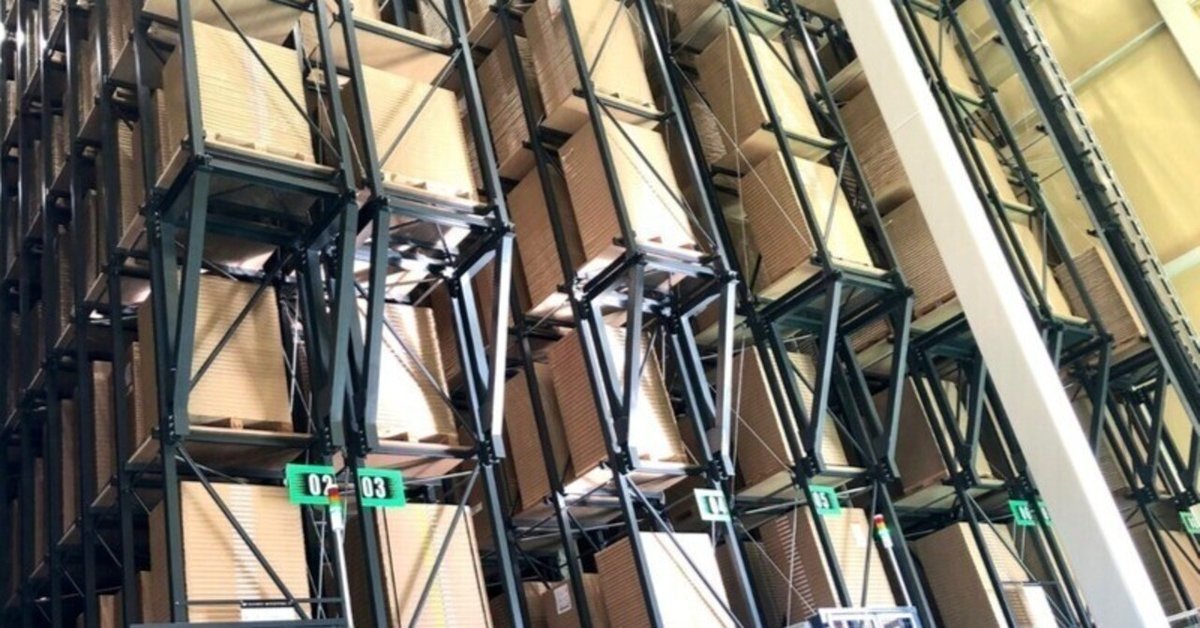
自動倉庫の功罪について
最新型自動倉庫の設置
30年ほど前の話になりますが、機能の違う三つの物流センターを統合し新たな物流センターを立ち上げるという経験をしました。統合前の三つのセンターはそれぞれ「メーカー物流」「量販店向けの卸物流」「小売物流」で、それぞれ別々の場所にあり、「メーカー物流」と「量販店向け卸物流」はアウトソーシングしていました。
会社としては3センターを統合することにより物流機能の効率化をはかり又、アウトソーシングにより外部に流出している資金を抑制する狙いがあったと思われます。
新センターには当時としては最新型の自動倉庫を設置されました。
レーン数:3 ラック数:8,500 最大格納ケース数:8,500
つまり1ラックに1ケースを格納する方式です。(当時としては珍しかったと思います)
この自動倉庫はセンターの各フロアー(新センターは4層構造でした)の搬送ラインと連携しており、出庫ケースは引き当てと同時にそれぞれの保管フロアーの搬送ラインに出庫されてくる方式で、フロアー業務としてはとても便利でした。
保管するケースの管理方法は入庫時に「管理NOシール」をケースに貼付し1Fの搬送ラインから入庫ラインに乗せ、あとはマテハン側が自動的に空きラックを探し格納されるという方式です。格納時にマテハン側で管理NOとラックNOの紐づけがなされます。管理NOにはSKUと入り数が紐付いています。これによりどの商品がいくつ、どのラックに格納されているかを管理していました。
この自動倉庫の良かった点
この自動倉庫を使っていて良かったと感じたことは、まず立体的構造で空間を有効的に使用できるので収納効率が良いという事、さらに必要な時に必要な商品が必要なフロアーの搬送ライン上に自動的に出庫になってくるという事でした。さらに良かったこととして、棚定量をオーバーして入荷してきた商品を自動倉庫に入れることでいわゆる延長在庫(棚に入りきらずに通路等に棚の延長として仮置きする)がなくなり、常に在庫フロアーの作業スペースや通路を十分に確保することでき、延長在庫が通路をふさぎピッキング作業に支障をきたすといった事がないということでした。さらにさらに良かったのは、自動倉庫に自動補充の機能を持たせ棚定量を切った商品を自動的に出庫させ、棚入れしておけば、ピッキング作業時には常に棚からピッキングするだけという状態が作れるという事でした。在庫フロアーには十分な作業スペースがあり、ピッキングは常に棚からのみで完結できるという、まさに理想のピッキングシーンが実現できると感じていました。
この自動倉庫の悪かった点
自動倉庫を使い始めて2年くらい経ち使い方にも小慣れてきたころ、
ふと立ち止まって「自動倉庫ってほんまに1億数千万の価値があるのかな」と考えるようになりました。
仮に入荷してきた商品を在庫としてケースのまま保管するとしたら、そのままフロアーに荷揚げし、棚の延長在庫として棚の横に置くだけですが、自動倉庫に入れるとなればまず入荷したケース内の商品をSKU単位に仕分けし、その後SKU単位でラックの規格サイズに合った段ボールケースに入れ替えなければなりません。(この自動倉庫は1ラック、1ケース方式なので入庫するケースのサイズは最大値と最小値が決まっています)入荷量が多い時には大変な作業量になります。たとえ1SKU、1ケースの形態で入荷したとしても、大きすぎるケースだった場合等はやはり入れ替え作業が発生します。さらに新品の段ボールケース使用することになるので段ボール費用もかさみます。
そして怖いのは、この入れ替え作業の時にミスが発生するということです。入り数のカウントを間違えたり、シール発行時に品番を間違えて発行してしまったり、シールは複数枚まとめて発行していたため、たとえ正しく発行したシールであっても貼付すべきケースを間違えたり、相当な確率でミスが発生していました。よく言われる「機械は間違わないがその機械を扱う人間は間違える」というやつです。
