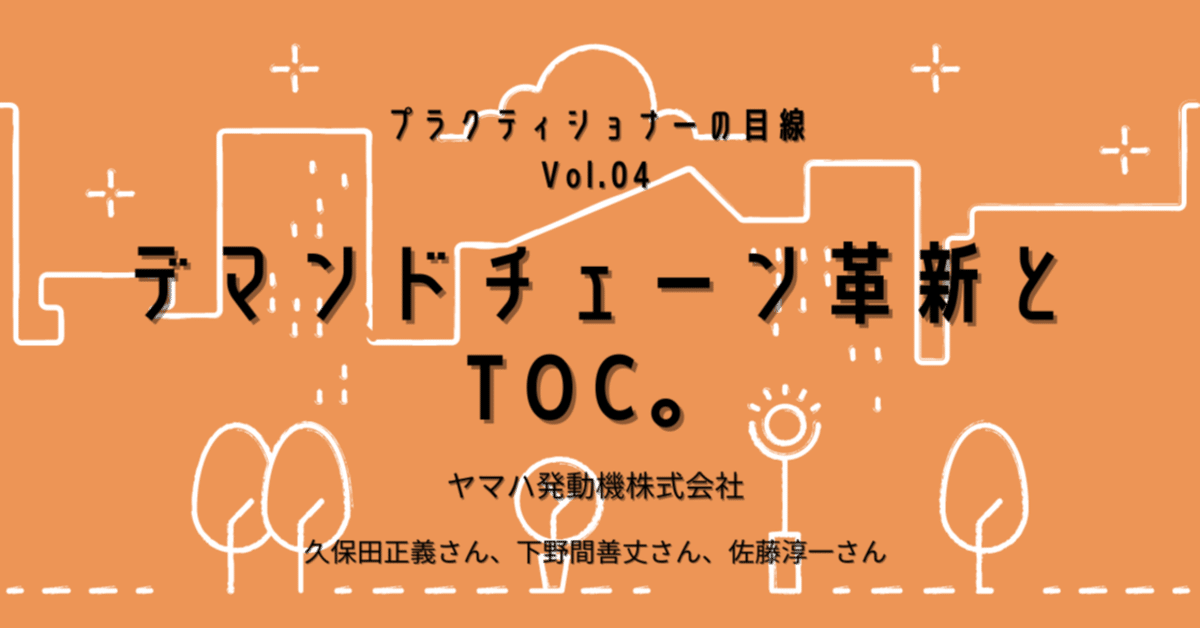
デマンドチェーン革新とTOC。
まえがき:
今回は、以前ご紹介したインタビュー記事「Vol.1:(前編)バブル崩壊、構造改革からのスタート」および「Vol.2:(後編)真の一貫工場へ。」でご協力いただいたヤマハ熊本プロダクツ株式会社(以下、YKP)の佐藤淳一さんに再度ご登場いただき、佐藤さんが2017年初めからヤマハ発動機株式会社(以下、YMC)のモーターサイクル事業に出向されて以降、YKPでの導入実績をYMC本体の問題解決にどのように繋げていかれたのか、その経緯を振り返っていただくところからお話を伺いたいと思います。
また、YMCからは、2018年11月の第41回TOCPA国際カンファレンスで「エンジン部品製造部門におけるMTO/MTAハイブリット生産方式導入」をご発表いただいた久保田正義さんと、2019年11月の第44回TOCPA国際カンファレンスで「MTA+*横展開の心得」をご発表いただいた下野間 善丈さんから、「YMCにおけるTOC導入と横展開」を牽引してこられたそのご経験を共有いただきたいと思います。
* MTA+(Hybrid-DBR: YMCではMake to Availability PLUS/Production Logic of Usable Signalと命名されています)
-熊本子会社から静岡本社への広がり。
『佐藤さん、2016年に福岡で開催されたカンファレンス*に、YMC本社の生産管理部長を招待されていましたね。』
*2016年5月に開催された第26回TOCPAカンファレスで、佐藤さんは「TOC補充ソリューションを用いた生産方式改革/受注生産(MTO)から在庫補充生産(MTA)への移行」というタイトルで、YKPでの取り組みを発表されています。
佐藤:はい、あの時の「これをオールヤマハで展開すれば、効果は熊本の50倍だ!」というYMC生産管理部長の言葉には大変勇気付けられました。私がYMC(磐田)に出向する前年の2016年、YMCでは「デマンドチェーン革新」を推進するための専門部署が発足し、既に「需要の変動に応える製造工場の在り方」について本格的な検討が始まっていました。そこへ2017年1月から生産管理の立場で合流し、デマンドチェーン革新プロジェクトのメンバー達と連携していくことになりました。
-デマンドチェーン革新部の構想。
佐藤:当時、私たちの状況をヒアリングしていただいた白土さん(株式会社ジュントスコンサルティング代表取締役)は、2016年に発足したデマンドチェーン革新部が構想していた内容とTOCの考え方との間に、多くの共通点があることに大変驚かれたそうです。そこで、デマンドチェーン革新部が構想していたスキームに連動する形で、かつ副作用をもたらすことなくTOCを適用していくための方法を、慎重に検討していくことにしました。