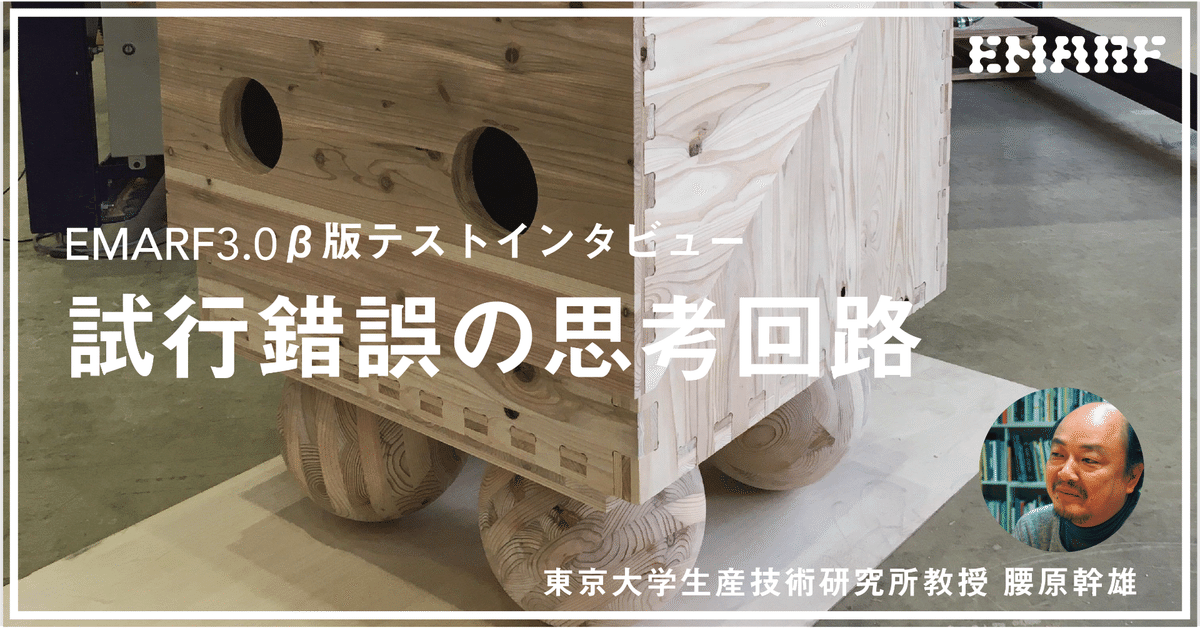
「EMARF3.0」β版テストインタビュー 腰原幹雄 (東京大学生産技術研究所教授・NPO法人team Timberize理事長)
VUILD株式会社は、5月27日に日本初のクラウドプレカットサービス「EMARF3.0」ローンチしました。そのリリースに先駆けて、株式会社乃村工藝社、株式会社オンデザインパートナーズ、SUPPOSE DESIGN OFFICE株式会社、辻琢磨建築企画事務所の皆さまに「EAMRF3.0」を体験していただきました。
今回は、東京大学生産技術研究所教授でありNPO法人team Timberize理事長の腰原幹雄さんにインタビューを実施。「EMARF3.0」を使った製作物の詳細や使用しての感想、「EMARF3.0」の改善提案などについて、VUILD株式会社代表の秋吉が伺いました。
Text by Naruki Akiyoshi
無人販売所製作プロジェクト
秋吉 まずは今回製作したものについてお聞かせください。
腰原 三浦半島に設置する野菜の無人販売所を作りました。無人販売所自体は半島内のいたるところに置いてあるのですが、農家の人たちがなんとなくで置いているだけのものも多いので、もうすこし整備すると魅力がある風景を作れるのではないかと考えました。
腰原 この無人販売所製作プロジェクト自体は、2019年にいくつかの大学と連携して実施していたもので、本来であれば3月頃に製作・設置して展覧会を開く予定でしたが、新型コロナウイルスの影響により進行が中断してしまいました。
秋吉 そのプロジェクトの概要を教えてください。
腰原 これは、以前から親交のあったクリエイティブディレクターの藤原大さんがプロデュースするkoyartというプロジェクトです。これから毎年継続的に無人販売所を制作していく予定で、今回はその第1弾として、関東学院大学、芝浦工業大学、東京大学が参加しました。
また、情報システムを導入して、無人販売所の課題を解決できればと考えています。無人販売所の最大の悩みは盗難被害です。センサー技術などを応用した盗難を未然に防ぐ仕組みやICタグの付与、キャッシュレス対応など、ローテクの無人販売所にハイテクなシステムを組み込むことで無人販売所の課題を解決しようと計画しています。将来的には、無人販売所自体が自動で移動するようになればいいなとも思っています。
秋吉 製作する上で意識されたことはなんですか?
