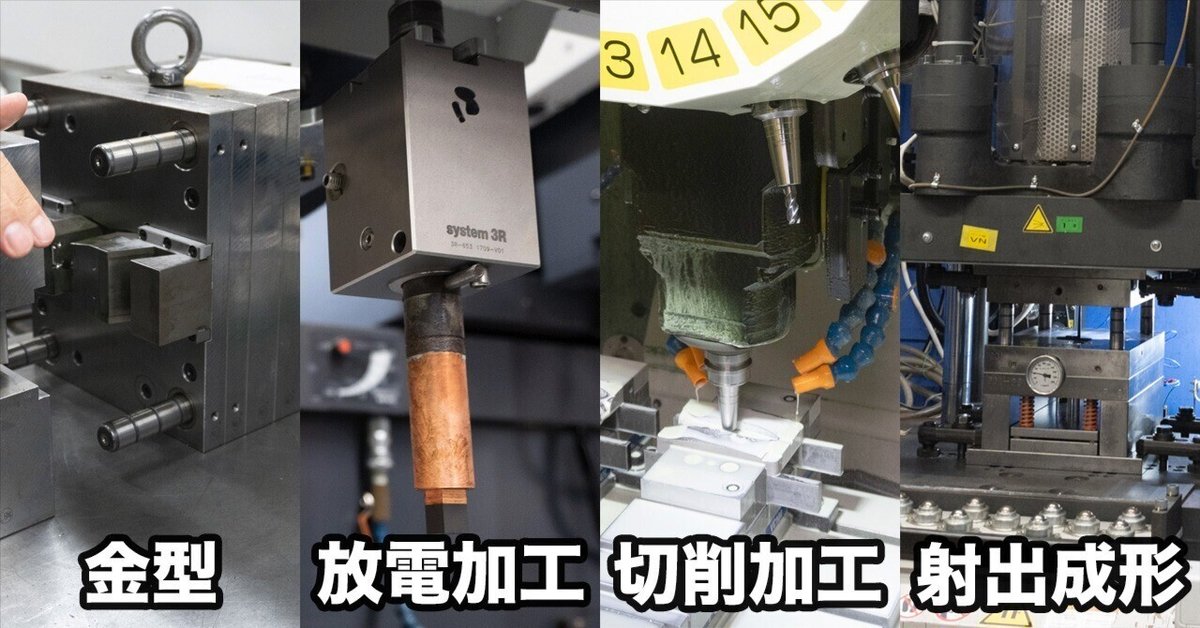
【永久保存版】スタートアップのための金型入門|金型による量産の流れを知ろう
ハードウェアスタートアップが製品を世の中に出す際に、避けては通れない量産。金型を用いた量産は、3Dプリンターなどのラピッドプロトタイピングツールと比較して、触れる機会が少なく、設計や見積もりのイメージが湧かない方も多いのではないでしょうか。
金型がどのようにできるのか、そもそもなぜ高額なのか?そうした疑問に答えるため、金型製造や射出成形、試作部品製作を行う「ミヨシ」に協力いただき、金型の製作から設計時に気をつけるポイントまで、工場見学の様子を交えながら紹介します。
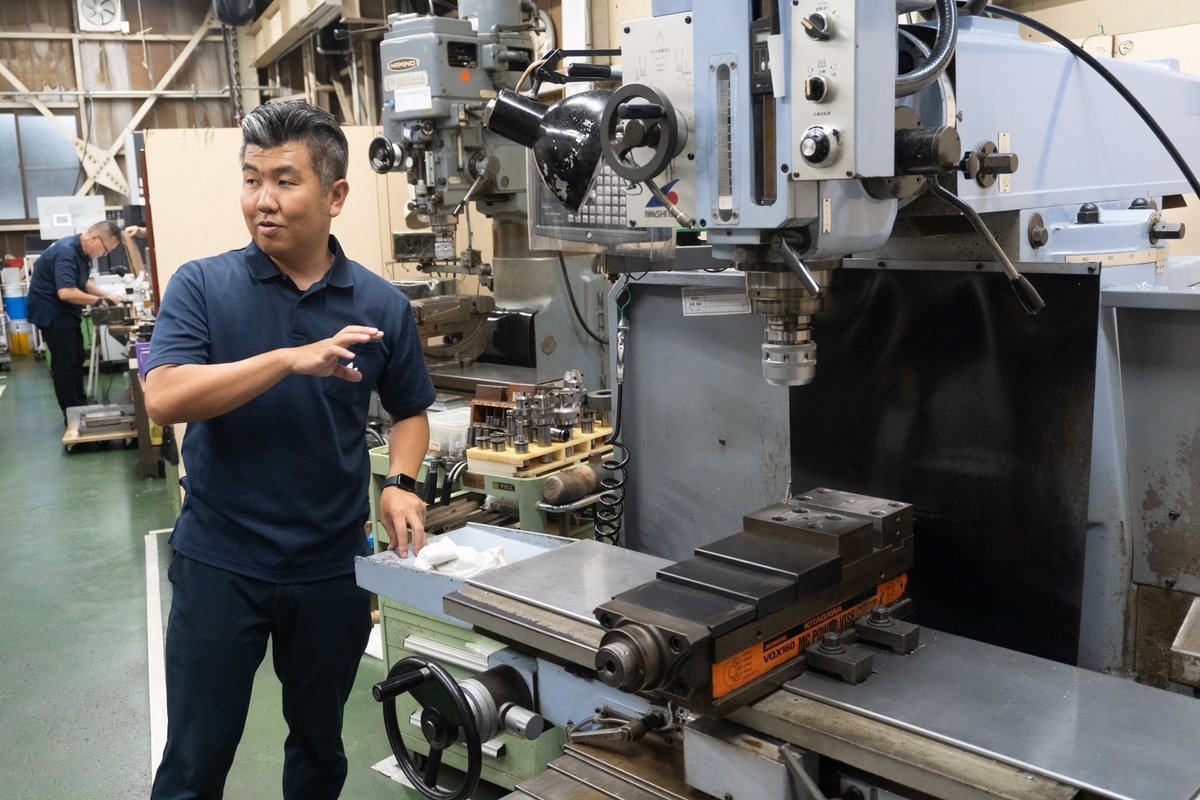
ミヨシ
1982年創業。金属試作品製作、治工具製作、プラスチック射出成形金型製作、射出成形が主な事業。少量生産用のカセット型、アルミ金型でイニシャルを抑えて少量生産を持つ。「捨てられないものづくり、人の役に立つものづくり」という企業理念のもと、近年はスタートアップからの依頼にも多数応じるほか、サスティナブル素材製品の共同開発にも取り組む。
