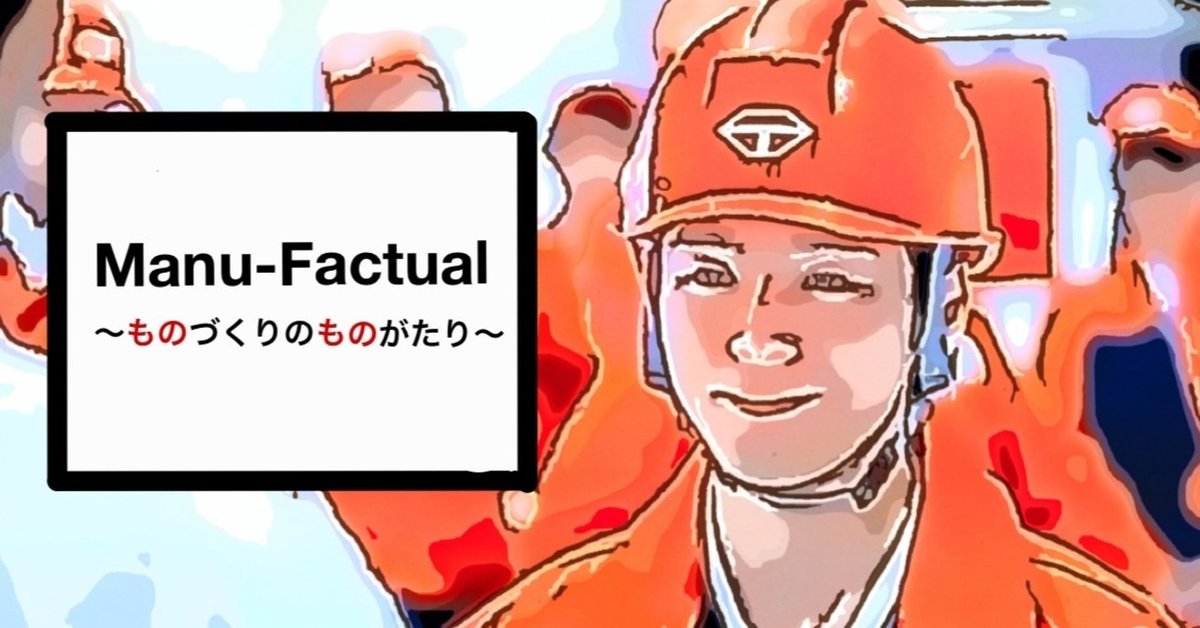
【トヨタ生産方式/TOC編13;理論の活用】
*前回までの投稿は上のマガジンに入れています。
前回まで、なんと12回も使って(長々とすみません)トヨタ生産方式(リーン生産方式)とTOCを解説をしました。今回は、健さんは出てこず、紫耀(ショウ)くんと倫也課長二人の対話を使って、この二つの理論をどのようにして現場への落とし込むのか流れの一例を簡単に記載します。
・・・・・・
実際の問題
👨🦱;おはよう。この間の健の講義を聞いて、うちの課のどの部分を変えていくべきだと思った?うちの現場ではどんな問題が起きている?
🧒;おはようございます。はい。うちの課は資材の課から受け取って、複数工程を通った部品が最終的に組み立てられて出荷されます。でもその複数工程の途中で出荷される場合も製品の導線が複雑です。そこで起こっている問題は下記だと思っています。
1,これまでは少品種大量生産でうまくいっていたので、大量に作って安くという文化が染みついている。結果、大ロットの大量生産にそもそも違和感はない。むしろ過去はそれが正であった。また、生産性重視の指標であるから、生産計画外のものも、在庫があればまとめ生産してしまう。それでコストが下がって評価されるという文化。
2,納期遅れが出たと聞くと、もっと作らなければとなり非ボトルネックもボトルネックも関係なく量産する。
3,結果、プッシュ生産により、後工程なっていくと、いらない部品まで設備前においてあり、本当に必要な部品をそろえるのに苦労する。
4,さらに置き場もなくなり、決めている置き場の決まりが守れなくなる。
5,そして、必要なものが見つけにくくなり、さらに指標は時間当たりの生産数量なので設備前にあるもので、今生産する必要のないものを生産する。→2に戻る。
6、このサイクルを繰り返しており、スループットが向上せず、在庫が溜まる、業務費用が上がるという状態となっている。結果赤字。
ということが起きていると思います。そしてうちも一部で新しい設備を入れてから、導入した工程の時間当たりの生産数量は上がっているので、混乱状態は設備導入前よりも悪化してるかもしれません。
👨🦱;やはり、そうか。一部だけ生産能力あげて、バランスを狂わせている可能性がある。要するに非ボトルネックで、過剰生産をしているんだ。品質自体はよくなったが、それではだめだ。ちなみに、それをどこで思ったんだい?