当時、「市場在庫が多すぎる」という問題に対して、「在庫を減らしつつ、かつその利用可能性を保証するための論理的な基準在庫をどう定めるか」が議論の焦点となっており、私たちはそこにフォーカスして議論を重ね、2017年7月頃、白土さんに本格的な現地調査を実施していただくことになりました。この調査の結果、MTIA(Make to Internal Availability)の適用可能性が高いことが明らかになったため、パイロット検証の実施を上申することになりました。
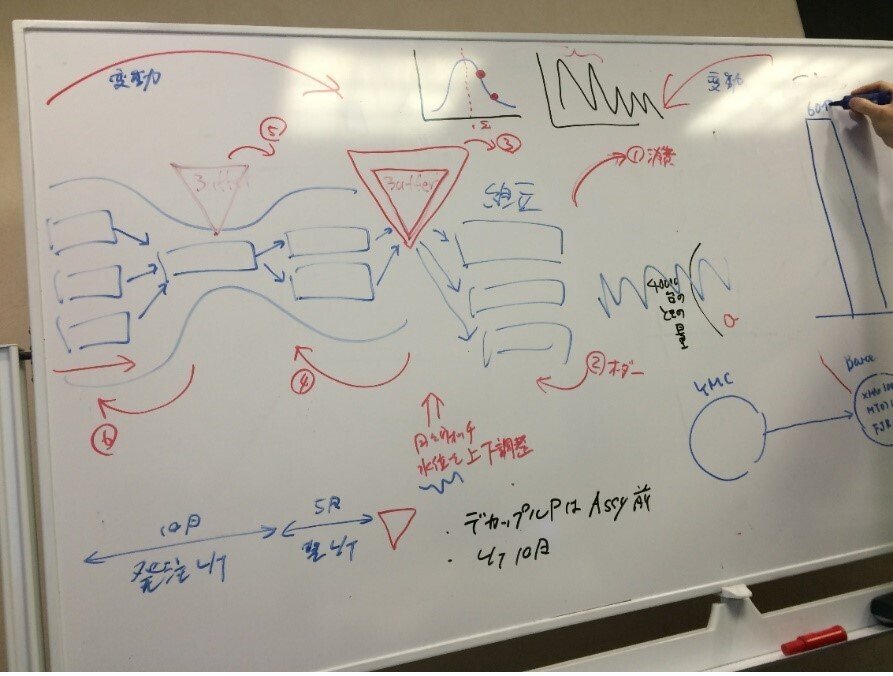
-適用可能性の検証(POC)
『久保田さんは、2017年に海外の駐在先から帰任されたと伺いましたが。』
久保田:はい、2017年の夏、生産管理担当として駐在していたブラジル現地法人から戻って生産企画に帰任する予定だったんですが、急遽アルミ鋳造工場に配属されることになりました。すっかり生産企画に戻るつもりでいましたから驚きましたね。帰任直後に、当時の執行役員から同工場の改革について命を受けることになったのですが、先ほど佐藤さんが説明されたような経緯については、知る由もありませんでした。(笑)
『帰任直後の工場の様子を教えていただけますか。』
-アルミ鋳造工場が抱えていた課題
久保田:アルミの鋳造加工部署内では、詳細な計画を立て、計画主導でリードタイム短縮や在庫削減を目指すプロジェクトに取り組んでいましたが、なかなか4M(Man:人、Machine:機械、Material:材料、Method:方法)リソースが安定しない、そして計画順守率も改善されない、という状況で、現場には手詰まり感が広がっていました。「どうやって改善していこうかな」と思案していた時、ベテランマネージャーの故飯尾さんから、ある企業に導入されたTOCの話を紹介され、その後ジュントスさんとお目にかかることになり
ました。正直なところ、最初は「本当にできるのかな?本当に効果が出るのかな?」という懐疑的な気持ちの方が強かったように思います。
『YKPでMTAに取り組まれていたことはご存じだったのですか?』
久保田:はい、佐藤さんからお話は聞いていました。ただ、「YKPでうまくいったので本社でもやってみよう!」という言い方はしませんでした。やはり、「自分達で考えて、新しいものにチャレンジしていこう!」と言う方が、前向きに受け止められやすいですからね。
佐藤:そうですね。TOC導入を検討する場面に数多く関わってきましたが、異なる部署やグループ会社で成功したものをそのまま適用しようとしても、「商材が違う。扱うものが違う。」ということになりますから、「環境ごとに異なるユニークな問題を丁寧に扱いながら、現場の土壌に合ったコトバに変換してコミュニケーションしていくことが重要」だと感じています。