https://www.miyoshi-mf.co.jp/
発注から完成までのリードタイム
金型を発注してから完成までの大まかな流れは、下記のようなものになります。
仕様の打合せ
射出成形に適した製品形状へのすり合わせ
金型設計、部材発注、金型加工
トライ成形(必要に応じて繰り返す)
規定数量の成形
ミヨシで生産する場合、IoT向けの基板が入るような筐体であれば、1,2の間で2週間から3ヶ月ほど。3,4の工程は1ヶ月、5には1〜2週間ほどを見込みます。
相談を行う際には、どのような製品なのか、使用方法(はめあう部品があるか)などの基本的な情報が必要です。
また、生涯生産数やターゲットプライスなど、ビジネスデベロップメント視点での情報も共有いただければ、それに合わせた提案が可能になります。たとえば、大量生産の場合は成形効率重視でランニングコストを抑えた金型を製作しますが、少量生産の場合であれば金型は簡易構造でイニシャルを抑えて製作し、代わりに製品単価は高めになる、といった具合です。
生産側の知見を活かすためにも、相談に持ち込む時点で可能な限り多くの情報を共有すると良いでしょう。
金型の切削から射出成形までの流れ
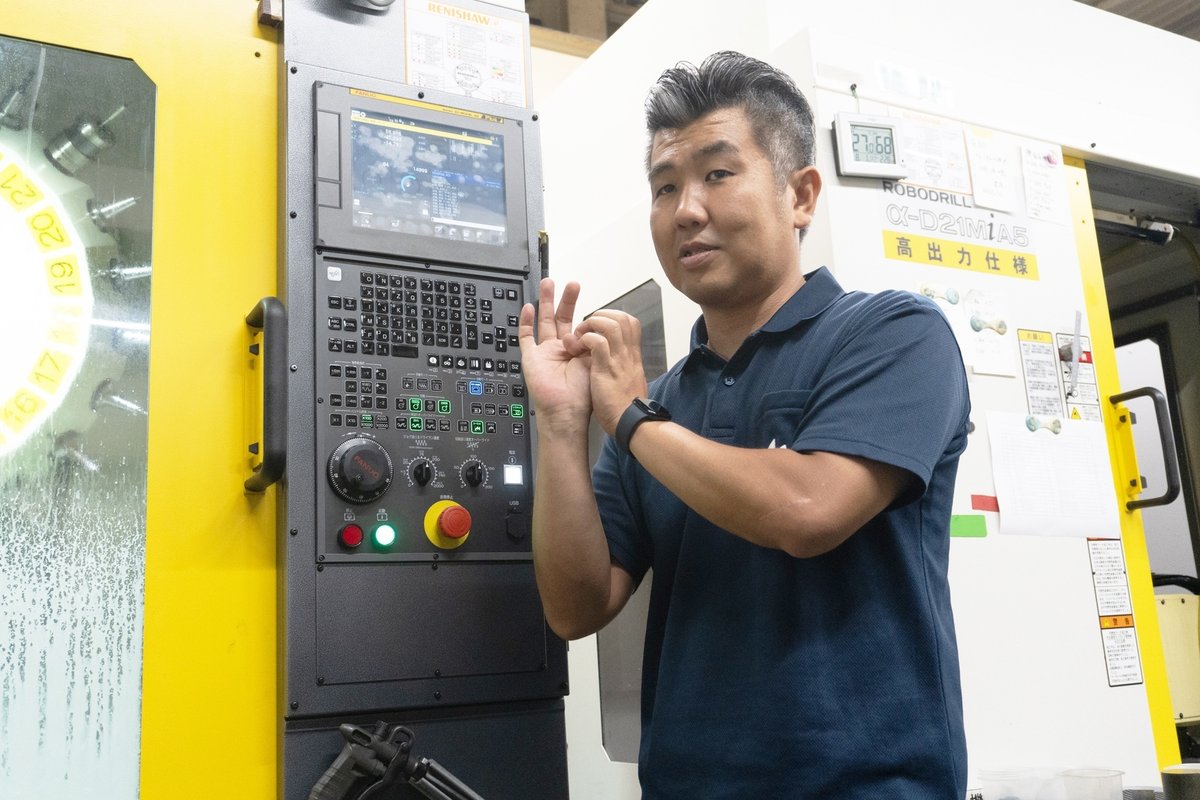
