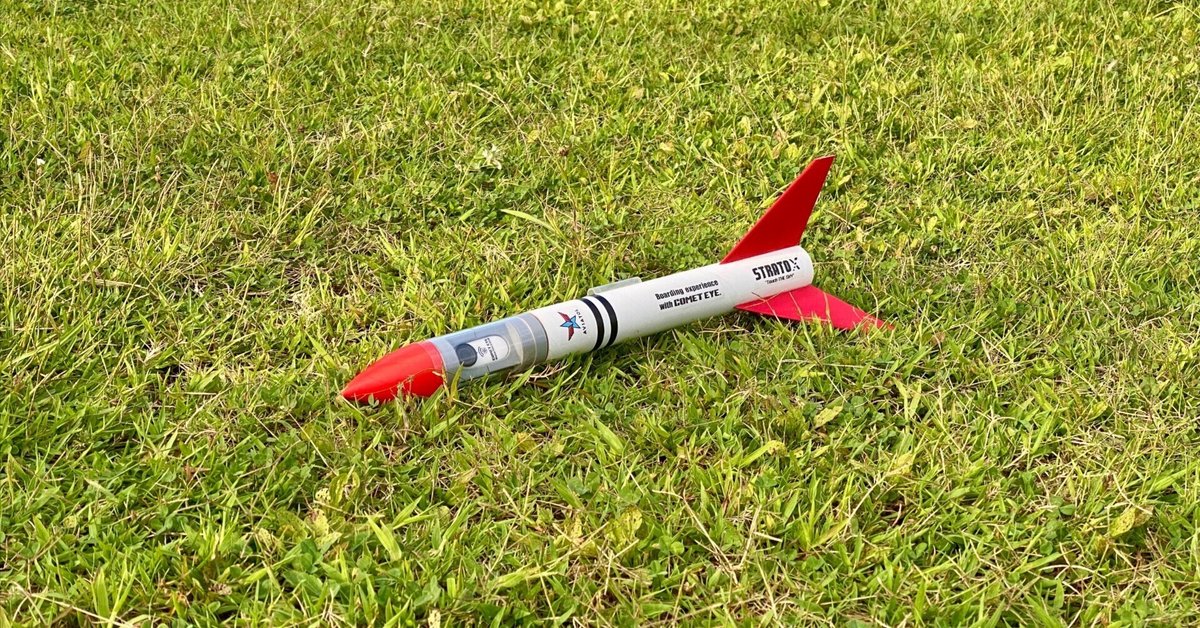
モデルロケットにカメラを搭載して映像をとる #計画&ロケット製作編
はじめに
皆さまお久しぶりです。
今回は少しチャレンジングな企画を実行してきましたので、皆さまにご報告したいと思います。
構想から8年、一度はあきらめた企画でしたが、タイミングときっかけが重なり、今回のフライトがようやく実現しました。
モデルロケットとは
タイトルにあるモデルロケットって何だろ?という方のために、簡単にモデルロケットのご説明をします(知っている方はスルーしてください)。
モデルロケットとはその名の通り、模型ロケットともいわれるロケットで、ロケットノズルと火薬が一体となったエンジン(モーター)をロケット本体に差し込んで打ち上げる小さな本物のロケットです。エンジンの中の火薬を燃やして発生するガスをロケットノズルを通すことで加速させ、そのガスを勢いよく出す反動で飛んでいきます。

直接エンジンに火をつけるのではなく、電気の力を使って離れた場所からエンジンに点火します。また、日本モデルロケット協会が定める安全上の自主基準があり、それには見学者や建物などを守るための保安距離が定められています。先にも述べたように『本物のロケット』ですので、安全に配慮した打ち上げをするのに従事者は必ずこれを守って打ち上げを実施します。
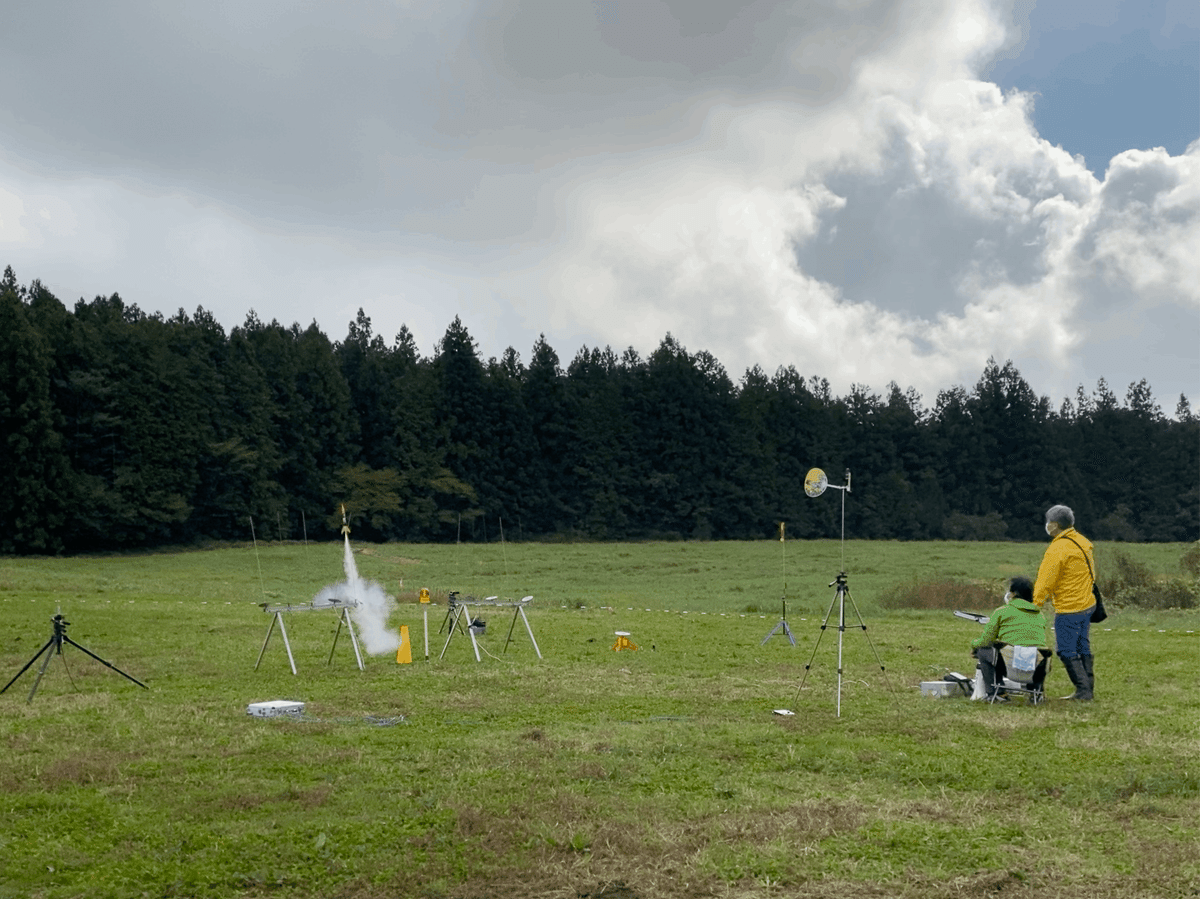
難しいように感じられるかもしれませんが、必ず守るルールとしては以上の安全上の自主基準が中心で、その他には大きな声で打ち上げのカウントダウンなどを行うなどがあります。安全に実験をさせる目的で定められているものなので、小学生の方でも安全な打ち上げを実施しています。
また、ロケットをもっと高く飛ばしたい、パラシュートで滞空時間を稼ぎたい、などの目標が出てくると、自然に材料の研究や物理の基礎が学べるようになり、突き詰めていくと物理の力学だけでなく、電気の知識や数学への理解など、幅が広い学びが実践的に体験できるツールでもあったりもします。
その延長線のひとつとして、今回のプロジェクトがあります。
構想とプロジェクトへの思い
『ロケットに乗っているような体験を提供する 』
この企画を思いついて一番初めに実験をおこなったのは2014年のことです。
具体的には、ロケットにカメラを搭載して動画を撮り、画面や今でいうゴーグルなどに投影して体験者にロケットに乗っているよな臨場感を体験していただく、というものです。
当時、モデルロケット全国大会のジャンケン大会で獲得した『LOAD STAR』というロケットのキットが家にあったので、それに市販のカメラを入れて打ち上げる計画を立てて取り組んでいました。
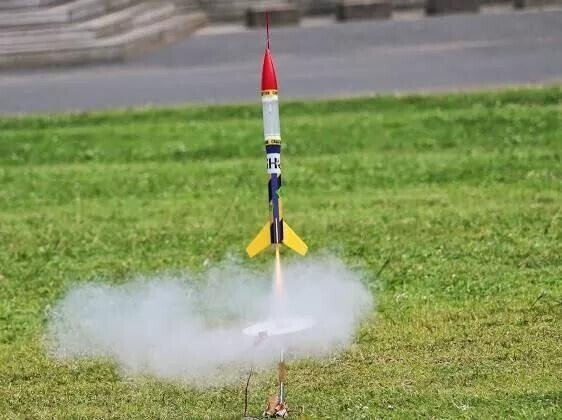
ただ、当時はロケットに搭載できるような小型カメラの画質が良くなく、思ったような映像が撮れないことがわかり断念しておりました。
また、当時からこだわっていたこととしてはもう1点あり、『C型エンジンまでを使って飛ばす』ということでした。
それはモデルロケットを初める方にとって最初の一歩は、日本モデルロケット協会が発行する『第4級ライセンス』を取得することだと思います。
その第4級で扱える範囲のエンジンの中で実現をする、すなわち、火薬の量が少なくても、頑張れば『こんなこともできるんだ』という可能性を感じてもらいたかった、という思いがあります。
ですので、この記事をみて、少しでも多くの方がモデルロケットに興味をもち、さまざまなチャレンジをしてくださることを願ってキーボードを叩いています。
よみがえるプロジェクト。始まりのきっかけ
2022年6月、友人のご紹介から千葉県の浦安市にある日の出南小学校でペットボトルロケット大会があるということから、そこでモデルロケットの試射ができないか、というお話をいただきました。
親子での参加者が中心となり、ペットボトルロケットが飛んだ距離を競う大会です。
私は機会をいただき、競技が始まる前にモデルロケットのライセンスを取る際のいちばん最初に打ち上げるロケットである『アルファⅢ』の打ち上げデモンストレーションを行いました。
上記の動画をご覧いただけた方はお分かりになったとは思いますが、初めて見るモデルロケットの速さと、打ち上げ高度の高さに皆さん驚かれていました。
その日の夕方、運営メンバーの方々が開かれた会合に参加させていただけることになり、運営されている方々の日々の活動のお話やモデルロケットのことなどで意見交換をさせていただきました。
その中で『ロケットの中にカメラを入れて動画撮影ができないか』というお話を運営委員の方からいただき、その数年前の記憶が一気によみがえってきました。
『一番大切なのは画質。そして重量はこのくらい、大きさはこのくらい…』
その場でスマホを立ち上げ、ロケットに搭載ができそうなカメラを即座に検索。
探しあてたのがこのカメラでした。
重さが30gを切り、形状もコンパクトであったため、モデルロケットに搭載できそうなスペックでした。
しかもキャンペーン中で安かったため、その次の日には注文しプロジェクトが始まりました。
プロジェクト、再び。
計画
今回のロケットの名前は、なるだけ高く飛んでほしいとの思いを込めて、成層圏(Stratosphere)という単語と、果たしてどこまで飛んでいけるのだろう?という意味合いの”X”を組み合わせた造語である、STRATO Xとしました。(何となくかっこいいでしょ?)
