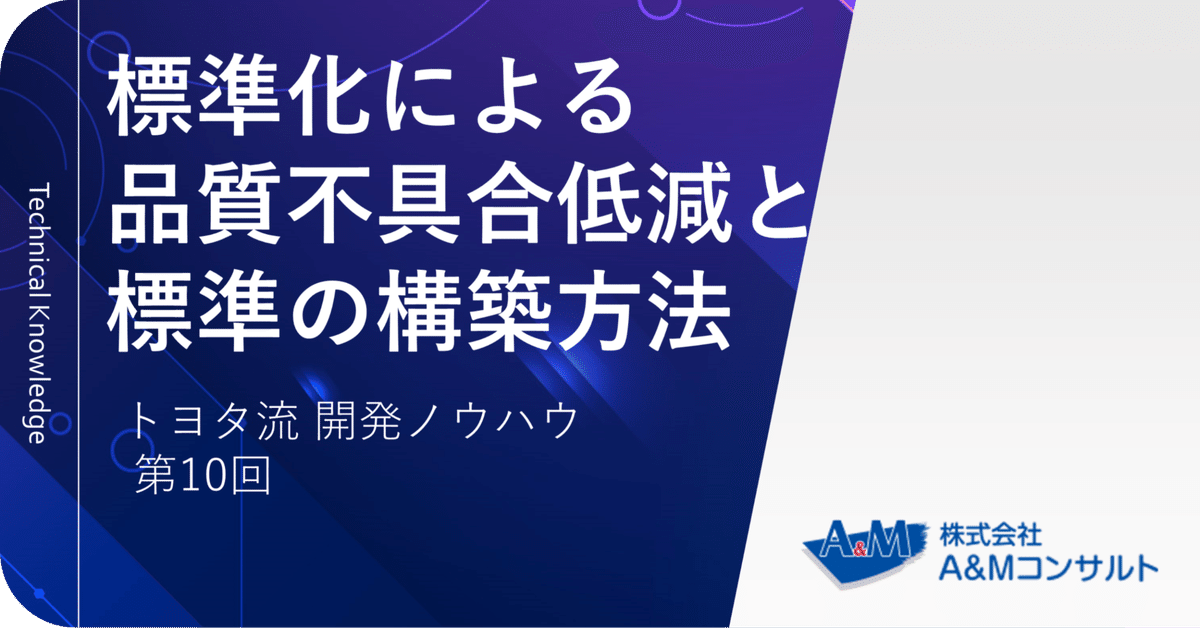
標準化による品質不具合低減と標準の構築方法|トヨタ流開発ノウハウ 第10回
その再発防止策、大丈夫ですか?
皆さんは、品質不具合やクレームに対処方法はどのような仕組みで運用していますか?
多くの企業が、原因を追究し、真因を見つけ、暫定対策、恒久対策、再発防止策を考え、品質不具合対策書のような報告資料を作成して終わっているのではないでしょうか。
また、再発防止策といっても、「教育します」、「チェックシートで確認します」、「2重チェックします」と記載していませんでしょうか?
これでは再発防止にならず、せっかくの品質不具合の情報を死んだ情報にしてしまいます。生きた情報に変換していかなければなりません。
では、「生きた情報」にするためには何をしたらいいのでしょうか?
品質不具合対策書をしっかりと記載できるように教育していけばよいのでしょうか?
