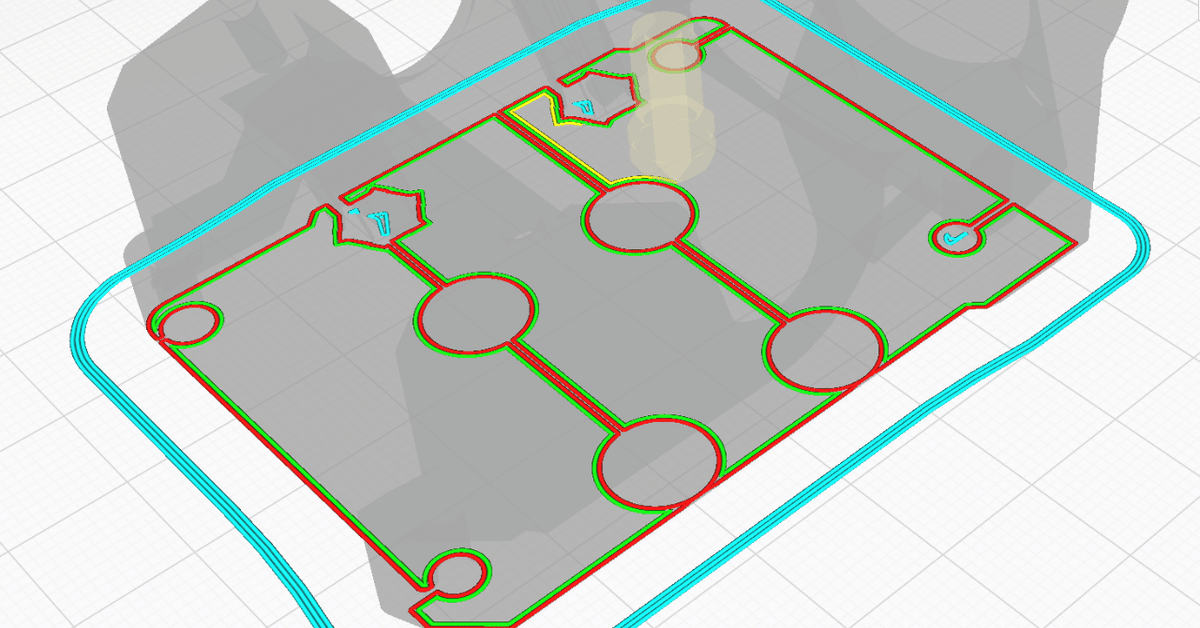
FDM/FFF3Dプリンターで印刷する機械部品をモデリングするときの、たくさんの小さな工夫
3Dプリンタは魔法の機械かもしれないが、魔法は魔法使いでなければうまく使えない。ハリーポッターだって魔法学校に通う。
魔法学校というわけではないですが、魔法をすこしでも簡単に成功させるための小さなトリックを紹介しようと思います。
定着を安定させる
何事もはじめが肝心。印刷のはじめ、つまり一層目をどうするべきか?
レベリングとか定着用の糊以外にも、3Dモデリングでできることもある。
1層目につながる穴を接続する
3Dプリントで気を抜けないのが一層目。小さな穴や飛び地形状がある場合、小さな部分の印刷が崩れたり剥がれたりして失敗する場合があります。
そこで、穴などには0.1mm程度のスリットを外側に向かって入れましょう。
(0.1mmを下回る場合スライサによってはスリットを埋められてしまう場合があるようです。)
深さは0.2mm程度で十分です。(一層目のレイヤーの厚みの半分超)
飛び地については幅0.8~1.0mm厚み0.2mm程度のバーを3Dモデルに加えて接続するといいでしょう。
(一般的な0.4mmノズルの場合で1往復分)
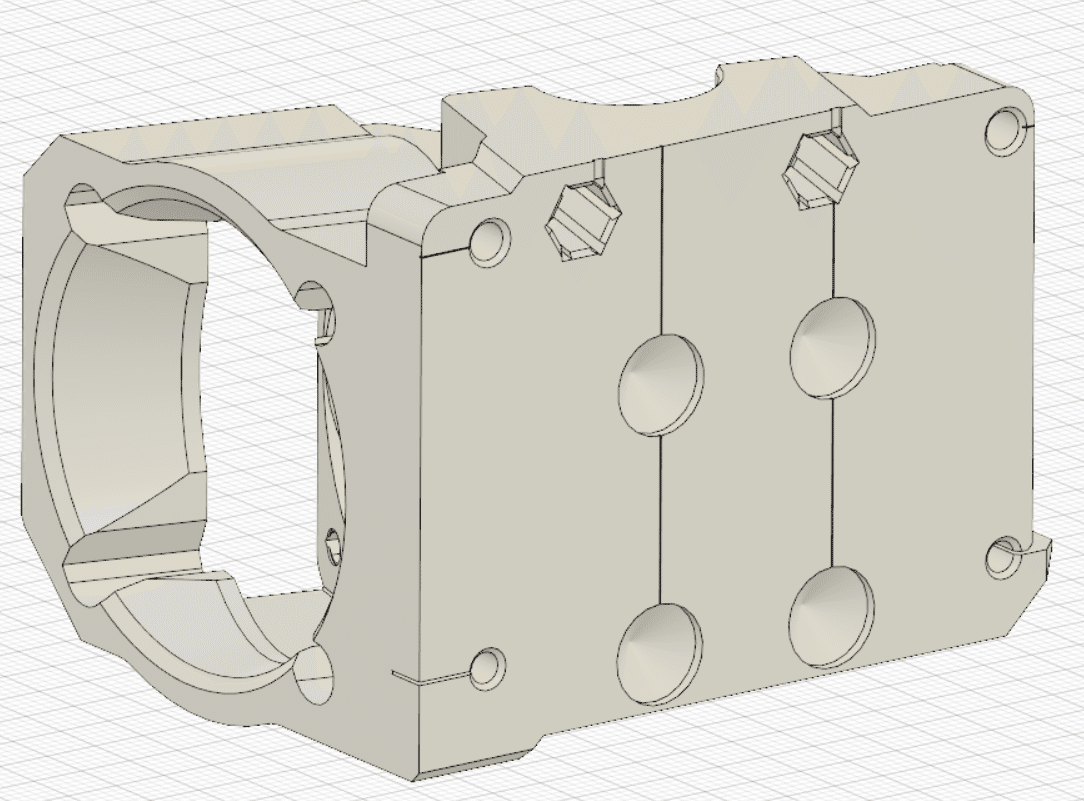
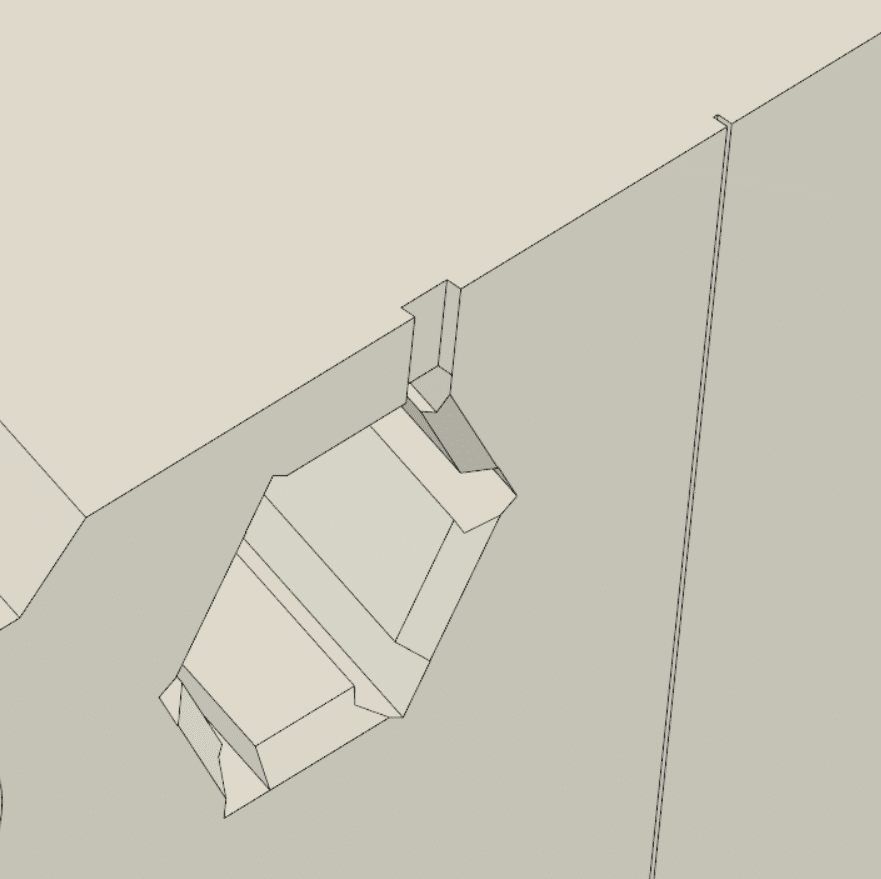
下の画像のように一筆書きに近くなるので、トラベルで引っかけたり小さな形状の初めに樹脂が出ないことも少なくなり印刷が安定します。
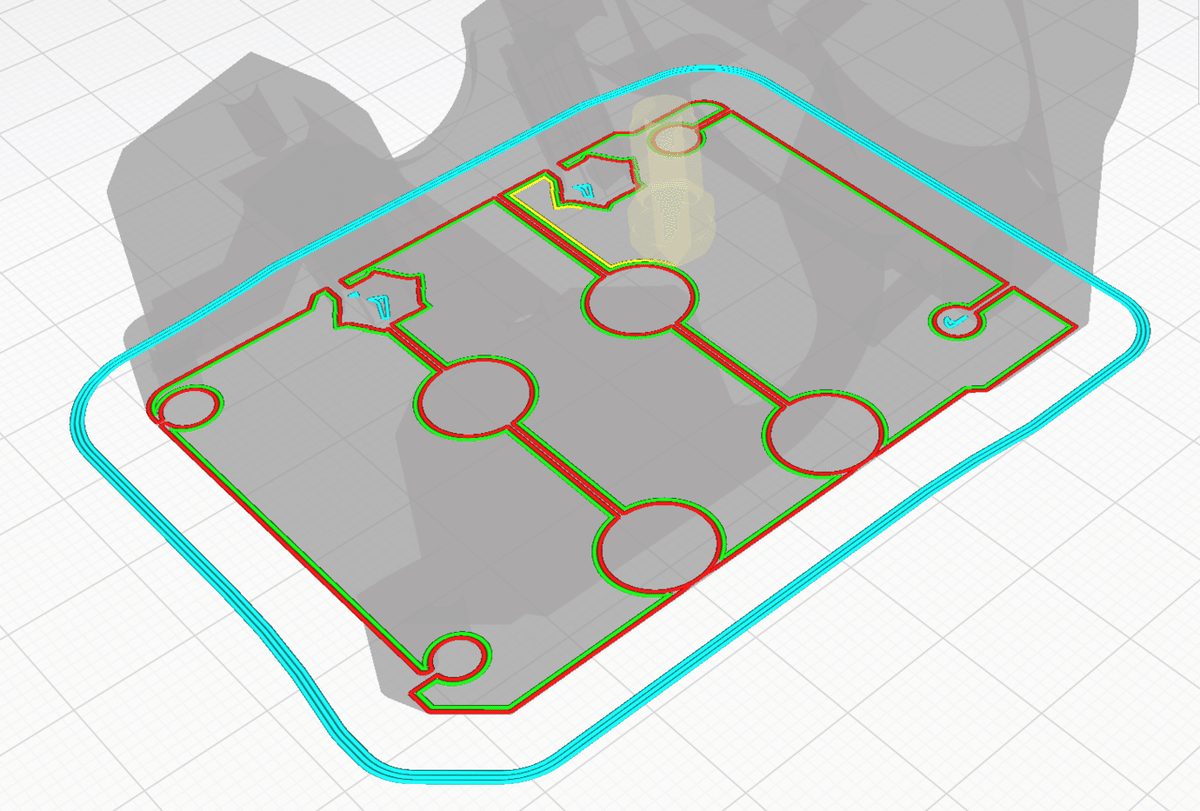
細い飛び出し部をつなげる/底面を広げる
定着の難易がそれなりでも、造形途中でトラブルになりがちな形状がいくつかある。例えば細く飛び出した底面や上に向かって広がって大きくなる形状である。