カメラモジュールは、ロケットのような速いスピードでも確実に映像を捉えてくれることを期待して、彗星(Commet)の目(Eye)COMMET EYEと名付けました。(これまた素晴らしい…(自画自賛))
そしてそれぞれにはタグラインを考え、STRATO Xにはニッキー・ミナージュの”Starships”という曲の中にも出てきますが”Touch The Sky”とし、
ロケットの全体像としてはLOAD STARを参考にすることにしました。
ノーズとカメラ搭載モジュールを上段とし、パラシュートとエンジンが入ったボディの部分を下段とするような全体像(下図参照)です。
また、映像としては『ロケットが真っ直ぐ打ち上がり、上昇しているところ』の映像が撮れれば今回は良しとしました。
上昇中はロケットのフィンにより、真っ直ぐ飛んでいるような映像を撮れると考えましたが、下降中はカメラモジュール自体が回転してしまい、安定した映像が撮れないことを想像したためです。
そして最初のラフスケッチとしてはこんな感じでした。
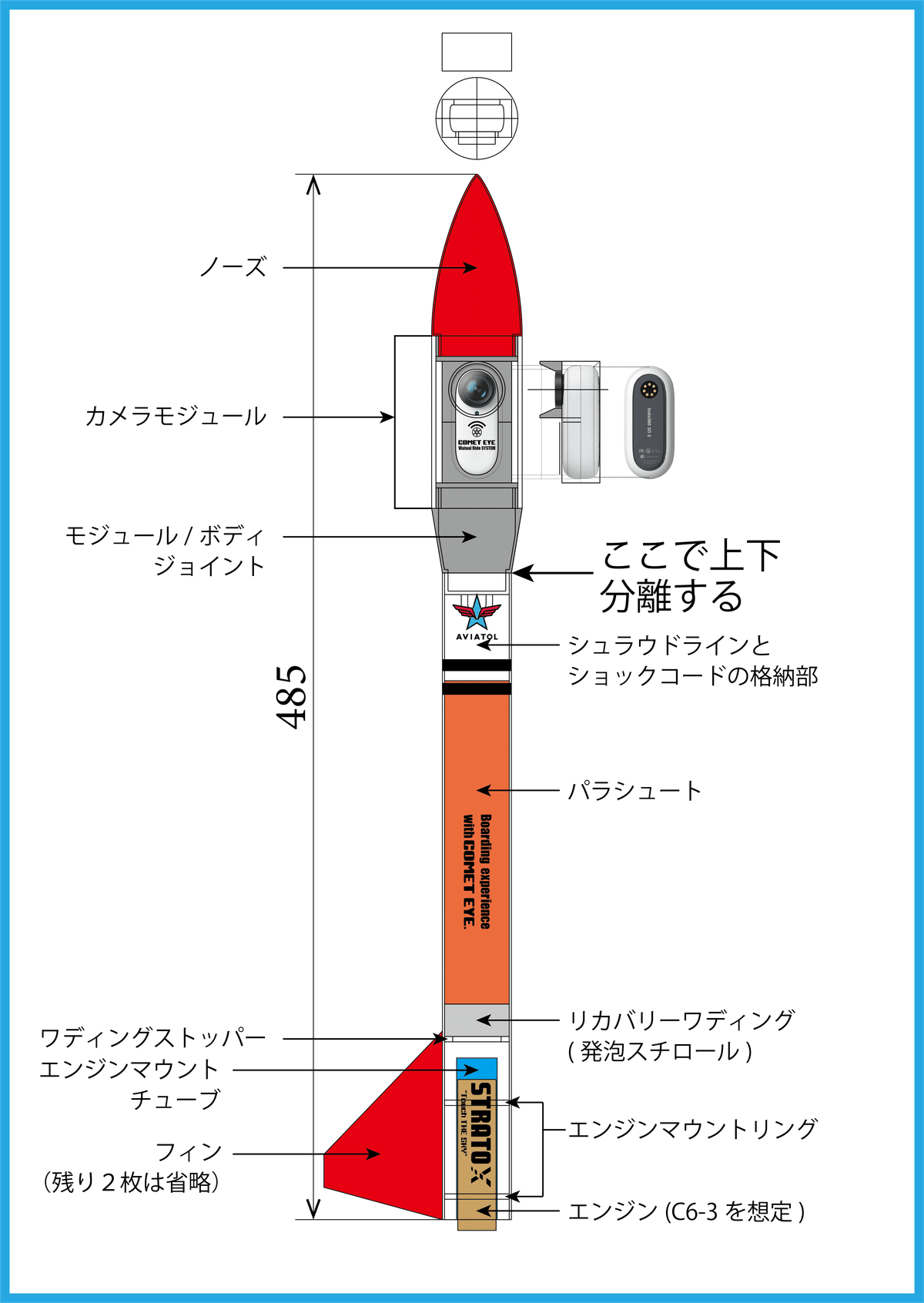
ロケットを作りはじめる際の全体像として、まずはロケットに搭載する『ペイロード』から考え始めることが第一です。
ロケットは本来、モノを運ぶための輸送機器ですので、その運ぶモノ(ペイロード)のことを常に考えながらプロジェクトを進めます。
それと同時に、そのペイロードをどのくらいの高さまで運べば良いか、ということも考えます。
今回の場合は、C型エンジンでどこまで飛ばせるか、ということがプロジェクトのキーコンセプトでしたので、一旦高度自体については全体のパーツが揃ってから重量を測定して計算してみることにしました。
次に本来であれば到達高度とロケットの重量予測からエンジンを選択します。今回運ぶペイロードの質量が重いということだけわかっていましたが、それ以外のことは初の取り組みであったためロケット全体の重量予測もできません。そのような状況の中でも使用できる最大の推力を出せるC型エンジンは必須であろうと考え、過去に使用実績のあるC6-3エンジンを選択しました。
その後、ペイロードを載せるモジュール設計、打ち上げに耐えうるボディの設計、ノーズコーンの設計、エンジンマウントの設計などを経て、それぞれを製造します。全体のパーツが出来上がってから重心位置を測定(フィンの部分は仮のオモリを取り付け位置につけます)し、最後にフィンの設計をします。
モデルロケットが飛ぶ際にはロケットノズルを振るなどの制御ができないため、特にランチャー離脱速度が遅い今回のロケットのような場合には、フィンの形状設計が重要になってきます。
