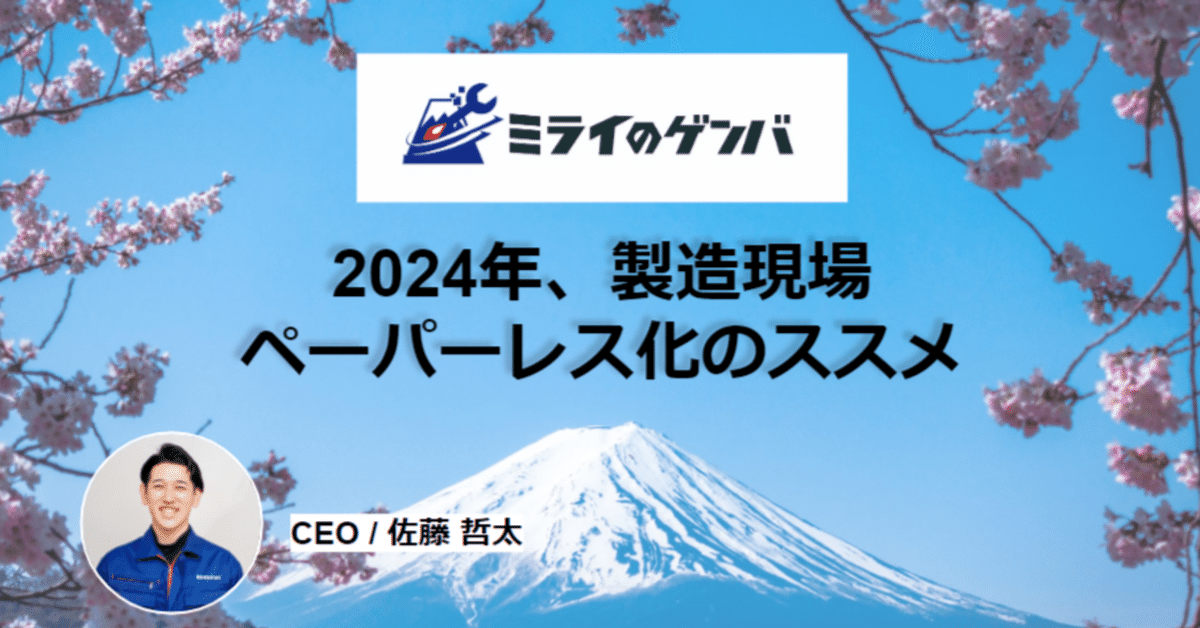
2024年、製造現場ペーパーレス化のススメ
こんにちは。ミライのゲンバ代表の佐藤です。
私達は、「未来の現場を増やす」をビジョンに、製造業DX SaaSミライのゲンバシリーズの開発・運営を行っております。
この度、シード期の資金調達として、総額1.74億円の調達を発表いたしました。
多くの方の協力や応援の上で、今の挑戦ができていることを嚙み締めると共に、そんな方々に「私達がどんなことを成し遂げたいか」をきちんと説明する責任があると強く感じています。
そこで今回は、私達のビジョンである「未来の現場を増やす」に込めた思いについてこちらの記事を書きました。
何故、今さら「ペーパーレス」なのか
ペーパーレスという言葉が使われだしたのは1970年代頃のようです。そこから第二期、第三期、IT技術の発展と共に、ペーパーレスな業務スタイルは大分普及したように感じます。
特に、IT業界やスタートアップに身を置く方は、社内の業務としてもそう感じるのではないでしょうか。
しかし、まだまだペーパーレス化が、必要なのに進んでいない領域があります。その一つが製造業界における現場作業の領域です。
実際に、私達が製造業の工場従事者に約600名を対象に行ったインタビューでも、約7割以上の現場では、未だに主な記録媒体が「紙帳票」でした。
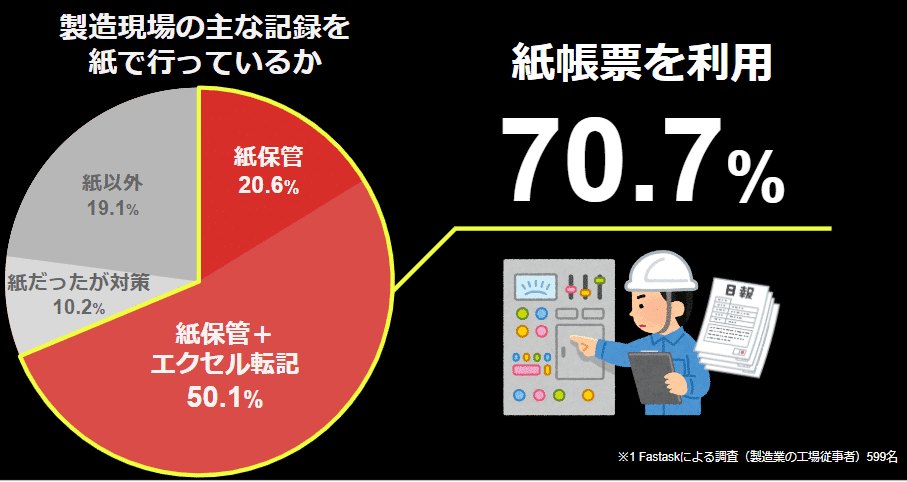
何故、ペーパーレス化の進展が、相対的に遅れているかについては、デスクワークを中心とする業界よりも、以下の様な事情で、デジタル化の難易度が高い環境だからです。
製造現場ではエクセルが使えず、専用ツールの導入が必要。
現場の製造プロセスを変えるための社内調整が大変。
データ化しても、十分に活用するスキルを持った人材がいない。
例えば、中堅・大手企業では、工場其々で、独自の紙帳票の運用が行われています。そして、その現場で働く人々ですら、運用の全貌を把握出来ない程
運用が複雑です。一つの会社に、このような工場が数十拠点あるのです。
これを一つのシステムで統一的に解決することが難しく、全社的なペーパーレス化の推進が困難になっています。
ミライのゲンバは、このような課題を、AIを活用し、従来のノーコードツールとは異なるアプローチで解決しており、数十拠点のペーパーレス化をワンプロダクトで実現することが可能です。
現場データは日本の宝だ。
現場で扱われる紙帳票ですが、例えば下図の様な記録が毎日行われています。