このような形状の場合は形状そのものを大きくするのが良いが、柔軟性が欲しいなどの理由で細い形状だからこそ意味がある場合が多い。
もちろんブリムなどを使用して定着させるのがセオリーであるが、ブリムが込み入ってしまうという欠点もある。
そこで一層目だけ形状を広げてブリムと類似の効果を得つつ、ブリムの場合の煩わしさを低減してみよう。
サポート材を減らす
サポート材を印刷するのも、外すのも手間だし、印刷時間も伸びる。
サポート材をつけ忘れて悲惨な事…….というのもありうる。
無くても成立する形状にしておくのも一手。
横方向の穴の上側をカットしてサポートを避ける
サポートが細い穴の中に残ると除去が厄介です。
さらに小さなサポートの生成は造形を不安定にする場合もあります。
これを避けるために印刷向きに対して上側を斜め45°にカットしてサポート材が生成されないようにします。
(プリンタの実力によっては60°程度でも良いでしょう。)
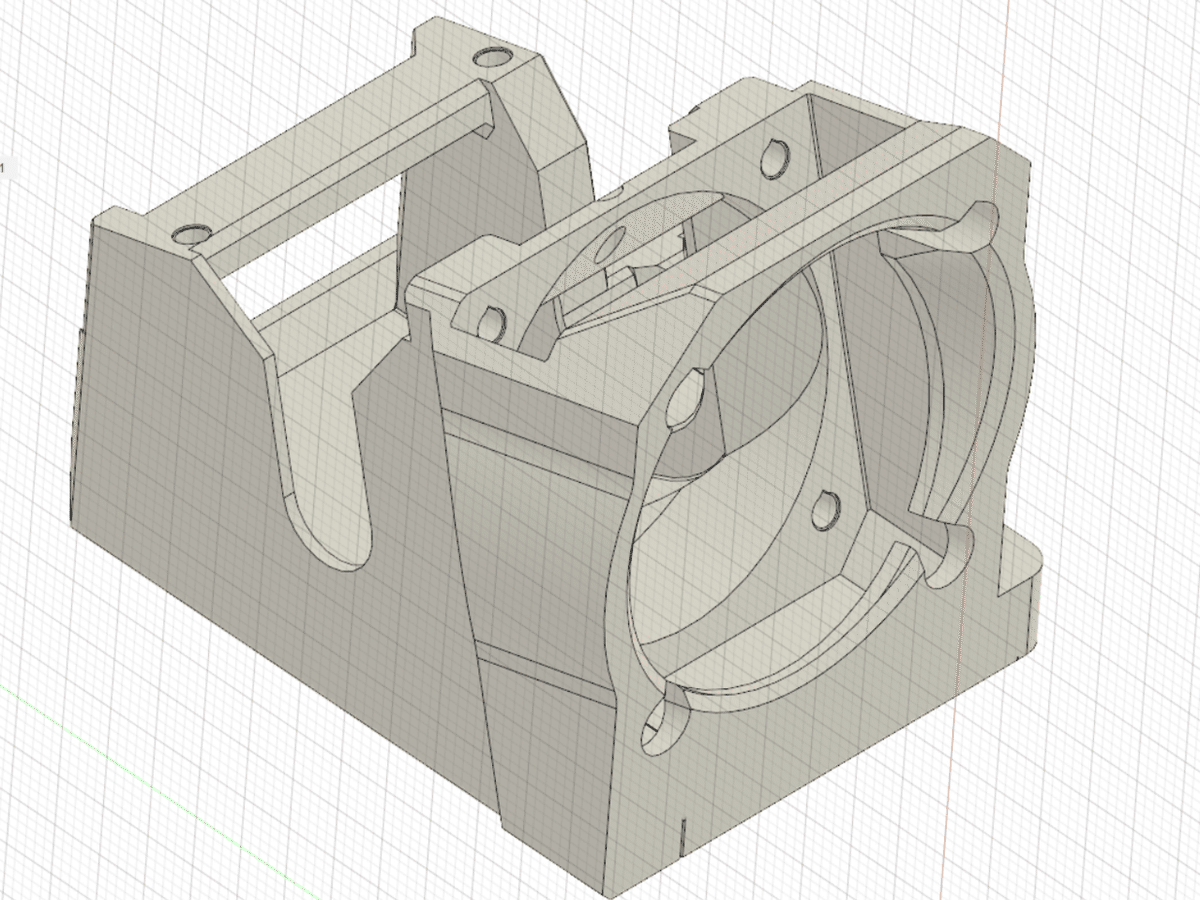
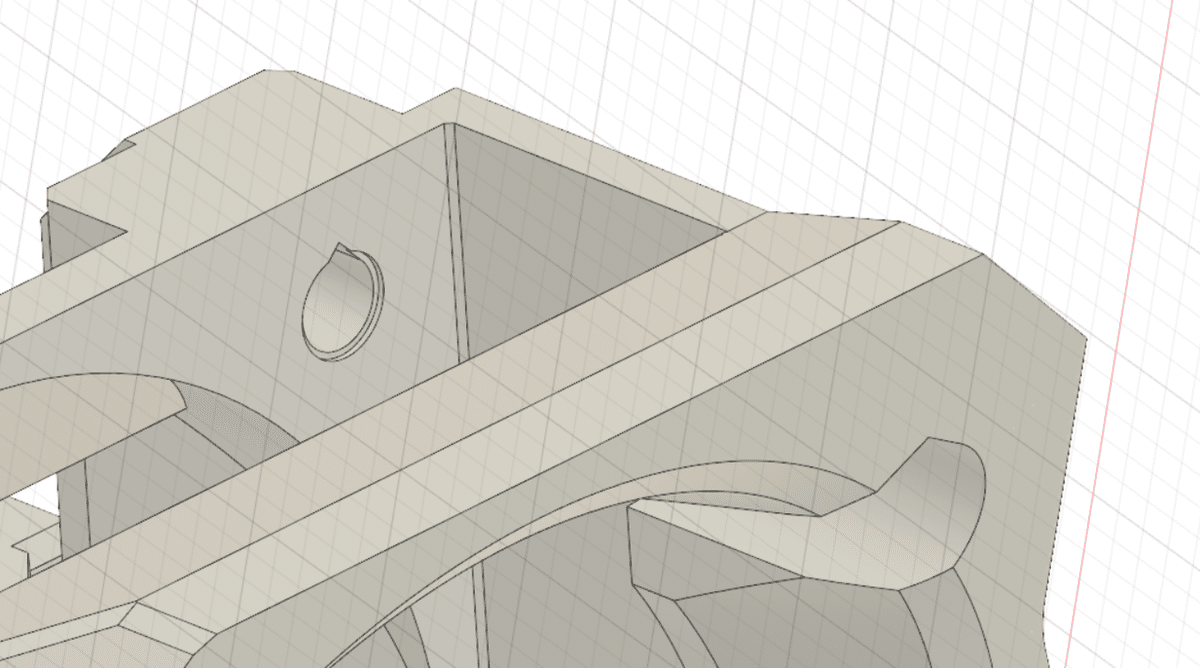
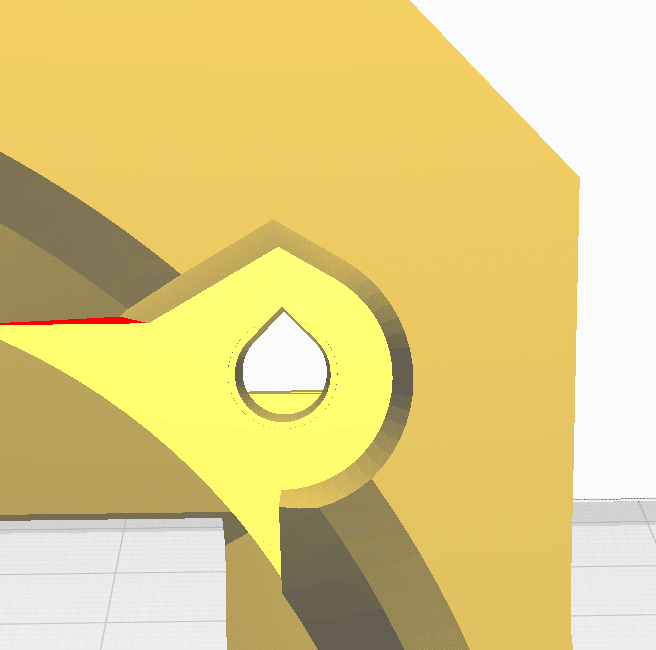
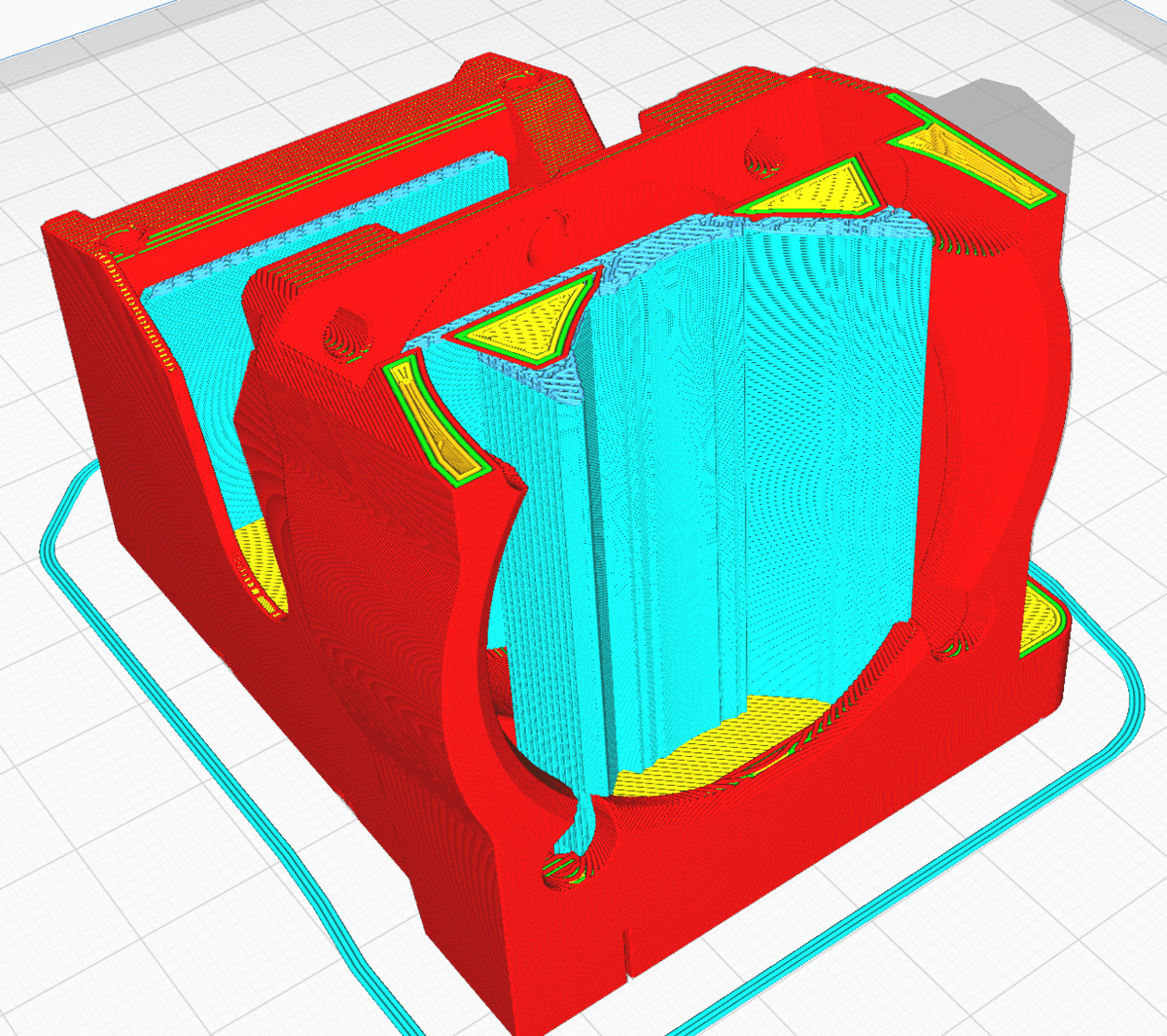
犠牲ブリッジ (わざとブリッジさせる)
例えば空中に浮かんだ水平面から垂直に穴があるような形状は造形にサポートが必要で、きれいに造形するのはサポート材や印刷時間、後処理工程に直結するので避けたい形状です。
ですが犠牲ブリッジ(Sacrifice bridge)と呼ばれる手法を効果的に用いると実用に十分な面を得ることができます。
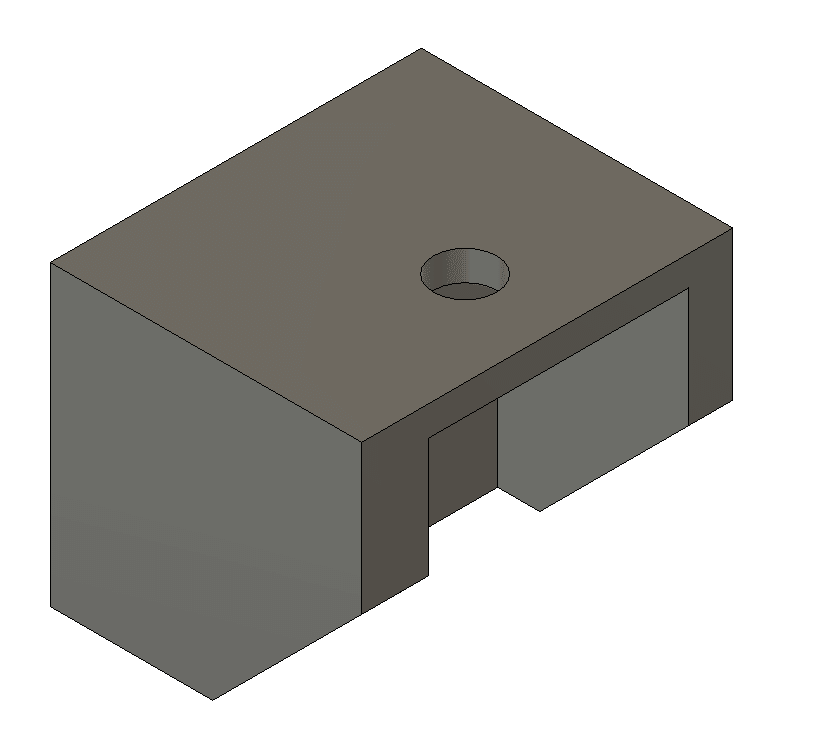
このような場合もちろんサポートインターフェイスを使用したりするのも一つの解決策ですが、3Dモデル側でもできる対策があります
積層一層分の厚みほどだけ穴を埋めてやりましょう。
