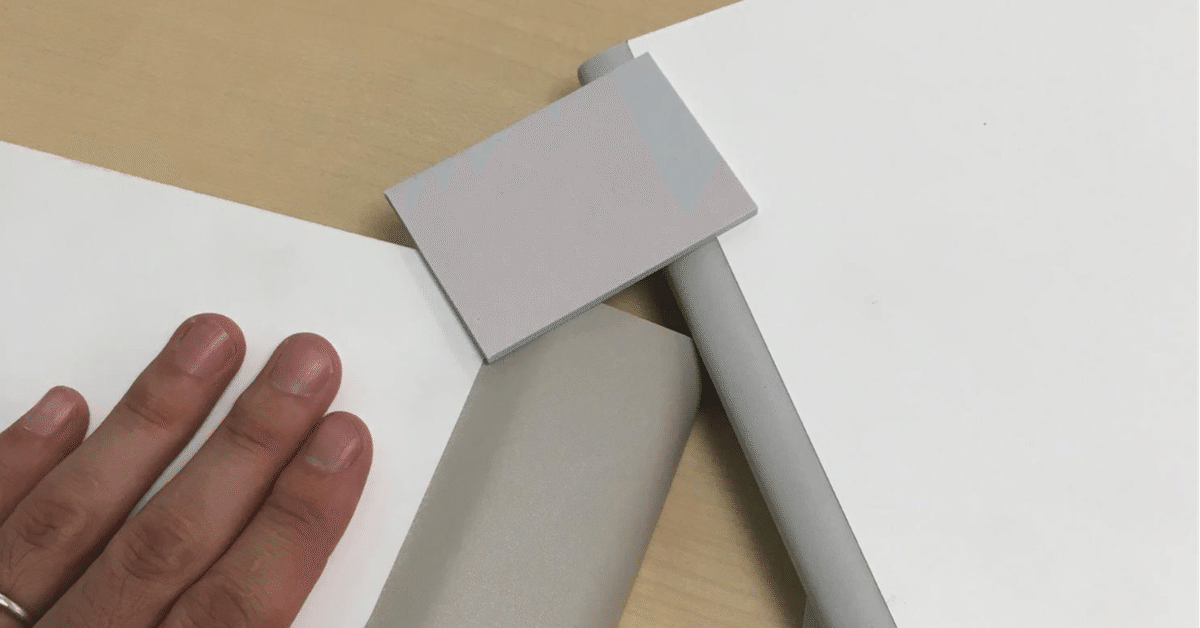
ideaboard® 開発ストーリー連載 #7_ものづくり編2 |形の実現に向けた製造課題へのアプローチ
この連載では、中西金属工業株式会社(以下、NKC)が、2019年に発売した新しいホワイトボード『ideaboard®(アイデアボード®)』の開発に関わったプロジェクトメンバーから広く話を聞き、ideaboardが世に生み出されるまでのストーリーを記録します。
〈過去の記事〉
ideaboard® 開発ストーリー連載 #1_発想編 | アイデアの種を育て続ける
ideaboard® 開発ストーリー連載 #2_デザイン開発編 | プロトタイピングと仮説の更新
ideaboard® 開発ストーリー連載 #3_デザイン開発編 | デザイン事務所 f/p design との協業
ideaboard® 開発ストーリー連載 #4_知的財産戦略編 |デザイナーの新たな収益モデルを考える
ideaboard® 開発ストーリー連載 #5_モニターテスト編 |更新した仮説の検証
ideaboard® 開発ストーリー連載 #6_ものづくり編 |トキハ産業株式会社との協業
第7回目となる今回も、引き続き、NKC 社長付 戦略デザイン事業開発室 KAIMEN 室長の長﨑 陸さんにお話を伺います。シンプルな形状が故に、複雑な製造要件のバランスを満たす必要のあるideaboard。トキハ産業株式会社、f/p design、NKCの3社で取り組んだ製造課題解決へのアプローチについてお聞きします。
長﨑 陸 / Riku Nagasaki
中西金属工業株式会社 社長付 戦略デザイン事業開発室 KAIMEN
NKC BUSINESS DESIGN CENTER
1. シンプルな形状の中で、複雑に影響し合う材料の選定
ーideaboardの形が決まっていよいよ製造にあたり、まずは何から取り掛かったんでしょうか?
アイデアが形として決まって、次はそれを実現するための中の芯材をどうしようかという話になっていきました。例えばハニカムボードみたいなものを使うのか、プラスティックダンボールを使うのか、発泡スチロールを使うのか。中の構造材によって、重さや、反りやすさ、耐久性も全部変わってくるので。
形は決まっているけど、材料は決まっていないという段階ですね。手探り状態です。それをf/p design(以下 f/p)さんと一緒に探して、大阪のスタジオにサンプルを全部並べて比較をしました。
面材も、いわゆるホワイトボード用のシートを使うのか、何か塗装で済ませるのか、マグネットが貼りつくようにするのかしないのかも決まっていませんでした。外側の面材と、内側の芯材の組み合わせを全て考えると膨大なことになるんですね。それを実際に体感しながらテストするために、材を試作品として買って実際に持ったりしながら検討していました。実際持ってみたら、補強しても使えないほどたわんでしまうものがあったり、1人で持つにはかなり重かったり。それぞれの材で厚みの差もあったり。その時は全く先が見えなくてかなり暗中模索の状態でした。
ー選定にあたり、どのような点を重視して選んでいきましたか?