腰原 たいていこういうイベントで製作されたものは会期中は使われるのですが、イベントが終わると壊れても誰も修理せず放置されてゴミになってしまうことが多いです。また、イベント期間中のことだけを考えているので、耐久性をあまり考えない見栄えを重視したアクロバティックな構造の瞬間芸におさまってしまう。それはあまり望ましくないので、反対にとことん単純化した構造の組み合わせの面白さを意識して作りました。
骨組みだけ用意してテント生地を貼り付ければ安く作ることはできるのですが、今回は少し分厚い木材をシンプルに組み合わせたモデルを考えました。また、開店中か閉店中かすぐ視認できるようにふたの開閉機構を付けています。
脚の部分を球体は、親しいメーカーに相談したのですが、上部は中断してしばらく放置していたのですが、再始動のときに秋吉さんに相談しました。その時に「EMARF」体験の話をいただき、ものと接することなくどれだけのことができるのかに興味を持ちました。また、(中断してしまった)共同プロジェクトとセットにして考えると面白いと思い製作に至りました。
「EMARF」を使用して見えてきた利点と限界
秋吉 ご相談いただいた際にスケッチを見させていただきましたが、そこから実際に製作するまでのプロセスについてお聞かせください。
腰原 どういうものを作るかまでは決まっていたのですが、面材など材料の大きさや厚みによってもののサイズが決まるため、プロジェクト全体においても部材の制限をどう設定するか悩んでしまい、なかなか踏ん切りがつかずにいました。なので相談した際にもまず最初に、どういう材料に対応しているのか、どれが一番加工しやすいのかを伺いました。
相談の上、今回は36mmのCLTを使用しました。製作を担当してくれたフィラス(博士課程学生)は、もともとノコギリやノミを使ってものづくりをしていたので木取り感覚に優れています。また、「EMARF」のシステムもうまく活用してくれたと思います。
秋吉 フィラスさんは「EMARF」で製作してみていかがでしたか?
フィラス 「EMARF」は、使っていて楽しいシステムでした。簡単かつ直観的で、デザインが決まれば、あとはジョイント(部材同士の接合部分)を考えれば良いだけです。また、Web上にデータをアップロードするだけで、実際のツールパス(木材を切削する機械の加工経路)がどのように動くのかを見られるというのはとても面白いと思いました。それによってCNCで加工するときに、どうやってデザインすべきかについての理解が深まったと思います。
秋吉 デザインを検討する上で、なにか問題・限界はありましたか?
