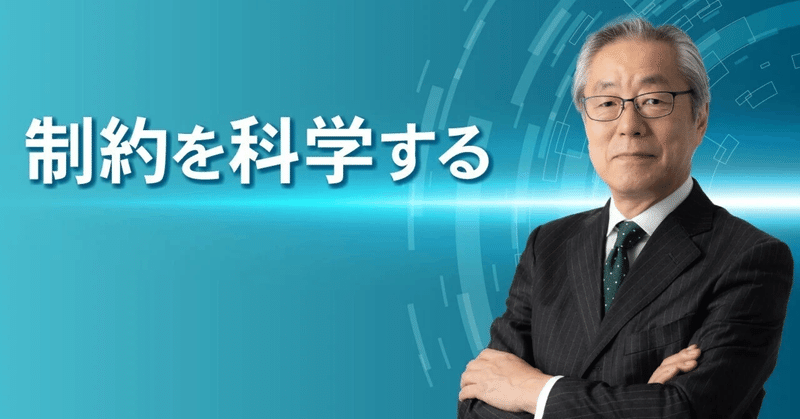
制約を科学する➁第1部(制約とは何か)-2(制約を徹底活用するという、カイゼンWay)
こんにちは、ゴール・システム・コンサルティングです。ゴール・システム・コンサルティング代表取締役村上悟の、TOC(制約理論)についての連載「制約を科学する」2回目をお届けします。TOCの基本から始まり、制約とは何かを深く考察するシリーズになっています。今回は、TOCの継続的な改善活動について、具体的な事例でお話します。ぜひご覧ください!
制約を徹底活用するという、カイゼンWay
TOCは継続的改善(POOGI=Process Of On-Going Improvement)というスローガンを掲げて、改善のサイクルを回し続けることを推奨しています。これはトヨタの「終わりのない改善(Continuous Improvement)」に対抗しゴールドラット博士が提唱したものですが、ここからは「制約」を徹底活用(Exploit)する事、これをさらに掘り下げて考えてみたいと思います。現在の制約を徹底活用して、将来に向けてスループットを最大にする具体的な方法です。
※継続的改善の具体的な5ステップについては、連載第1回をご覧ください。
実は「カイゼン」という単語は、世界中で「KAIZEN」として、ほぼそのまま通じます。今井正明さんという方が1988年に「KAIZEN」という本を英語で出版して大ベストセラーになったのがきっかけでした。当時はジャパン・アズ・ナンバーワンという本がベストセラーになったりして、日本の製造業が世界的な注目を浴びていた頃でした。ですから欧米諸国はニッポン流のカイゼンをコトバごと受け入れたのです。ゴールドラット博士も、セミナーで日本から「KAIZEN」を学んだとよく話していた事を想い出します。
では、TOCと「KAIZEN」の関係を見てゆきましょう。まず注意が必要なのは、TOCが掲げている「POOGI」と、従来の日本の現場で行われてきた「カイゼン」はその哲学が全く違う事です。
日本的なカイゼン活動の基本は、小集団活動をベースとしてそれぞれの職場が、自分たちの「困り事」になっている身近なテーマを地道に改善する活動が中心です。これはボトルネック(制約)とは関係なく、問題が発生するごとに、問題の根本原因、いわゆる「真因」を追及して改善するという「QCストーリー」を適用することです。一方、TOCは制約を「認識(Identify)」して「徹底活用(Exploit)」します。まずは、制約(ネック工程)がスループットを生み出している時間を最大にすること、つまり制約工程が止まっている時間をなくすことから取り組みます。
「小説ザ・ゴール」での取り組みは、昼休みにボトルネック設備を止めないようにしたり、ネック工程の前で検査をして不良品を選別しているだけで、「KAIZEN」活動を推進している側からすると低レベルに見えるかもしれません。
ただ、カイゼン活動を長年継続していると、カイゼン疲れのような症状が出てくる事があります。カイゼン活動はQCストーリーの手順に乗らないような問題(テーマ)は扱いにくいので、ある程度活動を進めてゆくと問題が目につかない(ない)ことが問題になったりします。ですから工場幹部は「業績直結のカイゼン活動」などというスローガンを掲げて、問題を見つけることに躍起になったりするのです。
そんな中でTOCが制約(ネック)工程が工場全体のスループットを決めていると主張したのです。するとカンのいい人は気がつく訳です。たしかにネック工程が工場全体のスループットを決めている、だから「制約工程」だけに集中すれば良いんだと・・「みんなで全部やる」の改善は必要がない、やめても大丈夫だと。
そこで、本当にパラダイムが変わって、どうやったらボトルネックをもっと動かせるかを考え始める訳です。TOCでは、「なぜ制約(ネック)工程の設備は止まっているのか」という事に集中しますから、原因をとことん調べて改善するアプローチを取ります。そのためには、現場だけではなく技術系のスタッフにも入ってもらい、ボトルネックを最大限動かす具体的な方法を議論するのです。
このように、制約に集中するという事は、今までは小集団活動に任せっぱなし、いうなれば現場に任せっきりだったカイゼンを、現場とスタッフが協力しながら「カイゼン」を進めるという事でもあります。
生産現場を横串で支える、生産技術や製品技術などのスタッフは新規設備の導入や既存設備のメンテナンスや修理などに時間を取られて、カイゼン活動に参加する余裕が中々生み出せないのが悩みと言われてきました。しかし、制約に集中して「カイゼン」するという視点で参加することで、多忙な時間の中でも成果が上がるやり方が見えてきますし、本当の意味で「終わりなき」カイゼンを実現できるのです。
ボトルネックに集中したカイゼン活動の威力(ある半導体系企業の事例)
では、ネック工程に「カイゼン」を集中する事で威力が何倍にも発揮された例を紹介しましょう。私の経験から言えば、相当なレベルでカイゼンが進んでいる工場でも、さらに20~30パーセントの水準で生産能力(スループット)を向上させる事が出来ます。ポイントは、まず正しく制約工程(ネック)を認識することと、スタッフが加わったカイゼンプロジェクトを集中して展開すること、の2つです。