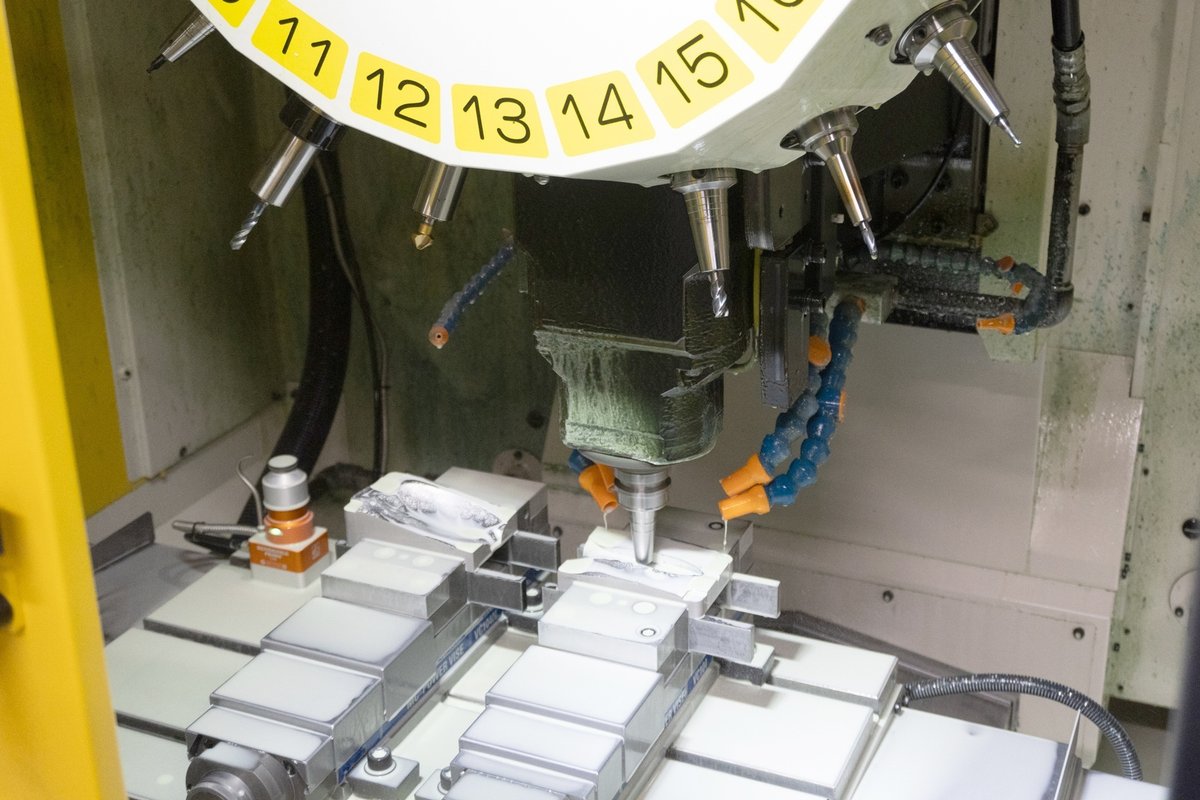
金型を加工する手段の一つである切削加工は、円形の刃物を高速で回転させて金属を削っていく方法です。CAM(Computer Aided Manufacturing)ソフトウェアで刃物の回転速度や移動量などを細かく指定し、G-codeと呼ばれる加工用プログラムに基づいて加工を行います。
CAMデータのクオリティのほか、機材自体の水平や細かなズレの有無、加工エリア内の温度による金属の膨張率の変化といった要因によって、仕上がりの精度が変化します。
ミヨシでは高頻度のメンテナンスはもちろん、震度3以上の地震が起きた場合には工作機械の水平確認ならびに水平だしをするなどをしています。こうした丁寧な管理によって、μ(マイクロ)単位での高精度な加工を可能にしています。
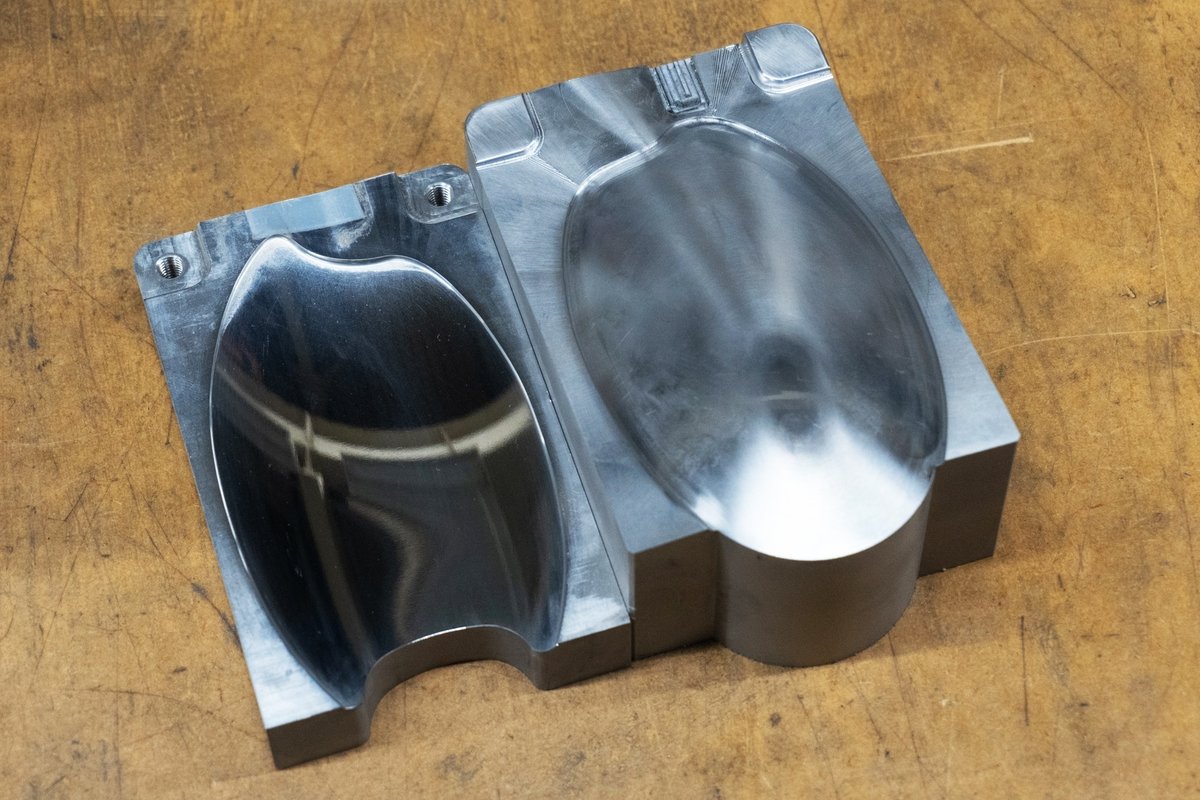
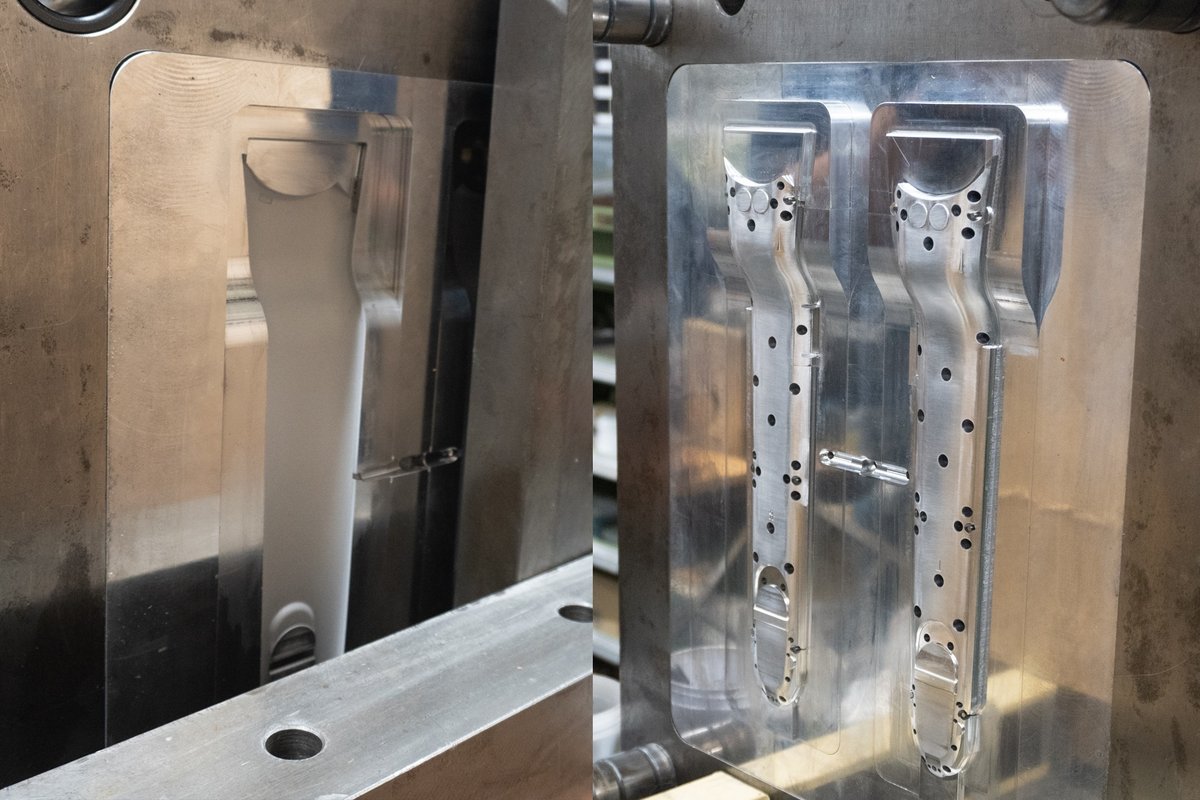
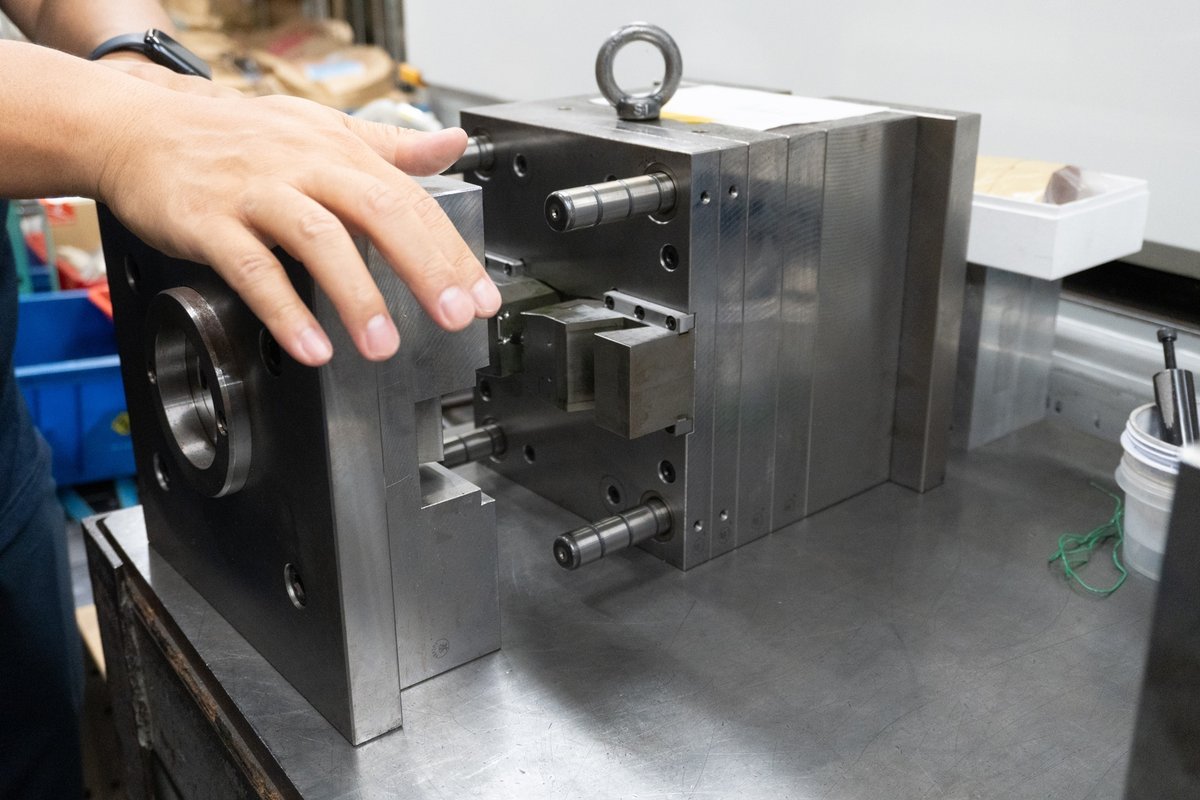