途中、計画のままでは製造ができないことがわかったり、重量が増えてしまうことがあったりしてフィードバックをかけることが必ずといってもいいくらいの確率で発生しますが、全体の流れとしては以上のような流れになります。
設計 / 製作
今回カメラは本国の公式サイトで注文したため、届くまで時間がありました。
ですのでカメラ搭載モジュールの製作は後にし、まずはもう一つの搭載物であるパラシュートを製作しようと考えました。
パラシュートの製作
パラシュートはロケットとペイロードを安全に地上へ着地させるための回収装置ですので、設計する際には全体の重量を見積もることが大切です。
前述のように、以前製作したLOAD STARの重量がエンジンを含めて120gに満たないくらいだったような曖昧な記憶がありましたので、それにおおよそ60g程度を加え180g程度であろう、と予想して設計を始めました。
180gのロケット+モジュールをどのようなパラシュートを使って回収するか。
それも経験がなかったことですので、まずは材料から探してみることにしました。
なるべく軽くて丈夫な素材を探すことはロケットを製作する方でしたら誰でも悩む問題だと思います。
私はもともと大学では材料の研究室に属していたくらい素材が好きでしたので、そのあたりの知識はあった方だと思います。
また航空機も好きで、そのパイロットが着ているような上着の素材なんかにも注目していました。
そのような影響もあり、軽くて丈夫であり、素材的に大気を確実に捉え、広がりやすいような素材を考えると、『ナイロン』が浮かびました。
ナイロンは市販のフライトジャケットなどに使われており、伸びにくく引っ張りにも強い特性があります。
最近ではエコバックの素材としても使われているようなポピュラーな素材です。
早速探してみると『自作エコバックの素材』として販売されているものがありました。
安全面を考え目立つようなカラーリングであるオレンジ色を購入し、パラシュートの素材とすることにします。
パラシュートの大きさですが、対角線が750mmの12角形を考えて設計しました。
600mmでは小さすぎるし、900mmでは大きすぎると考えていたためです。
ですが、万一のことがあった際に備え、600mmも900mmも同時に製作しておきます。
ナイロンの生地を切るのには、裁ちバサミを使えば楽に切れますが、穴を開けるとなると結構コツがいります。
薄い生地に円状に穴を開けるには『ポンチ』と呼ばれる円状に切れる治具とハンマー、厚めのゴム板、両面テープが必要です。
ナイロンの穴を開ける場所の下に両面テープを貼ったゴム板を敷きます。そしてナイロンの生地を貼ります。穴を空ける場所にポンチを添え、一気にハンマーで叩き穴を開けるのです。
その際、生地をちゃんと貼れていないとうまく穴が開けられなかったり、穴が円形に空かなかったりしますので注意が必要です。
