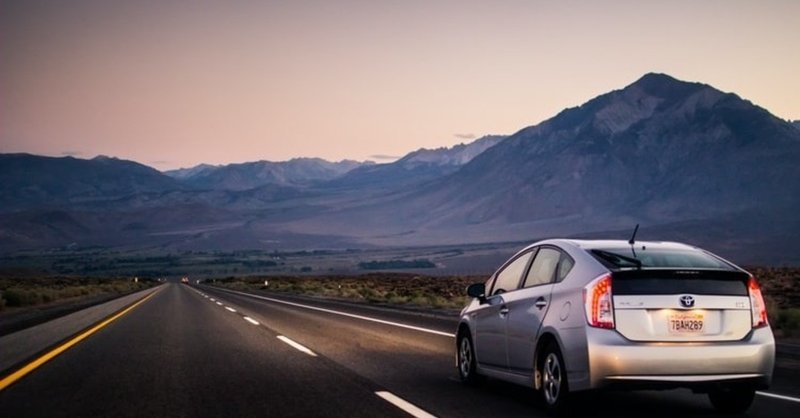
"ど"文系の私がトヨタ生産方式についてまとめてみた
”ど”文系で製造業の人材育成部門(しかも現場作業者への教育チーム!)に
配属された私が少しづつ製造業や人材育成に関するリテラシーを高めるために「名著」を読んで、自身の資産となるようアウトプット(まとめ)してみます。
同じような境遇(ど文系で製造業に就職・人事部門に配属)にいらっしゃる
日本全国の後輩の皆さんと私のアウトプットを共有できれば嬉しいです。
今回は【トヨタ生産方式-脱規模の経営をめざして-】
元トヨタ自動車(株)副社長 大野耐一著についてまとめてみます。
どのようにしてトヨタ生産方式は生まれたのか
つくれば売れる高度成長期ではアメリカ式の計画的な量産方法で量産効果のメリットを享受できるが、低成長期に突入すれば、通用しないどころかあらゆるムダを生み出している。そこで、多種少量生産でどうしたら原価が安くなる方法を開発できるかを考えた。
アメリカに比べて日本の生産性は8~9分の1、特に発達している自動車産業に比べれば10分の1程度だと知って、日本人はなにか大きなムダなことをやっているにちがいない、そのムダをなくすだけで生産性は10倍になるはずだ!と考えたのが出発点である。
トヨタ生産方式の基本思想
徹底したムダの排除
ムダを徹底的に排除して生産効率を上げて原価低減することを基本思想としていて、ムダとは①つくり過ぎのムダ ②手待ちのムダ ③運搬ムダ ④加工そのもののムダ ⑤在庫のムダ ⑥動作のムダ ⑦不良品をつくるムダ である。
生産現場に「流れをつくる」
生産現場に流れをつくることは基本条件・基礎であり、工程順に異なった機械を配列して1個1個つくったり、1台の旋盤、1台のフライス盤、1台のボール盤といったふうに1人の作業者が多数の工程を担当する(多工程持ち)ことで流れをつくっている。
生産の平準化
つくり過ぎのムダを排除するためにロットを小さくして、なるべく同じものを続けて流さないようにすることで生産の平準化を図っている。
少人化
生産量に対応して5人でも3人でもやれるようにすることで、定員化しないやり方である。
「なぜ」を5回繰り返すこと
「なぜ」を5回繰り返すことは思考原則であり、ものごとの因果関係とか、その裏にひそむ本当の原因を突き止めることができ、問題が起きた場合、原因の突き止め方が不十分であると、対策もピント外れになってしまう。
必要数=生産量
トヨタ生産方式を支える2本柱
ジャスト・イン・タイムと自働化
野球に例えるならジャスト・イン・タイムは連携プレー、自働化は選手一人一人の技を高めることである。
ジャスト・イン・タイムとは
1台の自動車を流れ作業で組み上げていく過程で、組付けに必要な部品が、必要なときにそのつど、必要なだけ、生産ラインのわきに到着すること。
物理的にも財務的にも経営を圧迫する在庫をゼロに近づけることができるが、実際にジャスト・イン・タイムの状態に持っていくことは至難の業である。
難しい理由その①
生産現場の計画は変更されるためにあるようなもので予測の狂い、事務管理上のミス、不良や手直し、設備故障、出勤状況の変化が要因となる。
難しい理由その②
各工程に生産計画を示すと後工程とは無関係に部品が生産され、一方では、欠品がありながら、不要不急な部品の在庫が山ほどたまる。
さらに悪いことには
生産現場の各ラインにおいて、正常と異常の状態の区別がつかなくなる。
どうすればよいか、
従来の考え(前工程が後工程へ物を供給する)を逆にみて、後工程が前工程に、必要なものを、必要なとき、必要なだけ引き取りに行くと考えてみた
→前工程は引き取られた分だけつくればよい
→何を、どれだけ欲しいのかをはっきりと表示すればよい(かんばん)
後工程引き取りの運搬管理方法に逆転!
