遠方から運んで使いますが、3Dプリンターの建築材料は現場近くの土を掘って資材に混ぜ込んで使います。遠方からの運送が不要なので省エネルギー化の利点「地産地消」で材料を調達できる。これは最大のメリットです。
2つ目は省人化が可能なこと。建築現場へはトラックのコンテナ、たった1つか2つ分に建築システムを積んで運び入れるんです。2、3人ほどの人数で組み立て可能で、おおよそ3時間ほどでクレーンシステムと呼ばれる建築現場を作り上げることができます。
建築3Dプリンターの稼働も2.3人の監督で十分で、機械で昼夜問わず建築すると先ほどのディオールのハウスは約120時間ほどで建ちます。将来的に省人化が大いに見込まれるシステムだと期待されていますね。
今までの3Dプリンティングのシステムは、大がかりなものが多いんですが、WASP社のものは、2.3人で解体、積み込み、建築作業ができるように設計されているので、家を建てられる3Dプリンティングシステムの中では、手軽に使えるものだと思います。
今回、弊社でこの建築用3DプリンターをWASP社の販売代理店として日本で販売することになりました。
mySDG編集部:日本でも3Dプリンターで家を建てられるんですね。WASP社のシステムは建築場所も選ばない印象なので被災地などにも活用できそうですね。
中野さん:ええ。COVID-19がきっかけで技術の発展があり、ここ2、3年で病棟や住宅を建築するプロジェクトの進行が目覚ましく、被災地への利用も期待値が高いと思いますね。中国ではCOVID-19専用の救急病棟を建てるために3Dプリンティングで病棟を建築していますし、被災地ではプレハブの代わりに使いたいと考える人は多くいると思います。
■金属・リサイクル・未来をサステナブルに造形する3Dプリント
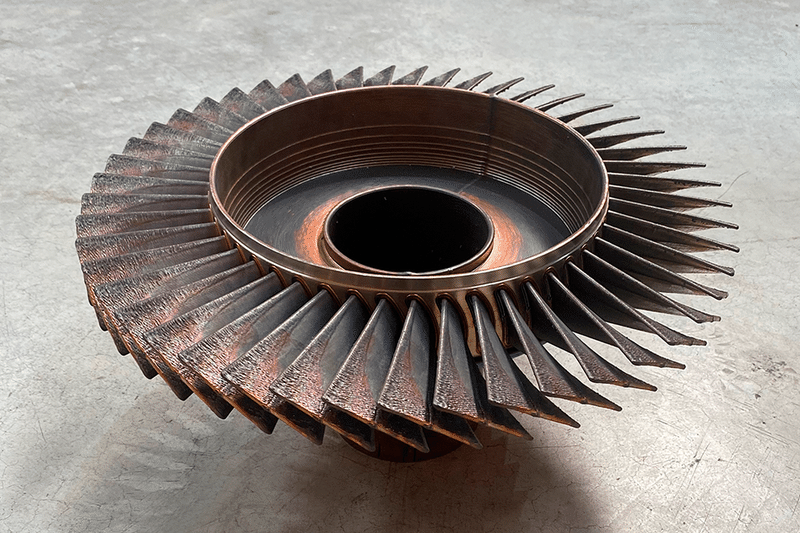
mySDG編集部:現在取り扱う製品ではどのようなものが多いのですか?
中野さん:今は金属にかなり引き合いがあり、特に大型の造形にお問い合わせが集まります。3Dプリンティングは臨機応変さと柔軟性があるシステムなので、金属部品を一品から手に入れることが可能で、最小ロットがないのがメリットなんです。
一般の方には印象にないと思いますが、非常に大きいもの、例えば直径60センチほどの金属製のタービンの羽根なども作れるんですよ。
mySDG編集部:強度はどれくらいあるものなのですか?