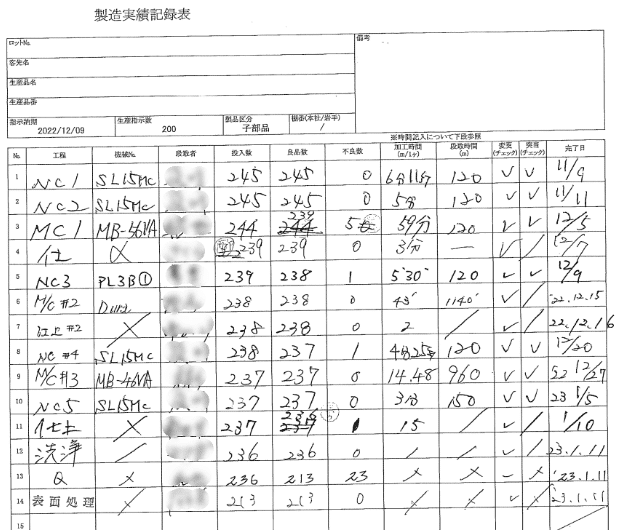
このサンプルの紙帳票のデータだけでも、以下の様なケースで、分析や活用されています。
過去の通過工程を参考に、新規受注時の通過工程や納期を決める。
品質不良の発生率から、想定原価との予実評価を行う。
作業時間の実績から、作業者の能力比較を行う。
作業時間の実績から、想定原価との予実評価を行う
それ以外にも、以下のような職人さんの加工ノウハウの記録も沢山含まれています。
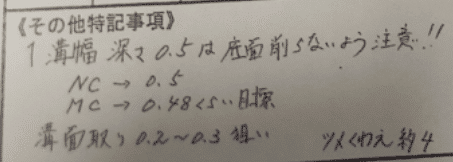
こちらでご紹介したもの以外にも、検査記録、設備点検表、日報、不良品報告書、ヒヤリハット報告書、工数記録表など、1工場で数種類から数十種類の紙帳票を運用しています。
これを、管理者や経営者が日々眺めることで、記憶や経験として定着させ、職人芸という形でアウトプットしていたり、
膨大なコストをかけて、エクセルやシステム転記をすることで、辛うじて活用できる状態にしている。というのがこれまででした。
2024年、現場データの真価が発揮できる時代になった。
昨今のChatGPTの盛り上がりにみる、AIの急速な汎用化により、これまで活用が難しかった、文脈理解を必要とするビックデータや非構造化データの活用可能性と価値が高まっています。
またノーコードツールのような設定作業を前提にしたアプリケーションではなく、AIによるパーソナライズを中心にしたアプリケーションの開発技術も急発展していると感じています。
私達は、この様な変化を捉えて、2024年だからこそ、製造現場のペーパーレス化を推進できるタイミングではないかと考えました。
現場データをデジタル化して成し遂げたいこと
このような現場の紙帳票をデジタル化することで私達が成し遂げたいことを3点挙げていきます。
①業務の効率化・データ活用で、工場の競争力を上げ続ける。
製造業のデジタル化を加速させ、現在の昭和モデルから、未来モデルへの移行を実現することで、業務効率化や売上・利益拡大のための前向きな活動を増やしていきます。
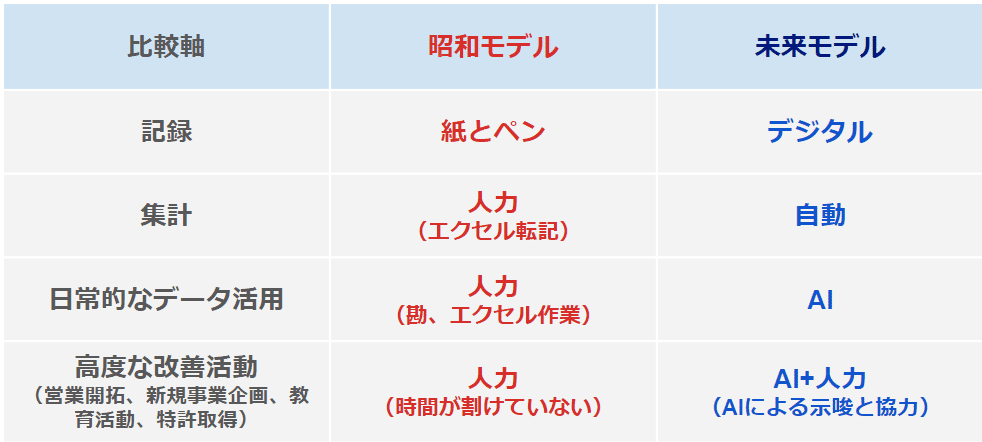
未来モデルへの移行は、コスト削減や時間捻出を生み出すと共に、中長期的には、そこから捻出された時間から新しい改善活動により複利的に効果が増大していきます。
2022年製造事業所調査(総務省・経済産業省)によると、国内製造業の総出荷額は、330兆円あるそうです。