ナイロンですと、切断した際の生地のほつれが気になるところですが、切断した箇所に『ピケ』というほつれ止め材を塗ればその心配がありません。
穴を開けた部分にはピケを塗った後、両面ハトメを使って穴を補強しています。私は金属のハトメを使いましたが、プラスチックのものもあるようなので、それでもいいと思います。
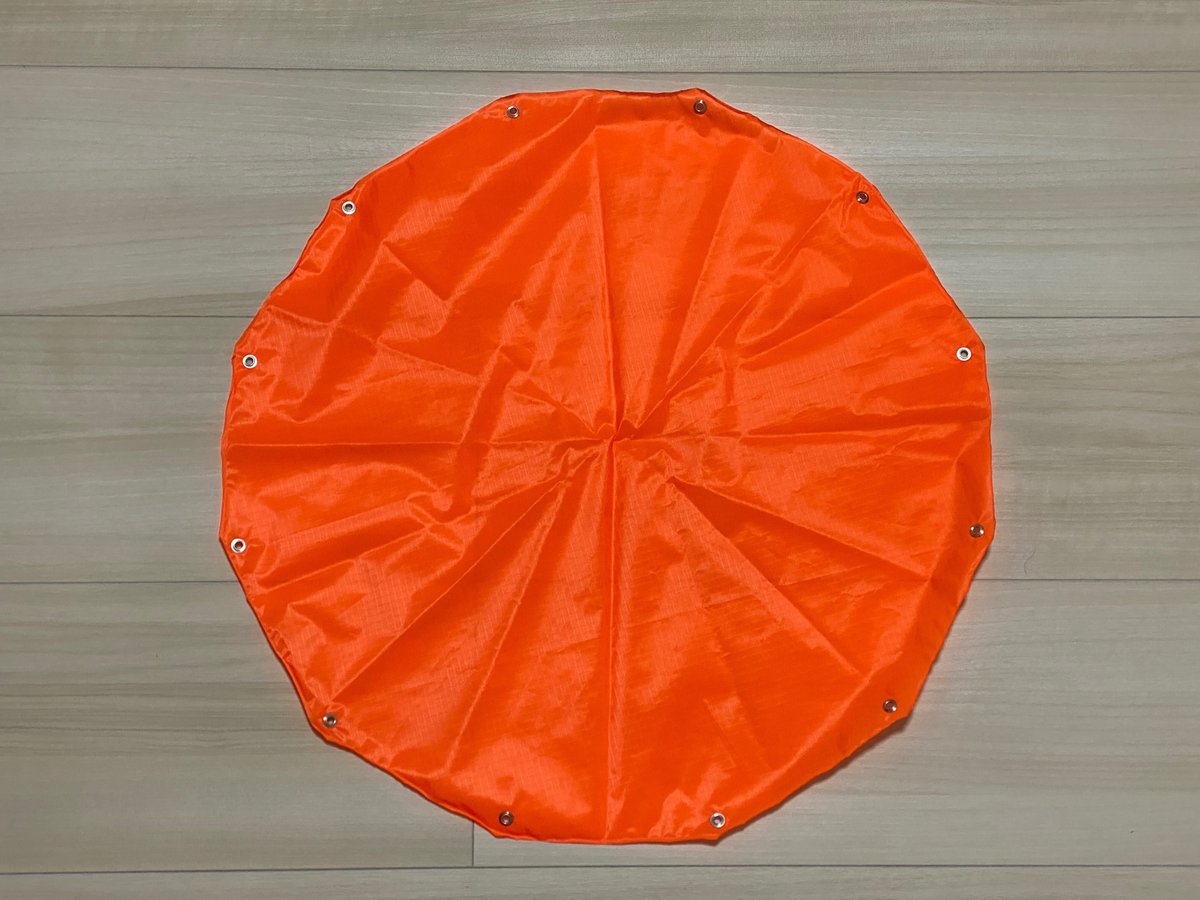
これでパラシュートの製作は出来ました。
カメラモジュールの製作
パラシュートを製作しているうちに、お待ちかねのカメラが届きました。
カメラモジュールが良質な映像が取れるかどうかが決まるポイントは、モジュールの円筒型の透明パーツの透明度にかかっています。しかも軽くて丈夫な素材であることは言うまでもありません。
アクリル、もしくはポリカーボネートの筒を探していると、厚みが2mmのものしか探し当てることができませんでしたが、ちょうどカメラの土台を含めた寸法に合うようなポリカーボネートの筒があったので、工場に連絡して特注で切っていただきました。重さが出てしまいますが、こればかりはしょうがなかったです。。
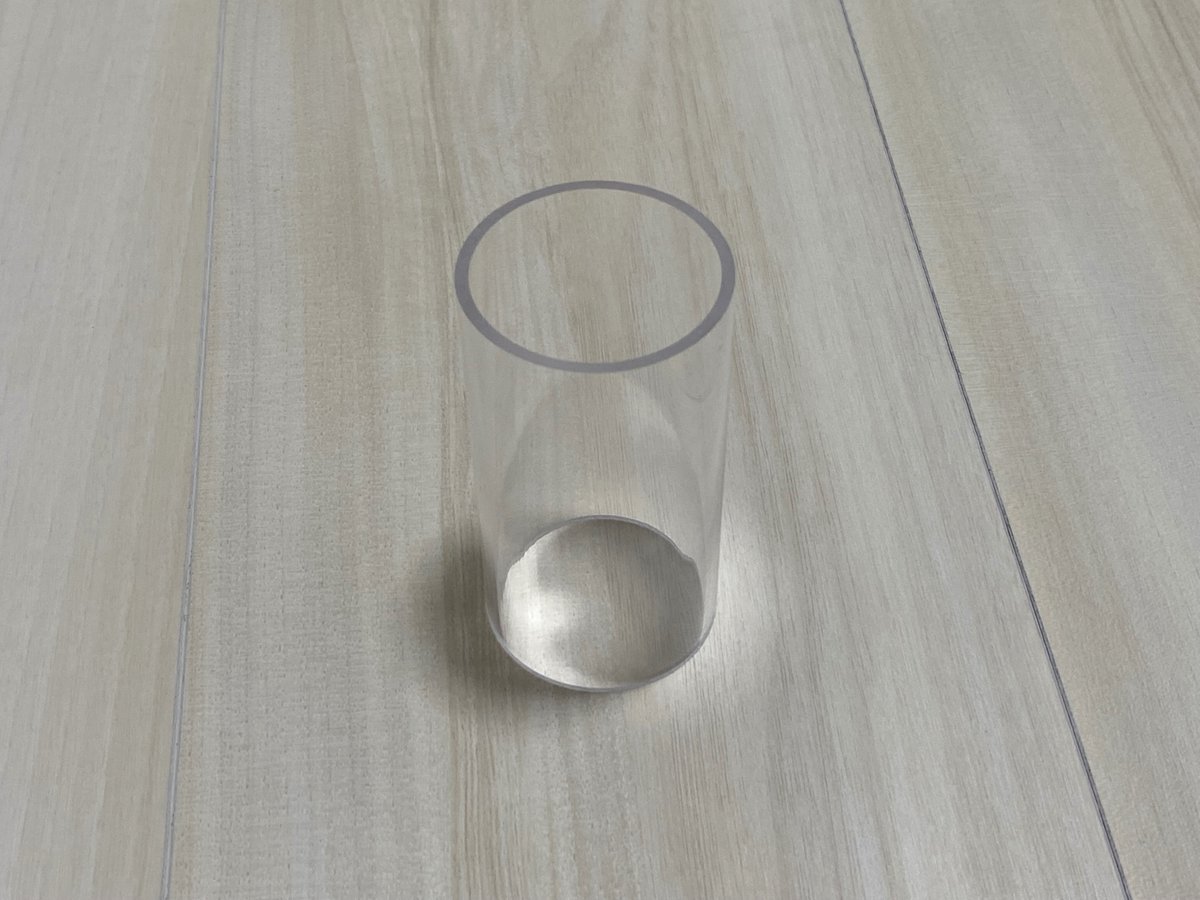
インターネットに上がっている寸法情報と写真から、カメラを固定するための土台を3D CADで設計します。
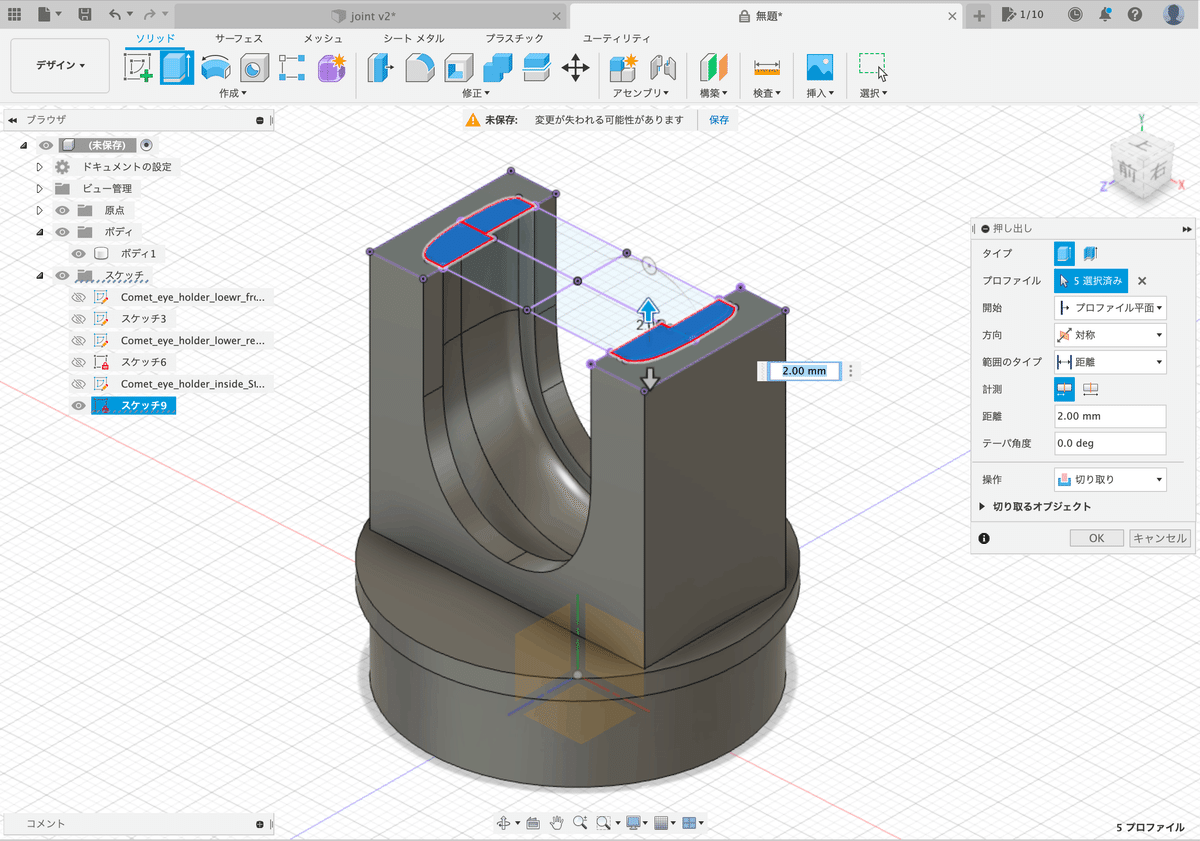
パラシュートがあるため着地の際には衝撃が加わらない見込みですが、万が一パラシュートが開かなかった場合などを考え、衝撃緩和材を挟める構造にしています。
(上画像の青い面を3D CADのスイープでくり抜いて緩衝材を挟めるようにします)
衝撃緩和材として一般的なのは綿や通称プチプチと呼ばれるような緩衝材がありますが、一部のシャープペンシルなどに使われているゲル状のグリップに代表されるゲルを用いました。
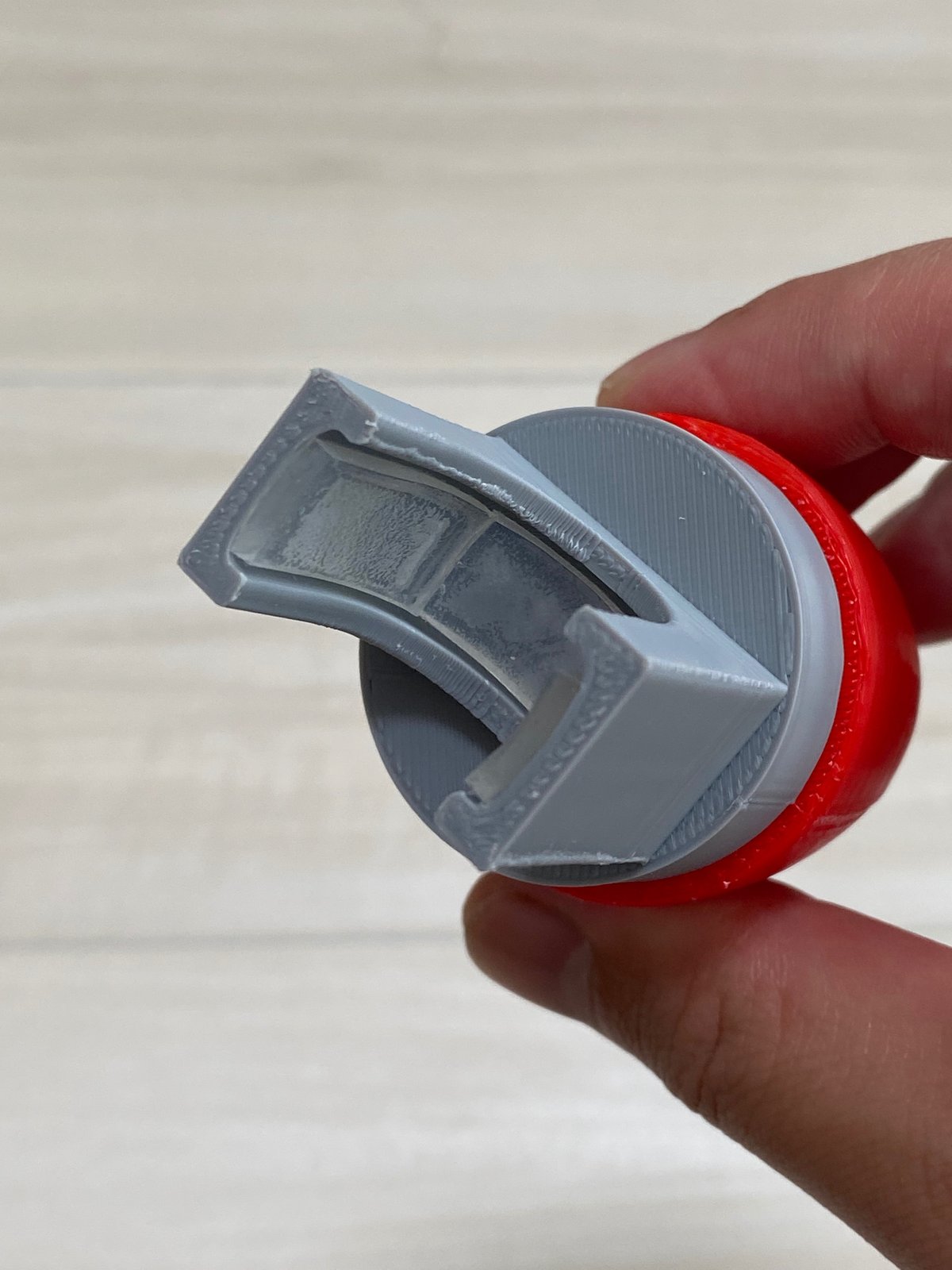
これを上下で用意します。
ノーズコーンの製作
ノーズはカメラモジュールの製作に比べれば全く難しくはありません。
3D CADでノーズ形状の半分を描き、それを中心軸を設定して回転させるだけで図面が完成します。
ちゃんとカメラモジュールとの接合部分も作っておくことを忘れずに。
形状のイメージとしては、『フォン・カルマン』ノーズをイメージしながら(出来上がりはだいぶ違う…が)抗力が少なくなるような形状を心がけました。(フォン・カルマンノーズは以下のリンク中の『Haack series中のVon Kármán』を参照)
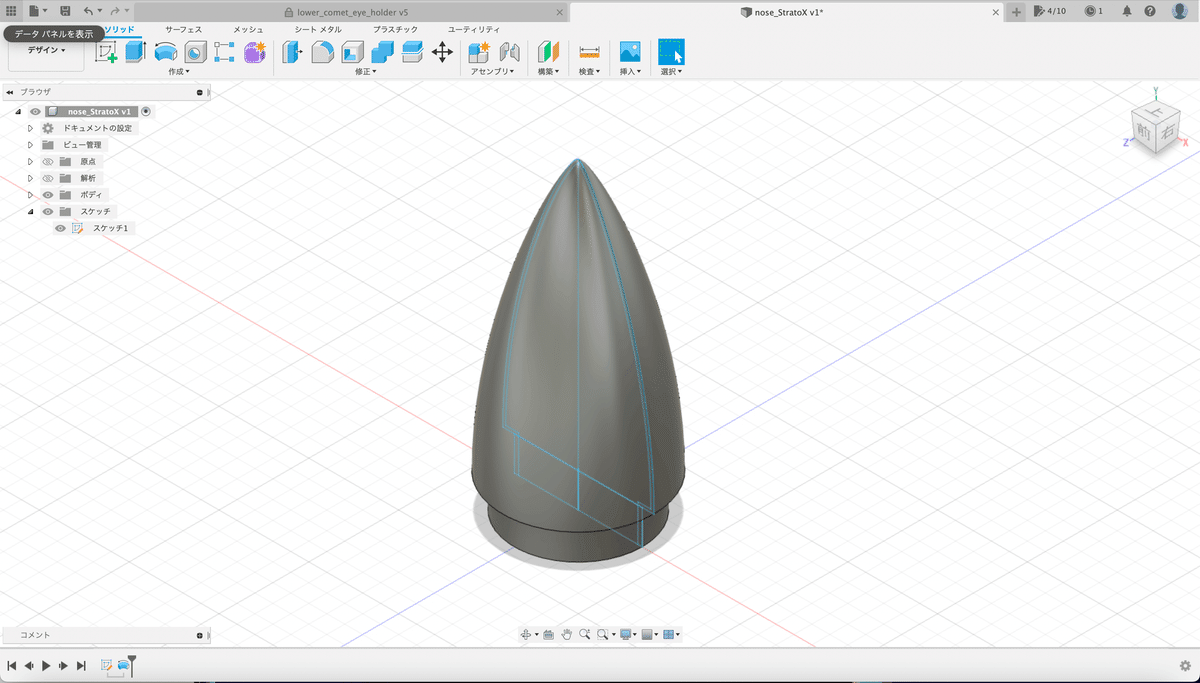
