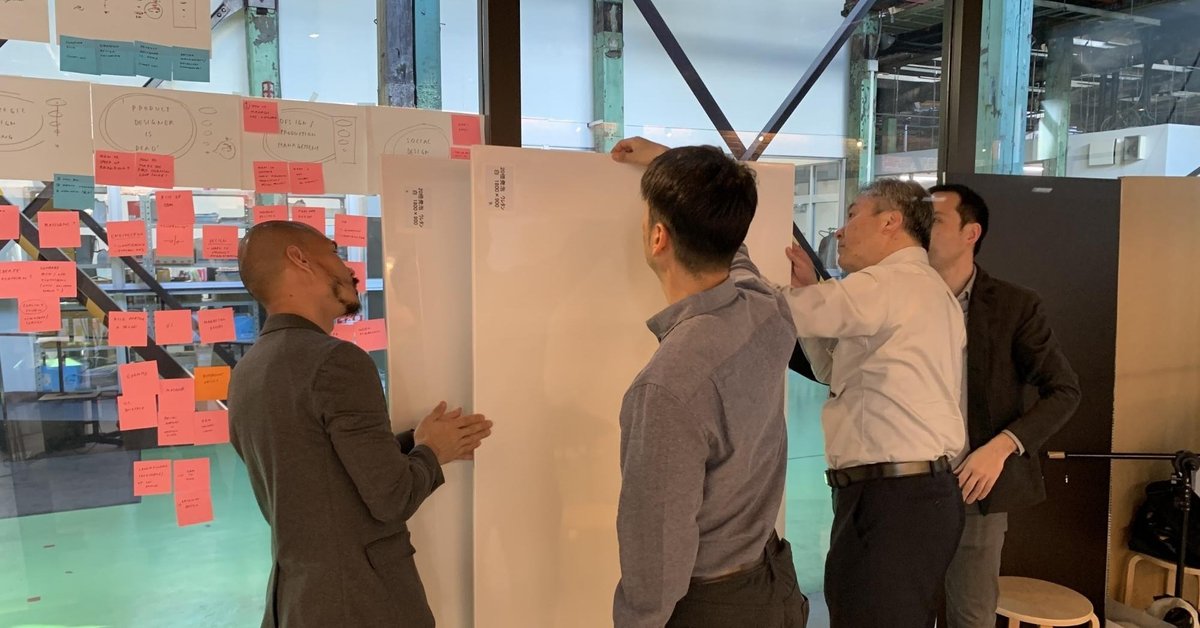
ideaboard® 開発ストーリー連載 #6_ものづくり編 |トキハ産業株式会社との協業
この連載では、中西金属工業株式会社(以下、NKC)が、2019年に発売した新しいホワイトボード『ideaboard®(アイデアボード®)』の開発に関わったプロジェクトメンバーから広く話を聞き、ideaboardが世に生み出されるまでのストーリーを記録します。
〈過去の記事〉
ideaboard® 開発ストーリー連載 #1_発想編 | アイデアの種を育て続ける
ideaboard® 開発ストーリー連載 #2_デザイン開発編 | プロトタイピングと仮説の更新
ideaboard® 開発ストーリー連載 #3_デザイン開発編 | デザイン事務所 f/p design との協業
ideaboard® 開発ストーリー連載 #4_知的財産戦略編 |デザイナーの新たな収益モデルを考える
ideaboard® 開発ストーリー連載 #5_モニターテスト編 |更新した仮説の検証
第6回目となる今回は、引き続き、NKC 社長付 戦略デザイン事業開発室 KAIMEN 室長の長﨑 陸さんに、ideaboardのシンプルさを一体成型で実現できる製造会社探し、そしてトキハ産業株式会社との出会いについてお聞きします。
長﨑 陸 / Riku Nagasaki
中西金属工業株式会社 社長付 戦略デザイン事業開発室 KAIMEN
NKC BUSINESS DESIGN CENTER
1.ideaboard最大の課題は一体成型の実現
ーまずはどのように製造工程の調整に入っていったかを聞かせてください。
ものづくりに関して、僕の方ではどこに頼めばいいのか皆目見当がつかなかったので、f/p design(以下 f/p)さんにすごく力を貸していただきました。f/pさんとすでにお付き合いがある企業とも連絡を取っていただいたし、デスクトップリサーチとかで全く新規の協業先も提案してくださいましたね。
その中で出てきたのが、トキハ産業株式会社(以下 トキハ産業)さんです。f/pさんともそれまで取引はなかったんですけど、一度、話を聞きに行ったらいいんじゃないかと。飛び込みに近い感じだったと思います。
他にもメールベースで問い合わせをした企業はいくつかあったかもしれないけど、結果的に、直接伺ったのはトキハ産業さんだけです。
ー具体的にどういった視点で、協業先を探していたんでしょうか。
プロトタイプを作っている段階で、f/pさんと僕たちの間で、この一体成型ってどうすればできるのか、みたいな議論がありました。この大きさのものを、そもそも一体成型で実現できるのか誰もわからない。
手の平サイズの樹脂成型みたいなものであれば金型もそこまで大きくはない。それでもやっぱり型の投資費用は数百万、一千万円以上かかってしまうんです。それがideaboardのようなサブロク板サイズになってくると、おそらくさらに桁が変わってくるなと。
今世の中にないアイデアを新しく創るためにしては、その投資はリスクが大きすぎるし、クラウドファンディングでどうにかなるレベルの金額でもない。その問題をまず解決しないといけないということが大きかったですね。
ーそれがトキハ産業ならできそうだと。
f/pさんがそういう課題も踏まえていろいろ見てくれて。トキハ産業さんの強みのひとつは、樹脂型を用いた一体成型なんですね。テーマパーク、介護福祉施設、幼稚園とかそういう場所で、不特定多数の人が安全に触れられるものを製造しているんです。例えば、周囲がウレタンの土手で盛り上がっているテーブル。介護施設で熱々のお味噌汁をテーブル上でこぼしても、テーブルから膝にかかって火傷することがない。土手の形は丸みを帯びているので手で触っても、肘が当たっても怪我しにくい。
トキハ産業さんがすごいのが、そのウレタン土手も含めて、テーブル材と一緒に成型してしまうんですね。接着剤を使って別パーツを貼りつけているわけではない。だからこそ耐久性が高く、掃除やメンテナンスがしやすい。そういう点に対して独自の技術を持っている会社です。ということは、ideaboardのウレタンや軟質素材の一体成型も実現できるんじゃないかと、コンタクトしてみたという感じです。
ー初めてトキハ産業さんに話しに行った時、どういった反応でしたか?