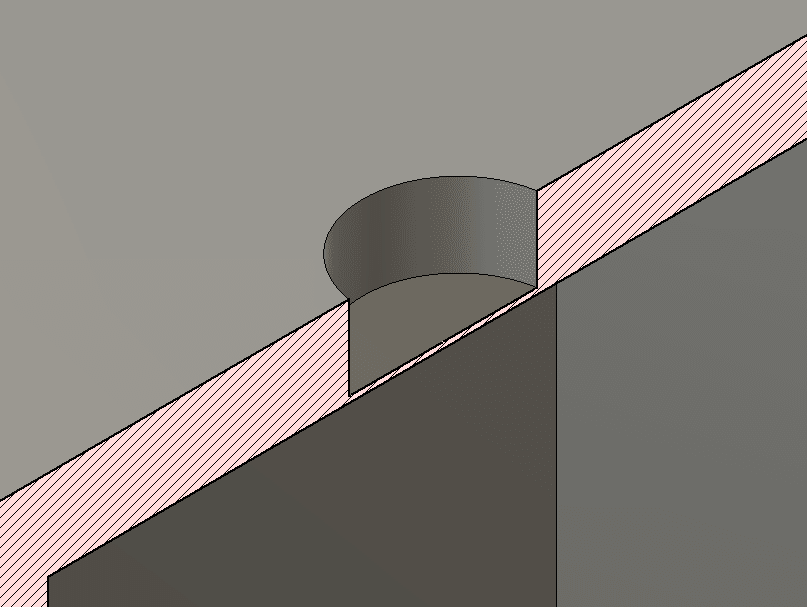
そうするとブリッジが形成されて、その上に穴の外周が綺麗に造形されます。
一層分(0.2mmの厚み程度)のブリッジですので、棒などで突けば容易に貫通しますので、ネジを通したりも問題なく可能です。

実際に印刷するとこれぐらい違います。(左:工夫なし/右:工夫あり)
穴のシェルが2層目以降すぐに安定しますし、見た目にも不安感が少ないですね。
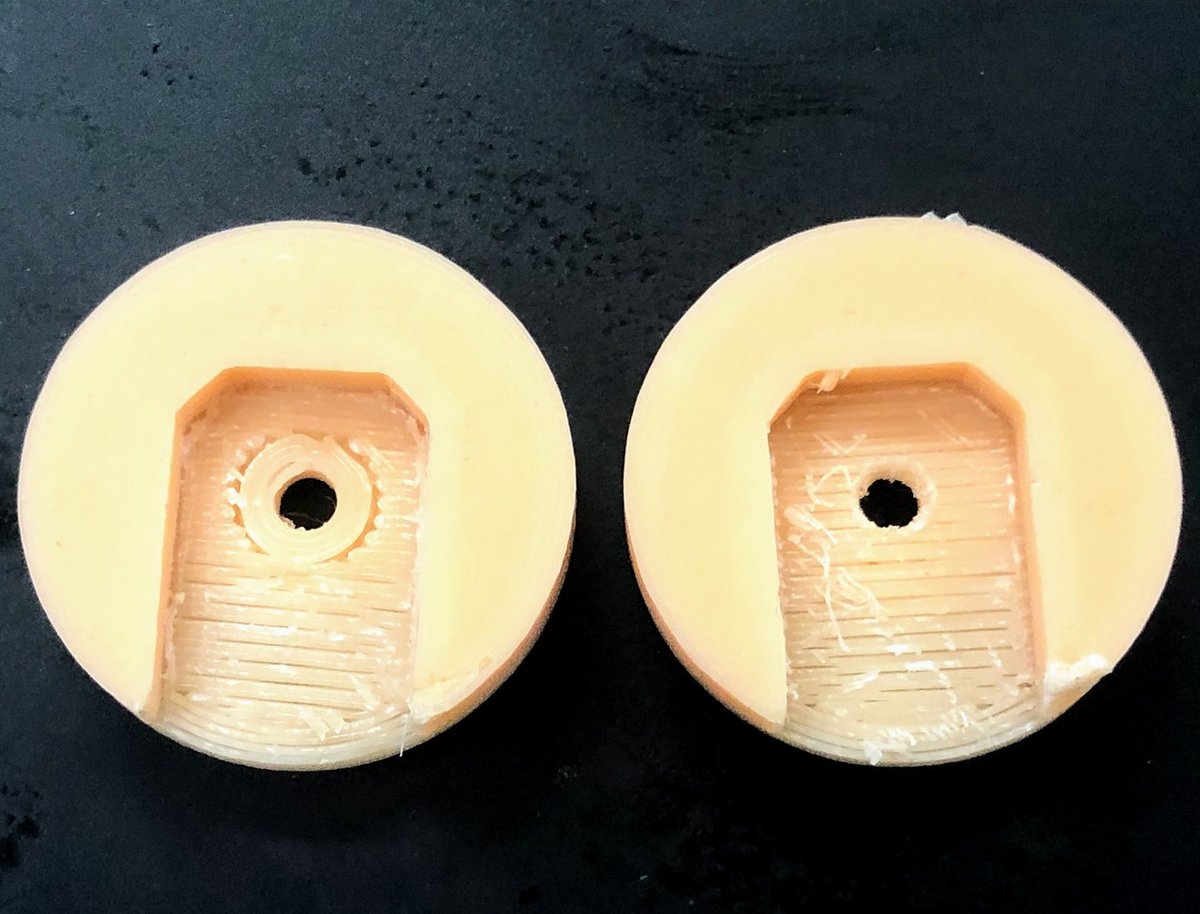
ボルト、ナット座面に対する犠牲ブリッジの応用
犠牲ブリッジによる六角ナット座面やボルトのザグリ座面に犠牲ブリッジを使用するのはRepRapの3Dプリンターの設計でよく見る手法です。
これを使用するとこの部分にサポートを付ける必要が無くなり、造形が容易になります。
やり方は下記の画像のようになります。
下面に向いた穴に対してこのように直線的なブリッジを誘導するように1レイヤー(0.2mm程度)の押し出しを行います。
M5以上など座面が大きい場合は右側のように、0.4mmと0.2mmの互い違いに押し出しとすると良いでしょう。
ボルト座面との接触面が減り座面が陥没しやすくなるため、この手法を嫌う人もいるようです。
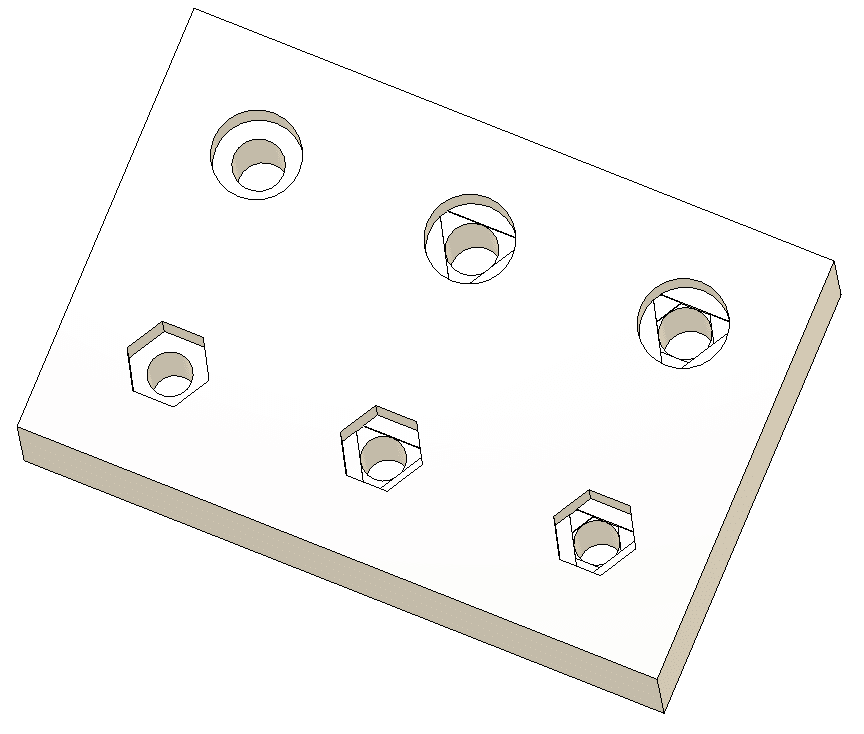
犠牲ブリッジの適用範囲を広げる
犠牲ブリッジはより広範囲に使用できます。
PrusaSlicerなどではブリッジのパス方向をかなり賢く自動調整してくれますが、どんなブリッジでもうまく行くわけではありません。
下記の点に注意しつつ、犠牲ブリッジを計画します。
ブリッジは橋の両端が必要です。
ブリッジ領域が四角形となるように分割します。
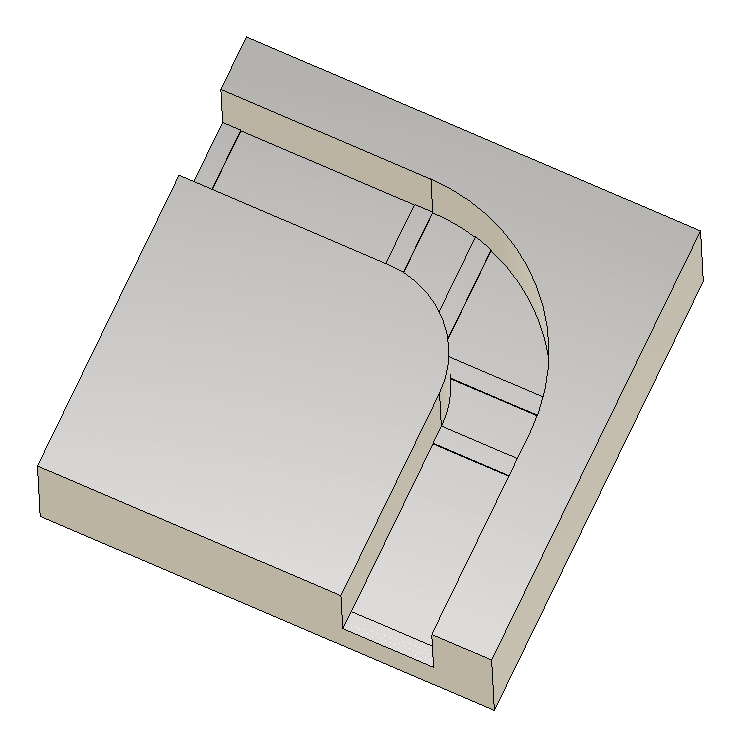
フィレット(R)より面取り(C)を多用する