仮にこの内、10%分の粗利創出効果が実現できると、33兆円規模の経済効果があると考えることができます。
一つ一つの工場の生産性や競争力が上がれば、新規営業や新規事業にも挑戦できます。こうして新しく生まれた利益は、国内で関わっている私達一人一人に行き渡り、生活をより豊かにしてくれると信じています。
「出来る!もっとやろう!」に溢れた、更にモメンタムのある産業にしていきたいです。
日本製鉄時代、長い間、原因が特定出来なかった鉄鋼製品の溶接不良について、対策に繋がる発見があった時の嬉しさやワクワクは今でも忘れません。
小さいことで良いのです。工場で働く方々が、改善活動に専念できる世界を広げていきたいと強く思います。
②来るロボット大活躍時代に繋がるデジタル中心のオペレーション
日本の深刻な人手不足問題を背景に、産業用ロボットや協業ロボット、IoTデバイスの導入も拡大するでしょう。
世界のロボット密度統計では、日本よりも特殊出生率が低く、人口減少の問題が深刻化しているシンガポールや韓国は、ロボット復旧率が日本の2倍以上に達しています。
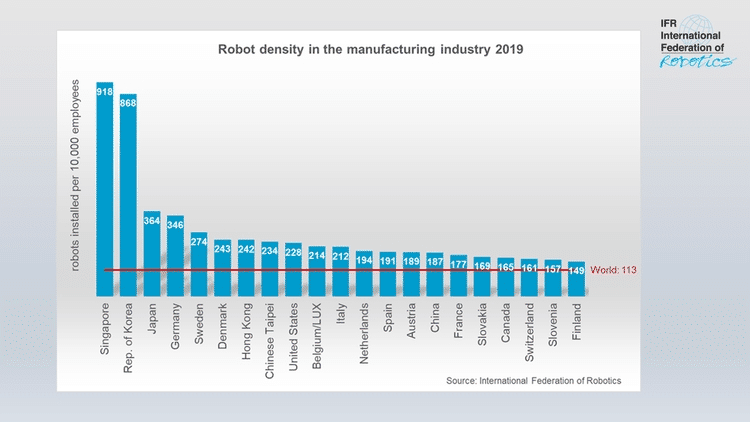
ここで問題になるのが、ロボットは、アルゴリズム(秩序ある処理フロー)に基づいて動作するため、アナログ中心の製造フローに、ポンっとロボットが導入され、自然にオペレーションに馴染んでいく訳ではないということです。
ロボットはベテラン職人のように、手書きで補足メモが書かれた紙の指示書を受け取っても、上手い具合に解釈をしてくれることはありません。
また自身の作業結果を、紙帳票に手書きして、次の検査工程に紙帳票を手渡ししてくれることもないのです。
将来のロボット活躍社会に繋いでいくためにも、製造指示から作業記録、その後の工程までデジタルで定義していくことが必須になると思っています。
ロボット導入だけでなく、足元で既に進展している海外人材やスポットワーカーの採用等の暗黙知に弱い、「労働者の多様化」においても同じことが言えると考えています。
③日本製 生産管理SaaSの海外輸出
ここまでデジタル化の遅れにフォーカスした話を続けてしまいましたが、とは言え、日本には、様々な領域で、優れた技術や成熟したオペレーションを持った製造拠点がたくさんあります。このような拠点が、米国に比べて、国土面積当たりの拠点数(拠点密度)が10倍以上あるのです。
日本の高い技術力と運用力を持つお客様と、一緒にプロダクトを磨き上げやすい環境は、正にジャパン・アドバンテージだと捉えています。