ダイセットと呼ばれる金型の本体(射出成形機に取り付け、製品を押し出す機構が備わっている部材)は材料費だけでも、小さいもので数万円、大きいものだと数十万円かかります。ここに切削した金型を組み合わせていくため、さらに材料費と加工費が重なっていくわけです。
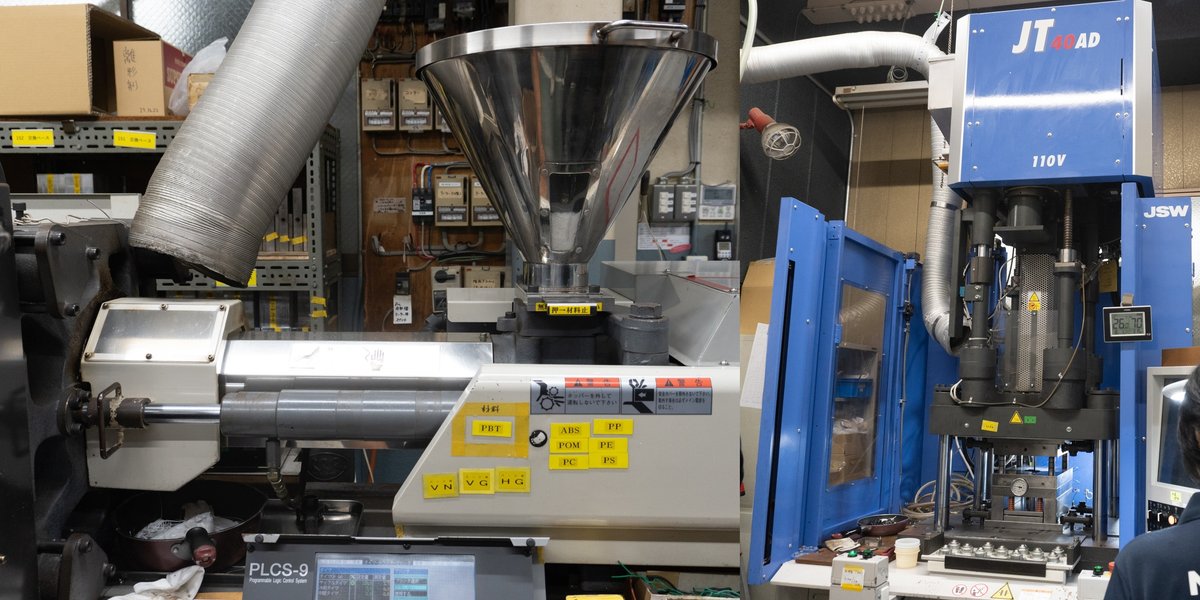
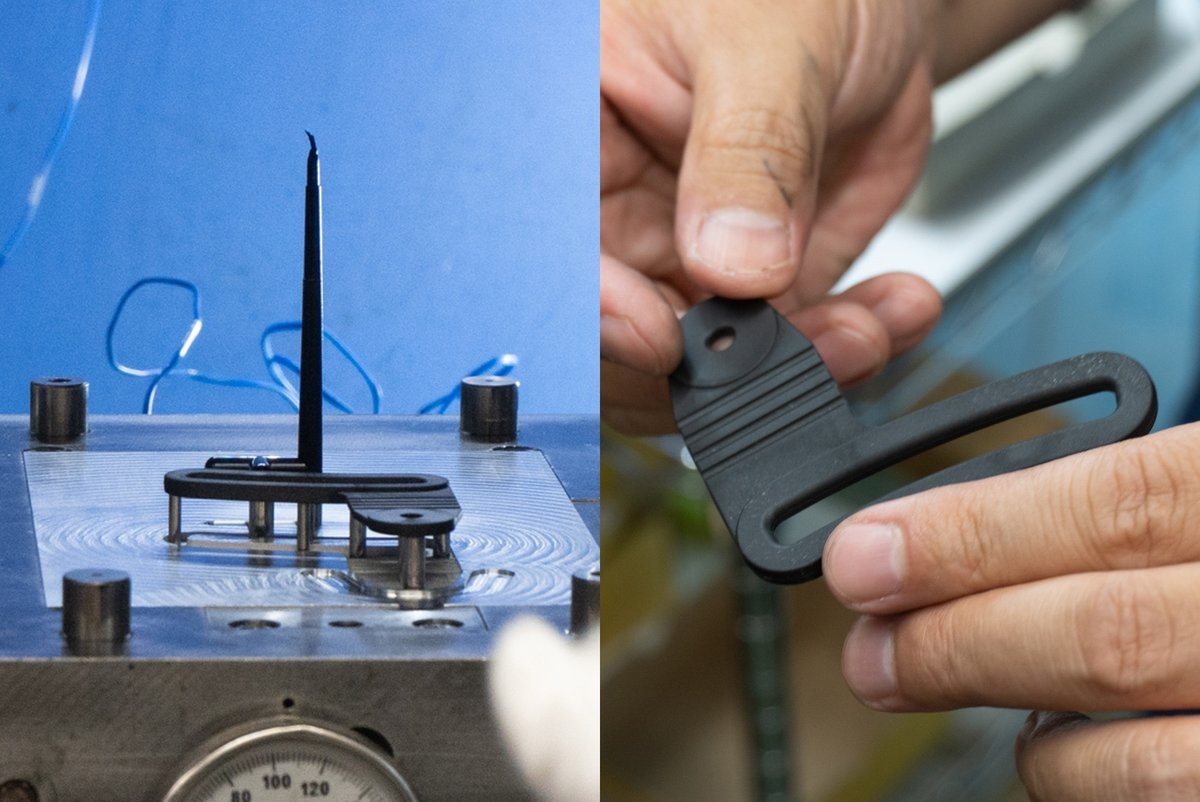
射出成形機は、ペレットと呼ばれる粒状の樹脂を複数のヒーターで溶かし、スクリューで混ぜながら金型に流し込んでいくための機械です。
横向きのものが一般的ですが、成形時にフィルムや端子やナット類などの部材を封入しやすい縦型のものも利用しています。金型に流し込まれた樹脂が専用のピンで型から取り外されることで、1回分の成形部品が手に入ります。
金型の価格はどう決まるのか
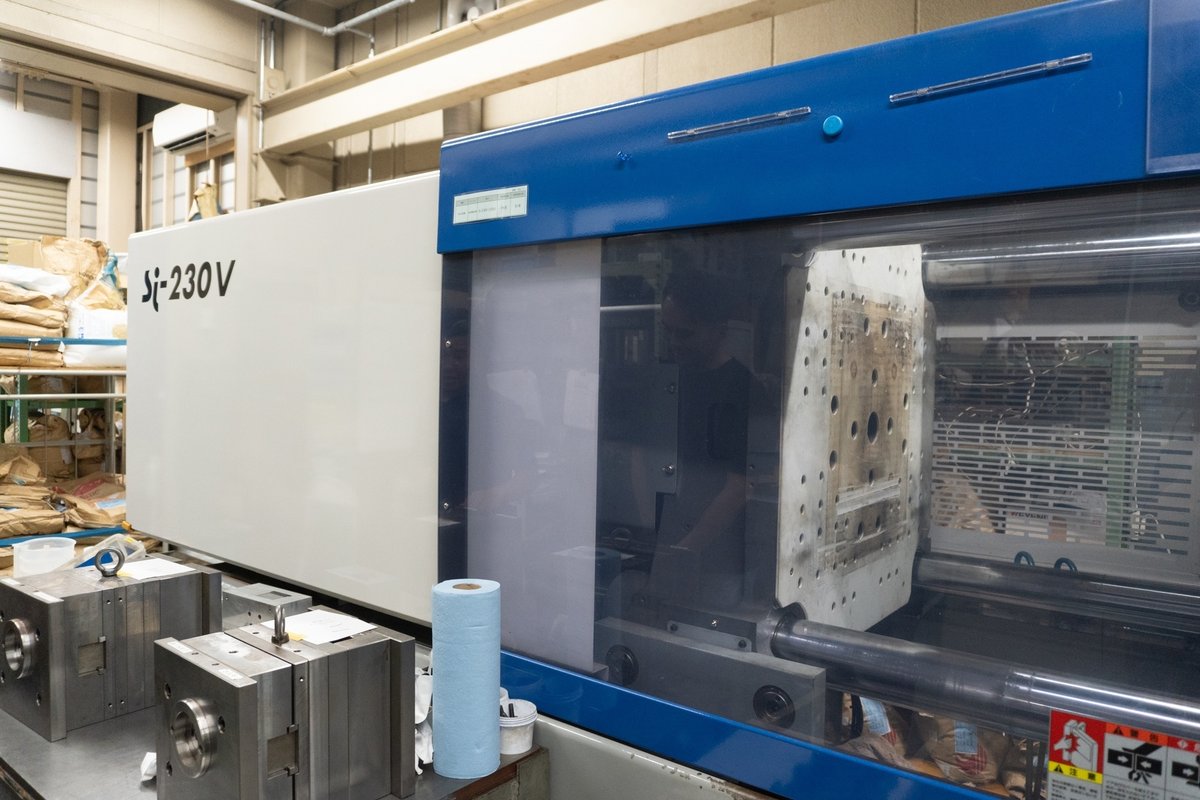
ある程度の数量を成形する金型には高い硬度が必要なため、調質鋼(熱処理を施した鋼材)と呼ばれるHRC※40以上の硬度の鋼材を使用することが多く、加工時間がかかるためその分価格が高くなります。こうした素材のほか、製品の大きさや角の多さによっても金型の費用は変化します。
