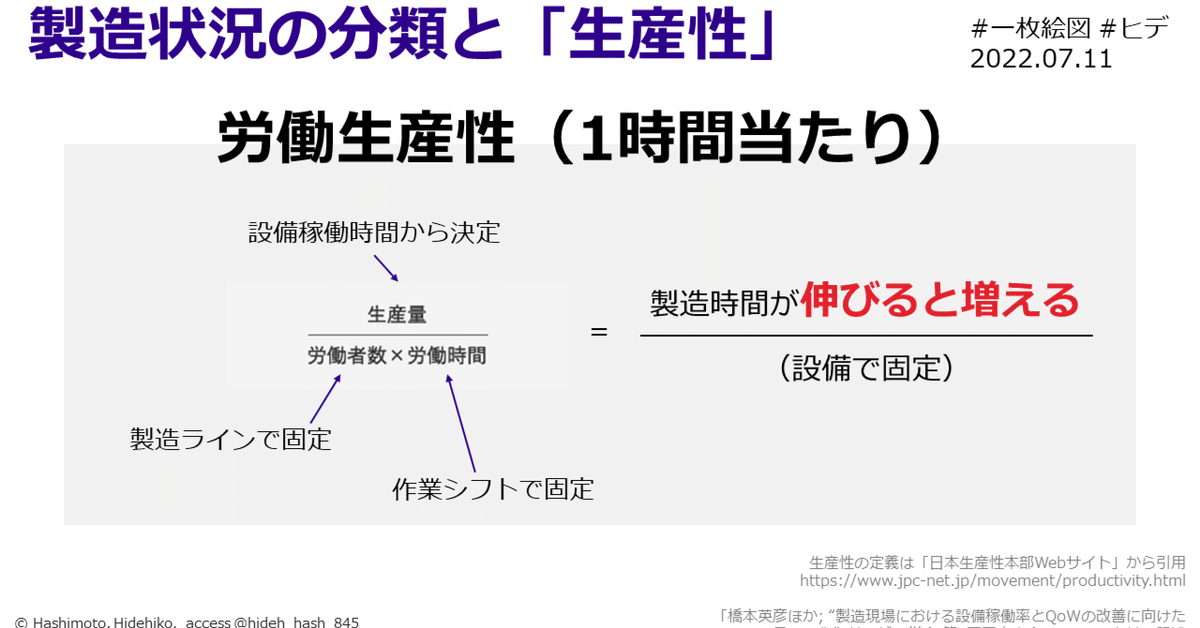
製造ラインにおける「生産性」はどう向上させる? その具体的な分析方法について。
はじめに
今日の日本では「生産性の向上」が喫緊の課題です。製造業も例外ではなく、「激しいコスト競争」「コモディティ化による競争力低下」に加え、「生産年齢人口の減少」も避けられない状況です。そのため、今後は一層の「生産性の向上」が求められます。
ところで、そもそも「生産性」とはどのように定義されるものなのでしょうか? 公益財団法人 日本生産性本部によれば、生産性は
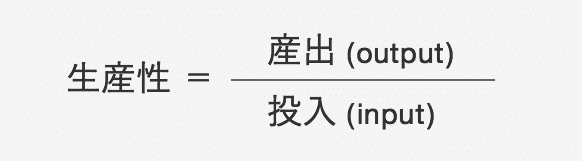
と定義しています。
ここでは、製造業の製造現場における「労働生産性」として、設備稼働時間に注目し、それを向上させるために、製造状況の分析を進めるための具体的な方法について記述していこうと思います。
労働生産性をどう定義するか? データをどう手に入れるか?