完成したノーズはこちら。
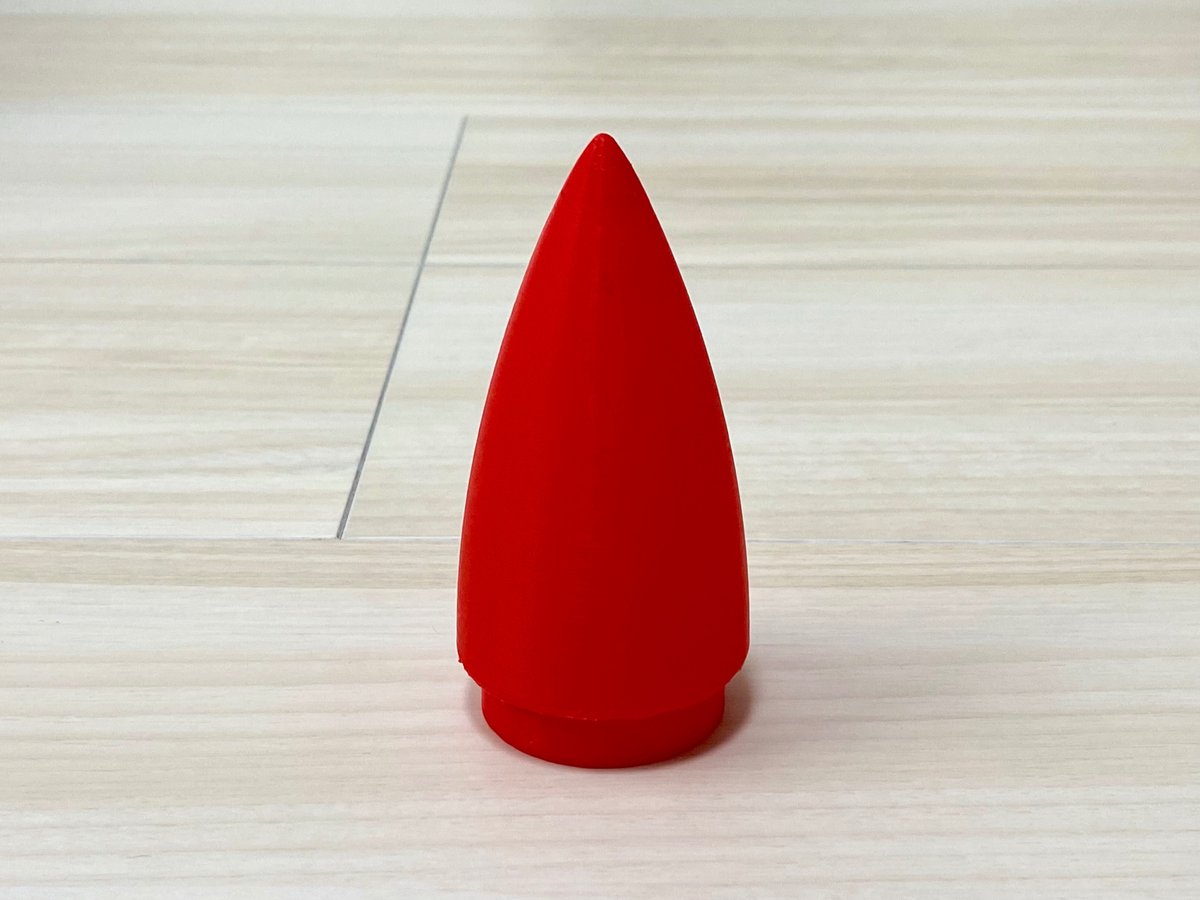
ボディの設計 / 製造
ボディは、エンジンマウント、リカバリーワディング、パラシュート、シュラウドライン、ショックコードが入る空間が必要です。さらにジョイントの接合部分もボディの長さに考慮する必要があります。
そして重要なのがボディからパラシュートがちゃんと出ることを確認することです。
パラシュートを入れたボディの反対側から、吹き矢のように息が漏れないように吹きかけて展開するかを必ず確認します。小さいことのようですが、初めての素材やボディを使用する際には特に大事なことなので、めんどくさがらずに行うようにします。
(No Imageです。。)
ジョイント部分の製造
ここはボディとカメラモジュール&ノーズを繋ぐ接続部分の設計に苦労しました。。。
3D CADで設計したデータを3Dプリンターでそのまま出力したところ、強度的に不安を感じるような出来栄えで。。。
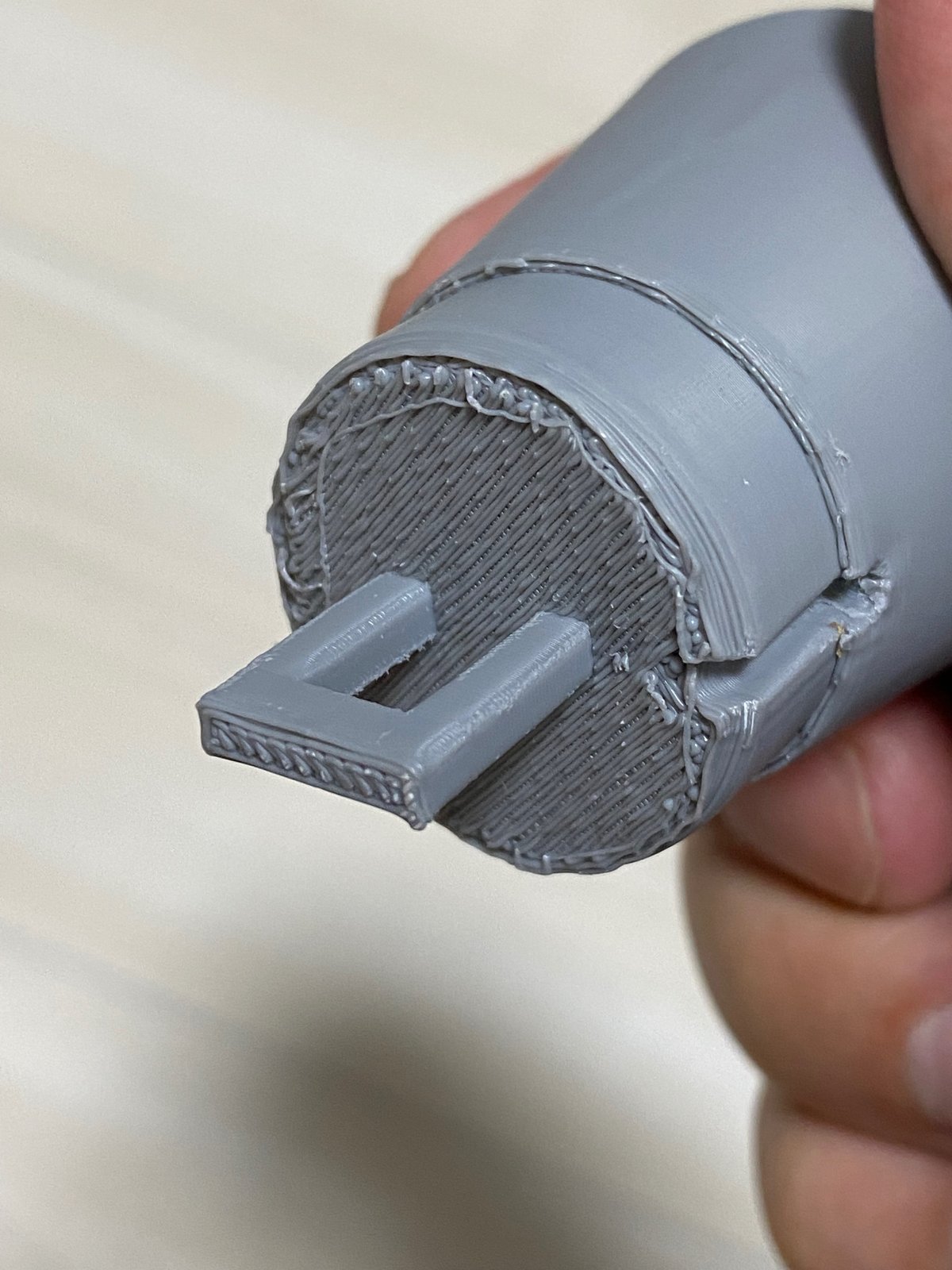
良い方法が思いつかなかったので、一旦このままで進めることに。。
カメラテスト
ここまででカメラモジュールができたので、実際に搭載してカメラのテストです。
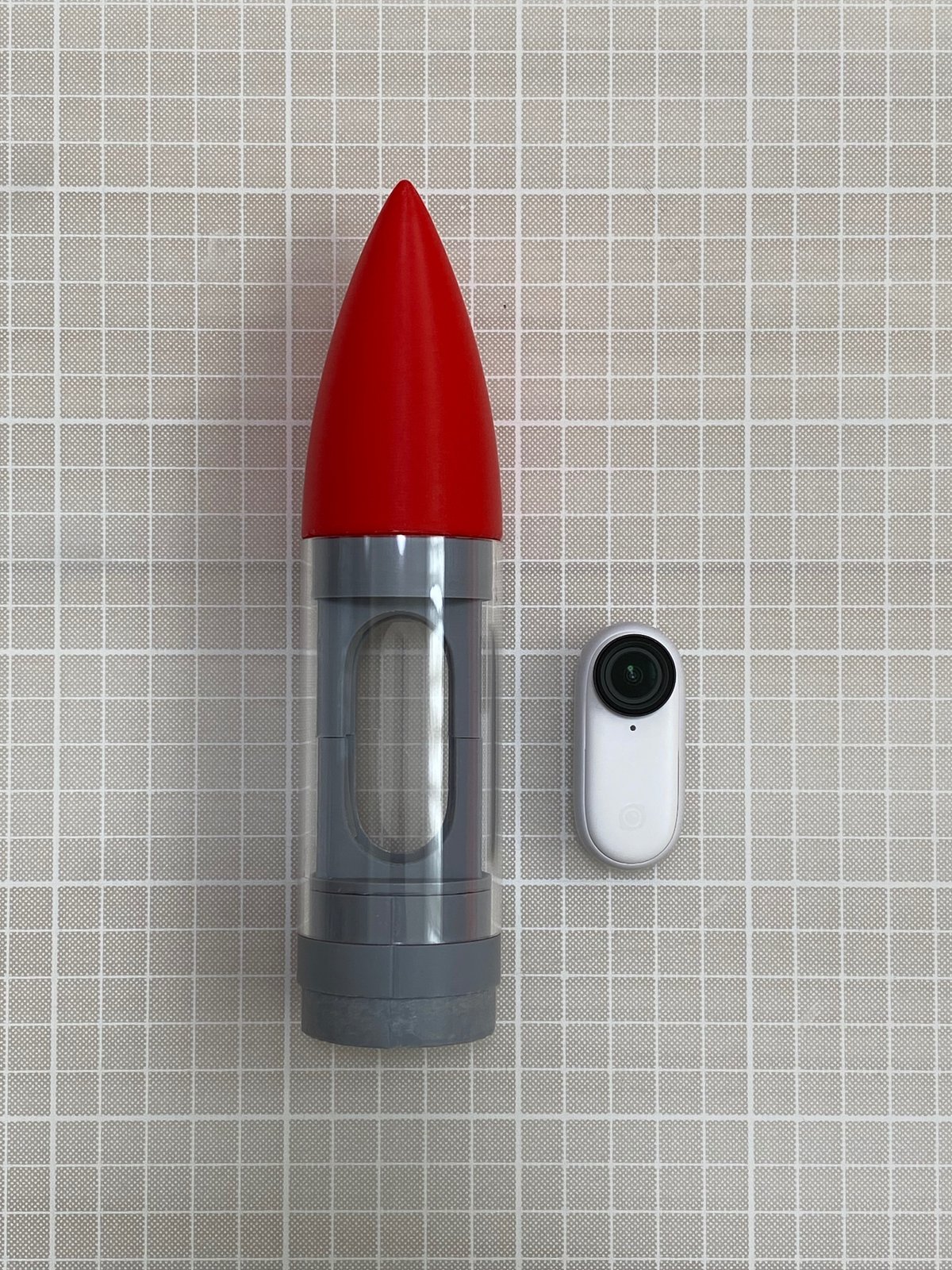
実態の映像は思ったいたよりも遥かに綺麗で、これはいける!と感動を覚えました。(周囲の民家が映ってしまっているので映像は非公開です。。)
パラシュート実験
ここでカメラモジュールとノーズが出来上がったので、実際にカメラを搭載してパラシュートがちゃんと機能するかをチェックします。
かなり慎重になりますが、これまでの自分の設計を信じて2階ほどの高さから落下させてみました。
(…。思ったより落下スピードが早い?)
ということで、パラシュートの径を900mmに変更して落下させてみました。
今度はかなりゆっくり落下することがわかり、このパラシュートでいくことにしました。
計画変更による弊害
少しヒントを出してしまっていましたが、このパラシュート変更がさまざまなところに影響を及ぼします。
まずボディです。
これまでで述べたように、パラシュート自体の大きさはもちろん、それにともないパラシュートのひも(シュラウドライン)も長くなる分、ボディの長さが足りません。。。
さらに、パラシュートのかさ(たたんだ時の体積)が大きくなる分、当初計画していたボディの直径ではパラシュートが出てこなくなることがわかりました。。。
(ここで負けるわけにはいかない。)
ということで設計をし直します。
再設計
ボディとジョイントの変更