たとえば、樹脂を押し出す際の圧力はかなり高いため、射出成形機は大きなアーム(トグル機構)で型を押し付け締めています。その力によって型番が分かれており、80トンであれば手のひら程度、230トンであればA4用紙くらいのサイズまでの成形が可能で、大きなものであるほど素材の費用や加工時間がかかり、費用が上乗せされていきます。
※HRC…硬さの単位。「ロックウェル硬さ」とも言う
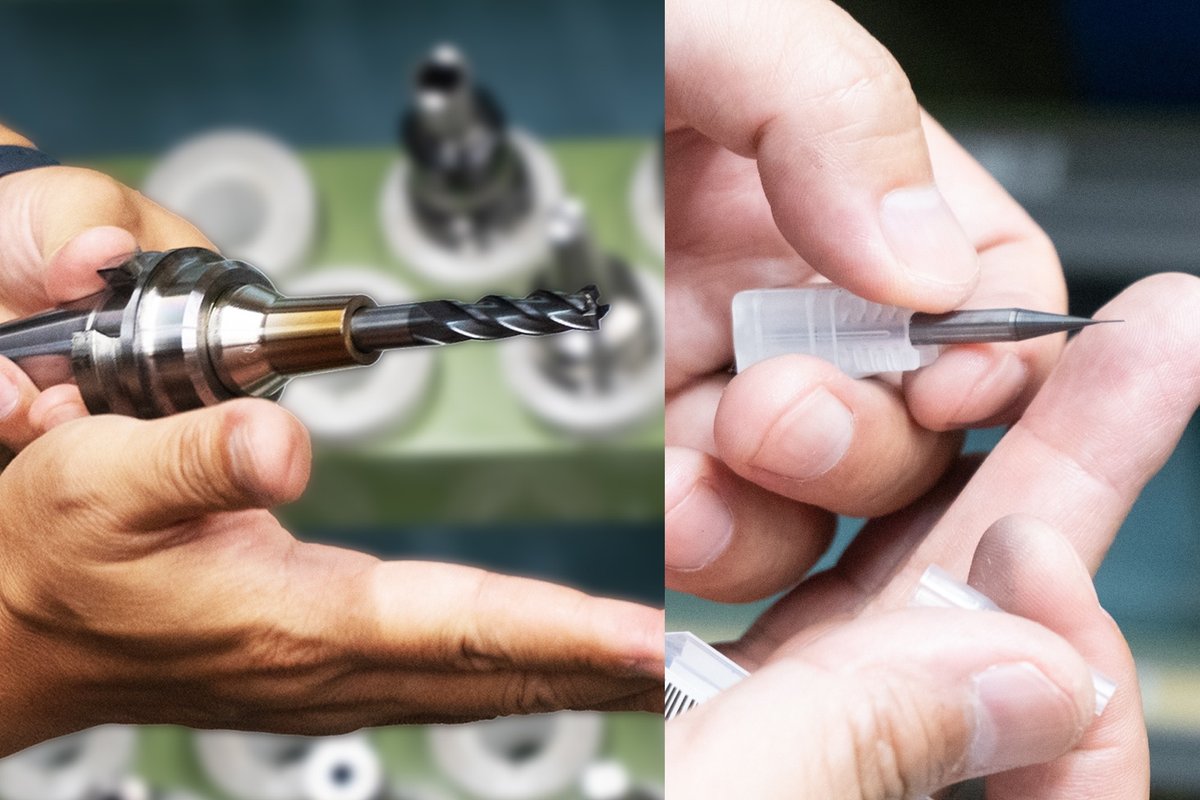
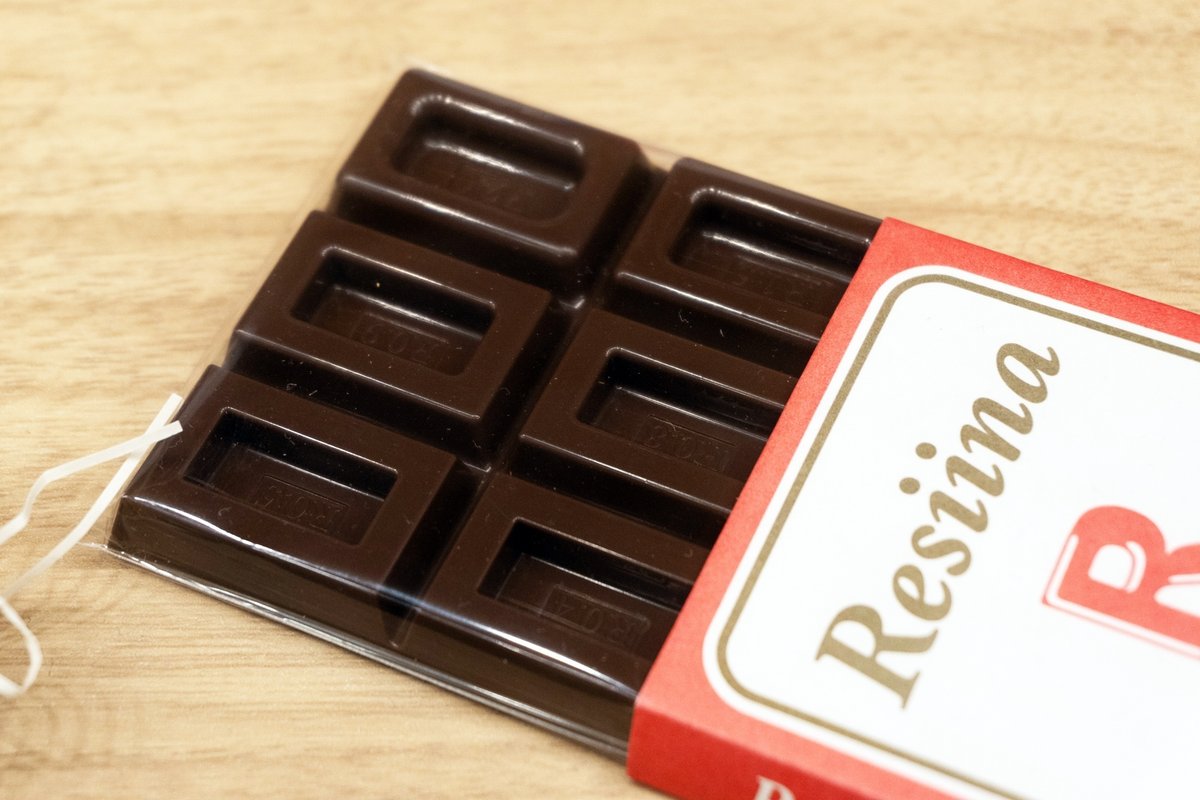
マシニングセンタやフライス盤では円形の刃物を使うため、素材を彫り込むような加工では内側のコーナーに丸みが出ます。どうしても直角を出したい場合には、電極材をスパークさせて部材を溶かしていく、放電加工などの選択肢があります。しかし、真四角の電極材を図面に合わせて作る必要があるため、切削加工よりもコストや工程が多くなることに注意が必要です。
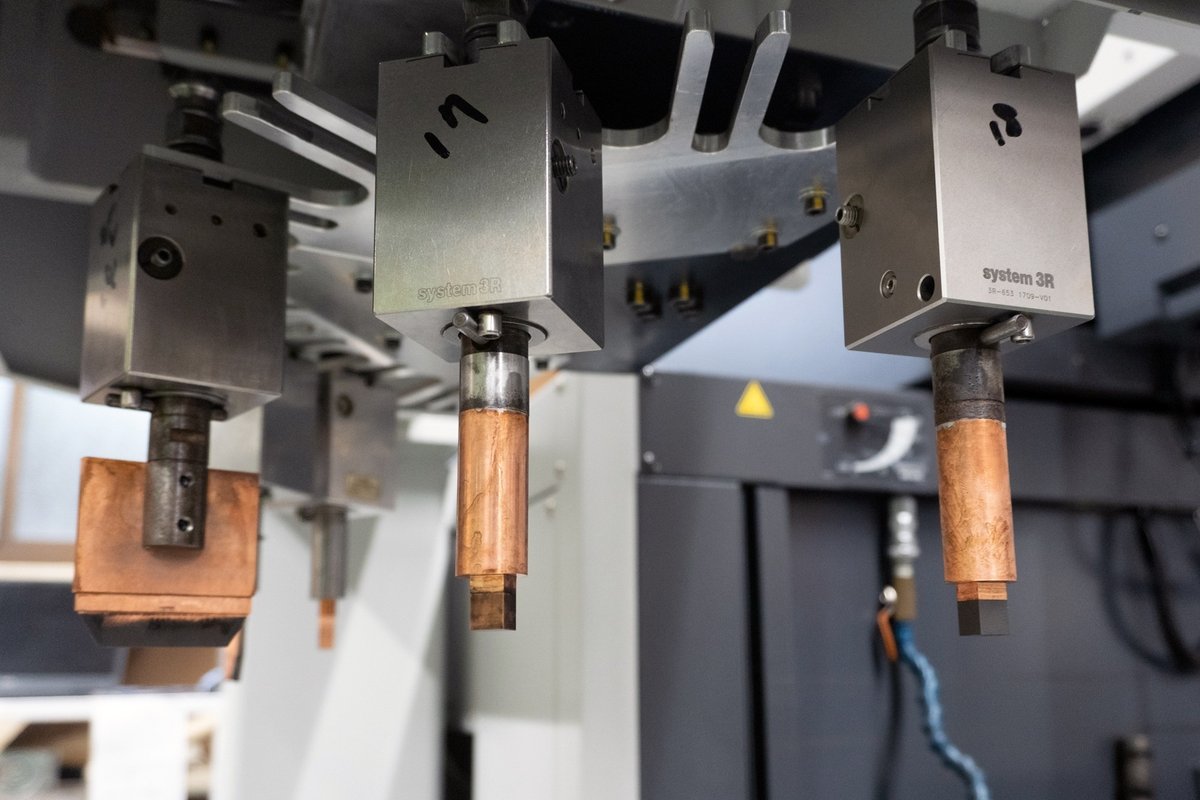
金型から成形部品を取り出すため、取り出しやすい形状とそうでない形状があります。たとえば勾配のないきれいな直角や、横穴が空いているような形状は通常の金型では製作しづらく、スライドという処理が必要になります。