-お医者さんの話。
久保田:以前、白土さんからお医者さんの話を例に挙げて説明を受けたことがあります。病気の症状が出ている患者さんを診察する時、その症状の根本原因が何であるかを注意深く突き止めてから処方箋を出す必要があるというお話です。この話はとても理解し易いものでしたから、私も現場で何度も使わせてもらいました。「良いソリューション(良い薬)があるからそのまま持ってくる」というアプローチにならないように注意しなければなりませんね。
佐藤:下野間さんの発表*にもあったように、「現場にある一次情報を拾って、まずは問題を正しく捉えること。」これは、適切な処方箋を書くために不可欠ですね。
*第44回TOCPA国際カンファレンス「MTA+横展開の心得」
『ソリューションありきではうまくいかないということですね。では、TOCが有効な処方箋だと確信されてからは如何でしたか。』
久保田:当時、製造現場は度重なるプロジェクト活動に疲れている感じで、「また何か新しいものをやるのか?」という雰囲気が漂っていましたから、これは一筋縄にはいかないと思いました。ただ、そんな中でもTOCの話を持ち掛けてくれた故飯尾さんだけは、「お前が分かったと言うならやってやろう!」と言ってくださり、現場の方々への説明や説得の場面で、度々力になって下さったのを覚えています。
-「計画生産からの脱却!?」が波紋を呼ぶ。
久保田:2017年12月。執行役員や統括本部長が出席する会議の場で、TOCソリューションの適用可能性に関する検証結果を説明し、POC(Proof of Conceptの略。以下、POC)実施可否の判断を仰ぐ機会がありました。しかしながら、「緻密な計画に基づく生産から、不確実性を上手く扱うための新しいアプローチへの転換だ!」と私が発言したことについては、大きな波紋が広がってしまいました。従来の計画主導型の改善スキームから、突然「在庫補充生産」を適用するという変革案でしたから当然かもしれません。計画の精度を上げていくことに全力を尽くしてきた私たちにとって、在庫を持つことは「悪」であって、プロセスの安定には貢献しないという考え方が根付いていました。しかし一方で、現実に目を向けてみると、計画の精度を求めながら在庫を削減するにしたがって、生産活動はさらに苦しくなっていく。そして苦しくなった現場に対して更なる改善が求められる、といったスパイラルに陥っていたように思います。ちょうど会議が終盤に差し掛かり、持ち帰りになることを半ば覚悟しかけていた時でした。当時の執行役員から「これはやってみないと分からないから、まずやってみよう!」という一言があり、その言葉に後押しされる形で、なんとかPOCをスモールスタートすることになりました。
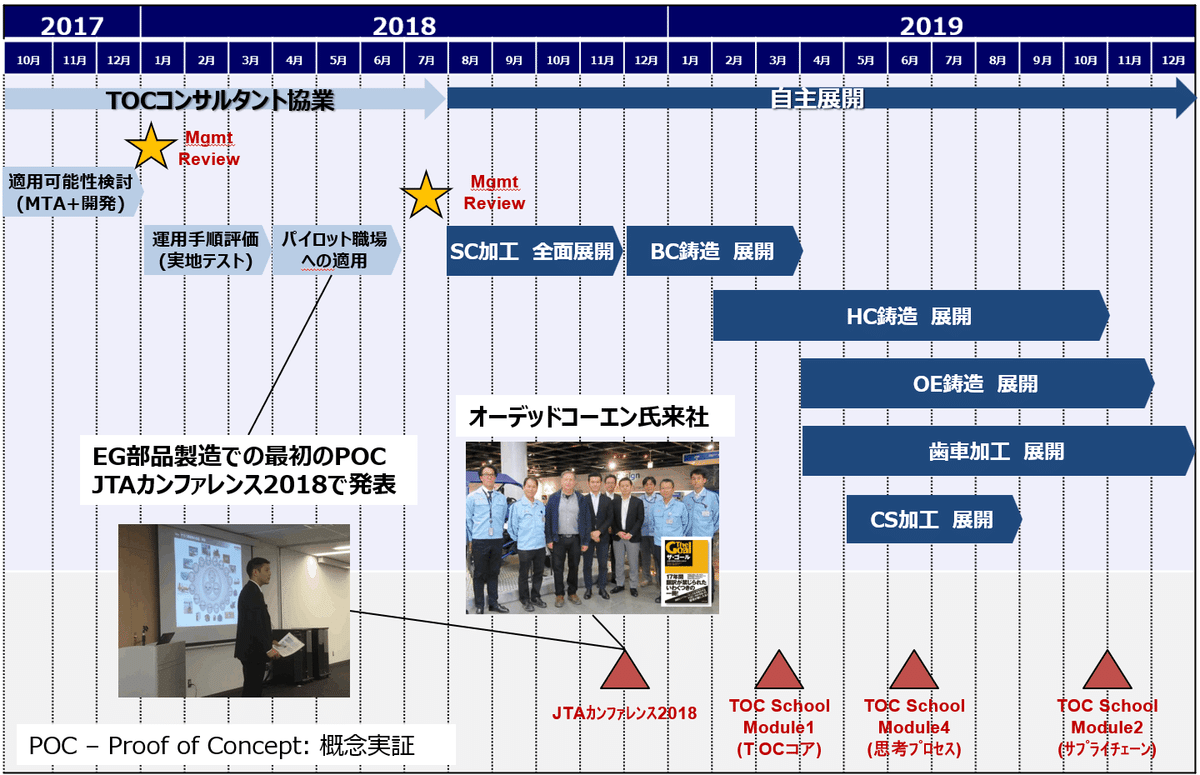
-いよいよPOCスタート!