1枚の板なので使っているうちに反ってしまうことがまず課題。前職のKYOTO Design Labで使っていた、周囲にアルミフレームをつけたものでさえ反っていたんです。壁に立てかけた時に、長手方向に対しての反りもあれば、ねじれという反りもあったりして。アルミフレームで周りを補強したとしても反ってしまうなら、ますます面材も、内側の芯材も、しっかりしたものにする必要があるな、ということは考えていました。
均質な材を切り出して、それに面材を貼り合わせてつくるという方法にちょっと自信がなくなってきた時期もあったんですよね。どうしても重くなるし、反ってしまう。例えばカーボンの角材を使って、ロの字型の枠に筋交いを入れたフレームを作って、それにシートを張れば軽いのができるんじゃないか、みたいなことも検討していましたね。ただすごく高くつきそうだなとか。
ー面材、芯材の選定にあたり、重さ・反り以外に考慮したことはありますか?
シートを貼って、ホワイトボード用のフィルムをシートの上から貼るのか、芯材に直接ホワイトボード用のフィルムを貼るのかという議論もありました。内側がダンボール材だと、中の波型の凸凹が、ホワイトボード用フィルムの表面に浮いてきてしまう。一般的なホワイトボードもある程度は波打っているし、そこまで突き詰めた平滑性はいらないんですが、そこはできるだけクオリティを高めたいなと。f/pさんとしても、自分たちのアウトプットのレベルには持っていきたい、という感じで。
だから、その段階で決まっていたのは、まずクオリティとしてはベストを目指そうということ。ただし一応Bプラン、Cプランも、作っておこうという感じで検討は広く進めていました。
ー重さ、反り、見た目の品質。材料を決めるという製造の初期段階の時点で、満たすべき要件がたくさんありますね。
ほんとに一番苦労したところだと思います。そういう意味でideaboardはすごくデリケートなバランスで保たれているんです。面材は面材でのいろんなチョイスがあり、その材料同士の貼り合わせやすさがある。どんな接着剤が効くか効かないかということがある。フチのウレタンの材料も何種類かあって、それと芯材を一体成型するときの相性の良さ、悪さがある。
面材と芯材とウレタンというすごく難しい材料が3つあって、どれかを立てるとどれかが立たないし、全部を良くしようと思うと全部まとめて重くなる。これはもう検討を重ねていく中で、最終的にすごくデリケートなバランスでうまく成り立った、という感じです。
ーそのデリケートなバランスの良し悪しは、どのように判断していったのですか?
それは常に人、使い手であるユーザーです。ideaboardのことを一切知らない人が、オフィスで一枚の白い板を持たされたときに、「重い!」と感じるのか、「まあ持てる」と感じるのか。「超軽い!」で成立することはもうその時点では考えていませんでした。持ってみたときの「あれ?思ったより軽い!」というところが、数値でいくと3kgなのか、4kgなのか、4.9kgなのか5.2kgなのか。トキハ産業さんのありがたいところで、試作品ができたら毎回持ってきてくださっていたんですね。それをみんなで持ってみて「う、重い」とか、「これはいけそう。でも反りますね」とか。試作品を常に人が持ってみて、その人が感じる印象を大事にしていました。
ー実際の大きさ、実際の材の組み合わせで持ってみるってことですよね?となるととても多く作らないといけないのでは?
