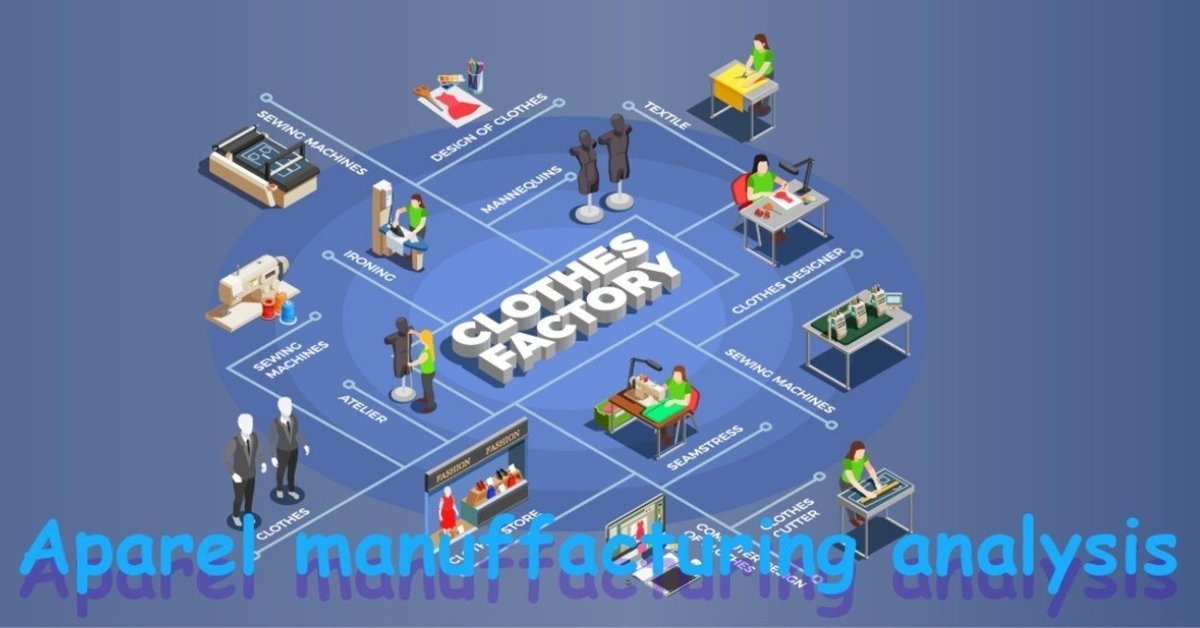
アパレルの生産管理で縫製工程分析を行った方が良い訳【初心に戻る】
こんにちは、タケロー・ニーノです。
工場さんに生産を依頼し、工賃の見積もりを出してもらう時は、どんな基準を持っているでしょうか??工程分析をした上で出してもらているでしょうか?なんとなく去年・一昨年の実績のままのイメージで、工場からの見積もりには取り合えず「安くしてください!!」って言ってることも多いのでは?
工場さん側も、ほとんど社長の頭の中で組み立てて、工程分析として書き出すことまではしてないことの方が多いかと思います。工場としては、分析を見てもらったところで、理解してもらえないって思ってたりします。
案外耳の痛いところではないでしょうか。ワタシが所属していた自社工場もあるメーカーの営業マン・生産マン共に工程分析が理解できる人は皆無でしたし、「工程が多くなるから工賃がこれだけ掛かります。」と説明しても、「じゃあ高いから他の工場を探して!!」って言われて終了でした。
商売=できるだけ安く作って、できるだけ高く売る ・・・これが基本なのは間違いありません。
分析をして工程数を理解して、ある程度フェアな話し合いの中でアパレルと工場の良好な関係で仕事ができないと、業界全体がお互いの足を引っ張って負のスパイラルになってしまってないかと危惧している次第です。
まずは基本のスリット付きTシャツの工程分析で考えてみます。
これは、非常に基本的な形のスリット付き半袖Tシャツのハンガーイラストです。スリットは二つ折りで、袖口の二本針は丸縫いではなく先に平状態で二本針始末をすることを想定しています。単純なデザインですが、これだけでも工場にはまだ目に見えない部分での選択肢があります。
それが、 袖を平で縫うか、 丸縫いするか、 ということです。
正直、外見(裏返さない)でこの違いを判断することは難しいです。着てみて分かる人は?はて、どのくらいいるでしょうか?因みに僕はその部分を見て買ったことはありません。
Tシャツ(脇ー袖下一気縫い) 工程分析と図解
Tシャツ(袖丸縫い) 工程分析と図解
縫製工程分析の考え方
1:3人のラインの場合 1日の持ち時間 : 60秒 × 60分 × 8時間 × 3人 = 86400秒
2:86400秒 ÷ ( 工程の合計タイム × 余裕率 ) = 1日の想定枚数
3:ラインの目標売上 ÷ 1日の想定枚数 = 見積もり工賃
工程分析はイメージだけでもOK 時間とコストの関係を頭の隅に入れましょう
先ほどの工程分析で見ていただければお分かりいただけると思いますが、、、袖丸縫いのTシャツは、脇ー袖下一気縫いのTシャツより、1着につき20秒多く時間がかかっていますね。20秒、長いと感じますか? 短いと感じますか?数十着くらいならさほど時間の長さは気にならないかもしれませんが、、、、(あくまでもイメージです。)
20秒差 × 3000枚の生産 = 60000秒
60000秒= 最も安い地域の最低賃金¥762 × 約5.5時間 × 3名 = ¥12573(法定福利・光熱費 他含まず)
60000秒= 脇ー袖一気縫いTシャツ 180枚分の縫製時間 = 工賃¥462の場合は ¥82800の売り上げ
さて、この数字をどうご覧になられるでしょうか? もちろんビジネスでは常にセオリー通りにはいかないものです。ですが、工場に仕事を依頼する立場として、理解すべき点は多いのではないでしょうか。
デザイン変更で工程が増える。
縫い方の指定で、作業時間が増える。
品質ネームが間に合わず、後付けになる。
生地の不良・プリント・刺繍不良でのパーツ裁ち直し
生産中の変更や確認事項の発生やトラブルは様々ですが、全て時間のロスに直結します。
工賃を安くしてください!!=短い時間で生産してください 、、、ということのはずですよね。
ならば、生産管理は工場さんに、時間ロスをさせてはいけないという意識で仕事をすべきではないでしょうか。。。
【結論】 アパレル生産管理は工程分析の基礎は知っておいた方が良い。
ファッションそのものって感性の部分があったり、クリエイティブが重要だけれども、プロダクト現場に繋がるお仕事は、正確さや緻密さや計算も重視しなければならないと思います。ワタシはアパレル業界に長年いて、そういった部分が足りないと感じて仕事をしてきました。
生産が上手くいかなくなったときは、初心を振り返って、過去にはなぜ工程分析なるものがあったのかを、見直してみるのもいいかもしれません。
読んでいただき、ありがとうございました。
いいなと思ったら応援しよう!
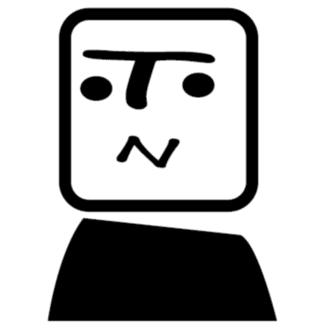