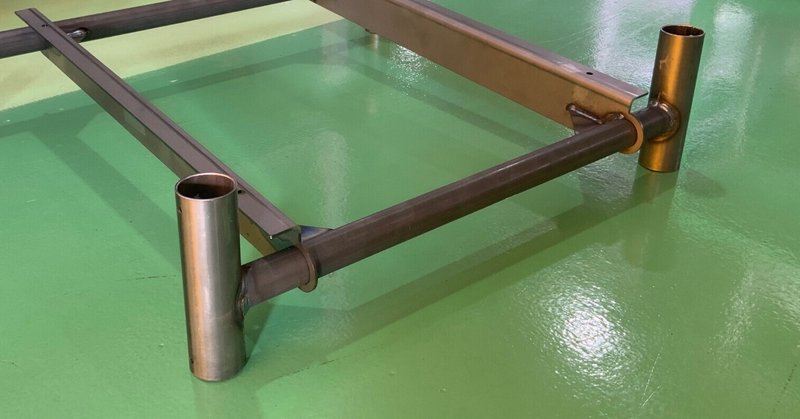
試作フレーム完成も・・・
新ブランドnewold(仮)の組み立て椅子は、最初の段階のメインフレームの試作製作中だったのだけれど、お願いしていた板金屋さんから完成の連絡が入った!これで一気に進むぞ、と心躍るも…出来を聞くと、
「ん〜、まぁ見てみてください。」と歯切れの悪い回答。
とりあえず現物確認に向かった。
工場に入って直ぐに目に入った。
見た瞬間は想定通りに出来上がっている。様に見えた。
「この設計のままだと、正直厳しいと思います。」
担当者T氏は、苦笑いしながら言った。
形にはなっていたものの、各部の精度が出ていない。
この椅子は、金属フレームに木製パーツ等が組み付けられるので、
精度と強度をこのフレームが一手に担う形になる。
それだけ精度が前提になる。
主な原因は、溶接。
部材も構造もシンプルにし、部材点数も最小限にしたが、
結果的に全て溶接による連結の設計だった。
しかも精度が要求される部分でのパイプとパイプの溶接もある。
試作前にも、溶接精度が厳しい事は指摘されたものの、
お互いまずは作ってみようということになったのだった。
結果やっぱり難しかったねって話だ。
このままの構造ならば、何種類もの溶接治具を作ること、
ネジか仕口加工を併用することが必要という話になった。
ただし、それが数を作る時にどれくらい良品が取れるかを考えると、
現実的にはかなり難しいのでは?となった。
それと、もう一つ想定より悪かった結果が。
それは重量。
かなりダイエット設計したつもりだったが、やはり結構重かった。
ここから劇的に軽量化することは、溶接問題も絡んで、
難しいことは簡単に想像できた。
実は以前にも金属フレームと木の椅子は作っている。
その時はパイプは使わず、鉄板を切り抜いて組み合わせる構造で、
溶接精度がそれほど精密でなくても、木部などでカバーできる構造だった。
しかし、やはり重かったため、重量軽減のためにアルミを用いたが、
アルミは材厚が厚くないと強度が保てず、結局は真鍮の補強部品を意匠的に用いて、リベット接合と併用することで強度を持たせていた。
様々な経験から編み出した設計では有ったけれど、
やはり精度と品質を担保するためには、
ロット数十個作る前提で、様々なイニシャルコストを掛ける必要があり、
加えて、仕上げを手作業で行うしかないため、
単価もどうしても高くなる、という話だった。
ということで、根本的に設計変更せざるを得ず、
2歩も3歩も戻ることになった。
方針としては、メインフレームを金属で作ることから離れ、
基本的な外観は保ちつつ、木製で再度設計することにした。
なかなか簡単にはいきませんね。
次回は環境に配慮した座面用クッション材のサンプルを入手してきたので、
その辺のことに触れたいと思っています。
では。
この記事が気に入ったらサポートをしてみませんか?