🧒;自分の担当は前工程設備だったので、あまり気に留めませんでしたが、健さんの講義の期間中に、健さんに“自分の工程の後ほかの工程にも5Sを展開しておけ”と言われて、活動をしていたんです。ほかの工程の整頓のステップで“置き場の見える化による製品の整頓”を行おうと思ったのですが、後工程になればなるほど、置き場を全然守れないんです。何度決めても全然決められた場所に置けないんです。なんでこんなこともできないんだって、理由を聞いたら、製品があふれて、置きたいけど置けないという理由があったのです。ちょうどトヨタ生産を習っているときでしたが、まさに作りすぎのムダだと思いました。ちなみにザゴール工場よりうちの工程のほうが複雑で、すべて学んだことが適応できるかは、どうかなと思っていますけど。
指標の再設定
👨🦱;そうか、思っていた通りだ。まぁ、すべては、まねできないとしても、トヨタ生産方式とザゴールから学ぶものは非常に多いよね。1週間ほどいろいろ考えて、下記のようにこれから方針を出そうと思っているよ。
一つ目は、まずゴールの再設定だ。ゴールは利益だよな。そして、現場に落とし込める指標でなければならない。これまでやっぱり生産性や歩留まりが指標として存在していたが、それれを指標にして目指せば目指すほどゴールから遠ざかる。だから、ジョナさんの言う通り、スループット、在庫、業務費用を指標に採用したいと思う。
🧒;確かに私も生産性、歩留まりばかり気にしていました。でも、具体的にどのような指標を考えているのですか?
👨🦱;スループットに関しては、ただ数量を作ったということではなくて、“売れるものを作った”、つまり“客先から要望されたものを必要な分だけ作った”という指標を作りたいと思う。“計画順守率”と設定したいと思う。これは計画数量だけでなくその製造した中身も評価するものだ。すべて同じものを作っているのであれば、生産数量だけ見ていればいい。でも、うちの工程のような、多品種少量生産の場合、作った順番、もしくは、何を作ったかも重要になってくるんだ。生産の質と量を確認する指標と言ったらいいかな。そして、もし計画以上に生産したら数字は下がるようにするんだ。
つまり、生産計画内の生産した量/(生産計画数量+生産計画外の製品を生産した数量)とするんだ。
🧒;おお、それなら勝手に大ロット生産をしていてもチェックできるようになるし、正しく順番を守っていたとしても生産数量が足りなかった場合、なぜ作れなかったかを確認できますね。作りすぎのムダも防げる。生産の量と質ですね。
👨🦱;そうだ。次は在庫だ。在庫は、データ自体はあるんだ。もちろん、棚卸があるからね。データは取れないとコンプライアンス上NGだ。
🧒;棚卸ってなんですか、棚をどうするんですか?
👨🦱;お、いいね。棚卸(たなおろし)っていうのは、月末に各工程に資材がどのくらいあって、仕掛りがどれだけあって、最終在庫がどれだけあってというのを確認するんだ。それをすべて資産として評価する。それが、損益計算書、つまりその工場の成績に計上されるんだ。
🧒;なるほど、それは重要ですね。って、なんの話でしたっけ?
👨🦱;おいおい、在庫管理だよ。要するに各工程の仕掛り在庫、最終製品在庫はわかるんだ。だから、日々すべての工程で見える化していこうと思う。そして、さらに、そこに標準在庫量を設定し、オーバーしている場合は前工程を止め、ショートしている場合は、リカバーさせるか後工程を止めるというようにするんだ。そして、ザゴールにあった通り、在庫がたまっているところがボトルネックと考えることができる。
🧒;なるほど。それでボトルネックを把握するっていうことですね。
👨🦱;ああ、たぶん、うちの場合は、最終工程に行く製品もあれば、途中で出荷されるものもある。そのため、オーダー次第で各設備の負荷が変わる。だから、ボトルネックは注文状況に応じて変わってくる可能性が高い。しかしながら常に異常は発見できる。そして、ザゴールと同じようにボトルネックの処理能力の向上を行っていく。これに関しては、多少の投資は覚悟する。赤字といっても、必要な部分には使うつもりだ。
🧒;なるほどです。これでボトルネックへのアクションも兼ねるわけですね。
👨🦱;そして業務費用だ。業務費用に関しては、歩留まりのみ目標を設定する。過去最も重要視していた、時間単位の生産効率を示す生産性の指標はすてる。
🧒;まじすか??