フィレットではどこかに強いオーバーハングが生成されることになりますが、面取りならサポートの生成は必要ないかもしれません。
そして半径の小さなフィレット(レイヤー厚みの3倍ぐらいまで)はどっちも大差がないので、どちらでも構わないなら面取りを使いましょう。
そしてフィレットはSTLファイルのデータサイズがとても増えます。
面取りも少し増えますが大した増加ではありません。
データのハンドリング、スライスを簡単にするためにも、面取りでよければ面取りましょう。
鋭いコーナーでの材料のはみ出しなどが発生し、コーナー部のやすり掛けが必要になるぐらいなら、0,5~1.0mm程度の面取りを施しましょう。これだけではみ出しは大きく軽減されます。
そしてフィレットを1つをやめた分のデータ量をたくさんの面取りに回すことができます。
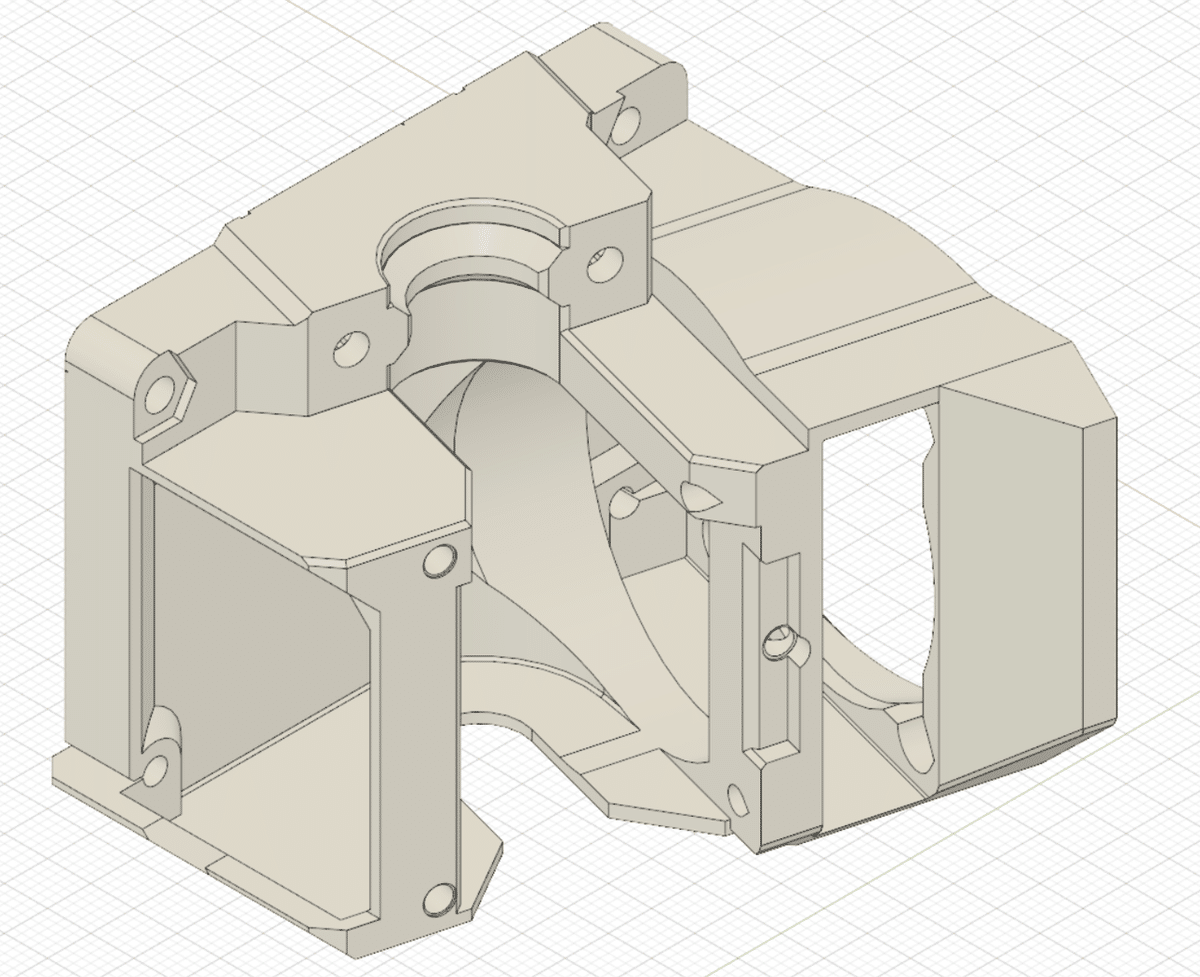
STLファイルは高解像度な設定でエクスポートする
穴が小さくなったり、なだらかな形状の部分がガタガタな感じで出力されるのはSTLファイルのエクスポート設定が原因かもしれません。
STLファイルのデータサイズが大きくなりますが、高品質な設定でエクスポートしましょう。
(スライスする時のことを考慮すると30Mbyte程度を超えない程度が目安)
STLファイルは理想の形状から妥協の産物として、小さな3角形の表面の集まりとして作られますので、曲面があると原理的に欲しい形状とは乖離していきます。
困っている話を聴くのは、小さな穴が小さく印刷されてシャフトが通らないとかネジがささらないとかでしょうか。
(プリンタの標準設定で樹脂を多めに出している場合もありますが、そもそもデータが...という場合があります。)
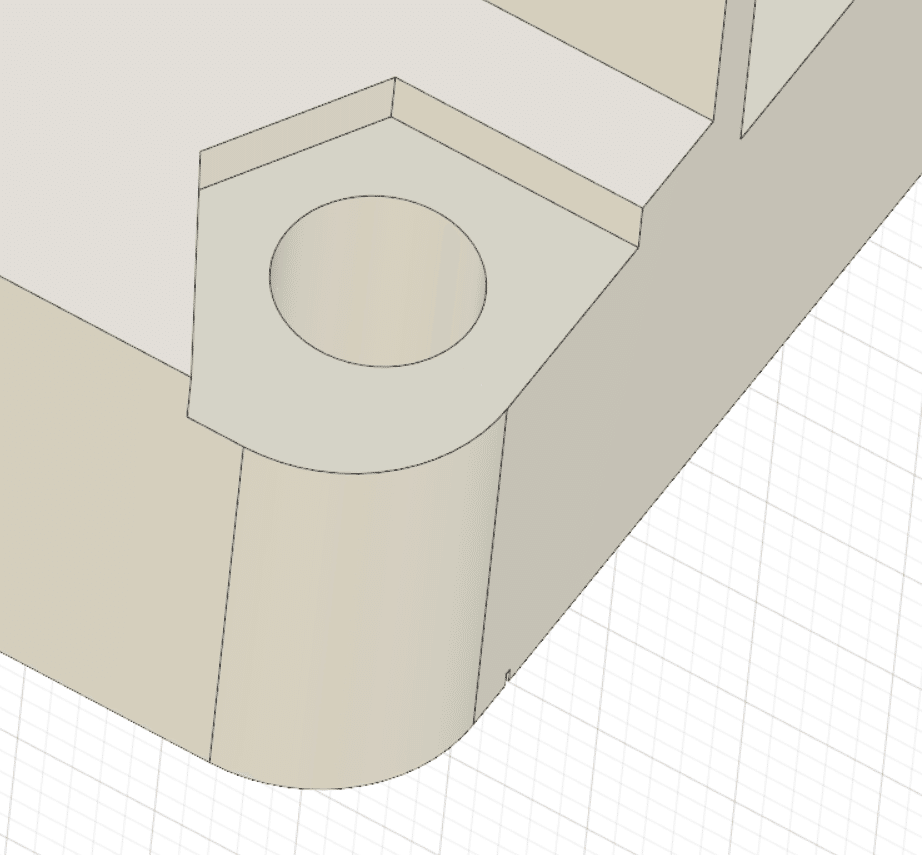
理想の穴の円周をつなぐようにメッシュを張っていくので、メッシュが荒いと実質的に面が内側に入り込んでいくのが分かるでしょうか?
