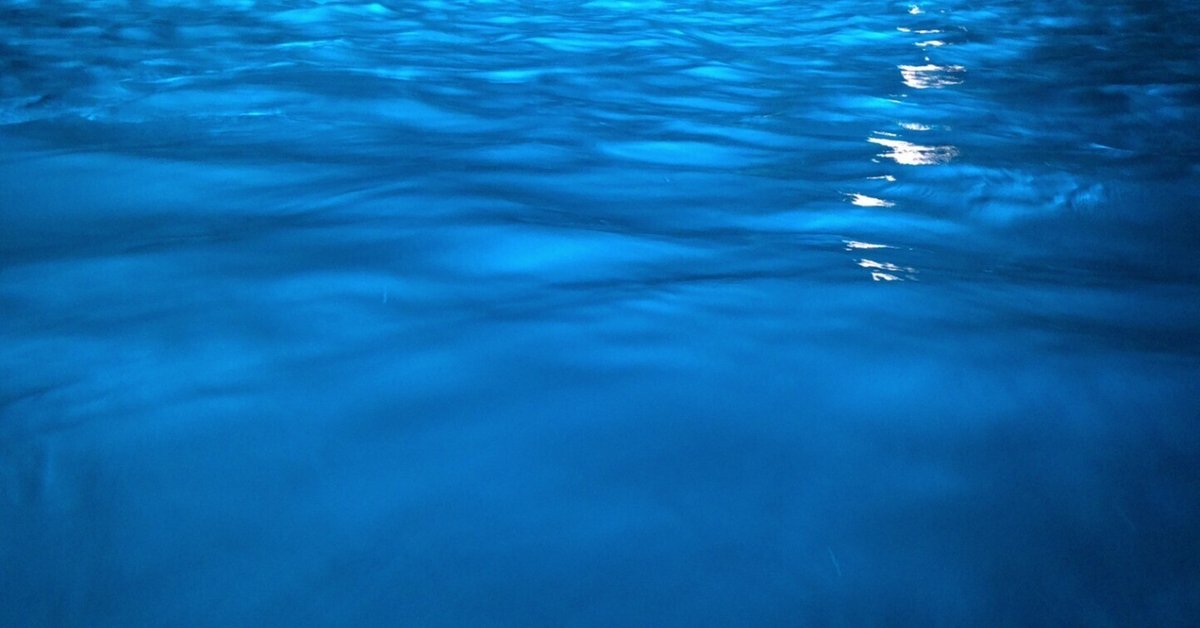
品質保証の目的と手段
これまで大企業から中小企業のいろいろな人達と仕事してきました。
業務を進める中で、目的の重要性があると思います。
目的を実現するために手段を設定し行動していくことになります。
何事もそうですが、まず最初に目的(目標)設定になりますが、どのレベル(階層)に置くのかを決める。
【大前提として】
目的をどこに置くのか
・工場全体としてなのか
・工程別にしたものか
手段は、レベルに合わせた項目を決めていく
製造工場ならQCD活動をすることが当たり前に活動していますが、特に品質対策においては重要事項になります。
改善活動の一環として品質改善報告を定期的に実施活動しています。
対策会議では、
いろいろな意見が出され議題に合わせた結論が出される
・不良内容
・発生原因
・対策案
・対策決定
・再発防止
・流出防止
・QC工程図に盛り込み
この対策会議では、再発防止の方法が決定されるが発生ミスに対する対策事項をその工程の手段としている。
ここで表面的な事実誤認が生まれることがある。
QC工程図
作業者は不良品を作ろうと思っているわけではありませんが、『不良原因は作業者の問題と、作業者がミスをした』と、とかく管理者は考える。
実は、作業者以外に管理方法の問題、品質保証体制の問題とか複数の問題が絡んでいる。
品質対策手法の一つとして、FMEA(潜在的故障モード影響解析:Failure Mode and Effects Analysis)があります。
製品や製造プロセスがもつリスクを設計段階で評価し、取り除く手法、製造工程で生じるすべての異常を想定することは困難で限界はあり参加メンバーのスキルに依存することになる。
不良は基本的に人的ミスで起きていることになる。
・設定ミス
・見逃し
・忘れ
・間違い
・作業ミス
・確認ミス
・イレギュラー対応の想定ミス
・不必要な行為でのミス
・言葉の定義の問題(解釈の違い)
・管理ミス
こういったことを想定しQC工程図に盛り込み品質保証を行うことになる。
不良事例
・チェックシートの記入漏れ
工程管理者からの回答は、
これまでAさんが行っていたが、記入が漏れるので第三者としてリーダーの確認を追加しました。また、作業者集めて今回の事例含めて再教育しました。
・対処療法
起きた問題に対する手段が増えていく。
・再発した
同じチェックシート記載漏れが再発した。
・現場確認
工程管理者から作業現場の作業を説明してもらうと
・作業標準書通り手順を説明されたが、チェックシートの記載がない。
・チェックシートを記入する決まった場所がなく、作業環境が整備されていない。
これまでの原因分析や調査や回答に工程管理者の問題がある。対処療法的な手段を実行することに目がいっている。原因はいつも、作業者の問題になっていることが多々あります。
また、教育不足の為、作業者に『教育しました』となる。
顧客先の立場的に言えば『教育されていない従業員に製造させているのか?』と思う。
車検に出した自分の車が、従業員がまったく教育されていない者が整備していたらどう思うか?と同じことですね。
目的と手段の問題
この事例では、そもそもチェックシートを使う目的は何か?
工程管理者が目的を忘れて、記載漏れをどうやって検出するかに思考が向いている。
製品が決められた作業を実行されたかを記録として残すエビデンスになるわけですね。
簡単に言えば、製品セット→実行→完了→チェックシート記入となる。
品質保証
品質保証としてQC工程図に製造条件、保証方法、不良流出防止、など目的を持って設計しているが、今回の事例のように簡単に対策事項を決めてしまうと不良発生の都度、新ルールが出来ることになる。
本来であれば、発生問題の原因と捉えて既存の品質保証におけるQC工程図の設計を見直すことでルールが増えることを防げることになると思うのです。
QC工程図の設計思想として『人はミスをする』を前提として製造全体の工程と、何処で何をどのように製造するとどのような物が出来るのか?を考えてQC工程図を設計し文書化することになる。
ところが、QC工程図には設計思想など書いてないのですね。
この設計思想を読み取れる工程管理者の育成が必要になります。
まとめ
何でも、そうですが目的があってそれを実現する手段となります。
品質保証を行う上で、QC工程図を作成していますが社内文書として説明文を作成しておくと良いと思います。
目的、背景、考え方、保証を実現している手段を階層が分かるように文書化しておくことで後日、誰が見ても分かるようにしておくと変更するにしても容易に出来るようになります。
解説文として用意しても良いかもしれません。
くれぐれも、目的を忘れないように。
この記事が気に入ったらサポートをしてみませんか?