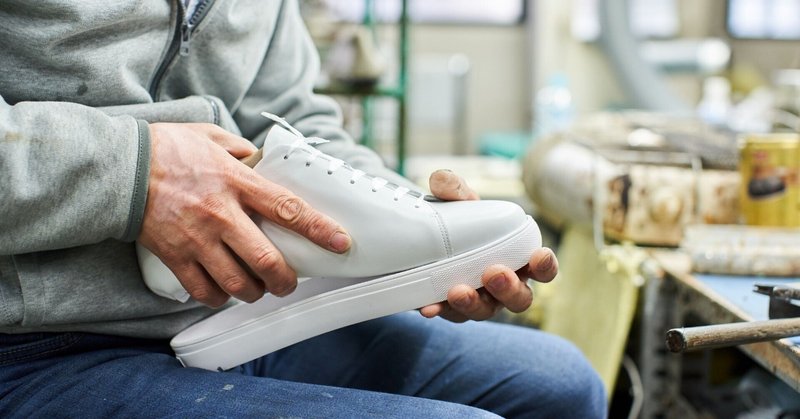
2年間の開発にかけた苦悩…リニューアルモデルの想いと経緯を公開
brightwayを作る株式会社インターナショナルシューズの上田 誠一郎(Twitter:@seiichiro_ueda)です。
現在、12月30日(金)18:00まで、brightwayのリニューアルモデルをMakuakeで先行予約販売を行っています。
皆さまの応援購入やシェアにより多くのサポーターが集まっております。誠にありがとうございます!!
今回はリニューアルモデルにかけた想いや開発の経緯を書かせていただきます。
運命の出会いから改良に向けて
brightwayのデビュー当時、まだ何もノウハウもない中、スニーカーを初めて開発しました。その時にある方が靴底を開発する企業を紹介して下さり、その方との出会いが運命を大きく変えてくれました。
ソールの悩みを相談し最初は近い代替品を探してテストなどしましたが、思うような履き心地にならず、最終的にはオリジナルソールを開発することを決意しました。
そこからが苦難の連続で、厚みを増して履き心地がよくなると思ったのに、逆にシルエットが悪くなったり、軽量化をしようとしたら履き心地が硬くなったりと、開発が進むたびに自分の理想とかけ離れたソールになっていきました。
そんな試行錯誤を続け、気付けば2年の歳月が過ぎていました。
なぜ開発に踏み切ったのか
なぜこんなに高いハードルがあるのに開発したのか。それは・・・
「愛用して下さる方に、本当に自信を持ってお届けできるような”最高の商品”を作りたい」
その1点だけです。
これまでbrightwayでは小ロットで仕入れが可能な既製品を使っていましたが、お客様からは下記のような声をいただいていました。
”履いていただく中で脱ぎ履きの際に踵をひっかけて脱いでしまうとゴムの上部分がちぎれてしまった”
”大きいサイズの方が特にソールのすり減りがかなり早い、すぐに底に穴が開いてしまった”
デザインも履き心地もいいのにソールの問題に引きずられ常に心配と不安が隣合わせにあった2年間。それを乗り越えたリニューアルのこだわりについて説明させてください。
リニューアルしたポイントとは?