メッシュが粗ければ粗いほど穴は小さく、軸は細くなります。
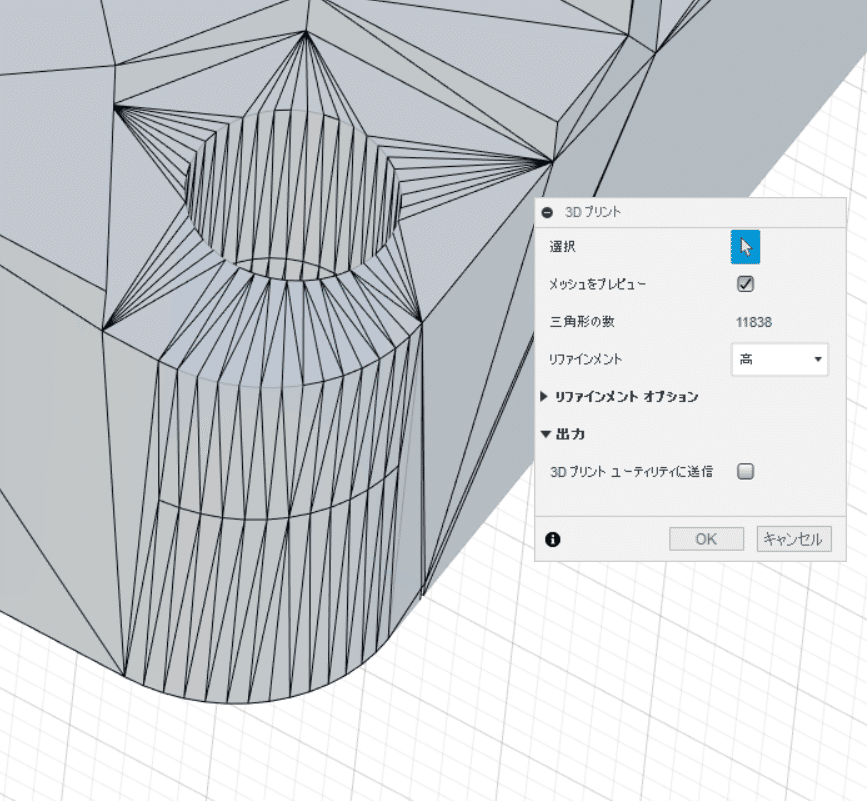
粗い場合はこんな感じにカクカクで内径が小さくなります

ナットを埋めたいときにナットのコーナーを逃がす
画像のまんまですが、鋭いコーナーを鋭く造形するのは大変です。
隅の部分は逃がしちゃいましょう。
画像のようにすれば最小限のクリアランスでナットが埋め込み可能です。
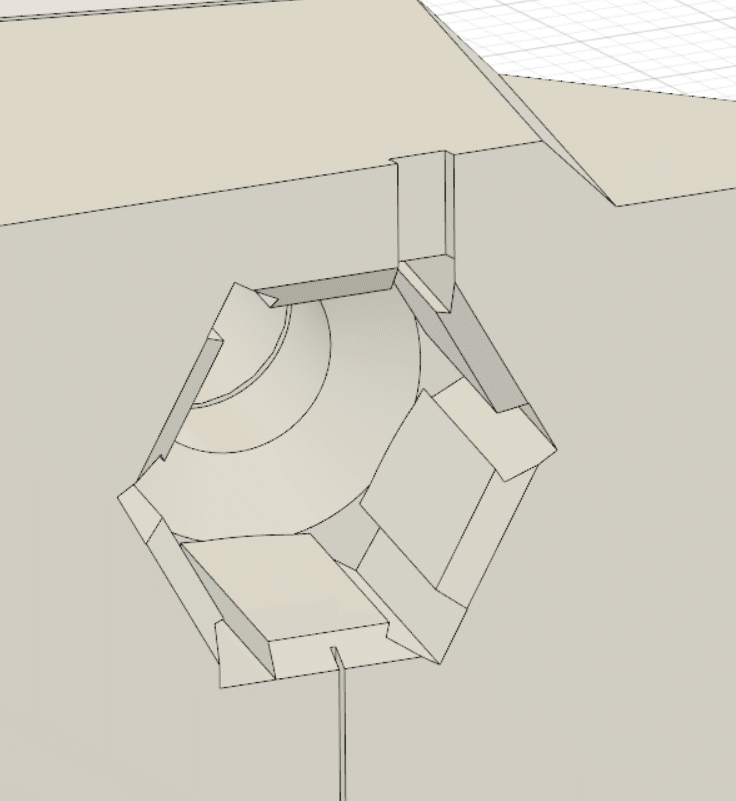
必要な部分だけ強度をアップさせる
軽量だけど丈夫なものを作りたい!
厚みは必要だけどインフィル率は低めにしたい、でもここだけは丈夫にしたい!という場合どうしましょう?
インフィルの割合を場所ごとに変更をするというのは、非常に大変です。
(スライサーの設定によっては不可能ではないですが...)
そこで、こんな方法もあります。
補強したい部分に0.1mm程度のスリットや小さな穴をモデリングしましょう。
(モデルは3DプリンタのGT2ベルトの固定具です。左右からのベルトテンションに耐える必要があります)
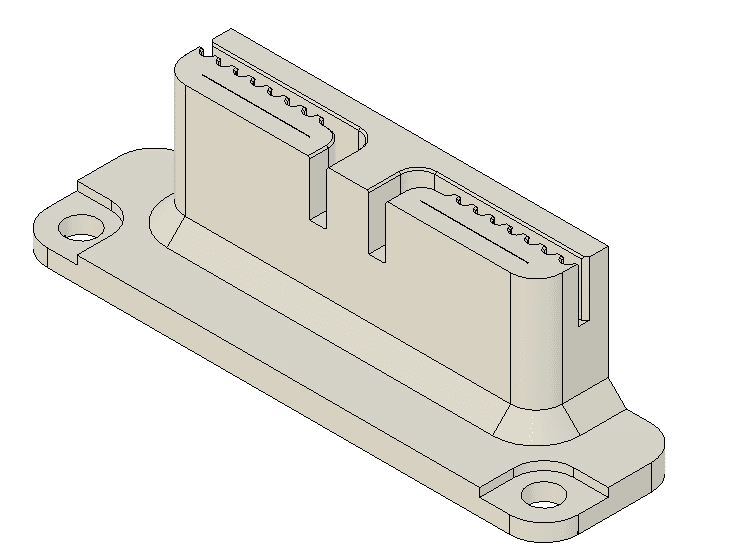
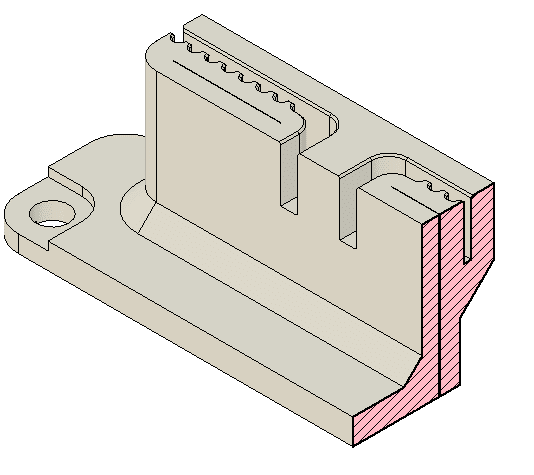
するとスライスが下の画像のようになります。
スリットの周りにシェルが造形されることにより実質的にインフィル100%と似たような状況になりました。
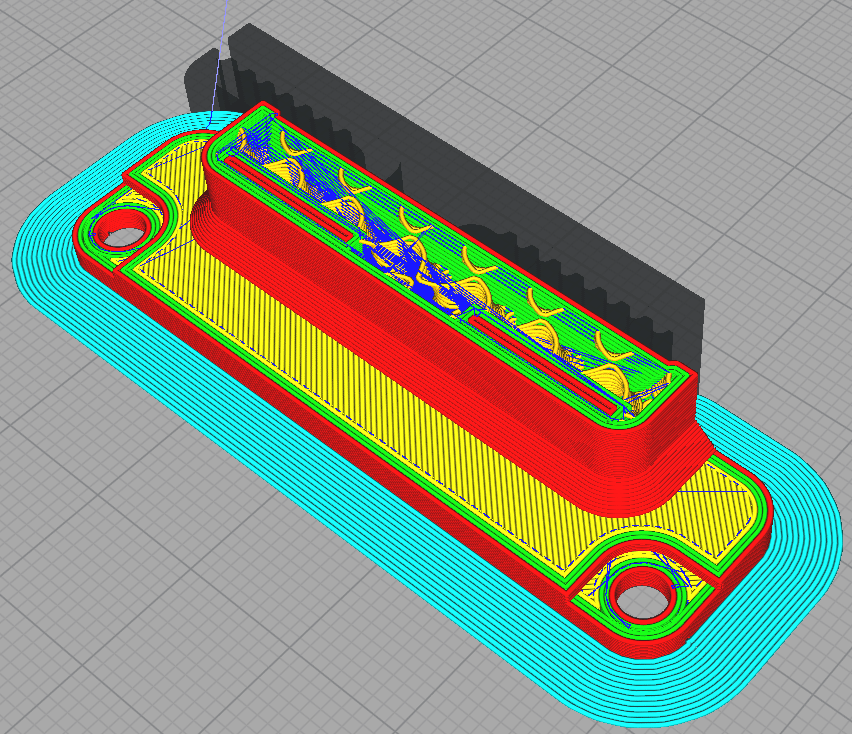
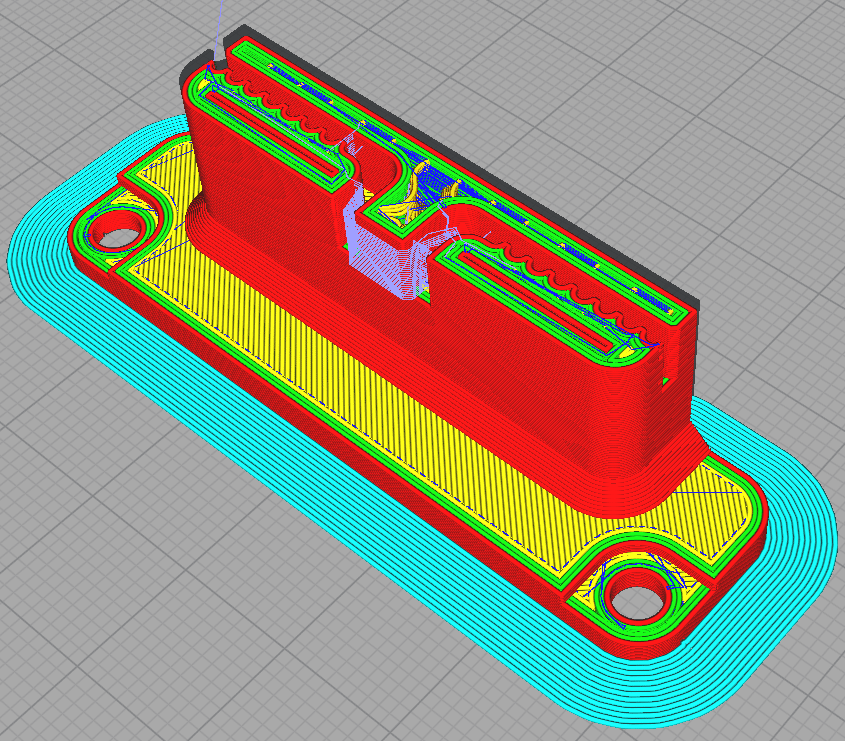
ネジ穴のタイトさを安定させる(直線部は精度が高い)
普通のネジを3Dプリント品にセルフタッピングによりねじ込んで固定する場合、どのようにモデリングしていますか?