久保田:2018年の1月から3月にかけて、まずは在庫の滞留問題を抱えていたダイカスト鋳造で、メインの2機種に絞ったPOCをスタートしました。補充生産の計画など、最初はエクセルで立案したので大変でしたが、エクセルだと計算式が良く分かりますから、MTAというソリューションのロジックを関係者が理解するのにはとても有効でした。このフェーズでは適用対象を限定していたため、得られた効果もごくわずかでしたが、「品目数や工程を拡げて適用すれば、より大きな成果が得られるだろう」という確かな手ごたえが得られたことは大きかったです。
-カムシャフト加工職場の問題が浮上。
久保田:そんな時、期せずしてカムシャフト加工職場の問題が打ちあがってきました。熱前加工→熱処理→熱後加工→ラップ工程と、複数の工程が連なる過程で、本来なら十分に能力が有るはずの「熱後加工」がネックになっているという不思議な状態だとのことでした。早速詳しくヒアリングしてみると、熱前加工ではロットサイズをまとめている一方で、後工程は出荷に追われて段取りを細かくせざるを得ないなど、職場間の連携がうまく取れていないことが分かりました。各職場の計画はMRPで展開されていたものの、その日の生産品目は各ラインを担当する現場リーダーの裁量に委ねられ、ホワイトボードに直接書き込まれるといった状況でした。カムシャフト加工内の各職場は、それぞれの工程を強化しようと懸命だったわけですが、全体像の理解を深めていくにつれて、MTAという在庫補充方式が「(単なる仕組みではなく)職場間や工程前後の関係性を築いていくための考え方」であることを職場のメンバーが理解し、そして大きな効能があることにも必ず気付いてくれるだろうという確信を得ました。
『カムシャフト加工でのPOCはスムーズに進んだのですか。』
-懐疑的な反応。
久保田:いざカムシャフト加工で始めてみようとしたものの、(私が最初そうであったように)周囲には懐疑的な声が多く、反応は冷ややかで、なかなか協力が得られませんでした。「これまでの改善活動でも解決できなかったんだから難しいだろう。」との声があったのも事実です。
-MTAは回転寿司。計画生産は寿司屋。
久保田:私は、カムシャフト加工の職長に了承を頂いた上で、現場のリーダーや段取りマンに直接コンタクトして、休憩所でMTA+の概要を説明する時間を割いてもらうことから始めました。なかなか理解してもらえずに苦労することが多かったので、「MTAは回転寿司。計画生産は寿司屋。」という喩え話を持ち出したり、ジョブショップゲームでソリューションの効果を体感してもらったり、またある時には現場のホワイトボードを使って表示するなど、あの手この手を使って、現場の人たちに理解してもらうための工夫を凝らしました。この時、彼らと膝を突き合わせながら、ソリューションの有効性を説明する場面でいつも力になっていただいたのが、故飯尾さんだったことを、ここでお伝えしておかなければなりません。
-「紙」でやると理解してくれる。
久保田:現場ではマグネットとポストイットを使って、全て手作りでスタートしました。紙でやった方が、みんなが確実に理解してくれるんですよね。実は、手作りのMTA管理ボード(以下の写真)は現場が自ら発案したものなんです。押し付けられたものではなく、自ら考えて作ったものを運用するわけですから、そこには何の抵抗もありませんでした。
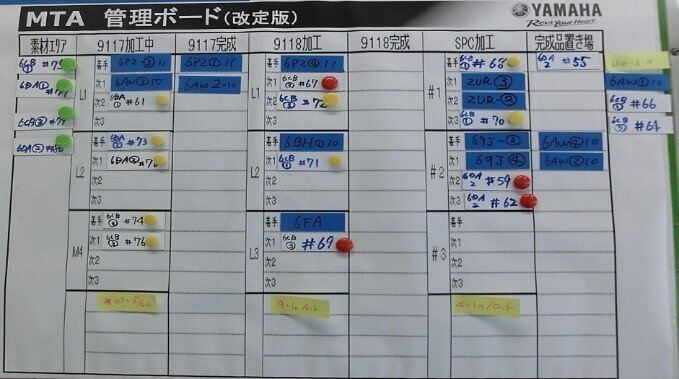
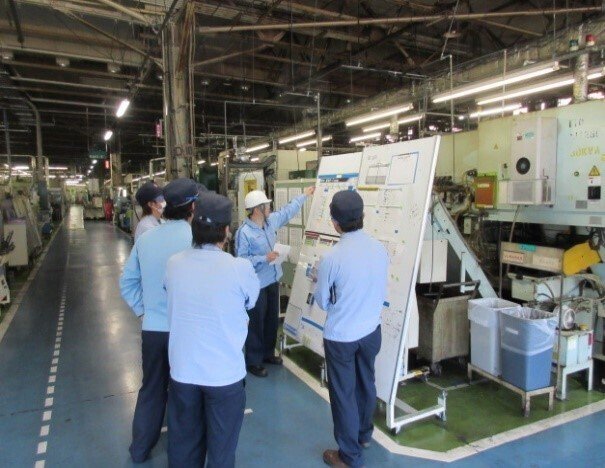
-見えてきた改善ポイント
久保田:工程が見えてくると、徐々に改善ポイント(ネック工程)が分かるようになり、その結果、現場から改善提案が生まれるようになりました。この提案に対して、製造技術などの関係部門から積極的な協力が得られたことで、現場はさらに活気づきました。幸いなことに、製造技術にはブラジル駐在中にお世話になった方がいて、現場のBM会議*に足を運んで下さったのは大変有難いことでした。こうして少しずつ協力者が増えるに従い、職長や工長も現場の変化に注目してくださるようになりました。その後間もなく、ネック工程の改善効果が顕れましたが、ネック工程に焦点を絞った改善活動を進めたことで、成果創出のメカニズムも分かりやすく説明することができ、当初懐疑的だった関係者からの理解も得られるようになっていきました。思い返せば、当時ご指導いただいた白土さんには、幾度も油まみれの現場に足を運んでもらったのですが、普段あまり見慣れないスーツ姿の方とのコミュニケーションが、現場にとっては良い刺激となり、変革機運がさらに高まっていったように思います。
*BM会議(Buffer Management会議の略)
-生産計画が要らない?