・かんばん
ジャスト・イン・タイムを実現するための管理の道具、長方形のビニールの袋に入った1枚の紙切れで引き取り情報と運搬指示情報および生産指示情報が記載してある。
自働化とは
自動化ではなく、ニンベンの付いた自働化、機械に人間の知恵を付与してを善し悪しの判断させる機能がビルド・インされているので、ちょっとした異常が起きた場合、すぐに機械が止まる仕組みになっている(不良品は生産されない)
ニンベンのある自動機械 = 自動定期装置付の機械
・定位置停止方式
・フルワーク・システム つくり過ぎのムダを防止するために標準手持量が常に保持されて各工程内が連動した状態で機械が稼働するシステム
・バカヨケ 不良品、作業ミス、怪我およびその他多くの具合の悪い点を自然に取り除いてくれるような仕組み
人は正常に機械が動いているときにいらずに、異常でストップしたときに初めてそこへ行けばよいので、1人で何台もの機械が持てるようになり、工数低減が進み、生産効率は飛躍的に向上する。
材料や機械に内在する問題が管理監督者の知らないところで繕われていては、問題がはっきりしない。
人手作業による生産ラインでも異常があれば、作業者自身がストップボタンを押してラインを止めるようにした。
目で見る管理(トヨタ生産方式の運営手段)
目で見る管理とは何が正常で何が異常かを目で見てすぐわかるようにすること。
・標準作業表
効率的な生産を遂行するための諸条件を考慮して、物と機械と人の動きを最も有効に組み合わせることを作業の組合せと呼び、この組合せの集約された結果を標準作業である
標準作業の三要素
・サイクル・タイム 1個あるいは1台を何分何秒でつくらなければならないか
・作業順序 作業社が時間の流れとともに作業をしていく順序
・標準手持ち 作業をしていくためにこれだけは必要だという工程内の仕掛品
・アンドン
生産現場にかかげられたライン・ストップ表示板で運転中は緑色、助けを呼ぶときには黄色、ライン・ストップが必要であれば、赤色を点灯する
(かんばん)
感想
時間は動作の影と呼ばれるが、遅いのはほとんどの場合、動作・手順がちがうことによって生じる
→これをどう指導するかが現場の管理者の腕であり、手順や急所、コツといったものをきちんと教え込み、また表示などを明確にすることによって、やりなおし作業や部品の取り違えといったムダな動作から早く抜け出すよう指導する
つくり過ぎのムダ=最も悪性かつその他のムダを隠してしまう
仕事の進み過ぎで、本来、手待ちにならなければいけない時間なのに、つぎの作業をやってしまい、手待ちがかくれてしまう
この繰り返しで在庫がたまってしまい、この在庫を移動させたり、きちんと積み直したりという動きが仕事と見なされてしまうと、ムダと作業の見分けがつかなくなる
この記事が気に入ったらサポートをしてみませんか?