f/pさんと一緒に、兵庫県朝来市にあるトキハ産業さんの工場にお邪魔して、現場を見せていただきました。
あらかじめNDAを結んだ上で情報をお渡ししたんですけど、「結構チャレンジングやなー」って感じでした(笑)。やっぱりウレタンの厚みが、普通よりかなり薄いんですよね。さらに板面のサイズが大きい。
トキハ産業さんとしては「どう作る?」「ここはもうちょっと分厚くできない?」とか。それに対してこっちも「いや、それは違うんです…。」みたいな感じで、最初はもう、いわゆる”デザイナーの強いこだわり”みたいに見られたかもしれないですね。でも、代表の方やエンジニアの方とか、最初からすごく親身に話を聞いてくれてありがたかったですね。
2. デザイナーとエンジニアの共通思考の実感
ートキハ産業さんとつながり、製造の実現性を一緒に探っていくプロセスはどのように進みますか?
トキハ産業さんも、期間にしたら半年以上ずっと伴走していただいて。物理的にも月1回くらいお会いして、その時の試作品や、材料の組み合わせの可能性とかを一緒に見たりしていました。
最初はとにかく成型。とくに内側の芯材と表面材の組み合わせをどうするかっていうところをトキハ産業さんも一緒に考えてもらうという感じでした。その組み合わせを選ぶプロセスが数ヶ月続きましたね。
ートキハ産業さんのように、技術を持った製造会社が、外部のデザイナーと一緒にものを開発していくというプロセスはあまりないのではないでしょうか。
最近は少なくはないですが、多くもないですね。最初にトキハ産業さんの工場を見に行った時、事務所の一角に過去のたくさんの試作品が置かれているのがチラリと見えたんですよ。ちょっとサンプルで試してみたものや、作ってみてすごく面白かったから参考のために一部だけ切り取って保管されているものたち。たぶん数十個、いや数百個あったんじゃないかな。結局それを見せてもらいながら、話を聞いたりしたんですけど。
要するに、造形や意匠を突き詰めるという意味でのデザインではもちろんないけど、試作を繰り返しながら最も良い有り様を探っていくという姿勢は、そのあたりのデザイナー以上にデザイナーなんですよね。それを見せてもらった時点で、私もf/pさんも「あ、これはいけるかも」みたいな感触はありました。
ー同じ姿勢、同じ思考でやっていけるかもという感触、すごく良いですね。
そうなんですよ。この結構無茶振りに近いアイデアに対して、どうしたら実現できるのかというのを同じ立場ですごく考えてくれました。もちろんプロなので、できない理由というのは合理的にたくさん言えるはずなんです。でも、それは分かったからじゃあどうしよう、というお互いに積み上げていく会話ができていたのでとても良かったなと思います。
あとは、f/pさんというエンジニア出身の人たちがいてくれたのもめちゃくちゃ大きかったですね。お互いに議論するベースとして、素材の変質性や温度の問題みたいな工学的な知識があると「なんでできないんですか??」みたいな水掛け論にならない。やっぱり同じエンジニアとして、トキハ産業さん側と信頼関係がつくれたのは大きいと思います。難しいのも理解できる、それでも私たちは造形を突き詰めたいので再度検討してほしい、ということを話せる雰囲気があったのでありがたかったです。
今振り返ると、三社のミーティングは和気藹々で、なんかゆるい感じ。「そうですよねー、難しいですよねー。」「でもねー。」みたいな。みんな結構ゆるゆると。意外とね(笑)。
次回 ideaboard 開発ストーリー連載_#7 へ続く
(取材・文 / (株)NINI 西濱 萌根, 撮影 / 其田 有輝也)
▼Click below to see the English version / 英字版はこちら