フィラス 材料の制限が今回のプロジェクトの進行を少し妨げた部分があると思います。「EMARF」のシステム上の課題の1つは、この材料のサイズの制限です。もしメーター板などのもう少し大きい部材が使えればサイズを修正することなく、本来想定していた正方形のものにすることができたと思います。
また、「EMARF」のシステムは全体としてとても柔軟ですが、同時に機械の性能からくる限界もあるという印象です。CNCに付随する3軸の加工という制限から、斜めの加工ができなかったり、片面からしか加工できなかったりするので、そのあたりを理解していないと、デザインがうまくできない部分があると思います。5軸の機械まで使えるようになると、その制限がなくなりデザインの幅が広がるので、サービスとしてよりよいものになるかと思います。(※斜めや3D曲面などの加工については近日対応予定)
腰原 垂直にしか刳り貫けない点にはたしかに限界はあると思います。ただもし、5軸以上の万能のCNCマシンがあったとして制限が何もなくなると、デザインを考えるのは自由度がありすぎて簡単ではなくなります。そういう意味ではある程度の制限はあってもいいかなという印象です。
「EMARF」でコストを抑える設計のコツ
秋吉 5軸の加工機があれば細かい調整もできますが、家具ぐらいのものだと規模が小さいためコストが必要以上に高くなってしまう可能性はあります。また部材に関して、CLTから合板に変えるだけでもコストは半分くらいになります。さらに厚みのある材料だと、機械が何周もして削らないといけないのでその分のコストが嵩みます。今回で言えば厚みを36mmから24mmにするだけでもコストを抑えられます。
腰原 今回は仕様を贅沢にして作ったとはいえ、コストに関する情報は最初に欲しかったですね。どういう加工をするとコストが高くなるのか、材料をどのように選択するとコストを抑えられるのかなどがもう少し分かればいいかと思います。例えば、CLTの1層目だけをくり抜くと、繊維方向の向きが変わるので表情が変わります。1層目と2層目の間で抉りを止めると模様が出てくるので面白いと思ったのですが、今のお話伺うと、この加工はコストが高くなりそうですね。
秋吉 切り抜いてしまうとコストを安く抑えられるのですが、彫り込みだと彫り込んでる面積分を削っていかないといけないので時間もコストも嵩んでしまいます。「EMARF」では周長、つまり機械が動いた分で金額を算出します。今回の無人販売所も防水のために構造が外に飛び出ないように突き抜けない接合部になっている箇所が多いので、その分周長も伸びるのでコストがかかっています。
腰原 ジョイントの数や切り込みの数を少なくした方が安くなるわけですね。
秋吉 ジョイントの数も選べて自動生成できるのですが、フィラスさんはどのように選択されましたか?
フィラス 意匠的にきれいに見せるためにシステム上限まで使用しました。
腰原 今回の場合だと、正面下段の小さいパネルのジョイントサイズに揃えたので、ジョイントの数が多くなってしまいました。見栄えの良さを追求してオーダーを複雑にすることもできるがその分コストが高くなる。構造面だけを優先させればジョイントの数も少なくできるので、コストを抑えられるということですね。
秋吉 フィードバックをうけて、コストについての情報も今後細かく公開していきたいと思います。
腰原 コストに関して言えば、大工仕事とCNCではコストの感覚が反転しています。大工の高等技術と言われていることは平面を作ることです。ノミで敷居や鴨居などの溝を平らに長く作るには高度な技術が求められるため、単価が高くなります。しかしCNCにとって、単純な溝を掘ることは簡単な作業なので大工に依頼するより安く抑えられます。一方で入り角を直角にすることは大工にとっては単純な作業ですが、刃を回転させて削っていくCNCの仕様上、直角にするためにはコストが余分にかかってしまいます。大工仕事の知識やコスト感覚を持っている人は注意が必要かもしれません。
アジャイル型の建築設計プロセスへの転換
腰原 いずれ農家自身が無人販売所を作りたいと思った時に、何をサポートしたらたどり着けるのかをいま考えています。やっぱり間にデザイナーや建築家っぽい人が入らないと難しいのか、フォーマットを限定すれば作れるのか、ディティールを都度修正してあげれば作れるのかなど、今後のプロジェクトの製作プロセスを検討しています。
秋吉 「EMARF」にとって、どんな人でも創意工夫して自由にチャレンジして失敗できる環境のプラットフォームであることが重要なのではないかと考えています。ものづくりをやっている人は試行錯誤するプロトタイピング思考が自然に身についているのですが、ものづくりから距離のある設計者は、一発で完璧なものが出来ると考えている場合も多くあります。少しづつ調整してより良いものにしていこうとする考え方をどのように共有していくべきでしょうか?
