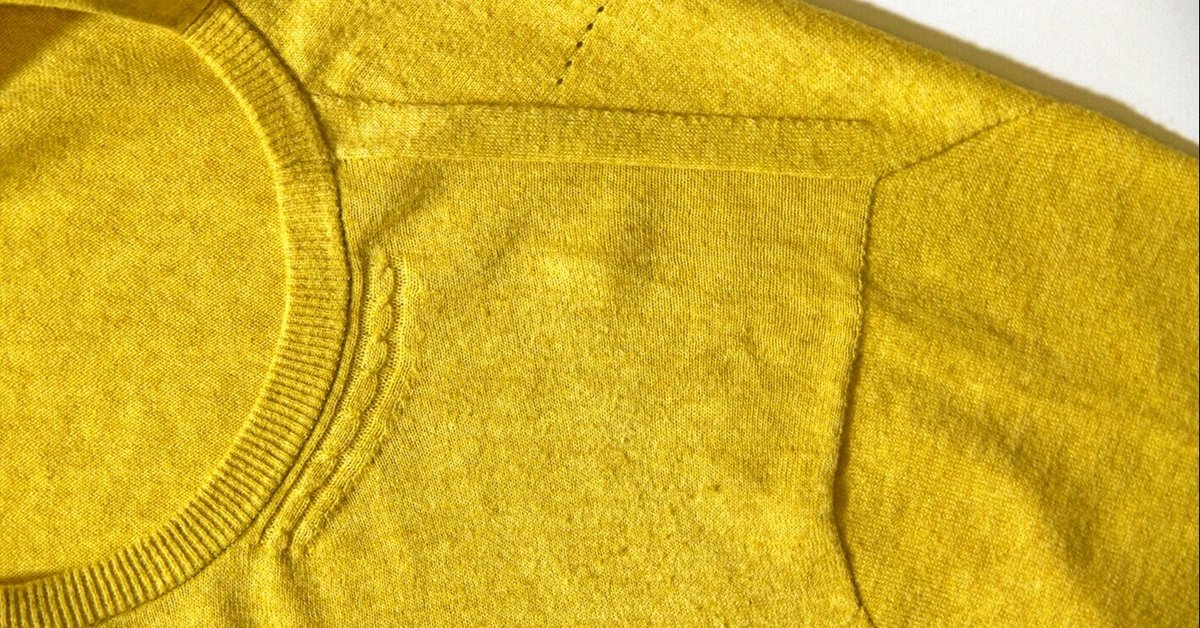
#05 ニット製品のつくり方(ホールガーメント編)
全3回にわたってお話ししてきたニット製品の作り方シリーズ。最後はホールガーメント編です。
ホールガーメント横編機は、和歌山県に本社を置く島製機製作所が1995年に発表した横編み機で、無縫製ニットと呼ばれる一体成型のニット製品が編める機械です。ニット・布帛に関わらず、それまでの服作りはパーツごとに裁断・編まれたものをミシンなどで縫製することで形にしてきましたが、ホールガーメント横編機で初めて縫製なしで服の形にすることができるようになりました。
ちなみに1998年にISSEY MIYAKEから発表された「A-POC」も一体成型の製品ですが、A-POCは経編みを用いた作り方になっていて、ホールガーメント機の編み方とはまた違った作り方になります。
この記事では、ホールガーメントでの作り方や特徴について書こうと思います。
- 編み立て -
成型編みでは、袖や身頃などの各パーツをそれぞれ分けて編んでいましたが、ホールガーメントでは1回の編み立てで右袖・前後身頃・左袖が同時に編まれていき、途中から別々に編まれていたそれぞれのパーツが編み付けられ、製品の形になっていきます。
基本的には袋状に編んでいき、袖と身頃、前後の肩を寄せ目でハギ合わせるのが特徴で、減らし目で編み目を重ねながら形にしていくので縫い代がない状態になります。
また、編み針の形状がホールガーメントを編むのに最適な形になっており、編み目を減らしたり増やしたりする時も、編み目が編み針から外れにくい仕様になっているのも大きな特徴の一つです。
(上)ラッチニードル(従来の横編機)
(下)スライドニードル(ホールガーメント横編機)
(写真:島精機製作所HPより)
- 縫製 -
「ホールガーメント=無縫製」と言われるように、縫製の工程が少なく、編み始めと編み終わりの糸仕末のみでセーターの形にできます。極力単価を抑えたい場合は、衿まで編み続きで作ると縫製の工程が完全に無くなるので、その分単価が安くなります。
ただ、衿まで編み続きで作る場合、ボートネックのような形状は大丈夫なのですが、クルーネックやVネックのような形状は衿が横に広がりやすくなるので、衿だけリンキングで別付けして伸び過ぎを防ぐ事も多いです。
※製品の工賃を抑えたくてホールガーメントを選ぶ人もいるかもしれませんが、ホールガーメント機の値段が普通の横編み機よりもだいぶ高額なので、減価償却費が上がり、編み工賃が高くなっていることがあります。なので必ずしもホールガーメントの方が安くなるとは一概に言えません。
- 加工〜アイロン -
加工やアイロンは、製品の状態で加工・アイロンをするケースが多いです。
アイロンを掛ける際は、他の作り方と違って脇や袖下などに目安となる縫い目が無いので、ねじれないように地の目をしっかり確認することが大切です。特にサンプルや先上げ確認の時に地の目が斜めになっている場合、編み地が斜行しているのかアイロンのせいなのか判断できないため、ちゃんと地の目を通した状態でアイロンしないといけません。
- ホールガーメントで作る場合のメリット -
・その①:縫い代が無い
編み立ての工程でも説明しましたが、ホールガーメントで作られたニット製品は袋状に編んでいく為、脇や袖ぐりなどの接ぎ合せの工程を編み機が行うので、縫い代がなく、フラットになっていることが特徴です。タイツなどのインナーのように皮膚との間にゆとりが無いアイテムやローゲージのような太い糸を使う製品の場合、縫い代がないことは着心地に大きく影響してきます。
・その②:編み立てだけで形にできる
無縫製であることを生産背景の側面で考えると、ニットに限らず縫製ができる人の数は国内では高齢化に伴い今後減少していくと言われています。縫える工場がどんどん減少している中、無縫製で作れるホールガーメントは編み立ての技術があれば製品のかたちにできるため、今後の縫製人口の減少に対応できる作り方の一つになると思います。
・その③:製品の品質を一定に保ちやすい
製品を作る時、特に2枚以上同じ製品を作る場合、必ず気をつけなければいけないことに品質管理があります。なるべく同じものになるよう一着一着に差が出ないようにを作ることが、量産の場合気をつけなければいけない事ですし悩みのタネでもあります。