この数が増えれば増えるほど、設計工数が増え加工に求められる精度が高くなり、費用にも上乗せされていきます。
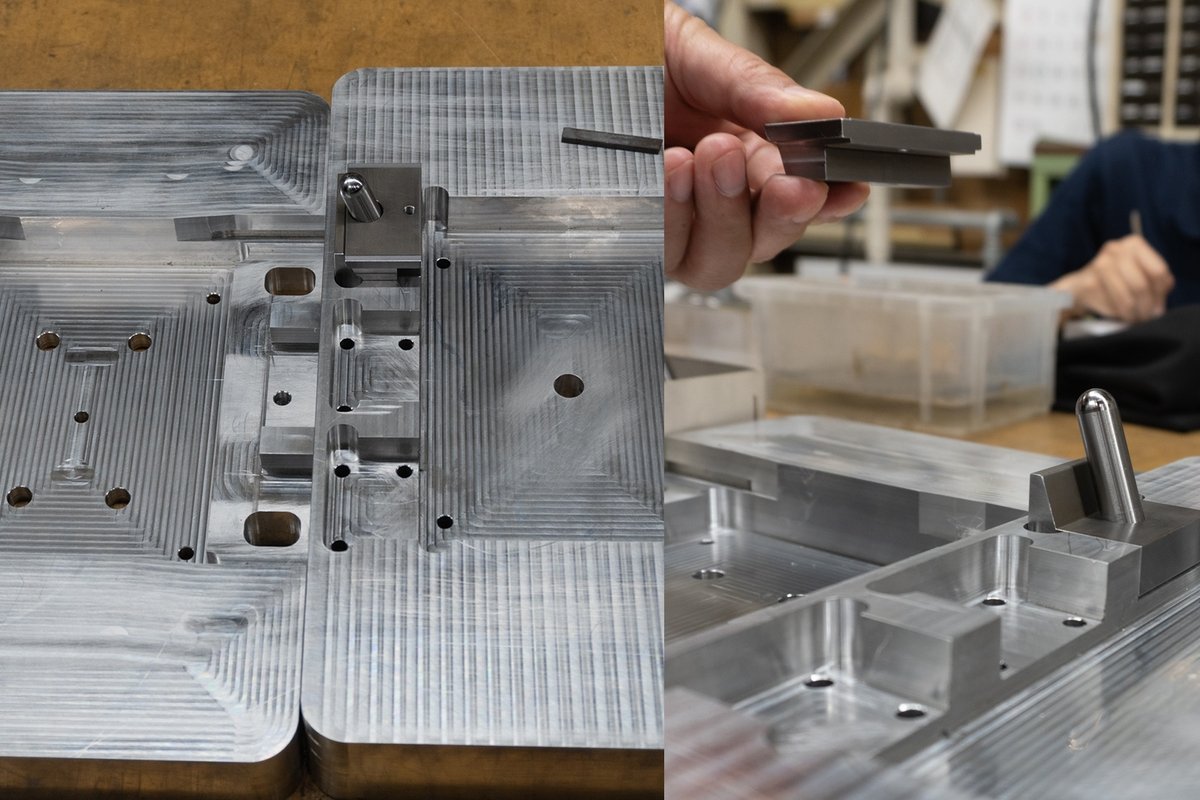
このように、金型の大きさや形状によって費用が変化するため、デザインだけを優先して依頼すると費用が高額になる場合があります。ある程度要件が決まった段階で、金型製作を視野に入れた製品設計や相談を進められると、金型メーカーや成形業者は仕事を進めやすくなります。
材料選択や仕上げの選択肢
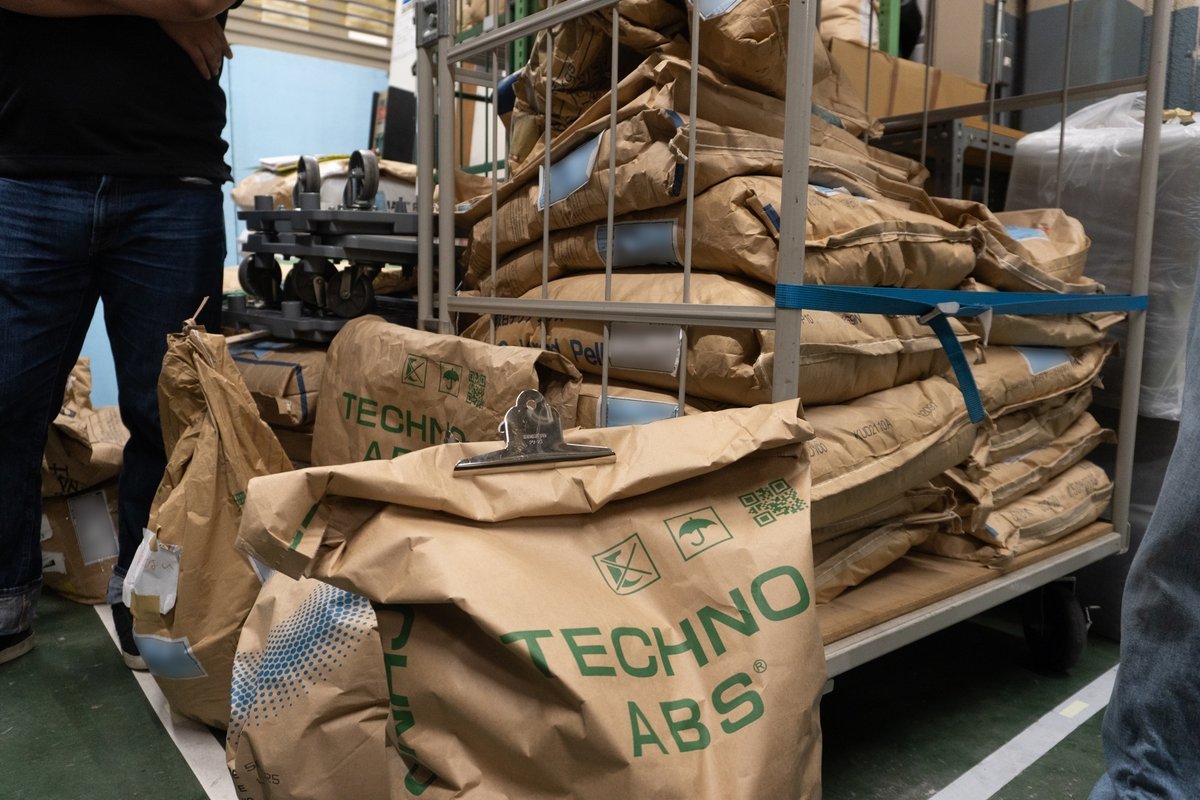
気をつけるべきこととして、成形材料は通常25kg以上でないと購入できません。中には最小購入量が300kgに設定されている材料や、生産まで半年ほどかかるものもあります。
色についても、「今ある色でいいので」と言われることがありますが、既にある色は他のお客様が指定していることが多く、流用できないケースが大半です。
独自に着色する場合も最低25㎏といった量の制限があったり、調色にも日数がかかったりする(早くても2週間、標準で1ヶ月程度)ため、カラーバリエーションを増やしたい場合にはコスト増を見込んでおきましょう。