佐藤:パイロット検証を進めていた頃、生産副本部長が「これって、生産計画は要らなくなるってことですよねえ。」と小さな声で呟かれたのを覚えているのですが、検証プロセスのまだ早い段階でソリューションの基本コンセプトを理解されていたことに驚嘆しました。通常、パイロット検証の過程では、「スモールスタート&スモールサクセス」を積み重ねていくことで、少しずつ「問題と解決策を繋ぐロジック」の理解が深まり、それが確信へと変化していきます。現場と上層部の双方が「ソリューションの方向性に間違いがないこと」に自信を持ち、相互尊重のスタンスを保ちながら更なる高みを目指せる組織でありたいですね。
『いよいよ本格的な導入開始ですね。』
-システムありきで思考停止にならないこと!
久保田:ホワイトボードとポストイットから始まったMTA+も、カムシャフトでの成果を踏まえて、遂にはロールアウトを見据えたシステム開発も始まりました。また他の職場への横展開も進み、得られる成果も大きくなっていきました。今、TOCソリューション導入時の最大のブレークスルーが何だったのかを振り返ってみると、それは「現場作業者が理解する事」だったと言えます。最初からシステムありきではなく、手書きのホワイトボードで始めたことがかえって良かったと感じています。現場が自ら考え、ボトムアップで発案された運用方法で進めたことも成功要因の一つだったと思います。
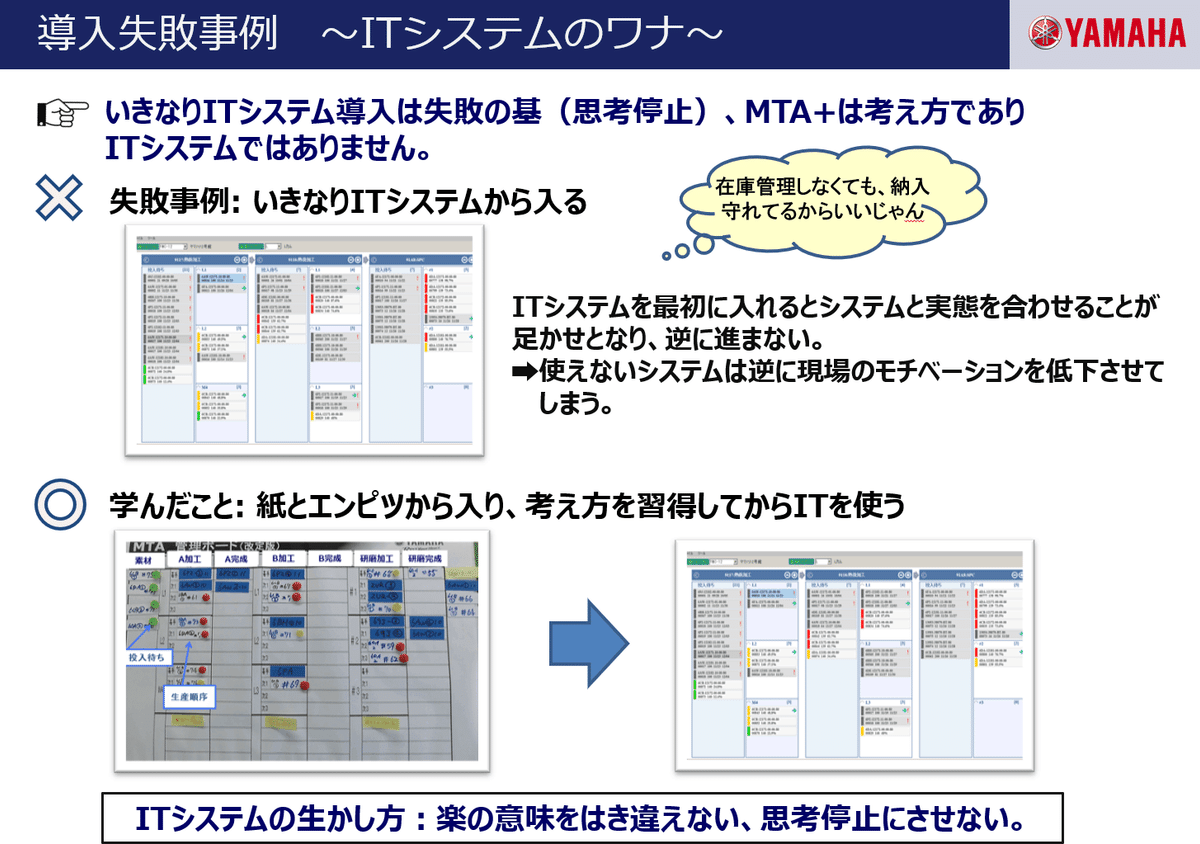
下野間:たしかに、システムありきではなくて、ボトムアップを大事にすることが必要ですね。トップダウンでやりなさいというだけでは、なかなか現場は動きません。一人ひとりが考えてこそ、初めて機能するのがTOCソリューションなんだと感じています。計画生産では、自分の守備範囲をしっかり守ることが求められますが、ある面でそれは、他の職場との繋がりについて考えることを自ら放棄してしまうことに陥りがちです。そういった環境では、ボトムアップで組織を活性化していくことはやはり難しいと感じています。MTA+では、隣の職場も見なければならなくなりますから、否応なく考えるようになるわけですが、これが「考える現場」に繋がっていくのではないでしょうか。