「M3ならφ2.8の穴を設定する?」「いや、うちはφ2.6だ」「タッピングネジだから関係ない」「インサートナット使うわ」
よろしい。インサートナットも有用。わかる。
でも手軽にいろいろな環境でできるだけ同じような保持力や締めやすさにできると良いですよね。
そこでセルフタッピングする穴は、そもそも6角や8角の穴にしてしまいましょう。
丸い穴だとSTLファイルへのエクスポート設定やプリンタの吐出樹脂量の違いで大きくバラついてしまいますが、角穴ならそのばらつきは小さくなります。
それに角穴ならその通りにSTLファイルが生成されます。
吐出の不安定さやコーナーでの樹脂余り、そしてネジ山で変形or削られた樹脂もネジ山の来ない角穴のコーナー部に集約されます。
こんな感じのモデルをモデリングして、ピッタリの角穴を探してみましょう。
四角よりは6角形か8角形の穴がお勧めです。
横穴に使う場合も30度か45度回せばサポートも入りません。
私の好みはM3の穴なら2面幅2.7mm六角穴です。
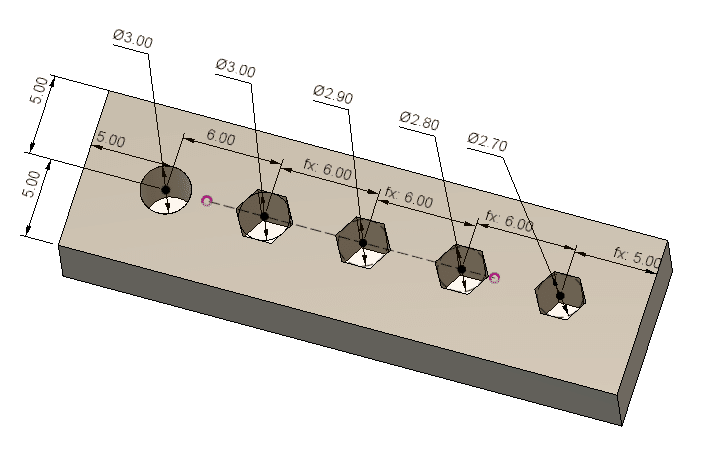
メッシュも、丸い穴と違って思ったとおりの形状になります。
データ量も小さくて済みます。
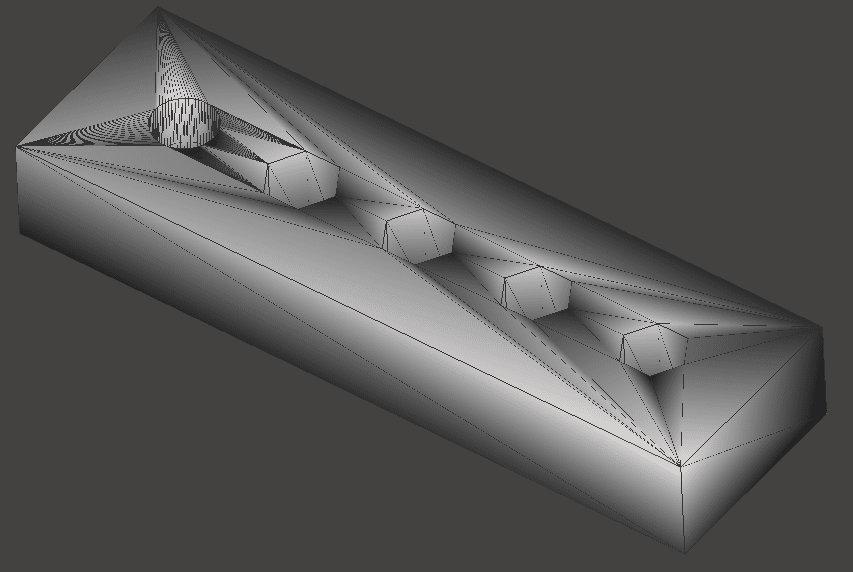
印刷してみてちょうどよい角穴を見つけてください。
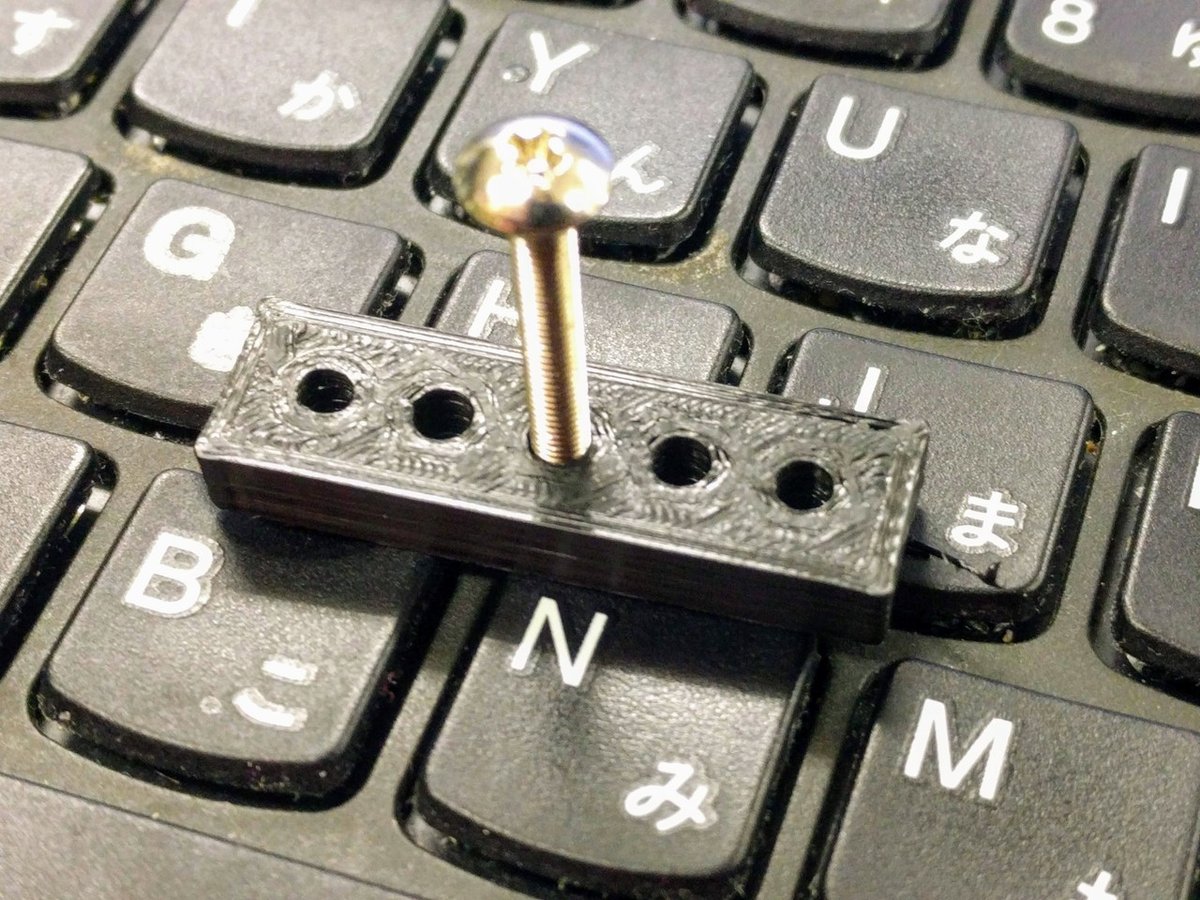
軸にスリットを入れて強く&簡単にする
Z軸方向に回転軸やはめ込み軸を作りたい場合に、こんなことが多いのではないでしょうか?