ここからはある半導体系の企業の事業所の事例をご紹介します。この事業所は、品質はTQC(TQC=Total Quality Control全社的に取り組む品質管理)、設備保全はTPM(Total Preventive Maintenance 全員参加の生産保全)を導入して、それぞれ優秀賞を受賞するほどのレベル。その事業所でリードタイム半減とスループット倍増を目指してTOCを導入しました。
まずステップ1の「制約を見つける(Identify)」ですが、数百台の設備が連なっている半導体工場は、ネック工程を正確に特定するのも結構難しいのです。ザ・ゴールで説明されているのは、仕掛かりが一番溜まっているところがネック工程ですが、多くの設備と多くの品種が存在する半導体系の工場では、正確に負荷と能力を基本にボトルネックを割り出さないとダメな場合が大半です。
これは、我々のような工場改善を行うコンサルタントの間では半ば常識ですが、多くの品種(製品)を多くの機械設備を使って生産するという工場の場合、「ザ・ゴール」に紹介されたNCX10のように、分かりやすいボトルネック工程が存在せず、どこがボトルネック工程か分からないという状況は決して珍しくないのです。
ボトルネックが見つかったら、次は徹底活用(Exploit)です。この事業所のネック工程設備の不稼働状況を調べてみると、設備が停止している要因は大きく3つありました。
1. 材料を供給したり取出したりする、付帯作業に多くの時間がかかっていた。
2. 品種を切り換えるための段取り作業、その中でもプログラムを呼び出したりする操作で多くの停止時間が発生していた。これは本来前もって、「外段取り化」しておける作業で、段取りを上手くやれば最小限の停止時間で済ませることが出来るはず。
3.一定時間稼働した後に行う、清掃作業や保守・点検も結構な時間を費やしていた。調べてみると、保守・点検の手順が統一されず、作業者によって掛かる時間が違ったりする現象が確認された。さらに、ちょこっと設備が停止するトラブル、いわゆるチョコ停で生じる調整時間もバカに出来ない時間が掛かっていた。
こうしてみると、動いているように見えてもスループットに結びつく稼働時間は予想以上に低く、品種切替のための時間、定期的な点検清掃時間、作業ミスによる不良などを差し引くと、実際の有効稼働時間は50%台という結果が確認されました。こうした詳細な稼働調査を行う事で、どんなカイゼンを行えば良いかが明確になり、カイゼンの焦点が明確になります。
まさに、これがボトルネック工程に集中するメリットで、現場とスタッフの総力を挙げ、IE、QC、PMといった手法を総動員してボトルネックのカイゼンを行うのです。
この事業所の場合、作業者に起因する停止は、作業の優先順位を変えることで、効果が出そうな項目が多く即実行することにしました。また、品種切替やチョコ停時間の対策は、設備に詳しい生産技術者と連携し調整方法を工夫したり、調整に伴って発生する不良も含めて対策することが可能となり、大きく改善に寄与したのです。
段取時間も段取分析を行って改善策を検討して実施しました。付帯作業の外段取化や調整レスやワンタッチ化などのカイゼンを組み合わせて、10分以内で段取を完了させる、いわゆるシングル段取を達成することに成功しました。
さらに実際の機械稼働の時間も、反応時間を早くするために添加剤のレシピを工夫するなどして、地道なカイゼンを組みあわせ最終的には有効稼働率を40%以上引きあげることに成功しました。
既にデミング賞やPM優秀賞を受賞した、カイゼン活動をやりきった工場での効果ですから本当にすごいことです。まさにこれがTOCとIE、QC、PMなどの既存の改善手法と組み合わせて制約工程を徹底的に活用するというお手本なのです。これまでも、個別のカイゼン活動で同じような対策を行っていたとしても、全ての設備や作業を対象にして行う改善とネック工程のスループットを向上させる活動では全く意識が違う事が理解して頂けると思います。
この視点は、もちろん「人的な資源制約」にも活用できます。例えば、設計部門の制約の場合には、制約業務の「定義」から始めるのです。設計業務の「何が」本当の意味での制約になっているのかを明らかにします。例えば、設計業務の中の「構造計算業務」ならば、その業務を「集中」して行う事が出来るように環境を整備すること、そしてその後にはその業務をこなせる後継人材の育成までトータルで行う事が求められます。
ここまでご覧いただきありがとうございました!GSCでは、最新のセミナー情報など、仕事に役立つ情報を週に1回お届けしています。登録無料・いつでも配信停止可能です。GSCのニュースを見逃したくない方は、ぜひご登録ください!
▼記事に関するコメントは、お気軽にコメント欄にご投稿ください。また、当社へのお問合せ等は、以下の問合せフォームよりご連絡ください。
▼ゴール・システム・コンサルティングは、ただいまYouTubeも隔週月曜公開中です!今回の「制約を科学する」第2回の内容は、YouTubeでもお話しています。ぜひご視聴ください!
この記事が気に入ったらサポートをしてみませんか?