佐藤:「ザ・ゴール」に登場するハービー君(歩くのが一番遅い子)のように、ボーイスカウトのハイキングの例なら単純明快で分かりやすいことが、縦割りに組織された職場同志が、一つのパーティとして動くということは本当に難しいですよね。
-TOCって楽じゃない。
下野間:足並みを揃えて一つの塊、パーティになっていくことは大変ですし、TOCって決して楽じゃないですよね。「なぜ私がこの工程を考えなきゃいけないのか?」、「なぜ遅い人に合わせなきゃいけないんだ?」とか。「なぜそこまでして。」と思ってしまう訳ですが、MTA+に内包されている「現場マネジメントの思想」と、「我々が本来目指していた現場の姿」が合致しているからこそ、そこに情熱が湧いてくるんじゃないかと思っています。
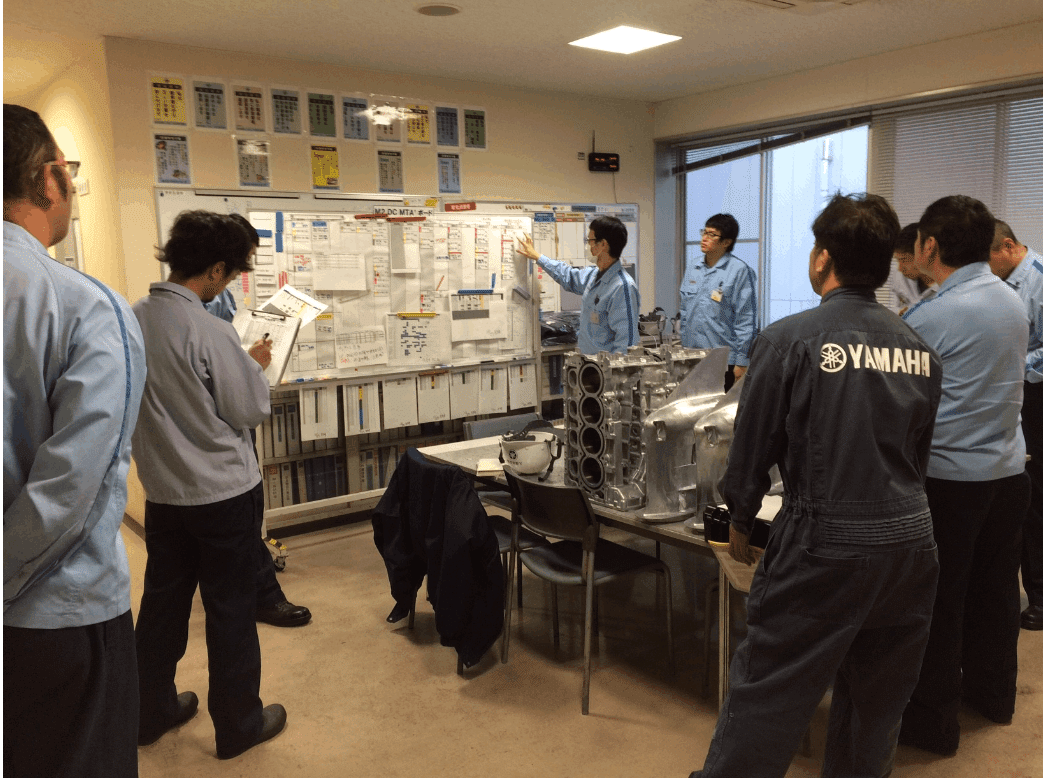
-ワクワクドキドキを大事にしたい。
下野間:今までの私たちには、どうしても「静的」というか、計画通りにという文化が根付いていました。ですから、MTA+という動的なソリューションを導入する過程では、そこに包含される全体最適の考え方が、鋳造やカムシャフトといった現場が求めていたこととピッタリ合致していることを体感しました。特に、BM会議のような場は、現場を活性化するためにとても大事だと思いますし、ダイバーシティ(多様性)というか、ボードの前で色んな人が繋がって、関わりあって、自分たちの職場をどうしていきたいのか、何を目指すのかということを共有して、ワクワクドキドキしながら、活き活きと関わりあっていくことが大切だと思うんです。
『横展開の際に意識されたことを改めて教えてください。』
-単なるコピーでは横展開できない。
下野間:現実の現場では、「絵にかいた工程」通りにモノが流れているということはありません。実際には行ったり来たりしていたり、隠れた検査工程が存在していたり、あるいは何日かするとまた復活してくるものがあります。モノづくりでは、部品表などもそうですが、一見無駄に見えてしまうようなところを救ってあげなければならないこともあり、パワーポイントに描いた工程だけでは分からないことを、丁寧に理解していく必要があるんです。ですから、「他の職場でうまくいったからと言って、そのままコピーしても絶対に上手く行きません。」