シールの発行・貼付に間違いがあると棚の実在庫と在庫データーに差異が発生し、必要な商品が出庫されてこないとか、不必要な商品が必要ないのに出庫になって出てくるといった現象が起こります。そして理想的だったフロアーが崩壊していきます。出庫になって出て来た時にシールの貼付間違いに初めて気付き、データーを修正したりして対処しますが大変なのはシール発行を間違え、さらにその間違いに気付かずそのままそのシールをケースに貼付し入庫してしまう場合(ブラックボックスの中)で、その商品が数日後あるいは、数か月後に出荷指示がかかり出庫になってくれば、まだ先ほどの様にデーター修正で対応できますが、さらに大変なことは、しばらく注文がなく出庫にならないまま棚卸を迎えたときです。実地棚卸は、あくまで自動倉庫内は正しいことを前提に棚在庫数だけをカウントしていましたので、入庫間違いがあると当然棚在庫で理論在庫と実棚数に差異が発生し、大きな棚卸差異となります。
棚卸後の調査対象となり色々調査をすることになりますが、いかんせん8,500ケースが保管されている立体型の自動倉庫内をすべて実地に調査することは極めて困難です。棚卸で修正になった間違った在庫データーで新しい期を迎え、その後入出庫が繰り返され、忘れた頃に間違ったシールが貼られたケースが出庫になって出てくることになります。ケースの中の商品はすでに季節外れ、又は型落ちとなっており営業的にも大きなロスを発生させることになってしまいます。現場では、入庫時の検品強化や、棚在庫数や当日の入荷数を超える数量のシールが発行されたときはエラーリストを発行するなどの間違い防止対策は取っていましたが、完全には防止出来ていませんでした。
又、この自動倉庫を使っている中で現場として困ったのは、終業時間間際に大型量販店からの大量のオンライン発注があり、営業側がそれを調整もせずそのまま倉庫側に転送してきたときでした。発注データーが飛んでくると、まずは棚在庫に引き当たるのですが、棚在庫では受注数を賄いきれないときは自動倉庫側へ出庫指示がかかります。量販店のこういった突然のオーダーは得てして大量発注であることが多く、時には自動倉庫からの出庫ケースが数100ケースにも200ケースにもなることがあります。数100ケースの出庫となると、いくら新型の自動倉庫といえども数時間はかかります。出庫フロアーの搬送ライン上にはそこまでのケース数はプールできないので、人手によるラインからの抜き取り作業が必要となります。そして予定外の残業が発生してしまいます。
又、この自動倉庫のランニングコストとして最も大きかったのは故障時の修理費用でした。自動倉庫が故障し出庫が出来ないとなれば顧客からの注文に対応できなくなり大変な事態となります。あわてて自動倉庫の業者に緊急連絡を入れてサービスマンに来てもらうのですが、タイミングよく近くにサービスマンがいるはずもなく、到着までに数時間も要することも度々でした。サービスマンが来てもすぐに復旧できるとは限りませんし、さんざん調べてもらった結果が部品の取り寄せ、あるいは別注にて作成ということもありました。こんなときは、「人間出庫」と言って、作業員が安全ベルトを使用して必要な商品が格納されているラックまでよじ登り、まさに命がけで出庫していました。サービスマンの出張費・技術料・滞在時間に応じた費用・部品代などなど修理費用はすぐに数十万円単位になります。いわんや作業員の安全確保など…。そんな故障が設置から年数が経つほどに頻繁に発生するようになっていました。
自動倉庫撤去の決断
そんな億を超える経費をかけて設置した自動倉庫なので物流側だけではなく本社サイドでも注目される設備でした。上層部の間でどのような話し合いがあったのか、今となってはわかりませんが、結論として自動倉庫は撤去することに決まりました。自動倉庫を撤去し、その場所に床を張り、通常のフロアーとして使用することになりました。(3フロアーが増坪)
保管ケースを床に隙間なく積み上げることで、保管可能数は自動倉庫使用時とそれほど変わらなかったです。但し、その積み上げたケースを積み降ろしするのは大変でした。さらに、ケースを高く積み上げることによって下の方のケースが圧し潰され、荷崩れが発生したりしました。
但し、増床したフロアーのスペースやケースの入出庫のために増員した人員はフレキシブルに活用でき、自動倉庫を撤去した効果はあったと思っています。
億の経費をかけて設置した自動倉庫を数千万の経費をかけて撤去することは、企業組織のなかでは各自の保身意識も働き難しいはずですが、時の先輩達はよく決断出来たなと思っています。
大型設備の導入は慎重に!
そして「先輩、ナイス決断でした!」
(乱文御免)
この記事が気に入ったらサポートをしてみませんか?