👨🦱;それは生産性を上げる発想になってしまうと、また大ロット生産の文化に戻る可能性がある。きちんと計画順守率が上がって、安定した時に効率が必要であれば考えればいい。いまは、矛盾する可能性がある指標を持たせたなくない。
🧒;なるほどです。
👨🦱;つまり、指標は、
-計画順守率(実際は遅れた場合の遅れた分の見える化)
-標準在庫量保持率
-歩留まり
にする。これを朝会で毎日PDCA回していくんだ。
🧒;大賛成です。
平準化の仕組みの構築~営業との協働~
👨🦱;そして、二つ目は、平準化の仕組みの構築だ。これがなければJITは成り立たないとトヨタ生産方式のところで習ったよな。これまで、営業が取ってきた数量を単純に受けて生産計画を受けていた。そのため、需要の変動をもろに受け変更に次ぐ変更で現場が混乱していたはずだ。これを変えないとやっぱりうまくいかないと思う。これからは、製造状況を営業に見える化し、事前に顧客に前もって情報をもらうように仕組みを作る。そして、1週間ごとにのみ生産数量を調整することとする。そのために営業との調整会議を週に1度実施することにした。その会議で、1週間の生産数量および日々の生産の優先順位を営業とともに決めるんだ。そして、営業もその情報をもって客先との調整を行い事前情報を得るというサイクルにする。もちろん、競合よりも短納期という前提だ。
🧒;いいと思うのですが、どうしても、顧客がすぐに対応してくれ、待てないという場合はどうするのですか?ザゴールのバーンサイド社的な感じの客がいたら。
👨🦱;その場合は、俺と営業課長とで受けるか受けないかを判断する。その場合は、もしかしたら、優先順位の中である製品は納期遅れになるかもしれない。でも、それをさせないために変更しやすいように中間在庫を徹底的に少なくして、リードタイムを短くしておくんだ。
🧒:そうか、リードタイムさえ短くしておけば急な変更でも対応できるというわけですね。すぐに造り終わるから、そのあとに生産できる隙間を作れるんだ。それでも、間に合わない場合はトップ判断でリスクをとるんですね。そりゃ現実はすべてがうまくいくということではないですしね。
ミズスマシチームの構築
👨🦱;そう。それが小説とは異なるところだよ。必ずトレードオフで選ぶときはあるからね。そして、3つ目がミズスマシチームの構築だ。いくら計画順守率が向上されてもやはり工程間の移動、次の段取りは必要になる。もちろん、これまで各工程の段取りマンが段取りをしてくれたが、前工程に何が残っていて、さらに自分より後工程に何が言っていて、緊急品は何で、、という全体間は把握できない。つまり、全体のモノの流れを管理するということはできていなかったんだ。だから、各工程の段取りマンでミズスマシチームを構築する。かれらはすべての生産計画を頭にいれ、自分の工程の段取りを全工程の段取りメンバーと情報共有しながら状況を把握する。また、不良等で支給品が発生した場合も、彼らが割り込み生産の指示を出し。状況を確認していくんだ。置き場の管理も彼らがしていくんだ。このチームの構築はもう部長に話して許可はもらっている。
🧒:おお。。。そうすると、5Sの整頓も製品の置き場でもできていきますね。
👨🦱;その通りだ。これから「指標の再設定、ボトルネックの処理能力アップ」「平準化の仕組みの構築」「ミズスマシチームの構築」をまず行っていく。気合い入れてプロジェクトとして実施していく。ショウには、ちょっと若いがこのプロジェクトリーダーになってもらって、実践をしてもらいたいと思う。
🧒;え??びっくりしましたが、わかりました!!
👨🦱;では、骨子となる資料を作って来週全リーダーに話をして早速進めていこう!
🧒;よろしくお願いします!!
・・・・・・・・・・・・・・・
最後に
最後ちょっと急ぎになってしまいましたが、本マガジンはこれで終わりとします。(お付き合いいただき本当にありがとうございました。)今回は、これまでの学びを参考に、実際の自分の現場に落とし込んでいく例を記載しました。トヨタ生産とTOCを織り交ぜながら、外部を巻き込んで、自分の問題に対応していく感じはなんとなくわかったかと思います。でも、これはあくまでも例です。実践は自分なりに、自職場の特性を理解して仮説を立てて進めていくことが一番重要だと思っています。結果が気になるかもですが、ご想像にお任せします。実践は根気との勝負になります。海外でも一緒です。ただ、1点今回、突然課長を登場させましたが、意図的なものです。最初は新人の学習という意味で書き始めましたが、やはり本当に現場を変えていくのはトップの覚悟でしかないです。そのトップをフォローする、もしくはきっかけを作るのが若手である部下の立ち位置になります。でもこれも必要条件で、この両方がないと、はっきり言って現場が変わることはありません。この構造をきちんと作るというのが重要です。トヨタ生産方式/TOC編はそれあった上でのツールを説明しているにすぎません。次のマガジンは、ドラッガーのマネジメント解説編に入ります。トップとミドルとボトムが協働していく組織には何が必要なのか、事業・組織の目的は何か。ここは私自身、日々悩みながら走っていますが、対話を使って解説していきたいと思います。
本マガジンは下記の本を参考にしています。
#製造
#現場
#理論と実践
#ものづくり
#トヨタ生産方式
#リーン生産方式
#改善
#かんばん
#7つのムダ
#TOC
#制約理論
#ザ ゴール