幸いにもこの部分の変更のみで良さそうで、またラフスケッチを描き直すところからスタートです。
市販品の筒で形状に合うものを再び探します。幸いにもポリカーボネートの筒と同じ外径のものがすぐに見つかりましたので、即採用。
最終的にはこのようなスケッチになりました。
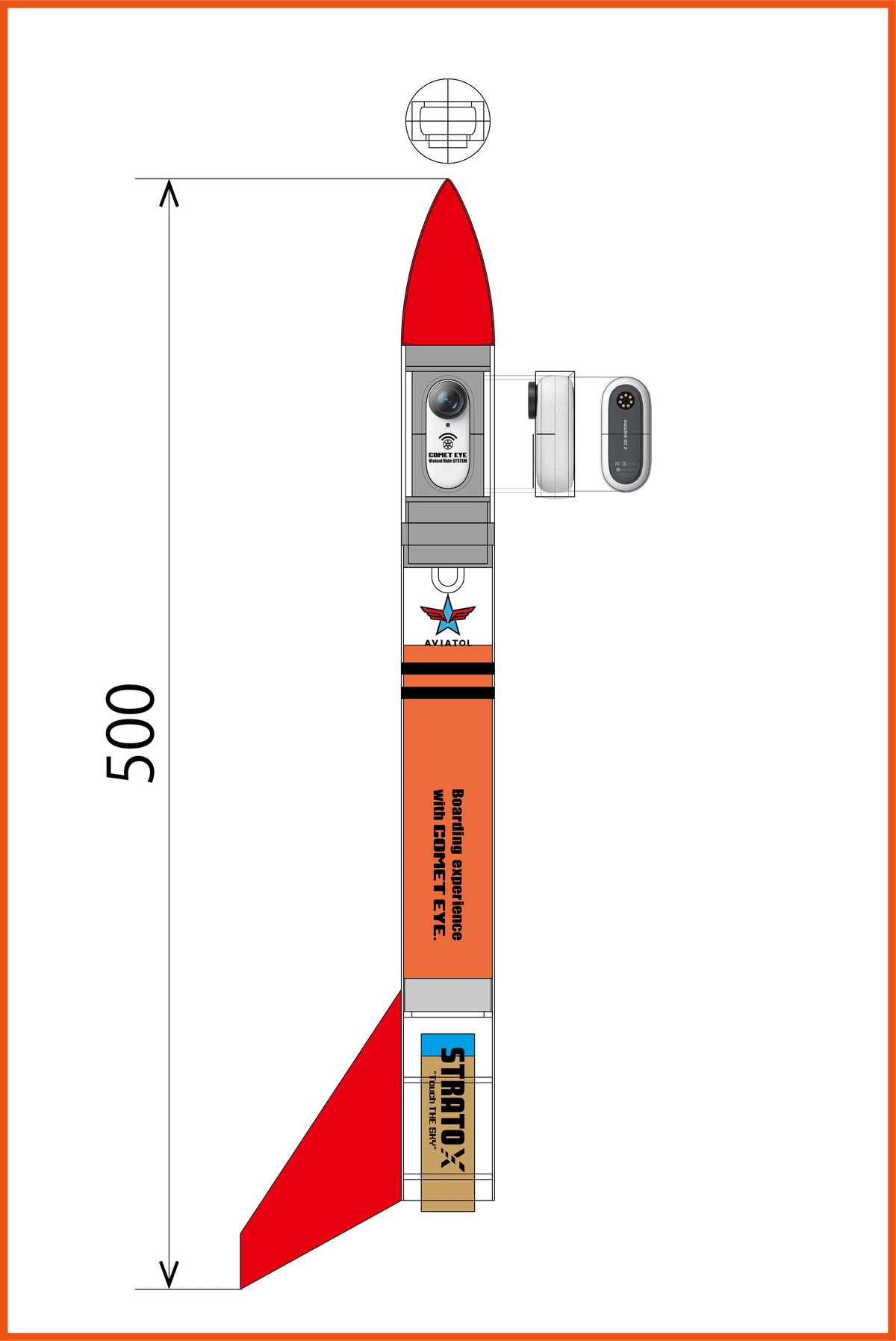
そして、ボディの部分やカメラモジュールが思ったよりもだいぶ重いことが分かりましたので、立ち上がりの推力がCエンジンの中で一番大きなエンジンである『C11-3』エンジンに変更しています。(これも私としては初使用のエンジン。。。果たしてどんなリスクがあるのか。。。)
ジョイントver2の製造
今度はボディチューブの直径がカメラモジュールの外径と同じになったので、ストレートで短いものに変更することができました。直径が違う場合、急激な外径の変化は避ける必要があります。それは飛翔中のロケット周りにおける空気の流れを考えたときに、急激な形状の変化があると空気の渦が発生し、空気抵抗が増えます。そのようなことを考える必要があったため、ジョイントには勾配をつけていました。
そして懸念していたジョイント部分ですが、ジョイントの部分自体を3Dプリンタのフィラメントで作ることをやめ、代わりにタイラップ(結束バンド)を通すような穴を開けておき、それでジョイント部分とすることにしました。
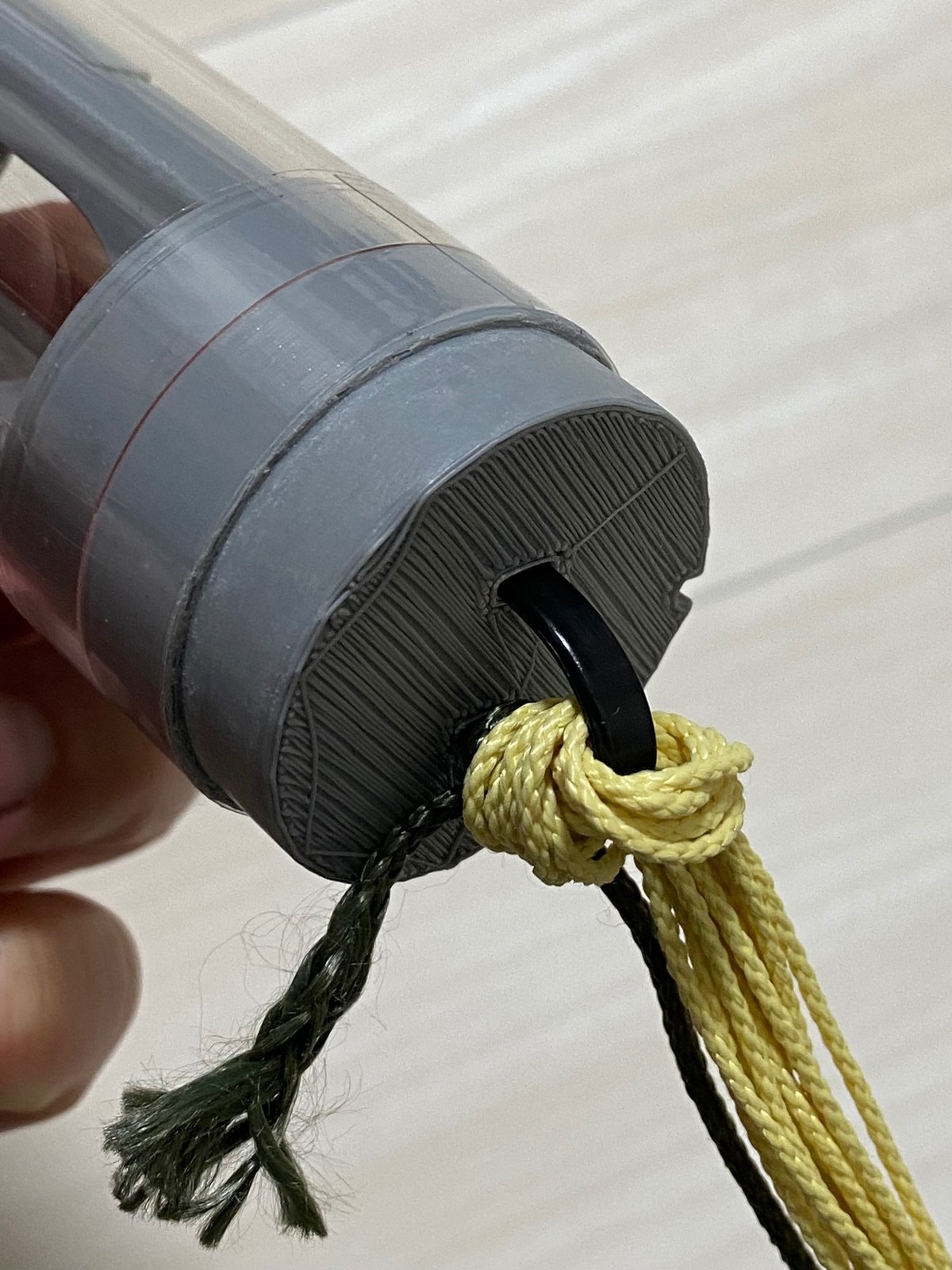
エンジンマウントの製造
『C11-3』エンジンは他のCエンジンとは規格が違います。太さが太く、φ24mmです。幸いにも過去のモデルロケット全国大会で優勝した際に副賞としていただいたEstes社の『DESIGNER'S SPECIAL』という、紙管やエンジンフック、ノーズコーンなどがたくさん入っているキットの中にちょうど良い筒があったので、それをそのまま切ってエンジンマウントチューブとして使いました。
エンジンマウントリングはMDFの2.5mm材をレーザーカッターで切って使用しています。
大きなエンジンなので、摩擦だけで固定すると万が一の時にエンジンだけ飛んでいってしまったり、逆噴射の際に空になったエンジンが落下して危ない可能性があったため、Estes社製アルファⅢキットに付属しているようなエンジンフックを使いました。
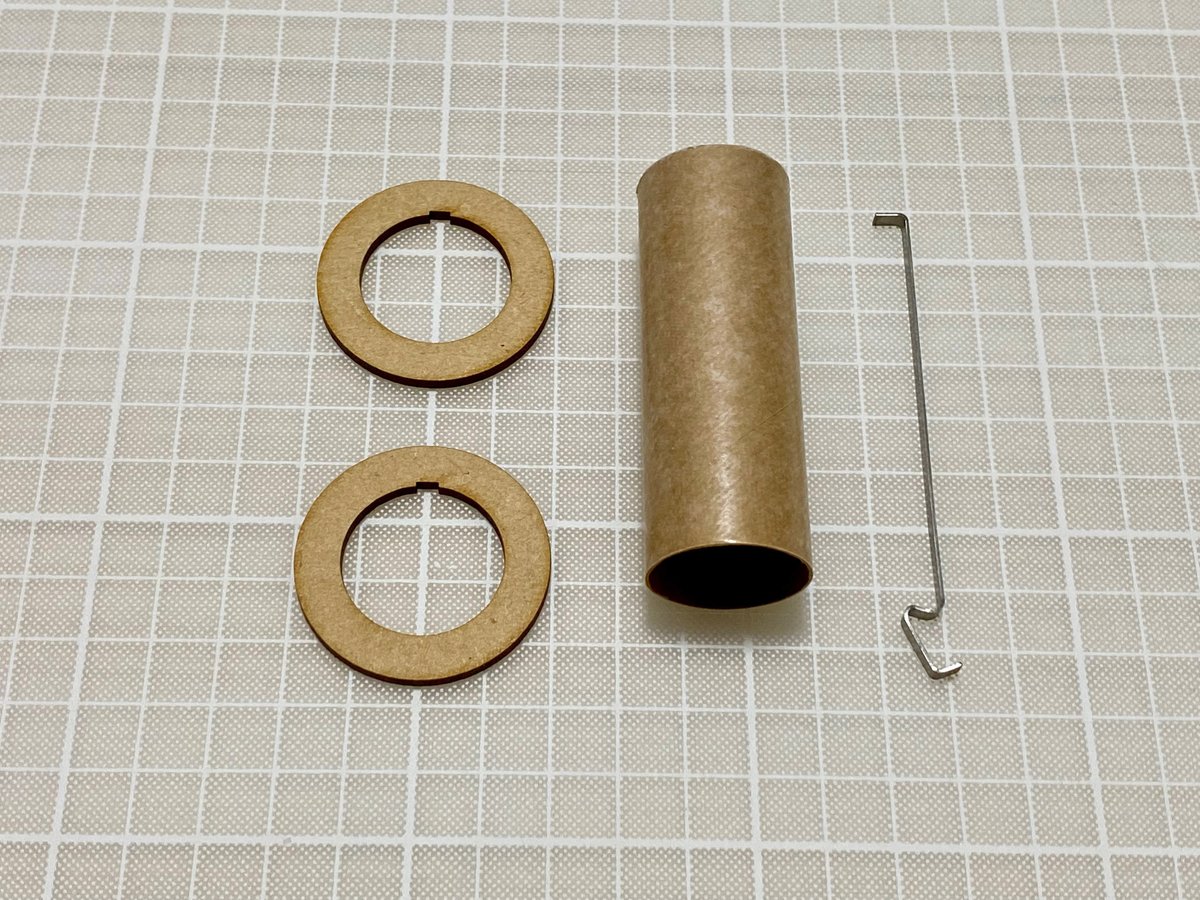
シュラウドライン/ ショックコードの製造
シュラウドライン、ショックコードはロケット全体の重さや熱対策などからアラミド繊維が必要であると考えました。アラミド繊維の糸(ケブラー)は使用の実績がありますが、その際の機体重量は40gにも満たない機体であったため、今回とは訳が違います。アラミド繊維の細い綱のようなものがネットで販売されていたので、それを採用しました。