また、異なる職場の現状調査を行う際には、(もちろん最初に職長や部長に話を通すのですが)現場を実際に動かしているリーダーに直接ヒアリングすることが肝要です。現場に存在している細かいところを拾ってくれているのが彼らですから、そこに寄り添って『一次情報』に基づいて問題構造を分析し、関係者のベクトルを合わせていくことが大事なポイントだと思っています。最後に、横展開の局面では「各職場の改善力を信じる」ということを挙げさせていただきたいです。横展開だからといって一律の進め方を押し付けるのではなく、職場毎の「スモールスタート・スモールサクセス」を重視し、また各職場が運用イメージを描ける範囲から始めることを許容することが、結果的に大きく育てることに繋がるものと考えています。急がば廻れと言いますが、皆様のご参考になれば幸いです。
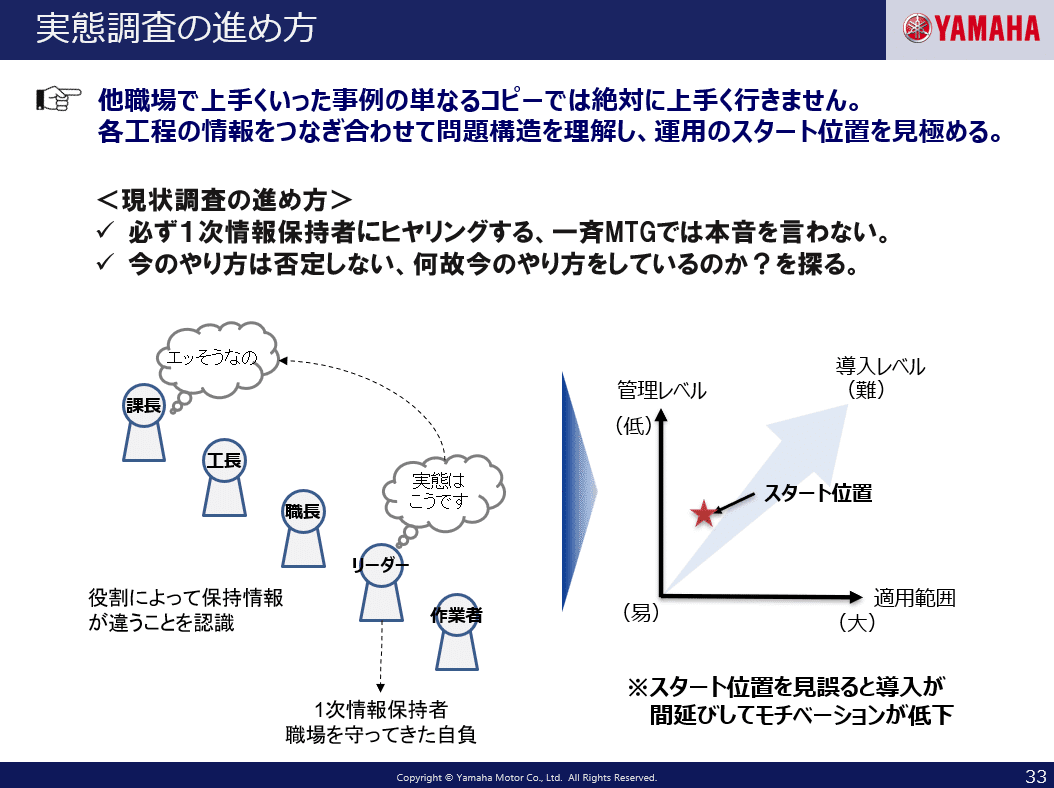
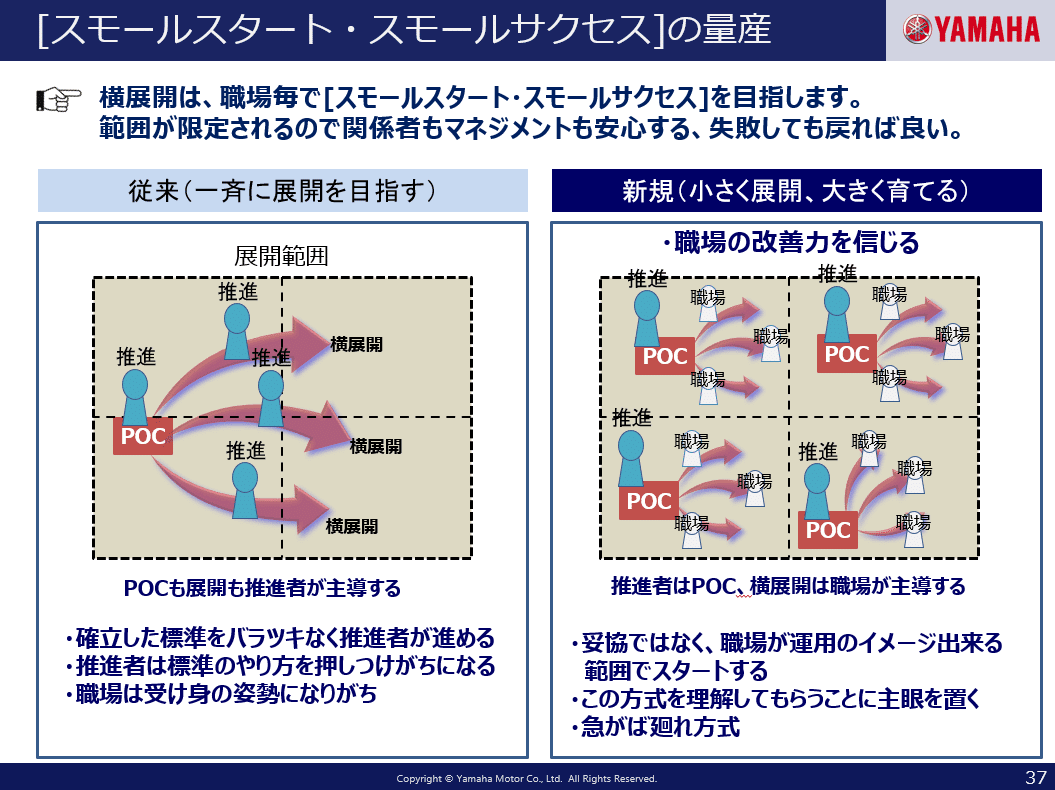
あとがき
「やれることからやるしかない」と腹を決められた久保田さんの逞しさと粘り強さがなければ、カムシャフト加工での成功には至らなかったものと推察します。また、下野間さんが「横展開の心得」と題して発表された内容から伝わってくるその説得力は、現場に寄り添う誠実さと、活き活きした現場づくりへの情熱から生まれたものであったことを確信しました。そして、「問題と解決策、感情とロジック、モノと人、人と人をつなぐウィングマン」として、いつも変革活動の渦を巻き起こしておられる佐藤さん。今後益々ご活躍されることを祈念しております。最後に、MTA+導入に関わった多くの人たちが厚い信頼を寄せた親分(本記事中に何度か登場された故飯尾さん)に直接お話を伺うことができないのが残念でなりませんが、間違いなく誰もが認めるMVPでいらっしゃったことと思います。YMCでは、デマンドチェーン革新におけるTOCソリューションの適用領域を、製造工場からサプライチェーンに拡大して展開しておられます。またの機会に、そのご経験から得られた知見をご披露頂きたいと考えております。
※YMCの久保田さんと下野間さんが発表されたプレゼン資料に、TOCソリューション導入にまつわる詳しい内容が掲載されています。是非合わせてご覧いただきたいと思います。