腰原 無人販売所プロジェクト自体は、ある程度まで計画して何年か寝かせていたプロジェクトです。関連しそうな提案があった時にすぐ出せるようにしてあるプロジェクトの種は他にもいくつかあります。大学であれば長い期間そういうプロジェクトの種を抱えておけるので、タイミングと背景次第でプロジェクトの花を咲かせることができます。普通の建築設計事務所では経済活動が欠かせないため、このようなプロジェクトの計画は難しいかと思います。
中には実現まで10年近くかかったプロジェクトもいくつかあります。世の中にないものを作ることは、スムーズにステップアップしていかないものです。そのための技術の一部を別のプロジェクトの中で練習していくようなイメージで、試行錯誤のバリエーションを収斂させていく思考回路が必要かもしれません。
秋吉 ものづくりを継続するとディテールの洗練など技術的な積み重ねがあるので、プロジェクトを経るごとにより良くなっていくことはありますが、設計者がバリエーションを志向するとうまく積み上がっていきません。ものづくりをベースにしたスタディープロセスの可能性についてはどう考えますか?
腰原 バリエーション志向は今の学生を見ていてもよくある傾向です。論文に関しても早めにテーマを設定した人の方が良いものができることが多い。テーマを設定すると色んなものがその視点で見えるようになるので、関係ないように見えていたものとの繋がりが見えてくるようになり、本質的なところにたどり着きやすくなります。テーマを定めていないと、視点がブレるのでバリエーションを追うばかりになってしまいます。
建築家の一番の悪いところはマイナーチェンジではなく、フルモデルチェンジばかりを目指すところです。構造家はディテールの転用などを柔軟に対応できるのですが、建築家はその志向があるので、生まれたアイデアを次に生かすことがあまりうまくできません。方向性を定めると試行錯誤できるようになるので、その辺りの思考回路を変えていく必要があると思います。
秋吉 VUILDでは最近、ウォーターフォールからアジャイルへ、つまり小さいアジャイルでディテールからバリエーションを決めたものを少しずつ成長させていく設計方法論を作ろうと試行錯誤しています。
腰原 そういう未来志向の思想を発展させることが、プロフェッサーアーキテクトの仕事だと思います。その思想を構築していくには長い時間がかかるので、経済性は成り立ちません。民間の経済ベースの設計ではできないことを、大学にいるような人たちがすべきだと思います。
「EMARF」に関して言えば、最初は小さいもので数をこなしてみて、次のステップで大きくしたものを試行錯誤していく。段階ごとのツールがあるので、その段階ごとに議論すべきことが変わっていくことが、一番いい積み上げ型の設計になるのではないでしょうか。
「EMARF」の建築生産領域での利用可能性
秋吉 先ほども材料の制限の話がありましたが、今後大型加工機を「EMARF」に対応できるようにして、ゼネコンがやっているような建築生産の領域まで接続させていきたいと考えています。そのような生産システムに敷衍していくためにはどのような条件が必要になるのでしょうか?
