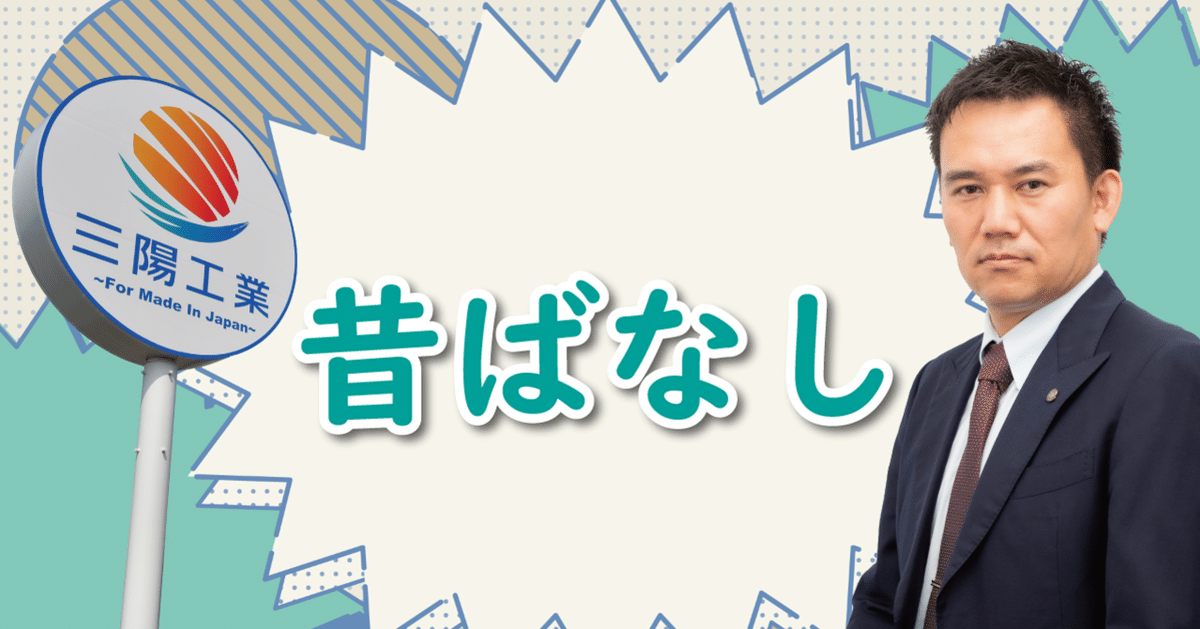
【173球目】昔ばなし
たまには昔ばなしでもしましょうかね。
記憶をたどりながら、こんなことあったなということをいくつか今日は書いていきます。
溶接研修職場
私が三陽工業に入社して1年目のことです。
当時のオートバイ生産は北米や欧州に向けて非常に好調でありました。
そんな中で溶接職場の人員が不足しているという話になりました。
よくあることですが、現場は溶接の経験者が欲しい。
しかしながら、溶接の経験者はそんなに簡単に見つかりません。
そんな状況でありましたので、職場側とお話をさせて頂き、三陽工業で溶接職場へ送り込む人員を教育することで話がまとまりました。
当時、研磨工場が神戸市西区伊川谷にありましたので、その研磨工場のスペースに溶接機を3台購入して設置し、講師は川崎重工のOBの方にお願いをしました。
たまたま溶接職場の元職場長が在籍してくれていたので、スムーズでしたね。
人によりますが、1週間から2週間の教育・訓練の後に川重へと配属になっていきました。
順調に人数も増えていきましたが、リーマンショックで終了です。
これはしかたがありません。
そして、ここ最近でもそういった流れが復活をしています。
子会社のサンテックの溶接職場にて教育・訓練を実施してから川重明石工場の溶接職場へと配属されていっています。
「歴史は繰り返す」ですね。
構内協力会
川崎重工明石工場のオートバイ部門に入っている協力会社で構成された構内協力がかつて存在していました。
17社でしたかね。少し記憶が定かではありませんが。
協力ハウスという名前の建屋に、ほぼ全ての企業が事務所を構えており、隣の部屋は別の会社、前の部屋も別の会社、そんな建物が存在しました。
この協力会、何が素晴らしいかというと、安全教育の仕組みが素晴らしかったのです。
新人が各社ごとに入ってきますが、その初日の安全教育や適性検査は私たち協力会社で分担して行います。
自社の社員の入職が無くても、教育実施をする場合もあります。
各社ごとにやること、やれることは違いましたが、それでも各社が協力をして非常にスムーズに初期教育を運営していました。
座学での教育や適性検査、体力測定等、本来メーカー側の機能として持つべきものが協力会に存在していたのです。
この協力会もリーマンショックにて解散。
2年ほど前まで建物はありましたが、その建物も取り壊されており、今や跡形もなく、記憶の中だけにあります。
しかしながら、この協力ハウスに出入りしていた、当時は他の企業の社員だった数名が現在は三陽工業の仲間であることはとても誇らしいことです。
ロボット
現在の森友工場に研磨ロボットがあった時期があります。
私が入社する前の話ですが、研磨作業をロボット化していく動きがあり、実際に稼働をしていたこともあります。
そんな流れもありましたので、川重明石工場で使わなくなったロボットを買い取らせていただき、リーマンショックまで、三陽工業からKawasakiのロボットスクールに配属になっていた社員と共に、動かそうとしていました。
しかしながら、当時から1部品あたりの生産個数が非常に少なくなっており、1つの部品を立ち上げる為にティーチングの工数が出てこない。
簡単に言うと、昔は1部品が毎日200個ずつ4-5年は流れていたものが、1部品が数十個、しかも1-2年で終わることもある状態になると、なかなかそこに取組むことが困難になります。
結果、そのロボットは撤去しました。
未来に向けては、もちろんその可能性も残してはいますが、現在の多品種小ロットとロボットの初期工数を考えると、現状のやり方が得策です。
もっとロボットが身近になる日が来ますかね。
アンテナは立てています。
昔ばなしについて
記憶を辿りながら3つほど書いてみましたが、今に繋がっているものがあったり、そうでないものがあったり。
しかしながら、1つも無駄なことはなかったと考えていますし、その全てが私にとっては大きな財産になっています。
そこから学ぶことが多かったですから。
これは三陽スタンダード⑧の
三陽工業には失敗という言葉はありません。全て経験と捉えます。
に繋がっています。
(⇩三陽スタンダードについてはコチラを参照)
このスタンダードは、私が創ったのではなく社員有志が創ってくれました。
私の考えとリンクしている三陽スタンダード。
三陽工業の強みの1つです。
本日もありがとうございました。
明日もよろしくお願いします。
最後まで読んでいただき、ありがとうございました!