パラシュートにつけるシュラウドラインは荷重が分散されるため、ショックコードより細い系のものを使いました。参考にAmazonで売られているもののリンクをあげておきます。長さについてですが、今回は記載しません。ある程度の答えはありますが、皆さん独自の研究に期待します。
フィンの設計
ここでようやくフィンの設計ができるようになります。フィンの設計にはロケット全体の重心位置がわかっていないとできません。フィン自体はまだ切り出していないので、仮としてフィンの重量分のおもり(まずは大体で予想します)をボディの後のほうにつけて重心位置を見積もります。
そして、フィンの設計には私の会社であるAVIATOL社内で開発中のロケット飛行シミュレーターアプリ『AVIENTER(アビエンター)』を用いました。安定性を簡易的に見積もるところの機能はすでにできているので、このロケットではその機能を使っております。
ただ、実際にその機能を使って設計して打ち上げたロケットは今までなかったため、今回のロケット打ち上げは『AVIENTER』の機能が本当に正しく動いているのか、それを実証するための打ち上げでもあったのです。
フィンの製造はレーザーカッターを用いました。材料は本来はバルサ材がよかったのですが、フィンが大きいことがネックとなり使用できません。
渋谷の東急ハンズで探していると、『フィンランド製耐水航空ベニヤ』の2.5mm厚のものが1セットだけ売っていました。他の厚さのものは全て品切れで、硬さから考えると2.0mm厚のものでも十分使用できそうでしたが、今回は2.5mm厚の板材からカットしています。
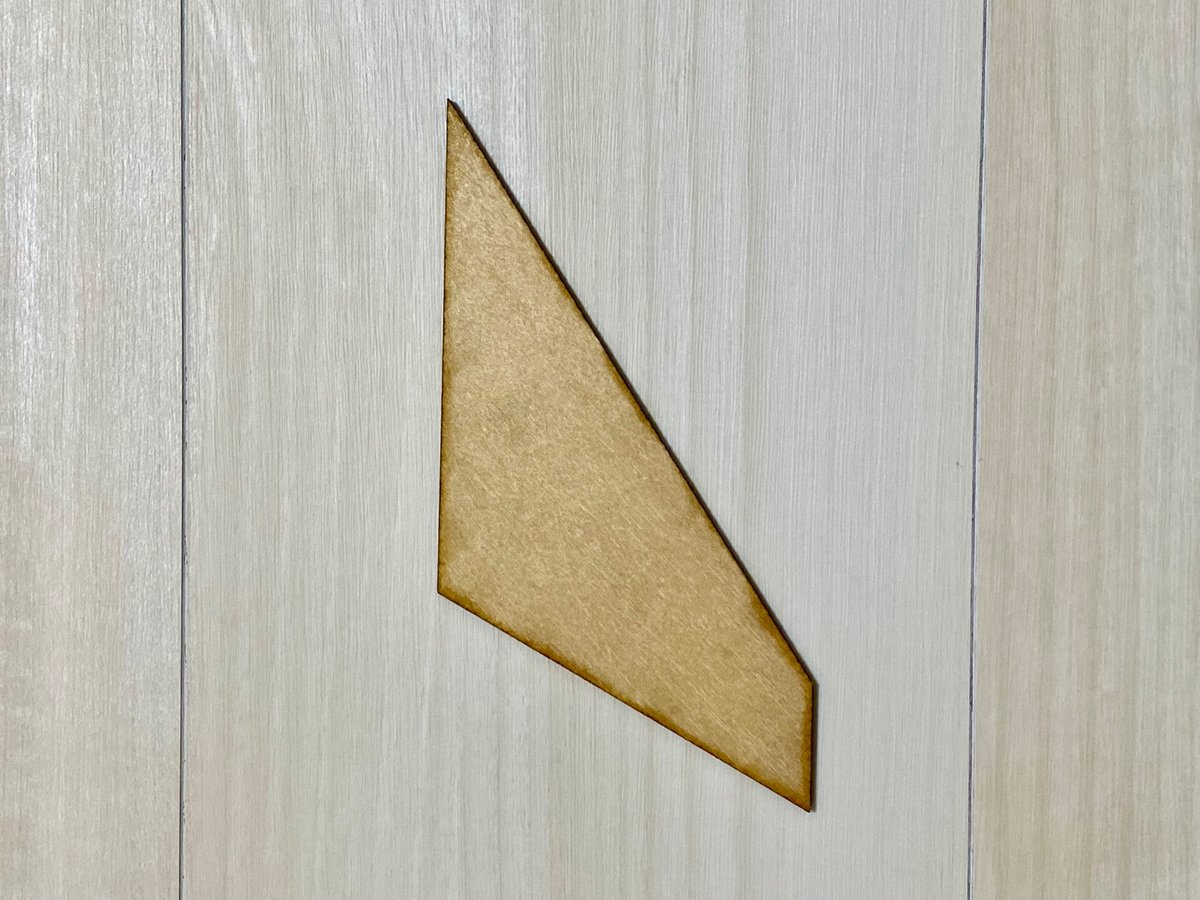
ランチラグパイプの製造
今回のロケット全部のパーツの重さを計測したら240gという、重量級のロケットになってしまいました。とてもランチロッドの径が3mmの発射台では、ランチロッドが発射の衝撃で曲がってしまい、危険な飛行に遭ってしまいそうだと直感的に判断できましたので、使える発射台をレール径(もしくは発射台の構造も)から考えなければなりません。。
ランチロッドが6mmの発射台は主にロケット甲子園で使用されていますが、中実ロッドで接合部がない場合は衝撃に対してある程度強さがあると思います。ただ、クルマで発射台を運搬する際には、発射台の長さを稼ごうとすると、どうしても接合/分解する方法しか私は考えられませんでした。(発射台の長さを稼ぐ必要がある、という話は『発射台&打ち上げ編』でご紹介します)