中野さん:ワイヤーDEDと呼ばれるシステムは鍛造品に近い、しっかりとした部品が作れます。10年前に3Dプリンティングが盛り上がった当時は、縦方向に弱い印象があったのですが、今は技術の進歩によって樹脂も金属もかなり頑丈に作れるようになりました。
mySDG編集部:通常であれば工場で作るような製品ですよね。
中野さん:そうですね。通常は金属をとかして成形する「鋳造」という作り方が主流で、中国での生産が主です。
それを船で運んで輸入しているのですが、最近アメリカでは国内生産に戻す動きが出ていて、金属製品の成型に3Dプリンティングを使いたいという要望があります。
mySDG編集部:SDGsの観点からお話をすると、金属の製品を海外から船で運ぶだけでCO2の排出をしてしまうので、3Dプリンターを使い消費する土地で作ればCO2排出量の削減になりますよね。
中野さん:ええ。3Dプリンターは地産地消で使われるのが基本なので、3Dデータはメールで遠隔地に送り、消費する現地で物を製造して使う。こうした地産地消の考えを日本国内で広めていきたいですね。
mySDG編集部:ちなみに海洋プラスチックなどのリサイクル素材を使う場合、金属に比べて難しいんでしょうか?
中野さん:一般的にリサイクル素材はちょっと難しいんですよね。
弊社でも過去に「海洋プラスチックを使用したスマホケース」を作るというプロジェクトがありまして、沖縄の海に捨てられたペットボトルをボランティアの方に回収いただいき、
弊社にて3Dプリントの材料にしたんですが、回収物には出所不明の海外製のものなど、あらゆる種類のプラスティックが混在していて、分別作業がとても難しかったんです。
SDGsにも関連深いリサイクル案件も多いのですが、素材に混ざり物があると造形品質が一様にならず、製品の品質保持が困難ですね。現在、品質向上を目指しつつ、ご期待に添えるよう開発を行っている最中です。
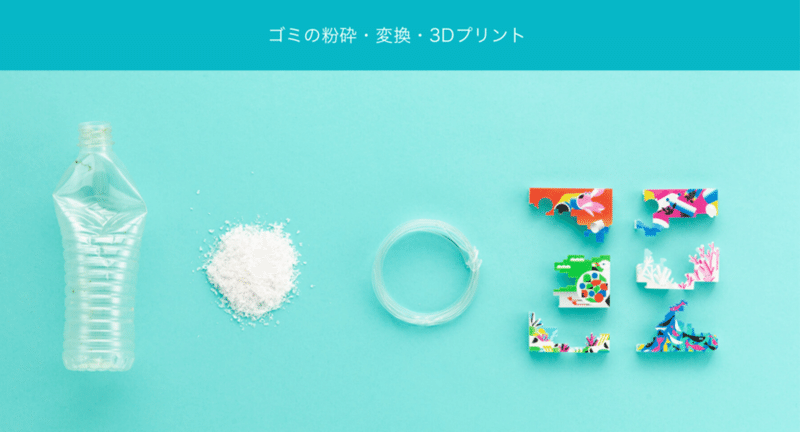
mySDG編集部:3Dプリンターを活用した将来の展望や目標を教えて下さい。
中野さん:3Dプリンターのシステムはとても進歩が早く、去年には無かった技術が今年は知名度を得て使用されています。
現在の一つの成功例は航空宇宙の分野でして、スペースXはすでに、ロケット部品に3Dプリンターを活用し、次々と宇宙へ打ち上げています。ロケットを丸々一台3Dプリントで作る会社もありますし、非常に開発が進んでますよね。今後は開発を進めて適用できる場所をあらゆる業界で探し、新たな3Dプリンティングの可能性を見つけ出していくことが必要だと思います。
私たちの会社は世界と比べても最新の3Dプリンターを取り入れてますので、体験・体感はもちろん、3Dプリンターの情報通の弊社になんでもお聞きいただけるとうれしいです。将来は3Dプリンティングで何でも作れるこの業界の第一人者になりたいですね。
この取り組みが参考になりましたら、ぜひいいね・シェア拡散で応援をお願いいたします🙌
mySDGへの取材依頼・お問い合わせは mysdg.media@bajji.life までお気軽にご連絡ください。
この記事が気に入ったらサポートをしてみませんか?