答えはNO!です。
もちろん、その教育を否定している訳ではありません。
品質を暫定的に対策するには必要な事柄です。
真因を追求し、即時打てる対策を考え、お客様にご迷惑をかける時間を出来る限り短くする。この考え方は一方で必要になりますが、この方法ばかりとっていてもモグラ叩きとなり、現場が疲弊していくだけです。
本来実施しなければならないのは、真の再発防止策です。
私が考える真の再発防止策は、設計工程での仕組みの修正や変更です。
真の再発防止策=標準への統合
この世の中で発生している多くの不具合は、設計起因が80%を超えています。
不具合内容を確認すると、干渉していたり、ボルトナットが脱落していたり、いかにも製造での問題点が多くあるように感じますが、実のところは違うのです。
例えば、図面上は干渉チェックを行い、問題がなかったとしても、他の部品の組付けの影響で干渉してしまったり、組付けにくいことによって、ボルトナットを完全に締め付けることが出来なかったりします(もちろん、製造段階の組付けミスやポカミスによって、発生している場合も多く存在します)。
結局のところ、真の問題≒真因は、そのような製造しにくい製品の構造に問題があるために発生していることがほとんどです。
このような状況から脱却する必要があり、それが「真の再発防止策=標準への統合」です。
不具合が発生した段階で、まずは暫定対策を検討していきます。その暫定対策を行っている間に恒久対策を検討していきます。その上で安全に製品が使用できるように対応していきます。
一方、その製品を含めた類似の製品群全体を考えて、同じ問題が起きないような構造を検討していきます。その検討した構造を標準に組み込むことが可能かどうか議論し、次のモデルチェンジや標準をアップデートできるタイミングで、変更していきます。
まとめていくと、下記の3つの仕組みが今の設計部門には必要になってきます。
①再発防止策の中に設計の変更を検討する仕組みを組み込む
②設計の変更をその製品だけに留めず、類似した複数の製品で同じ対応策が実行できるように検討する
③②の内容を標準に組み込み、流用元を必ず標準から使用するようにする
標準に組み込めたとしても、流用元を過去のモデルや製番から使用してしまうと対策が出来ていない流用元を使用することになってしまいます。そうすると、また類似の問題が起きてしまう可能性が高いのです。
設計の仕事の仕方を大きく変えていく必要があります。
この標準をいかに使用しやすい標準にするかがキモです。
標準の構築の仕方
もう一つのキーワードである標準の構築の仕方も解説していきましょう。
標準を常に流用元として使用してもらうためには、案件毎にカスタマイズしている内容の整理が必要です。そのカスタマイズしている内容を折り込み、将来的に変更される可能性のある内容も追加することで標準を使用しやすくなります。
そのような誰でも使用可能な標準の構築の仕方は次のようになります。
①体系化・基準設定
各カスタマイズ内容にどのような機能があるのか、現在は使用されていないカスタマイズ内容や将来的に不要となるバリエーションを視える化し、体系的に整理する。
また、各オプションやバリエーションをどのように選択しているのか、選択の考え方を明確にする。
②トレンドの見極め
各バリエーション内容をあらかじめ標準的に組み込む。
⇒仕様選択時にパラメーターを選択することで自動的にバリエーションが装置に組み込まれる【標準のグレード化】。また、すでにバリエーションが組み込まれた装置を準備しておき、図面作成が不要となり、生産性が向上し、お客様にもコストメリットを提供することが可能になる。
使用するお客様のことを考え、多くのお客様が選択される可能性の高いバリエーション内容を最初から組み込んでおく。これにはターゲットとなるお客様の明確化や、お客様の使用方法を詳細に分析する必要がある。
③統合・廃止
各バリエーションを統合する。
⇒統合することにより、部品の共通化、部品点数の削減を図り、コストメリットを抽出する。
④図面準備
②③の内容を図面化する。
バリエーションだけでは多岐に渡るお客様のニーズに合致することが難しいため、モジュール化の「変動・選択」の要素を組み込み、バリエーションを可変させるようにしておく。
このような標準の構築では、今後発生する不具合を未然に防止することを可能にするだけではなく、設計効率が向上します。
設計者に余裕が出ることで、しっかりと検図の時間を確保でき、製造現場に足を運ぶことが出来るようになり、品質はさらに向上していきます。
また、その時間的余裕は設計だけを行ってきた設計者が新たな製品を創造する=開発への挑戦も可能にできるでしょう。
このように1つの不具合やクレームを対策していくモグラ叩きの仕事の仕方から脱却を図り、企業としての競争力をつけていく必要があります。
最後に、これだけは皆さんにご理解いただきたい。
日本の製品は品質が素晴らしいと言われていますが、その品質レベルを他の国に追いつかれた時点で、コスト競争に入っていきます。コストだけでは勝ち残ることは非常に難しいのです。
品質レベルを向上する仕事の仕方を仕組み化した上で、新たな価値を創造する仕事に変革していかなければならないのです。
「競合よりも少しでも安く」は今やもう古い考え方です。
新しい価値を創造する企業へ変革を図ってほしい。その目的のためにも足元を固める標準化を進めていってほしいと考えています。
この記事が気に入ったらサポートをしてみませんか?