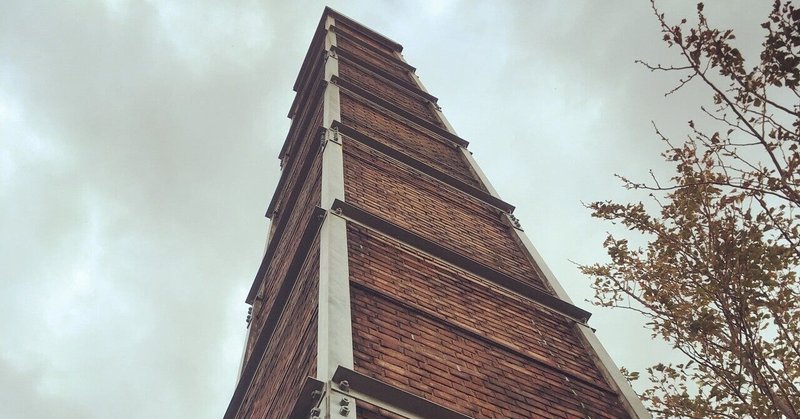
Episode 521 「カイゼン」結果で悪化です。
私が勤めるような「日配食品メーカー」に限らず、製造業では原料の搬入から商品の出荷まで、工場内で行われる生産活動の中で必ず「ロス」が発生するのです。
例えば…ウチの会社の話をすれば、小麦粉や澱粉のような「粉モノ」は業務用の大袋で搬入・納品されるワケです。
モノによって規格はバラバラですが、1袋が20kg前後のものが多いですかね…それを製造する商品に合わせて配合を変えながら使うのですが、1回の生産工程(これを1バッチという)が1袋単位で…というワケにはいかないのです。
1バッチの使用量が1袋を超えるものもあれば、1袋を使い切るのに10バッチ以上かかるようなものもあってですね、計量して小分けで使うような材料もあるのです。
それで、モノを計量して小分けにすると「ロス」が発生するのですよ。
簡単な話です、袋に付着した粉をキレイに使い切ることは出来ない、分ける個数や回数が多くなれば、その袋に残ってしまう「どうしても使い切れないもの」…つまり「ロス」が増えるというワケです。
その他、機械に付いて搔き集められない原料とか、重量不足で製品として出荷できないサイズのものとか、焦げちゃったものとかね…キレイに商品のカタチにならないものを「ゼロ」にすることは不可能なのです。
このように発生してしまう「ロス」は生産工程上「仕方がないもの」とされ、会社は一定量(数パーセント)のロスが出ることを前提に生産量を考えるのです。
このロス量を差し引いた生産量が「歩留まり」と呼ばれる実生産量になるワケです。
そうは言ってもですね、企業にとって「ロス」は敵なのですよ。
当然です…ロスが減れば、同じ重量の原材料なのに生産量は増える、そもそも失う分として計算しているワケですから、ロス率が下がれば(歩留まりが上がれば)その分はマルマル利益として計上できるのです。
だからね、生産現場はロス率が予定範囲であることに満足せず、徹底的にロスの原因を探すのね。
その代表的な方法が「QC手法」と呼ばれる品質管理方法なのです。
製造業と「QC手法」を用いた「カイゼン」の相性はとっても良くてですね、データ分析から問題点を発見して対策案を作り実行、効果測定をして定着させる…いわゆる「PDCAサイクル」で生産品質の向上をさせたい会社としては、部署の課題案件として従業員に「カイゼン」を指示するワケですよ。
この品質向上を目的とした「正しい『カイゼン』の使いかた」なら何の問題もないのです…でも。
中途半端な「QC手法」理解で恐いのは、カイゼンの目的を「品質向上」ではなく「収益改善」に求めてしまうパタンです。
ロス率削減(歩留まり改善)の結果としての「○%の収益改善」なら良いのです。
でも「収益改善目標達成のために歩留まりを○%改善せよ」はマズイ…特に、収益改善目標が人件費に向くのは最悪です。
バブル崩壊、その後のリーマン・ショックを経て、収益が思ったように伸びない製造業が、慣れ親しんだQC手法を収益を搾り取る道具として使う…。
日本の企業が得意な「カイゼン」こそが、日本に障害者雇用が根付かない「根本的な原因」だと言う気がしてならないのは、私だけだろうか?
— Ho+(HOTAS) (@HOTAS10001) March 4, 2021
このツイートの根にあるのは、改善の結果としての人員整理、余裕が無い組織でゆとりを必要とする人員構成を構築できない、その原因として「カイゼン」があったのではないか…という思いです。
戦後復興から高度成長期の日本を支えてきたのは製造業でした。
その製造業が日本の他業種に、そして世界に「カイゼン」という言葉を知らしめたのは事実でしょう。
そして、それが今、逆に雇用環境を悪化させた一因になってしまっている可能性を、私は感じずにはいられないのです。
この記事が気に入ったらサポートをしてみませんか?