まず、最初にしなければならないのは、
そもそも労働生産性という指標をどう算出するかを決めること
です。先に示した日本生産性本部にも「物的生産性」「付加価値生産性」といった大分類、さらに様々な詳細の分類が定義されています。
生産性が向上した、あるいは生産性が高いといったような場合、それが何を意味するかを知る必要があります。これを定量的な数字で表すことが生産性の測定ということです。
https://www.jpc-net.jp/movement/productivity.html
しかし、製造業の実務担当者がこの生産性を議論する場合、一番注意する必要があるのは定義の詳細よりも、むしろ
「その指標を算出するのに必要なデータが入手可能か?」
という観点です。なぜなら、理論上はいくらでも厳密であっても、現状で手に入らないデータを基に算出するのでは実行不可能だからです。また、理論上は算出可能でも現実には様々な制約があるため、
データの入手に一年もかかるようでは、その指標には実用性が全くない
ということにも注意が必要です。この生産性の指標は改善サイクルに使うためのものですから、算出に一年もかかるようでは改善に使えるわけがないからです。
その点を踏まえると「現状で手に入るデータで指標化できるか?」を考えることは重要です。また、どうしても足りないデータに関しては「製造現場のIoT化によりデータが入手可能にならないか?」を検討することも非常に重要となるでしょう。
製造現場における生産性を示す指標=設備稼働率
製造業では、いまや人の手で何かモノを作るということは無くて、なにかしらの生産設備が自動・半自動でモノづくりを行っていくということがほとんどです。特に大型の設備を使って作る大型の(たとえば「送配電用電力ケーブル」のような)モノであれば、「設備の稼働時間」がそのまま生産量に直結します。そのため、労働時間内にどれだけ稼働できたかを「設備稼働率」として定義し、それを生産性の指標としている例があります(産末に参考文献[1])。計算は単純で、
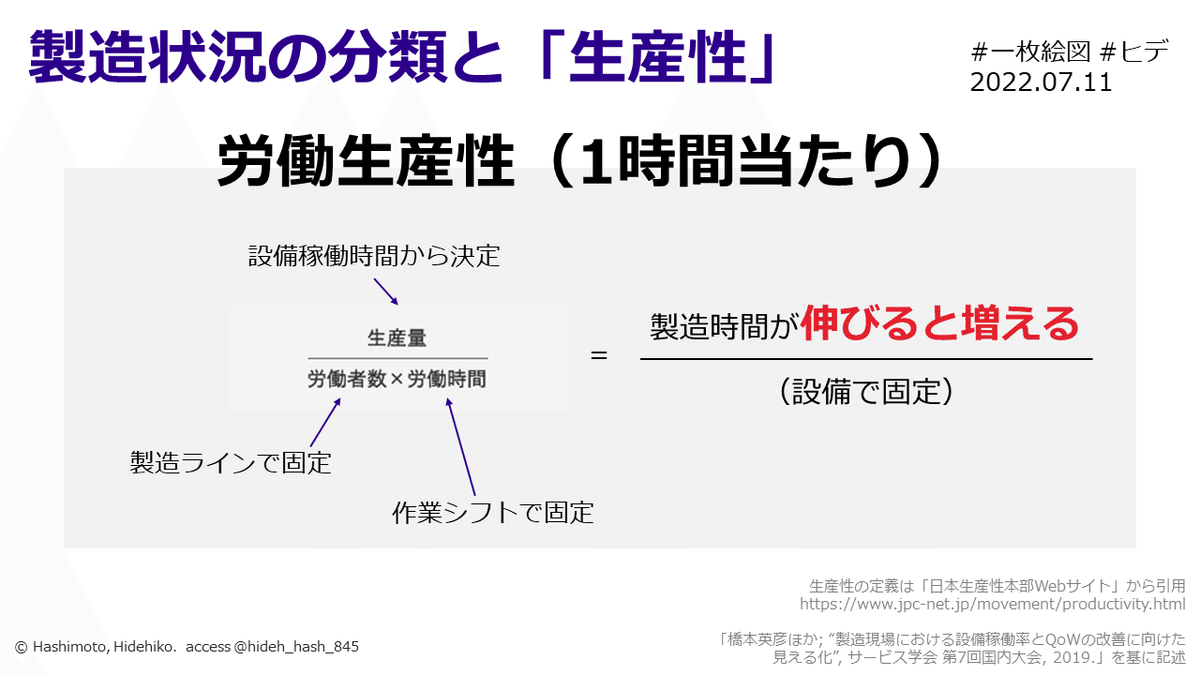
となります。すなわち、一言で言うと
就業時間内に設備をどれくらい長く稼働させられるか
で生産性を決めようというものです。
これは単純すぎると感じるかもしれません。しかし、現場がしなければならないことは、厳密な数値を出すことはありません。現場における「生産性の向上」、つまり「どうやって価値をたくさん産出するか」であって、そのために必要な手立てが分かれば良いのです。算出の簡易さによって、改善のための有効な施策が打てるのであれば、この指標で十分事足りているということが言えるでしょう。
設備稼働率製造状況の分析による例
さて、前章で示した通り、設備稼働率を算出する理由は「有効な施策が打つ」ためです。稼働率を単に出しただけでは意味が無くて、次は設備稼働率を上げるために何をしないといけないのか?を把握しないといけません。ここでは、過去に筆者が行い、学会発表した事例を基に、設備稼働率の「上げシロ」を見つけ出すための状況の分析手法について記述します。