・積層で割れやすいので細くて強度のある軸が難しい。
折れたり、再設計の結果太くなりがち。
・シェルのシーミング部(シェルの印刷スタート/エンド)が盛り上がり、回転しずらい
・印刷時の寸法誤差やはめ合いに敏感で、都度調整が必要
というわけでこんな方法を使ってみましょう。
軸にスリットをこのように入れます。
スリット自体は0.1~1㎜程度、はめ合いの敏感さを減らしたい場合はスリット幅を広げ、スリットを軸の中心よりやや奥まで切り込むと良いでしょう。
面取りをしておくとコーナー部での樹脂のはみだしが減ります。
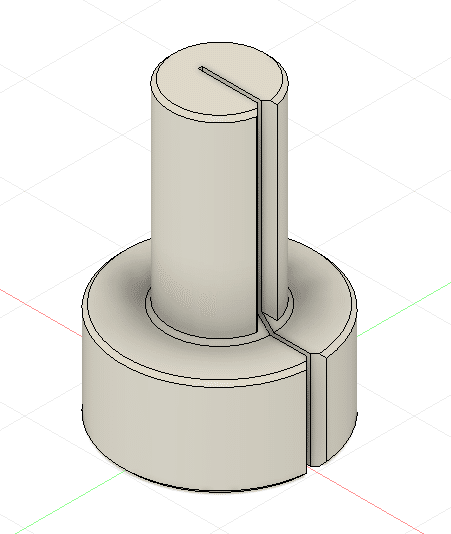
スライスするとこのようになります。
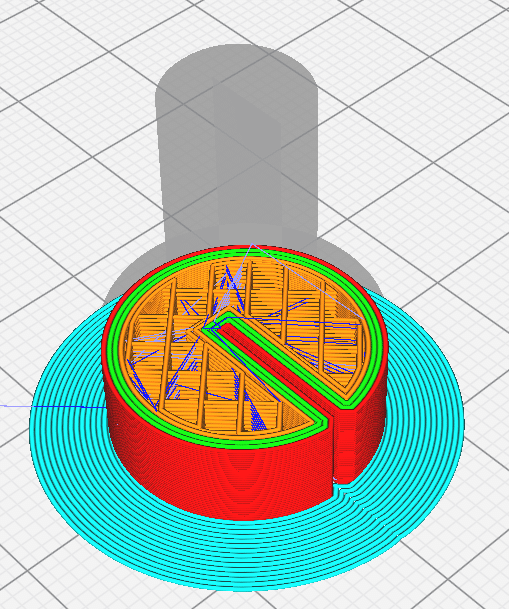
まずスリットによってシェルが内側に入り込みますので、中実度が高まり強度が増します。
そしてSeam Positionの設定をSharpest cornerにするとシーミングはスリットの内側に来ますので回転を邪魔しません。
さらにスリットのおかげで軸が直径方向に変形できますので、多少のキツめでも挿入でき、がたつきずらい軸になります。
印刷するとこんな感じ。
ガタつきはないけど手で差し込める軸と穴ができました。
穴側も浅くスリットを入れるとシーミングの影響を排除でき、内側が滑らかになります。
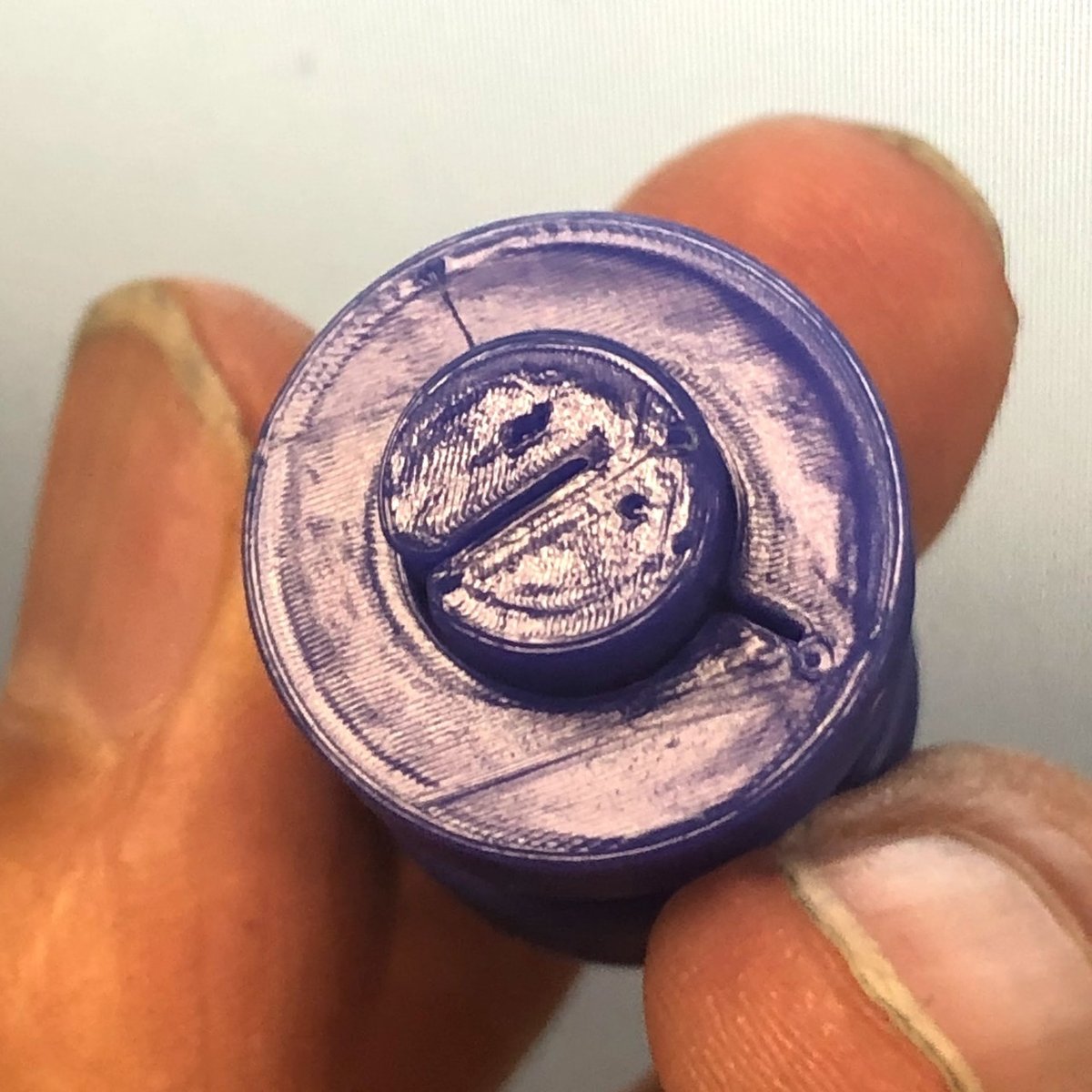
穴にキャップをして小さな印刷エリアを接続する
ネジで固定したい場合に造形の端に近いところに穴をあけたい場合が多いですが、端は印刷面積が小さいので造形が難しくなりがちで強度が出しずらい部分です。
そこで、XY方向の穴などにノズル直径の2倍の蓋を設定してます。(0.4mmのずるなら0.8mmの厚み)
ネジを通す時にはやや強引ですがとがったドライバーなどで蓋を破壊するか、尖り先のネジで無理やりネジを通します。
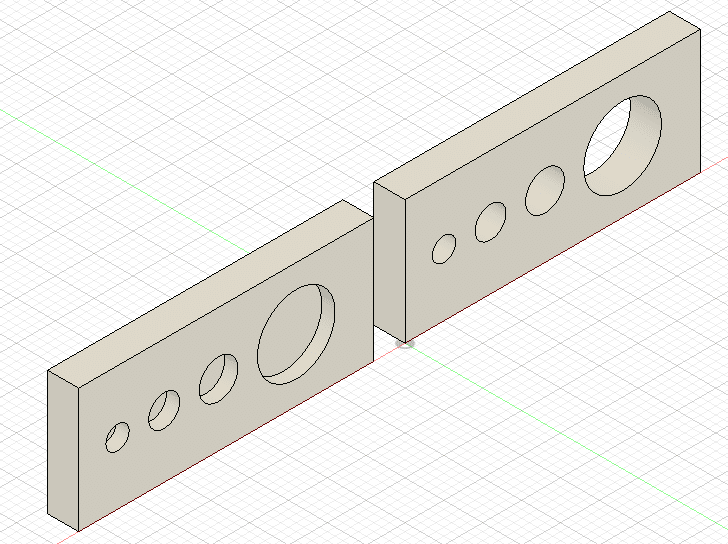
モデリングのポイントとしては穴の始まりから少し離したところに蓋をします。(今回は厚い部分ではないので中心付近)
このようにすると強引にネジを通しても、壊した蓋部分が挟まって締結の邪魔をすることが無いので安心です。
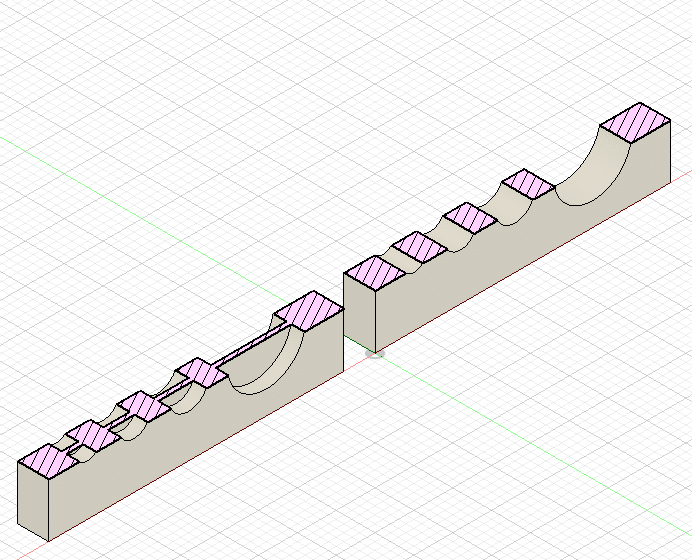
スライスはこんな感じになります。
アウターシェルが一筆書きに印刷され、リトラクションが減ってきれいに連続的に印刷されやすくなります。
印刷中の小さい部分の破損の可能性が減ります。

サポートが無くてもきれいに印刷されやすくなりますね。
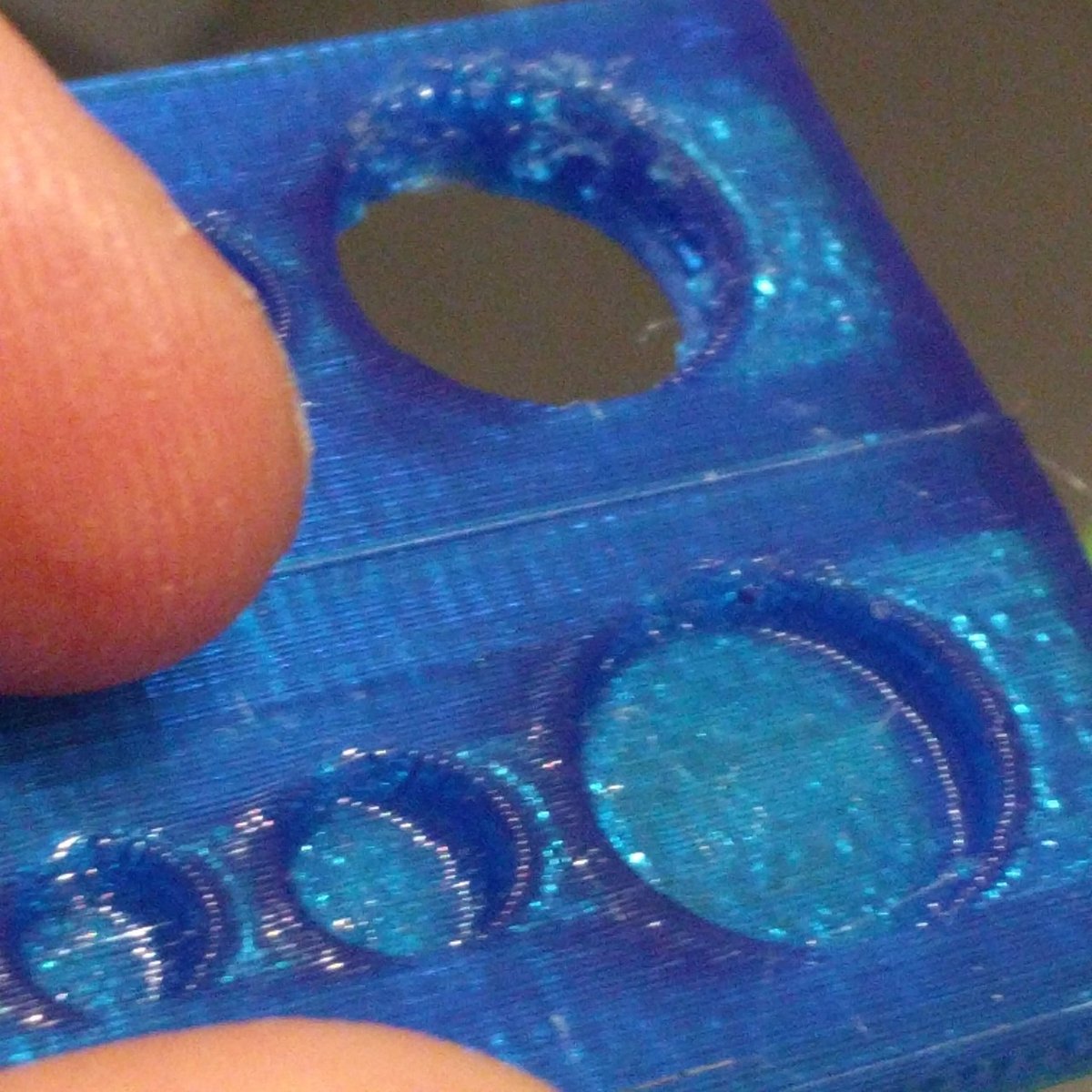
薄い部分のエッジにだけ肉厚を追加する
肉薄なケースを作りたい場合などがありますが、肉を薄くすると開放されたエッジや配線を通す穴などの開口部から破損する場合が良くあります。
そういう場合は全体の肉厚を厚くせず、開口部周囲のみ肉厚を追加しましょう。開口部周囲が肉厚になると、肉厚が増加した直接的な効果以上に開口部全体に応力が分散し壊れづらくなります。