パイプの場合、強度を稼ぐためにはパイプの直径を大きくし、なるべく内径の小さいものをであることがセオリーです。ただ、接合部分の曲げ強度のことを考えると、パイプの内径はなるだけ大きくする必要があったため、6mmより一回り大きな8mmのパイプを使うことにしました。
その条件から、ランンチラグパイプの内径が8mm以上であることが要求されることが決まりました。
パーツのオーバービュー
ということで、パーツが全て出揃いました。
これを組み立てていきます。
エンジンマウントをボディに接着する際には、慎重すぎるくらい多めに接着剤を使いました。エンジンの力はエンジンフックを伝い、エンジンマウントリングを通してロケット全体を押し上げます。先ほども記載しましたが、エンジンマウントも機体から外れてしまうと大きな事故につながる可能性を秘めています。くれぐれもエンジン周りの接着は慎重に行いましょう。
フィンをつける際には、3枚フィンの場合、ピッタリ120°の角度でつける必要があります。一番簡単な方法は紙に中心点を描き、まずはエンジンの直径の円を中心点を基準にして描きます。(その際、円のテンプレートがあると便利です。)その後、中心点から120°の線を分度器を使って描いていきます。最後にボディの直径の縁を中心点を基準にして描き、フィンを取り付ける際のガイドが完成します。
それを使ってボディの一部にペンで印をつけ、直角なL字型の建材?(ホームセンターに売っています)を印に合わせて線を引いていきます。
そこにフィンをつければ正確に120°で設置することができます。
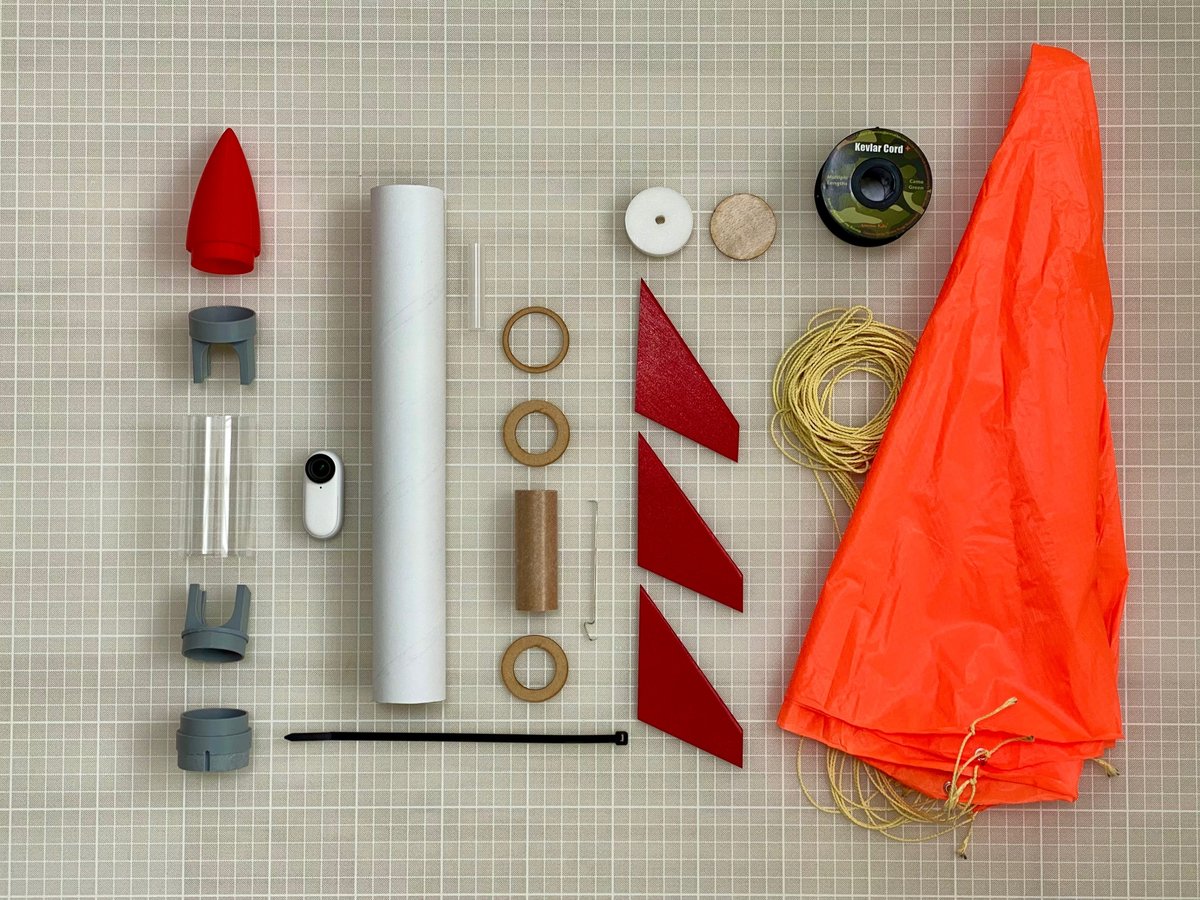

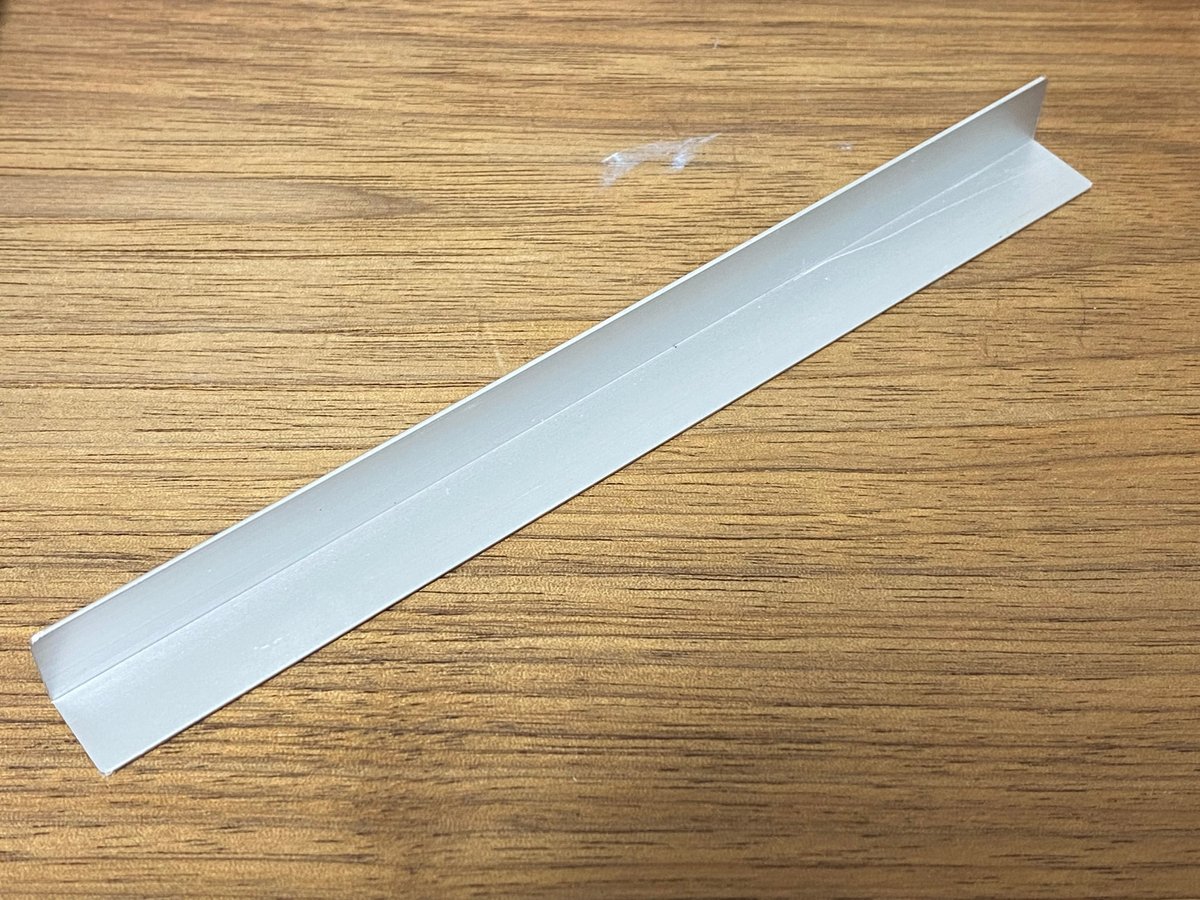
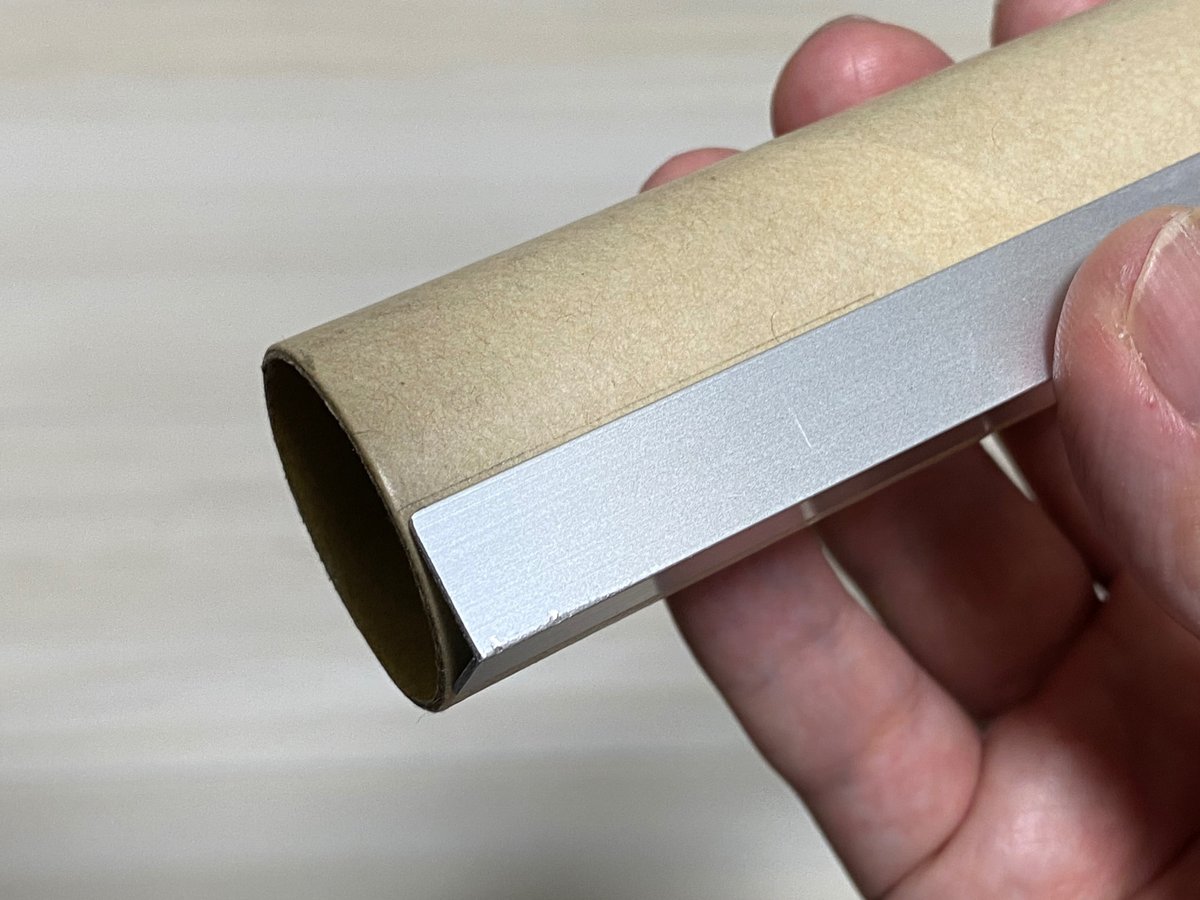
最終的に完成したロケット
最後は苦労して出来上がったパーツひとつひとつを組み立てていきます。
製作において最も充実感がある瞬間です。
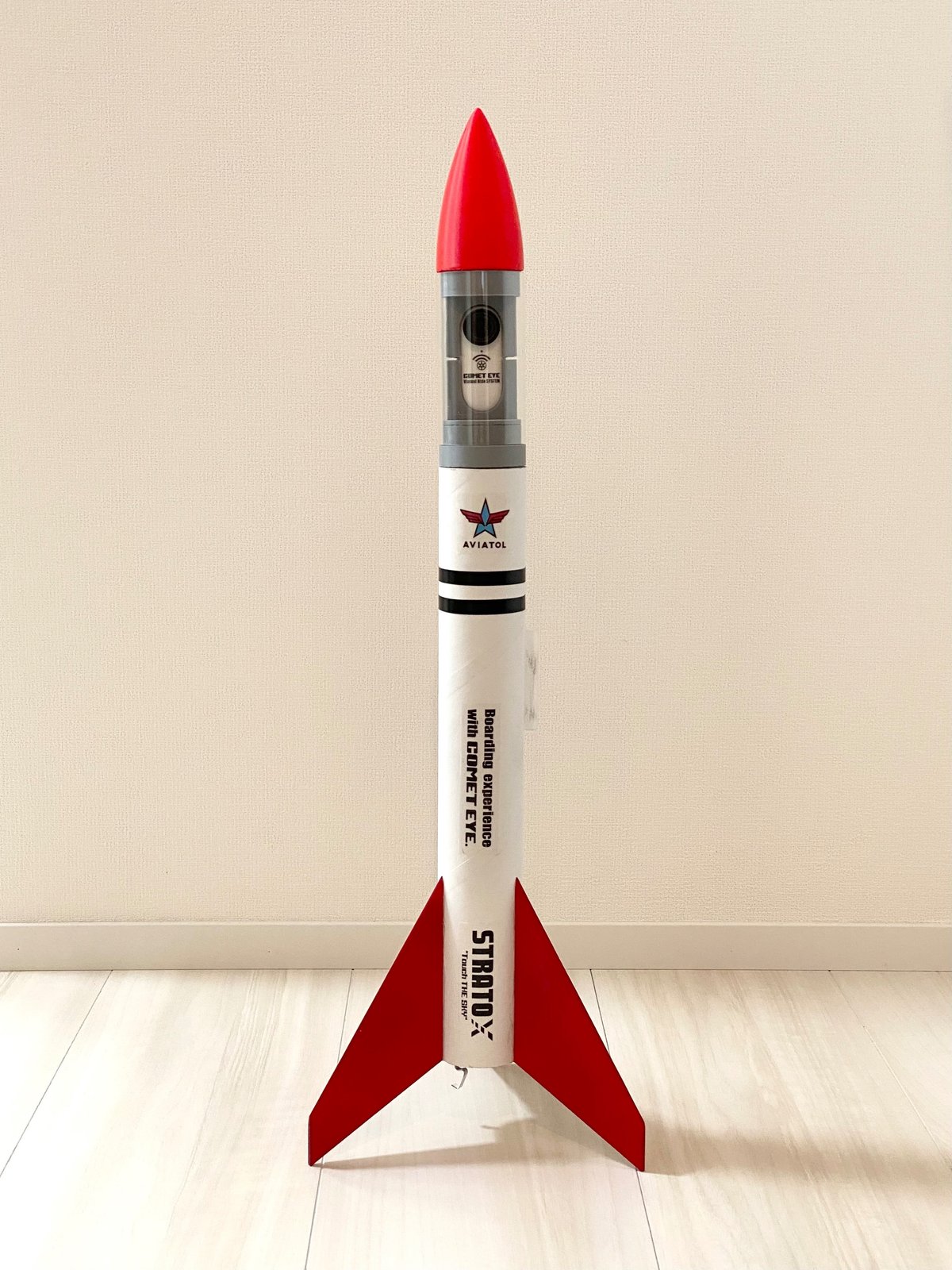
もう、言葉はいらないですよね。
この写真が『全て』です。
後記
実はここには詳しく書いていないような失敗が何個もありました。例えば塗装がうまくいかなかったり、フィンをつけたら重心位置が大幅に変わってしまいフィンを作り直すとか(←これはかなりの大ダメージ)…。
でも、この計画だけは絶対に失敗させてくなかった。今年のロケットランチ2022で必ず飛ばすんだ、みんなにロケットに乗っているような体験を味わってもらうんだ、という思いだけでここまでやってこれたのだと思います。
次の記事『モデルロケットにカメラを搭載して映像をとる #発射台製作&打ち上げ編』では『発射台製作と打ち上げの結果』をご紹介します。
この記事が気に入ったらサポートをしてみませんか?