まず、設備を使った製造状況の分類を行います。
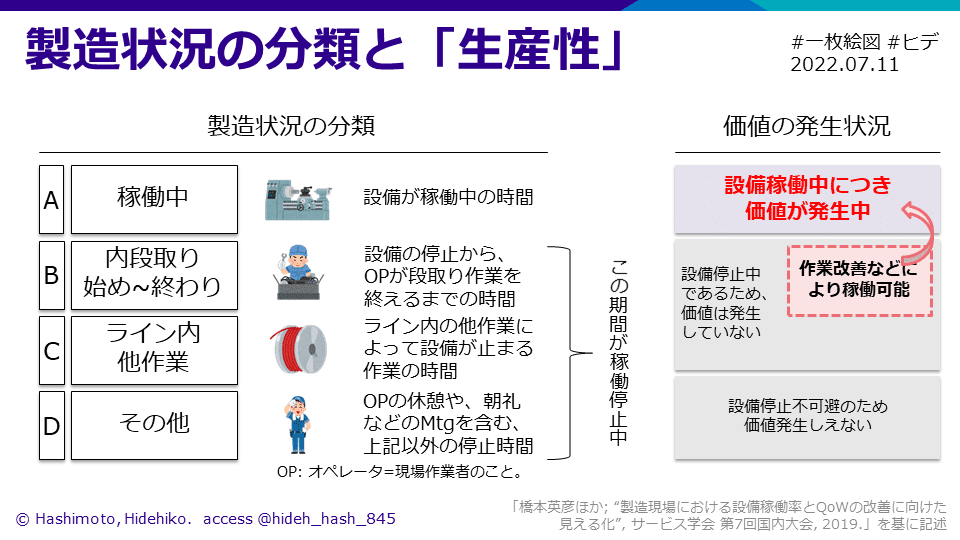
設備の状態は、「稼働中(A)」と「停止中」に分けられます。「稼働中」は文字通り価値を産出しているわけですが、「停止中」にも停止の理由があるはずです。この停止の理由を詳細に分析していきます。
最初に、内段取りによる設備停止時間(B)を挙げています。
「内段取り」は、機械設備を停止しなければできない段取り替えのことです。また、「外段取り」は、機械設備を停止せずにできる段取り替えのことです。
https://www.keyence.co.jp/ss/general/fa-glossary/0040.jsp
それから、段取り作業以外の設備停止時間(C)があります。これは前工程からの搬入、後工程への出荷、設備の故障、点検タイムなどがあります。
最後に、その他(D)です。ここには作業員の休憩、朝礼や各種ミーティング、安全活動、研修など、そもそも設備とは離れたところで行う日常/非日常業務などです。「会社員としては業務ですが、製造とは全く関係ない業務」と言い換えることができるかもしれません。
このように製造状況を分類した後、次に行うことは「どこが稼働時間向上に寄与するか?を分析すること」です。たとえば、(D)は稼働時間に寄与しようがありません。そもそも製造とは関係ない業務ですので。また、(C)も難しいです。となると、(B)の中の一部が(A)にできるかもしれないということがわかります。
一般に「段取り時間」や「段取り作業」という場合、内段取りに要する時間・作業を指します。内段取り作業は生産を停止して行うため、常に作業時間の短縮が求められます。そこで、近年では事前準備を徹底することで内段取りを外段取り化し、内段取りの作業時間を短縮するといった取り組みが注目されています。
https://www.keyence.co.jp/ss/general/fa-glossary/0040.jsp
それでは、(B)の中から、(A)に転化できるところはどうやって見つけたらよいのでしょうか?
製造状況の具体的な分析方法
(B)から(A)に切り替えるには、具体的に個別の作業を見つけ出し、それぞれ「減らす」「縮める」「並行して行う」など個別の対策を実施する必要があります。それでは、それら個別の作業はどうやって見つけ出したらよいのでしょうか?
具体的には、それぞれ「設備」「人(作業者)」のみに注目し、その時「その時、設備はどうなっていたか?」「その時、作業者は何をしていたか?」を個別の分類することで、製造状況を更に詳細化することができます。以下に、イメージ図を示します。この例では、それぞれさらに6状態ずつを定義し、状況の解像度を上げることに成功しています。
ここから先は
¥ 100
この記事が参加している募集
課金してくれるととても嬉しいです。シェアしてもらっても嬉しいです。「いいね」も嬉しいですし、フォローも嬉しいです。要するに、どんなことでも嬉しいです。