そうですね。トキハ産業さんも、普段なら大手から「これをこの仕様で収めてください。」と受注するケースが多いと思うので、安心して進められると思うんです。
でも、ideaboardはBtoCの商材に近いものなので、作ったからといって誰がどこで売るのかもわからない。ある意味トキハさんからしたら、今ideaboardに費やしてる人的・開発リソースは、例え営業であったとしても、無駄にもなりかねない。そういう意味で、どこまで入り込んでくださるのかは、正直わからなかったんです。僕たちとしても絶対作りきりたいけど、作りきれるかどうかはわからないんですよ。
だから毎回、試作品を作ってもらうたびに、本当に感謝という感じで。もちろん普通にビジネスとしての試作費用というものはあったんですけど、ただ、それを超える検討をしてくださっていたと思います。
2. 白いウレタンへのこだわりと、白だから生まれる多くの課題
ー面材、芯材の組み合わせに加えて、周囲を囲むウレタンについても検討に時間をかけたそうですね。
前回モニターテストの視点からお話した白いフチか黒いフチかの問題ですね。
最初はとにかく薄くて軽い、シンプルで、一枚のツヤッとした薄い豆腐みたいなものを思っていて。よりシンプルで、プリミティブなものにしようと。
そういう意味で、まず表面材のメラミンの白色。これは変えられるけど変えるためには大きな投資が必要なので、白色で決まってしまっている。じゃあ、周囲を囲むウレタンのほうも白がいい。ただ同じ白と言っても、定義によっては百種類、千種類もある。同じ白色に近づけるための、プロダクトデザイン、インダストリアルデザインの中では色合わせ、色決めという大事なステップです。
この案件では、コスト的に現実的で、且つトキハ産業が扱える白というのは限られていました。
ひとつは比較的安価で、色も調整しやすい軟質ウレタンという材料。これは、昔の古いパソコンが窓際に置かれてだんだん黄色くなるような、黄変が起きやすい。最初は色合わせもしやすくて安くできるけど、使ってるうちにフチだけ黄変してしまうのはよくないなと。もうひとつは無黄変の硬質ウレタン。少しコストが上がるし、製造時に温度をかなり上げる必要があり、芯材などの他の材料が変質するリスクが高まる。どちらにしても、うーん、どうしようと。
その時は作ってみて考える、ということで作ってもらって、使ってみて。そうすると、白ってやっぱり汚れるんですよね。ウレタンってパッと見たら表面が滑らかで艶もあるので、ホワイトボードぽく使えると思ってたんですよ。でも実際は、表面にものすごく細かい穴があって、使っていくうちに、最初は消ても段々、その穴にインクが入り込んで黒ずんでいってしまう。思ったよりも汚れてしまうってことが見えてきたんです。それで、当初から黒フチもあるかもなという話は出ていたので、白と黒どちらも作ってモニターテストした結果、ユーザーが扱いやすいのは完全に黒の方だったんですね。
黒にしたら黄変しても問題ない。もちろんいい黒を選ぶ必要はあるけど、表面材の白との色合わせをする必要もなくなる。白に執着することで生まれたいろんな課題が、黒にすることで全部解決できて、なおかつユーザーにとっての扱いやすさ、置きやすさといういい機能も加わった。これはとても苦労したんですけど、すごくいいかたちで課題解決された場面だったと思います。
3. 型成形の制約の中で保持する品質とコストのバランス
ーものづくりの観点で、他に印象に残っている検討事項などはありますか?
型成形するときは、どこから樹脂を注入するか。注入された樹脂の代わりにどこから空気を抜くか。
さらに、中身が取り出すために型はどこかで分割する必要があるので、どこで分割するか。このあたりはどんな型成形でも必ず大事になってくるんです。
なぜかというと、注型をする穴、空気を抜く穴、型の分割線というのは必ず跡が出て、それはそのまま外見品質に影響してしまうし、後加工で人の手がかかり、コストに直結することになる。
だから、どこに目立たないように最低限の穴を開け、どこにパーティングラインを入れ、人の手で後加工をしないといけないことも含めて、いろんな要素を天秤にかけながら決めていくんです。
さらにその樹脂型の中に、材料をセットする時には、完全機械化されている作業ではないので、どうしても人の手による誤差が出てしまう。それによってウレタン注型の身幅にも多少誤差が出てくるんですね。じゃあそれを1mm許すのか、0.5mm許すのか、いや2mmでも許せるのか、という判断が必要になる。
外見品質・性能品質と、コスト、型成形の制約というバランスをどう決めるかというところはなかなか難しく、大変でした。
あとは、内部の発泡剤の材料確保も苦労しましたね。発泡剤は、使われている業界的には厚みの誤差に対してあまり執着がない。1mm以上誤差が出ても問題ない現場で使われていることが多い材料なんです。でもideaboardは1mmも差が出ると大変。型成形なんかは1mm隙間があると、たちまち樹脂が漏れ出して一発で不良品になります。だからideaboardで許容する厚み誤差は、発泡剤が使われている業界ではありえないくらい小さな誤差です。いつも使ってくれる業界よりはるかに小さな納品量で、はるかに小さな誤差しか許容しない。だから、材料の提供元からはけっこう断られました。
最終的には、トキハ産業さんの業界の中での、会社として、人間としての信頼関係の中で、かなり離れたところまで直接足を運んでもらったりして材料供給をなんとか取り付けていただきました。
ものづくりの段階では、f/pさんとトキハ産業さんに多大なる力をお貸しいただいて、僕自身はもうなんか恐縮してちっちゃく消えそうな感じでしたね(笑)。
次回 ideaboard 開発ストーリー連載_#8 へ続く
(取材・文 / (株)NINI 西濱 萌根, 撮影 / 其田 有輝也)
▼Click below to see the English version / 英字版はこちら
この記事が気に入ったらサポートをしてみませんか?