ニットの場合、品質にバラツキを出してしまう要因は、例えば糸ムラや染色不良、乱寸が出やすい糸や編み組織の使用などいくつかあります。
その中に、縫製時の品質のバラツキも要因の一つとしてあります。ハサミで裁断する時に少し切り過ぎてしまったり、ミシンで縫っている時少し縫い込み過ぎたり余らせたり。一着一着人の手で作っているので全く同じように作る事はできません。なので極力差異がなくなるように工場さんは努力しているわけですが、数が増えれば増えるほどそういった差異が多くなってしまいます。
また、逆に小ロットの場合だと編み立てでトラブルが出ても編み直さずに縫製でカバーできることもありますが、ロットが増えていくとカバーできなくなってしまいます。
その点、ホールガーメントは無縫製なので人の手が入る部分が少ない為品質を一定にしやすく、枚数が多い時=大ロットほどその強みを発揮します。これがホールガーメントの一番のメリットだと思います。
なので、糸ムラや染色不良などが許容範囲に収まるように糸の生産背景をしっかり整えられると、小ロットから大ロットまで数に関係なく一定の品質で製品を作ることができます。
・その④:受注から製品になるまでの時間が短い
縫製の工程が無い分、データさえあれば製品の形にするまでの時間が短いので、他の作り方と比較すると短納期で量産することができ、デリバリーまでの期間が組みやすいです。
・その⑤:編み目の移しが得意
スライドニードルを採用しているので目落ちすることが少なく、目を移すことが得意なので、従来の横編み機では難しい大ベラシなどが可能です。
- ホールガーメントで作る場合のデメリット -
・その①:編める組織が限られている
ホールガーメントは機械の構造上、ミラノリブなどの総針組織が編めませんし、片畦のようなタックが必要な組織も技術が必要なため、編める工場が限られています。また、ボーダーのような多色使いは基本2色(頑張って3色)までで、それ以上色を入れたい場合は機械に別売りのパーツを取り付ける必要があったり柄組が複雑になる為、工場さんと相談が必要です。ちなみに一色につき一つ別売りのパーツを付けると、最大9色まで増やせます。
ホールガーメントで編める代表的な組織
・天竺
・1×1リブ(←編めるけどあまり得意ではない、2×2リブ以上は大丈夫)
・ガーター
・リンクス(1×1かのこは得意ではない)
・ケーブル
・レース柄
ホールガーメントで編めない代表的な組織
・両畦
・片畦(編める工場が限られる)
・総針
・ミラノリブ
・ハーフミラノ
・その②:編み巾(=針立て)を前身頃と後身頃で変えることができない
前身頃と後身頃は同時に編まれてしまう為、脇線の位置を調整して前後の巾を変えてるように見せることはできますが、基本的に前後同じ巾でしか編めません。なので、前後どちらかだけ目を減らしたりプリーツをとったりする事はできません。また、天巾も前後で変える事はできません。
・その③:捨て糸の量が多い
成型と同様に裁断の工程が無いため裁断クズなどのゴミが出ないので、カットで作る場合と比べると資源のロスが少ないと言えます。なので、サスティナブルについて関心が高まっている現在、サスティナブルな作り方として取り上げられることもありますが、編まれた後に捨てられる「捨て糸」として使われる糸が多いので、一概にゴミが少ないとも言い切れません。
※新しい機種では改善されてきているようです
-終わりに-
ホールガーメントが発表されてから25年が経ち、導入もだいぶ進んできましたが、まだまだ編みデータを作れる人材は少ないようです。また、ホールガーメントならではの表現方法もまだ少なく、量産時のメリットで選ばれることが多いようです。
現状では、成型・カット・ホールガーメントで比較すると、表現を求めるならカットや成型、量や短納期で作るならホールガーメントといった棲み分けになります。ただ、島精機さんが開発に力を入れているのがホールガーメントなので、今後も新しい表現方法が増える可能性もまだまだあるのかなと思います。
自分が作りたい服はどの作り方が最適なのか、どの工場にお願いするといいのか。はたまた、元々取引のある工場でできることは何なのか。これまで書いてきた「成型編」「カット編」「ホールガーメント編」の3つの記事が、何かの参考になれば嬉しいです。
いただいたサポートは、活動費に使わせていただきます。