・2018年11月:第41回TOCPA国際カンファレンス(発表者:久保田 正義氏)『エンジン部品製造部門におけるMTO/MTAハイブリット生産方式導入』
・2019年11月: 第44回TOCPA国際カンファレンス(発表者:下野間 善丈氏)『MTA+横展開の心得』
会社概要
ヤマハ発動機株式会社(2021年12月31日現在)
創立:1955年7月1日
本社:静岡県磐田市
従業員数(連結):51,249人
関係会社数:約140社
資本金:861億円
売上高(連結):1兆8,124億円
経常利益(連結):1,894億円
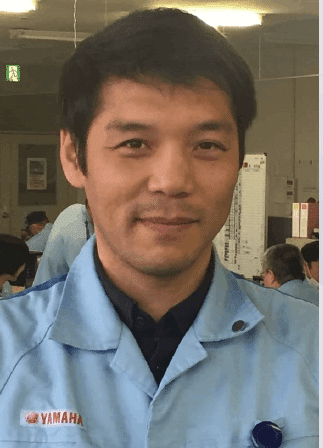
久保田正義氏の略歴
ヤマハ発動機株式会社
生産本部 生産戦略統括部 生産管理部 業務Gr グループリーダー
千葉県出身 東京理科大学(経営工学専攻)卒業。
2004年 ヤマハ発動機㈱入社。
本社生産管理部門で生産計画策定業務に従事。
海外拠点への生産管理システム導入PJを担当するなど、
システム/運用の両面での実務経験を積む。
2012年 ブラジル現地法人の生産管理駐在員として5年間勤務し、
多国間サプライチェーンの改善を実現。
2017年 本社製造部の生産管理担当へ。
エンジン部品製造へのMTA+導入を推進。
2020年 生産管理部門のグループリーダー(課長)として現在に至る。
TOCのS&Tツリーを用いて社内構造改革の推進責任者として活動中。
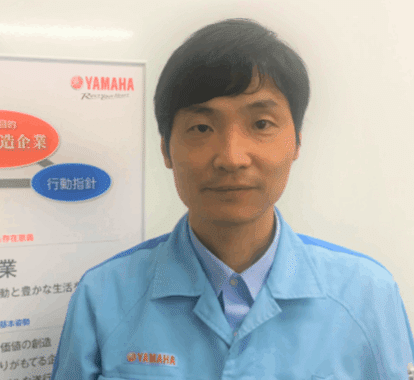
下野間善丈氏の略歴
ヤマハ発動機株式会社
生産本部 製造統括部 磐田第2製造部 推進課 課長
鹿児島県出身、鹿児島大学機械工学科卒業。
2007年 ヤマハ発動機㈱入社。
2015年 生産管理部門で生産プロセス改革業務に従事。
生産管理システム企画、導入PJを担当するなど、
システム/運用の両面での実務経験を積む。
2022年 生産本部製造統括部 磐田第2製造部推進課の課長として現在に至る。
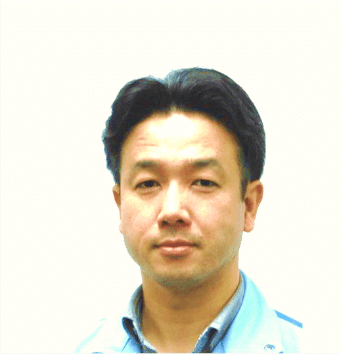
佐藤淳一氏(ヤマハ熊本プロダクツ株式会社)
過去のインタビュー記事(佐藤さん)を是非ご覧ください。
この記事が気に入ったらサポートをしてみませんか?