かつて、トヨタ自動車さんが生み出した偉大な「かんばん方式」は、KANBANとして、世界でも共通の概念となりました。
またものづくり産業を中心に、今日よりも明日が一歩でも良くなるための地道で継続的な活動や姿勢は、KAIZENという言葉で世界中に広まりました。
私達も、日本の製造業の皆様と磨き上げた、ミライのゲンバシリーズで、世界の製造業DX支援も進めていきたい。これも世界に対して、日本の製造業の復権に貢献するものと信じています。
最後に
日本のモノづくりは世界に誇れる技術力で、今でも世界中に付加価値を生み出しています。
「無駄でつまらない作業を減らしていくと共に、蓄積されたデータで新しい価値を生みだす」ことを通じて、世界の発展に貢献出来ると信じています。
当時、建材用の鉄鋼製品を製造する工場で働いていましたが、もっと自身の業務効率が上がり技術改善が多く進めらることが出来たなら、
製品を通じて、建設工期やコストの圧縮に、材料の観点で寄与できたと感じます。
例えば、食品製造の改善が進めば、昨日よりももっと健康的で、美味しい食品に出会えるかもしれません。その他にも、宇宙、半導体、自動車、生活用品、あらゆる業界の発展に、工場の発展を通じて関わっています。
お客様の工場が見違える程に、効率的な業務に変わり、感謝のお言葉をいただくことが何よりも嬉しく、やり甲斐を感じます。
そういった事例を一つずつ増やしていく喜びを仲間と共有しながら5年、10年、30年と実績を積み上げていきたいと思います。
中核メンバーを募集しています。
将来の幹部を担っていただくための中核メンバーを募集中です。
読んで下さった皆さん一人一人との出会いで、ビジョンの実現がグッと近づくこともあると思います。
現在、日本でトップレベルに、製造現場の紙帳票を知り尽くしたユニークなチームと、独自のAIモデルが生まれつつあります。
大いなる可能性と確信が入り混じった、とても面白いステージです。
比率20%(30-40時間/月程度)の副業的な活動からでも大歓迎です。
少しでも興味を持って下さった方は、まずはお気軽に、「採用ページ」または、私の「X」か「FaceBook」にお気軽にDMいただけると嬉しいです。
必ず、私からお返事させていただきます!
■採用ページ
https://ripe-moustache-891.notion.site/f9dfd6516cd6429097a33a9e18dd0cd1
■SNS
https://www.facebook.com/tetta.sato.3/