腰原 構造設計の観点から材料のプロパティに関して言えば、このシステムに木材は向いていません。鉄板や樹脂などの等方性の均質な部材でつくれば何の問題もないのですが、木材は繊維の方向などによって耐久性が異なるため、その点を考慮することが設計者側の手間になります。建築の規模になればなおさらに、もし梁の部材の木目の向きが90°回転していたら、構造性能は1/3程度になってしまうので致命的です。そのチェックを誰がするのか、性能を誰が保証するのかが課題になってきます。
また、同じ機械を使っても加工場所によって精度が異なることもありえます。ゼネコンの領域を目指すのであれば、品質管理も重要です。もちろん大工の精度がばらばらでも建物はできるので、その違いを許容できる世の中になれば問題ないのですが、今の社会や組織は効率化や均質化を目指す方向に進んでいるので、それらをコントロールできていると言えるかどうかによって信頼性も変わってくると思います。あとは生産プロセスの透明性を高めるために、加工現場を見られるようになればよりいいのではないでしょうか。
秋吉 今後、生産現場にカメラを設置して配信もしていこうと考えています。
腰原 品質管理はもちろん、実際の加工風景を見ることで工法や表現のアイデアも出てくると思います。
生産システム全体に関して言えば、日本には組み立て建築を好まない傾向があります。プレキャストコンクリート造が流行らない原因はそこで、なんとなく同じ部品を使ってコピーのようなものをたくさん並べて作る戸建て住宅のようなイメージが持たれています。
なので、「EMARF」の生産システムから生まれるアウトプットのバリエーションをアピールする必要があると思います。「EMARF」の面白いところはオートクチュール的に特注品を、既製品とあまり変わらない値段で作れるところでもあります。それをうまく見せないと、「規格標準化」「コピー」「大量生産」のような印象を持たれかねない。例えば、「サブロク板のCLTだけでこれだけのバリエーションができます」みたいな事例が見えてくるといいですね。いずれにせよ、単に加工や生産システムの提案をしているだけであって、デザインの提案や統一化を目指している訳ではないと明確に表明する必要があるかと思います。
秋吉 「標準化」などの言葉だと同じものしか作れない印象をもたれかねません。「EMARF」の場合は型がある訳ではないので、「フォーマット」などの表現の仕方もあるかと思っています。
腰原 現在、大規模木造用の標準規格を作っているのですが、私も同じ悩みを抱えています。私は単に部材の寸法規格を作りたいだけで、組み合わせ方の規格化考えていないのですが、勘違いされることが多くあります。表現方法については検討が必要かもしれません。
「EMARF」のライバルが必要かもしれない
秋吉 今受け持っている授業で、学生に同じ合板一枚からものづくりをしてもらっています。今年のうちに100事例くらい出る予定です。去年も実施していて、これも全て極端な例ですが、同じ合板一枚からできています。
腰原 見せていただいた事例のように、面材から細かい線材にくり抜いて作る発想は新しいですね。ただ、その分細くなると構造性能上の問題が発生するので、最小幅などは気をつけた方が良いかもしれません。
ここでする話じゃないかもしれませんが、本当ならこういうものが論文になるべきなのだと思います。「『EMARF』のような生産システムを作ったら、私が思ってもみないような結果ができるようになりました」みたいな、開発者すら思いつかなかった方法が出たというところが一つのゴールになる気がします。
秋吉 それも論文になるのですか?
腰原 もちろんそうなるまでの前段を整理する必要はあります。結論のために仕組み作りの流れを順番に整理していけば、生産システムに対する論文になります。自分のアイデアを積み上げた結果として特殊解を提示することも論文になりますが、自分が制作していないものを実例とすることで、論文の性質が変わると思います。
秋吉 最後に、今後の「EMARF」の仕組みを考える上でなにがあれば面白くなると思いますか?
腰原 「EMARF」のライバルが出て来ると面白いかもしれません。「EMARF」というよりはShopBotなのかもしれませんが、面材専門に対して線材専門や、二次元加工専門、三次元加工専門のような競合が現れてくると盛り上がっていく可能性があります。秋吉さんのところだけで線材までやりはじめると、市場をコントロールするかたちになってしまうので逆につまらなくなるかもしれません。
(2020年6月某日、Zoomにて実施)
-----------------------
【おまけ】サンプルデータを配付
さんかくスツールのデータの配布を開始しました。こちらのアンケートにご回答頂いた方限定に配布しています。EMARF活用にあたってサンプルとして出力していただいて良いですし、現在設計されている家具の参考としてもご利用いただけます。
さんかくスツールならびに、本棚のデータの配布を開始しました。こちらのアンケートにご回答頂いた方限定に配布しています。EMARF活用にあたってサンプルとして出力していただいて良いですし、現在設計されている家具の参考としてもご利用いただけます。
-----------------------------
facebook: https://www.facebook.com/VUILD.co.jp
instagram: @vuild_official & @vuild_architects
twitter: @VUILDinc