今回のリニューアルのポイントは3つです。
(1)アウトソール(靴底)のアップデート
(2)アッパー(表面)のレザーのアップデート
(3)木型(ラスト)のアップデート
中でも、最も苦労が多かったオリジナルのアウトソール(靴底)にフォーカスします。なぜなら、市場から見ても難易度が高いからです。
ラグジュアリーブランド以外、特に私たちのような小規模の企業・ブランドで合うとソールをオリジナルで作ることはまずありません。
それでも挑戦したのは、「愛用して下さる方に、本当に自信を持ってお届けできるような”最高の商品”を作りたい」という想いが軸にあったのが理由です。
開発詳細にいく前に、スニーカーのソールってどうやって作ってるの?ということをご説明します。
スニーカーのソールの作り方
マニアックなお話になりますが、スニーカーのソールについていくつか説明します。
※飛ばし読みしてもらってもOKです
ソールの材質・特徴について
スニーカーのソールには大きく分けて3つあります。
(1)合成ゴム
→汎用性が高くゴムの配合も可能
(2)IP(インジェクションパイロン)製法
→軽いのが魅力だがロットが大きい
(3)TPU(サーモプラスチックウレタン)製法
→複雑なデザインが可能だが重たいのが難点
(2)IPソールは軽くて厚底です。多くのデザイナーから使いたいと声をいただくものの、成型方法が特殊ゆえにミニマムロット(最低注文数)が1カラー2000足~と大きいのが難点です。
参考までに最近のラグジュアリーブランドの靴は重たいケースが多いのですが、これは(3)TPUソールを採用しているからです。複雑かつ立体的なデザインでブランドの個性が出るものの重たくなります。
今回brightwayで採用しているソールは(1)合成ゴムで、レザースニーカーでは最もよく使用されるゴムソールです。最先端の素材ではないけど、ロットも少なく(とはいっても500足ぐらいはいりますが)ゴムの配合もオリジナルでやりやすいため合成ゴムソールを採用しました。
モールドソールって何?
ソール作成のプロセスは大まかには下記の流れです。
(1)モールド金型・設計図面作成
(2)金型作成→モールドサンプル作成
(3)量産
スニーカーを作る際によく「モールド」という言葉が出ますが、これは鯛焼き機のような金属の型(金型)を作って、そこに樹脂を流し込み焼きあがると一体成型の立体的なソールが完成するという製法です。モールド(mold)は「型」という意味で、型で成型して作ったソールだからモールドソールですよ。といった感じです。
図面作成からこの金属の型を作成して、ここから樹脂を流し込む工程に入ります。(下記youtubeの2:00~5:00に流れる動画がモールド作成のプロセスです)
こうして完成した金型に下記動画のように樹脂を流し込んで、1足1足成型して作っていきます。
靴のモールドを作るハードルの高さ
前述の通り、私たちのような小規模の企業・ブランドでわざわざモールドソールを作ることはまずありません。
その大きな理由は初期開発費用とミニマムロット(最低注文数)の壁です。
初期開発費用は海外で作った場合、合成ゴムの型で1サイズ15万円前後、EVAやIPになると1サイズ30~50万円が相場になります。これだけでなく靴の最大のネックがサイズが多岐にわたることです。brightwayを例に挙げるとメンズ・レディースで11サイズあるので単純計算で×11となり、大きな初期開発費用が必要になるため壁になっています。
そしてもうひとつの壁がミニマムロット(最低注文数)。1オーダーで1色最低300~500足が必要なのです。その理由は合成ゴムを練り込むのですが、その1回で練り込む最低量が300~500足分ぐらいだからです。100足分だけ練り込んでと言っても配合の比率やレシピがあり、簡単に寮変更ができないのです。スープにこだわるラーメン屋さんで考え抜いたスープの量を3/2にしてほしいというと味が変わってできない、というのに似てます。
苦難を乗り越え最高のソールが完成
開発は苦戦だらけでしたが、同時にこの2年間はソールについて徹底的に向き合ったことで本当に財産となりました。
いろんなスニーカーを分解していく中でイタリアのスニーカーのソールの作り方や靴づくりの考え方も学び、それが今のスニーカーの開発に大きくプラスとなっています。時間はかかりましたが、その分学び得ることも多かったです。
結果的に5回も作り直すことになったのですが、途中で心が折れなかったのはbrightwayを愛用してくださる皆さまの存在があったからです。最大の応援団となってくれた皆さまにこのままでは終われない。
同時に開発に付き合ってくださったチームの皆さまのサポートが無ければこのリニューアルモデルは生まれていなかったと思います。
こうして多くの皆さまの力が終結したアウトソール。これを搭載したbrightwayのリニューアルモデルが12月30日18:00までMakuakeで先行予約販売しています。
ぜひ最後にプロジェクトを応援・シェアいただけたら嬉しいです。
この記事が気に入ったらサポートをしてみませんか?