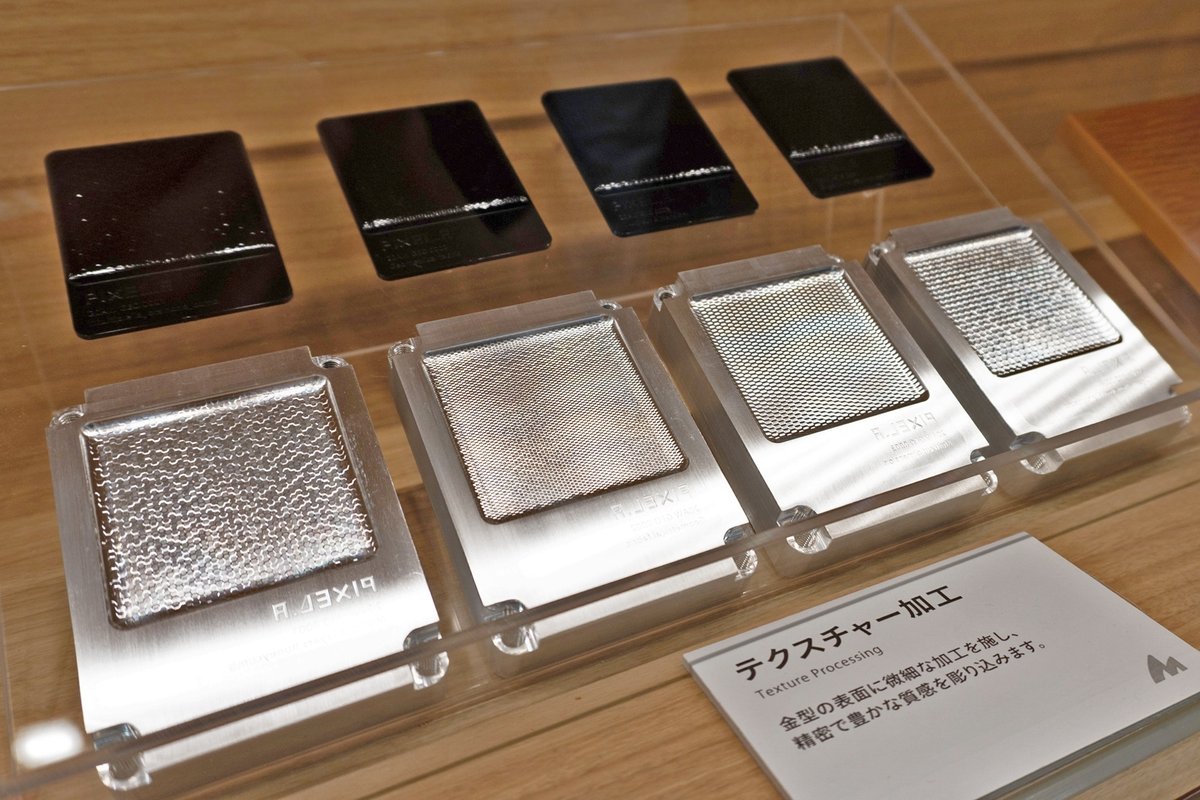
成形品に対する加飾には手間がかかります。塗装では色むらが出たり、膜圧が生まれたりしますし、フィルムを貼る際にも空気中のホコリが入るなどのリスクがあります。歩留まりも決して良くはないので、可能であれば成形だけで完結することを薦めています。
1000個以上の量産になるなら、金型製作の検討を
金型を起こすべきかどうかの判断は、製品の総量によって変わります。金型に初期コストがかかることは間違いありませんが、せっかく市場のニーズがあるのに3Dプリンターで製作しはじめ、気付いたら型がないまま数万個製作したという話も聞きます。
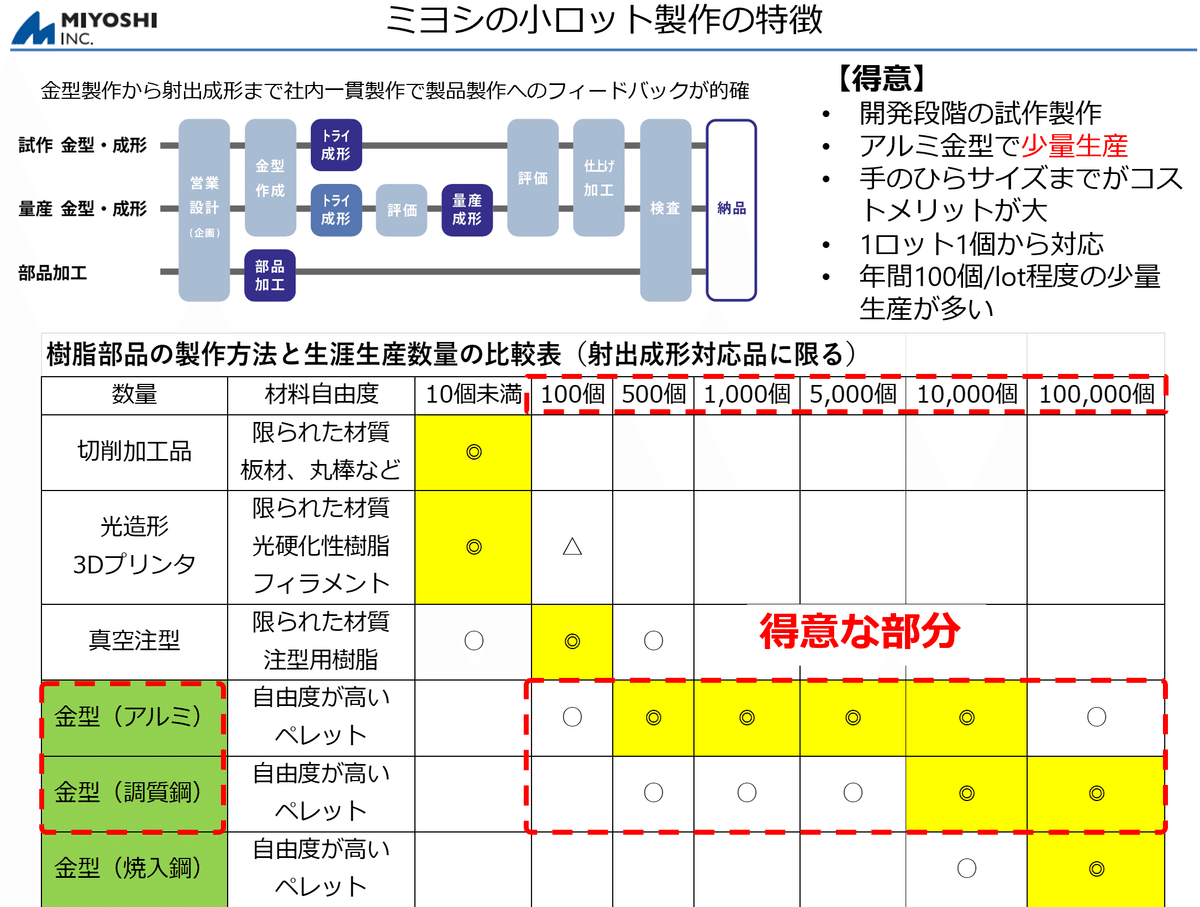
製造個数の見込みに応じて、異なる材料や製法を選択できる。
私の経験則ですが、1000個以上作る場合には金型のほうが一個あたりの単価は勝ります。
生産量が1000個を超えそうな場合には、金型製作に向けた準備や相談を始めると良いでしょう。ある程度の仕様や形状が出来上がった段階で、金型屋や成形会社への相談をしてみてください。
※次回は引き続きミヨシの杉山さんに、金型製造の契約にまつわるTipsやトラブル回避対策について伺います。
(取材・文:淺野義弘 / シンツウシン)
併せて読みたいオススメ記事
スタートアップ向け壁打ち相談会(対面・オンライン)のお知らせ
HAX Tokyoでは、グローバル展開を目指すハードウェア スタートアップや、これから起業を目指している方向けのカジュアルな壁打ち会を実施しています。
HAX Tokyoのメンターが相談をお受けしますので、ぜひお気軽にご相談ください。
【相談できることの一例】
資金調達を成功させるためにピッチ資料を改善したい
開発 設計など製造面での課題があり相談にのってほしい
PoCの良い進め方、いいプロトタイプ(MVP)の作り方を教えてほしい
企業との事業連携や事業開発をうまく進めるためのコツを知りたい
なお、HAX Tokyoへのエントリーやお問い合わせも、こちらの相談会でお請けしています。詳細は下記サイトからご確認ください。
この記事が参考になったら、SNSへのフォローもよろしくお願いします!
twitter https://twitter.com/HaxTokyo
facebook https://www.facebook.com/haxtokyo