スケッチのオフセットを使用すると簡単に肉付けをすることが可能です。
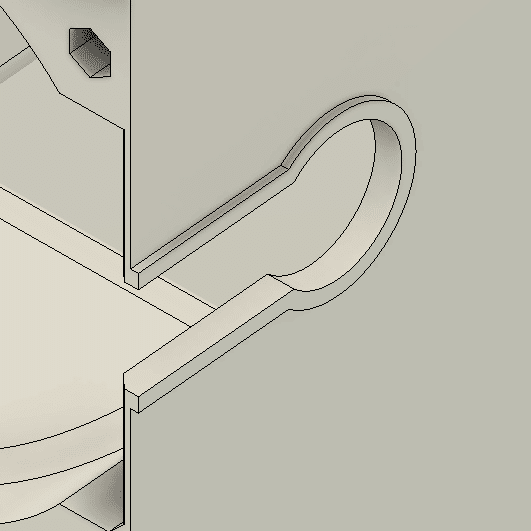
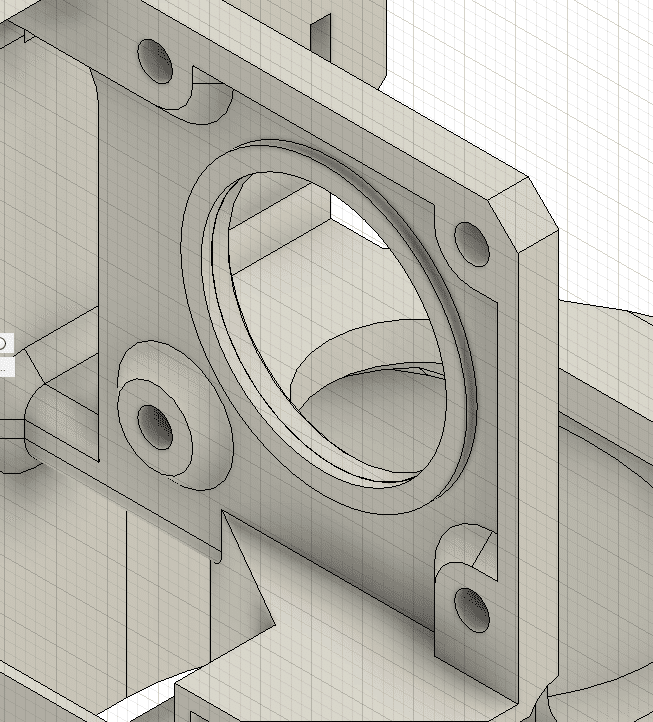
形状の強調
溝形状の先端をスリットにする
ギアのセレーションなど、ノズル直径に対して小さな谷形状を特別にはっきりと印刷したいときに使えるテクニックです。
ツイートのように、谷形状の先端に幅は0.1mm程度のスリットを形成し、シャープに造形されるように細工します。スリット幅が0.1mmを下回るとスライサーによっては上手く機能しない場合があります。
なお設定にもりますが、山形状側に小さなRを付けると最もエッジが尖がっている谷のエッジ側に終始点(シーム)が誘導される可能性が高いくなります。シームがスリット側に来ればよりピッタリと嵌めやすいでしょう。
スライス結果を良く確認しよう。
Thank yyou, @Shiba_8ro
3Dプリンタでセレーション(サーボ出力軸のギザギザ)穴を印刷する際にギザギザの谷をピン角にする方法を発見したんじゃがこれは以前ツイッタでみたものを思い出しただけなのかもしれない疑惑
— Yoshihiro Shibata (@shiba_8ro) November 1, 2023
軽く検索しただけでは前例は出てこなかったんじゃが前例があったら指摘プリーズなんじゃが pic.twitter.com/wIbrSPRwGy
上下に向いたナット埋め込みに対する方法
先ほどのメソッドをセレーションではなく、ナットの埋め込みに応用してみるとこのようになります。
下面に来る場合は犠牲ブリッジを併用しても良いでしょう。
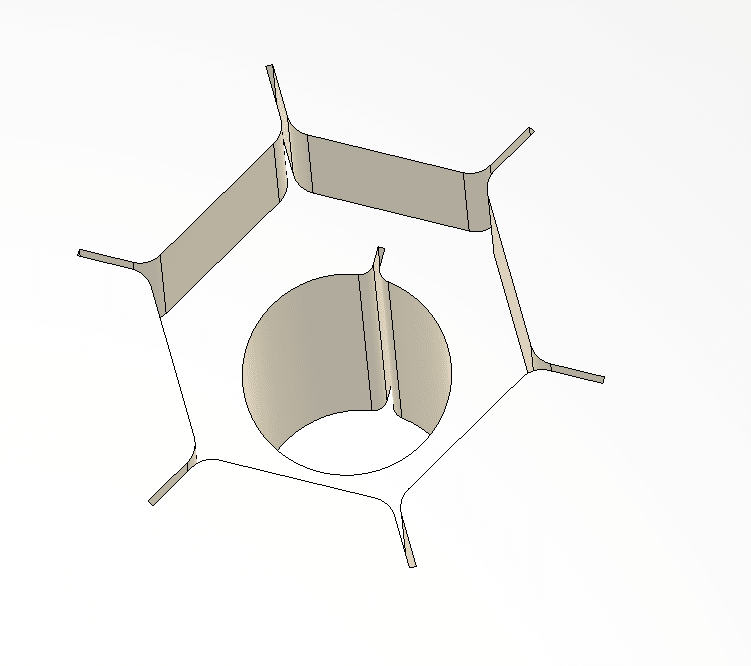
番外編
ネジは強度部材
熱によって樹脂を融着させるFFF/FDM方式は縦方向の引張強度が弱いといわれます。装置や材料、造形設定以外で強化するにはどうすればいいでしょう?
引張に弱ければ最初から圧縮しておけばいいのです。鉄筋コンクリートのように。
貫通させた穴の終わり付近の直径を絞って食いつかせたり、ナットを入れて固定をして材料を事前に圧縮しておくことで縦方向の引張りに対抗することができます。
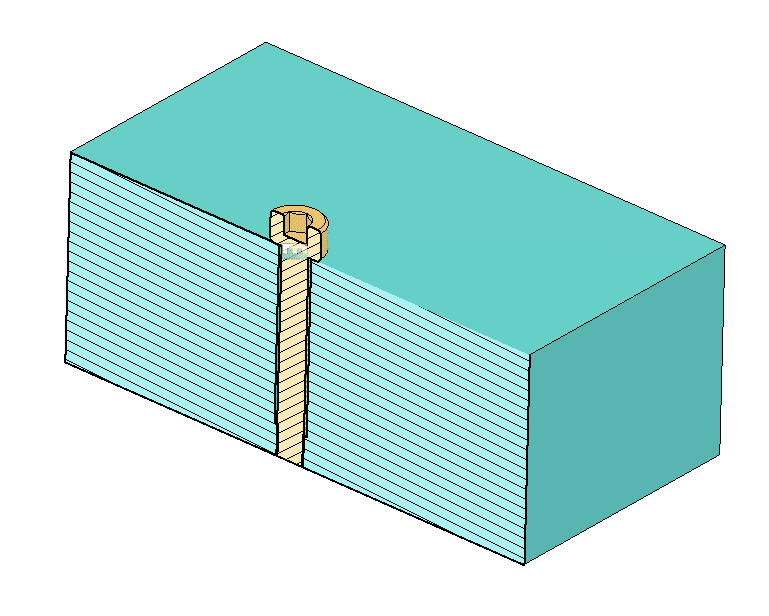
最後に
本記事では機能としての形状が大きく変わってしまうような「サポートが必要ないように水平に近いオーバーハングを避ける」等のTipsは載せていません。3Dプリントによって実現できる、より自由な造形をできるだけ制約なしに楽しんでほしいからです。
モデリングの最後の辺りで今回のTipsを使って印刷を少しでも簡単にしてもらえればと思います。
もしよろしければ購入やサポートを!
購入していただくと、新しいTipsが追加されるとお知らせが届きます。
そしてなによりご購入いただけるとやる気が出ます!
ここから先は
記事をサポートしていただくと、一層のやる気と遊び心を発揮して新しい記事をすぐに書いたり、3Dプリントを購入してレビューしたりしちゃうかもしれません。